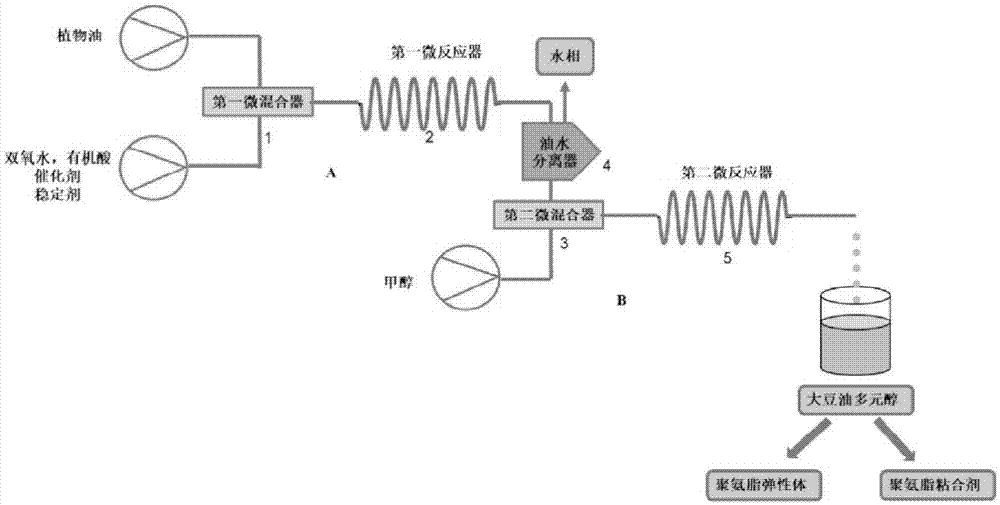
本发明涉及生物质多元醇及其制备方法和应用,具体涉及一种植物油多元醇及其制备方法和应用。
背景技术:
:传统的弹性体聚醚多元醇都是用甘油、二甘醇、丙二醇作为起始剂,环氧丙烷、环氧乙烷作为链增长剂,里面含有98%以上是石油衍生物。目前,人们希望减少对石油的依赖,改善环境。生物质多元醇与石油类多元醇相比,能耗降低23%,非可再生资源消耗降61%,温室气体排放减少36%,以其替代石油基多元醇生产聚氨酯已成为聚氨酯材料发展的重要方向。大豆油作为最廉价丰富的植物油,通过分子改性制成大豆油基多元醇,可用于聚氨酯合成,由此生产的聚氨酯产品不仅安全卫生,还表现出更好的机械性能、热稳定性和耐化学品性。聚氨酯胶黏剂是指在分子链中含有氨基甲酸酯基团(-nhcoo-)或异氰酸酯基(-nco)的胶粘剂。聚氨酯胶粘剂分为多异氰酸酯和聚氨酯两大类。多异氰酸酯分子链中含有异氰基(-nco)和氨基甲酸酯基(-nh-coo-),故聚氨酯胶粘剂表现出高度的活性与极性。与含有活泼氢的基材,如泡沫、塑料、木材、皮革、织物、纸张、陶瓷等多孔材料,以及金属、玻璃、橡胶、塑料等表面光洁的材料都有优良的化学粘接力。然而常规粘合剂的固化时间较长,粘合强度差,韧性低,熔解后流动性不好,稳定性差。部分聚氨酯胶粘剂需要进行改性,增加了粘合剂的成本。技术实现要素:发明目的:为了解决现有的环氧植物油环氧值较高、碘值较低,导致生成的多元醇产品羟值高、粘度高的问题,本发明第一发明提供了一种植物油多元醇的制备方法,第二方面提供了所述制备方法得到的植物油多元醇及其应用。技术方案:本发明所述一种植物油多元醇的制备方法,包括以下步骤:(1)将由双氧水、有机酸、催化剂和稳定剂制成的混合液与植物油分别泵入微通道模块化反应装置的第一微结构反应器中,停留6~8min进行环氧化反应;(2)将步骤(1)得到的环氧植物油与甲醇分别泵入微通道模块化反应装置的第二微结构反应器中,停留10~12min进行开环反应,即得植物油多元醇。步骤(1)中,所述有机酸为甲酸或乙酸,所述催化剂为硫酸或磷酸,所述稳定剂为乙二胺四乙酸;所述植物油为大豆油或棉籽油;所述植物油中的双键、双氧水、有机酸、催化剂和稳定剂的摩尔比为1∶4.5~75∶4.5~7.5∶0.035~0.06∶0.004~0.006,优选1∶6∶6∶0.04~0.05∶0.005。所述环氧化反应的反应温度50~62℃,优选60℃。所述第一微结构反应器的体积为15~60ml,优选为30~40ml。步骤(1)得到的环氧植物油的环氧值为4.5~4.7。优选地,所述双氧水、有机酸、催化剂和稳定剂制成的混合液和植物油先泵入第一微混合器混合,然后同时泵入第一微结构反应器进行环氧化反应。其中,所述混合液泵入微通道模块化反应装置的流速为0.5~1.5ml/min,优选为1.0ml/min;所述植物油泵入微通道模块化反应装置的流速为2.0~6.0ml/min,优选为4.0ml/min。所述步骤(2)中,所述环氧植物油中的环氧基和甲醇的摩尔比为1∶1.5~4.5。所述开环反应的反应温度为80~120℃,优选100℃;反应停留时间优选11min。所述第二微结构反应器的体积为79.6~706.2ml,优选219.44~303.38ml。得到的植物多元醇的粘度为500~1000mpa·s。优选地,第一微反应器的反应产物经油水分离器分离后得到环氧植物油,所述环氧植物油和甲醇先泵入第二微混合器混合,然后同时泵入第二微结构反应器进行开环反应。其中,所述甲醇泵入微通道模块化反应装置的流速为5.16~51.35ml/min,优选为21.95~22.58ml/min。所述微通道模块化反应装置包括通过管道依次顺序连接的第一微混合器、第一微结构反应器、第二微混合器、第二微结构反应器。优选第一微结构反应器和第二微混合器之间设有油水分离器。本发明第二方面提供上述制备方法制备得到的植物油多元醇。所述植物油多元醇的粘度为500~1000mpa·s。本发明第三方面提供所述植物油多元醇在制备聚氨酯弹性体或聚氨酯粘合剂中的应用。优选地,所述聚氨酯弹性体的制备方法参考现有技术,优选方法如下:在氮气保护下,采用预聚体法制备聚氨酯弹性体,将本发明制备的植物油多元醇与水、硅油、开孔剂、催化剂a-33、催化剂a-1、催化剂t-12混合,加入4,4`-二苯基甲烷二异氰酸酯,在70~90℃下反应1.5~2.5h后,用二正丁胺法测定反应体系中游离的nco含量,按扩链系数0.95加入1,4-丁二醇,搅拌混合均匀后浇注于90~120℃的平板钢制模具中,并进行硫化,在80~100℃烘箱中老化20~30h。其中,所述植物油多元醇、水、硅油、开孔剂、催化剂a-33、催化剂a-1、催化剂t-12的质量比为1∶0.015~0.025∶0.005~0.015∶0.015~0.025∶0.002~0.004∶0.0005~0.0015∶0.00005~0.00007。所述植物油多元醇与4,4`-二苯基甲烷二异氰酸酯的质量比为1∶0.7~1.05。优选地,所述聚氨酯粘合剂的制备方法可参考现有技术,优选方法如下:将本发明制备得到的植物油多元醇与丁香酚置于密闭容器,氮气置换;升温至120~140℃,抽真空,氮气鼓泡1~3h;加入异氰酸酯mdi-50,在55~70℃下反应1.5~3.0h,得到聚氨酯粘合剂。所述植物油多元醇、丁香酚、异氰酸酯mdi-50的质量比为1∶0.05~0.1∶0.25~0.4。有益效果:本发明采用微通道技术,制备得到了粘度为500~1000mpa·s的植物油多元醇,该多元醇粘度低,品质好,可替代传统聚醚多元醇,用于聚氨酯粘合剂和聚氨酯弹性体的制备。同时,本发明工艺简单,操作方便,能耗低,副反应少,反应效率高,所得的产物无需进一步处理,非常适合工业化生产。附图说明图1为本发明的流程图。具体实施方式本发明对所制备的大豆油多元醇的相关测定方法如下:(1)根据gb/t12008.3-2009测羟值;(2)根据gb/t12008.7-2010测粘度;(3)根据gb/t24451-2009测拉伸强度;(4)根据gb/t5532-2008测碘值;(5)根据gb6344-2008测伸长率;(6)根据gb6669-2008测压缩永久变形参数;(7)根据gb6670-2008测回弹性能;(8)根据gb10808-2006测撕裂强度;(9)根据gb/t2791-1995测t型剥离强度。实施例1(1)植物油多元醇的制备反应流程图见图1,取200g大豆油(含双键0.99mol)为i组分,取680.18g30%的双氧水(6mol)与281.81g甲酸(6mol)混合,再添加硫酸4.00g(0.04mol)以及edta2.19g(0.005mol)为ii组分,将i和ii组分分别以进样速率1.0ml/min、4.0ml/min同时泵入第一微混合器1中,混合后泵入第一微结构反应器2(30ml)中,保持反应停留时间6min,于常压和60℃下反应,得到的环氧大豆油的环氧值为4.52;取170g甲醇(5mol),设置进样速率为21.95ml/min,将经油水分离器4分离后得到的环氧大豆油和甲醇同时泵入第二微混合器3中,混合后泵入第二微结构反应器5(296.45ml)中,保持反应停留时间11min,于100℃下进行反应,收集油相产物即得大豆油多元醇。(2)植物油基聚氨酯弹性体的制备在氮气保护下,采用预聚体法制备聚氨酯弹性体,将100g大豆油多元醇与1.5g水、1.0g硅油、2g开孔剂、0.3g催化剂a-33、0.1g催化剂a-1、0.006g催化剂t-12混合,加入4,4`-二苯基甲烷二异氰酸酯100g,在80℃下反应2h后,用二正丁胺法测定游离的nco含量,按扩链系数0.95加入1,4-丁二醇,搅拌混合均匀后浇注100℃的平板钢制模具中,并进行硫化,在90℃烘箱中老化24h,即可制得大豆油基聚氨酯弹性体。(3)植物油基聚氨酯粘合剂的制备取100g大豆油多元醇与4g丁香酚置于密闭容器,氮气置换;升温至130℃,抽真空,氮气鼓泡2h;加入25g异氰酸酯mdi-50,在65℃下反应2h,得到聚氨酯粘合剂,t型剥离强度=4.5n(25mm)-1。实施例2(1)植物油多元醇的制备反应流程图见图1,取200g大豆油(含双键0.99mol)为i组分,取680.18g30%的双氧水(6m0l)与281.81g甲酸(6mol)混合,再添加硫酸4.00g(0.04mol)以及edta2.19g(0.005mol)为ii组分,将i和ii组分分别以进样速率1.0ml/min、4.0ml/min同时泵入第一微混合器1中,混合后泵入第一微结构反应器2(35ml)中,保持反应停留时间7min,于常压和60℃下反应,得到的环氧大豆油的环氧值为4.61;取170g甲醇(5mol),设置进样速率为22.39ml/min,将经油水分离器4分离后得到的环氧大豆油和甲醇同时泵入第二微混合器3中,混合后泵入第二微结构反应器5(301.29ml)中,保持反应停留时间11min,于100℃下进行反应。收集油相产物即得大豆油多元醇。(2)植物油基聚氨酯弹性体的制备在氮气保护下,采用预聚体法制备聚氨酯弹性体,将100g大豆油多元醇与1.5g水、1.0g硅油、2g开孔剂、0.3g催化剂a-33、0.1g催化剂a-1、0.006g催化剂t-12混合,加入4,4`-二苯基甲烷二异氰酸酯100g,在80℃下反应2h后,用二正丁胺法测定游离的nco含量,按扩链系数0.95加入1,4-丁二醇,搅拌混合均匀后浇注100℃的平板钢制模具中,并进行硫化,在90℃烘箱中老化24h,即可制得大豆油基聚氨酯弹性体。(3)植物油基聚氨酯粘合剂的制备取100大豆油多元醇与4g丁香酚置于密闭容器,氮气置换;升温至130℃,抽真空,氮气鼓泡2h;加入25g异氰酸酯mdi-50,在65℃下反应2h,得到聚氨酯粘合剂,t型剥离强度=4.4n(25mm)-1。实施例3(1)植物油多元醇的制备反应流程图见图1,取200g大豆油(含双键0.99mol)为i组分,取680.18g30%的双氧水(6mol)与281.81g甲酸(6mol)混合,再添加硫酸4.00g(0.04mol)以及edta2.19g(0.005mol)为ii组分,将i和ii组分分别以进样速率1.0ml/min、4.0ml/min同时泵入第一微混合器1中,混合后泵入第一微结构反应器2(40ml)中,保持反应停留时间8min,于常压和60℃下反应,得到的环氧大豆油的环氧值为4.63;取170g甲醇(5mol),设置进样速率为22.48ml/min,将经油水分离器4分离后得到的环氧大豆油和甲醇同时泵入第二微混合器3中,混合后泵入第二微结构反应器5(302.28ml)中,保持反应停留时间11min,于100℃下进行反应。收集油相产物即得大豆油多元醇。(2)植物油基聚氨酯弹性体的制备在氮气保护下,采用预聚体法制备聚氨酯弹性体,将100g大豆油多元醇与1.5g水、1.0g硅油、2g开孔剂、0.3g催化剂a-33、0.1g催化剂a-1、0.006g催化剂t-12混合,加入4,4`-二苯基甲烷二异氰酸酯100g,在80℃下反应2h后,用二正丁胺法测定游离的nco含量,按扩链系数0.95加入1,4-丁二醇,搅拌混合均匀后浇注100℃的平板钢制模具中,并进行硫化,在90℃烘箱中老化24h,即可制得大豆油基聚氨酯弹性体。(3)植物油基聚氨酯粘合剂的制备取100g大豆油多元醇与4g丁香酚置于密闭容器,氮气置换;升温至130℃,抽真空,氮气鼓泡2h;加入25g异氰酸酯mdi-50,在65℃下反应2h,得到聚氨酯粘合剂,t型剥离强度=4.7n(25mm)-1。实施例4(1)植物油多元醇的制备反应流程图见图1,取200g大豆油(含双键0.99mol)为i组分,取680.18g30%的双氧水(6mol)与281.81g甲酸(6mol)混合,再添加硫酸4.50g(0.045mol)以及edta2.19g(0.005mol)为ii组分,将i和ii组分分别以进样速率1.0ml/min、4.0ml/min同时泵入第一微混合器1中,混合后泵入第一微结构反应器2(35ml)中,保持反应停留时间7min,于常压和60℃下反应,得到的环氧大豆油的环氧值为4.62;取170g甲醇(5mol),设置进样速率为22.43ml/min,将经油水分离器4分离后得到的环氧大豆油和甲醇同时泵入第二微混合器3中,混合后泵入第二微结构反应器5(219.44ml)中,保持反应停留时间11min,于100℃下进行反应。将反应粗产物通入油水分离器除去水相后,收集油相产物即得大豆油多元醇。(2)植物油基聚氨酯弹性体的制备在氮气保护下,采用预聚体法制备聚氨酯弹性体,将100g大豆油多元醇与1.5g水、1.0g硅油、2g开孔剂、0.3g催化剂a-33、0.1g催化剂a-1、0.006g催化剂t-12混合,加入4,4`-二苯基甲烷二异氰酸酯100g,在80℃下反应2h后,用二正丁胺法测定游离的nco含量,按扩链系数0.95加入1,4-丁二醇,搅拌混合均匀后浇注100℃的平板钢制模具中,并进行硫化,在90℃烘箱中老化24h,即可制得大豆油基聚氨酯弹性体。(3)植物油基聚氨酯粘合剂的制备取100g大豆油多元醇与4g丁香酚置于密闭容器,氮气置换;升温至130℃,抽真空,氮气鼓泡2h;加入25g异氰酸酯mdi-50,在65℃下反应2h,得到聚氨酯粘合剂,t型剥离强度=4.4n(25mm)-1。实施例5(1)植物油多元醇的制备反应流程图见图1,取200g大豆油(含双键0.99mol)为i组分,取680.18g30%的双氧水(6mol)与281.81g甲酸(6mol)混合,再添加硫酸5.00g(0.05mol)以及edta2.19g(0.005mol)为ii组分,将i和ii组分分别以进样速率1.0ml/min、4.0ml/min同时泵入第一微混合器1中,混合后泵入第一微结构反应器2(35ml)中,保持反应停留时间7min,于常压和60℃下反应,得到的环氧大豆油的环氧值为4.65;取170g甲醇(5mol),设置进样速率为22.58ml/min,将经油水分离器4分离后得到的环氧大豆油和甲醇同时泵入第二微混合器3中,混合后泵入第二微结构反应器5(303.38ml)中,保持反应停留时间11min,于100℃下进行反应。将反应粗产物通入油水分离器除去水相后,收集油相产物即得大豆油多元醇。(2)植物油基聚氨酯弹性体的制备在氮气保护下,采用预聚体法制备聚氨酯弹性体,将100g大豆油多元醇与1.5g水、1.0g硅油、2g开孔剂、0.3g催化剂a-33、0.1g催化剂a-1、0.006g催化剂t-12混合,加入4,4`-二苯基甲烷二异氰酸酯100g,在80℃下反应2h后,用二正丁胺法测定游离的nco含量,按扩链系数0.95加入1,4-丁二醇,搅拌混合均匀后浇注100℃的平板钢制模具中,并进行硫化,在90℃烘箱中老化24h,即可制得大豆油基聚氨酯弹性体。(3)植物油基聚氨酯粘合剂的制备取100g大豆油多元醇与4g丁香酚置于密闭容器,氮气置换;升温至130℃,抽真空,氮气鼓泡2h;加入25g异氰酸酯mdi-50,在65℃下反应2h,得到聚氨酯粘合剂,t型剥离强度=4.5n(25mm)-1。对比例1(1)植物油多元醇的制备将200g大豆油(含双键0.99mol)、906.9g30%的双氧水(8mol)、375.75g甲酸(8mol)、14.014g硫酸(0.014mol)以及3.50gedta(0.008mol)混合,120℃下搅拌反应5h,得到的环氧大豆油用分液漏斗分出油相,测定其环氧值为4.98;向得到的环氧植物油中加入957g(29.88mol)甲醇,加热至85℃,继续搅拌反应3h,收集油相产物即得大豆油多元醇。(2)植物油基聚氨酯弹性体的制备在氮气保护下,采用预聚体法制备聚氨酯弹性体,将100g大豆油多元醇与1.5g水、1.0g硅油、2g开孔剂、0.3g催化剂a-33、0.1g催化剂a-1、0.006g催化剂t-12混合,加入4,4`-二苯基甲烷二异氰酸酯100g,在80℃下反应2h后,用二正丁胺法测定游离的nco含量,按扩链系数0.95加入1,4-丁二醇,搅拌混合均匀后浇注100℃的平板钢制模具中,并进行硫化,在90℃烘箱中老化24h,即可制得大豆油基聚氨酯弹性体。(3)植物油基聚氨酯粘合剂的制备取100g大豆油多元醇与4g丁香酚置于密闭容器,氮气置换;升温至130℃,抽真空,氮气鼓泡2h;加入25g异氰酸酯mdi-50,在65℃下反应2h,得到聚氨酯粘合剂,t型剥离强度=3.2n(25mm)-1。对比例2(1)植物油多元醇的制备将200g大豆油(含双键0.99mol)、906.9g30%的双氧水(8mol)、375.75g甲酸(8mol)、14.014g硫酸(0.014mol)以及3.50gedta(0.008mol)混合,130℃下搅拌反应5h,得到的环氧大豆油用分液漏斗分出油相,测定其环氧值为5.01;向得到的环氧植物油中加入963g(30.06mol)甲醇,加热至85℃,继续搅拌反应3h,收集油相产物即得大豆油多元醇。(2)植物油基聚氨酯弹性体的制备在氮气保护下,采用预聚体法制备聚氨酯弹性体,将100g大豆油多元醇与1.5g水、1.0g硅油、2g开孔剂、0.3g催化剂a-33、0.1g催化剂a-1、0.006g催化剂t-12混合,加入4,4`-二苯基甲烷二异氰酸酯100g,在80℃下反应2h后,用二正丁胺法测定游离的nco含量,按扩链系数0.95加入1,4-丁二醇,搅拌混合均匀后浇注100℃的平板钢制模具中,并进行硫化,在90℃烘箱中老化24h,即可制得大豆油基聚氨酯弹性体。(3)植物油基聚氨酯粘合剂的制备取100g大豆油多元醇与4g丁香酚置于密闭容器,氮气置换;升温至130℃,抽真空,氮气鼓泡2h;加入25g异氰酸酯mdi-50,在65℃下反应2h,得到聚氨酯粘合剂,t型剥离强度=3.0n(25mm)-1。对比例3(1)植物油多元醇的制备植物油多元醇的制备方法同实施例5,不同的是对比例3仅在第一微结构反应器2进行反应,反应结束后直接经油水分离器分离收集油相产物。取200g大豆油(含双键0.99mol)为i组分,取680.18g30%的双氧水(6mol)与281.81g甲酸(6mol)混合,再添加硫酸5.00g(0.05mol)以及edta2.19g(0.005mol)为ii组分,将i和ii组分分别以进样速率1.0ml/min、4.0ml/min同时泵入第一微混合器1中,混合后泵入第一微结构反应器2(35ml)中,保持反应停留时间7min,于常压和60℃下反应,得到的大豆油的环氧值为4.65,收集油相产物。(2)植物油基聚氨酯弹性体的制备在氮气保护下,采用预聚体法制备聚氨酯弹性体,将100g步骤(1)产物与1.5g水、1.0g硅油、2g开孔剂、0.3g催化剂a-33、0.1g催化剂a-1、0.006g催化剂t-12混合,加入4,4`-二苯基甲烷二异氰酸酯100g,在80℃下反应2h后,用二正丁胺法测定游离的nco含量,按扩链系数0.95加入1,4-丁二醇,搅拌混合均匀后浇注100℃的平板钢制模具中,并进行硫化,在90℃烘箱中老化24h,即可制得大豆油基聚氨酯弹性体。(3)植物油基聚氨酯粘合剂的制备取100g步骤(1)产物与4g丁香酚置于密闭容器,氮气置换;升温至130℃,抽真空,氮气鼓泡2h;加入25g异氰酸酯mdi-50,在65℃下反应2h,得到聚氨酯粘合剂,t型剥离强度=2.8n(25mm)-1。实施例1-5及对比例1-3制备得到的植物油多元醇的性能指标见表1,制备得到的植物油基聚氨酯弹性体性能指标见表2。表1植物油多元醇性能指标性能指标实施例1实施例2实施例3实施例4实施例5对比例1对比例2对比例3羟值(mgkoh/g)13812912713213515215875粘度(mpas/25℃)89375674976376512501292399碘值(g/100g)3839384039252235表2植物油基聚氨酯弹性体性能指标性能指标实施例1实施例2实施例3实施例4实施例5对比例1对比例2对比例3拉伸强度(kpa)11511812011911610210168伸长率(%)120125128127124112115102压缩永久变形参数(%)10991010151618回弹性能(s)891088664撕裂强度(ncm-1)56655442当前第1页12