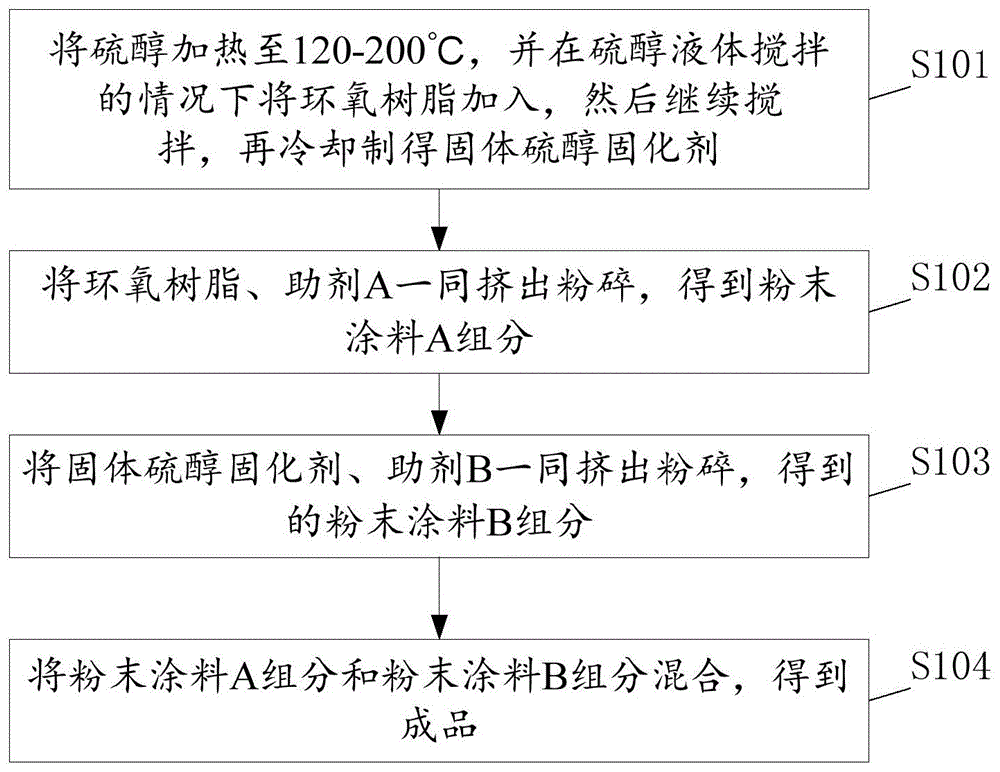
本发明涉及粉末涂料
技术领域:
,特别涉及一种固体硫醇固化剂、粉末涂料及其制备方法。
背景技术:
:粉末涂料是一种新型的不含溶剂的百分之百固体的涂料,不含有voc,是一种环保的涂料。粉末涂料由树脂、颜填料、固化剂及其它助剂,以一定的比例混合,再通过热挤塑和粉碎过筛等工艺制备而成。它们在常温下,贮存稳定,经静电喷涂、摩擦喷涂或流化床浸涂,再加热烘烤熔融固化,使形成平整光亮的永久性涂膜,达到装饰或者防腐蚀的目的。粉末涂料在过去40年中得到了非常迅速的发展,目前在中国市场上每年粉末涂料的销量在100万吨左右,而且以每年10wt%左右的速度在增长。其主要应用领域为建筑铝型材,家用电器,家具以及输油输水管道的防腐。尤其是最进几年,随着国家对环保的要求越来越高,溶剂型涂料的使用收到了很大的限制,粉末涂料越来越受到欢迎。传统的粉末涂料的制作方式为:将聚酯,环氧,颜料,填料和其它助剂混合均匀,放入挤出机挤出从而形成均匀的物质。聚酯和环氧一同挤出,是同时存在于同一个粉末涂料的粒子之中的。现有技术cn109762440a公开了一种低温固化型粉末涂料及其制备方法,其制作方式是:将a组分(包括环氧树脂和固化剂,固化剂可为聚酯树脂)、b组分(包括聚酯树脂和固化促进剂)分别预混合、熔融挤出,在压片冷却并粉碎,然后再将a、b组分在50-80℃下进行搅拌升温,粘结及造粒,最后再经破碎筛分,得到低温固化粉末涂料。现有技术中,选择的聚酯树脂或环氧树脂的固化温度必须高于熔融加工温度,由于熔融加工温度一定,导致现有技术无法生产得到超低温粉末涂料,目前采用这种生产粉末涂料方式的低温粉末涂料的固化温度最低在130℃。这是因为,即使使用最好冷却效果的挤出机,挤出机的出料口的温度一般会达到100℃以上,这样,环氧树脂和聚酯树脂在挤出的过程中已经开始发生交联反应。对比文件虽然将a组分(包括环氧树脂)、b组分(包括聚酯树脂)分别挤出,但是,a组分中包含固化剂,该固化剂为聚酯树脂或氨基固化剂,这样a组分在挤出时,环氧树脂和聚酯树脂在挤出的过程中已经开始发生交联反应。而在b组分中,除了聚酯树脂,还含有固化促进剂(相当于本申请的催化剂),聚酯树脂与固化促进剂一同挤出,无法生产出超低温90-110℃的粉末涂料。技术实现要素:本发明所要解决的技术问题在于,提供一种固体硫醇固化剂以及采用其的粉末涂料,可以实现低于100℃的超低温固化,且固化后可以获得性能优异的涂膜。本发明所要解决的技术问题在于,提供一种固体硫醇固化剂以及采用其的粉末涂料,所述粉末涂料可以大幅提高生产效率。本发明所要解决的技术问题在于,提供一种粉末涂料的制备方法,方法简单,可实施性强,成本较低,能制得固化温度低于100℃的超低温粉末涂料。为达到上述技术效果,本发明提供了一种固体硫醇固化剂,包括硫醇和含有环氧基团的固体物质,其中硫醇的活泼氢当量和含有环氧基团的固体物质的环氧当量之比为(2-4):1;所述固体硫醇固化剂是通过将硫醇加热至120-200℃,并在硫醇液体搅拌的情况下将含有环氧基团的固体物质加入,然后继续搅拌,再冷却制得。作为上述方案的改进,所述硫醇为多元硫醇、聚硫醇中的一种或多种;所述含有环氧基团的固体物质为环氧当量为650-5500的环氧树脂、异氰尿酸三缩水甘油酯中的一种或多种。作为上述方案的改进,所述硫醇为烷烃多元硫醇、聚酯型聚硫醇、聚醚型聚硫醇、改性硫醇中的一种或多种。作为上述方案的改进,所述硫醇为四(3-巯基丙酸)季戊四醇酯、山梨醇多巯基乙酸酯、季戊四醇四巯基乙酸酯、肌醇六(巯基丙酸酯)、四(3-巯基丙酸)季戊四醇酯、3-巯基丙酸-[2,4,6-三氧代-1,3,5-三嗪-1,3,5(2h,4h,6h)-次基]三-2,1-乙二醇酯中的一种或多种。相应的,本发明还提供一种粉末涂料,包括1-99wt%的粉末涂料a组分和1-99wt%的粉末涂料b组分;所述粉末涂料a组分是由含有环氧基团的固体物质、助剂a一同挤出粉碎,或者含有环氧基团的固体物质直接粉末破碎得到的粉末涂料;所述粉末涂料b组分是由固体硫醇固化剂、助剂b一同挤出粉碎得到的粉末涂料,其中,所述固体硫醇固化剂为硫醇和含有环氧基团的固体物质反应的产物,其中硫醇的活泼氢当量和含有环氧基团的固体物质的环氧当量之比为(2-4):1。作为上述方案的改进,所述粉末涂料组分a是由30-100wt%的含有环氧基团的固体物质和0-70wt%的助剂a一同挤出粉碎得到的粒径为5-50μm的粉末涂料;其中,所述粉末涂料组分a选用的含有环氧基团的固体物质为环氧当量为200-1500的环氧树脂、异氰尿酸三缩水甘油酯中的一种或多种;所述助剂a包括0-5wt%流平剂、0-2wt%脱气剂、0-40wt%颜料、0-20wt%填料。作为上述方案的改进,所述粉末涂料组分b是由30-80wt%的固体硫醇固化剂和20-70wt%的助剂b一同挤出粉碎得到的粒径为5-50μm的粉末涂料;其中,所述固体硫醇固化剂是通过将硫醇加热至120-200℃,并在硫醇液体搅拌的情况下将含有环氧基团的固体物质加入,然后继续搅拌,再冷却制得。作为上述方案的改进,所述硫醇为多元硫醇、聚硫醇中一种或多种;所述粉末涂料组分b选用的含有环氧基团的固体物质为环氧当量为650-5500的环氧树脂、环氧丙烯酸树脂,异氰尿酸三缩水甘油酯中一种或多种。作为上述方案的改进,所述硫醇为烷烃多元硫醇、聚酯型聚硫醇、聚醚型聚硫醇、改性硫醇中的一种或多种。作为上述方案的改进,所述硫醇为四(3-巯基丙酸)季戊四醇酯、山梨醇多巯基乙酸酯、季戊四醇四巯基乙酸酯、肌醇六(巯基丙酸酯)、四(3-巯基丙酸)季戊四醇酯、3-巯基丙酸-[2,4,6-三氧代-1,3,5-三嗪-1,3,5(2h,4h,6h)-次基]三-2,1-乙二醇酯中的一种或多种。作为上述方案的改进,所述助剂b包括0-3wt%的流平剂,0-2wt%的脱气剂,0-40wt%的颜料,0-20wt%的填料,0-5wt%助剂。相应的,本发明还公开一种粉末涂料的制备方法,包括:将硫醇加热至120-200℃,并在硫醇液体搅拌的情况下将含有环氧基团的固体物质加入,所述硫醇的活泼氢当量和含有环氧基团的固体物质的环氧当量之比为(2-4):1,然后继续搅拌,再冷却制得固体硫醇固化剂;将含有环氧基团的固体物质、助剂a一同挤出粉碎,或者将含有环氧基团的固体物质直接粉末破碎,得到粉末涂料a组分;将固体硫醇固化剂、助剂b一同挤出粉碎,得到粉末涂料b组分;将粉末涂料a组分和粉末涂料b组分混合,得到成品。实施本发明具有如下有益效果:(一)本发明提供一种固体硫醇固化剂,包括当量比为(2-4):1的硫醇和含有环氧基团的固体物质,且其通过将硫醇加热至120-200℃,并在硫醇液体搅拌的情况下将含有环氧基团的固体物质加入,然后继续搅拌,再冷却制得。所述固体硫醇固化剂能制得低于100℃的超低温固化的超低温粉末涂料,且所述超低温粉末涂料固化后可以获得性能优异的涂膜。(二)本发明提供一种粉末涂料,包括粉末涂料a组分和粉末涂料b组分,其中,粉末涂料a组分是由含有环氧基团的固体物质、助剂a一同挤出粉碎,或者含有环氧基团的固体物质直接粉末破碎得到的粉末涂料,粉末涂料b组分是由固体硫醇固化剂、助剂b一同挤出粉碎得到的粉末涂料。所述粉末涂料可以实现低于100℃的超低温固化,且固化后可以获得性能优异的涂膜。而且,所述粉末涂料在固化的过程中,可以只需把粉末涂料融化流平,可以使剩下的交联反应在后期进行,大幅提高了生产效率,可以避免因为需要固化而对底材进行长时间的加热而对底材的各种性能产生破坏,适用于热敏性底材。(三)本发明提供一种制备上述粉末涂料的方法,先制备粉末涂料a组分,再将固体硫醇固化剂、助剂b制成粉末涂料b组分,最后只需要将粉末涂料a组分和粉末涂料b组分混合,即可得到成品。上述制备方法工艺简单,可控性强,适合大规模生产。因此,本发明固体硫醇固化剂及其制得的粉末涂料,可以实现低于100℃的超低温固化,可以应用到中密度纤维板(mdf)、塑料等热敏性底材上面,装饰效果强,并不会对热敏性底材的性能造成不良影响。附图说明图1是本发明粉末涂料制备方法的流程图。具体实施方式为使本发明的目的、技术方案和优点更加清楚,下面将对本发明作进一步地详细描述。本发明提供了一种固体硫醇固化剂,包括硫醇和含有环氧基团的固体物质,其中硫醇的活泼氢当量和含有环氧基团的固体物质的环氧当量之比为(2-4):1。需要说明的是,环氧当量是指含有1mol环氧基的环氧树脂的质量。活泼氢当量是指含有1mol活泼氢的硫醇的质量。有机化学中,将包含巯基官能团(-sh)的一类非芳香化合物称为硫醇。从结构上来说,可以看成普通醇中的氧被硫替换之后形成的。除甲硫醇在室温下为气体外,其他硫醇均为液体或固体。巯基是硫醇化学性质的主要体现。其中s-h键涉及硫较大的3s/3p组成的杂化轨道与氢较小的1s轨道成键,所以s-h键较弱,硫醇具有酸性。-sh中的活泼氢可以和环氧基团发生亲和反应,因此可以作为环氧的固化剂,这个反应可以在室温温度下进行。所述硫醇为多元硫醇、聚硫醇中的一种或多种。优选的,所述硫醇为烷烃多元硫醇、聚酯型聚硫醇、聚醚型聚硫醇、改性硫醇中的一种或多种,包括但不限于四(3-巯基丙酸)季戊四醇酯、山梨醇多巯基乙酸酯、季戊四醇四巯基乙酸酯、肌醇六(巯基丙酸酯)、四(3-巯基丙酸)季戊四醇酯、3-巯基丙酸-[2,4,6-三氧代-1,3,5-三嗪-1,3,5(2h,4h,6h)-次基]三-2,1-乙二醇酯中的一种或多种。更佳的,所述硫醇为四(3-巯基丙酸)季戊四醇酯或山梨醇多巯基乙酸酯。所述硫醇具有和环氧基团在室温下发生反应的特点,因此,在本发明中可以起到降低反应温度的作用。所述含有环氧基团的固体物质为环氧当量为650-5500的环氧树脂、异氰尿酸三缩水甘油酯中的一种或多种。所述含有环氧基团的固体物质具有软化点高的特点,如南亚公司生产的neps-907,其软化点为120-130℃。所述含有环氧基团的固体物质与液体的硫醇反应之后,其产物的软化点可以达到60℃。如果采用软化点太低的树脂,则产物的软化点过低,会发生储存稳定性的问题。所述硫醇的活泼氢当量和含有环氧基团的固体物质的环氧当量之比为(2-4):1,这是为了将硫醇中的一部分活泼氢反应掉,将液体硫醇转化成含有活泼氢的固体硫醇,可以使其将来和环氧基团继续反应。优选的,所述硫醇的活泼氢当量和含有环氧基团的固体物质的环氧当量之比为(2-3):1。更佳的,所述硫醇的活泼氢当量和含有环氧基团的固体物质的环氧当量之比为2:1。进一步,所述固体硫醇固化剂是通过将硫醇加热至120-200℃,并在硫醇液体搅拌的情况下将含有环氧基团的固体物质加入,所加入的含有环氧基团的固体物质需要事先粉碎成粒径10-100μm的粉末,这样可以使含有环氧基团的固体物质迅速熔融并与硫醇发生反应,不至于出现局部焦化。然后继续搅拌,再冷却制得。所述固体硫醇固化剂需要将硫醇加热至120-200℃,当硫醇的温度超过120℃,可以使加入的环氧粉末树脂能够迅速的熔融并与硫醇发生反应。本发明将聚硫醇或者多元硫醇,与软化点较高的环氧树脂反应,让一部分的硫醇先进行反应,而留下一部分的硫醇,作为固化剂与粉末涂料的环氧树脂的反应基团。所述固体硫醇固化剂能制得超低温粉末涂料,所述超低温粉末涂料可以实现低于100℃的超低温固化,且固化后可以获得性能优异的涂膜。相应的,本发明还提供一种粉末涂料,包括1-99wt%的粉末涂料a组分和1-99wt%的粉末涂料b组分,其由粉末涂料a组分和粉末涂料b组分直接混合得到。所述粉末涂料a组分的粒径优选为5-50μm,优选为10-30μm。所述粉末涂料b组分的粒径优选为5-50μm,优选为10-30μm。具体的,所述粉末涂料a组分是由含有环氧基团的固体物质、助剂a一同挤出粉碎,或者含有环氧基团的固体物质直接粉末破碎得到的粉末涂料。优选的,所述粉末涂料组分a是由30-100wt%的含有环氧基团的固体物质和0-70wt%的助剂a一同挤出粉碎得到的粒径为5-50μm的粉末涂料。或者所述粉末涂料组分a是由含有环氧基团的固体物质直接粉末破碎制得。其中,所述粉末涂料组分a选用的含有环氧基团的固体物质为环氧当量为200-1500的环氧树脂、异氰尿酸三缩水甘油酯中的一种或多种。粉末涂料组分a选用的含有环氧基团的固体物质具有软化点低的特点,在熔融的时候,容易软化和流平,形成流平好的表面。同时软化点低,粘度低,分子运动快,容易和粉末涂料组分b的基团发生反应。另外,由于本发明主要是用于mdf等热敏性基材,因此,较低的反应温度对底材的破坏性小。粉末涂料a组分的环氧树脂与粉末涂料b组分的环氧树脂的选用原则不同,这是因为,a组分是需要直接做成粉末涂料,后期与b组分反应,是最终的涂膜,这就要求粉末涂料的粘度和软化点越低越好。而b组分的环氧需要首先和液体的硫醇进行反应,由于和液体硫醇反应,需要得到的产物为固体,就需要环氧的软化点和粘度越高越好,这样才能生成固体产物。如果粘度和软化点过低的话,无法形成固体产物。需要说明的是,粉末涂料a组分与粉末涂料b组分选用的含有环氧基团的固体物质,二者环氧当量不同,软化点也不同,本领域技术人员根据环氧当量和软化点,选择不同厂家不同型号的环氧树脂或相关物质即可。所述助剂a包括0-5wt%流平剂、0-2wt%脱气剂、0-40wt%颜料、0-20wt%填料,但不限于此。所述粉末涂料b组分是由固体硫醇固化剂、助剂b一同挤出粉碎得到的粉末涂料,优选的,所述粉末涂料组分b是由30-80wt%的固体硫醇固化剂和20-70wt%的助剂b一同挤出粉碎得到的粒径为5-50μm的粉末涂料。有机化学中,将包含巯基官能团(-sh)的一类非芳香化合物称为硫醇。从结构上来说,可以看成普通醇中的氧被硫替换之后形成的。除甲硫醇在室温下为气体外,其他硫醇均为液体或固体。巯基是硫醇化学性质的主要体现。其中s-h键涉及硫较大的3s/3p组成的杂化轨道与氢较小的1s轨道成键,所以s-h键较弱,硫醇具有酸性。-sh中的活泼氢可以和环氧基团发生亲和反应,因此可以作为环氧的固化剂,这个反应可以在室温温度下进行。所述硫醇为多元硫醇、聚硫醇中的一种或多种。优选的,所述硫醇为烷烃多元硫醇、聚酯型聚硫醇、聚醚型聚硫醇、改性硫醇中的一种或多种,包括但不限于四(3-巯基丙酸)季戊四醇酯、山梨醇多巯基乙酸酯、季戊四醇四巯基乙酸酯、肌醇六(巯基丙酸酯)、四(3-巯基丙酸)季戊四醇酯、3-巯基丙酸-[2,4,6-三氧代-1,3,5-三嗪-1,3,5(2h,4h,6h)-次基]三-2,1-乙二醇酯中的一种或多种。更佳的,所述硫醇为四(3-巯基丙酸)季戊四醇酯或山梨醇多巯基乙酸酯。所述硫醇具有和环氧基团在室温下发生反应的特点,因此,在本发明中可以起到降低反应温度的作用。所述含有环氧基团的固体物质为环氧当量为650-5500的环氧树脂、异氰尿酸三缩水甘油酯中的一种或多种。所述含有环氧基团的固体物质具有软化点高的特点,如南亚公司生产的neps-907,其软化点为120-130℃。所述含有环氧基团的固体物质与液体的硫醇反应之后,其产物的软化点可以达到60℃。如果采用软化点太低的树脂,则产物的软化点过低,会发生储存稳定性的问题。所述硫醇的活泼氢当量和含有环氧基团的固体物质的环氧当量之比为(2-4):1,这是为了将硫醇中的一部分活泼氢反应掉,将液体硫醇转化成含有活泼氢的固体硫醇,可以使其将来和环氧基团继续反应。优选的,所述硫醇的活泼氢当量和含有环氧基团的固体物质的环氧当量之比为(2-3):1。更佳的,所述硫醇的活泼氢当量和含有环氧基团的固体物质的环氧当量之比为2:1。进一步,所述固体硫醇固化剂是通过将硫醇加热至120-200℃,并在硫醇液体搅拌的情况下将含有环氧基团的固体物质加入,所加入的含有环氧基团的固体物质需要事先粉碎成粒径10-100μm的粉末,这样可以使含有环氧基团的固体物质迅速熔融并与硫醇发生反应,不至于出现局部焦化。然后继续搅拌,再冷却制得。所述固体硫醇固化剂需要将硫醇加热至120-200℃,当硫醇的温度超过120℃,可以使加入的环氧粉末树脂能够迅速的熔融并与硫醇发生反应。本发明将聚硫醇或者多元硫醇,与软化点较高的环氧树脂反应,让一部分的硫醇先进行反应,而留下一部分的硫醇,作为固化剂与粉末涂料的环氧树脂的反应基团。所述固体硫醇固化剂能制得超低温粉末涂料,所述超低温粉末涂料可以实现低于100℃的超低温固化,且固化后可以获得性能优异的涂膜。所述助剂b包括0-3wt%的流平剂,0-2wt%的脱气剂,0-40wt%的颜料,0-20wt%的填料,0-5wt%助剂,但不限于此。在上述助剂a和助剂b中,流平剂能促使粉末涂料在固化成膜过程中形成一个平整、光滑、均匀的涂膜,提高其流平性和均匀性,减少产生凹陷,斑点和斑痕的可能性,增加覆盖性,使成膜均匀、自然。脱气剂能消除粉末涂料在固化成膜中形成的气泡,保证粉末涂料在固化成膜过程中形成一个平整、光滑、均匀的涂膜。填料,是具有一定刚度、强度和遮盖力的无机化合物,可以提高粉末涂层的刚度和强度,且能节约配方成本。优选的,所述填料为硫酸钡、碳酸钙、滑石粉、高岭土、硅微粉、云母粉中的一种或多种。硫酸钡,化学性质稳定,粒径细分散好,对光泽的影响小,制得的粉末涂层的光泽流平都较为理想;碳酸钙的比表面积大,吸油量很大,一般是用在纹理粉末中;滑石粉,为片状结构,有一定的触变性,对粉末涂层的熔融流动性有较大的影响,价格便宜,但吸油量大,一般常用于纹理粉末中,同时提高涂层的耐划伤性能;云母粉,是一种复杂的硅酸盐类组成可以提高涂层的硬度和耐刮伤性能。硅微粉,云母粉等填料可以提供良好的硬度和耐划伤性能。颜料,可以赋予涂层绚丽多彩的色泽,改进涂料的机械化学性能,降低涂料的成本。所述颜料可以选用着色颜料、金属颜料、功能颜料、体质颜料中的一种或多种。其中,体质颜料的其他性质的变化范围很广,如相对密度、容量值、颗粒形状、颗粒大小、粒径分布、吸油量、化学活性等,这些体质颜料在构成粒子的大小形状上各不相同,使得其在高光泽和半光涂料中呈现出非常小的遮盖力,具有降低配方成本及控制光泽等作用。相应的,如图1所示,本发明还公开一种粉末涂料的制备方法,包括:s101、将硫醇加热至120-200℃,并在硫醇液体搅拌的情况下将含有环氧基团的固体物质加入,所述硫醇的活泼氢当量和含有环氧基团的固体物质的环氧当量之比为(2-4):1,然后继续搅拌,再冷却制得固体硫醇固化剂;s102、将含有环氧基团的固体物质、助剂a一同挤出粉碎,或者将含有环氧基团的固体物质直接粉末破碎,得到粉末涂料a组分;s103、将固体硫醇固化剂、助剂b一同挤出粉碎,得到的粉末涂料b组分;s104、将粉末涂料a组分和粉末涂料b组分混合,得到成品。现有粉末涂料的制作过程中,固体的环氧树脂和固化剂会通过挤出机挤出,而挤出的温度一般在120-140℃,而环氧和硫醇则可以在室温下发生反应,如果通过挤出机挤出,在挤出的过程中则会发生交联反应,无法制得超低温粉末涂料。为此,本发明分开制备粉末涂料a组分和粉末涂料b组分,具体是先将含有环氧基团的固体物质、助剂a一同挤出粉碎,或者将含有环氧基团的固体物质直接粉末破碎,制成粉末涂料a组分。此步骤将软化点较低的环氧树脂与助剂预先挤出,形成粉末涂料。再将固体硫醇固化剂、助剂b制成粉末涂料b组分,此步骤将聚硫醇或者多元硫醇,与软化点较高的含有环氧基团的固体物质反应,让一部分的硫醇先进行反应,而留下一部分的硫醇,作为固化剂与粉末涂料的含有环氧基团的固体物质的反应基团。这里将硫醇和高软化点的环氧的反应为关键点。尤其是含有环氧基团的固体物质的选择,软化点需要尽可能的高,制备出来的固体硫醇才能不至于是液体或者软化点很低的物质,造成无法制成粉末涂料,或者制成的粉末涂料玻璃化温度过低,储存稳定性差等问题。最后只需要将粉末涂料a组分和粉末涂料b组分混合,即可得到成品。上述制备方法工艺简单,可控性强,适合大规模生产。由于环氧和硫醇的反应可以在室温下反应,但是在粉末涂料中,需要熔融后,才能形成均匀的涂膜,所以,本发明选用软化点低于80℃的环氧树脂,用这种方法制成的超低温固化粉末涂料,才能实现低于100℃的超低温固化。另外,由于环氧和硫醇的反应可以在室温下进行,所以,在涂料固化的过程中,只需把粉末涂料融化流平,可以使剩下的交联反应在后期进行,这样,生产的效率可以大幅的提高。进一步,采用本发明粉末涂料,在生产中,可以避免因为需要固化而对底材进行长时间的加热,进而对底材的各种性能产生破坏。因此,这种粉末涂料可以应用到中密度纤维板(mdf),塑料等热敏性底材上面。从而实现超低温,低于100℃固化。需要说明的是,粉末涂料的制备方法中,硫醇、环氧树脂、粉末涂料a组分和粉末涂料b组分等技术细节,同上所述,在此不再赘述。下面以具体实施例进一步阐述本发明实施例1(一)粉末涂料a组分的制备:将环氧当量在550-600之间的环氧树脂、流平剂、安息香、钛白粉按如下比例称量:将混合好的物料放入挤出机中,设定温度为120℃。将挤出的物料放入咖啡磨中打碎,过筛,控制粒径为15μm左右。(二)粉末涂料b组分的制备:1、固体硫醇固化剂的制备:准备24.4g四(3-巯基丙酸)季戊四醇酯与150g环氧当量为1500-2000的环氧树脂(凯茵化工yd017)。即,四(3-巯基丙酸)季戊四醇酯的活泼氢当量与环氧树脂的环氧当量之比为2:1。将环氧树脂粉碎成粉末;平均粒径在30-50μm。将四(3-巯基丙酸)季戊四醇酯放入三口烧瓶中,加热到180℃,在搅拌的情况下将环氧树脂粉末逐步加入到烧瓶中,持续10分钟之后,将瓶中产物放出,冷却打碎,得到固体硫醇固化剂。2、固体硫醇固化剂、流平剂、安息香、钛白粉按如下比例称量:将混合好的物料放入挤出机中,设定温度为120℃。将挤出的物料放入咖啡磨中打碎,过筛,控制粒径为15μm左右。3、将30g粉末涂料a组分和70g粉末涂料b组分混合,得到成品。实施例2(一)粉末涂料a组分的制备:将环氧当量在550-600之间的环氧树脂、流平剂、安息香、钛白粉按如下比例称量:将混合好的物料放入挤出机中,设定温度为120℃。将挤出的物料放入咖啡磨中打碎,过筛,控制粒径为20μm左右。(二)粉末涂料b组分的制备:1、固体硫醇固化剂的制备:准备50g日本旭电化工的eh-316硫醇,sh当量131-137g,黏度(25℃)为500mpa·s以及300g环氧当量为3000的环氧树脂(国都生产的kd-9010)。即,eh-316硫醇的活泼氢当量与环氧树脂的环氧当量之比为4:1。将环氧树脂粉碎成粉末;将eh-316硫醇放入三口烧瓶中,加热到200℃,在搅拌的情况下将环氧树脂粉末逐步加入到烧瓶中,持续10分钟之后,将瓶中产物放出,冷却打碎,得到固体硫醇固化剂。2、固体硫醇固化剂、流平剂、安息香、钛白粉按如下比例称量:将混合好的物料放入挤出机中,设定温度为120℃。将挤出的物料放入咖啡磨中打碎,过筛,控制粒径为15μm左右。3、将100g粉末涂料a组分和20g粉末涂料b组分混合,得到成品。实施例3(一)粉末涂料a组分的制备:将异氰尿酸三缩水甘油酯tgic粉碎至粒径3-15μm。(二)粉末涂料b组分的制备:1、固体硫醇固化剂的制备:准备27g日本旭电化工的eh-316硫醇,sh当量131-137g,黏度(25℃)为500mpa·s以及300g环氧当量为3000的环氧树脂(国都生产的kd-9010)。即,eh-316硫醇的活泼氢当量与环氧树脂的环氧当量之比为2:1。将环氧树脂粉碎成粉末;将eh-316硫醇放入三口烧瓶中,加热到200℃,在搅拌的情况下将环氧树脂粉末逐步加入到烧瓶中,持续10分钟之后,将瓶中产物放出,冷却打碎,得到固体硫醇固化剂。2、固体硫醇固化剂、流平剂、安息香、钛白粉按如下比例称量:将混合好的物料放入挤出机中,设定温度为120℃。将挤出的物料放入咖啡磨中打碎,过筛,控制粒径为15μm左右。3、将22g粉末涂料a组分和100g粉末涂料b组分混合,得到成品。对实施例1-3得到的粉末涂料进行技术检测,结果如下:(1)将实施例1-3粉末涂料放入设定温度为100℃、90℃、80℃的胶化仪中,测量其焦化时间:项目实施例1实施例2实施例3焦化时间(100℃)220秒131秒173秒焦化时间(90℃)308秒236秒272秒焦化时间(80℃)437秒365秒391秒由上可知,本发明固化反应可以在100℃进行,而且反应速度很快。而且,本发明还可以在低于100℃(例如90℃、80℃)进行,反应速度也较快。(2)将实施例1-3的粉末涂料用静电抢喷涂于铝板之上,放入烘箱,100℃烘烤10分钟,取出铝板,冷却,铝板表面形成粉末涂层。对其形成的粉末涂层进行技术检测,结果如下:由上可知,本发明粉末涂料在金属板上形成的粉末涂层,用丙酮擦拭50次,没有露底现象,证明反应固化完全。而且,用光泽度仪测试其光泽为67%~78%,证明本发明粉末涂料在金属板可以取得平面效果。另外,上述涂料的附着力好,铅笔硬度高,使用性能良好。(3)将实施例1-3的粉末涂料用静电枪喷涂于中密度纤维板上,放入红外固化炉中,红外炉的设定温度为100℃,3分钟之后,将板取出,中密度纤维板表面形成粉末涂层。对其形成的粉末涂层进行技术检测,结果如下:项目实施例1实施例2实施例3用丙酮擦拭50次没有露底现象没有露底现象没有露底现象附着力0级0级0级铅笔硬度hbhbhb光泽71%75%81%由上可知,本发明粉末涂料在中密度纤维板等热敏性底材上形成的粉末涂层,用丙酮擦拭50次,没有露底现象,证明反应固化完全。而且,用光泽度仪测试其光泽为78-81,证明在中密度纤维板上可以取得平面效果。另外,上述涂料的附着力好,铅笔硬度高,使用性能良好。需要说明的是,所述光泽是在60°入射角测量涂层表面的光泽度。附着力的检测依据是gb9286,0-5表示附着力由好到坏,具体分级的标准描述为:0-切割边缘完全平滑,无一格脱落。铅笔硬度依据astm3363。以上所述是本发明的优选实施方式,应当指出,对于本
技术领域:
的普通技术人员来说,在不脱离本发明原理的前提下,还可以做出若干改进和润饰,这些改进和润饰也视为本发明的保护范围。当前第1页12