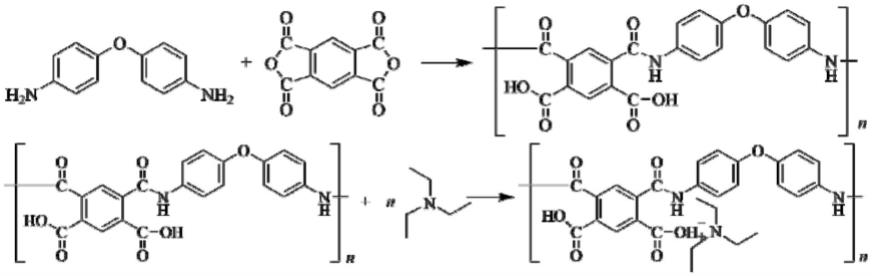
1.本发明涉及纤维材料及其制备方法,更具体地,涉及一种高强度聚酰亚胺气凝胶纤维及其制备方法。
背景技术:2.人类使用纤维材料的历史悠久,从棉、麻、丝绸、羊毛等的天然纤维到尼龙、腈纶、特氟龙等的合成纤维一直以来都是人类重要的隔热材料。合成纤维材料虽然诞生比较晚,但是其高性能、高强度、高精密度等特性是天然纤维材料所不具备的,然而,合成纤维材料在保温性能方面却没有更多优势,其原因在于使用传统方法纺织的合成纤维不具有三维网络结构,孔隙率和比表面积低,隔热效果与天然纤维相比没有显著的提高。
3.纤维的保温性能主要取决于纤维材料的密度、孔隙率、比表面积和材料中空隙的数量和大小。纤维材料的密度越小、孔隙率越大、比表面积越大、材料中空气含量越高,则保温性能越好。气凝胶由于其独特的多孔网络结构,被认为是新一代高效隔热材料,因此可以作为新一代合成纤维的备选材料。
4.聚酰亚胺材料具有无机材料的耐高温和耐腐蚀性能,同时又具有有机材料的良好力学性能,近年逐渐受到关注。如何将气凝胶的三维网络结构引入到聚酰亚胺纤维中,合成具有高比表面积和孔隙率,同时又能有良好的强度和弹性,以满足纺织化需求的聚酰亚胺气凝胶纤维,是保温领域的重要研究方向。实现高强度气凝胶纤维的简单连续化制备,代表着人类在合成纤维保温领域取得质的飞跃。
5.传统聚酰亚胺纤维湿法纺丝中凝固浴通常为有机溶剂和水的混合液,目的是减缓纤维凝固速度,避免快速的溶剂交换导致纤维表面形成致密膜,但较慢的凝固速度意味着更长的凝固时间和凝固浴尺寸,同时需要大量的有机溶剂,成本高且后处理工序复杂,因此如何以纯水作凝固浴是面临的一个难题。传统聚酰亚胺纤维的纺丝液浓度较高,一般为15%-18%的质量分数,加上其致密的结构,导致密度较大,但低浓度的纺丝液粘度低,可纺性差,如何制备低浓度、高粘度、良好可纺性且稳定的纺丝液是另一项挑战。
技术实现要素:6.鉴于上述内容,本发明提供一种高强度聚酰亚胺气凝胶纤维及其制备方法。
7.本发明包括如下两个方面:
8.第一方面,一种高强度聚酰亚胺气凝胶纤维,其特征在于具有由聚酰亚胺纳米纤维交联形成的三维网络结构,所述聚酰亚胺气凝胶纤维的拉伸强度为20-100mpa,弹性模量为800-1400mpa,比表面积为100-300m2/g,线密度为15-25tex,热导率为0.02-0.07w
·
m-1
·
k-1
,并且具有良好的可纺性。
9.第二方面,本发明提供一种聚酰亚胺气凝胶纤维的制备方法,其特征在于,包括如下步骤:
10.步骤s1,制备聚酰胺酸溶液;
11.步骤s2,对所述聚酰胺酸溶液进行纺丝前处理,得到聚酰胺酸盐纺丝液;
12.步骤s3,将所述聚酰胺酸盐纺丝液进行纺丝,得到聚酰胺酸盐水凝胶纤维;
13.步骤s4,将所述聚酰胺酸盐水凝胶纤维进行溶液置换,得到聚酰胺酸盐有机凝胶纤维,然后进行溶液中化学亚胺化,得到聚酰亚胺有机凝胶纤维;以及
14.步骤s5,将所述聚酰亚胺有机凝胶纤维进行溶剂置换,然后进行冷冻干燥或超临界干燥,得到所述聚酰亚胺气凝胶纤维。
15.本发明至少具有如下有益效果之一:
16.本发明提供的高强度聚酰亚胺气凝胶纤维具有典型的三维网络结构,具有较低的热导率和线密度,具有较高的强度和良好的韧性,具有良好的可纺性,可以应用于纺织、特种服饰和工业保温等领域;
17.本发明提供的高强度聚酰亚胺气凝胶纤维的制备方法采用的原料广泛易得,制备工艺简单,反应条件温和,反应过程可控,工艺流程连续,前后处理步骤少,可实现大规模生产。
附图说明
18.图1是本发明实施例1的聚酰亚胺气凝胶纤维的断面形貌sem图(左)及其局部放大sem图(右)。
19.图2展示的是本发明实施例2的聚酰亚胺气凝胶纤维吊起100g的砝码的示意图(左)以及在其打结后仍显示有一定的强度(右)。
具体实施方式
20.为使本发明实施例的目的、技术方案和优点更加清楚,下面将对本发明技术方案进行清楚、完整地描述。显然,所描述的实施方案仅仅是本发明的一部分,而不是全部的实施方案。基于所描述的本发明的实施方案,本领域普通技术人员所获得的所有其他实施方案,都属于本发明保护的范围。
21.除非另作定义,本发明中使用的技术术语或者科学术语应当为本发明所属领域的普通技术人员所理解的通常意义。
22.为解决上述技术问题,本发明采用以下技术方案:
23.根据本发明第一方面所述的高强度聚酰亚胺气凝胶纤维,其特征在于具有由聚酰亚胺纳米纤维交联形成的三维网络结构,所述聚酰亚胺气凝胶纤维的拉伸强度为20-100mpa,弹性模量为800-1400mpa,比表面积为100-300m2/g,线密度为15-25tex,热导率为0.02-0.07w
·
m-1
·
k-1
,并且具有良好的可纺性。
24.根据本发明第二方面所述的聚酰亚胺气凝胶纤维的制备方法,其特征在于,包括如下步骤:
25.步骤s1,制备聚酰胺酸溶液;
26.步骤s2,对所述聚酰胺酸溶液进行纺丝前处理,得到聚酰胺酸盐纺丝液;
27.步骤s3,将所述聚酰胺酸盐纺丝液进行纺丝,得到聚酰胺酸盐水凝胶纤维;
28.步骤s4,将所述聚酰胺酸盐水凝胶纤维进行溶液置换,得到聚酰胺酸盐有机凝胶纤维,然后进行溶液中化学亚胺化,得到聚酰亚胺有机凝胶纤维;
29.步骤s5,将所述聚酰亚胺有机凝胶纤维进行溶剂置换,然后进行冷冻干燥或超临界干燥,得到所述聚酰亚胺气凝胶纤维。
30.进一步地,所述步骤s1中,所述聚酰胺酸溶液由二酐单体与二胺单体在有机溶剂中聚合形成;
31.其中,所述二酐单体为选自均四甲酸二酐、联苯四羧酸二酐、二苯醚四羧酸二酐、苯酮四甲酸酐、双酚a型二酐、氧双邻苯二甲酸酐、联苯四甲酸二酐、均苯四甲酸酐中的一种或多种;
32.所述二胺单体为选自4,4'-二氨基二苯醚、对苯二胺、二异氰酸二苯甲烷酯、二异氰酸甲苯酯、4,4'-二氨基苯酰替苯胺、4,4
’‑
二氨基-2,2
’‑
二甲基-1,1
’‑
联苯、2,2'-双[4-(4-氨基苯氧基苯基)]丙烷、双(4-氨基苯氧基)苯中的一种或多种;
[0033]
所述有机溶剂为选自n-甲基吡咯烷酮、二甲基亚砜、n,n-二甲基甲酰胺和二甲基乙酰胺中的一种。
[0034]
进一步地,所述步骤s2中的纺丝前处理包括:
[0035]
步骤s21,将三乙胺加入所述聚酰胺酸溶液中来调整纺丝液的水溶性;
[0036]
步骤s22,将交联剂加入经步骤s21后的溶液中以提高纺丝液的可纺性;
[0037]
步骤s23,将经步骤s22后的溶液进行真空脱泡处理,得到聚酰胺酸盐纺丝液;
[0038]
所述交联剂为选自1,3,5-三(4-氨基苯氧基)苯、双[3-(三甲氧基甲硅烷基)丙基]胺、n1,n3,n5三(4-氨基苯基)苯-1,3,5-三甲酰胺、三(4-氨基苯基)胺、2,4,6-三(4-氨基苯氧基)-1,3,5-三嗪、1,3,5-三(4-氨苯基)苯、三聚氰胺及其衍生物中的一种或多种。
[0039]
更进一步地,所述步骤s2中,所述聚酰胺酸盐纺丝液中,聚酰胺酸盐的质量浓度为5-15wt%,所述二酐单体、二胺单体和交联剂摩尔比为(n+1)/n/m,其中n值为10~60,m值为0.5~1,所述二酐单体和三乙胺的摩尔比为0.8:1.2,优选为1:1。
[0040]
例如,在一种实施方案中,在步骤s1和s2中,所述聚酰胺酸溶液由均苯四甲酸酐,4,4-二氨基二苯醚,三乙胺和1,3,5-三(4-氨基苯氧基)苯反应得到。其反应机理参见如下反应方案(一):
[0041]
[0042][0043]
进一步地,所述步骤s3中,将所述聚酰胺酸盐纺丝液经过计量泵和喷丝头,采用湿法纺丝直接喷入凝固浴中,然后经清洗浴清洗,形成所述聚酰胺酸盐水凝胶纤维,所述凝固浴和清洗浴为纯水浴。
[0044]
进一步地,所述步骤s4中,所述化学亚胺化包括将用清水洗净的所述聚酰胺酸盐水凝胶纤维置于所述有机溶剂中进行3-4次溶剂置换,得到所述聚酰胺酸盐有机凝胶纤维;然后将所述聚酰胺酸盐有机凝胶纤维浸泡在含有乙酸酐和吡啶的有机溶液中化学亚胺化24-48小时,得到所述聚酰亚胺有机凝胶纤维。
[0045]
更进一步地,所述步骤s4中,所述有机溶剂与所述聚酰胺酸盐水凝胶纤维的体积比为5~15:1;加入的乙酸酐和吡啶的摩尔比为1:1,且乙酸酐与所述聚酰胺酸盐有机凝胶纤维的二酐单体摩尔量比为2~3:1。
[0046]
例如,在一种实施方案中,酰胺酸化学亚胺化形成酰亚胺的反应机理如下面的反应方案(二)所示:
[0047][0048]
进一步地,所述步骤s5中,所述溶剂置换采用乙醇进行多次置换,乙醇与所述聚酰
亚胺有机凝胶纤维的体积比为5~15:1,此后进行超临界干燥,所述超临界干燥过程中使用的超临界流体为超临界co2,压力设定为8.5~9mpa,干燥釜温度为40~50℃,干燥时间为12~36h,优选12~24h;
[0049]
或者,所述溶剂置换采用叔丁醇和水的混合溶液进行多次置换,所述叔丁醇和水的混合溶液中叔丁醇与水的体积比为2:3,所述混合溶液与所述聚酰亚胺有机凝胶纤维的体积比为5~15:1,此后进行冷冻干燥,所述冷冻干燥过程中的温度为-50~-30℃,压强为1~50pa,干燥时间为24~72h,优选为24~48h。
[0050]
与现有聚酰亚胺气凝胶纤维相比,本发明的聚酰亚胺气凝胶纤维通过引入三乙胺和聚酰胺酸中的羧基以离子键的方式结合生成聚酰胺酸盐,提高了聚酰胺酸的水溶性,避免纤维在纯水凝固浴中形成致密膜,从而可以用纯水作为凝固浴和清洗浴,节约成本的同时减少了环境污染;通过引入交联剂增大纺丝液的粘度并增加初生纤维的韧性,有效提高纺丝液的可纺性,同时降低了纺丝液中聚酰胺酸的质量分数,使其具有分子尺度的三维网络结构,从而赋予所述聚酰亚胺气凝胶纤维良好的强度和韧性。
[0051]
此外,与现有工艺相比,本发明提供的高强度聚酰亚胺气凝胶纤维的制备方法原料广泛易得,制备工艺简单,反应条件温和,反应过程可控,工艺流程连续,前后处理步骤少,可实现大规模生产。
[0052]
为了让本发明的目的、特征和优点能更加明显易懂,下面通过多个非限制性实施例来说明根据本发明实施方案的高强度聚酰亚胺气凝胶纤维及其制备方法。
[0053]
实施例
[0054]
实施例1
[0055]
取二胺单体对苯二胺10.814g(0.1000mol),溶于450ml有机溶剂n-甲基吡咯烷酮中。搅拌均匀后,取二酐单体3,3,4,4-联苯四羧酸二酐31.383g(0.1067mol)加入上述混合溶液中,常温水浴中机械搅拌三十分钟。待溶液完全透明后,得到聚酰胺酸溶液。取三乙胺13.900ml(0.1000mol)加入到所述聚酰胺酸盐溶液中,继续搅拌十分钟。然后取交联剂1,3,5-三(4-氨基苯氧基)苯1.784g(0.0045mol)溶于50ml n-甲基吡咯烷酮中,加入并继续搅拌十分钟。最后在真空环境下脱泡2小时,得到聚酰胺酸盐纺丝液。其中二酐单体、二胺单体、三乙胺和交联剂摩尔比为16:15:16:0.67。在聚酰胺酸盐纺丝液中,聚酰胺酸盐的质量分数为10.53wt%。
[0056]
在纺丝过程中,将脱泡后的所述聚酰胺酸盐纺丝液加入到储罐中,密封并加压1~2mpa来帮助所述聚酰胺酸盐纺丝液的流动。所述聚酰胺酸盐纺丝液采用湿法纺丝。具体地,采用直径0.5mm的喷丝头,喷丝头离凝固浴水面间隙为5cm,以1.8cm3/min的挤出速度纺丝,调控计量泵和绕丝机的频率,使绕丝机线速度与纺丝液线速度比为2:1。凝固浴和清洗浴为纯水浴,温度控制在5~15℃。所述聚酰胺酸盐纺丝液被计量泵从喷丝头中挤出到凝固浴中,经过凝固浴的溶剂置换固化形成直径约0.35mm的初生纤维。然后所述初生纤维经过导轮和绕丝机收集,在清洗浴中,表面残余的n-甲基吡咯烷酮被清洗,清洗时间1min,完成溶剂置换形成聚酰胺酸盐水凝胶纤维。
[0057]
然后将所述聚酰胺酸盐水凝胶纤维置于自身10倍体积n-甲基吡咯烷酮中溶剂置换4次,每次6小时,得到聚酰胺酸盐有机凝胶纤维。将溶剂置换后的所述聚酰胺酸盐有机凝胶纤维浸泡在乙酸酐和吡啶摩尔比为1:1的n-甲基吡咯烷酮溶液中24小时,得到聚酰亚胺
有机凝胶纤维。乙酸酐与所述聚酰胺酸盐有机凝胶纤维的二酐单体摩尔量比为2:1,温度控制在25℃。
[0058]
然后将所述聚酰亚胺有机凝胶纤维在自身10倍体积的乙醇溶液中溶剂置换4次,每次6小时,然后经过超临界干燥得到所述具有三维网络结构的聚酰亚胺气凝胶纤维。所述超临界干燥过程中使用的超临界流体为超临界co2,干燥釜压力控制为8.5~9mpa,干燥釜温度控制在40~50℃,干燥时间15小时。所得到的聚酰亚胺气凝胶纤维拉伸强度为62.5mpa,弹性模量为821mpa,比表面积为271m2/g,线密度为23.4tex,热导率为0.031w
·
m-1
·
k-1
。
[0059]
实施例2
[0060]
取二胺单体4,4'-二氨基二苯醚20.024g(0.1000mol),溶于450ml有机溶剂n-甲基吡咯烷酮中。搅拌均匀后,取二酐单体均苯四甲酸酐23.273g(0.1067mol)加入上述混合溶液中,常温水浴中机械搅拌三十分钟。待溶液完全透明后,得到聚酰胺酸溶液。取三乙胺13.900ml(0.1000mol)加入到所述聚酰胺酸盐溶液中,继续搅拌十分钟。然后取交联剂1,3,5-三(4-氨基苯氧基)苯1.784g(0.0045mol)溶于50ml n-甲基吡咯烷酮中,加入并继续搅拌十分钟。最后在真空环境下脱泡2小时,得到聚酰胺酸盐纺丝液。其中二酐单体、二胺单体、三乙胺和交联剂摩尔比为16:15:16:0.67。在聚酰胺酸盐纺丝液中,聚酰胺酸盐的质量分数为10.39wt%。
[0061]
在纺丝过程中,将脱泡后的所述聚酰胺酸盐纺丝液加入到储罐中,密封并加压1~2mpa来帮助所述聚酰胺酸盐纺丝液的流动。所述聚酰胺酸盐纺丝液采用湿法纺丝。具体地,采用直径0.5mm的喷丝头,喷丝头离凝固浴水面间隙为5cm,以1.8cm3/min的挤出速度纺丝,调控计量泵和绕丝机的频率,使绕丝机线速度与纺丝液线速度比为2:1。凝固浴和清洗浴为纯水浴,温度控制在5~15℃。所述聚酰胺酸盐纺丝液被计量泵从喷丝头中挤出到凝固浴中,经过凝固浴的溶剂置换固化形成直径约0.35mm的初生纤维。然后所述初生纤维经过导轮和绕丝机收集,在清洗浴中,表面残余的n-甲基吡咯烷酮被清洗,清洗时间1min,完成溶剂置换形成聚酰胺酸盐水凝胶纤维。
[0062]
然后将所述聚酰胺酸盐水凝胶纤维置于自身10倍体积n-甲基吡咯烷酮中溶剂置换4次,每次6小时,得到聚酰胺酸盐有机凝胶纤维。将溶剂置换后的所述聚酰胺酸盐有机凝胶纤维浸泡在乙酸酐和吡啶摩尔比为1:1的n-甲基吡咯烷酮溶液中24小时,得到聚酰亚胺有机凝胶纤维。乙酸酐与所述聚酰胺酸盐有机凝胶纤维的二酐单体摩尔量比为2:1,温度控制在25℃。
[0063]
然后将所述聚酰亚胺有机凝胶纤维在自身10倍体积的叔丁醇/水溶液中溶剂置换4次,每次6小时,所述叔丁醇/水溶液中,叔丁醇/水的体积比为2:3。然后经过真空冷冻干燥得到所述具有三维网络结构的聚酰亚胺气凝胶纤维。所述真空冷冻干燥过程中温度控制在-50~-30℃,压强控制在1~50pa,干燥时间24h。所得到的聚酰亚胺气凝胶纤维拉伸强度为54.5mpa,弹性模量为753mpa,比表面积为236m2/g,线密度为21.3tex,热导率为0.035w
·
m-1
·
k-1
。
[0064]
实施例3
[0065]
取二胺单体4,4'-二氨基二苯醚20.024g(0.1000mol),溶于750ml有机溶剂n-甲基吡咯烷酮中。搅拌均匀后,取二酐单体均苯四甲酸酐23.273g(0.1067mol)加入上述混合溶
液中,常温水浴中机械搅拌三十分钟。待溶液完全透明后,得到聚酰胺酸溶液。取三乙胺13.900ml(0.1000mol)加入到所述聚酰胺酸盐溶液中,继续搅拌十分钟。然后取交联剂1,3,5-三(4-氨苯基)苯1.571g(0.0044mol)溶于50ml n-甲基吡咯烷酮中,加入并继续搅拌十分钟。最后在真空环境下脱泡2小时,得到聚酰胺酸盐纺丝液。其中二酐单体、二胺单体、三乙胺和交联剂摩尔比为16:15:16:0.67。在聚酰胺酸盐纺丝液中,聚酰胺酸盐的质量分数为6.69wt%。
[0066]
在纺丝过程中,将脱泡后的所述聚酰胺酸盐纺丝液加入到储罐中,密封并加压1~2mpa来帮助所述聚酰胺酸盐纺丝液的流动。所述聚酰胺酸盐纺丝液采用湿法纺丝。具体地,采用直径0.5mm的喷丝头,喷丝头离凝固浴水面间隙为5cm,以1.8cm3/min的挤出速度纺丝,调控计量泵和绕丝机的频率,使绕丝机线速度与纺丝液线速度比为2:1。凝固浴和清洗浴为纯水浴,温度控制在5~15℃。所述聚酰胺酸盐纺丝液被计量泵从喷丝头中挤出到凝固浴中,经过凝固浴的溶剂置换固化形成直径约0.35mm的初生纤维。然后所述初生纤维经过导轮和绕丝机收集,在清洗浴中,表面残余的n-甲基吡咯烷酮被清洗,清洗时间1min,完成溶剂置换形成聚酰胺酸盐水凝胶纤维。
[0067]
然后将所述聚酰胺酸盐水凝胶纤维置于自身10倍体积n-甲基吡咯烷酮中溶剂置换4次,每次6小时,得到聚酰胺酸盐有机凝胶纤维。将溶剂置换后的所述聚酰胺酸盐有机凝胶纤维浸泡在乙酸酐和吡啶摩尔比为1:1的n-甲基吡咯烷酮溶液中24小时,得到聚酰亚胺有机凝胶纤维。乙酸酐与所述聚酰胺酸盐有机凝胶纤维的二酐单体摩尔量比为2:1,温度控制在25℃。
[0068]
然后将所述聚酰亚胺有机凝胶纤维在自身10倍体积的乙醇溶液中溶剂置换4次,每次6小时,然后经过超临界干燥得到所述具有三维网络结构的聚酰亚胺气凝胶纤维。所述超临界干燥过程中使用的超临界流体为超临界co2,干燥釜压力控制为8.5~9mpa,干燥釜温度控制在40~50℃,干燥时间16小时。所得到的聚酰亚胺气凝胶纤维拉伸强度为46.5mpa,弹性模量为634mpa,比表面积为283m2/g,线密度为19.1tex,热导率为0.033w
·
m-1
·
k-1
。
[0069]
虽然在前面的详述中已经给出了至少一个实施方案,但是应当理解的是存在大量变型。还应当理解,这些实施方案仅仅是示例性的,并不旨在以任何方式限制本发明的范围。相反,前面的详述将为本领域技术人员提供用于实施本发明实施方案的便利路线图。应当理解,在不脱离如所附权利要求书及其法律等效物所阐述的本发明范围的情况下,可以对示例性实施方案中描述的要素的功能和布置进行各种改变。