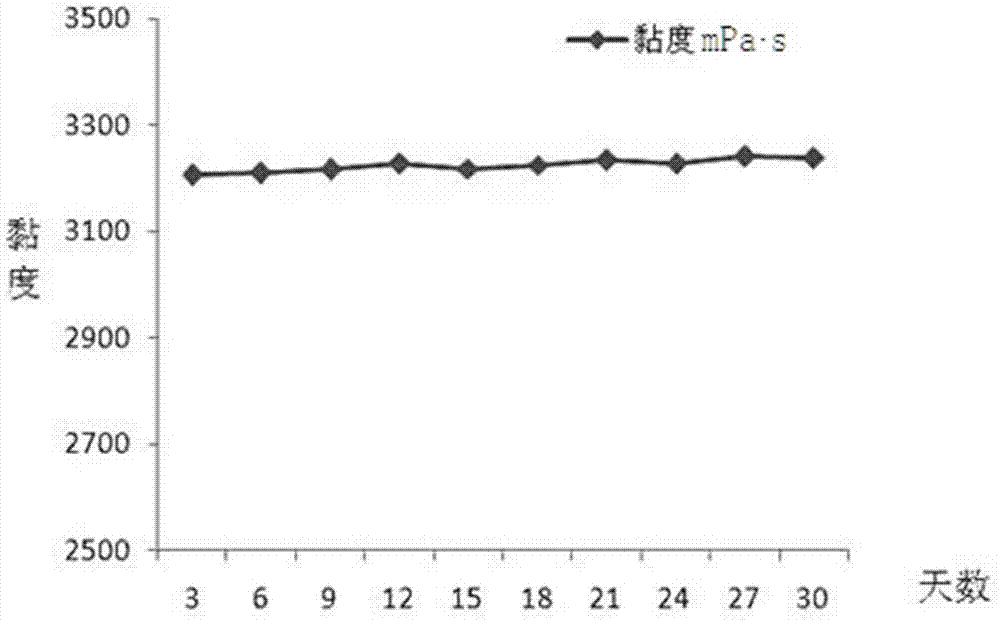
本发明属于颜色
技术领域:
,具体涉及一种荧光颜料色浆及其制备方法。
背景技术:
:随着科学技术的发展和人类生活水平的提高,人们对颜色的多样性需求越来越高。在颜料色浆中添加荧光效果,可以使颜料色浆所应用的产品大幅度提高附加值,增加新颖性,形成与目前市场主流产品的区分,吸引客户购买。关于荧光颜料色浆,cn103572617a公开了一种水性防沉不分层荧光颜料色浆,其特征在于,其原料组分按照重量百分比为:润湿剂:2~20%;分散剂:1~20%;稳定剂:0.1~10%;荧光颜料:25~55%;余量为去离子水;基于上述配方,水性防沉不分层荧光颜料色浆的制备工艺为:先将去离子水加入预分散釜内,边搅拌边添加稳定剂,添加完成后继续搅拌,然后边搅拌边依次加入润湿剂、分散剂和荧光颜料,直至混合均匀,继续搅拌;将上述混合液通过装有锆珠的卧式砂磨机进行研磨分散,分散后的混合液过滤测试分散粒度,转移到调色槽内调整色光浓度,即得到产品。以上文献所解决的技术问题是,获得一种水性防沉不分层荧光颜料色浆。技术实现要素:为了解决上述的技术问题,本发明提供了一种带有荧光特性、环保无害、着色力强、成分稳定、耐气候性强的颜料色浆及其制备方法。本发明是通过下述的技术方案来实现的:一种荧光颜料色浆,该色浆中主要原料的重量份数如下:颜料为耐晒黄、永固黄、联苯胺黄、永固橙、永固桔黄、永固红、耐晒大红、立索尔洋红、永固桃红、喹丫啶酮红、dpp红、永固紫、喹丫啶酮紫、酞青蓝、酞青绿、碳黑中的至少一种。荧光粉由硫化钙、硫化镁、硫酸钡、硫酸镁、硫酸钾、硫酸钠、硫酸锶、磷酸锂、硝酸锶、硝酸铜、硝酸银、硝酸钾、硫化铝、硫化钡、硫酸钾、硫酸锶中的至少两种荧光粉原料混合而制成;荧光粉为可发出红荧光、黄荧光、蓝荧光的荧光粉;发红荧光的荧光粉由硫酸钡、硫酸镁、磷酸锂、硝酸铜制成;发蓝荧光的荧光粉由硫化钙、硫酸钠、硫酸钾、硫酸锶、氯化钠、硝酸银、硫化镁制成;发黄荧光的荧光粉由硫化钡、硫化镁、硫化铝、硝酸钾制成。润湿分散剂为聚丙烯酸酯、改性聚丙烯酸酯、改性聚氨酯、聚丙烯酸酯钠盐、聚丙烯酸酯铵盐、聚羧酸烷醇铵盐、烷基聚氧乙烯醚、烷基酚聚氧乙烯醚硫酸钠盐、烷基聚氧乙烯醚硫酸铵盐、烷基聚氧乙烯醚磷酸酯、苯基酚聚氧乙烯醚中的至少一种。保湿剂为聚乙二醇及其衍生物、聚丙二醇及其衍生物、丙三醇、丁三醇、三甘醇、四甘醇、三乙醇胺、三乙二醇醚、二甘醇二丁醚、三甘醇一乙醚、四甘醇二甲醚中的至少一种。ph值调节剂为氨水、尿素、氢氧化钠、氢氧化钾和三乙醇胺中的任一种。防沉降剂为气相二氧化硅、有机膨润土和聚乙烯蜡中的至少一种。防腐剂为1-2苯并异噻唑啉-3-酮、2-甲基-4-异噻唑啉-3-酮、5-氯-2-甲基-4-异噻唑啉-3-酮/2-甲基-4-异噻唑啉-3-酮和卡松中的至少一种。上述的荧光颜料色浆的制备方法,包括以下的步骤:(1)将水、润湿分散剂、保湿剂、ph值调节剂、防沉降剂、防腐剂投入到预分散机中混合,分散机转速为300-500r/min,20min后得到均匀混合液;(2)将颜料加入上述均匀混合液中,进行预分散,分散机转速为1000-1500r/min,分散时间为30min-60min,得到预分散浆料;(3)将荧光粉原料混合后在133℃下加热灼烧50min,然后置于研磨机研磨,直到粒径分布d90小于1μm时停止研磨,再置于水中浸泡沉淀,所得沉淀物干燥后得到发不同颜色荧光的荧光粉;(4)将荧光粉加入到预分散浆料中,采用研磨机研磨,直至粒度分布d90小于1μm,停止研磨;(5)如果粒度达不到(4)中的要求,重复步骤(4)直至色浆粒度达到要求为止;(6)经研磨达到粒度要求的色浆,再经过质量检测、脱泡和过滤包装,得到最终产品荧光颜料色浆。步骤(3)和/或(4)中所采用的研磨机为篮式砂磨、立式砂磨和卧式砂磨中的任一种。本发明中发明人的思路是,通过调整配方及改进工艺,提供一种相容性好、成分稳定、耐气候性强、保持颜料色度,同时添加荧光成分的颜料色浆。其中,改变荧光粉的制作工艺代替传统的稀土三基色的荧光成分,提高了观赏性,同时在满足粒度要求的前提下大大降低了成本。本发明所提供的荧光粉,可以组合,获得所需荧光的颜色。本发明的有益效果在于,本发明所得的荧光颜料色浆具有储存期内不絮凝,不沉淀,不分层;流动性好,与应用体系相容性良好,着色效率高,成本低、完全无粉尘;重金属含量符合限量要求,使用安全、环保等特点。附图说明图1为实施例1中的产品高温下放置一个月之后的黏度变化图;图2为实施例2中的产品暴晒一个月之后的黏度变化图。具体实施方式下面结合具体实施例对本发明作更进一步的说明,以便本领域的技术人员更了解本发明,但并不因此限制本发明。各原料的生产厂家:防腐剂bit,即1-2苯并异噻唑啉-3-酮,佛山市丽源化工有限公司防腐剂mit,即2-甲基-4-异噻唑啉-3-酮,深圳市罗湖区宇哲洗涤原料厂防腐剂cmit,5-氯-2-甲基-4-异噻唑啉-3-酮/2-甲基-4-异噻唑啉-3-酮,杭州罗川化工有限公司防腐剂卡松,型号:dl101,济南德蓝化工有限公司抗氧化剂bha(丁基羟基茴香醚),常州市宇荣化工有限公司所采用的材料均来自市售常见原料;在此不一一罗列;实施例1制备一种添加了红荧光粉的颜料色浆,其具体的步骤如下:(1)按比例称取水20份、润湿分散剂10份、保湿剂20份、抗氧化剂bha0.3份、防沉降剂气相二氧化硅0.3份、防腐剂bit0.2份、ph值调节剂0.3份;将水、润湿分散剂、保湿剂、抗氧化剂、防沉降剂、防腐剂投入到预分散器中混合,分散机转速为500r/min,20min后得均匀混合液;润湿分散剂由聚丙烯酸酯、苯基酚聚氧乙烯醚、聚丙烯酸酯钠盐组成,聚丙烯酸酯:苯基酚聚氧乙烯醚:聚丙烯酸酯钠盐=2:1:1,(w/w);保湿剂由聚乙二醇及其衍生物和三乙二醇醚组成,聚乙二醇及其衍生物:三乙二醇醚=2:1,(w/w);ph值调节剂为氢氧化钠(固体颗粒);(2)将40份颜料永固红加入上述均匀混合液中,进行预分散,分散机转速为1500r/min,分散时间50min,得到预分散浆料;(3)红荧光粉的制备:按重量份数比例称取硫酸钡55份、硫酸镁40份、磷酸锂2份、硝酸铜3份,混合后在133℃下加热灼烧50min后,放入立式砂磨机中进行研磨,直到粒径分布d90小于1μm时停止研磨,将研磨后的物料置于水中浸泡并沉淀,得到沉淀物干燥得到红荧光粉;(4)添加红荧光粉的颜料色浆的制备:将3份红荧光粉加入至预分散浆料中,采用卧式研磨机对上述预分散浆料进行研磨,直至粒度分布d90小于1μm,停止研磨;(5)如果粒度达不到上述的要求,重复步骤(4)直至色浆粒度达到要求;(6)经研磨达到粒度要求的色浆,再经过质量检测、脱泡和过滤包装后,得到最终产品荧光颜料色浆。本发明与
背景技术:
中的“水性防沉不分层荧光颜料色浆”最大的区别是,采用的原料并非荧光颜料,而是颜料与荧光粉;在本发明的工艺中,将荧光粉与颜料分别进行处理;具体的处理工艺是:将颜料加入上述均匀混合液中,进行预分散,分散机转速为1500r/min,分散时间为50min,得到预分散浆料;将荧光粉加入至预分散色浆,采用研磨机对上述预分散浆料进行研磨,直至粒度分布d90小于1μm,停止研磨;主要原因是:色浆是一个分散体系,一般颜料在液体中以悬浮形式保持长时间的稳定状态是非常困难的,因为液体中颜料粒子多数络合成二次粒子聚积成块,当颜料粒子外包裹或吸附的分散剂受到其它物质的竞争或其电荷性能受到破坏时,颜料粒子相互间受到外力的牵引时,都容易产生颜料粒子间的凝聚、沉降甚至于沉积分层等等不稳定的情况发生,因此,其本身存在不稳定的倾向。本发明通过改进工艺,将颜料和荧光粉分别处理,并且调整配方,加入合适配比的分散剂(具体分析如下),使色浆的稳定性增强,克服由于颜料在色浆中不稳定发生沉降的现象,尤其是克服当颜料和荧光粉结合之后更容易产生分层沉降等现象这一缺陷。本发明所采用的分散剂和保湿剂,通过其润湿作用和渗透作用,渗入颜料粒子的间隙,在粒子的表面发生定向吸附,从而改变颜料粒子及荧光粉粒子的表面性能,并使粒子表面带电,形成双电层,从而阻止粒子的聚集,使颜料分散体系形成稳定。本发明所采用的分散剂并非任意选择的,分散剂的选择对于本发明的体系较为重要,其原因是,要使颜料及荧光粉都能被分散介质润湿,使分散剂吸附在粒子表面,降低表面自由能,打破颜料及荧光粉缔合的二次结构,形成稳定的体系。另外,本发明人经过考察和多次实验,获得了较为理想的颜料及荧光粉,筛选出了颜色适宜、颗粒度较松散、聚合度小宜于分散的颜料及荧光粉,使两者在色浆体系中呈现良好的“正态分布”曲线,而进一步达到此目的,必须结合特定的工艺,本发明的工艺中对颜料和荧光粉分别进行比如分散、灼烧研磨、再分散或反复分散处理的工艺,使颜料及荧光粉的晶体粒径集中在一个较为均一或者是说相对狭窄的范围内,避免出现过大或过小的粒子从而导致颜料或荧光粉分散不均出现沉降的问题。判断色浆黏度随时间和温度变化(如附图1):颜料色浆变化的主要原因是阳光中紫外光线与可视光线对颜料产品所引起的破坏,除此之外,热度以及潮湿也会加速颜色的改变;颜料色浆因为气候(温度或紫外线)影响造成的改变主要表现在颜色的变化、褪色、光泽的消失等现象上;本发明为了检验实施例1中产品的耐侯性,进行了以下的实验:测定方法:将色浆产品置于60-65℃下,3天之后,每隔3天都取样对其黏度进行检测,通过数据探索其黏度变化,从而判断其耐高温性能;从附图1中可以看出,制成的色浆在高温下放置一个月,其黏度随时间变化值非常小,一个月之后,其黏度基本无变化;这说明本发明的色浆产品其耐高温性能好,稳定性强;黏度并不是随着高温或时间而产生较大的变化;通过以上数据可以看出,实施例1的产品,其旋转黏度较为稳定(是在6r/min的条件下进行测定)。附图1和附图2中,横坐标均为天数,纵坐标均为黏度,黏度的单位是(mpa·s)。实施例2制备一种添加蓝荧光粉的颜料色浆,其具体的步骤如下:(1)按比例称取水20份、润湿分散剂10份、保湿剂20份、抗氧化剂bha0.3份、防沉降剂有机膨润土0.3份、防腐剂bit0.2份、ph值调节剂0.3份;将水、润湿分散剂、保湿剂、抗氧化剂、防沉降剂、防腐剂投入到预分散器中混合,分散机转速为500r/min,20min后得均匀混合液;润湿分散剂由改性聚氨酯、聚羧酸烷醇铵盐组成,改性聚氨酯:聚羧酸烷醇铵盐=1:3;(w/w);保湿剂由四甘醇和丙三醇组成,四甘醇:丙三醇=1:1,(w/w);ph值调节剂为氢氧化钠(固体颗粒);(2)将35份颜料酞青蓝加入上述均匀混合液中,进行预分散,分散机转速为1200r/min,分散时间为40min,得到预分散浆料;(3)蓝荧光粉的制备:按比例称取硫化钙63份、硫酸钠5份、硫酸钾5份、硫酸锶10份、氯化钠6份、硝酸银1份、硫化镁10份,混合后在133℃下加热灼烧50min后,放入研磨机进行研磨,直到粒径分布d90小于1μm,停止研磨,放入水中浸泡沉淀,得到沉淀物干燥得到蓝荧光粉;(4)添加蓝荧光粉的颜料色浆的制备:将蓝荧光粉3份加入至预分散浆料中,采用卧式研磨机对上述预分散浆料进行研磨,直至粒度分布d90小于1μm,停止研磨;(5)如果粒度达不到上述的要求,重复步骤(4)直至色浆粒度达到要求;(6)经研磨达到粒度要求的色浆,再经过质量检测、脱泡和过滤包装后,得到最终产品荧光颜料色浆。附图2为产品在太阳下暴晒一个月之后的黏度(暴晒时白天的平均温度为32℃,最高温度为39℃);从附图2中可以看出,产品的黏度也较稳定,其耐光性较好。实施例3制备一种添加了黄荧光粉的颜料色浆,其步骤如下:(1)按比例称取水20份、润湿分散剂10份、保湿剂20份、抗氧化剂bha0.3份、防沉降剂气相二氧化硅0.3份、防腐剂bit0.2份、ph值调节剂0.3份;将水、润湿分散剂、保湿剂、抗氧化剂、防沉降剂、防腐剂投入到预分散器中混合,分散机转速为500r/min,20min后得均匀混合液;润湿分散剂由烷基聚氧乙烯醚硫酸铵盐、苯基酚聚氧乙烯醚、聚丙烯酸酯钠盐组成,烷基聚氧乙烯醚硫酸铵盐:苯基酚聚氧乙烯醚:聚丙烯酸酯钠盐=1:1:1;(w/w);保湿剂由聚乙二醇及其衍生物和三乙二醇醚组成,聚乙二醇及其衍生物:三乙二醇醚=2:1,(w/w);ph值调节剂为氢氧化钠(固体颗粒);(2)将40份颜料耐晒黄加入上述均匀混合液中,进行预分散,分散机转速为1500r/min,分散时间为30min,得到预分散浆料;(3)黄荧光粉的制备:按比例称取硫化钡55份、硫化镁40份、硫化铝2份、硝酸钾3份,混合后在133℃下加热灼烧50min后,放入研磨机进行研磨,直到粒径分布d90小于1μm,停止研磨,放入水中浸泡沉淀,得到沉淀物干燥得到黄荧光粉;(4)添加黄荧光粉的颜料色浆的制备:将3份黄荧光粉加入至预分散浆料中,采用卧式研磨机对上述预分散浆料进行研磨,直至粒度分布d90小于1μm,停止研磨;(5)如果粒度达不到上述的要求,重复步骤(4)直至色浆粒度达到要求;(6)经研磨达到粒度要求的色浆,再经过质量检测、脱泡和过滤包装后,得到最终产品荧光颜料色浆。实施例4制备一种添加了红荧光粉的颜料色浆,其具体的步骤如下:(1)按比例称取水20份、润湿分散剂10份、保湿剂20份、防沉降剂气相二氧化硅0.3份、防腐剂mit0.2份、ph值调节剂0.25份;将水、润湿分散剂、保湿剂、防沉降剂、防腐剂投入到预分散器中混合,分散机转速为500r/min,20min后得均匀混合液;润湿分散剂由聚丙烯酸酯、苯基酚聚氧乙烯醚、聚丙烯酸酯钠盐组成,聚丙烯酸酯:苯基酚聚氧乙烯醚:聚丙烯酸酯钠盐=2:1:1,(w/w);保湿剂由聚乙二醇及其衍生物和三乙二醇醚组成,聚乙二醇及其衍生物:三乙二醇醚=2:1,(w/w);ph值调节剂为氢氧化钠(固体颗粒);(2)将40份颜料永固红加入上述均匀混合液中,进行预分散,分散机转速为1500r/min,分散时间50min,得到预分散浆料;(3)红荧光粉的制备:按重量份数比例称取硫酸钡55份、硫酸镁40份、磷酸锂2份、硝酸铜3份,混合后在133℃下加热灼烧50min后,放入立式砂磨机中进行研磨,直到粒径分布d90小于1μm时停止研磨,将研磨后的物料置于水中浸泡并沉淀,得到沉淀物干燥得到红荧光粉;(4)添加红荧光粉的颜料色浆的制备:将3份红荧光粉加入至预分散浆料中,采用卧式研磨机对上述预分散浆料进行研磨,直至粒度分布d90小于1μm,停止研磨;(5)如果粒度达不到上述的要求,重复步骤(4)直至色浆粒度达到要求;(6)经研磨达到粒度要求的色浆,再经过质量检测、脱泡和过滤包装后,得到最终产品荧光颜料色浆。对比例1将润湿分散剂调整为2份,其余与实施例1完全相同;对比例2将润湿分散剂调整为25份,其余与实施例1完全相同;对比例3对比例3中,(2)为:将40份颜料加入上述均匀混合液中,混合,得混合物料;(4)添加红荧光粉的颜料色浆的制备:将3份红荧光粉加入至(2)中的混合物料中,采用卧式研磨机对上述预分散浆料进行研磨,直至粒度分布d90小于1μm,停止研磨;其余的步骤与实施例1相同;对比例4(3)黄荧光粉的制备:按比例称取硫化钡55份、硫化镁40份、硫化铝2份、硝酸钾3份,混合得到黄荧光粉;其余步骤与实施例1相同;关于本发明所获得的色浆,发明人进行了以下的检测实验:检测方法:根据gb/t21473-2008《调色系统用色浆》对本发明所得的产品进行检测(其中具体的指标按照上述的标准附录中的方法进行),检测的结果如下:表1实施例1-4与各对比例的产品性能对比表从以上数据可以看出,本发明中实施例1-4中的色相差较小,彩度差及明度差也较小,说明了本发明的产品其色牢度较好,着色稳定性较好。而且实施例1-4中的黏度较为均一,数值相接近,证明产品的稳定性及重现性较好,同时产品的耐侯性较好,达到了5级,而对比其它实验对比例1-4,其耐侯性较差。对比例3、4调整了工艺步骤,未通过本发明的工艺步骤进行处理,所获得的产品其相对着色力较差,色相差较大。通过肉眼观察产品的外观,发现对比例3、4中的分层和沉淀现象比较严重。而实施例1-4中无分层现象。表2关于实施例1-4中的产品中重金属含量的检测(mg/kg)可溶性铅可溶性铬可溶性镉可溶性汞实施例122184321实施例220213925实施例324223728实施例423194522gb/t21473-2008中规定的重金属含量的标准是:可溶性铅≤90mg/kg,可溶性镉≤75mg/kg,可溶性铬≤60mg/kg,可溶性汞≤60mg/kg;重金属检测的方法是:gb18582-2001中附录c规定的方法;以上表格中的重金属含量的数据均小于上述国家标准中的规定数值,在安全的范围之内,本发明的产品是属于对环境友好型产品。通过以上数据可以看出,本发明的产品,具有较好的流动性,长时间储存不结块,不分层、不沉淀,无发霉现象产生;产品的黏度稳定;着色力强,重金属含量较低等特点。以上所述,仅为本发明的具体实施方式,但本发明的保护范围并不局限于此,因此,本发明的保护范围应以权利要求书所限定的保护范围为准。当前第1页12