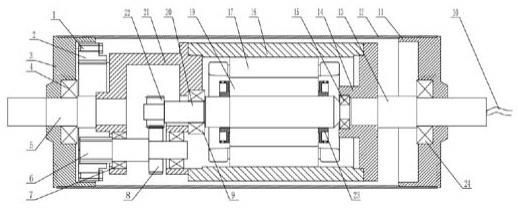
1.本实用新型属于电动滚筒技术领域,具体涉及一种高效节能电动滚筒。
背景技术:2.电动滚筒广泛应用于物流分拣设备等具有传送皮带进行物资输送的物流系统,由滚筒摩擦带动传送皮带移动,滚筒的转速一般是150至250rpm,现有的电动滚筒技术采用三相异步电机驱动,电机额定转速为2850rpm。因电机转速高,滚筒转速低,因此电动滚筒对应的减速比大,而减速比大,为了在滚筒有效空间内达到所需要的减速比,必须将与电机轴配合的主动齿轮做的很小,现有的结构基本是将该电机齿轮电机轴直接一体加工成型,而这样的一体结构不但增加电机轴的生产成本、降低降低电机轴的强度,也降低电机轴的互换性,加大设备维护成本;另外,辊筒内配置的润滑油对电机等转运系统有阻碍作用,驱动电机高速旋转时,搅油损耗大、整机温升比较高,导致运转效率低,一般电机效率只能达到在78%左右。
技术实现要素:3.本实用新型旨在应用永磁同步电机原理进行驱动以降低电动滚筒减速比,提供一种高效节能电动滚筒技术方案,以克服现有技术中存在的问题。
4.一种高效节能电动滚筒,包括筒体与前输出轴、后输出轴,前输出轴上设置与其转动配合的前端盖,后输出轴设置与其转动配合的后端盖,前端盖、后端盖分别与筒体固定套接配合,其特征在于前端盖的内端连接设置与其固定配合的内齿圈,前输出轴的内端连接设置箱体,箱体的另一端连接设置机壳,机壳的另一端连接设置电机端盖,机壳腔内配合设置嵌线定子、转子冲片、转轴,转子冲片内插接磁钢,转轴的后端与电机端盖转动配合,前端与箱体转动配合并伸入箱体内,伸入箱体内的转轴上连接设置与其固定配合的主动齿轮,主动齿轮经齿轮减速机构与内齿圈构成减速传动配合。
5.所述的一种高效节能电动滚筒,其特征在于所述的齿轮减速机构包括齿轴,齿轴安装在箱体上并与箱体转动配合,齿轴上连接设置与其固定配合的从动齿轮,从动齿轮与主动齿轮之间啮合构成减速传动配合,齿轴前端伸出箱体后与内齿圈之间啮合构成减速传动配合。
6.所述的一种高效节能电动滚筒,其特征在于所述的前端盖、后端盖与筒体之间分别采用过盈配合结构,。
7.所述的一种高效节能电动滚筒,其特征在于所述的主动齿轮与转轴之间通过链接键构成固定配合结构。
8.所述的一种高效节能电动滚筒,其特征在于所述的磁钢插接在转子冲片内构成方形结构。
9.所述的一种高效节能电动滚筒,其特征在于所述的嵌线定子与机壳之间、转子冲片与转轴之间分别采用过盈配合结构,所述的箱体、电机端盖分别通过螺栓与机壳连接固
定。
10.所述的一种高效节能电动滚筒,其特征在于所述的磁钢与转子冲片之间粘接固定。
11.所述的一种高效节能电动滚筒,其特征在于所述的转子冲片两端外侧设置平衡盘与磁钢顶触配合构成磁钢的轴向限位机构,平衡盘套接在转轴上并与其过盈配合。
12.所述的一种高效节能电动滚筒,其特征在于所述的后输出轴中设置通孔穿接引出线。
13.所述的一种高效节能电动滚筒,其特征在于所述的箱体与机壳采用一体结构。
14.所述的一种高效节能电动滚筒设计新颖、结构合理,本技术方案应用永磁同步电机原理设计驱动电机,降低电机额定转速与电动滚筒减速比,实现了将主动齿轮与电机轴分离、适当加大齿轮模数的设计结构,可提高电机轴互换性、增加整机强度、降低搅油损耗与电辊筒整机温升,经理论计算与实际试验测试,电机效率能达到92%,与现有技术相比电动滚筒减速比降低超过48%,效率提升超过18%。
附图说明
15.图1为本实用新型结构示意图;
16.图2为图1中a-a剖视结构示意图;
17.图中:1-端盖螺栓、2-内齿圈、3-前端盖、4-前轴承、5-前输出轴、6-齿轴、7-齿轴轴承、8-从动齿轮、9-电机前轴承、10-引出线、11-后端盖、12-筒体、13-后输出轴、14-电机端盖、15-电机后轴承、16-机壳、17-嵌线定子、18-磁钢、19-转子冲片、20-转轴、21-箱体、22-主动齿轮、23-平衡盘、24-后轴承。
具体实施方式
18.现结合说明书附图,详细说明本实用新型的具体实施方式:
19.如图所示为一种高效节能电动滚筒,前输出轴5、后输出轴13位于电动滚筒两端,使用时前输出轴5、后输出轴13的外端分别固定在设备的机架上,后输出轴13中设置通孔穿接引出线10以简化出线布设;前输出轴5上通过前轴承4设置与其转动配合的前端盖3,后输出轴13上通过后轴承24设置与其转动配合的后端盖11,前端盖3与后端盖11之间设置筒体12,前端盖3、后端盖11与筒体12之间分别采用过盈配合构成固定套接配合结构,前端盖3、后端盖11、筒体12连接构成一个旋转体;前输出轴5的内端连接设置箱体21,箱体21的前端套接在前输出轴5的内端且采用过盈配合构成固定连接结构,箱体21的另一端即后端通过螺栓与机壳16的前端固定连接,机壳16的后端通过螺栓与电机端盖14固定连接;机壳16腔内配合设置嵌线定子17、转子冲片19、转轴20,嵌线定子17与机壳16之间、转子冲片19与转轴20之间分别采用过盈配合结构,嵌线定子17与机壳16构成一个整体结构,转子冲片19与转轴20之间构成一个整体结构;转子冲片19内插接磁钢18,磁钢18插接在转子冲片19内构成方形结构,磁钢18插接在转子冲片19内进行适当固定或限位以防止发生轴线移动,可以将磁钢18与转子冲片19之间进行粘接固定,或者在转子冲片19两端外侧设置平衡盘23与磁钢18顶触配合构成磁钢18的轴向限位机构,平衡盘23套接在转轴20上并与其过盈配合;转轴20的后端通过电机后轴承15与电机端盖14转动配合,转轴20的前端通过电机前轴承9与
箱体21转动配合并伸入箱体21内,伸入箱体21内的转轴20上连接设置与其固定连接配合的主动齿轮22,主动齿轮22经齿轮减速机构与内齿圈2构成减速传动配合,内齿圈2通过端盖螺栓1固定连接在前端盖3的内端,设置在主动齿轮22与内齿圈2之间的齿轮减速机构采用多级减速机构,如图1所示为两级减速,齿轮减速机构包括齿轴6,齿轴6安装在箱体21上并通过前后设置的齿轴轴承7与箱体21转动配合,齿轴6上连接设置通过键连接结构形成固定配合的从动齿轮8,从动齿轮8与主动齿轮22之间啮合构成第一级减速传动配合,齿轴6前端伸出箱体21后与内齿圈2之间啮合构成第二级减速传动配合。
20.上述实施例中,为进一步优化结构,箱体21与机壳16采用一体结构,以简化装配工艺,提高生产效率。
21.应用上述实施例,前输出轴5、后输出轴13固定在设备机架上,嵌线定子17通电后产生磁场拖动磁钢18一起旋转,因磁钢18插接在转子冲片19内,磁钢18旋转通过转子冲片19带动转轴20转动,转轴20带动与其固定连接配合的主动齿轮22,从动齿轮8与主动齿轮22啮合传动并减速,从动齿轮8带动与其固定连接配合的齿轴6一起转动,内齿圈2与齿轴6啮合传动并减速,内齿圈2转动时带动与其固定连接配合的前端盖3转动,前端盖3转动带动与其形成固定连接结构的筒体12、后端盖11整体旋转,从而实现了转轴20经两级减速后带动前端盖3、内齿圈2旋转、前端盖3一起旋转,此时,转轴20的转速为1500rpm,相比现有技术中的三相异步电机额定转速2850rpm而言,驱动电机的转速已降低约48%,而筒体12的转速按设计需求是确定的,此时电动滚筒的减速比就降低了约48%,满足这样的减速比要求,转轴20上所配设的主动齿轮22可以适当放大,因此主动齿轮22可以采用中心孔结构,并通过键连接与主动齿轮22固定配合,这样实现了转轴20与主动齿轮22的分离结构,可提高转轴20的互换性,同时,转轴20的转速降低、减速比相应降低,主动齿轮22及齿轮减速机构所配齿轮的齿轮模数就可适当加大,可增加整机强度;电机额定转速从现有技术的2850rpm降低到本方案的1500rpm,搅油损耗与电辊筒整机温升都得到明显降低,经理论计算与实际测试,现有技术中电机效率约78%,而本技术方案中电机效率达到92%,效率提升超过18%。