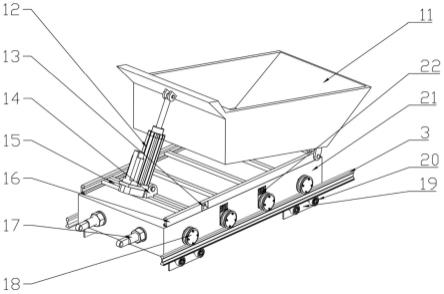
1.本发明涉及了一种输送自卸装置,具体涉及了一种新型上下轮轨道式输送自卸装置。
背景技术:2.由于焦化厂每年都生产大量的焦油渣,其具有很大的危害性对环境和土地都有巨大的污染,对人们身体健康也有很大伤害。随着研究者对焦油渣加工工艺的升级和新的炼焦方法的提出,会大大减少焦油渣产生的量,就会从源头上减少焦油渣,但任何先进的技术不可能完全消除废渣的生成,故需要对焦油渣进行运输和运输。在实际生产过程中,焦油渣槽内的固体焦油渣需要输送至远端的燃烧炉内充分燃烧,以避免对环境的污染。目前散装物料和工业废渣的运输主要都是采用带式输送机来进行运输。传统使用的标准带式输送机是在托辊组的基础上支撑输送带,两者之间运行阻力制约着运送线路的长度和运送量。况且固体焦油渣具有高粘度等特性,因此采用普通的固体输送带将无法实现固体焦油渣的远距离输送,采用轨道式输送可以极大节约成本。现有的输送系统无法实现较高程度的自动控制过程,也无法实现物料封闭式操作处理,带式输送机在运行中上下震动,产生灰尘严重影响环境。由于焦油渣产生的量较少,连续输送装置会极大的浪费能源消耗,增加了成本负担,经济效益低,因此需要一种可实现定量装货的设备。焦油渣的运输由于在工厂中,路况比较复杂,中间运输过程中会经历上坡的阶段,要求运输装置能进行爬坡。这些问题制约着带式输送机在工厂运输焦油渣,急需待解决。
技术实现要素:3.为了解决背景技术中存在的问题,本发明所提供一种新型上下轮轨道式输送自卸装置。本发明解决常规带式输送机阻力问题,设计和研究一种新型轨式输送机,具体针对到煤焦化工业的难题,能够实现固体焦油渣的远距离输送,并实现了焦油渣处理以保护生态环境的定量轨道输送可卸装置。
4.本发明采用的技术方案是:
5.本发明输送自卸系统包括输送自卸装置、压绳装置、牵引绞车、张紧装置、第一钢丝绳和第二钢丝绳,输送自卸装置、压绳装置、牵引绞车和张紧装置在输送自卸系统的输送方向上依次间隔固定布置。
6.第一钢丝绳的一端自牵引绞车的滚筒下侧的机身内引出,依次绕经张紧装置的张紧轮以及牵引绞车的滚筒上侧后,再绕经压绳装置一侧的压绳轮的下侧,进而连接至输送自卸装置,而后自输送自卸装置返回,绕经压绳装置的另一侧的压绳轮的下侧,最终引回牵引绞车;第二钢丝绳自张紧装置的机身引出,沿张紧装置的张紧轮的水平径向方向,连接至压绳装置的机身。
7.所述的牵引绞车可为无极绳牵引绞车等。
8.所述的张紧装置的张紧轮和牵引绞车的滚筒的圆心位于同一水平线上。张紧装置
可为重锤式张紧装置。设置张紧装置可以保证钢丝绳具有一定的预张力,这样可以防止钢丝绳打滑,减小输送的阻力。
9.张紧轮可沿第二钢丝绳左右移动,进而实现对第一钢丝绳的张紧。
10.所述的输送自卸装置包括尾轮、轮组、轨道、梭车和自卸轨道式装置,尾轮安装在轨道上远离压绳装置的一侧端部,托绳轮组安装在靠近尾轮的轨道上,梭车和自卸轨道式装置位于轨道顶部,自卸轨道式装置位于轮组和梭车之间;轮组包括托绳轮和压绳轮,托绳轮和压绳轮安装在轨道上,托绳轮布置于压绳轮的下方。
11.所述第一钢丝绳连接至梭车的车身的锲块并绕经梭车的储绳轮后穿出,再通过三环链连接至自卸轨道式装置的一端,然后穿设过自卸轨道式装置,从轮组的压绳轮和托绳轮之间穿过,之后绕经尾轮并返回,在轨道内部沿轨道的长度方向引出,绕经压绳装置的另一侧的压绳轮的下侧,最终引回牵引绞车的卷绳筒。压绳装置两侧的压绳轮分别位于轨道的两侧。
12.尾轮安装在运输线的终点位置,具有承受轨道式输送自卸系统反力的功能,还具有方便调节的功能,可以随时根据所需的运输长度调整第一钢丝绳的长度。
13.托绳轮组防止第一钢丝绳高度降低,压绳装置的压绳轮防止第一钢丝绳抬高,保持装置可以正常的运行。
14.所述的自卸轨道式装置包括运货厢、折返式伺服电缸、若干导向轮、若干行走轮、车体、支撑架和若干轨道轮轴;车体通过若干导向轮和若干行走轮滑动安装在轨道上,支撑架平行固定安装在车体的顶面,运货厢和折返式伺服电缸安装在支撑架顶部。
15.各个导向轮对称安装在车体的对称两侧面并滑动支撑在轨道上侧,每两个对称于车体的导向轮通过一根穿过车体的轨道轮轴连接;各个行走轮通过行走轮座对称安装在车体底部的对称两侧边并摩擦接触轨道下侧。
16.靠近梭车的运货厢底部的一侧两端铰接在支撑架顶部,远离梭车的运货厢顶部的一侧中间通过折返式伺服电缸铰接支撑架顶部;折返式伺服电缸的机身通过尾铰和轴承座铰接在支撑架顶部,折返式伺服电缸的丝杠铰接运货厢顶部的一侧中间,使得折返式伺服电缸朝运货厢倾斜。
17.支撑架包括若干横向支撑架和两个侧向支撑架,两个侧向支撑架平行于轨道长度方向并间隔布置,各个横向支撑架固定连接在两个侧向支撑架之间并构成平面的梯子形状;运货厢底部的一侧两端分别铰接在两个侧向支撑架上;折返式伺服电缸的机身铰接在其中一个横向支撑架上。
18.靠近梭车的车体的一侧面上还设有连接件,连接件通过连接至自身的三环链连接第一钢丝绳。
19.连接件用来连接车体和梭车,使梭车带动自卸轨道式装置,是刚性连接。使用三环链可以缓冲并有效减轻在行驶的过程中可能发生的刹车或启动时的碰撞。
20.轨道轮轴和车体之间设有轴卡。
21.所述的每个导向轮包括轨道轮封板、若干内六角螺钉、深沟球轴承、轨道轮和孔用弹性挡圈。
22.轨道轮支撑在轨道上侧,轨道轮的中心通过深沟球轴承连接轨道轮轴的一端,轨道轮的外端面通过若干内六角螺钉安装有轨道轮封板,轨道轮封板和深沟球轴承之间设有
孔用弹性挡圈。
23.轨道轮起到导向和防脱轨作用。由于装置运行过程中,主要承受径向载荷,轴向承受较小,故选用深沟球轴承。轨道轮轴与深沟球轴承进行配合,设有的孔用弹性挡圈固定深沟球轴承的轴向运动。轨道轮封板使得端面密封,防止灰尘、水、有害气体和其他杂物进入深沟球轴承内腔对深沟球轴承进行损伤,也可起到密封的作用。
24.所述的行走轮包括行走轮轴和行走轮套,行走轮轴的一端通过六角螺母固定安装在行走轮座内侧,六角螺母和行走轮座之间设有弹性垫圈和平垫圈;行走轮轴位于行走轮座外侧的另一端,通过深沟球轴承套装有行走轮套,行走轮套摩擦接触轨道的下侧。
25.每两个行走轮通过一个行走轮座安装在车体下侧,导向轮和行走轮的对称设置,可以防止自卸轨道式装置在轨道上的跳动,并使得自卸轨道式装置具有爬坡能力。弹性垫圈主要为了放松行走轮,平垫圈为了降低行走轮座的压应力,防止出现压溃和永久塑性变形。
26.还包括用于控制折返式伺服电缸运动的装置控制开关,装置控制开关安装在支撑架侧边,并电连接折返式伺服电缸的电机。
27.在装载有货物的运货厢需要自卸货物时,运货厢处于初始状态,装置控制开关控制折返式伺服电缸的电机运行,进而带动折返式伺服电缸的活塞杆向上顶动丝杆连接的运货厢顶部,使得运货厢从初始状态绕自身铰接在支撑架上的底部转动,运货厢自身倾斜为自卸状态,形成四杆机构故可以使运货厢产生翻转运动。货物自运货厢内倾倒出去,即完成自卸轨道式装置的自卸过程;完成自卸过程后,装置控制开关控制驱动折返式伺服电缸的活塞杆下拉运货厢,使得运货厢从自卸状态恢复为初始状态。
28.装置控制开关在自卸轨道式装置移动至固定自卸位置时自动开启,进而控制自卸轨道式装置的自卸过程。
29.所述的自卸轨道式装置的运货厢自靠近尾轮的轨道上的初始位置安装上货物后,牵引绞车借助第一钢丝绳与滚筒之间的摩擦力,通过带动滚筒绕自身轴线转动,带动第一钢丝绳绕正向传动,进而带动梭车和自卸轨道式装置在轨道上移动,自卸轨道式装置移动至自卸位置后停止移动,通过装置控制开关自动控制完成自卸轨道式装置的自卸过程。
30.自卸轨道式装置回程时,牵引绞车的卷绳筒带动第一钢丝绳绕反向传动,进而带动梭车和自卸轨道式装置在轨道上移动,自卸轨道式装置最终从自卸位置移动至初始位置,进行下一轮自卸过程。
31.梭车仅能沿轨道长度方向移动。梭车不仅能牵引自卸轨道式装置,还能固定和存储第一钢丝绳,增加运行的安全性和可靠性。
32.还包括若干减震器,每个减震器安装在对应的一个导向轮上方,并位于导向轮连接的一个轨道轮轴和车体之间。其中,车体四角的四个导向轮上方不安装减震器。
33.利用压力迫使减震器中的刚性弹簧发生变形运动,抑制导向轮经过不平的路段所产生的冲击,从而使得中间的导向轮能够在钢轨上正常的接触。
34.所述的车轴为轨道轮轴或行走轮轴,轨道轮轴和行走轮轴均是固定心轴,车轴的直径为行走轮轴套装有行走轮套一端的直径或轨道轮轴的直径,通过以下车轴优化方法确定:
35.获取自卸轨道式装置的自身质量和运载质量,根据当量载荷法通过自卸轨道式装
置的自身质量和运载质量计算出作用在车轴上的载荷,进而计算出此时车轴的弯矩m,然后通过应力计算公式σ优化选取车轴的直径,具体如下:
[0036][0037]
其中,[σ]w为预设许用应力,在车轴的材料选择优质碳素钢45时,[σ]w=170mpa。
[0038]
本发明的有益效果是:
[0039]
(1)传统使用的带式输送机是在托辊组的基础上支撑输送带,两者之间的摩擦阻力消耗了很大的一部分能量。而轨式输送机是通过钢轨和钢轮进行接触,两者之间发生弹性变形很小,所以摩擦力也不会很大,极大的节省了成本,在经济上更加有益。
[0040]
(2)轨式输送的焦油渣和车厢由于在运行过程中保持相对静止的状态,物料的堆积角可近似考虑为休止角,不仅使运输量增大还会使物料不产生相对运动,从而使摩擦大大减小,减少了很多灰尘,更有利于保护环境。
[0041]
(3)自卸轨道式装置利用导向轮和行走轮在钢轨上下运行,还在中间导向轮设置了减震器使其运行更加平稳,还具有较强的爬坡能力,适应化工厂运输固体渣的工况。
[0042]
(4)牵引系统采用的无极绳牵引,不仅操作简单,可靠性强还具有牵引能力强,节约能源的特点,十分适合搭配自卸轨道式装置运输物料。
[0043]
(5)电动缸受温度的影响十分小,结构比较简单,装置体积小故占用空间不大,这将会十分方便电缸的安装,而且控制的精度比较高,十分容易到达所要到达的位置。采用折返式安装形式可以使电缸的总体长度较短,能减小装置的占用空间,有较高的控制精度,电缸的行程较长。折返式电动缸利用电缸的推动能使车厢翻转更加迅速精确。
[0044]
(6)采用了四连杆设计和车厢内倾斜设计可以使车厢更加容易翻转和倾倒,实现定量运送的目的。
附图说明
[0045]
图1为本发明的一种可自卸轨道式输送机的整体结构示意图;
[0046]
图2为本发明的轨道式自卸装置的立体结构示意图;
[0047]
图3为本发明的导向轮的横向剖面图;
[0048]
图4为本发明的行走轮的横向剖面图;
[0049]
图中1、尾轮,2、轮组,3、轨道,4、三环链,5、梭车,6、压绳轮,7、牵引绞车,8、第一钢丝绳,9、张紧装置,10、自卸轨道式装置,11、运货厢,12、折返式伺服电缸,13、装置控制开关,14、轴承座,15、横向支撑架,16、侧向支撑架,17、连接件,18、导向轮,19、行走轮座,20、行走轮,21、车体,22、减震器,23、轨道轮封板,24、内六角螺钉,25、深沟球轴承,26、轨道轮轴,27、轴卡,28、轨道轮,29、孔用弹性挡圈,30、行走轮轴,31、行走轮套,32、六角螺母,33、弹性垫圈,34、平垫圈。
具体实施方式
[0050]
下面结合附图及具体实施例对本发明作进一步详细说明。
[0051]
如图1所示,本发明输送自卸系统包括输送自卸装置、压绳装置、牵引绞车7、张紧装置9、第一钢丝绳8和第二钢丝绳,输送自卸装置、压绳装置、牵引绞车7和张紧装置9在输
送自卸系统的输送方向上依次间隔固定布置。
[0052]
第一钢丝绳8的一端自牵引绞车7的滚筒下侧的机身内引出,依次绕经张紧装置9的张紧轮以及牵引绞车7的滚筒上侧后,再绕经压绳装置一侧的压绳轮6的下侧,进而连接至输送自卸装置,而后自输送自卸装置返回,绕经压绳装置的另一侧的压绳轮6的下侧,最终引回牵引绞车7;第二钢丝绳自张紧装置9的机身引出,沿张紧装置9的张紧轮的水平径向方向,连接至压绳装置的机身。
[0053]
牵引绞车7可为无极绳牵引绞车等。张紧装置9的张紧轮和牵引绞车7的滚筒的圆心位于同一水平线上。张紧装置9可为重锤式张紧装置。设置张紧装置9可以保证钢丝绳具有一定的预张力,这样可以防止钢丝绳打滑,减小输送的阻力。张紧轮可沿第二钢丝绳左右移动,进而实现对第一钢丝绳8的张紧。
[0054]
输送自卸装置包括尾轮1、托绳轮组2、轨道3、梭车5和自卸轨道式装置10,尾轮1安装在轨道3上远离压绳装置的一侧端部,托绳轮组2安装在靠近尾轮1的轨道3上,梭车5和自卸轨道式装置10位于轨道顶部,自卸轨道式装置10位于托绳轮组2和梭车5之间。轮组2包括托绳轮和压绳轮,托绳轮和压绳轮安装在轨道3上,托绳轮布置于压绳轮的下方。
[0055]
第一钢丝绳8连接至梭车5的车身的锲块并绕经梭车5的储绳轮后穿出,再通过三环链4连接至自卸轨道式装置10的一端,然后穿设过自卸轨道式装置10,从轮组2的压绳轮和托绳轮之间穿过,之后绕经尾轮1并返回,在轨道3内部沿轨道3的长度方向引出,绕经压绳装置的另一侧的压绳轮6的下侧,最终引回牵引绞车7的卷绳筒。压绳装置两侧的压绳轮6分别位于轨道3的两侧。尾轮1安装在运输线的终点位置,具有承受轨道式输送自卸系统反力的功能,还具有方便调节的功能,可以随时根据所需的运输长度调整第一钢丝绳8的长度。托绳轮组2防止第一钢丝绳8高度降低,压绳装置的压绳轮6防止第一钢丝绳8抬高,保持装置可以正常的运行。
[0056]
如图2和图3所示,自卸轨道式装置10包括运货厢11、折返式伺服电缸12、若干导向轮18、若干行走轮20、车体21、支撑架和若干轨道轮轴26;车体21通过若干导向轮18和若干行走轮20滑动安装在轨道3上,支撑架平行固定安装在车体21的顶面,运货厢11和折返式伺服电缸12安装在支撑架顶部。
[0057]
各个导向轮18对称安装在车体21的对称两侧面并滑动支撑在轨道3上侧,每两个对称于车体21的导向轮18通过一根穿过车体21的轨道轮轴26连接,轨道轮轴26和车体21之间设有轴卡27;各个行走轮20通过行走轮座19对称安装在车体21底部的对称两侧边并摩擦接触轨道3下侧。
[0058]
靠近梭车5的运货厢11底部的一侧两端铰接在支撑架顶部,远离梭车5的运货厢11顶部的一侧中间通过折返式伺服电缸12铰接支撑架顶部;折返式伺服电缸12的机身通过尾铰和轴承座14铰接在支撑架顶部,折返式伺服电缸12的丝杠铰接运货厢11顶部的一侧中间,使得折返式伺服电缸12朝运货厢11倾斜。
[0059]
自卸轨道式装置10还包括若干减震器22,每个减震器22安装在对应的一个导向轮18上方,并位于导向轮18连接的一个轨道轮轴26和车体21之间。其中,车体21四角的四个导向轮18上方不安装减震器22。
[0060]
利用压力迫使减震器22中的刚性弹簧发生变形运动,抑制导向轮18经过不平的路段所产生的冲击,从而使得中间的导向轮18能够在钢轨上正常的接触。
[0061]
支撑架包括若干横向支撑架15和两个侧向支撑架16,两个侧向支撑架16平行于轨道3长度方向并间隔布置,各个横向支撑架15固定连接在两个侧向支撑架16之间并构成平面的梯子形状;运货厢11底部的一侧两端分别铰接在两个侧向支撑架16上;折返式伺服电缸12的机身铰接在其中一个横向支撑架15上。
[0062]
靠近梭车5的车体21的一侧面上还设有连接件17,连接件17通过连接至自身的三环链4连接第一钢丝绳8。连接件17用来连接车体21和梭车5,使梭车5带动自卸轨道式装置10,是刚性连接。使用三环链4可以缓冲并有效减轻在行驶的过程中可能发生的刹车或启动时的碰撞。
[0063]
自卸轨道式装置10还包括用于控制折返式伺服电缸12运动的装置控制开关13,装置控制开关13安装在支撑架侧边,并电连接折返式伺服电缸12的电机。
[0064]
在装载有货物的运货厢11需要自卸货物时,运货厢11处于初始状态,装置控制开关13控制折返式伺服电缸12的电机运行,进而带动折返式伺服电缸12的活塞杆向上顶动丝杆连接的运货厢11顶部,使得运货厢11从初始状态绕自身铰接在支撑架上的底部转动,运货厢11自身倾斜为自卸状态,形成四杆机构故可以使运货厢11产生翻转运动。货物自运货厢11内倾倒出去,即完成自卸轨道式装置10的自卸过程;完成自卸过程后,装置控制开关13控制驱动折返式伺服电缸12的活塞杆下拉运货厢11,使得运货厢11从自卸状态恢复为初始状态。
[0065]
装置控制开关13在自卸轨道式装置10移动至固定自卸位置时自动开启,进而控制自卸轨道式装置10的自卸过程。
[0066]
自卸轨道式装置10的运货厢11自靠近尾轮1的轨道上的初始位置安装上货物后,牵引绞车7借助第一钢丝绳8与滚筒之间的摩擦力,通过带动滚筒绕自身轴线转动,带动第一钢丝绳8绕正向传动,进而带动梭车5和自卸轨道式装置10在轨道3上移动,自卸轨道式装置10移动至自卸位置后停止移动,通过装置控制开关13自动控制完成自卸轨道式装置10的自卸过程;
[0067]
自卸轨道式装置10回程时,牵引绞车7的卷绳筒带动第一钢丝绳8绕反向传动,进而带动梭车5和自卸轨道式装置10在轨道3上移动,自卸轨道式装置10最终从自卸位置移动至初始位置,进行下一轮自卸过程。
[0068]
梭车5仅能沿轨道3长度方向移动。梭车5不仅能牵引自卸轨道式装置10,还能固定和存储第一钢丝绳8,增加运行的安全性和可靠性。如图4所示,行走轮20包括行走轮轴30和行走轮套31,行走轮轴30的一端通过六角螺母32固定安装在行走轮座19内侧,六角螺母32和行走轮座19之间设有弹性垫圈33和平垫圈34;行走轮轴30位于行走轮座19外侧的另一端,通过深沟球轴承25套装有行走轮套31,行走轮套31摩擦接触轨道3的下侧。
[0069]
其中,自卸轨道式装置10的每两个行走轮20通过一个行走轮座19安装在车体21下侧,导向轮18和行走轮20的对称设置,可以防止自卸轨道式装置10在轨道3上的跳动,并使得自卸轨道式装置10具有爬坡能力。弹性垫圈33主要为了放松行走轮20,平垫圈34为了降低行走轮座19的压应力,防止出现压溃和永久塑性变形。
[0070]
每个导向轮18包括轨道轮封板23、若干内六角螺钉24、深沟球轴承25、轨道轮28和孔用弹性挡圈29。
[0071]
轨道轮28支撑在轨道3上侧,轨道轮28的中心通过深沟球轴承25连接轨道轮轴26
的一端,轨道轮28的外端面通过若干内六角螺钉24安装有轨道轮封板23,轨道轮封板23和深沟球轴承25之间设有孔用弹性挡圈29。
[0072]
轨道轮28起到导向和防脱轨作用。由于装置运行过程中,主要承受径向载荷,轴向承受较小,故选用深沟球轴承25。轨道轮轴26与深沟球轴承25进行配合,设有的孔用弹性挡圈29固定深沟球轴承25的轴向运动。轨道轮封板23使得端面密封,防止灰尘、水、有害气体和其他杂物进入深沟球轴承25内腔对深沟球轴承25进行损伤,也可起到密封的作用。
[0073]
针对输送自卸系统的一种车轴优化方法,具体如下:
[0074]
车轴为轨道轮轴26或行走轮轴30,轨道轮轴26和行走轮轴30均是固定心轴,车轴的直径为行走轮轴30套装有行走轮套31一端的直径或轨道轮轴26的直径,通过以下车轴优化方法确定:
[0075]
获取自卸轨道式装置10的自身质量和运载质量,根据当量载荷法通过自卸轨道式装置10的自身质量和运载质量计算出作用在车轴上的载荷,进而计算出此时车轴的弯矩m,然后通过应力计算公式σ优化选取车轴的直径,具体如下:
[0076][0077]
其中,[σ]w为预设许用应力,在车轴的材料选择优质碳素钢45时,[σ]w=170mpa。