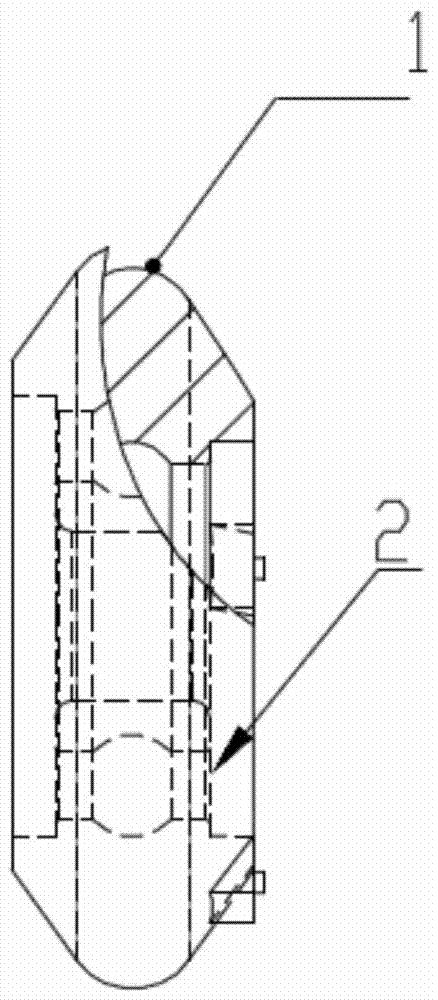
本发明涉及一种聚氨酯滚轮及其注塑工艺,通过此注塑工艺制备得到的滚轮制品,其聚氨酯胎圈与金属轮毂具备良好的粘结性能,广泛适用于自动扶梯滚轮、门挂轮等领域。
背景技术:目前制造聚氨酯滚轮有两种传统工艺方法:注塑工艺和浇注工艺。注塑工艺一般程序为:先用热塑性聚氨酯粒子注塑滚轮胎圈,再将轮毂通过低压机过盈压装入聚氨酯胎圈内,使胎圈包紧轮毂,从而制得滚轮;其中热塑性聚氨酯可选用聚酯MDI+抗水解剂热塑性聚氨酯粒子,金属轮毂可选用铝合金或45#钢,以及轴承可选用6203、6204等标准钢铁轴承。注塑工艺包括以下步骤:1)、聚氨酯胎圈注塑成型:使用160-260T低压注塑机注塑聚氨酯胎圈,由注塑模具控制制品包胶尺寸,胎圈注塑固化成型周期为65-70秒,注塑完成后注塑模具自动打开,操作工取出成型完毕的滚轮制品;2)、将聚氨酯胎圈脱模后放入100℃烘箱进行16小时后熟化作业;3)、再将轮毂通过低压压机过盈压装入聚氨酯胎圈内,使胎圈包紧轮毂;得到不带轴承的滚轮制品;4)、将金属轮毂包胶完成的聚氨酯滚轮进行轴承装配,得到带轴承的聚氨酯滚轮制品。注塑工艺使用的设备成本低,注塑设备成本:20-30万元/套设备及注塑模具成本:3-4万元/套模具/台注塑机。注塑程序简单,生产效率高;以100毫米外径聚氨酯扶梯梯级运行滚轮为例,注塑成型时间为65-70秒/循环,产量为1200-1300件/班(8小时)。人工成本低:每台注塑需要2名操作员工;聚氨酯材料成本低:热塑性聚氨酯材料均价为30-45元/公斤。但是由于金属轮毂与聚氨酯胎圈之间是通过低压压机过盈压装配制得,因此轮毂与聚氨酯胎圈之间是完全没有粘结力的,不能满足使用需求。传统注塑工艺生产的滚轮为例,其在20公斤负载,50米/分钟运行速度的环境下,仅仅运行8-10分钟就会出现胎圈脱出导致滚轮损坏的缺陷,而在<=150公斤负载,50米/分钟运行速度的环境下,也只能正常运行2000小时。因此传统注塑工艺制备的滚轮胎圈与轮毂的粘结力差,不能满足高性能的需要。对于胎圈与金属轮毂之间粘结力大于35牛顿/毫米的高性能滚轮制品,例如自动扶梯滚轮,一般需要采用热固性聚氨酯和预喷胶处理好的金属轮毂的高温浇注工艺进行制作;其中热固型聚氨酯可选用聚醚TDI聚氨酯预聚体,粘结剂可选用100-120℃高温反应型聚氨酯胶粘剂,金属轮毂可选用铝合金或45#钢,以及轴承可选用6203、6204等标准钢铁轴承。浇注工艺包括以下步骤:1)、对铝合金轮毂喷胶面使用石英砂粒或铁砂粒进行预喷砂打毛作业;2)、对喷砂后轮毂进行表面脱脂清洁作业;3)、对铝合金轮毂与聚氨酯粘接面使用100-120℃高温反应型聚氨酯胶粘剂进行喷胶;4)、将喷胶后的金属轮毂放置于湿度<75%,于5-30℃环境中干燥2-3小时;5)、将喷胶后的干燥的金属轮毂及滚轮浇注模具放入120℃烘箱预烘2-2.5小时;6)、将金属轮毂放入浇注模具中,通过浇注模具控制制品包胶尺寸,使用两组分或三组分低压聚氨酯弹性体浇注机在轮毂外侧浇注液态热固性聚氨酯材料;7)、将浇注完成制品与浇注模具放入100-120℃烘道内,进行12-15分钟液态聚氨酯高温固化成型作业;8)、热固性聚氨酯成型完毕后,将制品脱模并放入100℃烘箱进行16小时后熟化作业,得到滚轮制品;9)、将金属轮毂包胶完成的聚氨酯滚轮进行轴承装配,得到带轴承的聚氨酯滚轮制品。通过此浇注工艺制备得到的滚轮制品,其金属轮毂(铝合金或45#钢)与热固性聚醚TDI聚氨酯预聚体形成的胎圈之间的粘结强度均达到了45-55牛顿/毫米,粘结性能高,能很好的满足自动扶梯对其滚轮的高性能要求。以热固性聚氨酯浇注工艺生产的某聚氨酯自动扶梯梯级运行滚轮为例,其规格为:外径100毫米,宽度25毫米,内径20毫米,聚氨酯胎圈厚10毫米,硬度为95(邵氏A);铝合金轮毂厚16毫米,装配62042RS标准轴承。其在重载200公斤的条件下以50米/分钟的速度下,可正常运行2000小时,且滚轮无脱胶,聚氨酯破损等缺陷。装梯后可正常运行5年无质量缺陷。因此,高性能聚氨酯滚轮通常需要浇注工艺生产。但是传统浇注工艺也存在多个不足:1)、设备成本高,低压浇注设备成本为70-80万元/台;另外如预热烘道,烘箱,真空脱泡机,氮气注入机,预搅拌机等附加组件,设备成本通常在110-120万元/套;2)、生产效率低,浇注工艺聚氨酯固化成型需要20-25分钟/循环,一条浇注生产线产量为550-570件/班(8小时工作制);3)、人工成本高:4-5名操作人员;4)、材料成本高:目前热固性聚氨酯常用材料聚醚TDI聚氨酯预聚体价格为50-85元/公斤。本发明目的在于克服通过传统注塑和浇注工艺制备滚轮制品的各自不足,如传统注塑工艺制得的聚氨酯滚轮其胎圈和金属轮毂无粘结力,而传统浇注工艺的生产效率低,设备、材料和人力的成本都较高。本发明旨在提供一种聚氨酯滚轮的新注塑工艺,其整合了传统注塑和浇注工艺的优点,其采用的设备成本、材料成本和人力成本低,生产效率高,且制得的滚轮制品的金属轮毂和聚氨酯胎圈之间具备良好的粘结力(大于35牛顿/毫米),且具有高承载动态性能。
技术实现要素:本发明的发明思路在于吸取了传统注塑工艺生产效率高,投资成本低,浇注工艺产品性能高的特点,将传统注塑与浇注的优势结合;采用改良的注塑工艺生产出高性能要求的滚轮,该滚轮的金属轮毂与聚氨酯胎圈间粘合力大于35牛顿/毫米,具有高承载动态性能。本发明提供了一种聚氨酯滚轮的注塑工艺,该聚氨酯滚轮的胎圈与金属轮毂具有大于35牛顿/毫米的粘结力,其特征在于,该方法包括以下步骤:1)、对金属轮毂的喷胶面进行预喷砂打毛作业;2)、对步骤1)得到的金属轮毂进行表面脱脂清洁作业;3)、对步骤2)得到的金属轮毂的喷胶面使用高温反应型粘结剂进行预喷胶处理;4)、将步骤3)得到的预喷胶处理的金属轮毂,在湿度≤75%下,在5-30℃环境中,初步干燥处理2-3小时;5)、将步骤4)得到的初步干燥的预喷胶处理的金属轮毂在110-120℃下,预热2-10小时;6)、将步骤5)得到的预喷好粘结剂的金属轮毂先放入注塑模腔定位、固定后合模,再使用低压注塑机将液态热塑性聚氨酯材料由浇注机螺杆射入注塑模具胶口中,胶口为多点扇形均匀分布,且进胶方式为多点胶口同时进胶,使液态热塑聚氨酯材料能在极短的时间内在注塑模具内汇流成胎圈的形状,热塑性聚氨酯材料与金属轮毂的喷胶层的粘结剂充分接触、反应约65-70秒后,从注塑模具中取出成型的滚轮制品;7)、将步骤6)得到的滚轮制品进行后熟化处理,得到聚氨酯滚轮。本发明的一种实施方式是将步骤7)得到的滚轮制品进行轴承装配,得到带有轴承的聚氨酯滚轮。本发明的一种实施方式中,所述步骤1)中采用石英砂粒或铁砂粒预喷砂对金属轮毂进行打毛作业;且金属轮毂由铝合金或碳钢材料制得。本发明的一种实施方式中,所述步骤3)中所述高温反应性粘结剂是指使用在聚氨酯与铝合金或碳钢材料间,通过140-210℃的高反应温度使聚氨酯与铝合金或碳钢材料间产生大于35牛顿/毫米的高粘结力的高性能高温反应型粘结剂;该粘结剂可选自英国西邦公司的等粘结剂。本发明的一种实施方式中,所述步骤6)中所述热塑性聚氨酯材料是指反应型滑剂含量低于0.3%非反应型滑剂、且能保证快速注塑周期的聚酯MDI+抗水解剂的热塑性聚氨酯材料;该聚氨酯材料可选用BAYER公司的型号为U90、U95的TPU热塑性粒子或95邵氏A的TPU材料。本发明的一种实施方式中,所述步骤6)中所述的胶口为多点扇形分布,其中多点是指超过两点;优选为3-8点。本发明的一种实施方式中,所述步骤7)的后熟化处理条件为:在80-100℃,干燥10-16小时;最佳后熟化条件为100℃,10小时。为了能通过注塑工艺生产金属轮毂与聚氨酯胎圈间粘合力大的、且承载动态性能可以媲美浇注工艺生产的滚轮,本发明从五方面创新性地改进了传统的注塑工艺:第一、选用特殊的热塑性聚氨酯材料。普通热塑性聚氨酯材料为保证注塑时螺杆顺畅注塑周期短的工艺性能,在聚氨酯材料内通常含有0.3-0.5%反应型滑剂,但反应型滑剂会与金属轮毂表面的粘结剂进行反应,从而影响粘结剂与聚氨酯胎圈的粘结性能。因此,为了保证注塑生产的滚轮制品的粘结性能与传统浇注滚轮制品具有相当的粘结性能,即粘结力大于35牛顿/毫米;发明人选择了反应型滑剂含量低于0.3%、且能保证快速注塑周期的特殊聚酯MDI+抗水解剂的热塑性聚氨酯材料进行生产。此类热塑性聚氨酯材料属性为MDI+抗水解剂;具体可以选用BAYER公司的型号为U90、U95的TPU热塑性粒子或95邵氏A的TPU材料等。第二、选用特殊胶粘剂。由于选用的聚氨酯成型温度为200-220℃,如果选用传统浇注工艺时使用的100-120℃反应型聚氨酯胶粘剂,则会由于胶粘剂与聚氨酯的反应温度不一致导致胶粘剂与聚氨酯胎圈反应不充分,从而造成金属轮毂与聚氨酯胎圈的粘结力差甚至没有粘结力的缺陷;因此,发明人选用了200-220℃高温反应型特殊聚氨酯胶粘剂。此类高温反应型胶粘剂属性为聚氨酯与金属反应性粘结剂,具体可以选用英国西邦公司的等粘结剂。第三、生产工艺改进。发明人采用特殊的注塑工艺方法:1)工序更变:不同于传统聚氨酯滚轮注塑工序:即先使用热塑性聚氨酯粒子注塑滚轮胎圈,再将轮毂通过低压压机过盈压装入聚氨酯胎圈内,使胎圈包紧轮毂,轮毂与胎圈之间是没有粘结力。本发明是将用高温反应型特殊聚氨酯胶粘剂进行预喷胶处理后的金属轮毂放入注塑模具,使用注塑机在轮毂外侧高温下注塑聚氨酯胎圈,胶粘剂与聚氨酯在高温注塑过程中,反应后固化,从而得到轮毂与胎圈之间具有高粘结力(一般大于35牛顿/毫米)的高性能滚轮制品。2)工艺参数改变-提高注塑温度、注塑速度、降低保压压力。传统聚氨酯注塑工艺中注塑温度通常在170-195℃之间,这样的注塑温度不足以使200-220℃快速反应型胶粘剂与聚氨酯及金属轮毂完全反应,导致聚氨酯胎圈与铝合金或钢等金属轮毂之间的粘结力不佳,则滚轮负载运行时出现脱胶,胎圈破损缺陷,导致产品质量不合格。发明人将注塑温度提高至200-210℃之间,同时为了防止热塑性聚氨酯材料在高温注射成型过程中出现烧焦、窝气缺陷,将注塑速度加快5-8%,而保压压力降低3-5%,从而使聚氨酯材料在高速注射过程中能达到200-205℃的高料温,能与快速反应型聚氨酯胶粘剂充分反应,从而提高聚氨酯胎圈与铝合金或钢等金属轮毂之间的粘结性能,并以高速注塑时较低保压压力的方式,辅助高速注塑TPU时消除窝气缺陷,保证热塑性聚氨酯胎圈质量。第四、注塑模具结构的改变。传统注塑工艺中只注塑聚氨酯胎圈的模腔结构,而本发明是将预喷好粘结剂的金属轮毂先放入注塑模腔定位、固定后合模直接注塑聚氨酯胎圈到金属轮毂粘结面,从而滚轮制品成型。第五、改进模具的进胶方式:传统注塑工艺中,聚氨酯胎圈由模腔结构一点进胶汇流成型,而在本发明中,为了使热塑聚氨酯材料在液态时以极短的时间内在注塑模具内汇流成胎圈的形状,并与金属轮毂表面的粘结剂在高温下充分反应而提高了粘结性能,将进胶方式由一点式该改进为多点或者多点扇形式进胶,从而高速汇流成型。优选地,多点扇形式进胶为均匀多点扇形式进胶。优选地,多点扇形式进胶为3-8点式进胶。多点扇形进胶既减少了注塑时间,又提高了金属轮毂与胎圈间的粘结性能。术语解释PU是指聚氨酯。TPU是指热塑性聚氨酯弹性体。MDI是指二苯基甲烷二异氰酸酯。TDI是指甲苯二异氰酸酯。附图说明图1显示了本发明工艺中的一出四注塑模具示意图,该模具具备三点扇形均匀分布胶口(1)。图2显示了注塑滚轮产品的基本结构:最外层为TPU胎圈(1),内部为金属轴承(2),金属轴承(2)与TPU胎圈(1)之间由粘结剂粘结。图3显示了本发明工艺制备的滚轮制品的性能测试结果图。发明效果相比选用热固性聚氨酯弹性体的传统浇注工艺,本发明的改进的热塑性聚氨酯弹性体注塑成型技术有以下三点优势:其一、在金属轮毂与胎圈的粘结性能方面,选用高温反应型热塑性聚氨酯弹性体经本发明注塑工艺制备的聚氨酯滚轮优于选用热固性聚氨酯弹性体经传统浇注工艺制备的滚轮;粘结力测试结果对比见表1.表1.粘结力测试结果对比其二、改进后的注塑工艺比传统浇注工艺生产效率高约4-5倍,传统浇注工艺的生产效率为110-150件/人/班(8小时);而改进后的注塑工艺的生产效率是500-650件/人/班(8小时)。其三、在材料成本上,改进后的注塑工艺比传统浇注工艺低40%;传统浇注工艺选用的热固性聚氨酯价格为50-80元/公斤,而改进后的注塑工艺选用的热塑性聚氨酯价格为30-45元/公斤。其四、改进后的注塑工艺比传统浇注工艺设备成本低。以下实施例仅仅是为了辅助理解本发明,并非因此限定本发明的范围,凡是不脱离说明书中描述的本发明精神和范围下所做任何等效助剂、工序、步骤替换或改变,或直接或间接见本发明运用在相关的技术领域,均包括在本发明专利的保护范围之内。具体实施例实施例1制备不带轴承的聚氨酯滚轮,包括以下步骤:1)、对金属轮毂的喷胶面进行预喷砂打毛作业;2)、对步骤1)得到的金属轮毂进行表面脱脂清洁作业;3)、对步骤2)得到的金属轮毂的喷胶面使用高温反应型粘结剂进行预喷胶处理;4)、将步骤3)得到的预喷胶处理的金属轮毂,在湿度≤75%下,在5-30℃环境中,初步干燥处理2-3小时;5)、将步骤4)得到的初步干燥的预喷胶处理的金属轮毂在110-120℃下,预热2-10小时;6)、将步骤5)得到的预喷好粘结剂的金属轮毂先放入注塑模腔定位、固定后合模,再使用160-260T低压注塑机将液态热塑性聚氨酯材料由浇注机螺杆射入注塑模具胶口中,胶口为多点扇形均匀分布,且进胶方式为多点胶口同时进胶,使液态热塑聚氨酯材料能在极短的时间内在注塑模具内汇流成胎圈的形状,热塑性聚氨酯材料与金属轮毂的喷胶层的粘结剂充分接触、反应约65-70秒后,从注塑模具中取出成型的滚轮制品;7)、将步骤6)得到的滚轮制品进行后熟化处理,得到聚氨酯滚轮。实施例2制备带轴承的铝合金轮毂的聚氨酯滚轮,包括以下步骤:1)、对铝合金轮毂的喷胶面使用石英砂粒进行预喷砂打毛作业;2)、使用自动水清洗机对步骤1)得到的金属轮毂进行表面脱脂清洁作业;3)、对步骤2)得到的金属轮毂的喷胶面使用牌号为英国西邦49C的高温反应型粘结剂进行预喷胶处理;4)、将步骤3)得到的预喷胶处理的金属轮毂,在湿度<75%下,在5-30℃环境中,初步干燥处理2-3小时;5)、将步骤4)得到的初步干燥的预喷胶处理的金属轮毂放入烘箱中在110-120℃下,预热2-10小时;6)、将步骤5)得到的预喷好粘结剂的金属轮毂先放入注塑模腔定位、固定后合模,通过注塑模具控制制品包胶尺寸,再使用160-260T低压注塑机将牌号为BAYERU-95的液态热塑性MDI和抗水解剂聚氨酯粒子由浇注机螺杆射入注塑模具胶口中,胶口为3点扇形均匀分布,且进胶方式为3点胶口同时进胶,使液态热塑聚氨酯材料能在极短的时间内快速均匀的灌满模腔并使聚氨酯材料快速在注塑模具内汇流成胎圈的形状,热塑性聚氨酯材料与金属轮毂的喷胶层的粘结剂充分接触、反应,胎圈注塑固化成型周期为65-80秒,注塑完成后注塑模具自动打开,操作工取出成型完毕的滚轮制品;7)、将步骤6)得到的滚轮制品取出并放入100℃烘箱进行10-16小时后熟化作业;8)、步骤7)得到的滚轮制品进行轴承装配,得到带轴承的聚氨酯滚轮。实施例3制备不带轴承的聚氨酯滚轮,包括以下步骤:1)、对金属轮毂的喷胶面进行预喷砂打毛作业;2)、对步骤1)得到的金属轮毂进行表面脱脂清洁作业;3)、对步骤2)得到的金属轮毂的喷胶面使用高温反应型粘结剂进行预喷胶处理;4)、将步骤3)得到的预喷胶处理的金属轮毂,在湿度≤75%下,在5-30℃环境中,初步干燥处理2-3小时;5)、将步骤4)得到的初步干燥的预喷胶处理的金属轮毂在110-120℃下,预热2-10小时;6)、将步骤5)得到的预喷好粘结剂的金属轮毂先放入注塑模腔定位、固定后合模,再使用160-260T低压注塑机将液态热塑性聚氨酯材料由浇注机螺杆射入注塑模具胶口中,胶口为三点扇形均匀分布,且进胶方式为三点胶口同时进胶,使液态热塑聚氨酯材料能在极短的时间内在注塑模具内汇流成胎圈的形状,热塑性聚氨酯材料与金属轮毂的喷胶层的粘结剂充分接触、反应约65-70秒后,从注塑模具中取出成型的滚轮制品;7)、将步骤6)得到的滚轮制品进行后熟化处理,得到聚氨酯滚轮。为了更好地实现注塑产品聚氨酯胎圈与金属轮毂间的大于35牛顿/毫米的高粘结力又不会出现产品胎圈烧焦、缩水严重等不良缺陷,步骤6)中的注塑工艺参数改良为分段操作参数:1、高注射温度:第一段加温温度:198℃;第二段加温温度:210℃;第三段加温温度:215℃;第四段加温温度:195℃;第五段加温温度:205℃。2、高速注射:第一段注射速度:25%速度,第二段注射速度,压力:25%;第三段注射速度,压力:20%速度。3、降低保压压力:第一段保压压力:115bar,第二段保压压力:100bar。本发明工艺制备的滚轮制品的性能测试实验测试了本发明工艺制备的滚轮制品的轮毂与聚氨酯胎圈粘结性能,测试参数为:试样1:平均力=84.2848牛顿/毫米;最小力=55.9422牛顿/毫米;最大峰力=99.6134牛顿/毫米;平均峰力=83.0508牛顿/毫米;最小峰力=55.9422牛顿/毫米;中位峰力=99.6134牛顿/毫米试样2:平均力=94.8886牛顿/毫米;最小力=56.4578牛顿/毫米;最大峰力=119.5669牛顿/毫米;平均峰力=97.7442牛顿/毫米;最小峰力=59.8091牛顿/毫米;中位峰力=100.2834牛顿/毫米试样3:平均力=96.4850牛顿/毫米;最小力=65.4809牛顿/毫米;最大峰力=121.5263牛顿/毫米;平均峰力=92.4286牛顿/毫米;最小峰力=66.4088牛顿/毫米;中位峰力=96.5197牛顿/毫米性能测试结果见图3。表2、实施例3制备的滚轮制品的轮毂与聚氨酯胎圈粘结性能测试结果被粘轮毂材料被粘聚氨酯材料粘结强度(牛顿/毫米)铝合金热塑性聚氨酯胎圈55-10045#钢热塑性聚氨酯胎圈55-100粘结力试验结果表明:制备的滚轮制品的轮毂与聚氨酯胎圈之间具备卓越的粘结性能。测试了本发明注塑工艺制备的滚轮制品的动态寿命,试验标准为:试验机转筒外径为500毫米,高性能滚轮产品必须在转速为50米/分钟,200公斤受压的环境下运行2000小时,运行后滚轮样品必须仍能正常运行,胎圈、轮毂、轴承都无损坏。表3、动态寿命试验报告:滚轮制造公司:依合斯电梯扶手(上海)有限公司使用轴承:BR62042RS胎圈材质:聚酯MDI+抗水剂95邵A硬度热塑性聚氨酯滚轮尺寸规格:外径100毫米,宽度25.0毫米生产日期:2012-6-15从表3的动态寿命试验报告表明,本发明注塑工艺制备的热塑性聚氨酯滚轮制品,其胎圈与铝合金或钢等金属轮毂具备高粘结性能;能够很好满足载重电梯的动态寿命测试。