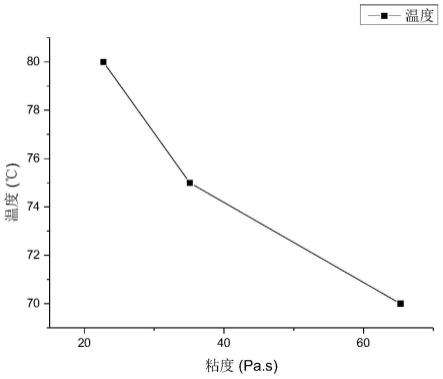
一种高粘度热固性树脂真空脱泡及浇铸体制备的方法
【技术领域】
1.本发明涉及浇铸体制备技术领域,具体的说,是一种高粘度热固性树脂真空脱泡及浇铸体制备的方法。
背景技术:2.众所周知,制备树脂浇铸体是研究树脂性能时的重要环节,而经搅拌混合后的树脂内部充满气泡,必须经过脱泡处理后才能制备浇铸体。为了在生产相关产品时得到合理的运用,应尽可能使浇铸体真实的反映树脂的性能,故在制备浇铸体时需要一种科学、严谨且操作性强的方法。
3.随着纤维增强树脂基复合材料在汽车工业、生物医学、体育器材以及航空航天领域的应用不断深入,应各种不同的应用场景,对树脂基体的性能提出了形形色色的要求。因此,研发人员会在树脂中添加各种改性组分,来提升树脂基体的性能,但是在部分改性组分的影响下,树脂基体的粘度会大幅升高,致使脱泡困难,所制备的浇铸体质量参差不齐。目前,制作高粘度浇铸体时常用的脱泡方法有:离心脱泡和真空脱泡。
4.离心脱泡是通过自转进行搅拌混合的同时围绕着中心轴进行公转,利用公转产生的离心力使树脂中的气泡排出树脂内部。离心脱泡具有无污染和操作简单等优点。但是,对于粘度稍高的树脂离心脱泡的效果并不明显,无法将高粘度树脂中的气泡全部排出。
5.真空脱泡是将树脂放置于真空箱体内,通过真空泵将箱体内空气抽出,使箱体内部呈负压状态,从而使树脂内部的气体溢出。真空脱泡具有脱泡量相比离心脱泡大,脱泡效率较高,效果也较明显等优点。但是,对于经过真空脱泡的高粘度树脂体系,其浇铸体的制备却较为困难。目前,制作浇铸体的方法主要有模具中闭模固化和敞口模具中固化。
6.模具中闭模固化的方法,是指将真空脱泡后的树脂转移至经预热的模具中,直至模具中树脂达到所需的量,且充分流平后进行闭模固化。闭模固化的优点有:固化物形状可设计性强,通常可以不经加工直接进行力学性能测试;树脂利用率高,基本没有浪费。但是高粘度树脂在转移过程中,经常会带入大量气泡,如果将模具放入真空箱内再抽真空,则会导致树脂溢出,使模腔内缺胶而无法制得预期的浇铸体,且该类模具通常为金属制造,成本较高,比较笨重,操作较为费力。
7.敞口模具中固化的方法,是指将一定量的树脂在敞口模具中进行真空脱泡,完成真空脱泡后撤去真空直接固化。该方法优点是,操作简单,可最大程度的去除树脂内部气泡。但是很难控制浇铸体的厚度和平行度,如果树脂投入少了,则厚度不能达到测试要求,如果树脂投入量过多,需用雕刻机削去过厚的部分,导致表面出现切削的痕迹(缺陷),则不能真实反映树脂性能。
8.中国专利公开号cn103692589a所述为使用低沸点溶剂对树脂进行稀释和升温进行脱出溶剂及气泡,该方法容易参入杂质,如溶剂未清除干净则无法反映树脂浇铸体的真实性能。而本技术所提供的方法是在下档板、密封条和挡流框所组成的敞口容器中进行升温脱泡,通过控制树脂的厚度和温度来达到好的脱泡效果,避免了杂质的混入。
9.中国专利公开号cn107984662a所述为使用热压罐工艺制作浇铸体,其脱泡办法为在热压罐中将树脂升温到凝胶点时,通过加压使树脂中的气泡通过导气布排出体系,该方法通过正压将树脂体系所处外环境压强变大,可能导致未能排出体系的气泡在树脂体系中体积变小,并随着树脂固化后,使树脂内部存在较大的内应力,也会影响到树脂真实性能的体现。本技术是使树脂体系处于负压环境中,使体系中气泡体积变大,获得较大的浮力,最终脱出树脂体系,我们的方法相比更有效。
10.中国专利公开号cn109483782a中所述为使用热压罐在不同的温度下多次进行加压、泄压操作,从而使树脂处于一个不稳定的外部环境中,促使树脂体系中的气泡排除,再用已调水平的模具将树脂在模具中固化,该方法明显的缺陷是无法很好的控制树脂的厚度,因为其在加压、泄压的过程中很容易导致树脂溢出。而本技术的方法是通过升温真空脱泡后,再使用限厚垫条将上下面板隔开一定距离,从而保证夹在中间的树脂厚度在预期厚度范围内。
技术实现要素:11.本发明的目的在于克服现有技术的不足,提供一种高粘度热固性树脂真空脱泡及浇铸体制备的方法。
12.本发明的目的是通过以下技术方案来实现的:
13.一种高粘度热固性树脂真空脱泡及浇铸体制备的方法,
14.a.确定树脂处理温度及时间:取树脂小样,用流变仪测量树脂的温度-粘度曲线,再用凝胶测量仪测量树脂在特定温度下的凝胶时间,综合考虑确定脱泡温度及时间,其中真空脱泡时的树脂粘度应控制在30pa.s以下,脱泡温度应在50~100℃之间,脱泡时间应控制在树脂在处理温度时的凝胶时间以内,一般为7小时以内;通过差示扫描量热仪对树脂进行热分析,确定固化制度;
15.所述高粘度树脂可以是环氧树脂、酚醛树脂、氰酸酯和双马来酰亚胺树脂中的一种或者几种的混合物。
16.b.模具准备:
17.1)涂脱模剂,将模具与树脂的所有接触面涂上脱模剂;
18.2)在光滑和平整的模板上放置挡流框,然后将密封条塞入挡流框与模板之间的间隙中;
19.3)将准备好的模具放入真空烘箱中,预热约30min;
20.c.真空脱泡:将高粘度配方树脂放入到已预热好的模具中,注意尽量使树脂块分散在模具上,通过模具表面的热传导,使树脂得到加热,而接触面的树脂由于升温较快,其粘度下降也较快,故树脂优先从下表面开始融化,融化的树脂层在流平过程中,同时在负压作用下脱泡,然后树脂完全流平,继续保持负压,直至树脂表面基本无气泡冒出,停止加热及抽真空,由于树脂流平过程中,树脂层较薄,气泡往往在体积变大的过程中就破溃而达到脱泡的目的。由于该方法实际在树脂完全流平前,已将大部分下层树脂中的气泡排出,故其脱泡效果更佳;
21.其中树脂厚度应控制在4mm以下,温度应控制在50~100℃,温度太高容易引起树脂爆聚,温度太低或者厚度太厚会导致脱泡效果较差。
22.d.树脂浇铸:将放置在模板上的挡流框撤去,然后在密封条外侧放置金属垫条(限厚),最后在上表面覆盖一块与下表面模板形状一致的光滑,平整的模板,并用夹子固定;
23.e.树脂固化:将整套模具倾斜放置于烘箱中,设置完固化温度及时间后,开始固化;固化温度可以设置在60~300℃范围内,固化时间控制在20小时以内;
24.f.脱模:将固化好的高粘度树脂浇铸体平板从模具中取出;
25.g.加工:使用磨削方式按照标准制样要求,加工样件。
26.所述的挡流框具有足够自重和高度,可以使挡流框、密封条和平板模具无缝连接,可以保证抽真空过程中树脂不溢出模具腔体。
27.与现有技术相比,本发明的积极效果是:
28.用该方法制备的高粘度树脂浇铸体平整、无气泡,能够较为真实的反映树脂性能,可提供较为可靠的数据。并且该方法具有操作简单,设备要求不高、环境无污染、样品质量批次稳定性高等优点。该方法特别适用于室温下为固态或半固态的高粘度树脂体系。
【附图说明】
29.图1高温固化环氧树脂粘-温曲线
30.图2高温固化环氧树脂t-β线性回归曲线
31.图3改性氰酸酯粘-温曲线
32.图4改性氰酸酯树脂t-β线性回归曲线
【具体实施方式】
33.以下提供本发明一种高粘度热固性树脂真空脱泡及浇铸体制备的方法的具体实施方式。
34.实施例1:
35.一种高粘度热固性树脂真空脱泡及浇铸体制备的方法,
36.a.确定树脂处理温度及时间:取树脂小样,用流变仪测量树脂的温度-粘度曲线,可得到如下图1,
37.由图1和图2可知当温度为80℃时,其粘度为22.7pa.s,再取树脂小样测试其80℃凝胶时间为2.5h,综合考虑确定脱泡温度为80℃、时间应控制在2小时以内,通过差示扫描量热仪对树脂进行热分析得到其t-β曲线(如图2所示),确定固化制度为120*2h+150*2h+180*2h;
38.所述高粘度树脂可以是环氧树脂。
39.b.模具准备:
40.1)涂脱模剂,将模具与树脂的所有接触面涂上脱模剂;
41.2)在光滑和平整的模板上放置挡流框,然后将密封条塞入挡流框与模板之间的间隙中;
42.3)将准备好的模具放入真空烘箱(烘箱升温至80℃)中,预热约30min;
43.c.真空脱泡:将高粘度配方树脂放入到已预热好的模具中,注意尽量使树脂块分散在模具上,通过模具表面的热传导,使树脂得到加热,而接触面的树脂由于升温较快,其粘度下降也较快,故树脂优先从下表面开始融化,融化的树脂层在流平过程中,同时在负压
作用下脱泡,然后树脂完全流平,继续保持负压,直至树脂表面基本无气泡冒出,停止加热及抽真空,由于树脂流平过程中,树脂层较薄,气泡往往在体积变大的过程中就破溃而达到脱泡的目的。由于该方法实际在树脂完全流平前,已将大部分下层树脂中的气泡排出,故其脱泡效果更佳;
44.其中脱完泡的树脂厚度应控制在4mm以下,温度应控制在75~85℃,温度太高容易引起树脂爆聚,温度太低或者厚度太厚会导致脱泡效果较差。
45.d.树脂浇铸:将放置在模板上的挡流框撤去,然后在密封条外侧放置金属垫条(限厚),最后在上表面覆盖一块与下表面模板形状一致的光滑,平整的模板,并用夹子固定;
46.e.树脂固化:将整套模具倾斜(与烘箱下表面呈60
°
倾斜)放置于烘箱中,设置完固化温度及时间后,开始固化;固化制度设置为120*2h+150*2h+180*2h;
47.f.脱模:将固化好的高粘度树脂浇铸体平板从模具中取出;
48.g.加工:使用磨削方式按照标准制样要求,加工样件。
49.所述的挡流框重500g,高度为10cm,可以使挡流框、密封条和平板模具无缝连接,可以保证抽真空过程中树脂不溢出模具腔体。
50.实施例2
51.一种高粘度热固性树脂真空脱泡及浇铸体制备的方法,
52.b.确定树脂处理温度及时间:取树脂小样,用流变仪测量树脂的温度-粘度曲线,
53.由图3以及图4可知当温度为100℃时,其粘度为19.2pa.s,再取树脂小样测试其100℃凝胶时间为3.5h,综合考虑确定脱泡温度为100℃、时间应控制在3小时以内,通过差示扫描量热仪对树脂进行热分析得到其t-β曲线(如图2所示),确定固化制度为150*2h+180*2h+260*2h;
54.所述高粘度树脂可以是氰酸酯树脂。
55.b.模具准备:
56.1)涂脱模剂,将模具与树脂的所有接触面涂上脱模剂;
57.2)在光滑和平整的模板上放置挡流框,然后将密封条塞入挡流框与模板之间的间隙中;
58.3)将准备好的模具放入真空烘箱(烘箱升温至100℃)中,预热约30min;
59.c.真空脱泡:将高粘度配方树脂放入到已预热好的模具中,注意尽量使树脂块分散在模具上,通过模具表面的热传导,使树脂得到加热,而接触面的树脂由于升温较快,其粘度下降也较快,故树脂优先从下表面开始融化,融化的树脂层在流平过程中,同时在负压作用下脱泡,然后树脂完全流平,继续保持负压,直至树脂表面基本无气泡冒出,停止加热及抽真空,由于树脂流平过程中,树脂层较薄,气泡往往在体积变大的过程中就破溃而达到脱泡的目的。由于该方法实际在树脂完全流平前,已将大部分下层树脂中的气泡排出,故其脱泡效果更佳;
60.其中脱完泡的树脂厚度应控制在4mm以下,温度应控制在95~105℃,温度太高容易引起树脂爆聚,温度太低或者厚度太厚会导致脱泡效果较差。
61.d.树脂浇铸:将放置在模板上的挡流框撤去,然后在密封条外侧放置金属垫条(限厚),最后在上表面覆盖一块与下表面模板形状一致的光滑,平整的模板,并用夹子固定;
62.e.树脂固化:将整套模具倾斜(与烘箱下表面呈60
°
倾斜)放置于烘箱中,设置完固
化温度及时间后,开始固化;固化制度设置为150*2h+180*2h+260*2h;
63.f.脱模:将固化好的高粘度树脂浇铸体平板从模具中取出;
64.g.加工:使用磨削方式按照标准制样要求,加工样件。
65.所述的挡流框重600g,高度为12cm,可以使挡流框、密封条和平板模具无缝连接,可以保证抽真空过程中树脂不溢出模具腔体。
66.以上所述仅是本发明的优选实施方式,应当指出,对于本技术领域的普通技术人员,在不脱离本发明构思的前提下,还可以做出若干改进和润饰,这些改进和润饰也应视为本发明的保护范围内。