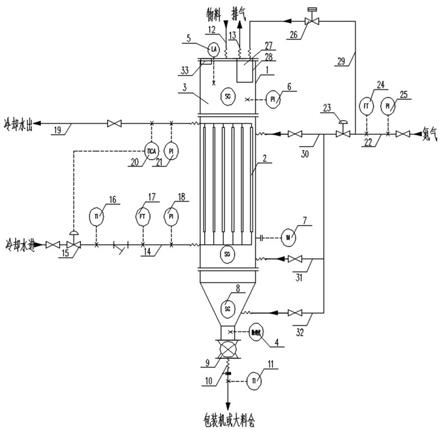
[0001]
本申请属于化工生产冷却设备技术领域,具体涉及一种高通量固体颗粒或粉尘的冷却装置。
背景技术:[0002]
在固体物料生产过程中,固体颗粒或粉末会携带大量热量,如不经处理会引起热量累积,造成产品保存时间缩短或变质腐坏、设备老化甚至起火等严重问题。因而,针对固体颗粒或粉末生产有一些专用的冷却设备或冷却塔,但是目前常用的针对固体物料生产的工业冷却塔普遍存在冷却效率低、处理量较小的问题,在一定程度上限制了生产规模的扩大。
[0003]
专利cn207540395u公开了一种固性粉末快速冷却装置,所述装置包括固定底座、气瓶、储水池、冷却主体、三角支架、出粉口、进水管、水泵、冷却水管、喷气板、进气管、密封板、密封罩、控制阀、进粉口、回水管、出气管、气泵、排气口和喷气管,当固体粉末由进粉口进入冷却主体内,经喷气管的气体降温,同时固性粉末在接触冷却水管时,对固性粉末有一定的冷却效果,通过气体冷却和液体冷却相结合的方式,冷却速度快、冷却效果好,使用方便。但是该装置中冷却水管为盘管结构,固性粉末容易附着在盘管上造成物料堆积,当物料堆积到一定程度就会严重影响冷却效果;而且该装置中没有实时监测系统,冷却水管的降温效果、管内压力等均无法获得,因而该装置并不适用于产业化固体物料的冷却。
技术实现要素:[0004]
为了解决上述技术问题,本申请的目的是提出一种高通量固体颗粒或粉尘的冷却装置,从而提供一种适用于产业化生产、冷却效果好的固体物料冷却装置。
[0005]
为了实现上述技术问题,本申请采用以下技术方案:
[0006]
一种高通量固体颗粒或粉尘的冷却装置,所述装置包括壳体、冷却组件和气体循环组件;
[0007]
所述壳体底部呈漏斗结构,壳体内部为中空的冷却腔;壳体的顶部设有进料管,壳体漏斗结构的底端设有出料管,进料管和出料管与壳体内部连通;
[0008]
所述冷却组件包括进水管、板式换热器和设于进水管上方出水管;所述进水管的一端与外部水源连通,进水管的另一端穿过壳体与位于冷却腔内的板式换热器相通;进水管上设有进水阀;所述板式换热器包括若干竖直设置的囊状换热夹层,所述囊状换热夹层的底端与进水管连通,囊状换热夹层的顶端与出水管连通;相邻囊状换热夹层之间形成固体颗粒或粉尘通过的通道;
[0009]
所述气体循环组件包括进气管线、排气管线、过滤除尘器和反吹管线;所述进气管线上设有进气阀;进气管线的一端与外部气源连接,进气管线另一端与壳体相连;壳体与进气管线的连接处设有进气口;所述排气管线位于壳体上部,壳体与排气管线的连接处设有排气口,排气口的位置高于进气口的位置;所述过滤除尘器位于排气口处,冷却腔内气体通
过过滤除尘器经排气口排出装置;所述反吹管线一端与外部气源连接,反吹管线的另一端与过滤除尘器连接;反吹管线上设置有脉冲阀门。
[0010]
优选的,所述囊状换热夹层由两层金属板围合焊接而成,两层金属板之间中空形成水流通道;所述囊状换热夹层的厚度为5~10mm;相邻囊状换热夹层之间的距离50~100mm。
[0011]
进一步优选的,所述囊状换热夹层的表面光洁度ra≤0.6μm。
[0012]
优选的,所述进气管线包括上进气管、中进气管和下进气管;上进气管、中进气管和下进气管与壳体的连接处分别设置上进气口、中进气口和下进气口;所述上进气口的位置低于囊状换热夹层的顶部;所述下进气口位于壳体漏斗结构的侧壁;所述中进气口位于上进气口和下进气口之间。通过三组进气管的设置为装置内物料提供反重力的作用力,既能延长物料在囊状换热夹层区域的停留时间提高冷却效果,又能保证装置内物料的充分流动,避免物料附着在囊状换热夹层表面。
[0013]
优选的,所述过滤除尘器位于冷却腔顶部并与冷却腔顶部的壳体固定连接;反吹管线的一端与过滤除尘器顶部的壳体连接,反吹管线与壳体的连接处设有反吹进气口;反吹管线的另一端与进气管线连接;进气管线上的进气阀设于反吹管线与进气管线连接处的近壳体段。将反吹管线与进气管线连接,并定期开启脉冲阀门,既能实现对过滤除尘器定期反吹,避免滤网阻塞造成装置内压力过大,保证过滤除尘器的正常运行,又避免气体耗损,节约气体使用量。
[0014]
优选的,所述冷却装置上设有若干检测组件;所述检测组件包括温度计、压力表、料位检测器和重量检测器;所述温度计包括检测进水温度的进水温度计、检测出水温度的出水温度计以及检测出料温度的出料温度计;所述料位检测器固定于壳体顶部,且料位检测器的检测端伸入冷却腔内;所述重量检测器位于壳体的下部。
[0015]
优选的,所述装置上还设有爆破膜;爆破膜的爆破压力小于壳体的最大承压。当装置内压力过大时,气体冲开爆破膜得到释放,保证生产安全。
[0016]
优选的,所述壳体侧壁开设有可视窗。可视窗可设置于壳体的不同位置,通过可视窗能够实时观察壳体冷却腔内物料的流动循环状态。
[0017]
本申请的有益效果为:
[0018]
1)在冷却腔内设置若干具有特定结构的囊状换热夹层,该囊状换热夹层换热面积大,表面光洁度高,既能对装置内固体物料进行充分冷却,又能避免物料在换热器上附着粘接;相邻囊状换热夹层之间的距离经过特定设计,在充分保证冷却效率的同时,进一步避免物料粘接形成搭桥而无法掉落的问题;
[0019]
2)设置了一组或多组进气管,为装置内物料提供反重力的作用力,既能延长物料在囊状换热夹层区域的停留时间提高冷却效果,又能保证装置内物料的充分流动。为了避免排气口处过滤除尘器效率下降,本申请在除尘过滤器上连接反吹管线,通过定期开启脉冲阀门,对过滤除尘器的过滤网形成定期反吹,避免过滤网被阻塞造成装置内压力过大,保证过滤除尘器的正常运行;
[0020]
3)本申请通过冷却组件和气体循环组件的组合设计使该装置适用大批量固体颗粒或粉尘的冷却处理;另外,通过在线检测组件的实时监测,以及在线检测组件与各阀门之间的连接配合,能有效提高装置整体的控制性和操作精度,产业化水平高。
附图说明
[0021]
图1 本申请的结构示意图。
[0022]
图中,1、壳体,2、囊状换热夹层,3、冷却腔,4、除铁仪,5、料位检测器,6、总压力表,7、重量检测器,8、可视窗,9、星型下料阀,10、出料管,11、出料温度计,12、进料管,13、排气管线,14、进水管,15、进水阀,16、进水温度计,17、进水流量计,18、进水压力表,19、出水管,20、出水温度计,21、出水压力表,22、总进气管线,23、进气阀,24、进气流量计,25、进气压力表,26、脉冲电磁阀,27、布袋除尘器,28、支撑架,29、反吹管线,30、上进气管,31、中进气管,32、下进气管,33、爆破膜。
具体实施方式
[0023]
以下结合具体实施方式对本申请作进一步的详细描述。需要说明的是,实施例中所述“上”、“下”、“左”、“右”、“内”、“外”等用语,仅为阐明各结构的相对位置关系,而非用以限定本申请可实施的范围,其相对关系的改变或调整,在无实质变更技术内容下,当亦视为本申请可实施的范畴。
[0024]
实施例1
[0025]
一种高通量固体颗粒或粉尘的冷却装置,如图1所示,包括壳体1、冷却组件、气体循环组件和在线检测组件;
[0026]
所述壳体1底部呈漏斗结构,壳体1内部为中空的冷却腔3;壳体1的顶部设有进料管12,进料管12与冷却腔3连通;壳体1漏斗结构的底部设有出料管10,出料管10与壳体1的连接处设有星型下料阀9,并在星型下料阀9附近设置出料温度计11。
[0027]
所述冷却组件包括进水管14、板式换热器和设于进水管14上方出水管19;
[0028]
所述进水管14的一端与外部水源连通,进水管14的另一端穿过壳体1与位于冷却腔3内的板式换热器相通;所述进水管14位于壳体1外侧段设有进水阀15、进水温度计16、进水流量计17和进水压力表18;进水管14伸入壳体1的内侧段通过螺栓与设于壳体1内壁的固定座固定连接;
[0029]
所述板式换热器包括若干竖直设置的囊状换热夹层2,相邻囊状换热夹层2之间形成固体颗粒或粉尘通过的通道;为了保证物料通过且不粘接成桥,相邻囊状换热夹层2之间的距离约为80mm。囊状换热夹层2由两层不锈钢板围合焊接而成,两层不锈钢板材之间中空,形成水流通道。囊状换热夹层2的厚度约8mm,较薄的换热板厚度可以减轻换热器整体的重量,保证换热面积尽可能大,从而保证换热效果。为了防止待冷却物料在囊状换热夹层2表面附着,囊状换热夹层2的两端呈尖形,并在囊状换热夹层2的表面进行抛光处理,其光洁度ra≤0.6μm。囊状换热夹层2的底端通过连接管与进水管14连通,囊状换热夹层2的顶端通过连接管与出水管19连通。
[0030]
所述出水管19位于壳体1中的内侧段通过螺栓与设于壳体1内壁的固定座固定连接;出水管19位于壳体1外侧的外侧段上设有出水温度计20和出水压力表21,根据进出水温度差和进、出水压力情况可以综合判断囊状换热夹层2中是否出现结垢情况。为了进一步提高装置整体控制的精确度和智能化,该冷却塔通过plc控制器进行操控;出水温度计20和进水阀15通过plc控制器电性连接,从而实现出水温度计20对进水阀15的调节控制;上述进水温度计16、进水流量计17、进水压力表18和出水压力表21也与plc控制器电性连接,从而实
现对装置运行中各检测器的实时在线检测;所述检测器与plc的连接方式采用本领域常规方法即可,由于不属于本申请的特定技术特征,故不再赘述。出水管19远离壳体1的端部连接有热交换器,出水管19内冷却水经过热交换器降温后进入进水管14,实现冷却水的循环利用。
[0031]
所述气体循环组件包括进气管线、排气管线、过滤除尘器和反吹管线;
[0032]
所述进气管线包括总进气管22、上进气管30、中进气管31和下进气管32;总进气管22的一端与外部气源连接,总进气管22的另一端分别与上进气管30、中进气管31和下进气管32连通;总进气管22上设有进气阀23。上进气管30、中进气管31和下进气管32的非总进气管22连接端(即远离总进气管22的端部)与壳体相连;壳体对应上进气管30、中进气管31和下进气管32的位置分别设有上进气口、中进气口和下进气口;所述上进气口的位置低于囊状换热夹层2的顶部;所述下进气口位于壳体1漏斗结构的侧壁;所述中进气口位于上进气口和下进气口之间。通过设置三组进气管能够为装置内物料提供反重力的作用力,既能延长物料在囊状换热夹层区域的停留时间提高冷却效果,又能保证装置内物料的充分流动,避免物料附着在囊状换热夹层2表面;上进气管30、中进气管31和下进气管32上均设有手动阀门。需要说明的是,上进气管30、中进气管31和下进气管32可以位于壳体同侧,也可分设于壳体的不同侧面,为了保证冷却腔内物料的充分流动,在壳体同一水平面的不同位置可设置多个进气管;
[0033]
所述排气管线13位于壳体1顶部,壳体1与排气管线13的连接处设有排气口,排气口的位置高于上进气口的位置;排气口处设置布袋式除尘器27,冷却腔3内气体通过布袋式除尘器27经排气口排出装置;所述布袋式除尘器27包括支撑架28和过滤网;支撑架28与冷却腔3顶部的壳体1固定连接;过滤网通过绳索与支撑架28可拆卸连接。布袋除尘器27顶部的壳体1上设置反吹管线29,反吹管线29与壳体1的连接处设有反吹进气口;
[0034]
在本实施例中,反吹管线29远离壳体1的端部与总进气管22相连,从而通过一个气源实现进气与反吹进气的双线进气。反吹管线29与总进气管22的连接处位于进气阀23的远壳体1端,同时在反吹管线29上设置脉冲电磁阀26。将反吹管线29与总进气管22连接,并定期开启脉冲阀门26,既能对布袋除尘器27的过滤网形成定期反吹,避免滤网阻塞造成装置内压力过大,保证布袋除尘器27的正常运行,又避免气体耗损,节约气体使用量。
[0035]
除了上述压力表、流量计和温度计,该冷却塔中的在线检测组件还包括位于壳体1顶部的料位检测器5和位于壳体1下部的重量检测器7;料位检测器5固定于壳体1顶部,且料位检测器5的检测端伸入冷却腔3内,通过料位检测器5可获知冷却腔3中的物料高度,避免物料堆积造成设备运行异常;而重量检测器7可实时监测物料的通过量。
[0036]
为了提高装置整体的安全性,壳体1的顶部设有爆破膜33,爆破膜33的爆破压力小于壳体1所能承受的最大压力;当冷却腔3中气压超过爆破膜33的爆破压力,气体冲开爆破膜33得到释放,保证冷却装置的安全。
[0037]
壳体1侧壁的上部、中部和下部分别开设有可视窗8,通过可视窗8能够实时观察装置内物料的流动循环状态。为了避免出料中携带因设备、管道磨损所产生的铁屑,星型下料阀9上方设有除铁仪4。
[0038]
本实施例中为了保证冷却效果并避免物料氧化返潮,所用气源为氮气;冷却装置使用前,首先开启进水管14和出水管19上的总阀门,同时调节进水阀15,启动冷却水循环;
然后打开进气阀23、脉冲电磁阀26以及上进气管30、中进气管31和下进气管32上的手动阀门,开启气体循环;最后打开进料调节阀和星型下料阀9,物料进入冷却腔开始冷却。为了避免排气口处产生扬尘,在排气管线13上设置负压风机(图中未画出),使排气口保持微负压状态,从而减少物料溢出避免耗损,保证生产环境安全、卫生;经囊状换热夹层2充分降温后的物料由星型下料阀9经出料管进入后续程序的包装机或大料仓。
[0039]
实施例2
[0040]
为了确定囊状换热夹层的厚度,以及囊状换热夹层之间合适的安装距离,发明人针对囊状换热夹层进行了若干实验性测试:
[0041]
冷却装置设计尺寸为1600mm*1200mm*6500mm;进料温度60℃,物料含水率0.25%;设定进料量为10t/h,不同囊状换热夹层的厚度及囊间距条件下,物料的出料温度及出料含水率测定结果见表1。
[0042]
表1 不同厚度与囊间距条件下物料出料温度与含水率对比
[0043]
。
[0044]
从上表可以看出,囊状换热夹层的厚度与进出物料的温差呈正比,说明囊状换热夹层的厚度越大,降温效果更好;但是囊状换热夹层的厚度过大容易导致冷却组件整体的重量过大,不易安装和固定;而且厚度过大意味着囊状换热夹层内的空间变大,容易发生形变,因此5~10mm是本申请囊状换热夹层较适宜的厚度。
[0045]
从囊状换热夹层的间距可以看出,间距过小或过大,物料的冷却效果均不理想,另外,申请人发现,在囊状换热夹层之间间距为3mm的情况下,进料一段时间后物料容易在相邻囊状换热夹层的表面附着,进而搭接成桥,造成物料下降通道堵塞,影响出料率和降温效果,间隔距离50~100mm是本申请囊状换热夹层较为合适的安装距离。