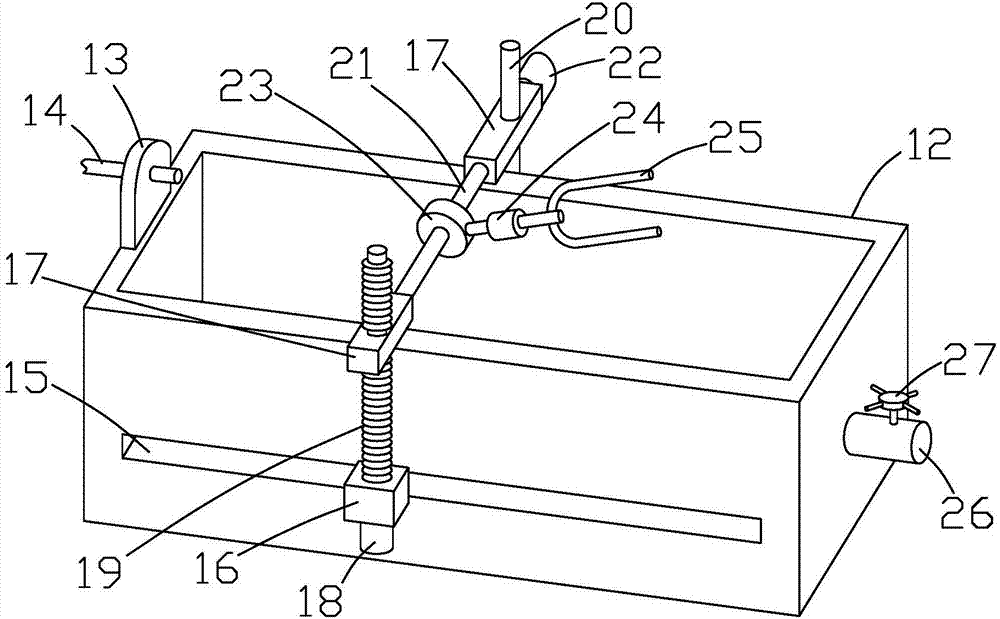
本发明涉及一种叠螺式污泥浓缩系统及其浓缩方法。
背景技术:
:污泥处理是对污泥进行浓缩、调质、脱水、稳定、干化或焚烧等减量化、稳定化、无害化的加工过程。随着环保力度的加强和人们对已有污泥处理处置技术局限性的进一步认识,污泥处理技术得到较快的发展。但是现有技术中的污泥处理设备占地面积较大,单位处理量有限,因此降低了污泥的处理效率,而且容易造成管路的堵塞,影响污泥处理的正常运行。技术实现要素:本发明目的在于针对现有技术所存在的不足而提供一种叠螺式污泥浓缩系统及其浓缩方法的技术方案,本发明的浓缩方法步骤简单,处理速度快、效果好,从根本上消除了堵塞的可能,减小了整个处理工艺的建设规模,减少了运行和维修管理成本,在全自动连续运行条件下,实现高效絮凝,连续完成污泥浓缩脱水工作。为了解决上述技术问题,本发明采用如下技术方案:一种叠螺式污泥浓缩系统,其特征在于:包括污泥池、絮凝混合槽、叠螺式浓缩机、第一自动泡药装置和第二自动泡药装置,污泥池通过切碎机连接絮凝混合槽,絮凝混合槽包括第一絮凝混合槽和第二絮凝混合槽,第一絮凝混合槽和第二絮凝混合槽分别连接第一自动泡药装置和第二自动泡药装置,第一自动泡药装置与第一絮凝混合槽之间、第二自动泡药装置和第二絮凝混合槽之间均设置有加药泵,第二絮凝混合槽连接叠螺式浓缩机,叠螺式浓缩机连接泥饼收集池,叠螺式浓缩机分别连接第一絮凝混合池和原水池,原水池通过输送泵连接污泥池;通过将切碎机连接在污泥池与絮凝混合槽之间,可以有效地将污泥中较大直径颗粒的杂质进行切碎,防止对管道造成堵塞,同时减小了颗粒杂质对叠螺式浓缩机的影响,延长了整个浓缩系统的使用寿命,二次加药絮凝的设计,可以有效提高污泥的絮凝效果,加速污泥在絮凝混合槽中的沉淀,提高了污泥浓缩脱水的效率,同时可以增大污泥的处理量。进一步,第一絮凝混合槽和第二絮凝混合槽均包括槽体,槽体的左侧顶端设置有支撑板,支撑板上固定有输泥管,槽体的右侧端面上设置有出料管,出料管上设置有第一阀门,槽体的前后两侧对称设置有滑槽,滑槽上移动连接有搅拌装置,通过将输泥管固定在支撑板上,可以实现稳定连续地输送污泥,经絮凝后的污泥可以经出料管排出,第一阀门用于控制污泥的流出速度。进一步,搅拌装置包括升降机构和搅拌机构,升降机构包括滑块、悬臂、丝杆和第一电机,滑块移动连接在滑槽上,悬臂位于滑块的上方,第一电机固定连接在滑块的底端,滑块通过丝杆连接一个悬臂,另一个悬臂通过导向杆连接滑块,两个悬臂之间通过转轴连接,转轴的端部连接有第二电机,第二电机固定连接在悬臂的端部,搅拌机构可以在升降机构的作用下左右移动,对槽体内部的污泥和药物搅拌均匀,加速污泥的沉淀,第一电机带动丝杆旋转,进而调节悬臂的高度位置,对搅拌机构进行高度调节,第二电机通过转轴带动搅拌机构旋转,对搅拌机构的搅拌角度进行调节。进一步,搅拌机构包括搅拌桨、第三电机和定位块,第三电机固定连接定位块,搅拌桨转动连接在第三电机上,第三电机随定位块转动,同时带动搅拌桨旋转,对槽体内部的污泥进行搅拌。进一步,叠螺式浓缩机包括机体和第四电机,机体内平行设置有两个螺杆,螺杆的顶端均设置有从动齿轮,第四电机位于机体的上方,第四电机上连接有主动齿轮,主动齿轮与从动齿轮相互啮合,机体的顶端侧面上设置有进料斗,机体的底端两侧分别设置有固体排泄管和液体输出管,液体输出管上设置有第二阀门,机体的外侧面上设置有支架,通过第四电机带动两个螺杆同时旋转,在消耗电能相等的情况下提高了污泥浓缩脱水的效率,与现有技术中单个转鼓的设计相比脱水浓缩效果更显著,浓缩后的液体从液体输出管流出,而固体则通过固体排泄管排入泥饼收集槽中,便于统一回收利用。进一步,机体的内侧面上设置有耐磨层,耐磨层有效提高了机体强度,减少磨损,延长了叠螺式浓缩机的使用寿命。进一步,液体输出管上设置有过滤网,过滤网可以有效防止浓缩后的污泥进入液体输送管而造成堵塞。如上述的一种叠螺式污泥浓缩系统的浓缩方法,其特征在于包括如下步骤:1)污泥拌合与切碎a、首先将未经处理的污泥输送至污泥池中,同时通入原水池中的水进行拌合稀释,在拌合过程中将颗粒直径大于25~30mm的杂质通过过滤网去除;b、然后将经过滤后的污泥通过输送管输送至切碎机,控制切碎机的转速在180r/min~255r/min;2)药剂絮凝a、将切碎后的污泥通过输泥管输送至第一絮凝混合槽中,同时打开第一自动泡药装置,加药泵将第一自动泡药装置中的药剂以1.2~1.8l/min的速度输送至第一絮凝混合槽中,然后通过第一电机带动丝杆转动,使悬臂带动搅拌机构移动至距离第一絮凝混合槽上方0.5m处,接着启动第二电机,使转轴带动搅拌机构旋转,直至搅拌机构竖直向下,再启动第三电机,使搅拌桨旋转,在第一电机控制搅拌机构上下移动的过程中,通过滑块沿着滑槽来回移动,使搅拌桨对第一絮凝混合槽中的污泥与药剂搅拌均匀;b、待第一絮凝混合槽中的搅拌时间达到10~15min后,打开出料管上的第一阀门,使第一絮凝混合槽中的污泥输送至第二絮凝混合槽中,并打开第二自动泡药装置,加药泵将第二自动泡药装置中的药剂以1.5~2.0l/min的速度输送至第二絮凝混合槽中,然后通过第一电机带动丝杆转动,使悬臂带动搅拌机构移动至距离第二絮凝混合槽上方0.5m处,接着启动第二电机,使转轴带动搅拌机构旋转,直至搅拌机构竖直向下,再启动第三电机,使搅拌桨旋转,在第一电机控制搅拌机构上下移动的过程中,通过滑块沿着滑槽来回移动,使搅拌桨对第二絮凝混合槽中的污泥与药剂搅拌均匀;c、经二次加药絮凝后的污泥输送至叠螺式浓缩机中;3)浓缩脱水a、加药絮凝后的污泥通过进料斗进入叠螺式浓缩机中,启动第四电机,使主动齿轮带动从动齿轮旋转,进而带动叠螺式浓缩机内部的两个螺杆旋转,污泥在自重的作用下向下掉落,同时两个螺杆将外围的污泥带入螺杆之间,增大污泥之间的挤压力,实现污泥的挤压浓缩脱水,污泥中的水分则沿着机体的内壁向下流动,经液体输出管分流至第一絮凝混合槽和原水池中;b、污泥加压至机体的底部后,在螺杆的作用下从固体排泄管将泥饼排出,防止对液体输出管造成堵塞。本发明由于采用了上述技术方案,具有以下有益效果:1、通过将切碎机连接在污泥池与絮凝混合槽之间,可以有效地将污泥中较大直径颗粒的杂质进行切碎,防止对管道造成堵塞,同时减小了颗粒杂质对叠螺式浓缩机的影响,延长了整个浓缩系统的使用寿命;2、二次加药絮凝的设计,可以有效提高污泥的絮凝效果,加速污泥在絮凝混合槽中的沉淀,提高了污泥浓缩脱水的效率,同时可以增大污泥的处理量;3、通过第四电机带动两个螺杆同时旋转,在消耗电能相等的情况下提高了污泥浓缩脱水的效率,与现有技术中单个转鼓的设计相比脱水浓缩效果更显著,浓缩后的液体从液体输出管流出,而固体则通过固体排泄管排入泥饼收集槽中,便于统一回收利用;4、本发明的浓缩方法步骤简单,处理速度快、效果好,从根本上消除了堵塞的可能,减小了整个处理工艺的建设规模,减少了运行和维修管理成本,在全自动连续运行条件下,实现高效絮凝,连续完成污泥浓缩脱水工作,该工艺运行稳定、效果好,克服了带式脱水机、框板式压滤机易堵塞、耗电量大灯缺点,最大限度地满足了污泥无害化、减量化、资源化处理的需求。附图说明下面结合附图对本发明作进一步说明:图1为本发明一种叠螺式污泥浓缩系统及其浓缩方法中浓缩系统的流程图;图2为本发明中第一絮凝混合槽和第二絮凝混合槽的结构示意图;图3为本发明中叠螺式浓缩机的结构示意图。图中:1-污泥池;2-切碎机;3-第一絮凝混合槽;4-第二絮凝混合槽;5-叠螺式浓缩机;6-泥饼收集池;7-第一自动泡药装置;8-第二自动泡药装置;9-原水池;10-输送泵;11-加药泵;12-槽体;13-支撑板;14-输泥管;15-滑槽;16-滑块;17-悬臂;18-第一电机;19-丝杆;20-导向杆;21-转轴;22-第二电机;23-定位块;24-第三电机;25-搅拌桨;26-出料管;27-第一阀门;28-机体;29-耐磨层;30-支架;31-进料斗;32-螺杆;33-第四电机;34-主动齿轮;35-从动齿轮;36-固体排泄管;37-液体输出管;38-第二阀门;39-过滤网。具体实施方式如图1至图3所示,为本发明一种叠螺式污泥浓缩系统,包括污泥池1、絮凝混合槽、叠螺式浓缩机5、第一自动泡药装置7和第二自动泡药装置8,污泥池1通过切碎机2连接絮凝混合槽,絮凝混合槽包括第一絮凝混合槽3和第二絮凝混合槽4,第一絮凝混合槽3和第二絮凝混合槽4分别连接第一自动泡药装置7和第二自动泡药装置8,第一絮凝混合槽3和第二絮凝混合槽4均包括槽体12,槽体12的左侧顶端设置有支撑板13,支撑板13上固定有输泥管14,槽体12的右侧端面上设置有出料管26,出料管26上设置有第一阀门27,槽体12的前后两侧对称设置有滑槽15,滑槽15上移动连接有搅拌装置,通过将输泥管14固定在支撑板13上,可以实现稳定连续地输送污泥,经絮凝后的污泥可以经出料管26排出,第一阀门27用于控制污泥的流出速度,搅拌装置包括升降机构和搅拌机构,升降机构包括滑块16、悬臂17、丝杆19和第一电机18,滑块16移动连接在滑槽15上,悬臂17位于滑块16的上方,第一电机18固定连接在滑块16的底端,滑块16通过丝杆19连接一个悬臂17,另一个悬臂17通过导向杆20连接滑块16,两个悬臂17之间通过转轴21连接,转轴21的端部连接有第二电机22,第二电机22固定连接在悬臂17的端部,搅拌机构可以在升降机构的作用下左右移动,对槽体12内部的污泥和药物搅拌均匀,加速污泥的沉淀,第一电机18带动丝杆19旋转,进而调节悬臂17的高度位置,对搅拌机构进行高度调节,第二电机22通过转轴21带动搅拌机构旋转,对搅拌机构的搅拌角度进行调节,搅拌机构包括搅拌桨25、第三电机24和定位块23,第三电机24固定连接定位块23,搅拌桨25转动连接在第三电机24上,第三电机24随定位块23转动,同时带动搅拌桨25旋转,对槽体12内部的污泥进行搅拌。第一自动泡药装置7与第一絮凝混合槽3之间、第二自动泡药装置8和第二絮凝混合槽4之间均设置有加药泵11,第二絮凝混合槽4连接叠螺式浓缩机5,叠螺式浓缩机5连接泥饼收集池6,叠螺式浓缩机5包括机体28和第四电机33,机体28内平行设置有两个螺杆32,螺杆32的顶端均设置有从动齿轮35,第四电机33位于机体28的上方,第四电机33上连接有主动齿轮34,主动齿轮34与从动齿轮35相互啮合,机体28的顶端侧面上设置有进料斗31,机体28的底端两侧分别设置有固体排泄管36和液体输出管37,液体输出管37上设置有第二阀门38,机体28的外侧面上设置有支架30,通过第四电机33带动两个螺杆32同时旋转,在消耗电能相等的情况下提高了污泥浓缩脱水的效率,与现有技术中单个转鼓的设计相比脱水浓缩效果更显著,浓缩后的液体从液体输出管37流出,而固体则通过固体排泄管36排入泥饼收集槽中,便于统一回收利用,机体28的内侧面上设置有耐磨层29,耐磨层29有效提高了机体28强度,减少磨损,延长了叠螺式浓缩机5的使用寿命,液体输出管37上设置有过滤网39,过滤网39可以有效防止浓缩后的污泥进入液体输送管而造成堵塞,叠螺式浓缩机5分别连接第一絮凝混合池和原水池9,原水池9通过输送泵10连接污泥池1;通过将切碎机2连接在污泥池1与絮凝混合槽之间,可以有效地将污泥中较大直径颗粒的杂质进行切碎,防止对管道造成堵塞,同时减小了颗粒杂质对叠螺式浓缩机5的影响,延长了整个浓缩系统的使用寿命,二次加药絮凝的设计,可以有效提高污泥的絮凝效果,加速污泥在絮凝混合槽中的沉淀,提高了污泥浓缩脱水的效率,同时可以增大污泥的处理量。如上述的一种叠螺式污泥浓缩系统的浓缩方法,包括如下步骤:1)污泥拌合与切碎a、首先将未经处理的污泥输送至污泥池1中,同时通入原水池9中的水进行拌合稀释,在拌合过程中将颗粒直径大于25~30mm的杂质通过过滤网去除;b、然后将经过滤后的污泥通过输送管输送至切碎机2,控制切碎机2的转速在180r/min~255r/min;2)药剂絮凝a、将切碎后的污泥通过输泥管14输送至第一絮凝混合槽3中,同时打开第一自动泡药装置7,加药泵11将第一自动泡药装置7中的药剂以1.2~1.8l/min的速度输送至第一絮凝混合槽3中,然后通过第一电机18带动丝杆19转动,使悬臂17带动搅拌机构移动至距离第一絮凝混合槽3上方0.5m处,接着启动第二电机22,使转轴21带动搅拌机构旋转,直至搅拌机构竖直向下,再启动第三电机24,使搅拌桨25旋转,在第一电机18控制搅拌机构上下移动的过程中,通过滑块16沿着滑槽15来回移动,使搅拌桨25对第一絮凝混合槽3中的污泥与药剂搅拌均匀;b、待第一絮凝混合槽3中的搅拌时间达到10~15min后,打开出料管26上的第一阀门27,使第一絮凝混合槽3中的污泥输送至第二絮凝混合槽4中,并打开第二自动泡药装置8,加药泵11将第二自动泡药装置8中的药剂以1.5~2.0l/min的速度输送至第二絮凝混合槽4中,然后通过第一电机18带动丝杆19转动,使悬臂17带动搅拌机构移动至距离第二絮凝混合槽4上方0.5m处,接着启动第二电机22,使转轴21带动搅拌机构旋转,直至搅拌机构竖直向下,再启动第三电机24,使搅拌桨25旋转,在第一电机18控制搅拌机构上下移动的过程中,通过滑块16沿着滑槽15来回移动,使搅拌桨25对第二絮凝混合槽4中的污泥与药剂搅拌均匀;c、经二次加药絮凝后的污泥输送至叠螺式浓缩机5中;3)浓缩脱水a、加药絮凝后的污泥通过进料斗31进入叠螺式浓缩机5中(叠螺式浓缩机与离心脱水机技术对比如表1所示),启动第四电机33,使主动齿轮34带动从动齿轮35旋转,进而带动叠螺式浓缩机5内部的两个螺杆32旋转,污泥在自重的作用下向下掉落,同时两个螺杆32将外围的污泥带入螺杆32之间,增大污泥之间的挤压力,实现污泥的挤压浓缩脱水,污泥中的水分则沿着机体28的内壁向下流动,经液体输出管37分流至第一絮凝混合槽3和原水池9中;b、污泥加压至机体28的底部后,在螺杆32的作用下从固体排泄管36将泥饼排出,防止对液体输出管37造成堵塞。对比项目叠螺式浓缩机离心脱水机耗电量非常少大污泥浓缩池不需要需要清洗冲淋水用量非常少小运转噪声、震动小大泥饼含水率≤45%≥80%污泥处理率≥95%80~90%表1叠螺式浓缩机与离心脱水机技术对比以上仅为本发明的具体实施例,但本发明的技术特征并不局限于此。任何以本发明为基础,为实现基本相同的技术效果,所作出地简单变化、等同替换或者修饰等,皆涵盖于本发明的保护范围之中。当前第1页12