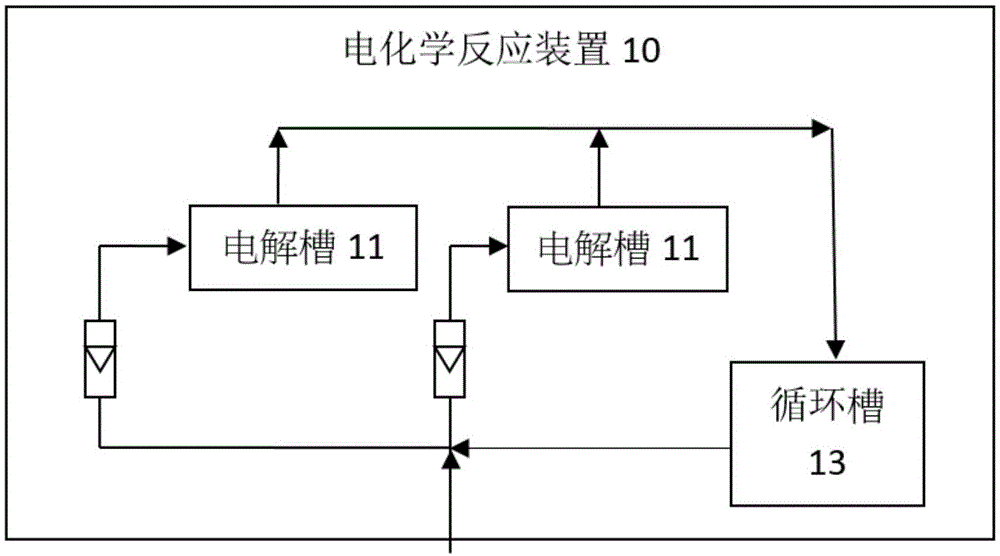
本发明涉及水处理工艺,尤其涉及一种高盐废水处理方法,使得处理后的高盐有机废水达到地表水iv类标准以进行排放。
背景技术:
:随着环保政策的日趋严格及排放标准的提高,对工业废水处理技术的要求也越来越高。特别是作为危险废物的高盐有机废水,原水含盐量在1.5~3%之间,cod在5000~10000mg/l,氨氮在200mg/l以上、最高可达1000mg/l,总磷在100mg/l以上、最高可达1000mg/l,此外还含有一定量的铜、镍等严控污染物。此类废水具有较高的盐度及cod浓度,属于难降解工业废水,需要采用特殊的技术手段,才可保证出水的达标排放。一般地,作为前端的处理,可采用以下几种技术方法:一是化学氧化,包括芬顿氧化、湿式催化氧化法、臭氧氧化、加压空气湿式氧化等;二是微生物氧化,因含盐量比较高,需要经过驯化,培育优势的耐盐微生物,一般对盐度的要求是不能超过2%;三是膜分离法,可采用多种不同功能的膜组件对废水进行处理,如微滤、超滤、纳滤、反渗透等功能性膜组件,通过组合的方式可实现不同标准的排水及分质分盐。但是对于高盐有机废水来讲,化学氧化及微生物氧化一般都难以直接达到排放标准,通常需要膜分离作为工艺达标的末端保障。因生化法处理的低成本,在可生化处理的场合,通常采用生化-膜分离法联用的方式。膜分离是一种物理分离方法,作为高盐有机废水,较难达到较高的浓缩倍数,膜分离的产水率在80%以下,膜浓缩液产率在20%以上。因膜浓缩液含有更高的盐分,对处理的工艺方法提出了更高的要求,是行业内研究的重点和难点。本发明针对高盐有机废水经生化处理及膜分离处理后的浓缩液的处理,提出了一种高盐废水处理方法及高盐废水处理系统,以使得上述浓缩液在处理后达到地表水iv类标准进行排放。技术实现要素:本发明的目的是提供一种高盐废水处理方法,以解决上述技术问题。一种高盐废水处理方法,对高盐有机废水经生化处理及膜分离处理后的浓缩液进行处理,其包括以下步骤:电化学处理:将废水通入一电化学反应装置中,所述废水在所述电化学反应装置中的停留时间为2小时~5小时;所述电化学处理时的电流密度为500a/m2~1000a/m2,电压为4.0v~6.0v,两电极板的间距为5mm~20mm;氧化处理:通过稀无机酸调节上述经过电化学处理后的废水的ph值为2.0~3.0,加入所述废水重量的0.5%~1.5%的七水硫酸亚铁至溶解,而后加入所述废水体积的0.5%~1.0%的双氧水溶液并反应1小时~3小时,所述双氧水溶液的浓度为10%~27.5%;以及净化处理:通过熟石灰调节上述经过氧化处理的废水的ph值为6~9,并继续反应0.5小时~2.0小时后过滤。进一步地,所述电化学反应装置包括电解槽,所述废水在所述电化学反应装置中循环反复进入所述电化学反应装置中的电解槽中进行电化学处理。进一步地,所述循环流量为所述电解槽体积的25倍~50倍。进一步地,所述电解槽为平行板式电解槽、同心圆式电解槽、辐射式电解槽及圆筒式电解槽中的至少一种。进一步地,所述电极板为二氧化锡复合电极、贵金属氧化物电极、亚氧化钛复合材料电极及不锈钢电极中的至少一种。进一步地,氧化处理时,边搅拌边加入所述双氧水溶液,所述双氧水溶液的浓度为27.5%。进一步地,所述稀无机酸为稀硫酸、稀盐酸或稀硝酸。进一步地,净化处理时,边搅拌边加入所述熟石灰,并继续搅拌反应0.5小时~2.0小时后过滤。进一步地,所述搅拌为机械搅拌、液体对流搅拌或空气对流搅拌。进一步地,所述高盐废水处理方法在所述电化学处理前,还包括过滤处理。与现有技术相比,本发明的高盐废水处理方法,其工艺流程短、处理效果稳定,且工艺运行灵活可控,适用性较强。同时,高盐有机废水经生化处理及膜分离处理后的浓缩液通过上述处理方法处理后达到地表水iv类标准。附图说明图1为本发明一具体实施例的电化学反应装置的结构示意图。主要元件符号说明电化学反应装置10电解槽11循环槽13具体实施方式下面将结合具体实施例对本发明的技术方案进行清楚、完整地描述。显然,所描述的实施方式仅是本发明一部分实施方式,而不是全部的实施方式。基于本发明中的实施方式,本领域普通技术人员在没有做出创造性劳动前提下所获得的所有其他实施方式,都属于本发明保护的范围。需要说明的是,“生化处理”是使废水与微生物混合接触,利用微生物体内的生物化学作用分解废水中的有机物和某些无机毒物,使有机物和无机毒物转化为无毒物质的一种污水处理方法。“化学需氧量(cod)”是以化学方法测量废水中需要被氧化的还原性物质的量,它是一个重要的废水中的有机物污染参数。“氨氮”是废水中氨氮含量指标,是衡量水质的一个重要标准,氨氮含量高会导致水体富营养化。“总磷”是水体中磷元素的总含量,是水体富含有机质的指标之一,磷含量过多会引起水华或赤潮,打乱水体的平衡。除非另有定义,本文所使用的所有的技术和科学术语与属于本发明的
技术领域:
的技术人员通常理解的含义相同。在本发明的说明书中所使用的技术手段的名称只是为了描述具体的实施例的目的,不是旨在于限制本发明。在不冲突的情况下,下述的实施例及实施例中的特征可以相互组合。本发明提供一较佳实施方式的高盐废水处理方法,用以处理高盐有机废水经生化处理及膜分离处理后的浓缩液,其包括以下步骤:步骤s1,将废水通入一电化学反应装置中进行电化学处理,所述废水在所述电化学反应装置中的停留时间为2小时~5小时。所述电化学处理时的电流密度为500a/m2~1000a/m2,电压为4.0v~6.0v,两电极板的间距为5mm~20mm。本实施方式中,所述废水在所述电化学反应装置中循环反复进入所述电化学反应装置中的电解槽中进行电化学处理,所述循环流量为所述电解槽体积的25倍~50倍。在其他实施方式中,所述废水可直接一次性加入所述电化学反应装置中的电解槽中以进行电化学处理,省略循环过程。所述电化学反应装置中电解槽可为但不仅限于平行板式电解槽、同心圆式电解槽、辐射式电解槽及圆筒式电解槽中的至少一种。所述电解槽中的电极板可为但不仅限于二氧化锡复合电极、贵金属氧化物电极、亚氧化钛复合材料电极及不锈钢电极中的至少一种。步骤s2,对上述经过电化学处理后的废水进行氧化处理。具体的,通过稀无机酸调节废水的ph值为2.0~3.0,加入所述废水重量的0.5%~1.5%的七水硫酸亚铁至废水中溶解,而后加入所述废水体积的0.5%~1.0%的双氧水溶液并反应1小时~3小时。所述双氧水溶液的浓度为10%~27.5%。优选的,加入七水硫酸亚铁至废水中搅拌溶解,再边搅拌边加入所述双氧水溶液,而后继续搅拌反应1小时~3小时。所述双氧水溶液的浓度为27.5%。优选的,所述稀无机酸为稀硫酸。在其他实施方式中,所述稀无机酸还可为稀盐酸或稀硝酸等酸类。步骤s3,对上述经过氧化处理的废水进行净化处理。具体的,加入熟石灰调节废水的ph值为6~9,并继续反应0.5小时~2.0小时后过滤,获得的滤液达到地表水iv类标准。优选的,边搅拌边加入熟石灰,并继续搅拌反应0.5小时~2.0小时后过滤。所述高盐废水处理方法中的搅拌可为但不仅限于机械搅拌、液体对流搅拌或空气对流搅拌等方式。本实施方式中,所述高盐废水处理方法在所述电化学处理前,还包括过滤处理。所述过滤处理可包括砂滤、炭滤及精滤中的至少一种。优选的,所述过滤处理为精滤。本发明的高盐废水处理方法,其工艺流程短、处理效果稳定,且工艺运行灵活可控,适用性较强。同时,高盐有机废水经生化处理及膜分离处理后的浓缩液通过上述高盐废水处理方法处理后达到地表水iv类标准。以下通过具体实施例来进一步详细说明本发明,但本发明并不限定于下述实施例。实施例提供一高盐有机废水经生化处理及膜分离处理后的浓缩液,所述浓缩液的盐度为6.0%,cod的含量为600mg/l,氨氮的含量为900mg/l,总磷的含量为110mg/l,铜离子的含量为2.5mg/l,镍离子的含量为2.06mg/l。请参阅图1,提供一电化学反应装置10,其包括两个电解槽11及一与所述两个电解槽11连通的循环槽13,每一电解槽11的容积为40l,所述循环槽13的有效容积为110l。每一电解槽11内的两电极板的间距为5mm。将上述浓缩液通入所述电化学反应装置10中,所述浓缩液通过管道进入电解槽11内进行电化学处理,而后进入循环槽13内排气后循环重新进入电解槽11,控制浓缩液在所述电化学反应装置10中的停留时间为3小时,控制每一电解槽的循环流量为1.0m3/h,电流密度为750a/m2,电压为4.5v。经过所述电化学反应装置10的电化学处理后的出水的cod含量及氨氮的含量可稳定地达到地表水iv类标准。将1m3经过所述电化学反应装置10的电化学处理后的出水用稀硫酸调节ph值至2.5,加入10kg的七水硫酸亚铁搅拌至溶解,再边搅拌边缓慢加入10l浓度为27.5%的双氧水溶液,而后继续搅拌反应1.5小时得到氧化处理的出水。将上述氧化处理的出水用熟石灰调节ph值至7.0,并继续搅拌反应1小时后过滤。累计处理10m3的浓缩液,最后滤过后的滤液的cod的含量均分别为0~19mg/l,氨氮的含量均分别为1.1mg/l~1.3mg/l,总磷的含量均分别为0.05mg/l~0.29mg/l,铜离子的含量均分别为0.01mg/l~0.05mg/l,镍离子的含量均分别为0.01mg/l~0.10mg/l。即高盐有机废水经生化处理及膜分离处理后的浓缩液在经由上述高盐废水处理方法处理后能够达到地表水iv类标准。上述实施例为本发明较佳的实施方式,但本发明的实施方式并不受上述实施例的限制,以上实施方式仅是用于解释权利要求书。然本发明的保护范围并不局限于说明书。任何熟悉本
技术领域:
的技术人员在本发明披露的技术范围内,可轻易想到的变化或者替换,都包含在本发明的保护范围之内。当前第1页12