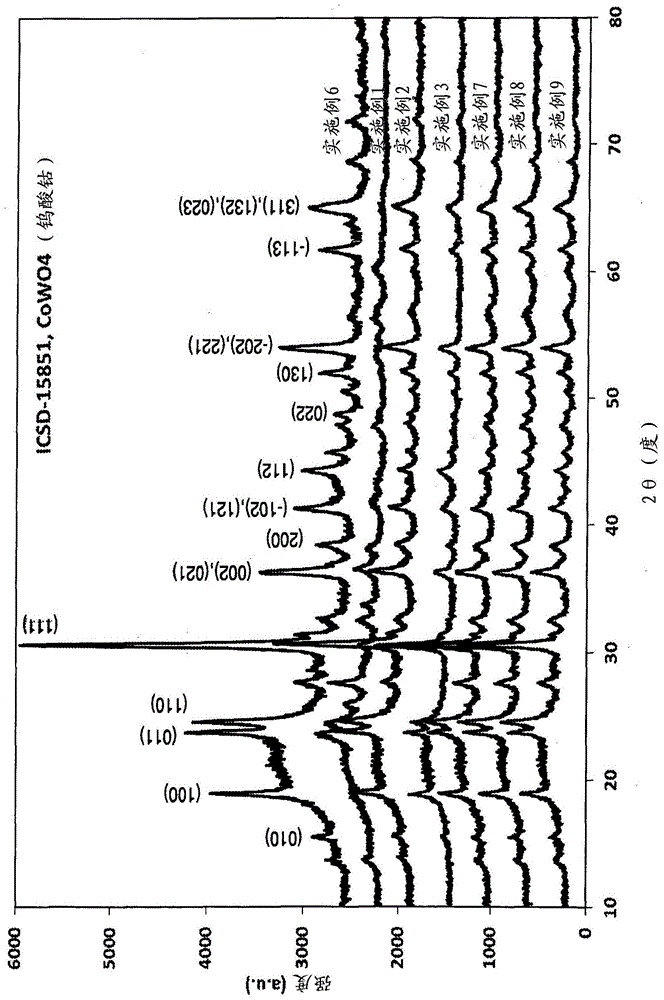
具有钴改性载体的加氢催化剂优先权要求本申请要求于2012年1月6日提交的美国临时申请No.61/583,874的优先权,通过援引将其全部并入本文。发明领域本发明涉及催化剂,涉及制备催化剂的方法,所述催化剂具有包含钴的改性载体,和涉及在本发明催化剂存在下从包含羧酸和/或其酯的原料产生乙醇的方法。发明背景用于工业用途的乙醇按照常规由石油化工原料例如油、天然气或煤生产,由原料中间体例如合成气生产,或者由淀粉质材料或纤维素材料例如玉米(corn)或甘蔗生产。由石油化工原料以及由纤维素材料生产乙醇的常规方法包括乙烯的酸催化水合、甲醇同系化、直接醇合成和费-托合成。石油化工原料价格的不稳定性促使按照常规生产的乙醇成本波动,在原料价格升高时使对乙醇生产的替代来源的需要比以往更大。淀粉质材料以及纤维素材料通过发酵转化为乙醇。然而,发酵通常用于适合于燃料或人类消费的乙醇的消费性生产。此外,淀粉质或纤维素类材料的发酵与食品来源构成竞争并且对用于工业用途所可生产的乙醇的量施加了限制。通过链烷酸和/或其它含羰基化合物的还原生产乙醇得到广泛研究,在文献中提及了催化剂、载体和操作条件的各种组合。EP0175558和美国专利号4,398,039已经提出各种羧酸在金属氧化物上的还原。Yokoyama等人的“Carboxylicacidsandderivatives”in:FineChemicalsThroughHeterogeneousCatalysis,2001,370-379中提供了用于转化各种羧酸的加氢催化剂的一些发展成果的概要。美国专利号8,080,694描述用于使烷酸加氢的方法,包括将气相中的包含氢和烷酸的气流通过加氢催化剂上方,所述催化剂包含:硅质载体上的选自铂、钯、铼及其混合物的铂族金属;和选自锡、铼及其混合物的金属助催化剂,所述硅质载体用选自WO3;MoO3;Fe2O3和Cr2O3的氧化还原助催化剂进行促进。美国专利号7,608,744描述用于选择性产生乙醇的方法:其通过在约250℃的温度在加氢催化剂组合物上进行乙酸的气相反应进行,所述催化剂组合物是负载于石墨上的钴和钯或负载于二氧化硅上的钴和铂,所述反应选择性地产生乙醇。美国专利6,495,730号描述了用于使用催化剂使羧酸加氢的方法,该催化剂包含负载含钌和锡的活性金属物质的活性碳。美国专利6,204,417号描述了用于在包含Pt和Re的催化剂存在下使脂族羧酸或酸酐或其酯或内酯加氢从而制备脂肪醇的另一方法。美国专利5,149,680号描述了用于在催化剂存在下使羧酸和它们的酸酐催化加氢为醇和/或酯的方法,该催化剂包含VIII族金属,例如钯,能与VIII族金属合金化的金属,和金属铼、钨或钼中的至少一种。美国专利4,777,303号描述了用于在催化剂存在下通过使羧酸加氢从而生产醇的方法,该催化剂包含高表面积石墨化碳上的为钼或钨的第一组分和为VIII族贵金属的第二组分。美国专利4,804,791号描述了用于在催化剂存在下通过使羧酸加氢从而生产醇的另一方法,该催化剂包含VIII族贵金属和铼。美国专利4,517,391号描述了通过使用主要含钴的催化剂的方法在高于大气压的压力下和在升高的温度时使乙酸加氢从而制备乙醇。现有方法遭受到阻碍商业可行性的各种问题,包括:(i)催化剂不具有对乙醇的必要选择性;(ii)催化剂有可能过于昂贵和/或对乙醇的生成呈非选择性并且产生不需要的副产物;(iii)过度的所需操作温度和压力;(iv)不足的催化剂寿命;以及/或者(v)所需的对乙酸乙酯和乙酸两者的活性。发明概述在第一实施方案中,本发明涉及催化剂,其包含改性载体上的贵金属和一种或多种活性金属。在一个实施方案中,改性载体包含(i)载体材料;(ii)钴;和(iii)包含选自钨、钼、钒、铌和钽的金属的载体改性剂。在一个实施方案中,改性载体可以包含0.5至20wt.%钴和0.1至40wt.%的量的载体改性剂,基于催化剂总重量计。优选,改性载体不包含贵金属和/或一种或多种活性金属,尤其是锡。贵金属选自铑、铼、钌、铂、钯、锇、铱和金。一种或多种活性金属选自铜、铁、钒、镍、钛、锌、铬、钼、钨、锡、镧、铈和锰,条件是贵金属和一种或多种活性金属是并非钴的金属。优选,贵金属是铂而活性金属是锡。贵金属可以以0.05至10wt.%的量存在,而一种或多种活性金属可以以0.1至20wt.%的量存在,基于催化剂总重量计。载体本身优选是硅质载体例如二氧化硅,或碳载体例如炭黑或活性碳,但是可以使用各种其它载体中的任意一种。在各个实施方案中,例如,载体可以选自二氧化硅,氧化铝,二氧化钛,二氧化硅/氧化铝,偏硅酸钙,热解二氧化硅,硅胶,高纯度二氧化硅,二氧化锆,碳,沸石及其混合物。载体改性剂可以包含各种形式的钨,比如钨氧化物形式或活性金属的钨酸盐。例如,载体改性剂金属可以包含钨酸钴。在本发明的又一实施方案中,涉及用于产生乙醇的方法,包括在催化剂存在下,在有效形成乙醇的条件下,在反应器中于升高的温度使包含乙酸和/或乙酸乙酯的原料与氢接触,条件是贵金属和一种或多种活性金属是并非钴的金属而其中所述改性载体包含(i)载体材料;(ii)钴;和(iii)包含选自钨、钼、钒、铌和钽的金属的载体改性剂。该方法可以形成包含乙醇和乙酸乙酯的粗产物,而其中所述粗产物具有0.1至40wt.%,例如0.1至30wt.%或10至25wt.%的乙酸乙酯稳态浓度。加氢可以在气相(vaporphase)中于125℃至350℃的温度、10kPa至3000kPa的压力和大于4:1的氢气与乙酸摩尔比下进行。乙酸可以形成自甲醇和一氧化碳,其中甲醇、一氧化碳和用于加氢步骤的氢各自衍生自合成气,而其中所述合成气衍生自选自天然气、油、石油,煤,生物质及其组合的碳源。在本发明的又一实施方案中,涉及包含下述步骤的合成方法:(a)将载体材料用钴前体和载体改性剂前体浸渍,以形成第一浸渍的载体,其中所述载体改性剂前体包含选自钨、钼、铌、钒和钽的载体改性剂金属;(b)将第一浸渍的载体加热至第一温度,以形成改性载体;(c)将改性载体用第二混合前体浸渍,以形成第二浸渍的载体,其中所述第二混合前体包含贵金属和一种或多种活性金属的前体;和(d)将第二浸渍的载体加热至第二温度,以形成包含在改性载体上的贵金属和至少一种活性金属的催化剂,条件是贵金属和至少一种活性金属是并非钴的金属。在第二实施方案中,本发明涉及包含在改性载体上的贵金属和至少一种活性金属的催化剂,条件是所述贵金属和所述至少一种活性金属是并非钴的金属,其中所述改性载体包含(i)载体材料;和(ii)钨酸钴。在一个实施方案中,改性载体还包含钨氧化物。优选,改性载体基本上不含锡。所述至少一种活性金属可以选自铜、铁、钒、镍、钛、锌、铬、钼、钨、锡、镧、铈和锰。在第三实施方案中,本发明涉及加氢催化剂,其包含贵金属和包含钴的载体,并且在煅烧之后具有基本如表4所示的X射线衍射图谱。优选,加氢催化剂包含在改性载体上的选自铑、铼、钌、铂、钯、锇、铱和金的贵金属和至少一种活性金属,其中所述至少一种活性金属选自铜、铁、钴、钒、镍、钛、锌、铬、钼、钨、锡、镧、铈和锰。改性载体可以包含载体材料和钨酸钴。在第四实施方案中,本发明涉及催化剂,其包含贵金属和包含钴的载体,并且在煅烧之后具有X射线衍射图谱,其中在2θ=10°以上存在局部最大值,其在下述各位置具有特征的半峰全宽(fullwidthatahalfmaximum):13.48至13.88的2θ值;15.11至15.87的2θ值;18.55至19.33的2θ值;23.2至24.28的2θ值;24.15至24.97的2θ值;27.34至28.02的2θ值;28.48至28.78的2θ值;30.17至30.99的2θ值;30.94至31.78的2θ值;32.33至33.05的2θ值;35.80至36.84的2θ值;38.04至38.84的2θ值;40.79至41.77的2θ值;43.71至44.85的2θ值;45.46至45.96的2θ值;47.65至48.13的2θ值;48.45至48.93的2θ值;50.21至50.83的2θ值;51.50至52.38的2θ值;53.53至54.47的2θ值;61.30至62.10的2θ值;64.37至65.71的2θ值;68.07至69.25的2θ值;和71.21至72.27的2θ值。附图说明参照所附非限制性图将更佳地理解本发明,其中:图1提供用于形成根据本发明的一个实施方案的催化剂的方法的非限制性流程图。图2是实施例1、2、3、6、7、8和9的催化剂的XRD图。发明详述催化剂组合物本发明涉及优选适宜用作加氢催化剂的催化剂组合物,涉及用于形成所述催化剂的方法,和涉及使用所述催化剂的化学过程。催化剂优选包含在载体优选改性载体上的一种或多种活性金属,并且可以适宜地用于使羧酸例如乙酸和/或其酯例如乙酸乙酯催化加氢至相应的醇例如乙醇。在一个实施方案中,本发明催化剂包含在改性载体上的贵金属和一种或多种活性金属。优选,贵金属和一种或多种活性金属是并非钴的金属。改性载体包含载体材料和包含选自钨、钼、钒、铌和钽的金属的载体改性剂。在一个方面,改性载体还包含钴,也即钴是改性载体的一部分。改性载体并不含加至所述改性载体上的金属中的任意一种,例如贵金属和一种或多种活性金属中的任意一种。例如如果铜是活性金属,则并不将铜加入改性载体。此外,钴并不与贵金属和一种或多种活性金属一起沉积在改性载体上。应理解钴与载体改性剂一起加至载体材料,而在钴和载体改性剂于载体材料上煅烧之后才加入贵金属和一种或多种活性金属。现在已发现这样的催化剂作为能够在加氢条件下将羧酸例如乙酸及其酯如乙酸乙酯都转化为它们相应的醇例如乙醇的多功能加氢催化剂特别有效。从而,在又一实施方案中,本发明催化剂包含在改性载体上的贵金属和活性金属,其中所述催化剂有效地用于提供大于20%、大于75%或大于90%的乙酸转化率,和大于0%、大于10%或大于20%的乙酸乙酯转化率。贵金属和活性金属本发明的催化剂优选包括浸渍在催化剂载体上的至少一种贵金属。贵金属可以选自例如铑、铼、钌、铂、钯、锇、铱和金。出于本发明意图,贵金属是并非钴的金属。用于本发明催化剂的优选贵金属包括钯、铂和铑。贵金属优选是在羧酸和/或其酯加氢至相应(一种或多种)醇中有催化活性的。贵金属可以为单质形式或为分子形式例如贵金属氧化物。催化剂包含小于5wt.%,例如小于3wt.%,小于2wt.%,小于1wt.%或小于0.5wt.%的量的这样的贵金属。在范围方面,催化剂可以包含0.05至10wt.%,例如0.1至5wt.%,或0.1至3wt.%的量的贵金属,基于催化剂总重量计。在一些实施方案中,贵金属的金属负载量可以小于一种或多种活性金属的金属负载量。除了贵金属之外,催化剂还包括布置(dispose)于改性载体上的一种或多种活性金属。出于本发明意图,一种或多种活性金属是并非钴的金属。不受理论所限,在作为改性载体的一部分时钴可以将载体改性剂金属或其氧化物分散在载体上。在浸渍或引入贵金属至改性载体之前,在将其浸渍和煅烧于载体上时,钴是改性载体的一部分。如本文所用,活性金属是指改善催化剂的转化率、选择性和/或产率的催化活性金属并且可以包括贵金属或非贵金属的活性金属。从而,包含贵金属和活性金属的催化剂可以包括:(i)一种(或多种)贵金属和一种(或多种)非贵金属的活性金属,或(ii)可以包含两种(或多种)贵金属。从而,贵金属作为示范性活性金属包括在本文当中。此外,应理解用术语"活性金属"指代本发明催化剂中的一些金属的用途并不意在表示也包括在本发明催化剂中的贵金属不是催化活性的。在一个实施方案中,催化剂中包括的一种或多种活性金属选自铜、铁、钒、镍、钛、锌、铬、钼、钨、锡、镧、铈和锰,前述贵金属中的任意一种,尤其是铼、钌和金及其组合。在一个实施方案中,一种或多种活性金属不包括钴。一种或多种活性金属不包括任何贵金属,从而包括铜、铁、钒、镍、钛、锌、铬、钼、钨、锡、镧、铈和锰及其组合。更优选,一种或多种活性金属选自铜、铁、镍、锌、铬和锡。在一个实施方案中,活性金属可以包含与至少一种其它活性金属组合的锡。一种或多种活性金属可以呈元素形式或分子形式,例如活性金属的氧化物,或其组合。在催化剂中存在的全部活性金属(包括前述的贵金属)的总重量优选是0.1至25wt.%例如0.5至15wt.%,或1.0至10wt.%。在一个实施方案中,催化剂可以包含0.5至20wt.%的量的钴和0.5至20wt.%的量的锡。出于本发明意图,活性金属可以布置于改性载体上。就本说明书而言,除非另外指明,重量百分数是基于包括金属和载体在内的催化剂的总重量计。在一些实施方案中,所述催化剂除含有贵金属外还含有至少两种活性金属。这至少两种活性金属可以选自上文所确定的任意活性金属,只要它们与贵金属不同或彼此不同。额外的活性金属还可以用于一些实施方案中。从而,在一些实施方案中,在载体上除了贵金属之外,还可以存在多种活性金属。对于一些示范性催化剂组合物的优选的双金属(贵金属+活性金属)组合包括铂/锡,铂/钌,铂/铼,铂/镍,钯/钌,钯/铼,钯/铜,钯/镍,金/钯,钌/铼,钌/铁,铑/铁,铑/镍和铑/锡。在一些实施方案中,催化剂包含在载体上的三种金属,例如一种贵金属和两种活性金属。示范性三元组合可以包括钯/铼/锡,钯/铼/镍,铂/锡/钯,铂/锡/铑,铂/锡/金,铂/锡/铱,铂/锡/铜,铂/锡/铬,铂/锡/锌,铂/锡/镍,铑/镍/锡,和铑/铁/锡。在一种优选的实施方案中,三元组合至少包含锡。在一些实施方案中,催化剂可以包含在载体上的多于三种金属。在催化剂包含在载体上的贵金属和一种活性金属时,活性金属以0.1至20wt.%,例如0.1至10wt.%,或0.1至7.5wt.%的量存在。在催化剂除了贵金属之外包含两种或更多种活性金属例如第一活性金属和第二活性金属时,第一活性金属可以以0.05至20wt.%,例如0.1至10wt.%,或0.5至5wt.%的量存在于催化剂中。第二活性金属的存在量可以为0.05至5wt.%,例如0.1至3wt.%或0.5至2.5wt.%。在一个实施方案中,在第二活性金属是锡时,金属负载量可以小于3wt.%,例如小于2.5wt.%或小于1.5wt.%。不受理论所限,由于锡的高挥发性具有较低锡浓度的催化剂可以具有延长的寿命。在一个实施方案中,一种或多种活性金属的金属负载量小于加至改性载体的钴的金属负载量。在一些实施方案中,在催化剂还包含第三活性金属时,第三活性金属可以以0.05至20wt.%,例如0.05至10wt.%或0.05至7.5wt.%的量存在。活性金属可以允许彼此合金化或者可以构成非合金化的金属溶液、金属混合物或者以一种或多种金属氧化物存在。优选的金属比可以取决于催化剂中所用活性金属而稍加变动。在一些实施方案中,贵金属与一种或多种活性金属的摩尔比是10:1至1:10,例如4:1至1:4,2:1至1:2或1.5:1至1:1.5。在又一实施方案中,贵金属可以以0.1至5wt.%的量存在,第一活性金属以0.5至20wt.%的量存在而第二活性金属以0.5至20wt.%的量存在,基于催化剂总重量计。在又一实施方案中,贵金属以0.1至5wt.%的量存在,第一活性金属以0.5至15wt.%的量存在而第二活性金属以0.5至15wt.%的量存在。在又一实施方案中,在最初将钴加至载体材料并作为改性载体的一部分煅烧,随后将锡加至改性载体时,优选具有大于4:1,例如大于6:1或大于11:1的钴:锡摩尔比。不受理论所限,基于相对锡的摩尔量的过量钴,可以改善催化剂的单功能性。载体材料本发明的催化剂包含任何合适的载体材料,优选改性载体材料。在一个实施方案中,载体材料可以是无机氧化物。在一个实施方案中,载体材料可以选自二氧化硅、氧化铝、氧化钛、二氧化硅/氧化铝、热解二氧化硅、高纯度二氧化硅、二氧化锆、碳(例如炭黑和活性炭)、沸石和它们的混合物。优选,载体材料包含硅质载体材料比如二氧化硅,热解二氧化硅,或高纯度二氧化硅。在一个实施方案中,硅质载体材料基本上不含碱土金属比如镁和钙。在优选的实施方案中,载体材料以基于催化剂总重量计25wt.%至99wt.%,例如30wt.%至98wt.%或35wt.%至95wt.%的量存在。在优选的实施方案中,载体材料包含硅质载体材料,例如二氧化硅,具有至少50m2/g,例如至少100m2/g或至少150m2/g的表面积。在范围方面,硅质载体材料优选具有50至600m2/g,例如100至500m2/g或100至300m2/g的表面积。高表面积二氧化硅,如说明书通篇使用的,是指具有至少250m2/g表面积的二氧化硅。出于本说明书的意图,表面积是指BET氮表面积,意指通过ASTMD6556-04测得的表面积,通过援引将其全部并入本文。优选的含硅载体材料还优选具有如通过压汞孔隙测量法(mercuryintrusionporosimetry)测定的5至100nm,例如5至30nm、5至25nm或5至10nm的平均孔径,以及如通过压汞孔隙测量法测定的0.5至2.0cm3/g,例如0.7至1.5cm3/g或0.8至1.3cm3/g的平均孔体积。载体材料和由此所得的催化剂组合物的形态可以宽泛地变化。在一些示例性实施方案中,载体材料和/或催化剂组合物的形态可以是丸粒、挤出物、球、喷雾干燥的微球、环、五辐轮状物(pentaring)、三叶形物、四叶形物、多叶形物或薄片,尽管优选圆柱形丸粒。优选地,含硅载体材料具有允许堆积密度为0.1至1.0g/cm3,例如0.2至0.9g/cm3或0.3至0.8g/cm3的形态。就尺寸而言,二氧化硅载体材料优选具有0.01至1.0cm,例如0.1至0.7cm或0.2至0.5cm的平均粒径,平均粒径是指球形颗粒的平均直径或非球形颗粒的平均最长尺寸。由于布置于载体上的贵金属和一种或多种活性金属通常为相对于载体的尺寸而言非常小的金属(或金属氧化物)颗粒或晶粒的形式,这些金属应该基本上不影响整个催化剂颗粒的尺寸。因此,上述粒径通常适用于载体尺寸以及最终催化剂颗粒,尽管优选将催化剂颗粒进行加工以形成大得多的催化剂颗粒,例如挤出形成催化剂丸粒。载体改性剂载体材料优选包含载体改性剂。载体改性剂可以调节载体材料的酸度。在一个实施方案中,载体改性剂包含选自钨、钼、钒、铌和钽的金属。用于载体改性剂的金属可以是其氧化物。在一个实施方案中,载体改性剂以0.1wt.%至50wt.%,例如0.2wt.%至25wt.%,0.5wt.%至20wt.%,或1wt.%至15wt.%的量存在,基于催化剂总重量计。在载体改性剂包含钨、钼和钒时,载体改性剂可以以0.1至40wt.%,例如0.1至30wt.%或0.1至20wt.%的量存在,基于催化剂总重量计。如所示,载体改性剂可以调节载体的酸度。例如,载体材料上的酸位如酸位或Lewis酸位可以通过载体改性剂进行调节以在乙酸和/或其酯加氢期间有利于对乙醇的选择性。可以通过使载体材料的表面酸度最优化来调节载体材料的酸度。载体材料还可以通过使载体改性剂改变载体材料的pKa来进行调节。除非上下文另外指明,其上的表面酸度或酸位数量可以通过F.Delannay编辑,“CharacterizationofHeterogeneousCatalysts”;ChapterIII:MeasurementofAcidityofSurfaces,370-404页;MarcelDekker,Inc.,N.Y.1984中所描述的技术进行测定,通过引用将其全文并入本文。一般而言,可以基于送至加氢工艺的进料流的组成调节载体的表面酸度以使醇产量,例如乙醇产量最大化。在一些实施方案中,载体改性剂可以是提高催化剂酸度的酸性改性剂。合适的酸性改性剂可以选自IVB族金属的氧化物、VB族金属的氧化物、VIB族金属的氧化物、VIIB族金属的氧化物、VIII族金属的氧化物、铝氧化物和它们的混合物。在一个实施方案中,载体改性剂包含选自钨、钼、钒、铌和钽的金属。在优选的实施方案中,载体改性剂包含选自钨、钒和钽的金属。此外,载体改性剂优选不包含亚磷酸(phosphorous)且并不制备自含亚磷酸的前体。在一个实施方案中,酸性改性剂还可以包括选自WO3,MoO3,V2O5,VO2,V2O3,Nb2O5,Ta2O5和Bi2O3的那些。还可以使用还原的钨氧化物或钼氧化物比如W20O58,WO2,W49O119,W50O148,W18O49,Mo9O26,Mo8O23,Mo5O14,Mo17O47,Mo4O11或MoO2中的一种或多种。在一个实施方案中,钨氧化物可以是立方氧化钨(H0.5WO3)。现出人意料且意想不到地发现将这些金属氧化物载体改性剂与贵金属和一种或多种活性金属组合使用可以产生具有多功能性的催化剂,并且该催化剂可以适合于在加氢条件下将羧酸例如乙酸,以及其相应的酯例如乙酸乙酯转化为一种或多种加氢产物例如乙醇。在其它实施方案中,酸性载体改性剂包括选自ZrO2,Nb2O5,Ta2O5,Al2O3,B2O3,P2O5和Sb2O3的那些。酸性载体改性剂包括选自ZrO2,Nb2O5,Ta2O5,和Al2O3的那些。除了载体改性剂之外,改性载体也包含钴。在一个实施方案中,改性载体包含0.5至20wt.%,例如1至15wt.%或1.5至10wt.%钴。在一个实施方案中,钴的金属负载量大于一种或多种活性金属的金属负载量。在一些任选的实施方案中,除了钴之外,改性载体还可以包含并非活性金属或贵金属的金属。优选,改性载体基本上不含锡。在一些实施方案中,酸性载体改性剂包含混合金属氧化物,该混合金属氧化物包含至少一种活性金属和IVB族、VB族、VIB族、VIII族金属例如钨、钼、钒、铌或钽的氧化物阴离子。氧化物阴离子例如可以为钨酸根、钼酸根、钒酸根或铌酸根的形式。示范性混合金属氧化物包括钨酸钴,钼酸钴,钒酸钴,铌酸钴,和/或钽酸钴。在一个实施方案中,催化剂不包含并且基本上不含钨酸锡。现已发现含有这类混合金属载体改性剂的催化剂可以提供在提高的转化率例如提高的酯转化率,和在减少的副产物形成例如减少的二乙醚形成方面所需的多功能程度。在一个实施方案中,催化剂包含在改性载体上的0.25至1.25wt.%铂,和1至5wt.%锡。改性载体包含二氧化硅或二氧化硅-氧化铝载体材料。使钴与载体改性剂一起布置于载体材料上。所述载体材料可以包含5至15wt.%酸性载体改性剂,例如WO3、V2O5和/或MoO3。在一个实施方案中,酸性改性剂可以包含钨酸钴,例如以0.1至20wt.%,或5至15wt.%的量的钨酸钴。在一些实施方案中,改性载体除包含一种或多种酸性改性剂外还包含一种或多种活性金属。改性载体可以例如包含选自铜、铁、钴、钒、镍、钛、锌、铬、钼、钨、锡、镧、铈和锰的一种或多种活性金属。例如,载体可以包含活性金属(优选不是贵金属),和酸性或碱性载体改性剂。优选地,载体改性剂包含选自钨、钼、钒、铌和钽的载体改性剂金属。在这方面,最终催化剂组合物包含布置于改性载体上的贵金属,和一种或多种活性金属。在优选实施方案中,改性载体中活性金属中的至少一种与布置于该载体上的活性金属中的至少一种相同。例如,催化剂可以包含用钴、锡和钨(任选地作为WO3,H0.5WO3,HWO4和/或作为钨酸钴)改性的载体。在该实施例中,催化剂还包含布置于改性载体上的贵金属例如钯、铂或铑,与至少一种活性金属例如钴和/或锡。不受理论所限,据信钨酸锡在改性载体或催化剂上的存在倾向于降低将乙酸转化为乙醇的催化活性。在用于改性载体上时,锡确实有助于改善的催化活性和催化剂寿命。然而,在锡与钨一起存在时,可以形成不希望的钨酸锡种类。为了防止钨酸锡的形成,已发现钴的使用可以抑制钨酸锡的形成。这使得钨酸钴优先钨酸锡而形成。此外,这使得可以将锡用在改性载体上,从而保持充足的催化剂活性和催化剂寿命。在一个实施方案中,改性载体包含钨酸钴和锡,但是改性载体基本上不含钨酸锡。催化剂的制备方法本发明还涉及用于制备催化剂的方法。不受理论限制,该催化剂制备方法可以改善乙酸转化率、酯转化率、乙醇选择性和总产率中的一个或多个。在一个实施方案中,将载体用一种或多种载体改性剂进行改性,随后用贵金属和一种或多种活性金属浸渍所得改性载体以形成催化剂组合物。例如,可以将载体用包含载体改性剂前体和钴前体的载体改性剂溶液浸渍。在干燥和煅烧后,将所得改性载体用包含贵金属前体且任选包含活性金属前体中的一种或多种的第二溶液进行浸渍,接着进行干燥和煅烧以形成最终催化剂。优选,加至改性载体的贵金属前体或活性金属前体的一种或多种不包含钴前体。在该实施方案中,载体改性剂溶液可以包含载体改性剂金属前体和钴前体。所述前体优选由在溶液中的各自金属的盐组成,所述盐在加热时转化为单质金属形式或金属氧化物。由于,在该实施方案中,将钴前体与载体改性剂前体同时地和/或依次地浸渍在载体材料上,在形成时钴可以与载体改性剂金属在分子金属相互作用,以形成一种或多种多金属的结晶种类比如钨酸钴。在其它实施方案中,钴可以不与载体改性剂金属前体相互作用和分开地沉积在载体材料上,例如作为离散的金属纳米粒子或作为无定形的金属混合物。从而,载体材料可以在用钴前体改性的同时用载体改性剂金属改性,而所得的钴可以或可以不为了形成一种或多种多金属的结晶种类而与载体改性剂金属相互作用。在一些实施方案中,可以将载体改性剂以颗粒物加入到载体材料上。例如,可以通过将载体改性剂颗粒与载体材料混合,优选在水中,将一种或多种载体改性剂前体(如果需要)加入到载体材料中。在混合时,对一些载体改性剂优选的是使用载体改性剂的粉末状物质。如果使用粉末状物质,则可以在将载体改性剂加入到载体中之前将其进行造粒、压碎和筛分。如所指出的,在大多数实施方案中,优选通过湿浸步骤加入载体改性剂。优选地,可以使用可变为载体改性剂的载体改性剂前体。一些示例性载体改性剂前体包括碱金属氧化物,碱土金属氧化物,IIB族金属氧化物,IIIB族金属氧化物,IVB族金属氧化物,VB族金属氧化物,VIB族金属氧化物,VIIB族金属氧化物,和/或VIII族金属氧化物,以及优选它们的水性盐。虽然金属氧化物和多氧离子(polyoxoion)盐绝大多数是不溶的,或者具有较差定义或有限的溶液化学,但是前过渡元素的同多和杂多氧阴离子类别构成重要的例外(exception)。这些络合物可以由如下通式表示:[MmOy]p-同多阴离子[XxMmOy]q-(x≤m)杂多阴离子其中M选自钨、钼、钒、铌、钽和它们的混合物,处于它们的最高(d0,d1)氧化态。这样的多金属氧酸盐阴离子绝大多(不唯一)基于准八面体配位的金属原子形成结构上截然不同的络合物类别。杂多或同多阴离子中可起附加物原子作用的元素即M可限于兼具有有利的离子半径和电荷组合以及形成dπ-pπM-O键能力的那些。然而对杂原子即X存在很少限制,所述杂原子可以选自实际上除稀有气体外的任何元素。参见例如M.T.Pope,HeteropolyandIsopolyOxometalates,SpringerVerlag,Berlin,1983,180;Chapt.38,ComprehensiveCoordinationChemistry,Vol.3,1028-58,PergamonPress,Oxford,1987,通过引用将它们全文并入本文。多金属氧酸盐(POM)和它们相应的杂多酸(HPA)具有若干优点从而使它们在经济和环境上受到关注。第一,HPA具有接近超酸范围(region)的非常强的布朗斯台德(Bronsted)酸度。此外,它们是在相当温和条件下表现出快速可逆多电子氧化还原转变的有效氧化剂。不同于沸石和金属氧化物,固体HPA还具有不连续的离子结构,包含相当灵活(mobile)的碱性结构单元例如杂多阴离子和抗衡阳离子(H+、H3O+、H5O2+等)。鉴于上文所述,在一些实施方案中,载体改性剂前体包含POM,其优选包含选自钨、钼、铌、钒和钽的金属。在一些实施方案中,POM包含杂POM。适宜POM的非限制性列表包括磷钨酸(H-PW12)(H3PW12O40·nH2O),偏钨酸铵(AMT)((NH4)6H2W12O40·H2O),七钼酸铵四水合物,(AHM)((NH4)6Mo7O24·4H2O),硅钨酸水合物(H-SiW12)(H4SiW12O40·H2O),硅钼酸(H-SiMo12)(H4SiMo12O40·nH2O),和磷钼酸(H-PMo12)(H3PMo12O40·nH2O)。本发明催化剂组合物中POM衍生的载体改性剂的使用目前出人意料且意想不到地显示出提供双-或多功能性的催化剂功能度,从而理想地获得乙酸和副产物酯例如乙酸乙酯的转化率,由此使它们适合于催化包含例如乙酸和乙酸乙酯的混合进料。将贵金属和一种或多种活性金属浸渍到载体例如改性载体上可以同时(共浸渍)或相继进行。在同时浸渍时,将两种或更多种金属前体混合在一起并将其一起加入到载体,优选改性载体中,接着进行干燥和煅烧以形成最终催化剂组合物。对于同时浸渍,如果所述两种前体与所期望的溶剂例如水不相容,则可以期望使用分散剂、表面活性剂、或者增溶剂例如草酸铵、或者酸例如乙酸或硝酸以促进第一、第二和/或任选的第三金属前体的分散或溶解。在相继浸渍时,可以首先将第一金属前体加入到载体中,接着进行干燥和煅烧,然后可以用第二金属前体浸渍所得材料,接着进行另外的干燥和随后的煅烧步骤以形成最终催化剂组合物。另外的金属前体(例如第三金属前体)可以与第一和/或第二金属前体一起加入或者在单独的第三浸渍步骤中加入,接着进行干燥和煅烧。当然,视需要可以采用连续浸渍和同时浸渍的组合。在其中将贵金属和/或一种或多种活性金属例如第一、第二或第三金属中的一种或多种依次即以多个浸渍步骤施加到催化剂的实施方案中,可以认为所述催化剂包含多个“理论层”。例如,在将钴浸渍于载体上、随后浸渍额外金属时,所得催化剂可据说具有包含钴的第一理论层和包含额外金属例如Pt和/或Sn的第二理论层。如上文所论述,在若干方面中,可以将多于一种活性金属前体以单个步骤共浸渍到载体上使得理论层可以包含多于一种金属或金属氧化物。优选地,相同的金属前体并未以多个连续浸渍步骤进行浸渍从而致使形成含有相同金属或金属氧化物的多个理论层。在该上下文中,虽然使用术语“层”,但是本领域技术人员将意识到催化剂载体上可以形成或不形成多个层,这例如取决于催化剂形成中所用的条件、每个步骤中所用金属的量和所使用的具体金属。在载体改性步骤中例如将载体改性剂前体浸渍到载体材料上,优选使用溶剂,例如水,冰乙酸,强酸如盐酸、硝酸或硫酸,或有机溶剂。载体改性剂溶液包含溶剂,优选水,载体改性剂前体,并且优选包含一种或多种活性金属前体。搅拌该溶液并使用例如始润浸渍技术将其与载体材料合并,在所述始润浸渍技术中将载体改性剂前体加入到孔体积与该溶液体积相同的载体材料中。通过将含有载体改性剂和/或活性金属中任一者或其二者的前体的溶液加入(任选滴加)到干燥的载体材料中来进行浸渍。然后毛细管作用将载体改性剂吸入载体材料的孔隙中。然后可通过干燥(任选在真空下)以去除载体混合物内的溶剂和任何挥发性组分并使载体改性剂沉积在载体材料之上或之内来形成浸渍的载体。干燥可以例如在50℃至300℃,例如100℃至200℃或约120℃的温度下进行任选1至24小时,例如3至15小时或6至12小时的时段。可以将经干燥的载体任选以斜线上升加热的方式,例如在300℃至900℃如400℃至750℃、500℃至600℃的温度或在约550℃下煅烧任选1至12小时例如2至10小时、4至8小时或约6小时的时间段,以形成最终的改性载体。在加热和/或施加真空时,前体的金属优选分解为它们的氧化物或单质形式。在一些情形中,在催化剂投入使用和煅烧例如经受在操作期间遭遇的高温之前,可以不完成溶剂的去除。在煅烧步骤期间,或者至少在使用催化剂的初始阶段期间,使这些化合物转化为金属的催化活性形式或其催化活性氧化物。一旦形成,改性载体可以成型为具有所需尺寸分布的颗粒,例如形成平均粒径为0.2至0.4cm的颗粒。可以将载体进行挤出、造粒、压片、压制、压碎或筛分为所需尺寸分布。可使用将载体材料成型为所需尺寸分布的任何已知方法。替代地,可以使用载体丸粒作为用于制备改性载体和最后制备最终催化剂的起始材料。在一个实施方案中,本发明催化剂可以用本体催化剂(bulkcatalyst)技术制备。本体催化剂可以由如下形成:将前体沉淀至载体改性剂和一种或多种活性金属。沉淀可以通过改变温度、压力和/或pH来加以控制。在一些实施方案中,本体催化剂制备可以采用粘合剂。载体材料可以不用于本体催化剂过程中。一旦沉淀,本体催化剂可以通过喷雾干燥、造粒、粒化、压片、制珠或制丸来造型。可以使用适宜的本体催化剂技术,比如描述于KrijnP.deJong,ed.,SynthesisofSolidCatalysts,Wiley,(2009),pg.308的那些,通过援引将其整个内容和公开并入。在一个实施方案中,将贵金属和一种或多种活性金属浸渍到载体上,任选浸渍到任意上述改性载体上。贵金属的前体优选用于金属浸渍步骤,所述前体例如包括有关贵金属的水溶性化合物或水可分散性化合物/络合物。类似地,还可以将一种或多种活性金属的前体浸渍到载体,优选改性载体中。取决于所使用的金属前体,可以优选使用例如水、冰乙酸、硝酸或有机溶剂的溶剂以有助于使一种或多种金属前体溶解。在一个实施方案中,形成金属前体的分别的溶液,随后在浸渍在载体上之前将它们进行混和。例如,可以形成包含第一金属前体的第一溶液,和可以形成包含第二金属前体和任选第三金属前体的第二溶液。第一、第二和任选第三金属前体中的至少一种优选是贵金属前体,而其它优选为活性金属前体(其可以包含或可以不包含贵金属前体)。任一种或这两种溶液优选包含溶剂,例如水、冰乙酸、盐酸、硝酸或有机溶剂。在一个示例性实施方案中,制备包含第一金属卤化物的第一溶液。第一金属卤化物任选包含卤化锡例如氯化锡,如氯化锡(II)和/或氯化锡(IV)。任选地,将第二金属前体(作为固体或作为单独的溶液)与第一溶液合并以形成合并的溶液。第二金属前体(如果使用)优选包含第二金属的草酸盐、乙酸盐、卤化物或硝酸盐。第一金属前体任选地包含活性金属,任选铜、铁、镍、铬、钼、钨或锡。还制备包含贵金属前体的第二溶液,在该实施方案中所述贵金属前体优选为贵金属卤化物,例如铑、铼、钌、铂或钯的卤化物。取决于是否需要第二金属前体,将第二溶液与第一溶液或所述合并的溶液合并以形成混合金属前体溶液。然后可以将所得混合金属前体溶液加入到载体,任选改性载体,接着进行干燥和煅烧以形成如上所述的最终催化剂组合物。所得催化剂在最终煅烧步骤之后可以洗涤或不洗涤。由于使一些前体溶解中的困难,可能期望降低第一和/或第二溶液的pH,例如通过使用酸例如乙酸、盐酸或硝酸如6至10MHNO3。在另一方面,制备包含第一金属草酸盐的第一溶液,例如铜、铁、镍、铬、钼、钨或锡的草酸盐。在该实施方案中,第一溶液优选还包含酸例如乙酸、盐酸、磷酸或硝酸如6至10MHNO3。任选地,将第二金属前体(作为固体或作为单独的溶液)与第一溶液合并以形成合并的溶液。第二金属前体(如果使用)优选包含第二金属草酸盐、乙酸盐、卤化物或硝酸盐,并且优选包含活性金属,也任选铜、铁、镍、铬、钼、钨或锡。也形成包含贵金属草酸盐,例如铑、铼、钌、铂或钯的草酸盐的第二溶液,该第二溶液任选还包含酸例如乙酸、盐酸、磷酸或硝酸如6至10MHNO3。取决于是否需要第二金属前体,将第二溶液与第一溶液或所述合并的溶液合并以形成混合金属前体溶液。然后可以将所得混合金属前体溶液加入到载体,任选改性载体,接着进行干燥和煅烧以形成如上所述的最终催化剂组合物。所得催化剂在最终煅烧步骤之后可以洗涤或不洗涤。在一个实施方案中,将浸渍载体,任选浸渍的改性载体在100℃至140℃、110℃至130℃或约120℃的温度干燥任选1至12小时例如2至10小时、4至8小时或约6小时。如果需要煅烧,优选该步骤中使用的煅烧温度小于上述所论述的改性载体形成中所使用的煅烧温度。例如可以在比第一煅烧步骤,即用于形成改性载体的煅烧步骤低至少50℃、至少100℃、至少150℃或至少200℃的温度下进行第二煅烧步骤。例如,可以将浸渍的催化剂在200℃至500℃、300℃至400℃或约350℃的温度煅烧任选1至12小时例如2至10小时、4至8小时或约6小时的时段。在一个实施方案中,如USPat.No.8,211,821中所描述的(通过引用将其全文并入本文),使用草酸铵来促进溶解金属前体中的至少一种,例如锡前体。在该方面,第一金属前体任选包含贵金属,例如铑、钯、或铂的草酸盐,第二金属前体任选包含草酸锡。另一活性金属前体(如果需要)包含铬、铜或锡的硝酸盐、卤化物、乙酸盐或草酸盐。在该方面,可以在作为增溶剂的草酸铵存在下制备第二金属前体的溶液,并且可以向其加入任选作为固体或单独溶液的第一金属前体。如果使用,可以将第三金属前体与包含第一前体和草酸锡前体的溶液合并,或者可以在加入第一金属前体之前将其与任选作为固体或单独溶液的第二金属前体合并。在其它实施方案中,酸例如乙酸、盐酸或硝酸可以替代草酸铵来促进草酸锡的溶解。然后可以将所得混合金属前体溶液加入到载体,任选改性载体,接着进行干燥和煅烧以形成如上所述的最终催化剂组合物。用于本发明各个实施方案的具体前体可以宽泛地变动。合适的金属前体可以包括例如金属卤化物、胺增溶的金属氢氧化物、金属硝酸盐或金属草酸盐。例如,铂前体和钯前体的合适化合物包括氯铂酸、氯铂酸铵、胺增溶的氢氧化铂、硝酸铂、四氨合硝酸铂、氯化铂、草酸铂、硝酸钯、四氨合硝酸钯、氯化钯、草酸钯、氯化钠钯、氯化钠铂、硝酸铂铵、Pt(NH3)4(NO4)2。通常,从经济学和环境方面的观点同时来看,优选铂和钯的可溶性化合物的水溶液。在一个实施方案中,贵金属前体不是金属卤化物并且基本上不含金属卤化物,而在其它实施方案中,如上文描述,贵金属前体是卤化物。催化剂使乙酸加氢的用途本发明催化剂的一个优点是该催化剂用于生产乙醇的稳定性或活性。因此,可认识到的是,本发明的催化剂完全能够用于乙酸加氢的商业规模工业应用,特别是乙醇生产。特别地,能够获得这样的稳定性程度,该稳定性程度使得催化剂活性可具有每100小时的催化剂使用小于6%,例如每100小时小于3%或每100小时小于1.5%的产率下降速率。优选地,一旦催化剂实现稳态状态,就测定产率下降速率。在洗涤之后,完成催化剂的干燥和煅烧,催化剂可以还原以便将其活化。还原在还原性气体优选氢存在下进行。于初始环境温度(其增至多达400℃)下将还原性气体任选地连续地通过催化剂上。在一个实施方案中,在催化剂已加载于反应容器中之后进行还原,加氢于所述反应容器中进行。在一个实施方案中,本发明涉及通过在任意上述催化剂存在下将包含选自乙酸、乙酸乙酯和它们的混合物的化合物的原料加氢生产乙醇的方法。一个特别优选的反应是由乙酸制备乙醇。该加氢反应可以按如下表示:HOAc+2H2→EtOH+H2O在一些实施方案中,该催化剂可以称作双功能催化剂,其原因在于该催化剂有效催化乙酸加氢为乙醇以及乙酸乙酯向一种或多种产物、优选乙醇的转化。有关本发明方法所使用的给进到反应器的原料、乙酸和氢气可以衍生自任何合适的来源,包括天然气、石油、煤、生物质等。作为实例,可以通过甲醇羰基化、乙醛氧化、乙烷氧化、氧化发酵和厌氧发酵生产乙酸。适合于乙酸生产的甲醇羰基化方法描述于美国专利No.7,208,624、7,115,772、7,005,541、6,657,078、6,627,770、6,143,930、5,599,976、5,144,068、5,026,908、5,001,259和4,994,608中,它们的全部公开内容通过引用并入本文。任选地,可以将乙醇生产与这种甲醇羰基化方法进行整合。由于石油和天然气价格波动,或多或少变得昂贵,所以由其它碳源生产乙酸和中间体例如甲醇和一氧化碳的方法已逐渐引起关注。特别地,当石油相对昂贵时,由衍生自较为可用的碳源的合成气体(“合成气”)生产乙酸可能变得有利。例如,美国专利No.6,232,352(通过引用将其全文并入本文)教导了改造甲醇装置用以制造乙酸的方法。通过改造甲醇装置,对于新的乙酸装置,与CO产生有关的大量资金费用得到显著降低或在很大程度上消除。使所有或部分合成气从甲醇合成环路进行分流并供给到分离器单元以回收CO,然后将其用于生产乙酸。以类似方式,用于加氢步骤的氢气可以由合成气供给。在一些实施方案中,用于上述乙酸加氢方法的一些或所有原料可以部分或全部衍生自合成气。例如,乙酸可以由甲醇和一氧化碳形成,甲醇和一氧化碳均可以衍生自合成气。合成气可以通过部分氧化重整或蒸汽重整形成,并且可以将一氧化碳从合成气分离出。类似地,可以将用于乙酸加氢形成粗乙醇产物步骤的氢气从合成气分离出。进而,合成气可以衍生自多种碳源。碳源例如可以选自天然气、油、石油、煤、生物质和它们的组合。合成气或氢气还可以得自生物衍生的甲烷气体,例如由垃圾填埋场废物(landfillwaste)或农业废物产生的生物衍生的甲烷气体。生物质衍生的合成气,与化石燃料比如煤或天然气相比,具有可检测的14C同位素含量。地球大气中在恒定的新形成与恒定降解之间中达到平衡,从而地球上大气中的碳中14C原子核的比例在长时间内是恒定的。活有机体中建立起与周围大气中相同的分布比n14C:n12C比,其在死亡时停止,并且14C分解的半衰期是约6000年。形成自生物质衍生的合成气的甲醇、乙酸和/或乙醇会期望具有基本上类似活有机体的14C含量。例如,甲醇、乙酸和/或乙醇的14C:12C比可以是活有机体的14C:12C比的1/2至约1倍。在其它实施方案中,本文描述的合成气、甲醇、乙酸和/或乙醇完全衍生自化石燃料,也即60,000多年前产生的碳源可以具有不可检测的14C含量。在另一个实施方案中,用于加氢步骤的乙酸可以由生物质发酵形成。发酵方法优选利用产乙酸(acetogenic)方法或同型产乙酸的微生物使糖类发酵得到乙酸并产生很少(如果有的话)二氧化碳作为副产物。与通常具有约67%碳效率的常规酵母法相比,所述发酵方法的碳效率优选大于70%、大于80%或大于90%。任选地,发酵过程中使用的微生物为选自如下的属:梭菌属(Clostridium)、乳杆菌属(Lactobacillus)、穆尔氏菌属(Moorella)、热厌氧杆菌属(Thermoanaerobacter)、丙酸杆菌属(Propionibacterium)、丙酸螺菌属(Propionispera)、厌氧螺菌属(Anaerobiospirillum)和拟杆菌属(Bacteriodes),特别是选自如下的物质:蚁酸醋酸梭菌(Clostridiumformicoaceticum)、丁酸梭菌(Clostridiumbutyricum)、热醋穆尔氏菌(Moorellathermoacetica)、凯伍热厌氧菌(Thermoanaerobacterkivui)、德氏乳杆菌(Lactobacillusdelbrukii)、产丙酸丙酸杆菌(Propionibacteriumacidipropionici)、栖树丙酸螺菌(Propionisperaarboris)、产琥珀酸厌氧螺菌(Anaerobiospirillumsuccinicproducens)、嗜淀粉拟杆菌(Bacteriodesamylophilus)和栖瘤胃拟杆菌(Bacteriodesruminicola)。任选地,在该过程中,可以将全部或部分的来自生物质的未发酵残余物例如木脂体气化以形成可用于本发明加氢步骤的氢气。用于形成乙酸的示范性发酵过程公开于美国专利号6,509,180,和美国公开号2008/0193989和2009/0281354,通过援引将其整体并入本文。生物质的实例包括但不限于农业废弃物、林业产品、草和其它纤维素材料、木材采伐剩余物、软木材碎片、硬木材碎片、树枝、树根、叶子、树皮、锯屑、不合格纸浆、玉米(corn)、玉米秸秆、麦秸秆、稻杆、甘蔗渣、软枝草、芒草、动物粪便、市政垃圾、市政污泥(municipalsewage)、商业废物、葡萄皮渣、杏核壳、山核桃壳、椰壳、咖啡渣、草粒、干草粒、木质颗粒、纸板、纸、塑料和布。又一生物质来源是黑液(blackliquor),其是木质素残余物、半纤维素和无机化学品的水溶液。美国专利No.RE35,377(也通过引用将其并入本文)提供了一种通过使含碳材料例如油、煤、天然气和生物质材料转化生产甲醇的方法。该方法包括使固体和/或液体含碳材料加氢气化以获得工艺气体,用另外的天然气将该工艺气体蒸汽热解以形成合成气。将该合成气转化为可以羰基化为乙酸的甲醇。该方法同样产生如上述有关本发明所可使用的氢气。美国专利No.5,821,111公开了一种将废生物质通过气化转化为合成气的方法,以及美国专利No.6,685,754公开了生产含氢气体组合物例如包含氢气和一氧化碳的合成气的方法,通过引用将它们全文并入本文。给进到加氢反应器的乙酸还可以包含其它羧酸和酸酐,以及醛和/或酮例如乙醛和丙酮。优选地,原料包含乙酸和乙酸乙酯。合适的乙酸进料流包含一种或多种选自乙酸、乙酸酐、乙醛、乙酸乙酯、乙缩醛、二乙醚和它们的混合物的化合物。在本发明的方法中还可以将这些其它化合物加氢。在一些实施方案中,在丙醇生产中羧酸例如丙酸或其醛的存在会是有益的。乙酸进料中还可以存在水。或者,可以直接从美国专利No.6,657,078(通过引用将其全文并入本文)中所描述的一类甲醇羰基化单元的闪蒸器取出蒸气形式的乙酸作为粗产物。例如,可以将粗蒸气产物直接给进到加氢反应器而不需要冷凝乙酸和轻馏分或者除去水,从而节省总体工艺费用。可以使乙酸在反应温度下气化,然后可以将气化的乙酸随同未稀释状态或用相对惰性的载气例如氮气、氩气、氦气、二氧化碳等稀释的氢气一起给进。为使反应在气相中运行,应控制系统中的温度使得其不下降到低于乙酸的露点。在一个实施方案中,可以在特定压力下使乙酸在乙酸沸点气化,然后可以将气化的乙酸进一步加热到反应器入口温度。在另一个实施方案中,将乙酸在气化前与其它气体混合,接着将混合蒸气一直加热到反应器入口温度。优选地,通过使氢气和/或循环气穿过处于或低于125℃的温度下的乙酸而使乙酸转变为蒸气状态,接着将合并的气态料流加热到反应器入口温度。在一些实施方案中反应器可以包括使用固定床反应器或流化床反应器的各种构造。在本发明的许多实施方案中,可以使用“绝热”反应器;即,具有很少或不需要穿过反应区的内部管道装置(plumbing)来加入或除去热。在其它实施方案中,可以使用径向流动的一个反应器或多个反应器作为反应器,或者可以使用具有或不具有热交换、急冷或引入另外进料的系列反应器。或者,可以使用配设有热传递介质的壳管式反应器。在许多情形中,反应区可以容纳在单个容器中或之间具有换热器的系列容器中。在优选的实施方案中,催化剂在例如管道或导管形状的固定床反应器中使用,其中典型地为蒸气形式的反应物穿过或通过所述催化剂。可使用其它反应器,例如流化床或沸腾床反应器。在一些情形中,加氢催化剂可以与惰性材料结合使用以调节反应物料流通过催化剂床的压降和反应物化合物与催化剂颗粒的接触时间。在一些实施方案中,在同一反应器中或者在例如串联的不同反应器中使用多个催化剂床。例如,在一个实施方案中,第一催化剂在第一催化剂级段中起到用于将羧酸例如乙酸加氢为其相应的醇例如乙醇的催化剂的作用,在第二级段中使用第二双功能催化剂将未反应的乙酸转化为乙醇以及将副产物酯例如乙酸乙酯转化为另外的产物,优选转化为乙醇。可以在这样的反应系统的第一和/或第二级段中的任一个或其二者中使用本发明的催化剂。反应器中的加氢可以在液相或气相中进行。优选地,在气相中于如下条件下进行该反应。反应温度可以为125℃至350℃,例如200℃至325℃、225℃至300℃或250℃至300℃。压力可以为10kPa至3000kPa,例如50kPa至2300kPa或100kPa至2000kPa。可以将反应物以大于500hr-1,例如大于1000hr-1、大于2500hr-1或甚至大于5000hr-1的气时空速(GHSV)给进到反应器。就范围而言,GHSV可以为50hr-1至50,000hr-1,例如500hr-1至30,000hr-1、1000hr-1至10,000hr-1或1000hr-1至6500hr-1。任选在刚刚足以克服穿过催化床的压降的压力下以所选择的GHSV进行加氢,尽管不限制使用较高的压力,但应理解,在高的空速例如5000hr-1或6,500hr-1下可能经历通过反应器床的相当大的压降。虽然该反应每摩尔乙酸消耗2摩尔氢气从而产生1摩尔乙醇,但进料流中氢气与乙酸的实际摩尔比可以为约100:1至1:100,例如50:1至1:50、20:1至1:2或18:1至2:1。最优选地,氢气与乙酸摩尔比大于2:1,例如大于4:1或大于8:1。对于混合原料,氢气与乙酸乙酯的摩尔比可以大于5:1,例如大于10:1或大于15:1。接触或停留时间也可以宽泛地变化,这些取决于如原料(乙酸和/或乙酸乙酯)的量、催化剂、反应器、温度和压力的变量。当使用除固定床外的催化剂系统时,典型的接触时间为几分之一秒到大于若干小时,至少对于气相反应,优选的接触时间为0.1至100秒,例如0.3至80秒或0.4至30秒。特别地,通过使用本发明的催化剂,乙酸和/或乙酸乙酯的加氢可以在反应器中获得向乙醇的有利的转化以及有利的选择性和产率。出于本发明意图,术语"转化率"是指进料中乙酸或乙酸乙酯(无论指定哪个)分别转化为并非乙酸或乙酸乙酯的化合物的量。转化率以基于进料中乙酸或乙酸乙酯计的百分数表示。乙酸转化率可以是至少20%,更优选至少60%,至少75%,至少80%,至少90%,至少95%或至少99%。在乙酸加氢期间,可以产生作为副产物的乙酸乙酯。在没有从混合气相反应物消耗任何乙酸乙酯的情况下,乙酸乙酯的转化率可被认为是负的。本文描述的一些催化剂本质上是单功能的,并且有效地用于将乙酸转化为乙醇,但是并不用于转化乙酸乙酯。单功能催化剂的使用可以引起在系统中不希望的乙酸乙酯积累,尤其是对于采用含有乙酸乙酯的一个或多个至反应器的循环流的系统。然而,本发明的优选催化剂为多功能的,其原因在于它们有效催化乙酸向乙醇的转化以及乙酸烷基酯例如乙酸乙酯向除乙酸烷基酯以外的一种或多种产物的转化。多功能催化剂优选对以足够大的速率消耗乙酸乙酯是有效的以便至少抵消乙酸乙酯产生的速率,从而获得非负乙酸乙酯转化率,即实现乙酸乙酯不净增加。这样的催化剂的使用可以例如产生有效地(effectively)为0%或大于0%的乙酸乙酯转化率。在一些实施方案中,本发明催化剂有效地提供至少0%,例如至少5%,至少10%,至少15%,至少20%或至少35%的乙酸乙酯转化率。在连续工艺中,在所述工艺达到平衡后,加入(例如再循环)到加氢反应器的乙酸乙酯和在粗产物中离开反应器的乙酸乙酯优选接近一定水平。催化乙酸乙酯以及乙酸转化的多功能催化剂的使用致使较低量的乙酸乙酯被加入到反应器中并且产生相对单功能催化剂较少的乙酸乙酯。在优选实施方案中,在实现平衡后,混合进料和粗产物中乙酸乙酯的浓度小于40wt.%、小于25wt.%或小于15wt.%。在优选实施方案中,所述工艺形成包含乙醇和乙酸乙酯的粗产物,并且该粗产物具有0.1至40wt.%例如0.1至20wt.%或0.1至10wt.%的乙酸乙酯稳态浓度。虽然期望具有高的乙酸转化率例如至少60%的催化剂,但是在一些实施方案中在乙醇的选择性高时低的转化率也可以接受。当然,应充分理解,在许多情形中,可通过适当的再循环料流或者使用较大的反应器来弥补转化率,但却较难于弥补差的选择性。选择性按基于转化的乙酸和/或乙酸乙酯的摩尔百分数表示。应理解由乙酸和/或乙酸乙酯转化的每种化合物具有独立的选择性并且该选择性不依赖于转化率。例如,如果所转化的乙酸的60摩尔%转化为乙醇,则乙醇选择性为60%。就本发明而言,总选择性是基于总的所转化的乙酸和乙酸乙酯计。优选地,乙醇的总选择性为至少60%,例如至少70%,至少80%,至少85%,或至少88%。该加氢过程的优选实施方案还具有对不期望的产物例如甲烷、乙烷和二氧化碳的低选择性。对这些不期望的产物的选择性优选小于4%,例如小于2%或小于1%。更优选地,这些不期望的产物以检测不到的量存在。烷烃的形成可以是低的,理想地,穿过催化剂的乙酸小于2%、小于1%或小于0.5%转化为烷烃,该烷烃除作为燃料外具有很小价值。如本文中所使用的术语“产率”是指加氢期间基于所用催化剂的千克计每小时所形成的规定产物例如乙醇的克数。优选的产率为每千克催化剂每小时至少100克乙醇,例如每千克催化剂每小时至少400克乙醇为或每千克催化剂每小时至少600克乙醇。就范围而言,所述产率优选为每千克催化剂每小时100至3,000克乙醇,例如400至2,500克乙醇每千克催化剂每小时或600至2,000克乙醇每千克催化剂每小时。在本发明的各种实施方案中,由反应器产生的粗乙醇产物,在任何随后处理例如纯化和分离之前,将典型地包含未反应的乙酸、乙醇和水。在表1中提供了粗乙醇产物的示例性组成范围。表1中所确定的“其它”可以包括例如酯、醚、醛、酮、烷烃和二氧化碳。在一个实施方案中,粗乙醇产物可以包含小于20wt.%,例如小于15wt.%、小于10wt.%或小于5wt.%的量的乙酸。就范围而言,表1的乙酸浓度可以包含0.1wt.%至20wt.%,例如0.1wt.%至15wt.%、0.1至10wt.%或0.1wt.%至5wt.%。在具有较低乙酸量的实施方案中,乙酸的转化率优选大于75%,例如大于85%或大于90%。此外,乙醇选择性也优选是高的,大于75%,例如大于85%或大于90%。可以使用若干不同的技术从使用本发明催化剂时反应器产生的粗乙醇产物回收乙醇产物。乙醇产品可以是工业级乙醇,包含基于该乙醇产品总重量计75至96重量%乙醇,例如80至96重量%或85至96重量%乙醇。工业级乙醇可以具有小于12wt.%例如小于8wt.%或小于3wt.%的水的水浓度。在一些实施方案中,当进一步使用水分离时,乙醇产物优选含有大于96wt.%,例如大于98wt.%或大于99.5wt.%的量的乙醇。具有进一步水分离的乙醇产品优选包含小于3wt.%例如小于2wt.%或小于0.5wt.%的水。由本发明实施方案生产的成品乙醇组合物可以用于各种应用,包括燃料、溶剂、化学原料、药物产品、清洁剂、消毒杀菌剂、氢转化或消费。在燃料应用中,可以使该成品乙醇组合物与汽油调合用于机动车辆例如汽车、船只和小型活塞发动机飞机。在非燃料应用中,该成品乙醇组合物可以用作化妆品和化妆品制剂的溶剂、清净剂、消毒剂、涂料、油墨和药品。该成品乙醇组合物还可以在药用产品、食品制剂、染料、光化学和乳胶处理的制造过程中用作处理溶剂。该成品乙醇组合物还可以用作化学原料以制备其它化学品例如醋、丙烯酸乙酯、乙酸乙酯、乙烯、二醇醚、乙胺、乙苯、醛、丁二烯和高级醇,特别是丁醇。在乙酸乙酯的制备中,可以将该成品乙醇组合物用乙酸酯化。在另一个应用中,可以使该成品乙醇组合物脱水以生产乙烯。可使用任何已知的脱水催化剂,例如沸石催化剂或磷钨酸催化剂,使乙醇脱水,所述脱水催化剂例如在共同未决美国公开No.2010/0030002和2010/0030001和WO2010146332中所描述,在此通过引用将它们的全部内容和公开内容并入本文。催化剂再生本发明催化剂是特别耐用的(robust)和具有长催化剂寿命。虽然如此,在长期使用的时间段内,本发明催化剂的活性还是可以逐渐降低。相应地,在本发明的又一实施方案中,本发明涉及用于再生废加氢催化剂的方法,包括,在有效形成加氢产物和废加氢催化剂的条件下,将加氢反应器中的羧酸和氢与加氢催化剂接触;并且在大于200℃、任选300℃至600℃的温度,在有效形成具有比废加氢催化剂更高的催化活性的再生的加氢催化剂的条件下,用再生介质处理废加氢催化剂,其中所述加氢催化剂包含在载体上的贵金属和一种或多种活性金属。在该上下文中,"废(spent)"意指,与早先使用时间段的相同催化剂相比,具有降低的转化率和/或降低的对希望产物例如乙醇的选择性的催化剂,其中所述降低选择性和/或转化率不可通过增加反应器温度多至设计限制来恢复。在又一实施方案中,本发明涉及用于再生废催化剂的方法,包括(a)在有效形成加氢产物和废加氢催化剂的条件下,将加氢反应器中的羧酸和氢与加氢催化剂接触;和(b)在大于200℃、任选地300℃至600℃的温度,在有效形成具有比废加氢催化剂更高的催化活性的再生的加氢催化剂的条件下,用再生介质处理废加氢催化剂,其中所述加氢催化剂包含在载体上的贵金属和一种或多种活性金属。处理可以在加氢反应器内或在加氢反应器外发生。例如,处理可以在再生单元中发生,其中所述方法还包括将废加氢催化剂从加氢反应器引导至再生单元的步骤,以及将再生的加氢催化剂从再生单元引导至加氢反应器的步骤。再生介质可以取决于是否希望仅仅从催化剂"剥离(strip)"例如含碳物质,或者是否希望完全再生而变化。取决于废催化剂的条件,再生介质可以选自蒸汽,氧(任选为空气、稀释的空气或在再生处理期间任选具有可变O2/N2比的氧/氮混合物的形式),或氢。优选,再生介质基本上不含羧酸反应物,任选地包含小于10wt.%羧酸,小于5wt.%羧酸,或小于1wt.%羧酸,例如乙酸。处理步骤可以例如在0.5至10巴,例如0.8至8巴或0.9至4巴的压力发生。再生可以例如在10至200小时,例如20至150小时或50至100小时的时间段内发生。优选,处理步骤中所用的条件足以将所得再生的加氢催化剂的羧酸转化率例如乙酸转化率,和/或乙醇选择性,相对于废催化剂的转化率和选择性增加至少25%,例如至少50%或至少75%。在又一方面,废催化剂具有相对新鲜催化剂降低或损失的乙醇选择性,而再生的催化剂恢复损失的乙醇选择性的至少25%,至少50%或至少75%。类似地,废催化剂可以具有相对于新鲜催化剂降低或损失的乙酸转化率,而再生的催化剂恢复损失的乙酸转化率的至少25%,至少50%或至少75%。如果蒸汽被用作再生介质,可以希望的是将再生的加氢催化剂干燥,随后将再生的加氢催化剂用于主要的加氢工艺当中。任选地在10至350℃例如50至250℃、70至180℃或80至130℃的温度,和任选地0.5至5巴例如0.8至2巴或0.9至1.5巴的绝对压力,和任选地在10至50小时例如10至20小时的时间段内进行干燥,如美国公开No.2011/0144398中所描述,通过援引将其全部并入本文。以下实施例描述本发明的催化剂和方法。实施例实施例1:Pt(1.09)Sn(1.2)/Co(2)WO3(12)/SiO2A.制备改性载体:Co(2)WO3(12)/SiO2催化剂制备方案的概要提供于图1中。金属浸渍溶液制备如下。首先,通过将5gCo(NO3)2·6H2O固体加入41gDI-H2O制备钴盐溶液。在Co盐完全溶解之后,将7.15gAMT(偏钨酸铵水合物)加至上述溶液。然后,在室温下于400rpm搅拌混合物5分钟。然后,将浸渍溶液加至在圆底烧瓶中的43gSiO2载体,以获得在载体上的均匀分布。在加入金属溶液之后,用80℃下的浴温和72毫巴下的真空用旋蒸仪将物质抽空至干1小时,随后在120℃在循环空气下干燥12小时。在炉中进行煅烧,程序温度是室温至160℃,速率为3℃/min,在160℃保持2小时;在550℃保持6小时,采用自160℃的3℃/min升温速率。B.改性载体的浸渍:Pt(1.09)Sn(1.2)/Co(2)WO3(12)/SiO2锡金属溶液制备如下。首先,通过将0.36g(NH4)2C2O4·H2O固体加入6gDI-H2O来制备草酸铵溶液。在草酸铵通过加热至60℃完全溶解之后,将0.21g草酸锡加至上述溶液。在该盐完全溶解之后,将该溶液冷却至室温。通过将1.08gPtC2O4溶液(10.12wt.%)加至4gDI-H2O来制备Pt金属溶液。将该溶液与锡溶液组合以制备浸渍溶液。然后,将浸渍溶液加至圆底烧瓶中的9.77g的改性二氧化硅载体,以获得在载体上的均匀分布。在加入金属溶液之后,用80℃下的浴温和72毫巴下的真空用旋蒸仪将物质排空至干2小时,随后在120℃在循环空气下干燥12小时。在炉中进行煅烧,程序温度是室温至160℃,速率3℃/min,在160℃保持2小时;在350℃保持6小时,采用自160℃的3℃/min升温速率。实施例2:Pt(1.09)Sn(1.2)/Co(5.3)WO3(12)/SiO2A.制备改性载体:Co(5.3)WO3(12)/SiO2金属浸渍溶液制备如下。首先,通过将13.25gCo(NO3)2·6H2O固体加入37gDI-H2O制备钴盐溶液。在Co盐完全溶解之后,将7.15gAMT加至上述溶液。然后,在室温下于400rpm搅拌混合物5分钟。然后,将浸渍溶液加至圆底烧瓶中的41.35gSiO2载体,以获得在载体上的均匀分布。在加入金属溶液之后,用80℃下的浴温和72毫巴下的真空用旋蒸仪将物质排空至干1小时,随后在120℃在循环空气下干燥12小时。用与实施例1相同的温度程序进行改性载体的煅烧。B.改性载体的浸渍:Pt(1.09)Sn(1.2)/Co(5.3)WO3(12)/SiO2通过将0.36g(NH4)2C2O4·H2O固体加入9gDI-H2O制备草酸铵溶液。在草酸铵通过加热多至60℃完全溶解之后,将0.21g草酸锡加至上述溶液。在该盐完全溶解之后,将该溶液冷却至室温。通过将1.08gPtC2O4溶液(10.12wt.%)加至4gDI-H2O来制备Pt金属溶液。将该溶液与锡溶液组合以制备浸渍溶液。然后,将浸渍溶液加至圆底烧瓶中的9.77g改性二氧化硅载体,以获得在载体上的均匀分布。在加入金属溶液之后,用80℃下的浴温和72毫巴下的真空用旋蒸仪将物质排空至干2小时,随后在120℃在循环空气下干燥12小时。用与实施例1相同的温度程序进行煅烧。实施例3:Pt(1.09)Sn(2.5)/Co(7.5)WO3(12)/SiO2A.制备改性载体:Co(7.5)WO3(12)/SiO2通过将37.79gCo(NO3)2·6H2O固体加至70gDI-H2O制备钴盐溶液。在Co盐完全溶解之后,将13.14gAMT加至上述溶液。然后,在室温下于400rpm搅拌混合物5分钟。然后,将浸渍溶液加至圆底烧瓶中的80.5gSiO2载体,以获得在载体上的均匀分布。在加入金属溶液之后,用80℃下的浴温和72毫巴下的真空用旋蒸仪将物质排空至干1小时,随后在120℃在循环空气下干燥12小时。用与实施例1相同的温度程序进行改性载体的煅烧。B.改性载体的浸渍:Pt(1.09)Sn(2.5)/Co(7.5)WO3(12)/SiO2通过将1.86g(NH4)2C2O4·H2O固体加入21.5gDI-H2O制备草酸铵溶液。在草酸铵通过加热多至60℃完全溶解之后,将1.09g草酸锡加至上述溶液。在该盐完全溶解之后,将该溶液冷却至室温。通过将2.7gPtC2O4溶液(10.12wt.%)加至10gD1-H20来制备Pt金属溶液。将该溶液与锡溶液组合以制备浸渍溶液。然后,将浸渍溶液加至圆底烧瓶中的24.1g改性二氧化硅载体,以获得在载体上的均匀分布。在加入金属溶液之后,用80℃下的浴温和72毫巴下的真空用旋蒸仪将物质排空至干2小时,随后在120℃在循环空气下干燥12小时。用与实施例1相同的温度程序进行煅烧。实施例4:Pt(1.09)Sn(2)/Co(6.5)WO3(12)/SiO2A.制备改性载体:Co(6.5)WO3(12)/SiO2通过将32.75gCo(NO3)2·6H2O固体加入73gDI-H2O制备钴盐溶液。在Co盐完全溶解之后,将13.14gAMT加至上述溶液。然后,在室温下于400rpm搅拌混合物5分钟。然后,将浸渍溶液加至圆底烧瓶中的81.5gSiO2载体,以获得在载体上的均匀分布。在加入金属溶液之后,用80℃下的浴温和72毫巴下的真空用旋蒸仪将物质排空至干1小时,随后在120℃在循环空气下干燥12小时。用与实施例1相同的温度程序进行改性载体的煅烧。B.改性载体的浸渍:Pt(1.09)Sn(2)/Co(6.5)WO3(12)/SiO2通过将1.49g(NH4)2C2O4·H2O固体加入21.5gDI-H2O制备草酸铵溶液。在草酸铵通过加热多至60℃完全溶解之后,将0.87g草酸锡加至上述溶液。在该盐完全溶解之后,将该溶液冷却至室温。通过将2.7gPtC2O4溶液(10.12wt.%)加至10gDI-H2O制备Pt金属溶液。将该溶液与锡溶液组合以制备浸渍溶液。然后,将浸渍溶液加至圆底烧瓶中的24.23g改性二氧化硅载体,以获得在载体上的均匀分布。在加入金属溶液之后,用80℃下的浴温和72毫巴下的真空用旋蒸仪将物质排空至干2小时,随后在120℃在循环空气下干燥12小时。用与实施例1相同的温度程序进行煅烧。实施例5:Pt(1.09)Sn(2.5)/Co(7.5)WO3(12)/SiO2A.制备改性载体:Co(7.5)WO3(12)/SiO2通过将93.89gCo(NO3)2·6H2O固体加入137gDI-H2O制备钴盐溶液。在Co盐完全溶解之后,将32.65gAMT加至上述溶液。然后,在室温下于400rpm搅拌混合物5分钟。然后,通过使用始润(incipientwetness)技术将浸渍溶液加至圆底烧瓶中的200gSiO2载体,以获得在载体上的均匀分布。在加入金属溶液之后,用80℃下的浴温和72毫巴下的真空用旋蒸仪将物质排空至干1小时,随后在120℃在循环空气下干燥5小时。用与实施例1相同的温度程序进行改性载体的煅烧。B.改性载体的浸渍:Pt(1.09)Sn(2.5)/Co(7.5)WO3(12)/SiO2第一次浸渍:首先,通过将6.53g(NH4)2C2O4·H2O固体加入78.75gDI-H2O制备草酸铵溶液。在草酸铵通过加热多至60℃完全溶解之后,将3.89g草酸锡加至上述溶液。在该盐完全溶解之后,将该溶液冷却至室温。通过将9.43gPtC2O4溶液(10.12wt.%)加至33.01gDI-H2O制备Pt金属溶液。将该溶液与锡溶液组合以制备浸渍溶液。然后,通过使用始润技术将浸渍溶液加至圆底烧瓶中的168.7g改性二氧化硅载体,以获得在载体上的均匀分布。在加入金属溶液之后,用80℃下的浴温和72毫巴下的真空用旋蒸仪将物质排空至干2小时,随后在120℃在循环空气下干燥5小时。第二次浸渍:重复第一步但是替代地用24.26gDI-H2O来稀释Pt草酸盐,然后在120℃将其干燥12小时。用与实施例1相同的温度程序进行煅烧。实施例6:Pt(1.09)Sn(1.5)/Co(7)WO3(12)/SiO2A.制备改性载体:Co(7)WO3(12)/SiO2通过将35.27gCo(NO3)2·6H2O固体加入73gDI-H2O制备钴盐溶液。在Co盐完全溶解之后,将13.14gAMT加至上述溶液。然后,在室温下于400rpm搅拌混合物5分钟。然后,通过使用始润技术将浸渍溶液加至圆底烧瓶中的81gSiO2载体,以获得在载体上的均匀分布。在加入金属溶液之后,用80℃下的浴温和72毫巴下的真空用旋蒸仪将物质排空至干1小时,随后在120℃在循环空气下干燥5小时。用与实施例1相同的温度程序进行改性载体的煅烧。B.改性载体的浸渍:Pt(1.09)Sn(1.5)/Co(7)WO3(12)/SiO2第一次浸渍:首先,通过将0.23g(NH4)2C2O4·H2O固体加入4.6gDI-H2O制备草酸铵溶液。在草酸铵通过加热多至60℃完全溶解之后,将0.13g草酸锡加至上述溶液。在该盐完全溶解之后,将该溶液冷却至室温。通过将0.68gPtC2O4溶液(7.965wt.%)加至2gDI-H2O制备Pt金属溶液。将该溶液与锡溶液组合以制备浸渍溶液。然后,通过使用始润技术将浸渍溶液加至圆底烧瓶中的9.74g改性二氧化硅载体,以获得在载体上的均匀分布。在加入金属溶液之后,用80℃下的浴温和72毫巴下的真空用旋蒸仪将物质排空至干2小时,随后在120℃在循环空气下干燥12小时。第二次浸渍:重复第一步但是替代地用1.4gDI-H2O来稀释Pt草酸盐,然后在120℃将其干燥5小时。用与实施例1相同的温度程序进行煅烧。实施例7:Pt(1.09)Sn(1.2)/Co(5.3)WO3(16)/SiO2A.制备改性载体:Co(5.3)WO3(16)/SiO2浸渍:金属浸渍溶液制备如下。首先,通过将33.18gCo(NO3)2·6H2O固体加入71gDI-H2O制备钴盐溶液。在Co盐完全溶解之后,通过将21.77gAMT加至上述溶液。然后,在室温下于400rpm搅拌混合物5分钟。然后,将浸渍溶液加至圆底烧瓶中的97.59gSiO2载体,以获得在载体上的均匀分布。在加入金属溶液之后,用80℃下的浴温和72毫巴下的真空用旋蒸仪将物质排空至干1小时,随后在120℃在循环空气下干燥12小时。用与实施例1相同的温度程序进行煅烧。B.改性载体的浸渍:Pt(1.09)Sn(1.2)/Co(5.3)WO3(16)/SiO2第一次浸渍:锡金属溶液制备如下。首先,将0.2g(NH4)2C2O4·H2O固体加入6.3gDI-H2O制备草酸铵溶液。在草酸铵通过加热多至60℃完全溶解之后,将0.11g草酸锡加至上述溶液。在该盐完全溶解之后,将该溶液冷却至室温。Pt金属溶液制备如下:通过将0.6843gPtC2O4溶液(7.965wt.%)加入上述锡溶液以制备浸渍溶液。然后,将浸渍溶液加至圆底烧瓶中的9.771g改性二氧化硅载体,以获得在载体上的均匀分布。在加入金属溶液之后,用80℃下的浴温和72毫巴下的真空用旋蒸仪将物质排空至干2小时,随后在120℃在循环空气下干燥12小时。第二次浸渍:重复第一步但是替代地用5.7gDI-水来溶解草酸铵,然后在120℃将其干燥5小时。用与实施例1相同的温度程序进行煅烧。实施例8:Pt(1.09)Sn(1.8)/Co(6.5)WO3(16)/SiO2A.制备改性载体:Co(6.5)WO3(16)/SiO2浸渍:金属浸渍溶液制备如下。首先,通过将40.69gCo(NO3)2·6H2O固体加入70gDI-H2O制备钴盐溶液。在Co盐完全溶解之后,将21.77gAMT加至上述溶液。然后,在室温下于400rpm搅拌混合物5分钟。然后,将浸渍溶液加至圆底烧瓶中的96.1gSiO2载体,以获得在载体上的均匀分布。在加入金属溶液之后,用80℃下的浴温和72毫巴下的真空用旋蒸仪将物质排空至干1小时,随后在120℃在循环空气下干燥12小时。用与实施例1相同的温度程序进行煅烧。B.改性载体的浸渍:Pt(1.09)Sn(1.2)/Co(5.3)WO3(16)/SiO2第一次浸渍:锡金属溶液制备如下。首先,通过将0.28g(NH4)2C2O4·H2O固体加入6.3gDI-H2O制备草酸铵溶液。在草酸铵通过加热多至60℃完全溶解之后,将0.16g草酸锡加至上述溶液。在该盐完全溶解之后,将该溶液冷却至室温。Pt金属溶液制备如下:通过将0.6843gPtC2O4溶液(7.965wt.%)加入上述锡溶液以制备浸渍溶液。然后,将浸渍溶液加至圆底烧瓶中的9.711g改性二氧化硅载体,以获得在载体上的均匀分布。在加入金属溶液之后,用80℃下的浴温和72毫巴下的真空用旋蒸仪将物质排空至干2小时,随后在120℃在循环空气下干燥12小时。第二次浸渍:重复第一步但是替代地用5.7gDI-水来溶解草酸铵,然后在120℃将其5小时。用与实施例1相同的温度程序进行煅烧。实施例9:Pt(1.09)Sn(1.2)/Co(7.5)WO3(16)/SiO2A.制备改性载体:Co(7.5)WO3(16)/SiO2浸渍:金属浸渍溶液制备如下。首先,通过将46.95gCo(NO3)2·6H2O固体加入70gDI-H2O制备钴盐溶液。在Co盐完全溶解之后,将21.77gAMT加至上述溶液。然后,在室温下于400rpm搅拌混合物5分钟。然后,将浸渍溶液加至圆底烧瓶中的94.86gSiO2载体,以获得在载体上的均匀分布。在加入金属溶液之后,用80℃下的浴温和72毫巴下的真空用旋蒸仪将物质排空至干1小时,随后在120℃在循环空气下干燥12小时。用与实施例1相同的温度程序进行煅烧。B.改性载体的浸渍:Pt(1.09)Sn(1.2)/Co(7.5)WO3(16)/SiO2第一次浸渍:锡金属溶液制备如下。首先,通过将0.2g(NH4)2C2O4·H2O固体加入6.3gDI-H2O制备草酸铵溶液。在草酸铵通过加热多至60℃完全溶解之后,将0.11g草酸锡加至上述溶液。在该盐完全溶解之后,将该溶液冷却至室温。Pt金属溶液制备如下:通过将0.6843gPtC2O4溶液(7.965wt.%)加入上述锡溶液以制备浸渍溶液。然后,将浸渍溶液加至圆底烧瓶中的9.771g改性二氧化硅载体,以获得在载体上的均匀分布。在加入金属溶液之后,用80℃下的浴温和72毫巴下的真空用旋蒸仪将物质排空至干2小时,随后在120℃在循环空气下干燥12小时。第二次浸渍:重复第一步但是替代地用5.7gDI-水来溶解草酸铵,然后在120℃将其5小时。用与实施例1相同的温度程序进行煅烧。实施例10:性能测试将实施例1-9的催化剂加至使用下述操作条件之一的试验设备当中。反应器系统和催化测试条件。试验单元包括四个独立的管式固定床反应器系统,其具有共同的温控、压力和气体和液体进料。反应器由3/8英寸(0.95cm)316SS管道制成,并且长度为121/8英寸(30.8cm)。气化器由3/8英寸(0.95cm)316SS管道制成,并且长度为123/8英寸(31.45cm)。反应器、气化器和它们各自的流出物转移管线是电热的(加热带)。反应器流出物被导通至冷却的水冷凝器和气液分离罐。自动收集冷凝液体,然后视需要人工从气液分离罐排出。未冷凝的气体通过人工背压调节器(BPR),然后通过水洗涤,并通气至通风橱。对于各实施例,将10ml催化剂(3mm丸)加载入反应器中。反应器入口和出口均用玻璃珠(3mm)填充以形成固定床。对于催化剂筛选使用下述操作条件:T=275℃,P=300psig(2068kPag),[进料]=0.138ml/min(泵速率),和[H2]=513sccm,气时空速(GHSV)=3367小时-1。用于测试的混合的进料组合物是69.92wt.%乙酸,20.72wt.%乙酸乙酯,5.7wt.%乙醇,2.45wt.%乙缩醛,0.65wt.%水,和0.55wt.%乙醛。粗产物通过配有火焰离子化检测器的气相色谱(AgilentGCModel6850)加以分析。除水外的液体产物流出物的GC分析结果提供于下表2中。丙酮以小于0.1wt.%的浓度检测到。然后计算催化剂性能结果,并提供于下表3中。实施例3的EtOAc转化率是2.93%,实施例5的EtOAc转化率是2.9%,实施例8的EtOAc转化率是0.59%,而实施例9的EtOAc转化率是5.3%。这展示改善的多功能催化剂,其可以有利地提供乙酸的高转化率和转化乙酸乙酯的能力。XRD表征来自实施例1-6的催化剂也通过X射线衍射(XRD)加以表征。样品的XRD图谱用RigakuD/MaxUltimaII粉末X射线衍射仪获得,采用CuKa辐射。X射线管于40kV和40mA进行操作。两种催化剂的XRD的主要相均鉴定为含有作为主要相的单斜CoWO4(钨酸钴)(ICSD-15851)。实施例1、2、3、6、7、8和9的催化剂的XRD图谱示于图2。实施例6的X射线衍射图谱基本上如表4所示:实施例6的催化剂包含单斜钨酸钴,其中所述催化剂具有X射线衍射图谱,其中在2θ=10°以上存在局部最大值,其在下述各位置具有特征的半峰全宽:13.48至13.88的2θ值;15.11至15.87的2θ值;18.55至19.33的2θ值;23.2至24.28的2θ值;24.15至24.97的2θ值;27.34至28.02的2θ值;28.48至28.78的2θ值;30.17至30.99的2θ值;30.94至31.78的2θ值;32.33至33.05的2θ值;35.80至36.84的2θ值;38.04至38.84的2θ值;40.79至41.77的2θ值;43.71至44.85的2θ值;45.46至45.96的2θ值;47.65至48.13的2θ值;48.45至48.93的2θ值;50.21至50.83的2θ值;51.50至52.38的2θ值;53.53至54.47的2θ值;61.30至62.10的2θ值;64.37至65.71的2θ值;68.07至69.25的2θ值;和71.21至72.27的2θ值。虽然详细描述了本发明,但在本发明的精神和范围内的各种修改对于本领域技术人员而言将是显而易见的。通过引用将上文论述的所有出版物和参考文献并入本文。此外,应理解引述的本发明的各个方面以及多个实施方案和多个特征的各个部分可以部分或全部地进行组合或者互换。在前述各个实施方案的描述中,如本领域技术人员所可认识到的,引用另一个实施方案的实施方案可以与其它实施方案适当地组合。此外,本领域技术人员将认识到前述描述仅仅是举例方式,并且不意欲限制本发明。