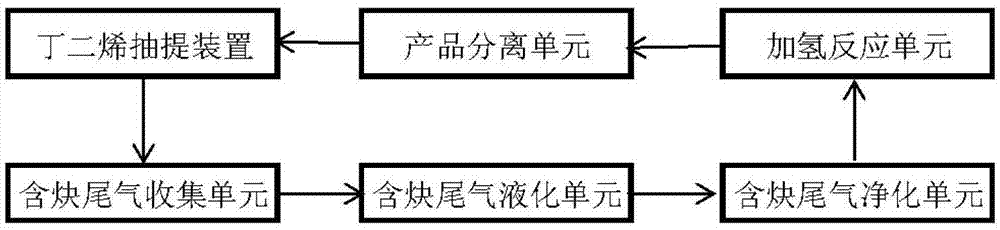
本发明属于石油化工
技术领域:
,具体涉及一种炔烃加氢选择性催化剂及其制备方法和应用。
背景技术:
丁二烯是一种重要的石油化工基础有机原料和合成橡胶单体,是碳四馏分中最重要的组分之一,在石油化工烯烃原料中的地位仅次于乙烯和丙烯。丁二烯最主要的来源是以乙烯装置副产的混合碳四为原料,通过溶剂抽提的方法分离得到。乙烯装置副产的混合碳四馏分通常含有40wt%~60wt%的丁二烯,0.5wt%~2.0wt%的炔烃,主要包括甲基乙炔(ma),乙基乙炔(ea)和乙烯基乙炔(va),其它为丁烷(正丁烷和异丁烷)和丁烯(正丁烯、异丁烯、反-丁烯-2和顺-丁烯-2)。目前工业上主要采用乙腈(acn)、n-甲基吡咯烷酮(nmp)或二甲基甲酰胺(dmf)为溶剂抽提丁二烯,抽提后的丁二烯可以满足其作为聚合单体纯度的要求。受裂解深度及裂解技术等因素的影响,混合碳四中炔烃含量有逐渐增加的趋势,为保证丁二烯纯度,需要加大抽提深度,这导致装置能耗增加,含炔尾气(主要组成为乙烯基乙炔、丁二烯和丁烯)排放量增大,丁二烯收率下降,装置经济性变差。由于含炔尾气中含有大量乙烯基乙炔(通常为20wt%~35wt%),易燃易爆风险大,工业应用价值不高,一般是用其它碳四烃或甲烷稀释后排入火炬燃烧或作为低价值燃料出售。如果将这部分含炔尾气进行处理,不仅可以回收大量的丁二烯和丁烯,还可消除含炔尾气排放带来的安全隐患,实现变废为宝的目的。含炔尾气处理主要是采用催化选择加氢的方法,利用高选择性加氢催化剂将尾气中含有的乙烯基乙炔转化为1,3-丁二烯,乙基乙炔转化为丁烯,另有少量丁烷生成。加氢后的含炔尾气分离不凝气后返回原料储罐与原料混合或直接返回到丁二烯抽提装置回收丁二烯和丁烯,从而提高丁二烯纯度,减少丁二烯损失,使含炔尾气得到很好的利用,并消除含炔尾气的排放。含炔尾气选择加氢技术的关键之一是催化剂,要求催化剂有较高的加氢活性、选择性,尤其要具有良好的运转稳定性,即不仅要将尾气中的炔烃脱除到较低水平(可直接返回丁二烯装置作为抽提原料),更要确保乙烯基乙炔尽量转化为1,3-丁二烯以最大量回收丁二烯,同时要求催化剂有较高的稳定性,有较好的耐水、溶剂、重组分等杂质的能力和长的运转稳定性以适应工业装置长周期运转的要求。目前含炔尾气选择加氢催化剂主要为贵金属催化剂和非贵金属催化剂,有单纯以钯或铜为活性组分的单金属催化剂,或者是以钯和铜等为活性组分的多金属催化剂。铜催化剂用于选择加氢除炔时,选择性较高,但由于反应温度高,二烯烃和炔烃易生成聚合物沉积在催化剂表面,因此催化剂失活快,使用寿命短。钯催化剂活性比铜催化剂高,使用条件缓和,因而寿命长,但是选择性比铜催化剂稍差,且钯容易与炔烃发生络合,造成钯的流失,一般通过添加助剂的方法来改善钯与炔烃的相互作用,延长催化剂的使用寿命。美国专利us3,898,298公开了一种pd/al2o3催化剂,活性组分钯含量为0.05~0.2wt%,载体为氧化铝,该催化剂通常用于炔烃含量较低(小于1.0wt%)的含炔碳四物料选择加氢,乙烯基乙炔加氢率通常超过90%,但1,3-丁二烯加氢损失率较大。美国专利us4,547,600公开了一种pd、ag双金属催化剂,该催化剂用于低炔烃含量(乙烯基乙炔约1.95%)物料加氢时,催化剂加氢活性高,乙烯基乙炔含量可降至300ppm左右,而用于中等炔烃含量(乙烯基乙炔约4.10%)物料加氢时,乙烯基乙炔转化率仅70%左右。同时该催化剂运转700多小时后,钯流失严重,流失率高达10%,因此该催化剂不适用于炔烃含量更高物料的加氢。专利cn201110205694.9公开了一种碳四炔烃选择加氢镍和铜双金属催化剂,镍和铜是采用可溶性盐的水溶液浸渍到载体上,由于活性组分含量高,催化剂对水、溶剂和重组分等杂质的耐受能力较强,但是反应的绝热温升较高,反应器出口温度超过80℃,这会加剧炔烃和二烯烃的聚合,影响催化剂长周期运转。该催化剂同样仅适用炔烃含量低的物料加氢。专利03159237.6公开了丁二烯装置残余物的利用方法,采用一段、双段或多段加氢工艺,将含炔物料处理后回收丁二烯、1-丁烯或作为燃料,其中炔烃选择加氢为丁二烯催化剂采用钯铜银或钯铜催化剂。该工艺每段反应器均有大量的产物进行循环,循环物料与新鲜物料的循环比10~30,大循环比增加了装置能耗。该工艺催化剂丁二烯选择性差,炔烃主要转化为丁烯,该专利公开的工艺及催化剂不适用于炔烃加氢回收丁二烯。专利cn103787811b公开了一种丁二烯尾气的加氢方法,采用液相烃将丁二烯尾气吸收后通过两段加氢用作乙烯裂解原料。一段加氢采用镍催化剂,8-30的大循环比,二段采用镍-钼催化剂高温加氢。该方法不仅能耗高,而且加氢产物只能作为乙烯裂解料使用。专利cn201410771106.1公开了一种炔烃选择加氢方法,采用氧化铌-氧化铝为载体的钯铅催化剂,要求含炔碳四物料中炔烃含量不超过25%,待加氢物料中炔烃含量不高于10%,当炔烃含量较高时,采用抽余碳四进行稀释。专利cn1,321,544a公开了一种用于选择加氢除炔的多金属催化剂,活性组分为铜和钯,载体用碱金属、碱土金属或其混合物处理,也可加入ag、pb、bi、zr、pt等助剂金属。催化剂只能处理炔烃含量低于1.3wt%的碳四馏分。该催化剂cu含量较高,在处理炔烃含量较高的物料时,操作温度较高,催化剂选择性和稳定性会较差。cn101,428,228a公开了一种选择性加氢催化剂及其制备方法,以氧化铝为载体,包含活性组分钯、助剂铜,助剂x1和助剂x2,以催化剂总重量100%计:含钯0.1~0.5%,铜0.1~6%,x10.5~15%,x20.5~5%,0~2%选自钴、镍、钼、钨、镧、银、铈、钐、钕中的一种或多种助剂金属;其中x1选自iva元素,x2选自碱金属、碱土金属或其混合物。催化剂中助剂元素的引入是通过浸渍载体或催化剂前体来实现的,催化剂适用于丁二烯抽提后富含炔烃残余物料的选择加氢除炔,但只能处理炔烃含量高、丁二烯含量低的碳四物料。结焦是导致催化剂失活的另一个重要原因之一,产生结焦的主要原因一是催化剂选择性不好,炔烃和二烯烃聚合等副反应太多,二是反应温度太高或者是绝热温升太高,导致不饱和烃在高温下聚合加剧。一旦生成胶质,则会覆盖活性中心或堵塞催化剂孔道,从而降低催化剂活性、选择性及稳定性,并最终导致催化剂失活无法正常运转。现有技术以钯为活性组分的催化剂由于易受加氢物料中水、溶剂及重组分等杂质干扰从而加氢活性尤其运转稳定性较差,为改善这一情况,通过浸渍的方法引入不同种类助剂,以促进钯的分散,并与钯产生协同效应提高催化剂选择性及稳定性。在现有技术中,用助剂的可溶性盐浸渍载体时,由于载体本身孔结构的不均匀性及难以实现浸渍条件控制的一致性等问题,助剂在催化剂中呈现非均匀分布,与钯的协同作用得不到充分发挥,导致催化剂加氢活性、选择性和稳定性很难达到平衡。尤其是ib和/或iva元素,特别是cu、ag、si、sn、pb等元素的引入,由于含量远高于钯含量,因此浸渍法并不是优选方案。技术实现要素:针对现有技术存在的缺陷,本发明提供一种炔烃加氢选择性催化剂及其制备方法和应用。本发明催化剂在引入ib和/或iva的cu、ag、si、sn、pb等元素时,根据这些元素与钯相互作用机理以及所要达到的目的而选择不同的引入方式,即一部分采用固-液相的浸渍方式引入,一部分采用在载体制备时的液-液相引入,并且合理分配两部分引入的比例,在催化剂活性、选择性及稳定性之间找到平衡,目的是使助剂组分在载体中的分布更加均匀,尤其是助剂组分含量高时,这种效果更加明显,从而提高催化剂的加氢活性和选择性(高达60%以上)、稳定性(1000h运转活性基本不降低,而且结焦率小于1.5%,钯基本不流失)。更重要的是,本发明催化剂由于活性高,选择性好,因此加氢条件温和,入口温度、绝热温升、操作压力及循环比低,特别适于高炔烃含量的含炔碳四物料加氢,尤其适于高丁二烯含量的含炔碳四物料加氢,经本发明催化剂及工艺处理后的含炔物料,可直接返回到抽提装置回收丁二烯和丁烯,增产丁二烯和丁烯,消除含炔尾气排放,提高装置经济效益。实现本发明目的的炔烃选择性加氢催化剂,按照重量百分比,以0.1~0.8%金属钯为活性组分,90~99%氧化铝为载体,添加有0~5%碱金属和/或碱土金属氧化物为改性助剂,0.05~10%ib和/或iva元素氧化物为助催化组分;其中催化剂各组分中,钯、碱金属和/或碱土金属以浸渍的方式引入,ib和/或iva元素中的一部分以浸渍的方式,另一部分在制备载体时引入;催化剂比表面积为20~100m2/g,孔容为0.15~0.75ml/g。其中,所述的载体形状为球形、齿球形、条形、三叶草形或通过挤条、压片或滚球等方式得到的其它形状载体,优选的三叶草形或的球形、齿球形。所述的碱金属为li、k、rb、cs中的一种或多种,优选为li、k,添加量为0.05~2.5%,优选为0.5~1.5%。所述的碱土金属为mg、ca、sr、ba中的一种或多种,优选为mg、sr,添加量为0.05~2.5%,优选为0.5~1.5%。所述的ib元素为cu、ag、au中的一种或多种,所述的ib元素的一部分是ag和/或au以浸渍的方式引入,添加量为0.1~3.0%,优选为0.5~2.0%;另一部分是cu在制备氧化铝载体时引入,添加量0.5~10%,优选为1.5~6.0%。所述的iva元素为si、ge、sn、pb中的一种或多种,所述的iva元素的一部分是pb和/或ge以浸渍的方式引入,添加量0.2~3.5%,优选为0.4~2.5%;另一部分是si和/或sn在制备氧化铝载体时引入,添加量为2.0~10%,优选为3.0~5.0%。本发明的炔烃选择性加氢催化剂的制备方法,按照以下步骤进行:a、载体制备:将铝源用水稀释浓度150~250gal2o3/l,搅拌下加入沉淀剂,在50~100℃成胶、洗涤、过滤、打浆,然后在50~100℃老化,再经过滤、干燥、焙烧后制得拟薄水铝石,在成胶和/或打浆过程中加入ib元素cu和/或iva元素si和/或sn得到可溶性盐溶液;取上述拟薄水铝石,加入硝酸、柠檬酸、田菁粉和水混合捏合,然后成型,80~150℃干燥10-12小时、750~1100℃焙烧8-12小时,制得成品氧化铝载体;b、载体改性:取成品氧化铝载体,测量其吸水率,按照吸水率和改性剂含量,配制碱金属和/或碱土金属水溶液,调整好溶液ph值,将成品氧化铝载体倒入溶液中浸渍,陈化、80~150℃干燥6~8h,750~1100℃焙烧4-8小时制得改性氧化铝载体;c、催化剂制备:按照催化剂中各组分含量及改性载体吸水率,配制钯溶液和/或ib元素ag和/或au的可溶性盐溶液和/或iva元素pb和/或ge的可溶性盐溶液,混合均匀后将ph值调整到2.5~6.0,将称量好的改性载体置于溶液中浸渍,陈化、80~150℃干燥6~8小时,350~600℃焙烧6~8小时,制得成品催化剂。其中,所述的铝源为氢氧化铝、硫酸铝、氯化铝、硝酸铝、偏铝酸钠中的一种或多种;所述的沉淀剂为偏铝酸钠、二氧化碳、碳酸钠、尿素、碳酸铵、碳酸氢铵中的一种或多种;所述的铜的可溶性盐选自硝酸铜、硫酸铜、氯化铜中的一种或多种;所述的si的可溶性盐选自硅酸钠、偏硅酸钠、硅溶胶中的一种或多种;所述的sn的可溶性盐选自氯化锡、氯化亚锡、硝酸锡中的一种或多种。所述的钯溶液是氯化钯、硝酸钯或醋酸钯溶液。所述的碱金属为li、k、rb、cs中的一种或多种,优选li和/或k,碱金属是以可溶性盐的形式引入;碱土金属为mg、ca、sr、ba中的一种或多种,优选mg和/或sr,碱土金属是以可溶性盐的形式引入。所述的浸渍液的ph值用氨水、碳酸氢钠、碳酸钠、碳酸钾、碳酸氢钾溶液来调整。本发明的炔烃选择性加氢催化剂,用于含炔碳四馏分中炔烃的选择加氢,按照以下步骤进行:乙烯基乙炔和乙基乙炔经加氢反应单元转化为丁二烯和丁烯,加氢产品从产品分离单元返回丁二烯抽提装置,回收丁二烯及丁烯或进入含炔尾气收集单元与原料混合,再次进行液化和净化,反应器为鼓泡式绝热固定床反应器,加氢反应采用两段加氢工艺,各段反应器入口温度20~80℃,优选为30-60℃,操作压力0.45~1.5mpa,优选0.60~1.0mpa,氢气/炔烃摩尔比0.5~2.5,优选0.8~1.5,新鲜料空速0.4~2.5h-1,优选0.8~1.5h-1,产品与新鲜料比例为2~8,优选3~6。本发明的炔烃选择性加氢催化剂用于等温固定床反应器。与现有技术相比,本发明的特点和有益效果是:本发明主要从以下方面来解决催化剂的结焦问题:一是通过添加碱金属和/或碱土金属改性剂修饰调控载体表面酸性,大幅降低易聚合的强酸性中心,二是添加助剂与活性金属钯形成较强的相互作用,以减弱催化剂初活性,因为反应初期的结焦对催化剂活性影响更加显著,通过采用一定的手段,在促进钯更好分散的同时与助催化剂组分及载体间形成较强的作用,产生协同效应,在提高选择性的同时降低结焦等副反应,从实施效果看,本专利制备的催化剂达到了这一效果。本发明催化剂,由于作为助催化组分的ib和/或iva元素氧化物是以不同方式引入的,部分会促进钯的分散,提高加氢活性,部分与钯形成合金或固溶体,增强钯与助催化组分、钯与载体之间的相互作用,从而提高加氢选择性及运转稳定性,抑制钯流失。本发明的特点在于:本发明的催化剂加氢活性高,选择性好,抗水、溶剂等杂质性能强,运转稳定性优异,催化剂制备方法简单易操作。1000h评价后催化剂性能基本不降低,结焦率小于1.5%,钯基本不流失。适用丁二烯抽提装置炔烃含量高的含炔碳四选择加氢或者丁二烯含量高的含炔碳四选择加氢,将乙烯基乙炔转化为丁二烯,乙基乙炔转化为丁烯,加氢产物可返回抽提装置直接回收丁二烯和丁烯,或者返回抽提装置原料储罐,与原料混合后一起作为抽提装置进料。本发明催化剂具有以下优点:一是加氢活性和选择性实现了较好的平衡,解决了催化剂存在的活性高选择性差或者选择性高活性差的不匹配问题。二是催化剂具有较高的加氢稳定性,胶质生成量少,耐水、溶剂及重组分波动能力强。三是催化剂使用条件温和,加氢反应在室温、较低压力下具有较好的加氢性能,尤其是循环比低,产品循环量少,减少了对催化剂的冲击,并降低装置能耗。四是活性组分钯分散度高,流失率低,运转周期长。五是本发明催化剂不仅适用于炔烃含量高的原料加氢,而且特别适用丁二烯含量高的含炔碳四物料加氢,可有效提高丁二烯装置进料中丁二烯潜含量,减小对丁二烯抽提装置的影响。碱金属和/或碱土金属主要起到修饰载体表面酸性和提高热稳定性的作用,ib和/或iva元素氧化物主要起到促进活性,改善选择性及降低结焦,提高抗杂质能力和延长运转稳定性的作用。附图说明图1是本发明的炔烃选择性加氢催化剂用于含炔碳四馏分中炔烃的选择加氢的流程图。具体实施方式:下面列举实施例并结合附图对本发明进行详细说明,但本发明不受这些实施例的限制。实施例1-10实施例1~10的炔烃选择性加氢催化剂载体为al2o3,各组分如表1所示,其制备过程为:a、载体制备:配制浓度为200gal2o3/l偏铝酸钠溶液1l,加热至70℃,配制浓度为80gal2o3/l硫酸铝溶液2l,加热至70℃;在成胶罐中加入1.0l蒸馏水,加热至70℃,并流加入上述两种浆液,保持ph值8.0,温度70℃进行成胶,在成胶过程中加入浓度为0.05mol/l的cu盐溶液和/或sn盐溶液和/或si盐溶液;成胶结束后在ph值8.0、温度70℃老化60min。老化结束后,注入65℃去离子水,在200rpm搅拌速率下对老化后的浆液进行打浆、洗涤、过滤,滤饼在100℃干燥3h后得到含cu和/或sn和/或si的拟薄水铝石;b、载体改性:将上述制得的拟薄水铝石、硝酸、柠檬酸、水等混合后捏合,挤条成型,120℃干燥4h、600℃焙烧6h制得载体,然后浸渍一定量的碱金属和/或碱土金属盐溶液,120℃干燥4h、1100℃焙烧4h制得含碱金属和/或碱土金属的载体;c、催化剂制备:配制硝酸钯、硝酸银和/或硝酸铅的溶液,调节ph值后浸渍载体,120℃干燥4h、500℃焙烧8h制得催化剂。实施例11-20实施例11~20的炔烃选择性加氢催化剂载体为al2o3,各组分如表1所示,其制备过程为:a、载体制备:在成胶罐中配制浓度为200gal2o3/l硝酸铝溶液1l,配制浓度为80gal2o3/l硫酸铝溶液1l,混合均匀加热至75℃;往成胶罐中通入co2气体,保持ph值8.0~8.5,温度75℃进行成胶,成胶结束后在ph值8.0、温度70℃老化60min;老化结束,注入75℃去离子水,洗涤后在200rpm搅拌速率下进行打浆,同时加入浓度为0.05mol/l的cu盐溶液和/或sn盐溶液和/或si盐溶液,打浆60min后过滤,滤饼在120℃干燥8h后得到含cu和/或sn和/或si的拟薄水铝石;b、载体改性:将上述制得的拟薄水铝石、硝酸、柠檬酸、水等混合后捏合,挤条成型,120℃干燥4h、650℃焙烧8h制得载体;然后浸渍一定量的碱金属和/或碱土金属盐溶液,120℃干燥4h、1060℃焙烧6h制得含碱金属和/或碱土金属的载体;c、催化剂制备:分别配制醋酸钯、硝酸银和/或醋酸铅的溶液,调节溶液ph值后浸渍载体,120℃干燥4h、450℃焙烧8h制得催化剂。实施例21-30实施例21~30的炔烃选择性加氢催化剂载体为al2o3,各组分如表1所示,其制备过程为:a、载体制备:配制浓度为200gal2o3/l硝酸铝溶液1l,配制浓度为80gal2o3/l硫酸铝溶液1l,将两种溶液混合后加热至50℃;在成胶罐中配制碳酸钠和碳酸氢铵的混合溶液并加热到60℃,将硝酸铝和硫酸铝的混合溶液加入到成胶罐中,保持ph值8.0~8.5,温度60℃进行成胶,在成胶过程中加入浓度为0.05mol/l的cu盐溶液和/或sn盐溶液和/或si盐溶液;成胶结束后在ph值8.0、温度60℃老化60min。老化结束后,注入75℃去离子水洗涤,然后在200rpm搅拌速率下进行打浆,同时再加入浓度为0.05mol/l的cu盐溶液和/或sn盐溶液和/或si盐溶液,继续打浆60min后洗涤,过滤,滤饼在130℃干燥8h后得到含cu和/或sn和/或si的拟薄水铝石;b、载体改性:将上述制得的拟薄水铝石、硝酸、柠檬酸、水等混合后捏合,挤条成型,120℃干燥4h、650℃焙烧8h制得载体,然后浸渍一定量的碱金属和/或碱土金属盐溶液,120℃干燥4h、950℃焙烧6h制得含碱金属和/或碱土金属的载体;c、催化剂制备:然后分别配制硝酸钯、硝酸银和/或硝酸铅的溶液,调节溶液ph值后浸渍载体,120℃干燥4h、600℃焙烧8h制得催化剂。实施例1~30的炔烃选择性加氢催化剂,用于含炔碳四馏分中炔烃的选择加氢,如图1所示,按照以下步骤进行:乙烯基乙炔和乙基乙炔经加氢反应单元转化为丁二烯和丁烯,加氢产品从产品分离单元返回丁二烯抽提装置,回收丁二烯及丁烯或进入含炔尾气收集单元与原料混合,再次进行液化和净化,反应器为鼓泡式绝热固定床反应器,加氢反应采用两段加氢工艺,各段反应器入口温度20~80℃,优选为30-60℃,操作压力0.45~1.5mpa,优选0.60~1.0mpa,氢气/炔烃摩尔比0.5~2.5,优选0.8~1.5,新鲜料空速0.4~2.5h-1,优选0.8~1.5h-1,产品与新鲜料比例为2~8,优选3~6。对比例1-5对比例1~5组分如表1所示,取al2o3载体在550℃焙烧8h,然后浸渍一定量碱金属和/或碱土金属盐溶液,120℃干燥4h、1060℃焙烧6h制得含碱金属和/或碱土金属的载体;然后浸渍一定量的含cu和/或含sn和/或含si溶液,120℃干燥4h、500℃焙烧后再浸渍硝酸钯、硝酸银和/或硝酸铅,120℃干燥4h、500℃焙烧8h制得催化剂。对比例6-10对比例6~10组分如表1所示,将拟薄水铝石、硝酸、柠檬酸、水、含cu和/或含sn和/或含si溶液混合捏合,挤条成型,120℃干燥、550℃焙烧4h,制得氧化铝载体;然后浸渍一定量碱金属和/或碱土金属盐溶液,120℃干燥4h、1000℃焙烧6h制得含碱金属和/或碱土金属的载体;然后浸渍一定量的硝酸钯、硝酸银和/或硝酸铅,120℃干燥4h、500℃焙烧8h制得催化剂。对实施例1~30及对比例1~10所制得的催化剂的催化能力进行评价,评价条件为:采用绝热鼓泡固定床反应器,单段或两段加氢工艺,反应器入口温度30~45℃,反应压力0.8~1.0mpa,h2/va摩尔比0.75~2.0,新鲜料液时空速1.0~2.0h-1,催化剂装填量50ml。反应工艺流程:碳四馏分经计量泵计量后升至反应压力,经预热后与氢气混合从反应器下部进入催化剂床层,反应产物冷却后进行气液分离,分离后的不凝气放空,液体排入产品罐。当采用两段加氢时,一段加氢产物不经分离直接进入二段反应器,二段反应器根据产品中炔烃含量配入氢气。催化剂还原:评价前,120℃,1.0mpa,通氢气还原8小时,氢气空速100h-1。催化剂再生:经1000h评价后的催化剂卸下,在马弗炉中通空气550℃焙烧4小时。采用气相色谱分析原料及产品组成。本实施例中炔烃加氢率和丁二烯选择性按如下公式计算:实施例及对比例催化剂具体评价条件和结果见表1。表1实施例和对比例催化剂评价结果采用两段加氢工艺,将实施例14制得的催化剂分别装填在一、二段反应器,每个反应器装填催化剂50ml。在反应器入口温度30℃,操作压力0.95mpa,一段h2/va(mol)=1.0,二段h2/va(mol)=0.8,新鲜料空速1.2~1.5h-1条件下,累计评价1000小时,催化剂性能评价结果见表2。表2实施例14催化剂1000h评价结果1000小时评价后的催化剂、再生催化剂与新鲜催化剂分析测试结果见表3。表3实施例14催化剂测试结果新鲜剂1000h评价后再生剂钯含量(wt%)0.40-0.395比表面积(m2/g)52.540.850.4结焦率(wt%)-1.45-从表1~表3的结果对比可以看出,本发明是市里的制备的催化剂的转化率与对比例相当,且选择性更好,长时间使用后的钯含量和比表面积无显著变化,证明其稳定性优异。当前第1页12