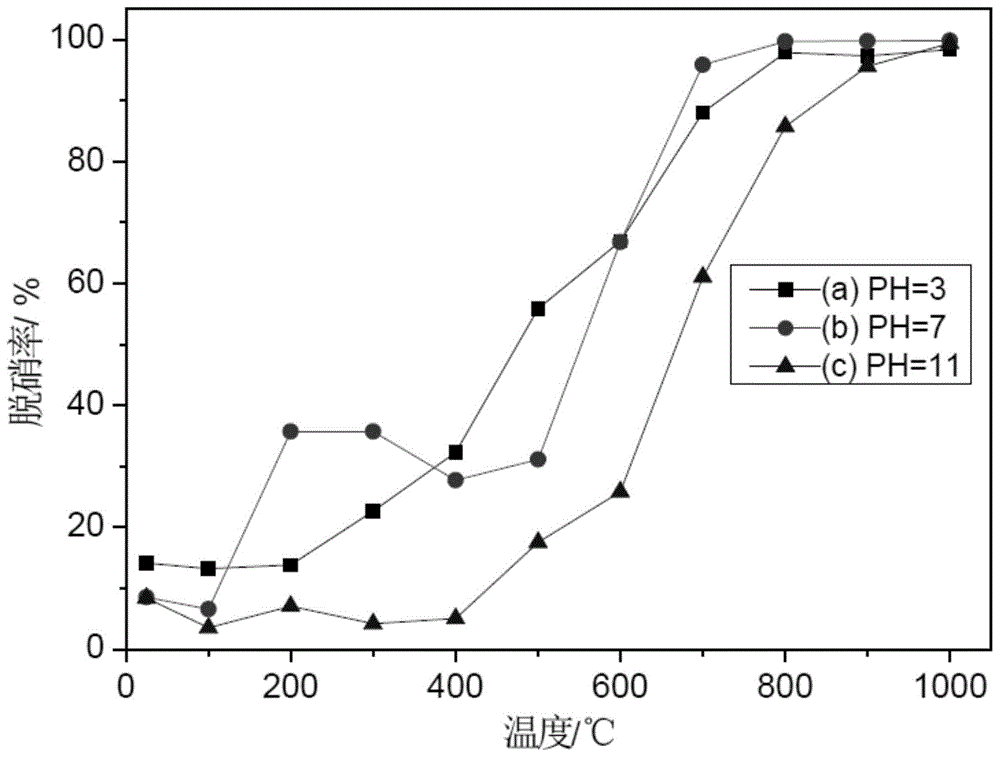
本发明涉及一种结合水泥生产工艺,利用工业废渣去除氮氧化物的方法,具体涉及一种使用镍渣制备可适用于水泥窑炉中的脱硝材料及其脱硝方法,属于工业窑炉烟气脱硝处理
技术领域:
。
背景技术:
:氮氧化物(nox)作为大气污染物之一,对人体健康、生态系统和建筑设施都有直接和潜在的危害。nox的主要来源是化石燃料的燃烧,主要包括机动车尾气、工业生产产生的氮氧化物等。水泥窑炉氮氧化物的排放量仅次于火电厂和机动车尾气,成为第三大污染源。目前,比较成熟的水泥窑炉脱硝技术有低氮燃烧控制技术、选择性催化还原技术(scr)和选择性非催化还原技术(sncr)。低氮燃烧技术成本较低,但脱硝效率低,一般不超过30%,无法达到国家的排放标准。sncr脱硝技术是利用nh3、尿素等做还原剂,在800~1000℃内与nox反应生成n2。脱硝效率低,一般为30%~50%,且液氨消耗量较大(氨氮比约为1.6)。scr脱硝技术是指在催化剂的作用下,利用还原剂(如nh3、尿素)与nox反应生成n2和h2o。当前scr催化剂的价格较高,性能不太稳定,易出现催化剂中毒,导致催化剂的使用寿命短。且scr和sncr这两种脱硝技术都需要使用氨气或尿素作为还原剂,需要储氨(尿素)和喷氨(尿素)装置,占地面积大,反应装置复杂,投资成本及运行成本高,且可能会出现氨逃逸现象,造成二次污染。因此,选择成本低,不使用氨气或尿素等还原剂且具有较高的脱硝率的脱硝材料,具有重要意义。镍渣是在冶炼镍过程中所形成的以feo、sio2为主要成分的熔融物经水淬后形成的粒化炉渣,是排放量最大的工业废渣之一。根据我国镍生产工艺,每生产1t镍约排出6~16t镍渣。在目前对镍渣的处置方式都是堆存闲置,由于长期得不到合理利用,国内堆存的镍渣已达到4000万吨,每年还新增约200万吨。堆存闲置不仅占用土地,对周边环境造成严重污染,并对人类健康造成极大危害,而且镍渣中有价组分也得不到循环利用。因此,在处理镍渣时尽可能保留活性组分fe,去除杂质元素ca,mg等,使其具有较好的脱硝作用,节约成本的同时,也实现对镍渣的资源化利用。本发明旨在利用镍渣为原料,制备一种高比表面积的脱硝材料,且结合水泥生产工艺,将此脱硝材料直接喷入水泥窑炉中,随着物料进入预热器和分解炉中,在不使用氨气或尿素等还原剂时,随窑炉内温度的升高,达到较高脱硝率的方法。技术实现要素:针对以上问题,本发明以镍渣为原料研制出一种适合水泥窑炉脱硝无机多孔材料,再结合水泥生产工艺,在不使用氨水或尿素等还原剂下达到较高脱硝率的方法。(1)以镍渣为原料制备适用于水泥窑炉的脱硝材料的方法,其特征在于,包括以下步骤:以镍渣为原料制备多孔脱硝材料,将镍渣粉末与稀释后的盐酸溶液混合搅拌2h,镍渣粉末与盐酸溶液混合比例为10g镍渣粉末混合于60ml浓度为3mol/l的稀释盐酸;加入氢氧化钠碱溶液调节ph为3~11后,搅拌30min;离心洗涤三次以上,将分离出的沉淀物置于80℃干燥箱中干燥12h,制得多孔脱硝材料。进一步,氢氧化钠溶液的浓度为2mol/l。(2)在烟气条件为1000ppmno,n2为平衡气,气体流速为300ml/min,温度条件为25℃~1000℃时脱硝。脱硝方法,将制备的多孔脱硝材料置于脱硝测试装置中测试其脱硝效率。以n2为平衡气,催化剂用量为2ml,烟气组成为ω(no)=1000ppm,在室温25℃升温至1000℃,在不同温度点测定出口烟气的成分及含量,计算出随温度变化脱硝率的变化,从而表征出多孔材料的脱硝性能,在高温温度区域700℃~1000℃多孔材料的脱硝率较高,基本达到80%以上,最高可达99.8%。(3)将利用镍渣制备的多孔脱硝材料与水泥生料以不同比例混合,测试混合后试样在高温度700℃~1000℃的脱硝效率,当多孔材料所占质量比为1%~5%时,在测得脱硝率仍达80%以上。其中脱硝材料占混合料质量比为3%-5%,在700℃~1000℃温度范围内脱硝更高。本发明的优点为:一是采用工业废渣之一的镍渣为原料,使用简单的化学处理得到高比表面积的多孔脱硝材料,工业废渣再利用,真正实现变废为宝。二是本发明不使用氨水或尿素等还原剂,避免了氨水或尿素等还原剂储运过程中的安全隐患及二次污染问题;同时本发明将水泥生料与所制备多孔材料混合喷入水泥窑炉中,无需增加多余的装置,也无需对现有窑炉改造,操作简单且成本较低。且测定了利用镍渣制备的多孔脱硝材料在25℃~1000℃温度条件下的脱硝效率表明,在高温区700℃~1000℃多孔材料的脱硝率较高,基本达到80%以上,最高可达99.8%。附图说明图1是本发明部分实施例1、实施例2和实施例3的脱硝率具体实施方式下面结合实施例对本发明作进一步说明,但本发明并不限于以下实施例。实施例1将10g镍渣粉末与60ml浓度为3mol/l的盐酸溶液混合,室温搅拌2h后,在持续搅拌中,滴加2mol/l的naoh溶液,调节ph为3,搅拌30min;离心分离出底部沉淀,洗涤3次后,80℃干燥12h,制得脱硝材料粉末。模拟烟气成分1000ppmno,n2为平衡气,气体流速为300ml/min,在25℃~1000℃的温度范围内测试脱硝效率,随温度升高脱硝率增大,在高温区700℃~1000℃脱硝率较高基本在85%,最高脱硝率为98.3%,脱硝率随温度变化曲线见图1(b)。实施例2将10g镍渣粉末与60ml浓度为3mol/l的盐酸溶液混合,室温搅拌2h后,在持续搅拌中,滴加2mol/l的naoh溶液,调节ph为7,搅拌30min;离心分离出底部沉淀,洗涤3次后,80℃干燥12h,制得脱硝材料粉末。模拟烟气成分1000ppmno,n2为平衡气,气体流速为300ml/min,在25℃~1000℃的温度范围内测试脱硝效率,在高温区700℃~1000℃脱硝率较高基本在95%,最高脱硝率为99.8%,脱硝率随温度变化曲线见图1(b)。实施例3将10g镍渣粉末与60ml浓度为3mol/l的盐酸溶液混合,室温搅拌2h后,在持续搅拌中,滴加2mol/l的naoh溶液,调节ph为11,搅拌30min;离心分离出底部沉淀,洗涤3次后,80℃干燥12h,制得脱硝材料粉末。模拟烟气成分1000ppmno,n2为平衡气,气体流速为300ml/min,在25℃~1000℃的温度范围内测试脱硝效率,在高温区800℃~1000℃脱硝率为85%,最高脱硝率为99.4%,脱硝率随温度变化曲线见图1(c)。实施例4脱硝材料的制备如实施例2所述,将制备的脱硝材料与水泥生料按照一定的质量比混合,多孔材料与水泥生料混合比例为3%:97%,使用研钵将多孔材料与水泥生料研磨均匀后,将2ml混合试样装入脱硝试验管中。在烟气条件为1000ppmno,n2为平衡气,气体流速为300ml/min,脱硝温度为700~1000℃,利用脱硝设备测试多孔材料与水泥生料混合后的脱硝率基本为60%以上(如表1)。实施例5脱硝材料的制备如实施例2所述,将制备的脱硝材料与水泥生料按照一定的质量比混合,多孔材料与水泥生料混合比例为5%:95%,使用研钵将多孔材料与水泥生料研磨均匀后,将2ml混合试样装入脱硝试验管中。在烟气条件为1000ppmno,n2为平衡气,气体流速为300ml/min,脱硝温度为700~1000℃,利用脱硝设备测试多孔材料与水泥生料混合后的脱硝率仍较高,保持在90%以上(如表1)。表1.实施例4和实施例5的脱硝率/%700℃800℃900℃1000℃实施例464.8381.0292.4596.63实施例593.7695.3497.8296.95当前第1页12