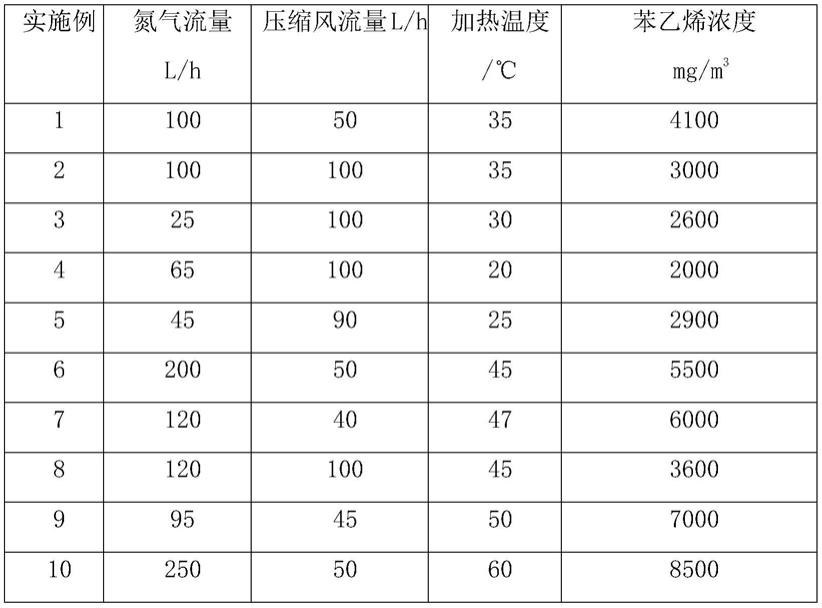
[0001]
本发明涉及苯乙烯废气处理技术领域,具体涉及一种用于苯乙烯废气处理的氧化催化剂及其制备方法和应用。
背景技术:[0002]
苯乙烯单体化学性质活泼,是一种重要的聚合单体,它可以自身聚合或与其他单体聚合,广泛用于合成高分子材料、涂料、医药等领域。苯乙烯在环境温度下就可以发生缓慢的热激发聚合反应。在废气处理中,苯乙烯属于挥发性有机化合物及恶臭气体。挥发性有机化合物(简称vocs)是一大类有机废气,通常指常温下饱和蒸汽压大于70pa,常压下沸点小于260℃的有机化合物。主要包括烃类、苯及其衍生物、酚及其衍生物、醇类、醛类与酮类等。苯乙烯属于典型的单环芳香类vocs,通过呼吸会对人体粘膜、肝、肾、肺和神经系统产生毒性和致癌性。2017年7月1日起实施的石化工业污染物排放标准gb 31571-2015明确限定苯乙烯排放浓度不超过50mg/m3。
[0003]
在苯乙烯的生产、储存、装车过程中,随着产品储罐液面上升,气体空间体积逐渐缩小,油气逐渐排出,再加上工艺设备等因素,实际操作时也存在废气外泄漏的情况,装车尾气和生产装置直排气中,苯乙烯含量都达不到国家规定的排放标准,需要进行回收处理,从根本上解决废气污染环境的问题。
[0004]
挥发性有机化合物常用的治理方法包括吸收、吸附、氧化、冷凝、燃烧、膜分离法,废气中有价值的有机物回收方法一般采用冷凝、吸附、氧化、膜分离法或他们的组合方法等。由于苯乙烯废气处理过程中存在易聚合的难题,目前炼化企业在苯乙烯储、运过程中产生的大量苯乙烯废气,大多未经处理直接排放,污染环境、存在巨大隐患。
[0005]
cn201310265450涉及一种高浓度间歇排放有机废气处理工艺,利用一种酸性吸附液,向其中适时加入氧化剂naclo或naclo3溶液作为废气吸收液,吸附后接活性炭吸附反应器,分解出的气体氧化剂、废气中的有机物可在吸附剂上发生氧化反应,生成液相产物而使气体净化。该发明采用氧化和吸附两段工艺处理废气,吸附剂可作为有机物或氧化剂的缓冲容器,以适用于不稳定的废气排放量和浓度,可用于含硫化氢、硫醇、硫醚、氨的挥发性有机物废气的处理。但该专利所用的氧化剂溶液ph值不稳定,虽然在弱酸条件下氧化反应能力强,但弱酸条件下氯气释放快,因此只能在弱碱性条件下使用,虽防止了氯气释放,但氧化反应速度慢。
技术实现要素:[0006]
针对现有技术的上述不足,本发明提供一种用于苯乙烯废气处理的氧化催化剂及其制备方法和应用,以次氯酸钠溶液为氧化剂,以有机酸盐、有机酸及烷氧基苯酚化合物作为氧化催化剂,在氧化催化剂各组分的协同作用下,使次氯酸钠溶液组成及ph值稳定,在弱酸条件下氧化反应能力强并避免了大量氯气的释放,打破了传统的弱酸条件下氯气释放快、只能在弱碱性条件下防止氯气释放的模式,提高了氧化反应速度。解决了现有的苯乙烯
废气氧化处理中氧化剂氧化能力低的难题,经济可行。
[0007]
本发明的技术方案为:
[0008]
用于苯乙烯废气处理的氧化催化剂,包括a、b和c三种组分,a组分是有机酸盐,b组分是有机酸,c组分为烷氧基苯酚类化合物,以质量份数计,各组分的配比为a组分20~90份,b组分1~35份,c组分100份。
[0009]
进一步地,a组分30~75份,b组分5~25份,c组分100份。
[0010]
进一步地,所述a组分为环烷酸盐、苯甲酸盐、柠檬酸盐及酒石酸盐中的一种或多种的混合物;所述b组分为环烷酸、苯甲酸、柠檬酸或酒石酸;所述c组分为3-叔丁基-4-羟基甲氧基苯酚,3-叔丁基-4-羟基乙氧基苯酚,2,6-二叔丁基-4-甲氧基苯酚,对叔丁基邻苯二酚中的一种或多种的混合物。
[0011]
进一步地,所述a组分为钠盐、钾盐或钴盐。
[0012]
进一步地,所述a组分为柠檬酸盐,b组分为柠檬酸,c为组分为3-叔丁基-4-羟基甲氧基苯酚,或者a组分为酒石酸盐,b组分为酒石酸,c组分为对叔丁基邻苯二酚。
[0013]
进一步地,还包括溶剂和分散剂,所述溶剂和分散剂为多元醇或醇醚类化合物,如乙二醇,丙二醇,丙三醇,乙二醇单丁醚;也可以是烷基苯类化合物,如甲苯,乙苯等。
[0014]
本发明的氧化催化剂,a组分有机酸盐为主催化剂,b组分有机酸和c组分烷氧基苯酚类化合物为助催化剂。其中,当使用次氯酸钠溶液作为处理苯乙烯废气的氧化液时,其ph值是不固定的,且不同ph值条件下次氯酸钠溶液的氧化性也是不同的,即次氯酸钠溶液的氧化性受ph值影响。因此,本发明的氧化催化剂中,b组分作为ph调节剂,c组分作为稳定剂,用于调节稳定次氯酸钠溶液的ph值。最终,在a、b、c三种组分的协同作用下,次氯酸钠溶液的ph值稳定,不会随氧化反应的进行而变化,在弱酸条件下氧化反应能力强并避免了大量氯气的释放,打破了传统的在弱碱性条件下进行氧化反应的模式,使次氯酸钠溶液的ph值在不同反应条件下稳定在较佳范围内。
[0015]
本发明还提供了一种用于苯乙烯废气处理的氧化催化剂的制备方法,将前述的a、b和c三种组分在室溫下充分混合均匀,即得氧化催化剂。
[0016]
进一步地,在氧化催化剂中加入多元醇、醇醚类化合物或烷基苯类化合物,加入量不超过氧化催化剂总量的30%。
[0017]
本发明还提供了一种苯乙烯废气的处理方法,包括以下步骤:
[0018]
(1)苯乙烯废气进入包括氧化反应塔、储液槽和水洗塔的氧化反应系统,以玻璃分馏柱作为氧化反应塔,烧瓶作为储液槽。氧化反应塔上端设有出气口、氧化液进料口和循环液进料口,下端设有进气口和出料口,出料口连接储液槽;从氧化反应塔的氧化液进料口进入的次氯酸钠氧化液,与从进气口进入的苯乙烯废气逆流接触完成氧化反应,反应完的废气由上端出气口排出,反应完的次氯酸钠溶液则从出料口进入储液槽,与采用前述制备方法制备得到的氧化催化剂混合;储液槽中的次氯酸钠溶液一部分排出,一部分通过机械隔膜泵循环至氧化反应塔的循环液进料口,与从进气口进入的苯乙烯废气逆流接触再次完成氧化反应,以提高氧化效率,降低次氯酸钠溶液的消耗量;内部填充有陶瓷环填料;
[0019]
(2)从氧化反应塔上端排出的苯乙烯废气经管线从下入口进入水洗塔,水从顶部上入口进入,与苯乙烯废气逆流接触,并进行外循环,进一步脱除苯乙烯废气以及分解的极少量氯气,避免造成气体的二次污染,苯乙烯废气从水洗塔塔顶排出,可实现达标排放。
[0020]
在氧化反应过程中,次氯酸钠溶液液与苯乙烯废气接触,苯乙烯废气大部分先溶解或附着在溶液中成为液相苯乙烯,再被氧化;c组分的加入,其酚羟基的氢先被氧化成较稳定的半醌式自由基,猝灭一个较活泼的自由基;再进一步氧化成更稳定的醌,又猝灭一个较活泼的自由基。即苯乙烯聚合是自由基聚合,c组分加入后,猝灭较活泼的自由基,可以达到抑制自由基聚合的目的,起到阻聚作用,从而使苯乙烯在聚合前即被氧化,减少聚合损失,提高了氧化效率。
[0021]
进一步地,步骤(1)中,所述陶瓷环填料的直径为3~6cm,填料的高度为氧化反应塔长度的60%~80%,氧化反应塔中每隔2~20厘米高度布置一个分布器,分布器上布满直径为1~3厘米的小孔,小孔呈菱形排列,使气液充分接触,提高氧化效率。
[0022]
进一步地,步骤(1)中,所述氧化反应塔的长径比为(10~30):1,氧化催化剂的加入量为次氯酸钠溶液的0.1%~5%,从氧化液进料口添加的次氯酸钠溶液的浓度为6%~15%,次氯酸钠溶液的循环浓度为7~10%,ph值为3~9,氧化反应温度为20℃~50℃,苯乙烯废气与次氯酸钠溶液的体积比为(10~100):1。
[0023]
进一步地,步骤(1)中,所述氧化反应塔的长径比为10~15:1,氧化催化剂的加入量为次氯酸钠溶液的0.8%~3%,次氯酸钠溶液的循环量与排出量的比例为(0.5~10):1,次氯酸钠溶液的循环ph值为5~7;氧化反应温度为25℃~50℃,苯乙烯废气与次氯酸钠溶液的体积比为(20~70):1。
[0024]
进一步地,步骤(2)中,所述水洗塔长径比(5~10):1,水洗温度20℃~60℃,水循环量与苯乙烯废气的体积比为(1~50):1。
[0025]
进一步地,步骤(2)中,水洗温度为25℃~45℃,水循环量与苯乙烯废气的体积比为(1~30):1。
[0026]
进一步地,水循环量与苯乙烯废气的体积比为(5~20):1。
[0027]
进一步地,步骤(2)中,所述水洗塔中设有2~6片折流板,将水洗塔中的水和气体分布均匀,提升水洗效果。
[0028]
本发明的有益效果在于:
[0029]
1.本发明的氧化催化剂,充分利用了三种组分之间的协同作用,使次氯酸钠溶液组成及ph值稳定,在弱酸条件下氧化反应能力强并避免了大量氯气的释放,打破了传统的弱酸条件下氯气释放快、只能在弱碱性条件下防止氯气释放的模式,提高了氧化反应速度。同时,c组分酚羟基的氢先被氧化成较稳定的半醌或醌式自由基,猝灭一个较活泼的自由基,从而避免了苯乙烯在氧化前即部分聚合,提高了氧化效率。
[0030]
2.本发明的苯乙烯废气的处理方法,采用氧化反应+水洗的处理工艺,在氧化反应塔中布置多个分布器,使气液充分接触,提高氧化效率。将次氯酸钠氧化液循环使用,有效降低了次氯酸钠溶液的消耗量。通过水洗工艺,在进一步脱除气体中少量的苯乙烯废气的同时,有效防止了气相中夹带氯气,避免造成气体二次污染,确保处理后的废气达到国家排放标准。整个工艺运行具有氧化效率高、安全可靠的特点,实现了易聚合的苯乙烯废气的安全脱除。
附图说明
[0031]
为了更清楚地说明本发明实施例或现有技术中的技术方案,下面将对实施例或现
有技术描述中所需要使用的附图作简单地介绍,显而易见地,对于本领域普通技术人员而言,在不付出创造性劳动的前提下,还可以根据这些附图获得其他的附图。
[0032]
图1是本发明中氧化反应系统的连接示意图。
[0033]
图中,1-氧化反应塔、2-储液槽、3-水洗塔、4-机械隔膜泵、5-不锈钢反应器、6-混合器。
具体实施方式
[0034]
为了使本技术领域的人员更好地理解本发明中的技术方案,下面将结合本发明实施例中的附图,对本发明实施例中的技术方案进行清楚、完整地描述,显然,所描述的实施例仅仅是本发明一部分实施例,而不是全部的实施例。基于本发明中的实施例,本领域普通技术人员在没有做出创造性劳动前提下所获得的所有其他实施例,都应当属于本发明保护的范围。
[0035]
实施例1~10苯乙烯废气的制备
[0036]
在1升带搅拌的不锈钢反应器5中加入700ml苯乙烯,电加热温度20~60℃,反应器中鼓入氮气,产生含苯乙烯的气体,作为苯乙烯废气源。产生的苯乙烯废气通过管线与压缩风分别通入装有φ6
×
6陶瓷填料的混合器6中,在混合器6中苯乙烯气体与压缩风混合均匀。其中,氮气和压缩风各通过气体转子流量计计量,通过调节加热温度以及不同气体压力与流量,可得到不同的苯乙烯废气浓度。其中,电加热温度优选为25℃~45℃,氮气与压缩风的配比是(0.25~5):1,最好为(0.5~3):1,在此范围内得到的混合气体中苯乙烯气体的含量在2000~8500mg/m3范围内可调。
[0037]
不同条件下产生的混合气体中苯乙烯气体含量如表1所示:
[0038]
表1
[0039]
[0040]
由此可见,通过调节加热温度、氮气与压缩风流量,可得到不同含量的苯乙烯废气,满足各种试验要求。
[0041]
实施例11~19不同氧化催化剂配方的苯乙烯废气氧化处理
[0042]
按照实施例1~10的方法制备不同浓度的苯乙烯废气,随后进入氧化反应系统。氧化反应系统包括氧化反应塔1、储液槽2和水洗塔3,以玻璃分馏柱作为氧化反应塔1,以烧瓶作为储液槽2,储液槽2体积2l。氧化反应塔1上端设有出气口、氧化液进料口和循环液进料口,下端设有进气口和出料口,出料口连接储液槽2;从氧化反应塔1的氧化液进料口进入的次氯酸钠氧化液,与从进气口进入的苯乙烯废气逆流接触完成氧化反应,反应完的废气由上端出气口排出,反应完的次氯酸钠溶液则从出料口进入储液槽2,与按表2的配比加入到储液槽2的氧化催化剂混合;储液槽2中的次氯酸钠溶液一部分排出,一部分通过机械隔膜泵4循环至氧化反应塔1的循环液进料口,与从进气口进入的苯乙烯废气逆流接触再次完成氧化反应。
[0043]
从氧化塔上端排出的气体经管线从下入口进入水洗塔3,水从顶部上入口进入,与苯乙烯废气逆流接触,并进行外循环,进一步脱除苯乙烯气以及分解的极少量氯气,处理后的苯乙烯废气从水洗塔3塔顶排出。
[0044]
使用了不同氧化催化剂的苯乙烯氧化处理结果如表2所示:
[0045]
表2中a1表示环烷酸,a1na、a1k、a1co分别代表环烷酸的钠、钾、钴盐;a2表示苯甲酸,a2na、a2k、a2co分别代表苯甲酸的钠、钾、钴盐;a3表示柠檬酸,a3na、a3k、a3co分别代表柠檬酸的钠、钾、钴盐;a4表示酒石酸,a4na、a4k、a4co分别代表酒石酸的钠、钾、钴盐;c1为3-叔丁基-4-羟基甲氧基苯酚,c2为3-叔丁基-4-羟基乙氧基苯酚,c3为2,6-二叔丁基-4-甲氧基苯酚,c4为对叔丁基邻苯二酚。
[0046]
表2
[0047]
[0048]
[0049][0050]
从表2的各实施例和对比例3可以看出,采用本发明的氧化催化剂用于处理苯乙烯废气时,即使废气中苯乙烯废气含量达到8500mg/m3,处理后排放的苯乙烯废气含量仍可满足50mg/m3的国家排放标准。同时,未加本发明的氧化催化剂时,苯乙烯废气的去除率仅61.1%,说明本发明的氧化催化剂提高了氧化效率。
[0051]
从表2的各实施例和对比例1和2可以看出,改变催化剂配方,少加其中一种组分,苯乙烯去除率都明显下降,表明各组分协同作用显著,带来了有益的效果,苯乙烯去除率达到98.3%以上。
[0052]
此外,本发明的氧化催化剂对次氯酸钠溶液的氧化能力及稳定性的的影响还表现在其能够分解生成的氯气。检测实施例12-14的水洗塔出口氯气的浓度,并设对比例,其中对比例与相应实施例除了氧化催化剂和次氯酸钠溶液的循环ph不一致外,其他反应条件都相同,试验处理结果如表3所示:
[0053]
表3
[0054]
[0055][0056]
可见,本发明的复合氧化催化剂体系,充分利用组份之间的协同作用,使得次氯酸钠溶液在弱酸条件下氧化能力强并避免了大量氯气的释放,打破了传统的弱酸条件下氯气释放快、只能在弱碱性条件下使用以防止氯气释放的模式。
[0057]
实施例20~27不同分布器及水洗塔设置的苯乙烯气体处理
[0058]
在苯乙烯进口浓度6000mg/m3条件下,氧化反应塔1长60cm,内径30mm,柱内填充直径为4cm的陶瓷环填料,陶瓷环填料的高度为氧化反应塔1长度的80%。次氯酸钠溶液的循环量与排出量比为8:1,氧化反应温度35℃,次氯酸钠溶液浓度10%,苯乙烯废气与次氯酸钠溶液的体积比为50:1。水洗塔3长60cm,内径100mm,水循环量与苯乙烯废气体积比为20:1,水洗温度40℃。氧化催化剂配比为:a3co:a3:c1=70:40:100,加入量为3%。
[0059]
不同分布器及水洗塔3设置的苯乙烯废气处理结果见表4,其中,对比例8和9的苯乙烯废气进口浓度分别为2000mg/m3、3000mg/m3:
[0060]
表4
[0061]
[0062][0063]
由表4的各实施例和对比例7-9可知,在苯乙烯进口浓度为2000mg/m3、3000mg/m3条件下,没有分布器时,出口苯乙烯浓度小于50mg/m3;而在苯乙烯进口浓度高达6000mg/m3条件下,没有分布器时,出口苯乙烯浓度大于50mg/m3,在氧化反应塔1有分布器时,出口苯乙烯废气的浓度则达到了排放要求。说明分布器的设置,能够使气液充分接触,提高氧化效率。
[0064]
由对比例10和11可知,不设置水洗塔3时,出口检测出氯气,表明采用水洗塔3工艺能够有效防止气相中夹带的氯气,避免了二次污染。
[0065]
尽管通过参考附图并结合优选实施例的方式对本发明进行了详细描述,但本发明并不限于此。在不脱离本发明的精神和实质的前提下,本领域普通技术人员可以对本发明的实施例进行各种等效的修改或替换,而这些修改或替换都应在本发明的涵盖范围内/任何熟悉本技术领域的技术人员在本发明揭露的技术范围内,可轻易想到变化或替换,都应涵盖在本发明的保护范围之内。因此,本发明的保护范围应所述以权利要求的保护范围为准。