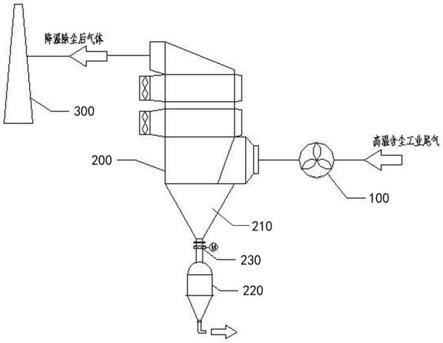
1.本发明属于工业尾气处理技术领域,涉及一种工业尾气降温除尘的方法,尤其涉及一种工业尾气降温除尘的装置系统及其降温除尘的方法。
背景技术:2.近年来,随着烟气净化环保领域中干法脱硫脱硝方法的不断推广,活性炭/焦的需求量激增,从而进一步扩大了活性炭/焦生产企业的产出规模。目前我国活性炭/焦生产企业的规模普遍偏小,且以往活性炭/焦生产行业对高温含尘工业尾气的排放要求较低,从而导致活性炭/焦生产企业尾气污染现象较为突出。
3.当前活性炭/焦生产企业普遍采用水洗方法对高温含尘工业尾气进行降温除尘,这种方法虽然可以达到尾气降温除尘的目的,但是存在水资源浪费、同时还会产生污泥、废渣等二次污染的问题。随着我国大气环境污染防治力度的加大,针对活性炭/焦生产企业高温含尘工业尾气降温除尘方法的要求也随之更高。
4.cn206064038u8公开了一种烟气降温除尘装置,包括底部相互连通设置的降温处理箱体与除尘处理箱体,降温处理箱体设置顶部高温烟气进口、侧壁常温水进口以及侧壁高温水出口,降温处理箱体的内部通过盘管连通所述侧壁常温水进口与所述侧壁高温水出口,且盘管邻近所述顶部高温烟气进口设置,盘管所在区域形成高温烟气水盘管换热区,除尘处理箱体设置顶部处理烟气出口以及邻近所述顶部处理烟气出口设置的水雾喷淋组。所述方法虽然可以实现烟气降温除尘,但是存在水资源浪费、高温能量损耗大、管路易阻塞等缺陷,同时还会产生污泥等二次污染。
5.cn208583477u公开了一种烟气降温除尘设备,设备壳体的下部设有烟道入口,壳体的上部设有烟道出口,壳体内设有烟气降温喷淋机构、电除尘机构、粉尘冲洗水机构,壳体外设有与烟气降温喷淋机构、粉尘冲洗水连接的水池和与电除尘机构连接的电源。所述设备虽然可以将烟气降温与净化两种功能整合在同一筒体内,实现工业烟气降温、除尘的功能,但是同样存在水资源浪费、管路阻塞等缺陷,同时还会产生污泥等二次污染。
6.cn1847410a公开了一种转炉烟气降温除尘新方法,所述方法将烟气用换热器进行换热冷却,使得烟气初步降温至900℃,随后将温度约为900℃的烟气进行蒸发冷却,喷射冷却水滴,将烟气温度降至70-80℃;降温后的烟气再进行喷淋除尘,用喷射水滴来捕集尘粒,含尘粒的水滴落下,从排污口排出,从而实现烟气降温、除尘功能,但是同样存在水资源浪费等缺陷,产生污泥等二次污染,同时工艺组成复杂。
7.cn205683768u公开了一种高效节能烟气降温除尘净化器,包括壳体、隔板、出气口、进水口、进气口、排水口,在壳体内部自上而下交错焊接有数个隔板,使壳体内部的空腔形成一条曲折迂回的通道;在壳体的顶板上设有一个出气口,在第一个隔板上部的壳体左侧板上设有一个进水口,在壳体左侧板的下部设有一个进气口和一个排水口。所述净化器虽然可以对高温烟气进行降温除尘净化,但是同样存在水资源浪费等缺陷,同时还会产生污泥等二次污染。
8.由此可见,如何提供一种工业尾气降温除尘的装置系统及其降温除尘的方法,简化工艺流程,提升污染物脱除效率,实现节能减排,避免二次环境污染,成为了目前本领域技术人员迫切需要解决的问题。
技术实现要素:9.本发明的目的在于提供一种工业尾气降温除尘的装置系统及其降温除尘的方法,所述装置系统实现了工业尾气降温与除尘功能结构一体化的目的,所述方法简化了工艺流程,提升了污染物脱除效率,实现了节能减排,避免了二次环境污染。
10.为达到此发明目的,本发明采用以下技术方案:
11.第一方面,本发明提供一种工业尾气降温除尘的装置系统,所述装置系统沿尾气流向包括依次连接的增压单元、降温除尘单元和排气单元。
12.所述降温除尘单元沿粉尘流向包括依次连接的降温除尘器和仓泵输灰器。
13.所述增压单元与降温除尘器的进气口连接。
14.所述排气单元与降温除尘器的出气口连接。
15.所述仓泵输灰器与降温除尘器的出料口连接。
16.本发明提供的装置系统集工业尾气的降温与除尘功能于一体,相较于当前普遍采用的水洗降温除尘装置系统,避免了水资源浪费、管路易阻塞、产生污泥等二次污染的问题,且无需额外配置水雾喷淋组,降低了运行投资和三废处理的成本,实现了节能减排的目的。
17.优选地,所述降温除尘器与仓泵输灰器之间还连接有旋转卸料阀。
18.本发明中,所述旋转卸料阀用于控制粉尘的流出速度。
19.优选地,所述增压单元包括增压风机。
20.优选地,所述排气单元包括排气筒。
21.优选地,所述降温除尘器包括壳体和所述壳体内层叠设置的气固分离区和换热区。
22.优选地,所述气固分离区包括层叠设置的圆柱段和锥斗段。
23.优选地,所述圆柱段内部设置有挡尘板。
24.本发明中,待净化的工业废气经增压单元的增压作用后通过进气口进入降温除尘单元,在所述挡尘板和气固两相巨大惯性差别的作用下,固体粉尘趋于向下运动至出料口排出气固分离区,气体在流经挡尘板时发生方向偏转后向上运动至换热区,从而实现了尾气的除尘与降温同步进行。
25.本发明中,所述挡尘板可调节开度,便于根据工业尾气的含尘量、温度等条件进行开度调节。
26.优选地,所述锥斗段内部设置有辅助松动风管。
27.本发明中,所述辅助松动风管的设置有助于粉尘向出料口流动,并防止出料口发生堵塞现象。
28.优选地,所述辅助松动风管与锥斗段的斜面夹角为80
°‑
100
°
,例如可以是80
°
、82
°
、84
°
、86
°
、88
°
、90
°
、92
°
、94
°
、96
°
、98
°
或100
°
,但并不仅限于所列举的数值,该数值范围内其他未列举的数值同样适用。
29.优选地,所述换热区设置有轴流通风机和换热管。
30.本发明中,所述轴流通风机将冷空气引入换热管,实现了工业尾气与冷空气之间的热量交换,从而达到了降温的目的。
31.优选地,所述换热管为可拆卸式结构。
32.本发明中,所述可拆卸式结构的换热管便于发生管道阻塞等故障时及时进行检修与维护。
33.第二方面,本发明提供一种采用如第一方面所述装置系统进行工业尾气降温除尘的方法,所述方法为:将工业尾气经增压单元的增压作用后通入降温除尘单元,降温除尘后的尾气经排气单元排出,所得粉尘进入仓泵输灰器。
34.本发明提供的方法采用特定结构的装置系统进行工业尾气的降温与除尘,简化了工艺流程,提升了污染物脱除效率,实现了节能减排,避免了二次环境污染。
35.优选地,所述增压单元的增压风量为装置系统满负荷工况下尾气量的100%-120%,例如可以是100%、102%、104%、106%、108%、110%、112%、114%、116%、118%或120%,但并不仅限于所列举的数值,该数值范围内其他未列举的数值同样适用。
36.本发明中,所述增压单元的压头设置在装置系统满负荷工况下并考虑尾气10℃温度裕量下阻力的120%。
37.优选地,所述降温除尘单元中降温除尘器的容积为装置系统单位时间内尾气处理体积的1.2-1.6倍,例如可以是1.2倍、1.25倍、1.3倍、1.35倍、1.4倍、1.45倍、1.5倍、1.55倍或1.6倍,但并不仅限于所列举的数值,该数值范围内其他未列举的数值同样适用。
38.优选地,所述降温除尘单元通过冷空气与尾气之间的热量交换进行降温处理。
39.优选地,所述冷空气的气速为尾气气速1.2-1.6倍,例如可以是1.2倍、1.25倍、1.3倍、1.35倍、1.4倍、1.45倍、1.5倍、1.55倍或1.6倍,但并不仅限于所列举的数值,该数值范围内其他未列举的数值同样适用。
40.优选地,所述粉尘经仓泵输灰器输送至生产企业燃料利用场所进行再利用,实现了资源的回收利用,符合节能环保的要求。
41.相对于现有技术,本发明具有以下有益效果:
42.(1)本发明提供的装置系统集工业尾气的降温与除尘功能于一体,相较于当前普遍采用的水洗降温除尘装置系统,避免了水资源浪费、管路易阻塞、产生污泥等二次污染的问题,且无需额外配置水雾喷淋组,降低了运行投资和三废处理的成本,实现了节能减排的目的;
43.(2)本发明提供的方法采用特定结构的装置系统进行工业尾气的降温与除尘,简化了工艺流程,提升了污染物脱除效率,避免了二次环境污染。
附图说明
44.图1是实施例1-5提供的装置系统结构示意图;
45.图2是实施例1-5提供的装置系统中降温除尘器结构示意图;
46.图3是对比例1提供的装置系统结构示意图;
47.图4是对比例1提供的装置系统中除尘器结构示意图。
48.其中:100-增压单元;200-降温除尘单元;210-降温除尘器;211-壳体;212-气固分
离区;213-换热区;214-挡尘板;215-辅助松动风管;216-轴流通风机;217-换热管;218-冷空气进口;219-热空气出口;220-仓泵输灰器;230-旋转卸料阀;300-排气单元;400-除尘单元;410-除尘器。
具体实施方式
49.下面通过具体实施方式来进一步说明本发明的技术方案。本领域技术人员应该明了,所述实施例仅仅是帮助理解本发明,不应视为对本发明的具体限制。
50.实施例1
51.本实施例提供一种工业尾气降温除尘的装置系统,如图1所示,所述装置系统沿尾气流向包括依次连接的增压单元100、降温除尘单元200和排气单元300;所述降温除尘单元200沿粉尘流向包括依次连接的降温除尘器210、旋转卸料阀230和仓泵输灰器220;所述增压单元100与降温除尘器210的进气口连接,所述排气单元300与降温除尘器210的出气口连接,所述仓泵输灰器220通过旋转卸料阀230与降温除尘器210的出料口连接。
52.本实施例中,所述增压单元100为增压风机,所述排气单元300为排气筒。
53.如图2所示,所述降温除尘器210包括壳体211和所述壳体211内层叠设置的气固分离区212和换热区213;所述气固分离区212包括层叠设置的圆柱段和锥斗段,所述圆柱段内部设置有挡尘板214,所述锥斗段内部设置有辅助松动风管215,且所述辅助松动风管215与锥斗段的斜面夹角为90
°
;所述换热区213设置有轴流通风机216和换热管217,所述换热管217通过冷空气进口218与轴流通风机216连接,换热后所得热空气通过热空气出口219排出,且所述换热管217为可拆卸式结构。
54.实施例2
55.本实施例提供一种工业尾气降温除尘的装置系统,所述装置系统中除了将辅助松动风管215与锥斗段的斜面夹角改为80
°
,其余结构及条件均与实施例1相同,故在此不做赘述。
56.实施例3
57.本实施例提供一种工业尾气降温除尘的装置系统,所述装置系统中除了将辅助松动风管215与锥斗段的斜面夹角改为100
°
,其余结构及条件均与实施例1相同,故在此不做赘述。
58.实施例4
59.本实施例提供一种工业尾气降温除尘的装置系统,所述装置系统中除了去除旋转卸料阀230,即仓泵输灰器220与降温除尘器210的出料口直接连接,其余结构及条件均与实施例1相同,故在此不做赘述。
60.相较于实施例1,本实施例由于去除了旋转卸料阀,导致粉尘的流出速度无法得到及时控制,给操作人员带来一定程度的不便。
61.实施例5
62.本实施例提供一种工业尾气降温除尘的装置系统,所述装置系统中除了将换热管217改为固定式结构,即不可拆卸,其余结构及条件均与实施例1相同,故在此不做赘述。
63.相较于实施例1,本实施例由于采用固定式结构的换热管,导致在发生管道阻塞等故障时无法及时进行检修与维护。
64.对比例1
65.本对比例提供一种工业尾气除尘的装置系统,如图3所示,所述装置系统沿尾气流向包括依次连接的增压单元100、除尘单元400和排气单元300;所述除尘单元400沿粉尘流向包括依次连接的除尘器410、旋转卸料阀230和仓泵输灰器220;所述增压单元100与除尘器410的进气口连接,所述排气单元300与除尘器410的出气口连接,所述仓泵输灰器220通过旋转卸料阀230与除尘器410的出料口连接。
66.本对比例中,所述增压单元100为增压风机,所述排气单元300为排气筒。
67.如图4所示,所述除尘器410包括壳体211和所述壳体211内层叠设置的圆柱段和锥斗段,所述圆柱段内部设置有挡尘板214,所述锥斗段内部设置有辅助松动风管215,且所述辅助松动风管215与锥斗段的斜面夹角为90
°
。
68.应用例1
69.本应用例应用实施例1提供的装置系统进行工业尾气的降温除尘,所述降温除尘的方法为:将工业尾气经增压单元100的增压作用后通入降温除尘单元200,降温除尘后的尾气经排气单元300排出,所得粉尘经仓泵输灰器220输送至生产企业燃料利用场所进行再利用。
70.本应用例中,所述增压单元100的增压风量为装置系统满负荷工况下尾气量的110%,所述降温除尘单元200中降温除尘器210的容积为装置系统单位时间内尾气处理体积的1.4倍,所述降温除尘单元200通过冷空气与尾气之间的热量交换进行降温处理,且所述冷空气的气速为尾气气速1.4倍。
71.应用例2
72.本应用例应用实施例2提供的装置系统进行工业尾气的降温除尘,所述降温除尘的方法为:将工业尾气经增压单元100的增压作用后通入降温除尘单元200,降温除尘后的尾气经排气单元300排出,所得粉尘经仓泵输灰器220输送至生产企业燃料利用场所进行再利用。
73.本应用例中,所述增压单元100的增压风量为装置系统满负荷工况下尾气量的100%,所述降温除尘单元200中降温除尘器210的容积为装置系统单位时间内尾气处理体积的1.2倍,所述降温除尘单元200通过冷空气与尾气之间的热量交换进行降温处理,且所述冷空气的气速为尾气气速1.2倍。
74.应用例3
75.本应用例应用实施例3提供的装置系统进行工业尾气的降温除尘,所述降温除尘的方法为:将工业尾气经增压单元100的增压作用后通入降温除尘单元200,降温除尘后的尾气经排气单元300排出,所得粉尘经仓泵输灰器220输送至生产企业燃料利用场所进行再利用。
76.本应用例中,所述增压单元100的增压风量为装置系统满负荷工况下尾气量的120%,所述降温除尘单元200中降温除尘器210的容积为装置系统单位时间内尾气处理体积的1.6倍,所述降温除尘单元200通过冷空气与尾气之间的热量交换进行降温处理,且所述冷空气的气速为尾气气速1.6倍。
77.对比应用例1
78.本对比应用例应用对比例1提供的装置系统进行工业尾气的除尘,所述除尘的方
法为:将工业尾气经增压单元100的增压作用后通入除尘单元400,除尘后的尾气经排气单元300排出,所得粉尘经仓泵输灰器220输送至生产企业燃料利用场所进行再利用。
79.本对比应用例中,所述增压单元100的增压风量为装置系统满负荷工况下尾气量的110%,所述除尘单元400中除尘器410的容积为装置系统单位时间内尾气处理体积的1.4倍,所述除尘单元400通过冷空气与尾气之间的热量交换进行降温处理,且所述冷空气的气速为尾气气速1.4倍。
80.相较于应用例1,本对比应用例只能实现对工业尾气的除尘功能,而不能实现降温功能,无法实现尾气中热量的循环回收。
81.由此可见,本发明提供的装置系统集工业尾气的降温与除尘功能于一体,相较于当前普遍采用的水洗降温除尘装置系统,避免了水资源浪费、管路易阻塞、产生污泥等二次污染的问题,且无需额外配置水雾喷淋组,降低了运行投资和三废处理的成本,实现了节能减排的目的;此外,本发明提供的方法采用特定结构的装置系统进行工业尾气的降温与除尘,简化了工艺流程,提升了污染物脱除效率,避免了二次环境污染。
82.申请人声明,以上所述仅为本发明的具体实施方式,但本发明的保护范围并不局限于此,所属技术领域的技术人员应该明了,任何属于本技术领域的技术人员在本发明揭露的技术范围内,可轻易想到的变化或替换,均落在本发明的保护范围和公开范围之内。