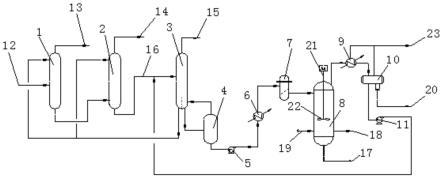
1.本发明涉及化工、环保技术领域,特别是一种萃取剂废液的回收方法。
背景技术:2.环氧丙烷,主要应用于生产聚丙烯、聚醚、丙二醇等产品。工业化的环氧丙烷生产工艺有氯醇法、共氧化法及直接氧化法,其中共氧化法包括po/mtbe法、posm法、pochp法,目前共氧化法的产能已超过环氧丙烷总产能的50%,且新增环氧丙烷项目也主要采用共氧化法,该方法已成为主流的环氧丙烷生产技术。
3.共氧化法生产环氧化丙烷的生产过程具有相似性,反应液中除了目标产物环氧丙烷外,还有水、乙醛、甲酸甲酯等杂质,从反应液中提纯高浓度的环氧丙烷一般需要多级精制工艺,粗环氧丙烷通过两级萃取精馏方式获得合格的环氧丙烷产品。共氧化法的环氧丙烷装置精制单元使用正辛烷或异辛烷作为萃取剂,在萃取精馏过程脱除粗环氧丙烷中甲酸甲酯、乙醛等轻组分杂质,环氧丙烷在精制过程开环生成丙二醇及其低聚物,由于丙二醇、二丙二醇、丙二醇低聚物等重组分杂质沸点高于萃取剂,因而随萃取剂循环利用过程会发生累积,从而影响杂质如甲酸甲酯的脱除效率。现有的粗环氧丙烷精制方法如图1所示,其中为保证循环系统内成分满足工艺要求,需要在萃取剂再生塔的塔釜设有萃取剂废液的排放线的方式对萃取剂废液进行焚烧处理,废液的排放量为80kg/h,其中萃取剂含量约占96wt%以上,新鲜萃取剂价格昂贵,现有技术中无法将萃取剂进行资源化的回收而萃将取剂废液当做废液焚烧,造成资源严重浪费。
技术实现要素:4.本发明的目的在于提供一种萃取剂废液的回收方法,能够回收的萃取剂具备利用条件返回至装置中再利用,实现萃取剂废液的减量化和资源化,完成高价值萃取剂的资源化回收,充分发挥萃取剂的经济价值。
5.为实现上述目的,本发明提供如下技术方案:一种萃取剂废液的回收方法,其特征在于,包括:
6.(1)将萃取精馏分离装置中得到的萃取剂含量为96.0~99.3%、重组分含量为0.5~2.5%、水含量为0.2~1.5%的萃取剂废液输送进入废液浓缩器进行浓缩,得到浓缩后的萃取剂废液;
7.(2)将步骤(1)得到的浓缩后的萃取剂废液通过萃取剂废液泵送至预冷器进行冷却,得到冷却的萃取剂废液;
8.(3)将步骤(2)得到的冷却的萃取剂废液输送至过滤器中去除颗粒物,得到过滤后的萃取剂废液;
9.(4)将步骤(3)得到过滤后的萃取剂废液输送进入重组分分离器中经过负压、蒸汽加热和搅拌后进行分离重组分,废液送至焚烧系统处理后达标排放,轻组分通过重组分分离器上部的第一出口处进入冷凝器中进冷冻液进行冷却,将气相转化为液相后,得到重组
分含量低于0.05~0.08%的萃取剂粗产品;
10.(5)将步骤(4)得到的萃取剂粗产品输送进入除水器进行分离水分,将含水量为40~60ppm油相流出分离滤芯后,获得重组分低于0.1%、水含量低于100ppm的回收萃取剂,将得到的回收萃取剂输送回进入萃取精馏分离装置中重复利用,除水器中的废水送至污水处理系统。
11.进一步的,步骤(1)中所述萃取剂废液中的萃取剂为正辛烷、异辛烷的同分异构体的一种或者多种异辛烷的同分异构体的组合,所述重组分为丙二醇、二丙二醇、丙二醇低聚物中的一种或多种。
12.进一步的,步骤(1)中所述废液浓缩器为闪蒸器或bku式换热器。
13.进一步的,步骤(2)中所述萃取剂废液泵5的压力设置为0.3~0.5mpaa,所述萃取剂废液泵的出口设置有30~50目的滤网,所述预冷器中设置有冷媒介质,所述预冷器对浓缩后萃取剂废液冷却的温度设置为75~85℃。
14.进一步的,步骤(3)中所述过滤器内设置有180~220目的滤网。
15.进一步的,步骤(4)中所述重组分分离器内是采用低压蒸汽对过滤后的萃取剂废液进行加热,所述低压蒸汽的蒸汽等级为s1饱和蒸汽,所述低压蒸汽的温度为100℃。
16.进一步的,步骤(4)中所述冷凝器内设置有冷媒介质,所述冷凝器的操作温度为5~20℃。
17.进一步的,步骤(4)中所述重组分分离器的搅拌速率为950~1000r/min,所述重组分分离器的操作压力为70~90kpaa。
18.进一步的,步骤(4)中所述重组分分离器下料口的管道设置有保温装置,所述保温装置的温度控制在80~90℃。
19.进一步的,步骤(4)中所述除水器内设置有聚滤芯和分离滤芯,所述除水器内下部设置有集水功能的水包,所述水包的油水控制界面设置在距离除水器底部位置的30~50cm。
20.本发明的有益效果:本发明的回收方法适用处理不同含量范围的重组分、水分的萃取剂废液,操作弹性大,对来源于化工装置的萃取剂废液要求低,适用性广泛,采用独特的回收技术,可使用压力等级低的蒸汽的方法进行分离重组分,运行成本低;系统操作温度低,可避免回收操作过程中重组分的自聚反应风险,安全风险低,可靠性高。其中本发明的回收方法从废液中回收高价值的异辛烷,实现废物的减量化和资源化;同时降低了需要焚烧处理的萃取剂废液量,减少了后续焚烧的处置成本以及减少焚烧处置过程烟气对环境的影响,同时萃取剂回收率在90%以上,获得重组分含量低于0.1%、水含量低于100ppm的回收萃取剂,能解决高价值的萃取剂损失问题,获取最大化的经济价值。
附图说明
21.图1为本发明现有技术的装置连接示意图;
22.图2为本发明萃取精馏的化工装置连接示意图。
23.其中:1、杂质脱除塔,2、环氧丙烷产品塔,3、萃取剂再生塔,4、废液浓缩器,5、萃取剂废液泵,6、预冷器,7、过滤器,8、重组分分离器,9、冷凝器,10、除水器,11、回收萃取剂输送泵,12、粗po进料口,13、轻组分排出口,14、环氧丙烷出料口,15、杂质排放口,16、残液排
放口,17、热媒出口,18、热媒进口,19、污水排放处理管道,20、搅拌棒,21、刮板,22、真空系统,23、废液处理口。
具体实施方式
24.下面结合附图和具体实施例对本发明做进一步说明。
25.请参阅图2,本发明提供了一实施例:一种萃取剂废液的回收方法,包括:
26.(1)将萃取精馏分离装置中得到的萃取剂含量为96.0~99.3%、重组分含量为0.5~2.5%、水含量为0.2~1.5%的萃取剂废液输送进入废液浓缩器4进行浓缩,得到浓缩后的萃取剂废液;
27.(2)将步骤(1)得到的浓缩后的萃取剂废液通过萃取剂废液泵5送至预冷器6进行冷却,得到冷却的萃取剂废液;
28.(3)将步骤(2)得到的冷却的萃取剂废液输送至过滤器7中去除颗粒物,得到过滤后的萃取剂废液;
29.(4)将步骤(3)得到过滤后的萃取剂废液输送进入重组分分离器8中经过蒸汽加热和搅拌后进行分离重组分,废液送至焚烧系统处理后达标排放,轻组分通过重组分分离器8上部的第一出口处进入冷凝器9中进冷冻液进行冷却,将气相转化为液相后,得到重组分含量低于0.05~0.08%的萃取剂粗产品;
30.(5)将步骤(4)得到的萃取剂粗产品输送进入除水器10进行分离水分,将含水量为40~60ppm油相流出分离滤芯后,获得重组分低于0.1%、水含量低于100ppm的回收萃取剂,将得到的回收萃取剂输送回进入萃取精馏分离装置中重复利用,除水器10中的废水送至污水处理系统。
31.将萃取精馏分离装置中得到的萃取剂废液经过废液浓缩器4进行加热浓缩后提高萃取剂废液的中重组分的浓度,可以减少后续分离能耗,将浓缩后的萃取剂废液送至预冷器6进行冷却至温度适宜后再输送至过滤器7进行过滤颗粒物,避免大颗粒物进入系统,将过滤后的萃取剂废液输送至重组分分离器8中通过蒸汽加热、搅拌等步骤分离重组分物质,轻组分物质变成气相进入到冷凝器9中,将气相转化成液相,此时得到的产物是重组分含量低于0.05~0.08%的萃取剂粗产品,将得到的产物继续经过除水、除杂的程序后,所得到的产品就是重组分低于0.1%、水含量低于100ppm的回收萃取剂,该萃取剂的质量是完全达到能够进入到萃取精馏分离装置中进行再利用的标准。
32.请继续参阅图2,本发明一实施例中,步骤(1)中所述萃取剂废液中的萃取剂为正辛烷、异辛烷的同分异构体的一种或者多种异辛烷的同分异构体的组合,所述重组分为丙二醇、二丙二醇、丙二醇低聚物中的一种或多种。异辛烷的同分异构体或者多种异辛烷的同分异构体的组合为共氧化法的环氧丙烷装置精制单元中常见的萃取剂。
33.请继续参阅图2,本发明一实施例中,步骤(1)中所述废液浓缩器为闪蒸器或bku式换热器。采用闪蒸器或者是bku式换热器能够对萃取剂废液进行更快、更有效率的进行提浓。
34.请继续参阅图2,本发明一实施例中,步骤(2)中所述萃取剂废液泵5的压力设置为0.3~0.5mpaa,所述萃取剂废液泵5的出口设置有30~50目的滤网,所述预冷器6中设置有冷媒介质,所述预冷器6对浓缩后萃取剂废液冷却的温度设置为75~85℃。其中将萃取剂废
液泵5的压设置为0.3~0.5mpaa,可以便于输送至萃取剂回收系统,萃取剂废液泵5的出口设置有30~50目的滤网,可以避免机械大颗粒物进入萃取剂回收系统。预冷器6中的冷媒介质可以采用循环水,使得可以保证对浓缩后的萃取剂废液进行冷却时的温度不会过高或过低,避免发生温度过高的话,浓缩后的萃取剂废液在管道内发生闪蒸或挥发量大的现象而不利于分离,温度过低的话,就会导致重组分容易析出粘结回收系统的设备,存在粘堵的风险。
35.请继续参阅图2,本发明一实施例中,步骤(3)中所述过滤器7内设置有180~220目的滤网。使得过滤掉大颗粒物,避免大颗粒物进入重组分分离器8影响分离设备的功能。
36.请继续参阅图2,本发明一实施例中,步骤(4)中所述重组分分离器8内是采用低压蒸汽对过滤后的萃取剂废液进行加热,所述低压蒸汽的蒸汽等级为s1饱和蒸汽,所述低压蒸汽的温度为100℃。重组分分离器8的加热是通过低压蒸汽来进行实现的,通过加热和搅拌能够帮助实现重组分更有效的分离。
37.请继续参阅图2,本发明一实施例中,将步骤(4)中所述冷凝器9内设置有冷媒介质,所述冷凝器9的操作温度为5~20℃。冷凝器9的冷媒介质可以采用冷却液,使得能够保证气相的萃取剂能够冷凝成液相。
38.请继续参阅图2,本发明一实施例中,步骤(4)中所述重组分分离器8的搅拌速率为950~1000r/min,所述重组分分离器8的操作压力为70~90kpaa。在重组分分离器8中设置一定的的压力、搅拌棒设置一定的速率能够更好的进行中重组分的分离。
39.请继续参阅图2,本发明一实施例中,步骤(4)中所述重组分分离器8下料口的管道设置有保温装置,所述保温装置的温度控制在80~90℃。在重组分分离器8内的下料口的管道设置有保温装置,并将温度控制在80~90℃,能够保证要排出的废液不析出重组分,解决堵管道的风险。
40.请继续参阅图2,本发明一实施例中,步骤(4)中所述除水器10内设置有聚滤芯和分离滤芯,所述除水器10内下部设置有集水功能的水包,所述水包的油水控制界面设置在距离除水器10底部位置的30~50cm。能够使得当含水的回收萃取剂进入聚结器后,先流经聚结器滤芯,将极小的水滴聚结成较大的水珠,水珠靠自重从萃取剂中分离去除,沉降下来进入水包;萃取剂经过分离滤芯,由于分离滤芯具有较好的亲油憎水性,进一步分离水分,让含水量为40~100ppm油相流出除水器10,水包的油水控制界面的能够保证水包下端排放的废水不带走萃取剂,从而获得合格的回收萃取剂。
41.本发明具有以下工作原理:通过冷却、过滤、蒸发、冷凝、除水等提纯方式,利用丙二醇、二丙二醇、丙二醇低聚物等重组分杂质沸点高于萃取剂的特性来分离萃取剂废液中的重组分和水分,回收的萃取剂具备利用条件可以进行再利用,减量后的萃取剂废液按原有方式送至焚烧系统处理,分离出来的少量废水送至污水处理系统。通过本发明的方法,实现萃取剂废液的减量化和资源化,完成高价值萃取剂的资源化回收,充分发挥萃取剂的经济价值;同时降低萃取剂废液的处置成本,起到环境保护效果。
42.本发明中提到的焚烧系统和污水处理系统为现有技术,本领域中的技术人员已经能够清楚了解,在此不进行详细说明。
43.以上所述仅为本发明的较佳实施例,不能理解为对本技术的限制,凡依本发明申请专利范围所做的均等变化与修饰,皆应属本发明的涵盖范围。