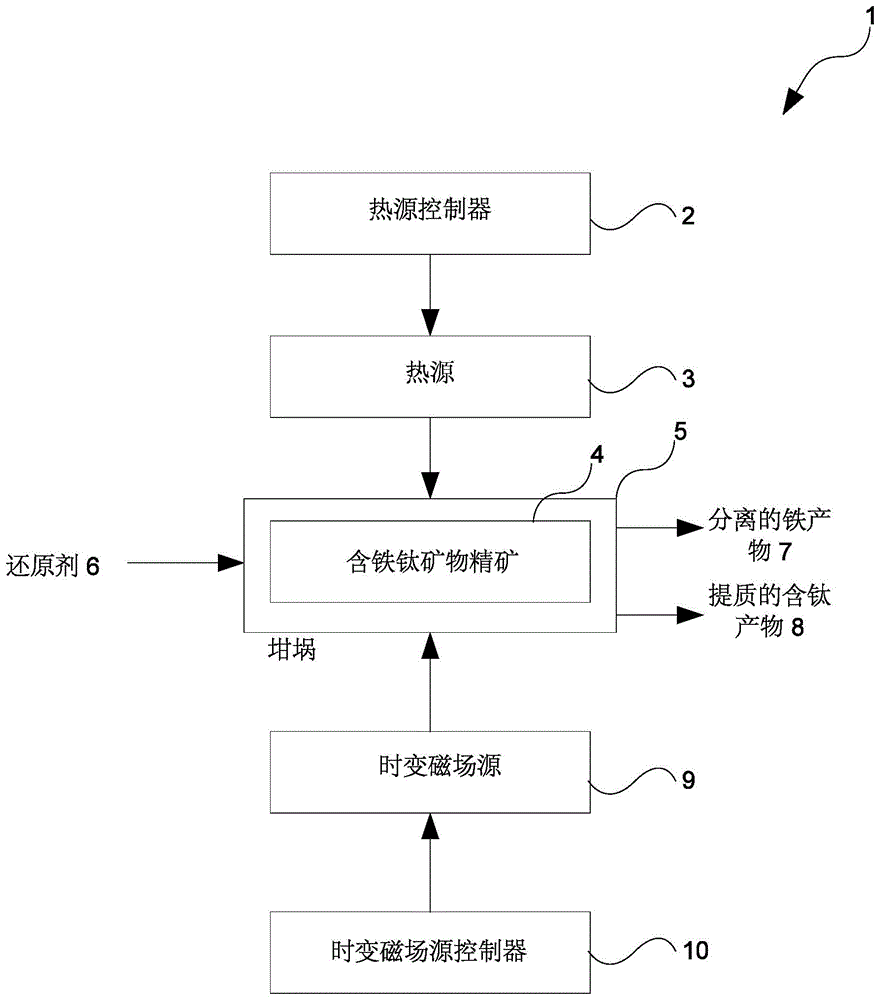
本发明通常涉及通过去除铁杂质来提高矿石或矿物精矿品位,并且具体地,但不一定完全地,涉及使用感应电磁场精选含铁钛矿物精矿以从矿物精矿中分离出铁内容物,从而提高含钛矿物精矿的钛内容物品位。含钛矿物精矿可含有显著量的铁内容物,例如,但不限于,钛铁矿、白钛石、钛磁铁矿和含钛铁砂。尽管本文所述的实施方案主要参考使用时变磁场作为分离含铁钛矿物精矿中的氧化亚铁和/或氧化铁等铁内容物的影响能源进行描述,但是应当注意,本发明不必限于用于含铁钛矿物精矿,并且可以用于其它分离冶金工艺。
背景技术:
:每年在钛金属和二氧化钛颜料的生产中消耗大量的钛。必须将这些工业所使用的钛提取到极高的纯度。钛在自然界中以矿物金红石的形式存在,其主要由杂质水平低的二氧化钛组成,并且以多种含铁钛矿物如钛铁矿的形式存在,该含铁钛矿物由二氧化钛与二价铁和三价铁氧化物组合组成。通过称为氯化物途径的工艺,可以很容易地将金红石中的钛内容物提取为金属或颜料等级,所述氯化物途径是相对简单的工艺,包括金红石与氯气的反应。由于金红石的杂质低并且氯可以回收和再利用,这代表了相对便宜的一步工艺。使用氯化物途径不能经济地回收含铁钛矿物的钛内容物,这主要是由于铁含量高,但可以通过称为硫酸盐途径的工艺以适于颜料制造的形式回收。硫酸盐途径工艺涉及27个单独的单元操作,因此具有比氯化物途径高得多的操作成本。其还不能经济地回收钛提取中使用的硫酸试剂或在加工过程中溶解的大量杂质,特别是铁。结果,该途径还具有高试剂和流出物处置成本。然而,金红石的可用性远远满足不了对钛的需求,特别是在颜料工业中,情况现在由于储量迅速减少而加剧。该情况在历史上意味着金红石价格一直保持在比钛铁矿高得多的水平,所述钛铁矿在钛内容物方面是主要含铁钛原料。钛工业在获得适于钛金属生产的原料和获得适于高等级二氧化钛颜料生产的原料方面面临两难境地,其中所述钛金属生产只能通过氯化物途径生产。由于对流出物处置相关问题的环境意识大大提高,钛工业也不得不应对硫酸盐途径附带的恶劣环境声誉。解决该两难境地的现有技术尝试包括通过更可接受的环境友好的方式来还原合适的相对便宜的含铁钛精矿、特别是钛铁矿的铁内容物,以生产可适于氯化物途径工艺或硫酸盐途径工艺之一或两者的原料,从而解决在钛含量方面的较高价格。例如,现有技术的还原工艺包括应用碳热铁还原作为提高含铁的含钛矿物精矿品位的方式。碳热铁还原涉及使用回转窑以实现低于所得钛产物熔点(<1600℃)的反应,在本文中称为低温工艺,或者通过使用电弧炉实现高温度(>1600℃)下的反应—在本文中称为高温工艺,导致所有反应产物的熔化。高温工艺和低温工艺都存在经济困难。具体地,低温工艺导致铁作为细分散的金属颗粒存在于反应产物中。然后必须将这些铁颗粒氧化并通过酸浸移除,以产生适当提质的产物,导致高操作和残留物处置成本。高温工艺允许从熔化的钛产物中相对简单地移除所得的熔融铁,因为其在炉中形成单独的层。然而,高温工艺涉及高操作成本,因为需要更高的温度,其必须通过使用电力产生,并且高温工艺涉及由于熔融钛产物(“矿渣”)在炉衬层上的严重腐蚀性质导致的高维护成本。由于与低温工艺相关的环境困难和高温工艺的高电力需求,目前在可获得非常便宜的电力的地方使用电弧炉技术来实现含钛矿物精矿的品位提高。us2721793a(magri,jr.等人)在1955年10月25日(d1)公开了在相对较低的温度下对含铁钛矿石的选矿,其通过在足够的硼化合物的存在下将矿石中很大比例的铁内容物还原为单质铁,以从这样获得的单质铁中形成具有低于矿石中还原的含钛相的流点的流点的铁-硼组合物,在选矿过程中,将装料保持在铁-硼组合物的流点与含钛相的流点之间的温度。magri工艺降低了所形成的单质铁的流点或粘度,使得该铁的很大一部分从矿石流出并聚结成球体或集合体(pool),所述球体或集合体通过物理方式从含钛相中移除。us20090324440a1(marsh)(d2)公开了一种用于化学还原含铁矿石或精矿的提取冶金工艺,其特征在于在加热矿石或精矿的同时将矿石或精矿暴露于微波(mw)能量和射频(rf)能量中,其中选择mw和rf能量水平以使得所述矿石或精矿几乎没有或没有另外的加热。k.g.anisonyan,g.b.sadyhov,t.v.olyunina,t.v.goncharenko,l.i.leon,“magnetizingroastingofleucoxeneconcentrate(白钛石精矿的磁化焙烧)”,russianmetallurgy(metally)(俄罗斯冶金(冶金)),2011年7月,2011卷,第7期,第656-659页(d3)公开了在600℃至800℃的温度范围内磁化焙烧白钛石,只有氧化铁被还原为金属态。cn1775368a(武汉理工大学等)在2006年5月24日(d4)公开了通过煅烧和随后的磁选从钛矿石中获得铁矿渣。us3552564a(burgener等人)在1971年01月05日(d5)公开了一种在变化的磁场中的铁磁矿石选矿机(包括钛铁矿),但没有公开矿石的还原。ca2302712a1(councilscientific&industrialreserarch[in](科学与工业研究理事会))在2001年10月24日(d6)公开了由钛铁矿制备合成的金红石,包括通过电弧等离子体熔炼金属化钛铁矿,然后研磨、氧化、浸出、过滤、洗涤和干燥从生铁中分离的二氧化钛。ru2295582c1在2007年3月20日(d7)公开了一种通过经历旋转的电磁场、熔化矿渣和还原炉渣中的金属来处理含钛矿渣的方法。上述现有技术文献都没有公开在时变磁场的存在下还原含铁钛矿石中大部分铁内容物以产生铁球体。此外,上述现有技术文献中都没有单独地或组合地向本领域技术人员明显地暗示在低于矿物精矿的含钛相的流点的温度下,使用时变磁场来提高含铁钛矿物精矿品位的设备(和工艺),所述含铁钛矿物精矿包含按feo计算大于10%重量的铁内容物,所述设备包括:时变磁场源控制器,其用于所述控制时变磁场源以控制铁内容物的还原,其中将所述时变磁场用于促进还原的铁内容物聚结成铁球体。应当理解,如果在本文中提及任何现有技术信息,则这样的提及并不等于承认所述信息在澳大利亚或任何其它国家构成本领域普通常识的一部分。技术实现要素:本发明通常具体涉及使用时变磁场作为影响能量源,用于在低于矿物精矿的含钛相的流点的温度下,例如在低于1600℃或更低的温度下,分离含铁钛矿物精矿的氧化亚铁和/或氧化铁等铁内容物,从而解决或至少提供了对上述低温工艺的细分散金属颗粒的酸浸的高操作和处置成本以及上述高温工艺的高能量成本的替代方案。我们发现,时变磁场的应用令人惊讶地具有显著的影响,能够在比常规工艺显著更低的温度下并且显著更快地分离矿石的组分,分离出的矿石然后可以方便地进行物理分离。例如,当应用于分离含铁钛矿物精矿中的氧化亚铁和/或氧化铁等铁内容物时,时变磁场有助于使铁内容物聚结成铁球体,铁球体随后可通过物理方式移除。在该阶段,时变磁场的这样的影响的确切原因仍然是推测性的,但我们推理所示的效应属于称为磁流体动力学的物理学领域。例如,moffatt在“电磁搅拌”1中描述了施加到导体的交变磁场(单相或多相),无论是固体还是流体,都将会在导体中感应出电流,从而产生洛伦兹力分布。此外,moffatt表示,虽然可以考虑在冶金加工领域(例如,铝冶炼的主要工业工艺)中应用,但是在除了最理想化的情况之外的所有情况下,对电磁搅拌产生的流动的理解仍处于相当初始的水平。我们发现,时变磁场在分离矿石组分领域的应用带来了令人惊讶的结果。我们发现了加速通常的化学反应和在化学反应过程中出现的相关电子流的能力,关于这一点,一种理论认为,时变磁场产生的力影响矿石的粒子(电子/分子等)在较低温度下反应,而不是在通常的较高温度下反应。具体地,为了分离含铁钛矿物精矿中的氧化亚铁和/或氧化铁等铁内容物,我们发现,与酸浸等相反,时变磁场影响铁内容物,使其聚结成球体,球体随后可以有利地通过物理方式移除。我们进一步发现,需要发明新的炉设备来应用我们的发现,其中,与将交变磁场用于加热矿石的常规感应炉相反,新的炉设备具有独立的热源和时变磁场源,使得可以独立于时变磁场的强度控制矿石的加热,以便可以控制时变磁场以调节反应温度(如铁内容物还原反应的温度)以及所得分离组分的物理性质(如铁球体的尺寸)。因此,考虑到前述内容,根据一个方面,提供了使用时变磁场来提高含铁钛矿物精矿品位的冶金工艺,所述含铁钛矿物精矿包含按feo计算大于10%重量的铁内容物,所述工艺包括:在时变磁场的存在下,在低于所述矿物精矿的含钛相的流点的温度下,还原大部分铁内容物,其中将所述时变磁场用于至少促进还原后的铁内容物聚结成铁球体;以及随后物理分离所述铁球体。大多数铁球体的直径可大于106μm。所述冶金工艺还可以包括:提供热源;提供单独的时变磁场源;以及独立于所述热源控制所述时变磁场源。可以独立于所述时变磁场源控制所述热源,以加热含铁钛矿物精矿。与所述热源相比,所述时变磁场贡献极微量的加热。控制所述时变磁场源可包括控制所述时变磁场以控制所述铁球体的尺寸。控制所述时变磁场源可包括控制所述时变磁场以控制所述铁球体的生成速率。所述热源可以包括燃油、燃气和燃煤热源中的至少一种。物理分离所述铁球体可包括破碎或研磨阶段,随后是筛分、空气分级和磁选中的至少一种。所述温度可低于1600℃。所述温度可低于1500℃。所述温度可低于1400℃。所述温度可以在1000℃至1370℃之间。所述铁内容物可以是氧化亚铁和氧化铁中的至少一种。为还原所述铁内容物提供碳源。所述碳源可以包括焦炭、木炭和煤中的至少一种。可以根据以下反应将所述矿物精矿中的二价铁内容物还原为铁金属:feo+c→fe+co可以根据以下反应将所述矿物精矿中的三价铁内容物还原为铁金属:fe2o3+3c→2fe+3co所述碳源可以包括一氧化碳。可以根据以下反应将所述矿物精矿中的二价铁内容物还原为铁金属:feo+co→fe+co2可以根据以下反应将所述矿物精矿中的三价铁内容物还原为铁金属:fe2o3+3co→2fe+3co2所述含铁钛矿物精矿可以是钛铁矿(fetio3)矿物精矿。所述温度可以在1050℃至1350℃之间。可以将所述精矿暴露于所述时变磁场中2分钟至60分钟的保持时间。所述冶金工艺可进一步包括根据预定tio2含量控制所述温度和保持时间。所述冶金工艺可进一步包括向所述含铁钛矿物精矿中添加磁性添加剂。所述磁性添加剂包括磁铁矿和钛磁铁矿中的至少一种。所述含铁钛矿物精矿可以是白钛石、钛磁铁矿和含钛铁砂中的至少一种。所述冶金工艺可进一步包括包含向所述铁产物报告的化学添加剂。所述化学添加剂可包括硼酸盐和磷酸盐。所述冶金工艺可进一步包括在添加所述碳源之前向所述含铁钛矿物精矿中添加水分。所述冶金工艺可进一步包括向所述含铁钛矿物精矿中添加约20%的水分。所述冶金工艺可进一步包括浸出以移除直径小于106μm的铁球体。所述浸出可以使用硫酸铁。根据权利要求34所述的冶金工艺,其进一步包括机械搅拌约10分钟。所述浸出可以涉及氧化/还原反应fe+2fe+++→3fe++。所述冶金工艺可进一步包括通过空气、氧气、臭氧或过氧化氢中的至少一种氧化所得的亚铁离子来再生所述反应所需的铁离子。根据另一个方面,提供了在低于含铁钛矿物精矿的含钛相的流点的温度下,使用时变磁场来提高含铁钛矿物精矿品位的设备,所述含铁钛矿物精矿包含按feo计算大于10%重量的铁内容物,所述设备包括:时变磁场源控制器,其用于控制所述时变磁场源以控制所述铁内容物的还原,其中将所述时变磁场用于促进还原的铁内容物聚结成铁球体。所述设备可进一步包括热源,并且其中独立于所述时变磁场源控制所述热源以加热所述含铁钛矿物精矿。还公开了本发明的其它方面。附图说明尽管存在可落入本发明范围内的任何其它形式,但现在将仅通过示例的方式参照附图描述本公开的优选实施方案,其中:图1示出了根据本公开的实施方案的使用时变磁场来增强含铁钛矿物精矿的选矿的示例用说明性工艺路线;图2示出了根据本公开的实施方案的用于所述工艺的示例性应用方法,其中ac电流通过线圈以产生时变磁场;图3示出了根据本公开的实施方案的使用时变磁场来增强含铁钛矿物精矿的选矿的示例性工艺;图4示出了根据本公开的实施方案的还原工艺所需的基本路线;图5示出了根据本公开的实施方案的图4的路线,其中将硫酸铁的浸出包含到还原路线中;以及图5示出了根据本公开的实施方案的图4的路线,其中将硫酸铁的浸出包含到还原路线中。具体实施方式为了促进对根据本公开的原理的理解,现在将参考附图中示出的实施方案,并且将使用特定语言来描述这些实施方案。然而,应该理解的是,不因此意图限制本公开的范围。相关领域的已掌握本公开的技术人员通常可想到本文所示的发明特征的任何改变和进一步修改,以及如本文所示的本公开的原理的任何另外应用,都认为落入本公开的范围内。在公开和描述使用时变磁场来精选含铁钛矿物精矿的工艺和设备之前,应理解本公开不限于本文所公开的特定配置、工艺步骤和材料,因此可以有所不同。还应理解,本文采用的术语仅用于描述特定实施方案的目的,并不旨在限制,因为本公开的范围仅受权利要求及其等同物的限制。在描述和要求保护本公开的主题时,将根据下面列出的定义使用以下术语。必须注意,如本说明书和所附权利要求书中所用的,除非上下文另外清楚地指明,否则单数形式“一(a)”、“一个(an)”和“该(the)”包括复数指示物。如本文所用的,术语“包含(comprising)”、“包括(including)”、“含有(containing)”、“其特征在于”及其语法等同物是包含性或开放式术语,其不排除另外的、未列举的元素或方法步骤。应当注意,在以下描述中,不同实施方案中的同样或相同的参考标号指代相同或相似的特征。我们已经发现,将含铁钛矿物如钛铁矿与适量的碳如焦炭、煤或木炭的混合物暴露于由适当定位的外部电线圈产生的时变磁场,将导致含铁钛矿物的铁内容物在低于1400℃的温度下、特别是在1000℃至1300℃之间的温度下迅速还原为铁金属,并且通过控制感应的时变磁场,该金属可以迅速聚结成铁球体。通常,本文所述的实施方案涉及钛铁矿(fetio3)矿物精矿与碳源如焦炭、木炭、煤等之间的反应,由此根据以下反应式将矿物精矿中的二价铁和三价铁内容物还原为铁金属:二价铁:-feo+c→fe+co三价铁:-fe2o3+3c→2fe+3co但也可能涉及使用其它还原剂,例如一氧化碳,在这种情况下,反应根据以下反应式进行:二价铁:-feo+co→fe+co2三价铁:-fe2o3+3co→2fe+3co2在上述反应中,时变磁场的应用允许铁颗粒聚结成金属球体,而提质的含钛级分保持为固相。本文公开的工艺涉及通过在接近被加热的装料附近的线圈施加的交变电流(ac)来产生时变磁场。我们已经发现,通过应用电磁场强度、温度和保持时间的合适组合,可以控制所得金属球体的尺寸,使得可以通过简单的物理方式容易地从反应产物中移除金属球体,而不是化学浸出。特别地,使用钛铁矿精矿作为原料,已经发现通过施加合适的电磁场,可以在1050℃至1350℃的温度下使用2分钟至30分钟的保持时间形成直径>1mm的铁金属球体,从而在通过研磨和筛分移除它们之后,可以产生提质的钛级分,其范围为70%至85%tio2。我们还发现,可以控制温度和保持时间以达到预定的铁还原水平,从而产生具有预定tio2含量的提质的钛铁矿。我们还发现,将原料中含有的任何磷提取到铁产品中,留下不含磷酸盐的提质的产物,这是提质的产物潜在应用于具有低磷耐受性的二氧化钛颜料生产中的重要考虑因素。我们还发现,即使少量的高磁性材料如磁铁矿和钛磁铁矿的存在也会显著降低操作温度范围和保持时间,这可导致加工成本降低。我们进一步发现,通过包含多种化学添加剂,包括硼酸盐和磷酸盐,可以降低所需的操作温度范围和保持时间两者,这两种化学添加剂都向铁产物报告。尽管我们没有发现含钛原料的粉碎的益处,但是在将碳源的粒径范围保持在大于0.5mm时发现了益处。我们还发现,在装入炉中之前向钛铁矿/碳混合物中添加水然后彻底混合可导致在同等操作温度下稠度的改善和还原效率的提高这两者。我们还发现,在106微米下筛分后,还原的钛铁矿中的铁金属内容物或在该筛分步骤后通过磁选提取的高磁性级分可以通过用硫酸铁溶液浸出10分钟而被移除。我们还发现,在混合之前向钛铁矿/碳/水混合物中添加钛磁铁矿,将使得达到给定水平的铁还原和ugi(提质的钛铁矿)质量所需的操作温度可以明显降低。工艺路线现在转向图1,示出了使用时变磁场增强含铁钛矿物精矿的选矿的示例用说明性工艺路线1。可以看出,路线1包括坩埚、炉、窑5等,坩埚、炉、窑5包含含铁钛矿物精矿4。为了还原矿物精矿4的铁内容物,添加还原剂6,如焦炭、煤、一氧化碳等。坩埚5的输出包括分离的产物7和提质的含钛产物8。可以看出,路线1包括热源3和时变磁场源9。在实施方案中,热源3和时变磁场源9可以由相同的设备产生,其中,例如,热量和时变磁场由感应加热线圈提供。然而,试验和实验发现,需要将时变磁场源与热源分开以进行独立控制,使得例如如上所述可以控制时变磁场以影响铁内容物聚结成铁球体。例如,可以控制时变磁场的强度和/或频率以影响从所述工艺产生的铁球体的尺寸。因此,图1代表优选的实施方案,其中路线1包括独立的热源3和时变磁场源9。关于这一点,热源3可以通过非导电方式提供热量,如来自常规的燃气、燃油或燃煤热源的热量。此外,热源3和时变磁场源9可以包括对其的独立控制装置。因此,可以看出,热源3可以包括热源控制器2,将热源控制器2配置成控制坩埚5的操作温度,坩埚5独立于时变磁场源控制器10被控制,将所述时变磁场源控制器10配置成至少控制时变磁场的强度和频率,如上所述,时变磁场被控制为至少用于影响铁还原以及影响铁球体的尺寸的聚结或其产生速率。例如,我们发现路线1的操作可以导致产生最小球直径约为150微米(0.15mm)的球体形式的生铁和最大粒径为150微米(0.15mm)的提质的钛铁矿产物。应用方法现在转向图2,示出了所述工艺的示例性应用方法,其中ac电流通过线圈12以产生穿过并围绕线圈12的时变磁场。时变磁场可以在放置在线圈12内的任何材料内产生涡电流。具体地,向线圈12施加交变电流将感应出穿过线圈12的电磁场,其中场的方向取决于电流的方向。此外,穿过线圈12的交变电流将导致时变磁场以与交变电流频率相同的速率改变方向,其中,例如60hz电流将导致电磁场每秒钟切换方向60次。电磁场赋予的力和能量取决于目标材料的电导率、电阻率和磁化率。因此,工艺1的潜在应用包括基本上如图2a所示的分批方式,其包括炉15,炉15中具有线圈12。炉15内可以放置坩埚13,坩埚13具有容纳矿物精矿4的石墨衬层14。可替代地,所述工艺可以基本上如图2b所示以连续方式实施,其中使用了回转窑17。如上所述,回转窑17可以通过常规方式进行加热,如通过燃油、燃气或燃煤来加热。可以看出,线圈12围绕窑17,其中将矿物精矿4在一端进料,使得产物16从窑17的另一端排出。在替代实施方案中,也如图2b所示,线圈12可以位于回转窑17旁边,而不是与窑17同轴。理想地,坩埚13和回转窑17由非磁性材料制成,如不锈钢或铝。工艺现在转向图3,示出了使用时变磁场增强含铁钛矿物精矿的选矿的示例性工艺20。在步骤17中,将含铁钛矿物精矿4与合适的还原剂组合,并在时变磁场的存在下加热,所述含铁钛矿物精矿4包含按feo计算大于10%重量的铁内容物。大部分铁内容物在低于矿物精矿的含钛相的流点的温度下被还原。时变磁场的应用至少有助于将还原的铁内容物聚结成铁球体。在步骤18中,使装料冷却,其中在步骤19中,将产物破碎或研磨至约106μm。在步骤19中,通过物理方式筛分破碎产物的铁内容物,其中将尺寸大于约106μm的铁球体作为金属产物7分离。在步骤20中,将剩余的tio2固体和尺寸小于106μm的细生铁通过具有1,000至1,500高斯场强的干辊磁体进行分离,以再循环到炉中,从而通过所述工艺的操作不会产生固体废物或几乎不会产生固体废物。剩余产物仍然是提质的含钛产物8。示例性测试结果下文提供示例性测试结果以说明本文所述工艺的性能。下面示出的所有测试结果都是使用由跨国公司(acrossinternational)提供的ih15系列实验室感应加热器进行的。加热器装有75mmid铜质水冷感应线圈,将所述线圈设计成包含合适尺寸的二氧化硅夹套。150ml容量的石墨坩埚位于夹套内。虽然在这些实施例中感应加热器既是热源又是时变磁场,如上所述,但是在一个优选的实施方案中,为了独立控制矿石的加热和时变磁场的作用,分开的热源和时变磁场源是理想的。然而,从下面可以看出,线圈最初可用于加热矿石,然后控制其施加与铁内容物的还原相关的时变磁场的作用,并使其聚结成铁球体。下面的所有实施例都涉及将约100克选定的含钛矿物精矿和碳的混合物置于石墨坩埚中,然后通过调节输入到线圈的电流,将混合物加热到如由高温计测量的预定温度范围,然后将混合物保持在该温度范围内一段预定时间,如用秒表测量该预定时间。示例性测试结果-实施例1在该实施例中,将86克已知分析的goondicum钛铁矿精矿与12克yarrabee半无烟煤(0.106mm至0.25mm)混合并装入石墨坩埚中。然后将已知产生最大加热速率的电流设定施加到线圈上,直到温度升至1350℃,之后根据需要调节线圈电流以将温度保持在1300℃至1375℃的范围内另外20分钟。然后将最终的固体倒入陶瓷碗中,冷却至室温,观察到其主要由包含在含钛固体基体中的小球体形式的铁金属组成。将该产物球磨5分钟后,发现通过在106微米下的简单筛分步骤可以容易地将铁金属球体与含钛固体分离。将从该实验获得的铁球体和含钛固体(提质的钛铁矿-ugi)称重并进行分析。然后通过在250微米和425微米下的筛分确定铁球体的尺寸范围。结果如下:铁球体的尺寸分布如下:尺寸范围含量(%)+425μ30.5-425μ+250μ28.0-250μ+106μ41.5这些结果表明,已经将钛铁矿中62.4%的铁内容物还原成含有91.6%铁的铁金属,并且已经将100%的钛内容物提取为含有73.3%tio2的ugi。应注意,将100%的p2o5内容物提取到铁金属中。使用readingspilot实验室辊磁选机在600高斯下对ugi产物进行磁选。然后称重并分析非磁性级分和磁性级分。然后使用磁力搅拌器将磁性级分在100ml的10%盐酸中浸出60分钟。然后通过过滤回收固体,干燥,称重并分析。结果如下:该结果表明,初始ugi(表示为产物的<106微米的级分)可以通过在1500高斯下的磁选进一步提质为80.6%tio2和9.0%fe的非磁性级分,然后通过盐酸浸出将来自该磁选的磁性级分提质为类似的ugi产物。因此,初始ugi仍含有一些物理附着于细ugi颗粒的细铁金属,表明在期望温度区域内允许的保持时间不足以使铁完全凝结成+106微米的球体,实际上已经将钛铁矿中83.5%的铁内容物还原为金属,其中钛内容物作为含有81%tio2的ugi形式100%回收。由于其高tio2硫酸盐溶解度(>97%)、低铁含量和低水平的有害杂质,该ugi产物理想地适于作为钛渣的替代品通过硫酸盐途径来生产二氧化钛颜料。示例性测试结果-实施例2在该实施例中,将86克已知分析的goondicum钛铁矿精矿与12克yarrabee半无烟煤(1mm至2mm)混合并装入石墨坩埚中。然后将已知产生最大加热速率的电流设定施加到线圈上,直到温度升至1350℃,之后根据需要调节线圈电流以将温度保持在1300℃至1375℃范围内另外40分钟。然后将最终的固体倒入陶瓷碗中,冷却至室温,观察到其主要由包含在含钛固体基体中的小球体形式的铁金属组成。将该产物球磨5分钟后,发现通过在106微米下的简单筛分步骤可以容易地将铁金属球体与含钛固体分离。将从该实验获得的铁球体和含钛固体(提质的钛铁矿-ugi)称重并进行分析。然后通过在250微米和425微米下的筛分确定铁球体的尺寸范围。结果如下:铁球体的尺寸分布如下:尺寸范围含量(%)+425μ34.5-425μ+250μ38.7-250μ+106μ26.8这些结果表明,已经将钛铁矿中93.1%的铁内容物还原成含有91.6%铁的铁金属,并且已经将100%的钛内容物提取为含有85.4%的tio2的ugi。应注意,将100%的p2o5内容物提取到铁金属中。示例性测试结果-实施例3在该实施例中,将86克已知分析的低等级goondicum钛铁矿精矿与12克yarrabee半无烟煤(2.0mm至4.0mm)混合并装入石墨坩埚中。将已知产生最大加热速率的电流设定再次施加到线圈上,直到温度升至1350℃,之后根据需要调节线圈电流以将温度保持在1300℃至1375℃的范围内另外10分钟。然后将最终的固体倒入陶瓷碗中,冷却至室温,观察到其主要由包含在含钛固体基体中的小球体形式的铁金属组成。将该产物球磨5分钟后,发现通过在106微米下的简单筛分步骤可以容易地将铁金属球体与含钛固体分离。将从该实验获得的铁球体和含钛固体(提质的钛铁矿-ugi)称重并进行分析。然后通过在250微米和425微米下的筛分确定铁球体的尺寸范围。结果如下:铁球体的尺寸分布如下:尺寸范围含量(%)+425μ36.5-425μ+250μ34.0-250μ+106μ29.5这些结果表明,已经将钛铁矿中71.6%的铁内容物还原成含有89.4%铁的铁金属,并且已经将100%的钛内容物提取为含有67.7%的tio2的ugi。应当注意,将用于该实施例的钛铁矿中100%的相当高水平的p2o5再次提取到铁金属中。该实施例证明,还原剂的粒径增加可导致反应时间的明显减少。示例性测试结果-实施例4在该实施例中,将86克已知分析的goondicum钛磁铁矿与12克yarrabee半无烟煤(2.0mm至4.0mm)混合并装入石墨坩埚中。将已知产生最大加热速率的电流设定再次施加到线圈上,直到温度升至1150℃,之后根据需要调节线圈电流以将温度保持在1100℃至1200℃的范围内另外30分钟。然后将最终的固体倒入陶瓷碗中,冷却至室温,发现其主要由包含在含钛固体基体中的小球体形式的铁金属组成。将该产物球磨5分钟后,发现通过在106微米下的简单筛分步骤可以容易地将铁金属球体与含钛固体分离。将从该实验获得的铁球体和含钛固体(提质的钛铁矿-ugi)称重并进行分析。然后通过在250微米和425微米下的筛分确定铁球体的尺寸范围。结果如下:铁球体的尺寸分布如下:尺寸范围含量(%)+425μ42.0-425μ+250μ36.5-250μ+106μ21.5这些结果表明,已经将钛铁矿中95.0%的铁内容物还原成含有91.6%铁的铁金属,并且已经将100%的钛内容物提取为含有48.7%tio2和8.6%铁的ugi。该ugi产物代表了独特且极具吸引力的钛铁矿精矿替代品,作为通过硫酸盐途径生产二氧化钛颜料的原料,同时表现出与可获得的钛铁矿原料相似的tio2含量,已经发现其比钛铁矿(92%至96%的二氧化钛溶解度)对硫酸盐介质更具反应性(>99.9%的二氧化钛溶解度),但是铁含量低得多,都是亚铁形式。水添加我们发现,在装入炉中之前向钛铁矿/碳混合物中添加水然后彻底混合可在同等操作温度下导致稠度的提高和还原效率的提高这两者。具体地,在装入熔炉坩埚之前使用的混合程序中,在添加碳源之前,向钛铁矿精矿中添加20%的水分,可以导致可重复性的提高,并降低在给定还原时间内实现同等ugi产量和质量所需的操作温度。我们认为,这可能是由于还原剂碳在装料中的分布更均匀,然而,在该阶段不排除其它物理或化学影响的可能性。硫酸铁浸出我们还发现,在106微米下筛分后的还原的钛铁矿中的铁金属内容物或在该筛分步骤后通过磁选提取的高磁性级分可以通过用硫酸铁溶液浸出10分钟来基本上完全移除。当在硫酸盐工艺中应用ugi时,细铁颗粒的存在可能是不期望的,这例如是由于氢排放的原因。因此,使ugi产物中细铁颗粒的存在最少化非常重要。由于炉步骤中不完全的球形成,或者由于设计成移除残留铁金属的磁选步骤效率低下,在研磨和筛分步骤之后,细铁颗粒可能存在于从炉中排出的<106微米的还原固体的含钛级分中。由于颗粒在干辊磁选机有效运行的颗粒尺寸范围之外,可能会出现磁选效率低下的情况。还有可能的是,固体的级分可与铁颗粒的级分具有相似的磁化率。已经发现,含钛固体产物中的任何残留细铁金属内容物都可以通过随后的浸出步骤移除,包括用化学计量量的硫酸铁作为稀溶液机械搅拌固体10分钟,然后过滤、洗涤和干燥。所述工艺涉及快速氧化/还原反应:fe+2fe+++→3fe++。该方法比例如酸浸更好,因为不涉及氢排放,并且可以反应表现出快得多且更完全。还已知该反应中所需的铁离子可以通过空气、氧气、臭氧或过氧化氢来氧化所得亚铁离子而容易地再生。反应中涉及硫酸铁的反应如下:4fe+4fe2(so4)3→12feso412feso4+6h2o+3o2→4fe2(so4)3+4fe(oh)3或总体而言,4fe+6h2o+3o2→+4fe(oh)3已经发现,通过使用该方法,从炉排出物的<106微米尺寸级分和从其中提取的磁性级分两者中获得的浸出固体与通过在600高斯下的磁选从<106微米尺寸的级分中提取的非磁性产物具有相似的tio2和fe含量。钛磁铁矿的添加在进一步改进中,已经发现在混合之前,通过向钛铁矿/碳/水混合物中添加钛磁铁矿,可以明显降低达到给定水平的铁还原和ugi质量所需的操作温度。已经发现,通过向钛铁矿装料中添加钛磁铁矿,可以大大改进还原工艺的操作。有益效果包括在较低的操作温度下更快速的还原和含钛固体排放物的物理性质的改善,因为固体具有土质地并且可更容易且完全地从炉坩埚中排出。如果钛磁铁矿/钛铁矿比值与在goondicum操作中处理的矿石中出现的相似,则这些效果尤其明显。众所周知,钛磁铁矿的居里点(curriepoint)约为500℃,因此可以预期其以与石墨坩埚衬层相似的方式作用,达到该温度。然而,实验结果表明在该温度范围之外,有益效果持续。改进的实施例下面给出三个另外的示例性实施例5、6和7,以证明上述改进。示例性测试结果-实施例5在该实施例中,将150克已知分析的goondicum钛铁矿精矿与30克yarrabee半无烟煤(0.106mm至0.25mm)和30ml水充分混合。然后将固体混合物装入石墨坩埚中。然后将已知产生最大加热速率的电流设定施加到线圈上,直到温度升至1150℃,之后根据需要调节线圈电流以将温度保持在1200℃至1250℃的范围内另外20分钟。然后将最终的固体倒入陶瓷碗中,冷却至室温,观察到其主要由包含在含钛固体基体中的小球体形式的铁金属组成。将该产物球磨5分钟后,发现通过在106微米下的简单筛分步骤可以容易地将铁金属球体与含钛固体分离。将从该实验获得的铁球体和<106微米的含钛固体(提质的钛铁矿-ugi)称重并进行分析。然后通过在250微米和425微米下的筛分确定铁球体的尺寸范围。结果如下:铁球体的尺寸分布如下:尺寸范围含量(%)+425μ28.5-425μ+250μ26.0-250μ+106μ45.5这些结果表明,已经将钛铁矿中75.8%的铁内容物还原成含有91.6%铁的铁金属,并且已经将100%的钛内容物提取为含有80.8%tio2和13.3%fe的ugi。应注意,将100%的p2o5内容物提取到铁金属中。然后,使用readingspilot实验室辊磁选机在600高斯下对<106微米固体产物进行磁选。然后称重并分析非磁性级分和磁性级分。然后使用机械搅拌器将磁性级分在100ml的10%硫酸铁中浸出10分钟。然后通过过滤回收固体,干燥,称重并分析。结果如下:该结果表明,通过该程序可以获得含有89.6%tio2和4.6%fe的更高等级的固体作为非磁性级分,类似等级的产物来自磁性级分的硫酸铁浸出。将非磁性固体与浸出的磁性固体组合,得到含有89.6%tio2和4.6%fe的最终ugi产物。该结果表明,初始的<106微米固体含有细铁金属颗粒,并且磁选不能完全有效地将这些细铁颗粒与非金属固体分离。该结果证明,要么表明了在所期望的温度区域内使铁完全凝结成+106微米的球体的保持时间不足,要么表明了固体的粒径范围低于设计为在100微米至450微米范围内操作的磁选设备的有效操作所需的粒径范围。假设从ugi中移除所有铁金属,这些结果表明实际上钛铁矿中86.9%的铁内容物已经还原成金属,其中钛内容物100%回收,产生含有89.5%tio2和4.8%fe的最终ugi产物。该测试证明,含有80.8%tio2和13.3%fe的ugi可由高等级(酸浸出的)goondicum钛铁矿生产而无需磁选,但含有细铁颗粒。通过随后的磁选,可以提取该产物的90%的tio2内容物,作为不含铁金属且含有89.5%tio2和4.8%fe的非磁性级分。可以将含有余量的tio2内容物和细铁金属颗粒的磁性级分再循环到炉中或者可以更有利地用硫酸铁浸出,以产生具有与非磁性级分相似组成的固体,从而提取100%的tio2内容物作为不含铁金属且含有89.5%的tio2和4.8%的fe的ugi。示例性测试结果-实施例6在该实施例中,将150克已知分析的中间等级goondicum钛铁矿精矿与30克yarrabee半无烟煤(0.106mm至0.25mm)和30ml水充分混合。然后将固体混合物装入石墨坩埚中。然后将已知产生最大加热速率的电流设定施加到线圈上,直到温度升至1150℃,之后根据需要调节线圈电流以将温度保持在1200℃至1250℃的范围内另外20分钟。然后将最终的固体倒入陶瓷碗中,冷却至室温,观察到其主要由包含在含钛固体基体中的小球体形式的铁金属组成。将该产物球磨5分钟后,发现通过在106微米下的简单筛分步骤可以容易地将铁金属球体与含钛固体分离。将从该实验获得的铁球体和含钛固体(提质的钛铁矿-ugi)称重并进行分析。然后通过在250微米和425微米下的筛分确定铁球体的尺寸范围。然后使用机械搅拌器将<106微米固体级分在100ml的10%硫酸铁中浸出10分钟。然后通过过滤回收固体,干燥,称重并分析。结果如下:铁球体的尺寸分布如下:尺寸范围含量(%)+425μ29.5-425μ+250μ25.5-250μ+106μ45.0在筛分之后<106级分的分析表明,已经将钛铁矿中76.9%的铁内容物还原成含有91.6%铁的铁金属,并且已经将100%的钛内容物提取为含有75.9%tio2和12.2%fe的<106微米固体。随后这些固体的硫酸铁浸出表明实际上已经将93.8%的铁内容物还原成铁金属,并且有可产生具有84.2%tio2和4.7%fe的最终ugi。该测试证明含有75.9%tio2和12.2%fe的ugi可由中间等级goondicum钛铁矿生产而无需磁选,但含有细铁颗粒。证明通过硫酸铁浸出可以从该产物中移除细铁金属颗粒,以得到不含铁金属且含有84.2%tio2和4.7%fe的改善的ugi产物。在该实施例中,与示例性测试5中获得的相比,较低的最终ugitio2含量是由于所用钛铁矿中含有较高水平的杂质(已知主要是钛磁铁矿、黑云母、辉石、磷灰石和长石)导致的。还证明实现了更高程度的铁还原,表明这些杂质中的一些或全部有助于还原机制。这在钛磁铁矿的情况下很有意义,已知所述钛磁铁矿在示例性测试5中所用的钛铁矿的配制品中已经被完全移除。示例性测试结果-实施例7在该实施例中,将116克已知分析的中间等级goondicum钛铁矿精矿与34克已知分析的钛磁铁矿、30克yarrabee半无烟煤(106微米至250微米)和30ml水充分混合。在充分混合之后,将其装入石墨坩埚中。施加电流设定,使得温度经过10分钟的时间段升至1000℃。然后增加电流设定,使温度在15分钟之后线性上升到1240℃。然后将最终的固体倒入陶瓷碗中,冷却至室温,观察到其主要由包含在含钛固体基体中的小球体形式的铁金属组成。注意到固体具有土状稠度,容易从坩埚中倒出来,很少或根本没有粘附在坩埚表面。将该产物球磨5分钟后,发现通过在106微米下的简单筛分步骤可以容易地将铁金属球体与含钛固体分离。将从该实验获得的铁球体和含钛固体(提质的钛铁矿-ugi)称重并进行分析。然后通过在250微米和425微米下的筛分确定铁球体的尺寸范围。结果如下:铁球体的尺寸分布如下:尺寸范围含量(%)+425μ50.5-425μ+250μ24.4-250μ+106μ25.1该测试证明可以在不需要磁选的情况下生产含有68.0%tio2和18.9%fe的ugi。随后这些固体的硫酸铁浸出产生具有81.4%tio2和6.4%fe的最终ugi,表明实际上已经将90.7%的铁内容物还原成铁金属。应注意,将100%的p2o5内容物提取到铁金属中。该测试的结果清楚地确定了添加钛磁铁矿所产生的有益效果,证明了钛磁铁矿能够在相当低的温度和保持时间下实现高水平的还原。这提供了显著的潜在经济优势,尤其是当与观察到的从炉中移除最终固体的容易程度结合来看时。goondicum操作的一个重要考虑是,最终含钛固体中,无论是未浸出的还是浸出的ugi固体中,tio2含量都很高,这表明可以利用大量目前毫无价值的钛磁铁矿来提高可接受质量ugi的产量,特别是因为本测试中使用的钛铁矿是中间等级的。较高等级的钛铁矿原料(如目前的最终产物)与lims目前废弃的钛磁铁矿尾矿组合,可以预期将通过该方法生产的ugi中的tio2含量增加至少2%,从而得到或多或少相当于单独由钛铁矿生产的产物。改进的工艺意义除了在炉工艺中观察到的益处之外,向炉进料中添加水也是可能的优点,因为在干燥之前最终的钛铁矿含有5%至10%的水分。因此可以去除对干燥的需要。还原工艺所需的基本路线如图4所示。由于安全考虑,ugi进入硫酸盐颜料工业的关键营销考虑因素是预先对铁金属含量的严格规范。硫酸铁浸出提供了从ugi中去除铁金属的简单而安全的方法,并提供保险,如果其它方式可以实现该结果,如更适于所涉及的粒径范围或更长的炉保持时间的替代磁选设备,最终的选择成为经济方面的问题。在装有特定设计的通气搅拌器的反应容器中,通过使用ph3.4的硫酸亚铁溶液,可以最经济地实现铁浸出步骤,其中通过用氧,如空气、氧气或臭氧来氧化亚铁离子而产生瞬时铁离子。可替代地,可以通过以期望速率将过氧化氢直接添加到浸出溶液中来实现氧化。图5示出了将硫酸铁浸出包含在还原路线中。图6示出了包含与磁选结合的硫酸铁浸出。在图4至图6的所有三个路线中都作为选项示出了包含钛磁铁矿。可以将通过铁浸出产生的氢氧化铁副产物排放到尾矿中,出售给硫酸铁制造商或作为水分补充的一部分再循环到炉中。在后一种情况下,氢氧化铁将被还原成铁并且将表现为增加的铁球产物。解释实施方案整个本说明书中对“一个实施方案(oneembodiment)”或“实施方案(anembodiment)”的引用意指将结合所述实施方案描述的特定特征、结构或特性包括在本发明的至少一个实施方案中。因此,贯穿本说明书在多个地方出现的短语“在一个实施方案中(inoneembodiment)”或“在实施方案中(inanembodiment)”不一定都是指相同的实施方案,而是可以指相同的实施方案。此外,在一个或多个实施方案中,特定特征、结构或特性可以以任何合适的方式组合,如本领域普通技术人员可从本公开中显而易见的。类似地,应当理解,在本发明的示例性实施方案的以上描述中,本发明的多个特征有时在单个实施方案、附图或其描述中组合在一起,以便简化本公开并帮助理解多个发明方面中的一个或多个。然而,本公开的方法不应解释为反映这样的意图:所要求保护的发明需要比每个权利要求中明确记载的更多的特征。而是,如所附权利要求所反映的,本发明的方面在于小于单个前述公开的实施方案的全部特征。因此,具体实施方案的详细描述之后的权利要求在此明确地并入具体实施方案的详细描述中,其中每个权利要求自身作为本发明的单独实施方案。此外,虽然本文所述的一些实施方案包括一些特征但不包括在其它实施方案中包括的其它特征,但是不同实施方案的特征的组合意味着落入本发明的范围内,并且形成不同的实施方案,如本领域技术人员将理解的。例如,在所附权利要求中,任何要求保护的实施方案都可以以任何组合使用。对象的不同实例如本文所使用的,除非另有说明,否则使用序数形容词“第一”、“第二”、“第三”等来描述共同的对象,仅仅表示引用相同的对象的不同实例,而不是旨在暗示所描述的对象必须在时间上、空间上、排序上或以任何其它方式处于给定的顺序中。具体细节在本文提供的描述中,阐述了许多具体细节。然而,应该理解,可以在没有这些具体细节的情况下实施本发明的实施方案。在其它情况下,没有详细示出公知的方法、结构和技术,以免混淆对本说明书的理解。术语在描述附图中所示的本发明的优选实施方案时,为了清楚起见,将采用特定术语。然而,本发明并不旨在限于如此选择的特定术语,并且应理解,每个特定术语包括以类似方式操作以实现类似技术目的的所有技术等同物。将术语如“向前”、“向后”、“径向”、“周向”、“向上”、“向下”等用作方便的词语以提供参考点,而不应解释为限制性术语。包含和包括在所附权利要求中和本发明的前述描述中,除非上下文由于明确的语言或必要的含义而另外要求,否则以包含的意义使用词语“包括(comprise)”或变体如“包含(comprises)”或“含有(comprising)”,即,指定所述特征的存在,但不排除在本发明的多个实施方案中存在或添加另外特征。所述术语中的任何一个:如在本文中所使用的,包含(including)或其包含(whichincludes)或包含有(thatincludes)也是开放性术语,其还意味着至少包括该术语之后的元素/特征,但不排除其它元素/特征。因此,包含(including)与包括(comprising)同义并且意指包括。发明范围因此,尽管已经描述了认为是本发明的优选实施方案的内容,但是本领域技术人员将认识到,在不脱离本发明的精神的情况下,可以对其进行其它和进一步的修改,并且旨在要求保护所有这样的改变和修改都落入本发明的范围内。例如,上面给出的任何式子仅仅代表可以使用的程序。可以从框图中添加或删除功能,并且可以在功能块之间交换操作。可以在本发明的范围内描述的方法中添加或删除步骤。尽管已经参考具体实施例描述了本发明,但是本领域技术人员将理解,本发明可以以许多其它形式进行实施。工业应用性从上面显而易见的是,所描述的布置可适用于冶金工业。当前第1页12