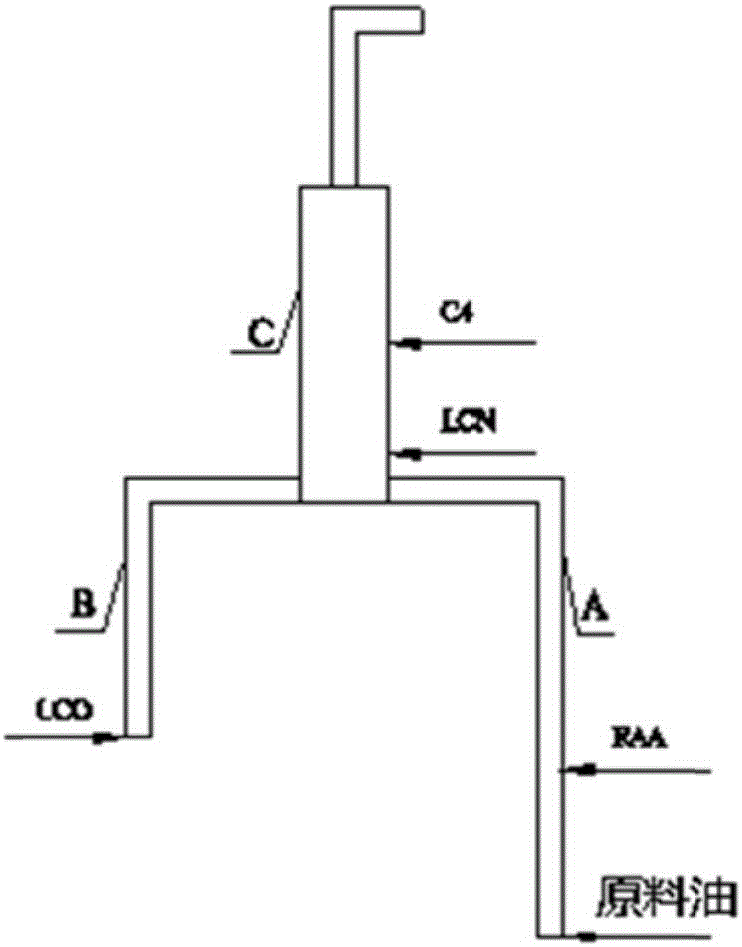
本发明涉及烃油加工生产乙烯和丙烯的领域,并具体涉及一种多产乙烯和丙烯的烃油加工方法及加工系统。
背景技术:
:乙烯是重要的有机化工基本原料,其主要用于生产聚乙烯、乙丙橡胶、聚氯乙烯等。乙烯同时也是世界上最大的化工产品之一,占全球整个石化产品产量的75%以上;丙烯也是重要的有机化工原料,其主要用于制丙烯腈、环氧丙烷、丙酮等。乙烯和丙烯用以生产多种重要有机化工原料、生成合成树脂、合成橡胶及多种精细化学品等,作为重要的化工中间物需求日益增长。采用传统的蒸汽裂解制乙烯、丙烯路线,对轻烃、石脑油等化工轻烃需求量较大,预计2020年需化工轻油70万吨/年,而国内原油普遍偏重,化工轻油难以满足乙烯、丙烯原料的需求,在石油资源不足的情况下,蒸汽裂解原料的多样化已成为乙烯、丙烯工业发展趋势。蒸汽裂解原料主要有轻烃(如乙烷、丙烷和丁烷)、石脑油、柴油、凝析油和加氢尾油,其中,石脑油的质量分数约占50%以上,典型石脑油蒸汽裂解的乙烯收率约29%-34%,丙烯收率为13%-16%,丙烯/乙烯比约为0.5,较低的丙烯/乙烯产出比难以满足当前丙烯需求的现状。采用石油烃催化裂解技术,通过工艺参数与催化剂性质的优化,可以有效提高低碳烯烃选择性,同时多产轻芳烃,该技术是当前乃至未来低碳烯烃和芳烃生产技术的研究热点。为了提高低碳烯烃特别是乙烯、丙烯的产率,以及轻芳烃的产率,现有技术主有:cn1234426a将重质石油烃和水蒸气在提升管和密相流化床组成的复合反应器的下部与催化剂接触;轻质石油烃进入复合反应器的上部即密相流化床底部与催化剂接触。cn1667089a将原料油或部分加氢循环油与再生的催化裂解催化剂、水蒸气在催化裂解反应器内接触反应。cn101362669a是在不同裂化性能的烃类与原料与催化裂解催化剂接触,在流化床反应器内进行裂化反应得到目的产物低碳烯烃、芳烃和再裂化的原料,再将轻芳烃经加氢、抽提后,将可裂化原料返回提升管,其中c2-c4烷烃进入蒸汽裂解进一步反应,乙烯和丙烯产率在20重量%以上,同时联产甲苯与二甲苯等芳烃。cn101362961a提出将馏程为160-260℃的原料与催化裂解催化剂接触,在流化床反应器内进行裂化反应得到目的产物低碳烯烃和芳烃,以使乙烯和丙烯产率和选择性增加。cn101469275b公开了一种劣质原油生产低碳烯烃的方法,其特征在于将预处理后的总酸值大于0.5mgkoh/g,特性因数k值大于12.1的原油经预热后直接引入催化裂化反应器中与催化剂接触,并在催化裂化反应条件下进行反应,分离反应后的油气和待生催化剂,反应油气送至后续分离系统,得到不同馏程的产物,待生催化剂经汽提、再生后循环使用,该技术克服了现有技术中加工此类原油生成较多辛烷值较低汽油致使经济效益较低的缺陷,有利于多产低碳烯烃,提高汽油辛烷值,提高了此类劣质原油加工的经济效益。cn102337154a提出在催化裂化条件下,将烃类原料与催化裂化催化剂在复合反应器中接触,得到低碳烯烃、富含轻芳烃汽油等产品,进一步分离得到轻芳烃。cn102344832a公布了一种石油烃催化转化方法,其特征在于原料油在反应器内与富含中孔沸石的催化剂接触进行反应,分离待生催化剂与反应油气,待生催化剂经再生后返回反应器,分离反应油气得到包括乙烯、丙烯、丙烷、丁烷和富含芳烃的催化汽油的产物,其中催化汽油经选择性加氢后,进入芳烃抽提装置分离得到目的产物轻芳烃,而抽余油与丙烷、丁烷经蒸汽裂解进一步生产乙烯、丙烯。从以上现有技术来看,烃类催化转化生产低碳烯烃的技术的开发主要集中于重质油催化裂解技术方面,由于重油的馏程范围较宽,烃类分子较大,产物结构纷繁复杂,非目标产物产率较高,为了提高低碳烯烃收率,通常采用较高的反应温度,造成在增加低碳烯烃产率情况下,干气产率尤其是甲烷产率大幅度增加。而以轻质原料油如石脑油为原料的催化裂解技术正处于研发阶段,就世界范围而言,乙烯生产一直以轻烃和石脑油为主要裂解原料,而石蜡基、中间基原料在裂解原料中所占比例甚少,但我国轻烃原料油资源有限,且大部分原油属重质油,直馏石脑油产量很少,迫使乙烯生产中蜡油原料所占比例较高。为了满足日益增长的低碳烯烃特别是丙烯需求以及轻芳烃的需求,并提高重质原料如常压蜡油等资源利用率,有必要开发一种降低催化裂解反应温度,同时,将蜡油馏分最大限度地转化为乙烯和丙烯的催化转化方法,进而实现石油资源的高效利用。技术实现要素:本发明的目的是为了克服现有技术存在的问题之一,提供一种多产乙烯和丙烯的烃油加工方法及加工系统,以同时增产乙烯和丙烯。为了实现上述目的,本发明提供了一种多产乙烯和丙烯的烃油加工方法,所述方法包括催化裂解步骤和油气分离后处理步骤,该催化裂解步骤包括:将原料油、重石脑油芳烃抽提后的抽余油和催化裂解催化剂在第一反应区中接触反应,生成第一反应混合物;将回炼的轻柴油和催化裂解催化剂在第二反应区中接触反应,生成第二反应混合物;将所述第一反应混合物、所述第二反应混合物、回炼的轻石脑油、以及回炼的c4烯烃在第三反应区中接触反应,生产第三反应混合物;将所述第三反应混合物送入沉降器进行待生催化剂和油气分离得到产品油气;所述油气分离后处理步骤中将所述产品油气进一步分为氢气、甲烷、产品乙烯和丙烯、乙烷、丙烷、c4烷烃、c4烯烃、轻石脑油、重石脑油、轻柴油、重柴油及以上组分,并将所述重石脑油进行芳烃抽提以形成轻芳烃和重石脑油芳烃抽提后的抽余油;其中将所述c4烯烃c4烯烃与轻石脑油、轻柴油和重石脑油芳烃抽提后的抽余油一起回流至相应反应区。同时本发明还提供了一种多产乙烯和丙烯的烃油加工系统,该系统包括催化裂解单元,所述催化裂解单元包括:第一提升管反应器,所述第一提升管反应器上设有原料油入口和第一反应混合物出口,并可选的设有重石脑油芳烃抽提后的抽余油回炼口;第二提升管反应器,所述第二提升管反应器上设有轻柴油回炼口和第二反应混合物出口;第三提升管反应器,所述第三提升管反应器上设有反应混合物入口、c4回炼口、以及第三反应混合物出口;其中所述第三提升管反应器中反应混合物入口分别与所述第一反应混合物出口及第二反应混合物出口相连。应用本发明所提供的多产乙烯和丙烯的烃油加工方法及加工系统,具有如下有益效果:1、通过对回炼的轻柴油进行单独催化裂解处理,有利于选择更适合轻柴油催化裂解的反应条件,进而优化轻柴油的催化裂解效果,多产汽油和低碳烯烃;2、通过对回炼的轻柴油进行单独催化裂解处理,可以在原料油催化裂解过程中不考虑轻柴油的催化裂解条件,进而可以降低原料油的催化裂解温度,从而降低干气和焦炭的量、增产乙烯和丙烯的量、同时降低催化裂解装置的耗能;3、通过将c4和轻石脑油在特定位置回炼,有利于促使轻柴油的催化裂解反应物和原料油的催化裂解反应物进一步进行催化裂解,进而有利于增产乙烯和丙烯的量。附图说明图1示出了根据本发明实施方式中提升管反应装置的结构示意图;图2示出了根据本发明实施方式中催化裂解单元的结构示意图;图3示出了根据本发明实施方式中烃油加工系统的结构示意图。附图标记说明具体实施方式在本文中所披露的范围的端点和任何值都不限于该精确的范围或值,这些范围或值应当理解为包含接近这些范围或值的值。对于数值范围来说,各个范围的端点值之间、各个范围的端点值和单独的点值之间,以及单独的点值之间可以彼此组合而得到一个或多个新的数值范围,这些数值范围应被视为在本文中具体公开。在本发明中提供了一种多产乙烯和丙烯的烃油加工方法,所述方法包括催化裂解步骤和油气分离后处理步骤,其中所述催化裂解步骤包括:将原料油、重石脑油芳烃抽提后的抽余油和催化裂化催化剂在第一反应区中接触反应,生成第一反应混合物;将回炼的轻柴油和催化裂化催化剂在第二反应区中接触反应,生成第二反应混合物;将所述第一反应混合物、所述第二反应混合物、回炼的轻石脑油、以及回炼的c4烯烃在第三反应区中接触反应,生产第三反应混合物;将所述第三反应混合物送入沉降器进行待生催化剂和油气分离得到产品油气;所述油气分离后处理步骤中将所述产品油气进一步分为氢气、甲烷、产品乙烯和丙烯、乙烷、丙烷、c4烷烃、c4烯烃、轻石脑油、重石脑油、轻柴油、重柴油及以上组分(沸点高于重柴油的馏分),并将所述重石脑油进行芳烃抽提以形成轻芳烃和重石脑油芳烃抽提后的抽余油;其中将所述c4烯烃与轻石脑油、轻柴油和重石脑油芳烃抽提后的抽余油一起回流至相应反应区。根据本发明的方法,可以将前述所提及的回炼原料可以根据产品需要,部分或全部回炼。根据本发明的方法,在所述第一反应区内部包括上喷嘴和下喷嘴,为了增加回炼轻柴油的转化率,优选情况下,所述原料油从下喷嘴进料,回炼的重石脑油芳烃抽提后的抽余油从上喷嘴进料;优选地,在所述第一反应区位于上下喷嘴之间的区间中,烃油的停留时间为0.2-5秒,优选0.5-2秒,例如可以为0.5、0.8、1、1.2、1.5、1.8、2以及这些比值中的任意两个所构成的范围中的任意时间值(秒)。剂油比为3-50,优选为5-12,例如可以为5、6、7、8、9、10、11、12以及这些比值中的任意两个所构成的范围中的任意比值;在上喷嘴至出口之间的区间中,烃油的停留时间为0.8-9.8秒,优选2-6秒,例如可以为2、2.5、2.8、3.2、3.5、4.2、4.8、5.2、5.8、6以及这些比值中的任意两个所构成的范围中的任意时间值(秒);剂油比为4-50,优选为5-12,例如可以为5、6、7、8、9、10、11、12以及这些比值中的任意两个所构成的范围中的任意比值。根据本发明的方法,在所述第二反应区中,烃油的停留时间为2-30秒,优选1-5秒。在第二反应区中的并未单独加入催化剂,其中催化剂是由第一反应区中烃油携带进入第二反应区。其中c4烯烃是以c4烯烃产品总量的10-100wt%回练,其中的烃油比在5-60范围内,优选为15-35,例如可以为15、18、20、22、25、28、30、32、35以及这些比值中的任意两个所构成的范围中的任意比值。根据本发明的方法,在所述第三反应区中内部包括上喷嘴和下喷嘴,为了增加重石脑油芳烃抽提后的抽余油的转化率,优选情况下,所述回炼的轻石脑油从下喷嘴进料,回炼的c4烯烃从上喷嘴进料;其中在第三反应区中上喷嘴和下喷嘴的位置均高于第一反应混合物和第二反应混合物输入的位置。优选地,在所述第三反应区位于上下喷嘴之间的区间中,烃油的停留时间为0.2-5秒,优选0.5-3秒,例如可以为0.5、0.8、1.2、1.5、2.2、2.5、2.8、3以及这些比值中的任意两个所构成的范围中的任意时间值(秒);剂油比为5-60,优选为5-12,例如可以为5、6、7、8、9、10、11、12以及这些比值中的任意两个所构成的范围中的任意比值;在上喷嘴至出口之间的区间中,烃油的停留时间为0.8-30秒,优选1-12秒,例如可以为1、1.5、2.0、2.6、3.2、4.2、5.6、6.2、7.3、8、8.8、9.6、10、10.5、11.2、12以及这些比值中的任意两个所构成的范围中的任意时间值(秒),剂油比为5-60,优选为5-12,例如可以为5、6、7、8、9、10、11、12以及这些比值中的任意两个所构成的范围中的任意比值。根据本发明的方法,烃油是从反应区的下部进入,向上流动,其中由“下喷嘴”进料的物料先进入反应区,而由“上喷嘴”进料的后进入反应区,并与先进料的物料混合反应。根据本发明的方法,前述提及的“剂油比”是指催化剂与烃油的重量比,其中烃油是指进入相应“区间”的原料烃油的总和,例如在第一反应区“上下喷嘴之间的区间”中烃油为原料油的量;“上喷嘴至出口之间的区间”中烃油为原料油与重石脑油芳烃抽提后的抽余油的总量。根据本发明的方法,优选情况下,所述第二反应区的反应温度高于所述第一反应区和第三反应区的反应温度,且所述第一反应区的接触反应的温度低于620℃。其中所述第二反应区中主要考虑回炼的轻柴油的催化裂解温度,通过促使轻柴油催化裂解有利于增产乙烯和丙烯的量;而第一反应区中可以不考虑轻柴油的催化裂解温度,这样催化裂解反应可以在相对较低的温度下进行,有利于在降低能耗的同时,降低干气和焦炭的含量;同时在第三反应区中,轻柴油已经在第二反应区中发生裂解反应,而进入至第三反应区中的经裂解生成的反应物可以在相对较低的温度下进一步裂解,因此第三接触反应的温度也可以相对降低,进而在降低能耗的同时,降低干气和焦炭的含量。根据本发明的方法,其中对于第一反应区、第二反应区、第三反应区的接触反应条件在满足前述温度变化规则的情况下,可以在较为宽泛的范围选择;优选情况下,所述第一反应区的接触反应条件包括:反应温度为500-620℃,优选为520-590℃,例如可以为530℃、540℃、550℃、560℃、570℃、580℃、590℃以及这些点值中的任意两个所构成的范围中的任意数值;压力为0.1-1.0mpa,优选为0.2-0.4mpa。优选情况下,所述第二反应区的接触反应条件包括:反应温度为600-750℃,优选为620-690℃,例如可以为620℃、630℃、640℃、650℃、660℃、670℃、680℃、690℃以及这些点值中的任意两个所构成的范围中的任意数值;压力为0.1-1.0mpa,优选为0.2-0.4mpa。优选情况下,所述第三反应区的接触反应条件包括:反应温度为490-610℃,优选为540-590℃,例如可以为540℃、550℃、560℃、570℃、580℃、590℃以及这些点值中的任意两个所构成的范围中的任意数值;压力为0.1-1.0mpa,优选为0.2-0.4mpa。根据本发明的方法,在第一反应区和第二反应区中通入预提升介质,以带动催化裂解催化剂上升,进而在反应器底部形成密度均匀的催化裂解催化剂活塞流。其中预提升介质可以为水蒸气、炼油厂干气、轻质烷烃、轻质烯烃中的一种或多种。根据本发明的方法,其中三次接触反应可以在任意的催化裂解反应器中进行,例如既可以在提升管反应器中进行,又可以在流化床反应器中进行;既可以在上行式反应器中进行,又可以在下行式反应器中进行;优选情况下,上述三次接触反应均在提升管反应器中进行,且当在提升管反应器中进行时,优选催化裂解装置自身干气代替预提升蒸汽,部分/全部取代雾化蒸汽之后引入反应器,通过提高干气氢分压,降低干气产率,由此可以进一步提高丙烯的选择性。根据本发明的方法,重点在对于工艺流程的改进,其中对于催化裂解过程中所采用的催化裂解催化剂可以没有特殊要求,只要适用于作为催化裂解催化剂使用即可,优选情况下,所述催化裂解催化剂为含有中孔沸石的催化裂解催化剂;更优选所述催化裂解催化剂以其总重量为基准,含有2-60重量%的沸石、10-99重量%的无机氧化物、0-70重量%的粘土;其中所述沸石中包括中孔沸石和可选的大孔沸石,优选以所述沸石的总重量为基准,所述沸石中含有50-95重量%的中孔沸石和5-50重量%的大孔沸石,更优选所述沸石中含有70-95重量%的中孔沸石和5-30重量%的大孔沸石。本发明所使用的催化裂解催化剂中,所述中孔沸石和大孔沸石沿用本领域常规的定义,即中孔沸石的平均孔径为0.5-0.6nm,大孔沸石的平均孔径为0.7-1.0nm。在本发明中可以选用的中孔沸石优选为具有mfi结构的沸石,例如zsm系列沸石和/或zrp沸石;优选情况下,在本发明中所选用的中孔沸石可以是通过磷等非金属元素和/或铁、钴、镍等过渡金属元素进行改性的中孔沸石;其中关于zrp沸石的详细描述可以参见us5,232,675中的记载,例如zrp-1;其中关于zsm系列沸石选自zsm-5、zsm-11、zsm-12、zsm-23、zsm-35、zsm-38、zsm-48和其它类似结构的沸石之中的一种或几种的混合物,其中关于zsm-5的详细描述可以参见us3,702,886。大孔沸石可以选自由稀土y(rey)、稀土氢y(rehy)、不同方法得到的超稳y(dasy)、高硅y构成的这组沸石中的一种或更多种的混合物。本发明所使用的催化裂解催化剂中,所述无机氧化物主要起到粘接剂的作用,优选选自二氧化硅(sio2)和/或三氧化二铝(al2o3)。其中二氧化硅前驱体为在焙烧的条件下能够转变为二氧化硅的物质,优选可以为硅溶胶;其中氧化铝前驱体为在焙烧的条件下能够转变为三氧化二铝的物质,优选为水合氧化铝和/或铝溶胶;所述水合氧化铝为选自薄水铝石、拟薄水铝石、三水合氧化铝和无定形氢氧化铝中的一种或几种。本发明所使用的催化裂解催化剂中,所述粘土主要起到基质(即载体)的作用,优选所述粘土为选自硅藻土、膨胀珍珠岩、高岭土、多水高岭土、硅质岩、水解氧化硅、大孔氧化硅和硅胶中一种或几种,优选选自高岭土和/或多水高岭土。根据本发明的方法,催化裂解催化剂在经历催化裂化反应后形成待生催化剂,该待生催化剂通过再生形成再生剂,所形成的再生剂被输送至第一反应区和第二反应区再次应用,其中对于再生处理的工艺条件采用相应催化剂的常规再生条件即可。根据本发明的方法,为了进一步增产乙烯和丙烯产品,优选情况下,所述油气分离后处理步骤还包括将所述乙烷、丙烷和c4烷烃与水蒸气接触反应以生成产品乙烯和丙烯,并副产乙烷、丙烷、c4烷烃、c4烯烃和蒸汽裂解轻石脑油,优选所述接触温度为700-1000℃;优选将副产的乙烷、丙烷、c4烷烃回流继续与水蒸气接触反应;优选将副产的所述c4烯烃和所述蒸汽裂解轻石脑油返回至第三反应区。众所周知,轻芳烃(苯、甲苯和二甲苯,简称btx)也是一种重要的有机化工原料,产量和规模仅次于乙烯和丙烯,其衍生物广泛用于生产化纤、塑料和橡胶等化工产品和精细化学品。根据本发明的方法,为了进一步增产轻芳烃,优选情况下,所述油气分离后处理步骤还包括将所述重石脑油进行芳烃抽提以形成轻芳烃和重石脑油芳烃抽提后的抽余油;此外,为了进一步增产乙烯和丙烯,优选情况下,将所述重石脑油芳烃抽提后的抽余油回流至第一反应区;此外,为了缩短重石脑油芳烃抽提后抽余油的反应时间减少生焦量,优选情况下,优选所述重石脑油芳烃抽提后的抽余油的进料喷嘴高于所述加氢处理重质蜡油的进料喷嘴。在本发明芳烃抽提的步骤中,对于抽提溶剂可以没有限定,例如所述抽提溶剂选自环丁砜、n-甲基吡咯烷酮、二乙二醇醚、三乙二醇醚、四乙二醇、二甲基亚砜和n-甲酰基吗啉醚中的一种或几种;对于芳烃抽提的操作条件可以没有特殊要求,例如该芳烃抽提的操作条件包括:温度为40-120℃,抽提溶剂与重石脑油的体积比为0.5-5:1。根据本发明的方法,优选情况下,所述原料油为重质油;更优选原料油为加氢处理重质蜡油,优选为流程大于350℃的加氢处理重质蜡油。根据本发明的方法,优选情况下,作为原料的所述重质油为选自或包括石油烃和/或其他矿物油。其中石油烃选自减压瓦斯油、常压瓦斯油,焦化瓦斯油、脱沥青油、常压渣油,加氢处理渣油、加氢处理瓦斯油、催化柴油,加氢催化柴油中的一种或几种,其他矿物油选自煤液化油,油砂油,页岩油中的一种或几种。优选所述重质油为石蜡基或中间基原料,优选所述重质油的密度为0.87-0.93g/cm3。优选为0.88-0.91g/cm3。残炭值为0-6wt%,优选为0-2wt%。根据本发明的方法,优选情况下,所述加氢处理的主要操作条件包括:反应温度为350-400℃,优选为360-390℃,例如可以为360℃、370℃、380℃、390℃以及这些点值中的任意两个所构成的范围中的任意数值;反应压力为7-15mpa,优选为9-13mpa,体积空速为0.5-1.5h-1,优选为0.6-1.2h-1,氢油比(氢气与烃油的体积比)为400-1500,优选为600-1200。根据本发明的方法,优选情况下,所述加氢处理中所采用的加氢催化剂包括:载体和负载在所述载体上的第ⅵb族金属和/或第ⅷ族非贵金属氧化物、且以所述加氢催化剂的总重量为基准,所述第ⅵb族金属以氧化态计的含量为3-35重量%,所述第ⅷ族非贵金属以氧化态计的含量为0.3-8重量%;优选所述载体为氧化铝和/或硅铝载体;优选第ⅵb族金属为mo和/或w;优选第ⅷ族金属为co和/或ni。其中硅铝载体是指含有氧化铝和氧化硅的复合载体。根据本发明的方法,为了进一步降低低附加值产品,并在不增加能耗的基础上,增产乙烯、丙烯和芳香烃,优选情况下,将所述重柴油及以上组分回流至所述加氢处理的步骤中,优选在实际操作中,将重柴油及以上组分中下层浆料(较重的部分)排出,而上层油料回流至所述加氢处理的步骤。同时,对应于本申请所提供的上述多产乙烯和丙烯的烃油加工方法,在本发明中还提供了一种多产乙烯和丙烯的烃油加工系统,所述系统包括催化裂解单元30,如图1所示,该催化裂解单元30包括:第一提升管反应器a,所述第一提升管反应器a上设有原料油入口、重石脑油芳烃抽提后的抽余油回炼口和第一反应混合物出口;第二提升管反应器b,所述第二提升管反应器b上设有轻柴油回炼口和第二反应混合物出口;第三提升管反应器c,所述第三提升管反应器c上设有反应混合物入口、c4回炼口、以及第三反应混合物出口;其中所述第三提升管反应器c中反应混合物入口分别与所述第一反应混合物出口及第二反应混合物出口相连。根据本发明的系统,如图2所示,优选情况下,所述催化裂解单元30还包括沉降装置32和再生装置33,所述沉降装置32的反应混合物入口与所述第三提升管反应器c的第三反应混合物出口相连,所述沉降装置32的待生剂出口与所述再生装置33的待生剂入口相连,所述再生装置33的再生剂出口分别与第一提升管反应器a和第二提升管反应器b的催化剂入口相连。其中沉降装置32和再生装置33均采用常规装置即可,沉降装置32中包括旋风分离器321和汽提器322;再生装置33中包括旋风分离器331和主风分布板332;沉降装置32和再生装置33之间的待生剂输送管道上形成有待生剂循环滑阀323;再生装置33与第一提升管反应器a和第二提升管反应器b之间的再生剂输送管道上分别设置有再生剂循环滑阀333。根据本发明的系统,优选情况下,所述系统还包括原料油供应单元,所述原料油供应单元与第一提升管反应器a上原料油入口配合连接,用于向所述第一提升管反应器a中供应原料油;根据本发明的系统,如图3所示,优选情况下,所述系统还包括催化裂解分馏单元40、气体分离单元、轻重汽油分离单元50、以及轻重柴油分离单元60;所述催化裂解分馏单元40与所述沉降装置32配合连接,用于将沉降装置分离得到的产品油气分馏为干气42a、液化气42b、石脑油41b、42c、柴油及以上组分41c;所述气体分离单元50与所述催化裂解分馏单元40配合连接,用于将所述干气42a和液化气42b分离得到氢气、甲烷、产品乙烯和丙烯、乙烷、丙烷、c4烷烃和c4烯烃,其中c4烯烃作为c4烯烃回流至所述第三提升管反应器c;所述轻重石脑油分离单元50与所述催化裂解分馏单元40配合连接,用于将石脑油41b和42c分为轻石脑油51a和重石脑油51b,其中所述轻石脑油51a回流至所述第三提升管反应器c;所述轻重柴油分离单元60与所述催化裂解分馏单元40配合连接,用于将所述柴油及以上组分41c分为轻柴油61a和重柴油及以上组分61b,其中将所述轻柴油61a回流至所述第二提升管反应器b。优选情况下,所述第一提升管反应器a内部设置有上喷嘴和下喷嘴,所述下喷嘴与原料油入口相连,所述上喷嘴与回炼的重石脑油芳烃抽提后的抽余油相连。优选情况下,所述第三提升管反应器c内部设置有上喷嘴和下喷嘴,所述下喷嘴与轻石脑油回炼口相连,所述上喷嘴与c4烯烃回炼口相连。根据本发明的系统,其中催化裂解分馏单元40主要用于对催化裂解产品油气进行分馏,其中包括催化裂解主分馏塔41和轻组分分离罐42;其中经过催化裂解主分馏塔41将沉降装置分离得到的产品油气分馏为塔顶油气41a、石脑油41b、以及柴油及以上组分41c。轻组分分离罐42包括吸收塔、解析塔、再吸收塔、稳定塔等,其能够将由催化裂解主分馏塔41排出的塔顶油气41a分离为干气(主要为h2、ch4、c3组分)42a,液化气(c3和c4)42b和石脑油42c,其中干气(主要为h2、ch4、c3组分)42a,液化气(c3和c4)42b被输送至后续气体分离单元,而石油脑42c被输送至轻重汽油分离单元。根据本发明的系统,其中气体分离单元主要用于对催化裂解分馏单元40分馏获得的干气42a和液化气42b中的低碳烯烃进行分离处理。该气体分离单元中包括有富气压缩机,脱丙烷塔、脱丁烷塔、脱甲烷塔,脱乙烷塔、乙烯精馏塔、丙烯精馏塔和丁稀精馏塔等。在实际操作中,催化裂解分馏单元40分馏获得的干气和液化气经富气压缩机提高压力后送入脱丙烷塔。经过分离,脱丙烷塔底排处c4和c5馏分,经冷却后进入脱丁烷塔,脱丁烷塔顶物流进入丁烯精馏塔,脱丁烷塔底物流排出c5馏分,该c5馏分可以与轻石脑油并流后作为轻石脑油返回至第三提升管反应器c;丁烯精馏塔顶排出的c4烯烃(丁烯)返回催化裂解单元30中第三提升管反应器c,丁烯精馏塔底c4烷烃(丁烷)可选地返回催化裂解单元30或(优选地)输送至后续蒸汽裂解单元。脱丙烷塔顶排出c3-馏分,经冷却后送入脱甲烷塔,脱甲烷塔顶排出主要含甲烷和氢气的燃料气,脱甲烷塔底物流送入脱乙烷塔;脱乙烷塔顶物流送入乙烯精馏塔,脱乙烷塔底物流送入丙烯精馏塔,乙烯精馏塔顶排出聚合级乙烯,乙烯精馏塔底排出的乙烷后续送蒸汽裂解单元。丙烯精馏塔顶排出聚合级丙烯,丙烯精馏塔底排出的丙烷送裂解单元。根据本发明的系统,为了进一步增产乙烯和丙烯,优选情况下,所述系统还包括蒸汽裂解单元,所述蒸汽裂解单元与所述气体分离单元配合连接,用于将乙烷、丙烷和c4烷烃与水蒸气接触反应以生成产品乙烯和丙烯、并副产乙烷、丙烷、c4烯烃和c4烷烃、c5组分和蒸汽裂解轻石脑油,其中副产的乙烷、丙烷和c4烷烃回流至所述蒸汽裂解单元;副产的c4烯烃和蒸汽裂解轻石脑油(c5组分并流至该轻石脑油中)回流至所述第三提升管反应器c。该蒸汽裂解单元的反应条件参照前述方法部分的描述。根据本发明的系统,优选情况下,所述系统还包括芳烃抽提单元,所述芳烃抽提单元与所述轻重石脑油分离单元50配合连接,用于对重石脑油进行芳烃提取并获取重石脑油芳烃抽提后的抽余油,所述重石脑油芳烃抽提后的抽余油可以回流至所述第一提升管反应器a,也可以输送至蒸汽裂解单元进行裂解。其中芳烃提取单元可以采用常规的芳烃抽提单元,例如在芳烃抽提单元中可以包括抽提蒸馏塔、抽提蒸馏溶剂回收塔、液液抽提塔、汽提塔和液液抽提回收塔等。该芳烃抽提单元的反应条件和所使用的抽提溶剂参照前述方法部分的描述。根据本发明的系统,优选情况下,所述系统还包括加氢精制单元10和加氢分馏单元20,所述加氢精制单元10与所述原料油供应单元配合连接,用于氢化处理所述原料油得到氢化产物;所述加氢分馏单元20与所述加氢精制单元10配合连接,用于将所述氢化产物分馏获取加氢处理重质蜡油;所述加氢分馏单元20与所述催化裂解单元30中第一提升管反应器a的原料油入口配合连接,用于向所述第一提升管反应器a中供应加氢处理重质蜡油(馏程大于350℃的重质组分)。根据本发明的系统,其中加氢处理单元10可以采用常规的加氢处理单元,例如其中主要包括有新氢压缩机11、原料预热炉12、加氢精制反应器13、换热器14、水冷器15、高压分离器16和低压分离器17。其中新氢压缩机11通过原料预热炉12与加氢精制反应器13相连,加氢精制反应器13的出口端通过先后设置的高压分离器16和低压分离器17与后续的加氢分馏单元相连,其中高压分离器16将加氢精制产物中混合的氢气分离,这部分循环氢气返回至原料预热炉12中,其中低压分离器17将加氢精制产物中的塔顶气脱除。此外,为了形成整个系统的热平衡,并适用于高压分离器16的温度,优选情况下,在加氢精制反应器13和高压分离器16之间还形成有换热器14和水冷器15。该加氢精制反应器13的反应条件参照前述方法部分的描述。根据本发明的系统,其中加氢分馏单元20主要用于对加氢精制产物进行分馏,其中包括加氢精制分馏塔21,并且经过该加氢精制分馏塔21将加氢精制产物分馏为塔顶不凝气21a、石脑油馏分21b、航煤馏分21c、优质车用柴油馏分21d以及塔底重质蜡油21e(加氢处理重质蜡油,优选为馏程大于350℃的重质组分),其中塔底重质蜡油被送入至后续的催化裂化单元。根据本发明的系统,为了进一步提高催化裂解副产品的利用率,减少低附加值产品,优选情况下,所述轻重柴油分离单元70分离获得的重柴油及以上组分回流至所述加氢精制单元。下面将结合具体实施例和对比例对发明多产乙烯和丙烯的烃油加工方法及加工系统予以进一步的说明。在如下实施例和对比例中所用的重质原料油1为源自中国石油化工股份有限公司镇海分公司的加氢蜡油,重质原料油2为源自中国石油天然气公司大庆石化分公司的减压蜡油,其主要性质如表1所示。表1.项目重质原料油1重质原料油2密度(20℃,g/cm30.9030.8582运动粘度(100℃),mm2/s8.3254.174凝点,℃-15-20运动粘度(80℃),mm2/s12.5826.143苯胺点,℃-103.4折光指数,(nd70)-1.4585残炭,wt%0.520.21碱性氮,ppm236155c,84.5385.98n,ppm582417h,12.5613.66s,ppm1352885初馏点2682625%32131010%34533330%39538250%52341470%45144490%50249095%526513链烷烃含量,wt%2814在如下实施例和对比例中所用的催化裂解催化剂制备方法简述如下:1)将20gnh4cl溶于1000g水中,向此溶液中加入100g(干基)晶化产品zrp-1沸石(齐鲁石化公司催化剂厂生产,si/al=30(摩尔比),稀土含量re2o3=2.0重量%),在90℃交换0.5h后,过滤得滤饼;加入4.0gh3po4(浓度85重量%)与4.5gfe(no3)3溶于90g水中,与滤饼混合浸渍烘干;接着在550℃温度下焙烧处理2小时得到含磷和铁的mfi结构中孔沸石,经元素分析化学,该中孔沸石包括:0.1wt%的na2o、5.1wt%的al2o3、2.4wt%的p2o5、1.5wt%的fe2o3、3.8wt%的re2o3、以及88.1wt%的sio2。2)用250kg脱阳离子水将75.4kg多水高岭土(苏州瓷土公司工业产品,固含量71.6重量%)打浆,再加入54.8kg拟薄水铝石(山东铝厂工业产品,固含量63重量%),用盐酸将其ph调至2-4,搅拌均匀,在60-70℃下静置老化1小时,保持ph为2-4,将温度降至60℃以下,加入41.5kg铝溶胶(齐鲁石化公司催化剂厂产品,al2o3含量为21.7重%),搅拌40分钟,得到混合浆液。3)将步骤1)制备的含磷和铁的mfi结构中孔沸石(干基为22.5kg)以及dasy沸石(齐鲁石化公司催化剂厂工业产品,晶胞常数为2.445-2.448nm,干基为2.0kg)加入到步骤2)得到的混合浆液中,搅拌均匀,喷雾干燥成型,用磷酸二氢铵溶液(磷含量为1重量%)洗涤,洗去游离na+,干燥即得催化裂解催化剂样品,该催化剂的组成为18重量%含磷和铁的mfi结构中孔沸石、2重量%dasy沸石、36重量%的氧化铝和44重量%的高岭土。上述制备的催化裂化催化剂的主要性质如表2所示。表2.在如下实施例和对比例中所用的加氢处理催化剂制备方法简述如下:称取偏钨酸铵((nh4)2w4o13·18h2o,化学纯)和硝酸镍(ni(no3)2·18h2o,化学纯),用水配成200ml溶液。将溶液加入到氧化铝载体50g中,在室温下浸渍3小时,在浸渍过程中使用超声波处理浸渍液30分钟,冷却,过滤,放到微波炉中干燥约15分钟。该催化剂的组成为:30.0重量%wo3、3.1重量%nio和66.9重量%的氧化铝。在如下实施例和对比例中所用的抽提溶剂为环丁砜,化学纯。实施例1所采用的烃油加工系统:如图3所示;所采用的烃油加工方法:将重质油原料1(性质如表1中样品a所示)输送至原料预热炉12,与来自新氢压缩机11的氢气混合,加热后,进入加氢精制反应器13(反应条件包括:温度为370℃,氢分压为10mpa,氢油(体积)比为800,体积空速为1.0h-1,其中加氢催化剂为前述提供的加氢催化剂)。该加氢精制反应器13分三个反应区,中间区通入冷氢以调节反应温度。反应后的油气进入换热器14,换热后物料进入水冷器15进一步冷却后,进入高压分离器16分离出循环氢(循环氢经过循环氢压缩机压缩后进入原料预热炉12),高压分离器16分离后的重组分进入低压分离器17,后进入加氢精制装置分馏塔21,塔顶分离出塔顶不凝气21a进入瓦斯官网,分馏塔中段抽出石脑油馏分21b,以及航煤馏分21c和优质车用柴油的调21d和塔底流程大于350℃的重质组分(加氢处理重质蜡油)。将加氢处理重质蜡油预热至260℃作为原料油通过提升管管线进入催化裂解单元中的第一提升管反应器a(第一反应区)中,与回炼的重石脑油芳烃抽提后的抽余油(raa)31d(raa进入上喷嘴,加氢处理重质蜡油进入下喷嘴)、雾化蒸汽、以及催化裂化催化剂(为前述提供的催化裂化催化剂)进行接触反应(反应条件参见表3)生产第一反应混合物;与此同时,将回炼的轻柴油31a(lco)通过回流管线进入催化裂解单元中的第二提升管反应器b(第二反应区)中,与雾化蒸汽和催化裂解催化剂(为前述提供的催化裂化催化剂)进行第二接触反应(反应条件参见表3),生成第二反应混合物,并使得第一反应混合物和第二反应混合物进入催化裂解单元中的第三提升管反应器c(第三反应区)中,与回炼的轻石脑油31c(lcn)、回炼的c4烯烃31b(c4烯烃进入上喷嘴,轻石脑油进入下喷嘴)进行第三接触反应(反应条件参见表3),生成第三反应混合物,使得第三反应混合物进入沉降装置32(压力为0.13mpa)的旋风分离器321中分离出待生剂和产品油气,待生剂进入汽提器322进行汽提,汽提后的待生剂通过待生剂循环滑阀323进入再生器33中与再生器底部主风分布板332进入的空气接触(压力为0.15mpa、温度为700℃、床层密度为3kg/m3)烧焦;所生产的烟气和再生剂通过旋风分离器331进行分离,烟气通过进入烟道,再生剂进入再生器底部,通过再生剂循环滑阀333进入催化裂解单元中第一提升管反应器a和第二提升管反应器b中。由沉降装置32分离产生的产品油气通过油气输送管线进入催化裂解主分馏塔41,被分为塔顶油气41a、石脑油41b、以及柴油及以上41c。其中塔顶油气41a经过转油线进入轻组分分离罐42,经过吸收塔、解析塔、再吸收塔、稳定塔等将塔顶油气41a分离为干气(主要为h2、ch4、c2组分)42a、液化气(c3、c4)42b与石脑油42c;将轻组分分离罐42分离产生的干气42a和液化气42b通过油气输送管线进入气体分离单元(包括富气压缩机,脱丙烷塔、脱丁烷塔、脱甲烷塔,脱乙烷塔、乙烯精馏塔、丙烯精馏塔和丁稀精馏塔等),被分离为氢气、甲烷、产品乙烯和丙烯,乙烷、丙烷、c4烷烃、c4烯烃和c5馏分;其中c4烯烃回流至第三提升管反应器c中进行回炼;将气体分离单元产生的乙烷、丙烷和丁烷输送至蒸汽裂解单元与水蒸气在830℃下接触反应,以生成产品乙烯和丙烯、乙烷、丙烷、c4烯烃和c4烷烃、c5组分和蒸汽裂解轻石脑油,其中乙烷、丙烷和c4烷烃回流至蒸汽裂解单元生产乙烯和丙烯,c4烯烃和蒸汽裂解轻石脑油回流至第三提升管反应器c中进行回炼;将催化裂解主分馏塔41产生的石脑油41b和轻组分分离罐42分离的石脑油42c通过油气管道输送至轻重石脑油分离单元50,分离为轻石脑油51a和重石脑油51b;其中轻石脑油51a回流至第三提升管反应器c中进行回炼;将轻重石脑油分离单元50中分离的重石脑油51b输送至芳烃抽提单元,经环丁砜抽提,抽提温度为100℃,环丁砜溶剂与汽油的体积比为3.0:1分出轻芳烃(btx)和催化重石脑油芳烃抽提后的抽余油,其中催化重石脑油芳烃抽提后的抽余油回流至第一提升管反应器a中进行回炼;将将催化裂解主分馏塔41产生的柴油及以上组分41c通过油气管道输送至轻重柴油分离单元60,分离为轻柴油61a和重柴油及以上61b,其中轻柴油61a回流至第二提升管反应器b中进行回炼;重柴油及以上组分61b返回至加氢精制反应器13进行回炼。该装置稳定运行后的产品分布如表5所示。实施例2-3所采用的烃油加工系统:参照图3所示烃油加工系统,区别在于,不包括加氢精制反应器13、加氢精制装置分馏塔21、以及与两者相关的装置;所采用的烃油加工方法:参照实施例1,区别在于,采用重质油原料2(性质如表1)代替重质油原料1;且重质油原料2未经加氢处理直接预热至260℃作为原料油通过提升管管线进入催化裂解单元中。该烃油加工方法中第一、第二以及第三提升管的反应条件如表3所示,该装置稳定运行后的产品分布如表4所示。对比例1所采用的烃油加工系统:参照图3中系统,区别在于,不包括三个提升管反应器,仅包括一个提升管反应器;所采用的烃油加工方法:采用实施例1中的工艺方法,区别在于在催化裂化单元中,将加氢处理重质蜡油预热至260℃作为原料油通过提升管管线进入仅包括一个提升管反应器的催化裂解单元中,且将lco和lcn的混合物回流至该提升管反应器中(加氢处理重质蜡油进入上喷嘴,lco和lcn的混合物进入下喷嘴)。该系统中提升管反应器的反应条件如表4所示;该装置稳定运行后的产品分布如表5所示。对比例2-3所采用的烃油加工系统:参照图3中系统,区别在于,1)不包括加氢精制反应器13、加氢精制装置分馏塔21、以及与两者相关的装置;2)不包括三个提升管反应器,仅包括一个提升管反应器;所采用的烃油加工方法:采用实施例2-3中的工艺方法,区别在于在催化裂化单元中,将重质油原料2预热至260℃作为原料油通过提升管管线进入仅包括一个提升管反应器的催化裂解单元中,并将lco和lcn的混合物回流至该提升管反应器中(加氢处理重质蜡油进入上喷嘴,lco和lcn的混合物进入下喷嘴)。该系统中提升管反应器的反应条件如表4所示;该装置稳定运行后的产品分布如表5所示。表3.表4.表5.以上详细描述了本发明的优选实施方式,但是,本发明并不限于此。在本发明的技术构思范围内,可以对本发明的技术方案进行多种简单变型,包括各个技术特征以任何其它的合适方式进行组合,这些简单变型和组合同样应当视为本发明所公开的内容,均属于本发明的保护范围。当前第1页12