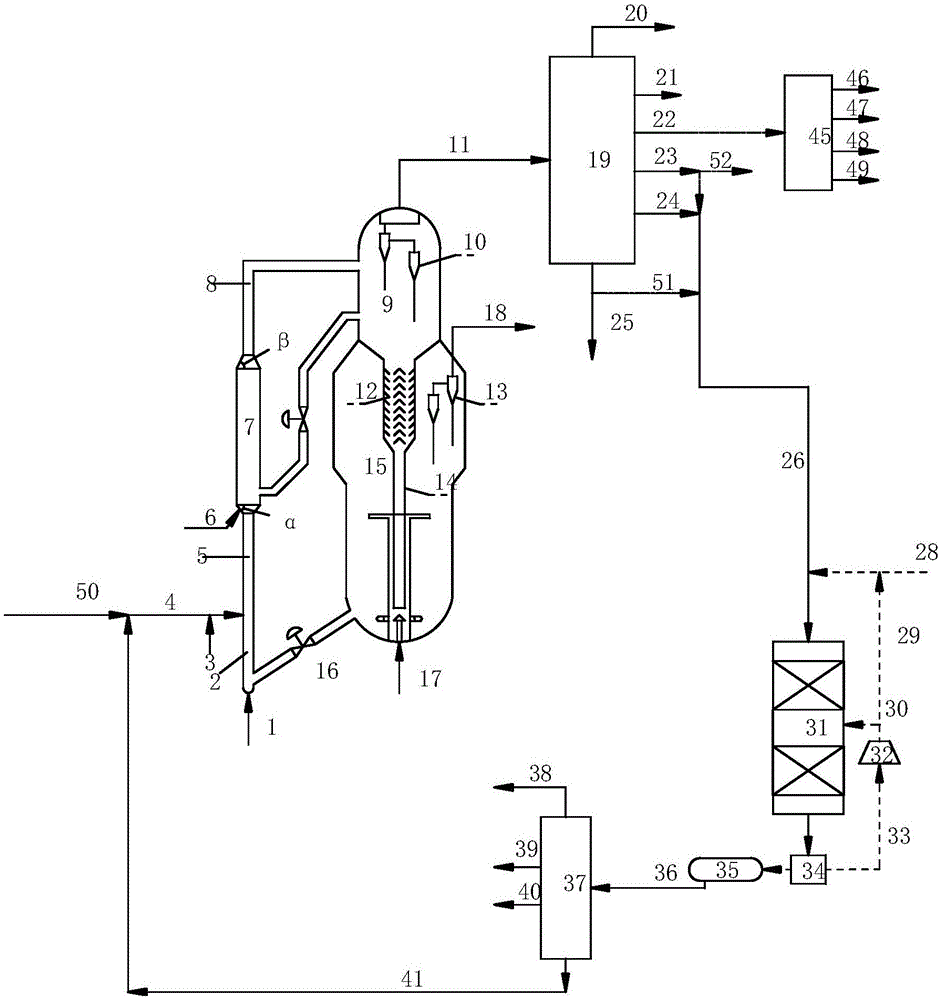
本发明涉及一种多产异丁烷和轻质芳烃的催化裂化方法。
背景技术:
:芳烃中的苯、甲苯、二甲苯(简称btx)是重要的化工原料,苯可以用来合成苯乙烯、苯酚和苯胺等产品,甲苯既可以作为有机合成的优良溶剂,而且是合成甲酚的理想原料;二甲苯中的邻二甲苯、间二甲苯和对二甲苯是有机合成的基础原料。异丁烷作为重要的化工原料,可用于与c3~c5烯烃发生烷基化反应制备烷基化油制取烷基化油;与丙烯发生共氧化反应生产环氧丙烷(po)并联产叔丁醇(tba)或者生产甲基叔丁基醚(mtbe);通过异丁烷脱氢反应制备异丁烯。随着我国化工行业的发展,市场对于btx和异丁烷的需求日益增加,如何扩展其来源是目前我国化工技术发展的目标之一。常规的催化裂化工艺主要用于生产汽油并已取得汽油产率高达50重%以上的突破,满足了汽油无铅化的要求,提高了汽油的辛烷值,但无论是通过改变工艺条件,还是使用新型的沸石催化剂来提高汽油辛烷值,都是以提高汽油组分中的烯烃含量来增加汽油的辛烷值,目前汽油组分中烯烃含量为35~65重%,这与国家标准对烯烃含量的要求相差甚远。液化气组成中烯烃含量更高,大约在70重%,其中丁烯是异丁烷的数倍,难以作为烷基化原料。美国专利usp5154818公开了一种多种原料催化裂化生产较多高辛烷值汽油的方法,轻质烃类原料与待生催化剂在常规提升管反应器的第一反应区接触发生芳构化反应和低聚反应,生成的油气和重质烃类原料进入第二反应区,与再生催化剂接触发生裂化反应,生成的油气和待生催化剂在沉降器中分离,油气去分离系统分离,汽提后的待生催化剂一部分返回第一反应区,另一部分则进入再生器进行烧焦再生,热的再生催化剂返回第二反应区循环使用。美国专利us5685972公开了一种从催化裂化石脑油制取btx的方法。该方法使用的原料为催化裂化石脑油和焦化石脑油,使用的催化剂优选zsm-5或者带有加氢功能组分的催化剂。中国专利cn104560166a公开了一种催化转化方法,该方法为:催化裂化轻循环油经切割得到轻馏分和重馏分、重馏分经加氢处理得到加氢重馏分,轻馏分和加氢重馏分分开进入到催化裂化装置的副提升管反应器、重质石油烃进入催化裂化装置的主提升管反应器。该方法能够最大限度地优化满嘴轻循环油不同馏分催化裂化反应所需的苛刻条件,从而最大限度地生产高辛烷值的催化汽油。中国专利cn990304a公开了一种多产异丁烷和富含异构烷烃汽油的催化转化方法,其重油加工能力提高、干气和油浆产率下降、汽油烯烃和硫含量大幅降低、装置能耗进一步减小。该技术于2002年实现工业化,目前已应用到100多套fcc装置,取得巨大的经济效益和良好社会效益。技术实现要素:本发明的目的是提供一种多产异丁烷和轻质芳烃的催化裂化方法,本发明的方法能够多产轻质芳烃和异丁烷。为了实现上述目的,本发明提供一种多产异丁烷和轻质芳烃的催化裂化方法,该方法包括:(1)、将催化裂化原料油送入催化裂化反应器中与催化裂化催化剂接触并依次在不同反应条件下进行第一催化裂化反应和第二催化裂化反应,得到反应产物和待生催化剂;其中,所述催化裂化原料油中双环以上环烷烃的含量大于25重量%;(2)、将所得反应产物进行分离,得到干气、液化气、汽油、轻循环油、重循环油、以及得到或不得到油浆;(3)、将步骤(2)中所得轻循环油、重循环油和油浆任选地送入加氢装置与加氢催化剂接触并进行选择性加氢处理,得到加氢尾油作为所述催化裂化原料油送入所述催化裂化反应器中;(4)、任选将步骤(2)中所得汽油进行抽提精制,得到轻质芳烃。可选的,所述催化裂化原料油中双环以上环烷烃的含量大于40重量%。可选的,所述催化裂化原料油为选自深度加氢轻循环油、延迟焦化装置的重馏分油、催化裂化轻循环油、催化裂化重循环油、催化裂化重馏分油、油浆、加氢裂化柴油、渣油加氢裂化柴油、蜡油加氢裂化柴油、生物柴油、页岩油柴油馏分、煤液化柴油馏分、常压塔顶油、常压塔抽出的馏分油、直馏减压蜡油、加氢蜡油、焦化蜡油、脱沥青油、抽出油、抽余油、常压渣油和减压渣油中的至少一种二次加工原料和/或至少一种所述二次加工原料进行加氢所得加氢尾油。可选的,若所述二次加工原料中双环以上环烷烃的含量不大于25重量%,将所述二次加工原料进行芳烃抽提和/或所述选择性加氢处理后再作为所述催化裂化原料油。可选的,所述第一催化裂化反应的条件包括:反应温度为520℃-620℃,反应时间为0.5-3.0秒,剂油重量比为(3-15):1;所述第二催化裂化反应的条件包括:反应温度为420-530℃,反应时间为2-30秒,剂油重量比为(3-18):1。可选的,所述第一催化裂化反应的条件包括:反应温度为530℃-600℃,反应时间为0.8-2.0秒,剂油重量比为(4-12):1;所述第二催化裂化反应的条件包括:反应温度为460-510℃,反应时间为3-15秒,剂油重量比为(4-15):1。可选的,所述催化裂化反应器为等直径提升管、等线速提升管、变径提升管、流化床、或等直径提升管与流化床构成的复合反应器。可选的,所述变径提升管沿竖直方向由下至上依次设置有同轴且流体连通的预提升段、第一反应区、第二反应区和出口区,所述出口区末端设置有用于连接沉降器的水平管,所述第一反应区的内径小于第二反应区,所述第二反应区的内径大于出口区,所述变径提升管的总高度为10-60米,所述催化裂化催化剂送入所述预提升段中,所述催化裂化原料油送入所述第一反应区的下部,所述第一催化裂化反应在第一反应区中进行,所述第二催化裂化反应在第二反应区中进行。可选的,所述第一反应区和第二反应区的结合区域设置有至少一个用于送入激冷介质的激冷介质入口;和/或所述第二反应区中设置有取热器,所述取热器的高度占第二反应区高度的50-90%。可选的,所述激冷介质为选自冷激剂、冷却的再生催化剂、冷却的半再生催化剂和新鲜催化剂中的至少一种,所述激冷剂为选自液化气、粗汽油、稳定汽油、轻循环油、重循环油和水中的至少一种。可选的,所述催化裂化催化剂包括裂化活性组分和载体;以干基计,所述裂化活性组分包括10-90重量%的fau型沸石和10-90重量%的五元环结构沸石;所述fau型沸石为选自y型沸石、hy型沸石和超稳y型沸石中的至少一种,所述五元环结构沸石为选自zsm-5系列沸石、高硅沸石和镁碱沸石中的至少一种,所述五元环结构沸石含或不含稀土以及含或不含磷。可选的,所述选择性加氢处理的条件包括:氢分压为10.0-30.0兆帕,反应温度为300-500℃,液相体积空速为0.1-10.0小时-1,氢油体积比为100-1500nm3/m3。可选的,所述加氢催化剂包括加氢活性组分和载体,所述加氢活性组分为第vib族非贵金属和/或第viii族非贵金属,所述载体为选自氧化铝、二氧化硅和无定型硅铝中的至少一种。可选的,步骤(4)中所述抽提精制的条件包括:抽提溶剂为选自环丁砜、二甲亚砜、n-甲酰基吗啉、四甘醇、三甘醇和n-甲基吡啶烷酮中至少一种,温度为50-110℃,抽提溶剂与汽油的重量比为2-6。可选的,所述芳烃抽提的条件包括:温度为50-70℃,溶剂与原料重量比为0.5-2,溶剂选自糠醛、二甲亚砜、二甲基甲酰胺、单乙醇胺、乙二醇和1,2-丙二醇中的至少一种。本发明的优点在于:1、充分利用富含多环环烷烃的原料油,可以实现对富含多环环烷烃的原料油高效利用。2、产物液化气中异丁烷含量有效提升,汽油产率大于40重%,产物汽油中轻质芳烃含量提高。本发明的其他特征和优点将在随后的具体实施方式部分予以详细说明。附图说明附图是用来提供对本发明的进一步理解,并且构成说明书的一部分,与下面的具体实施方式一起用于解释本发明,但并不构成对本发明的限制。在附图中:图1是本发明提供的方法第一种具体实施方式的流程示意图。图2是本发明提供的方法第二种具体实施方式的流程示意图。图3是本发明提供的方法第三种具体实施方式的流程示意图。附图标记说明1管线2预提升段3管线4管线5第一反应区6管线7第二反应区8出口区9沉降器10旋风分离器11管线12汽提器13旋风分离器14待生立管15再生器16再生斜管17管线18管线19分馏系统20管线21管线22管线23管线24管线25管线26管线27管线28管线29管线30管线31加氢装置32循环压缩机33管线34高压分离器35低压分离器36管线37加氢装置分馏系统38管线39管线40管线41管线42芳烃抽提装置43管线44管线45抽提精制装置46管线47管线48管线49管线50管线51管线52管线具体实施方式以下结合附图对本发明的具体实施方式进行详细说明。应当理解的是,此处所描述的具体实施方式仅用于说明和解释本发明,并不用于限制本发明。本发明提供一种多产异丁烷和轻质芳烃的催化裂化方法,该方法包括:(1)、将催化裂化原料油送入催化裂化反应器中与催化裂化催化剂接触并依次在不同反应条件下进行第一催化裂化反应和第二催化裂化反应,得到反应产物和待生催化剂;其中,所述催化裂化原料油中双环以上环烷烃的含量大于25重量%;(2)、将所得反应产物进行分离,得到干气、液化气、汽油、轻循环油、重循环油、以及得到或不得到油浆;(3)、将步骤(2)中所得轻循环油、重循环油和油浆(若进行加氢处理,则优选经过过滤)任选地送入加氢装置与加氢催化剂接触并进行选择性加氢处理,得到加氢尾油作为送入所述催化裂化原料油送入所述催化裂化反应器中;(4)、任选将步骤(2)中所得汽油进行抽提精制,得到轻质芳烃(例如苯、甲苯、二甲苯),液化气可以分离得到丙烯和异丁烷等产品。根据本发明,所述催化裂化原料油中双环以上环烷烃的含量优选大于40重量%,且含量越高越好。所述催化裂化原料油可以为选自深度加氢轻循环油、延迟焦化装置的重馏分油(cgo)、催化裂化轻循环油(lco)、催化裂化重循环油(hco)、催化裂化重馏分油(fgo)、油浆、加氢裂化柴油、渣油加氢裂化柴油、蜡油加氢裂化柴油、生物柴油、页岩油柴油馏分、煤液化柴油馏分、常压塔顶油、常压塔抽出的馏分油、直馏减压蜡油、加氢蜡油、焦化蜡油、脱沥青油(dao)、抽出油、抽余油、常压渣油和减压渣油中的至少一种二次加工原料和/或至少一种所述二次加工原料进行加氢所得加氢尾油。本发明催化裂化反应所产生的油浆可以任选地先进入油浆过滤系统,然后进入加氢精制装置进行加氢饱和,再循环至本发明所述的催化裂化反应器,或所产生的油浆直接外甩出装置;所述加氢饱和的条件可以与选择性加氢反应相同或类似。另外,若所述二次加工原料中双环以上环烷烃的含量不大于25重量%,可以将所述二次加工原料进行芳烃抽提和/或所述选择性加氢处理后再作为所述催化裂化原料油,芳烃抽提优选将原料分为富含多环环烷烃的抽余油和富含多环芳烃的抽出油,抽出油再通过加氢精制饱和其多环芳烃,形成多环芳烃。根据本发明,芳烃抽提是本领域技术人员所熟知的,例如,所述芳烃抽提的条件可以包括:温度为50-70℃,溶剂与原料重量比为0.5-2,溶剂为选自糠醛、二甲亚砜、二甲基甲酰胺、单乙醇胺、乙二醇和1,2-丙二醇中的至少一种。根据本发明,催化裂化反应是本领域技术人员所熟知的,第一催化裂化反应主要发生裂化反应,所述第一催化裂化反应的条件可以包括:反应温度为520℃-620℃,优选为530℃-600℃,反应时间为0.5-3.0秒,优选为0.8-2.0秒,剂油重量比为(3-15):1,优选为(4-12):1;所述第二催化裂化反应主要发生选择性氢转移、异构化反应和芳构化反应,其条件可以包括:反应温度为420-530℃,优选为460-510℃,反应时间为2-30秒,优选为3-15秒,剂油重量比为(3-18):1,优选为(4-15):1,水油比为(0.03-0.3):1,优选为(0.05-0.3):1,压力为130-450千帕。根据本发明,催化裂化反应器是本领域技术人员所熟知的,优选为可以实现两类不同反应的反应器,例如,所述催化裂化反应器可以为等直径提升管、等线速提升管、变径提升管、流化床、或等直径提升管与流化床构成的复合反应器,优选为变径提升管。一种实施方式,所述变径提升管沿竖直方向由下至上依次设置有同轴且流体连通的预提升段、第一反应区、第二反应区和出口区,所述出口区末端设置有用于连接沉降器的水平管,所述第一反应区的内径小于第二反应区,所述第二反应区的内径大于出口区,所述变径提升管的总高度(包括预提升段、第一反应区、第二反应区和出口区)为10-60米,所述催化裂化催化剂送入所述预提升段中,所述催化裂化原料油送入所述第一反应区的下部,所述第一催化裂化反应在第一反应区中进行,所述第二催化裂化反应在第二反应区中进行。预提升段的直径与常规的等直径提升管反应器相同,一般为0.02米-5米,其高度占反应器总高度的5-10%。第一反应区的结构类似于常规的等直径提升管反应器,其直径可与预提升段相同,也可较预提升段稍大,第一反应区的直径与预提升段的直径之比为(1.0-2.0):1,其高度占反应器总高度的10-30%。原料油和催化剂在该区混合后,在较高的反应温度和剂油比、较短的停留时间(一般为0.5秒-3.0秒)下,主要发生裂化反应。第二反应区比第一反应区直径大,其直径与第一反应区的直径之比为(1.5-5.0):1,其高度占反应器总高度的30-60%,其作用是降低油气和催化剂的流速和反应温度。降低该区反应温度的方法,可以从该区与第一反应区的结合部位注入冷激介质,和/或通过在该区设置取热器,取走部分热量以降低该区反应温度,从而达到抑制二次裂化反应、增加异构化反应和氢转移反应的目的。冷激介质可以为选自冷激剂、冷却的再生催化剂和冷却的半再生催化剂中的至少一种。其中冷激剂可以为选自液化气、粗汽油、稳定汽油、轻循环油、重轻循环油和水中的至少一种;冷却的再生催化剂和冷却的半再生催化剂是待生催化剂分别经两段再生和一段再生后冷却得到的,再生催化剂碳含量一般为0.1重%以下,优选为0.05重%以下,半再生催化剂碳含量一般为0.1-0.9重%,优选为0.15-0.7重%。若设置取热器,则其高度占第二反应区高度的50-90%,油气在该反应区停留时间可以较长,为2-30秒。根据本发明,经过使用的待生催化剂可以送入再生器中进行烧焦再生,再生所得再生催化剂作为催化裂化催化剂循环回催化裂化反应器中。为了增加第二反应区中的氢转移反应和异构化反应,如图1-3所示,可以任选将沉降器中的经过冷却后的待生催化剂作为一种冷激介质输送至第二反应区,以多产异构烷烃和轻芳烃。根据本发明,催化裂化催化剂是本领域技术人员所熟知的,例如所述催化裂化催化剂可以包括裂化活性组分和载体;以干基计,所述裂化活性组分可以包括10-90重量%、优选20-40重量%的fau型沸石和10-90重量%、优选60-80重量%的五元环结构沸石;所述fau型沸石可以为选自y型沸石、hy型沸石和超稳y型沸石中的至少一种,所述五元环结构沸石可以为选自zsm-5系列沸石、高硅沸石和镁碱沸石中的至少一种,所述五元环结构沸石可以含或不含稀土以及含或不含磷。根据本发明,选择性加氢处理用于产生富含双环以上的多环环烷烃的加氢尾油(或称为加氢馏分油),所述选择性加氢处理的条件可以包括:氢分压为10.0-30.0兆帕,优选为15-20兆帕,反应温度为300-500℃,优选为330-450℃,液相体积空速为0.1-10.0小时-1,优选为0.5-5小时-1,氢油体积比为100-1500nm3/m3。所述加氢催化剂可以包括加氢活性组分和载体,所述加氢活性组分可以为第vib族非贵金属和/或第viii族非贵金属,所述载体可以为选自氧化铝、二氧化硅和无定型硅铝中的至少一种。根据本发明,抽提精制是本领域技术人员所熟知的,用于提取汽油中轻芳烃(btx),例如步骤(4)中所述抽提精制的条件可以包括:抽提溶剂为选自环丁砜、二甲亚砜、n-甲酰基吗啉、四甘醇、三甘醇和n-甲基吡啶烷酮中至少一种,温度为50-110℃,抽提溶剂与汽油的重量比为2-6。第一种具体实施方式,将催化裂化原料油送入变径提升管反应器的催化裂化装置,从反应器的第一反应区下部进入与催化剂接触,主要发生裂化反应,反应后生成的油气上行至反应器的第二反应区下部与降温后催化剂接触主要进行氢转移反应和异构化反应,反应后流出物进入沉降器;分离得到包括干气、液化气、汽油、轻循环油、重循环油和油浆的反应产物;轻循环油、重循环油油、油浆任选地和其他处理单元馏分油任选地进入到加氢装置在加氢催化剂作用下进行选择性加氢处理、得到加氢尾油返回催化裂化装置。待生催化剂经汽提、再生然后进行分离,大的颗粒催化剂进入第一反应区下部,小的颗粒催化剂经降温后进入第二反应区下部。下面结合附图对本发明所提供的第一种具体实施方式予以进一步的说明,但是并不因此而限制本发明。图1是用变径提升管反应器制取异丁烷和富含芳烃汽油的流程,设备和管线的形状、尺寸不受附图的限制,而是根据具体情况确定。预提升蒸汽经管线1从提升管预提升段2进入,热的再生催化剂经再生斜管16进入提升管预提升段由预提升蒸汽进行提升。来自管线50和管线4的其他处理单元馏分油作为催化裂化原料油与来自管线3的雾化蒸汽按一定比例从提升管预提升段进入,与热催化剂混合后进入第一反应区5内,在一定的条件下进行第一催化裂化反应。反应物流与来自管线6的冷激剂和/或冷却的催化剂(图中未标出)混合进入第二反应区7,进行第二催化裂化反应,反应后的物流进入出口区8,该反应区提高物流的线速,使反应物流快速进入气固分离系统中的沉降器9、旋风分离器10,反应产物经管线11去分离系统19,经分馏得到干气经管线20进行后续处理;液化气经管线21经后续装置处理得到异丁烷;汽油优选地经管线22进入精制抽提装置45得到苯、甲苯和二甲苯目的产物分别从管线46、管线47、管线48和管线49送出;轻循环油任选地经管线23、管线52送出催化裂化装置,重循环油任选地经管线24以及管线26进入到加氢装置31处理后回炼;油浆任选地经管线51外甩出装置。催化裂化反应后带炭的催化裂化待生催化剂进入汽提器12,经汽提后由待生立管14进入再生器15,待生催化剂在来自管线17的空气中烧焦再生,烟气经旋风分离器13分离后经管线18出再生器,热的再生催化剂经再生斜管16返回提升管底部循环使用。第二种具体实施方式,原料油经加氢装置进行加氢并处理得到加氢尾油作为催化裂化原料油送入新型变径提升管反应器的催化裂化装置,预热后的加氢尾油从反应器的第一反应区下部进入与催化剂接触,主要发生裂化反应,反应后生成的油气上行至反应器的第二反应区下部与降温后催化剂接触主要进行氢转移反应和异构化反应,反应后流出物进入沉降器;分离得到包括干气、液化气、汽油、轻循环油、重循环油和油浆的反应产物;轻循环油、重循环油、油浆任选地和其他处理单元馏分油进入到加氢装置在加氢催化剂作用下进行加氢处理、得到加氢尾油。待生催化剂经汽提、再生然后进行分离,大的颗粒催化剂进入第一反应区下部,小的颗粒催化剂经降温后进入第二反应区下部。下面结合附图2对本发明所提供的第二种具体实施方式予以进一步的说明,但是并不因此而限制本发明。图2是用变径提升管反应器制取异丁烷和富含芳烃汽油的流程,设备和管线的形状、尺寸不受附图的限制,而是根据具体情况确定。预提升蒸汽经管线1从提升管预提升段2进入,热的再生催化剂经再生斜管16进入提升管预提升段由预提升蒸汽进行提升。来自管线27的其他处理单元馏分油和来自管线28的氢气按一定比例进入到加氢装置31,经加氢处理并经高压分离器34和低压分离器35分离,液体产品从管线36经加氢装置分馏塔37分离得到气体、加氢汽油、加氢轻循环油和加氢尾油分别经管线38、管线39、管线40和管线41送出,氢气经管线33进入到氢气循环压缩机32进行加压后经管线30以及管线29和管线28循环至加氢装置31,加氢尾油作为催化裂化原料油经管线41、管线4与来自管线3的雾化蒸汽按一定比例从提升管预提升段进入,与热催化剂混合后进入第一反应区5内,在一定的条件下进行第一催化裂化反应。反应物流与来自管线6的冷激剂和/或冷却的催化剂(图中未标出)混合进入第二反应区7,进行第二催化裂化反应,反应后的物流进入出口区8,该反应区提高物流的线速,使反应物流快速进入气固分离系统中的沉降器9、旋风分离器10,反应产物经管线11去分离系统19,经分馏得到干气经管线20进行后续处理;液化气经管线21经后续装置处理得到异丁烷;汽油优选地经管线22进入精制抽提装置45得到苯、甲苯和二甲苯目的产物;轻循环油任选地经管线23、管线52送出催化裂化装置、重循环油任选地经管线24和管线26进入到加氢装置31处理后回炼;油浆任选地经管线51外甩出装置。催化裂化反应后带炭的催化裂化待生催化剂进入汽提器12,经汽提后由待生立管14进入再生器15,待生催化剂在来自管线17的空气中烧焦再生,烟气经管线18出再生器,热的再生催化剂经再生斜管16返回提升管底部循环使用。第三种具体实施方式原料油经芳烃抽提装置得到抽出油和抽余油,抽出油经加氢装置进行加氢并处理得到加氢尾油,所述的加氢尾油和所述的抽余油混合后作为催化裂化原料油送入新型变径提升管反应器的催化裂化装置,预热后的加氢尾油从反应器的第一反应区下部进入与催化剂接触,主要发生裂化反应,反应后生成的油气上行至反应器的第二反应区下部与降温后催化剂接触主要进行氢转移反应和异构化反应,反应后流出物进入沉降器;分离得到包括干气、液化气、汽油、轻循环油、重循环油和油浆的反应产物;轻循环油、重循环油、油浆任选地和其他处理单元馏分油进入到加氢装置在加氢催化剂作用下进行加氢处理,得到加氢尾油。待生催化剂经汽提、再生然后进行分离,大的颗粒催化剂进入第一反应区下部,小的颗粒催化剂经降温后进入第二反应区下部。下面结合附图3对本发明所提供的第三种具体实施方式予以进一步的说明,但是并不因此而限制本发明。图3是用变径提升管反应器制取异丁烷和富含芳烃汽油的流程,设备和管线的形状、尺寸不受附图的限制,而是根据具体情况确定。预提升蒸汽经管线1从提升管预提升段2进入,热的再生催化剂经再生斜管16进入提升管预提升段由预提升蒸汽进行提升。来自管线43的其他处理单元馏分油进入到芳烃抽提装置42,芳烃抽提装置温度控制在60℃;经抽提得到抽出油和抽余油,抽出油经管线27和来自管线28的氢气按一定比例进入到加氢装置31,经加氢处理并经高压分离器34和低压分离器35分离,液体产品经加氢装置分馏塔37分离得到气体、加氢汽油、加氢轻循环油和加氢尾油,氢气经管线33进入到氢气循环压缩机32进行加压后循环至加氢装置31,加氢尾油作为催化裂化原料油和来自管线44的抽余油经管线41、管线4与来自管线3的雾化蒸汽按一定比例从提升管预提升段进入,与热催化剂混合后进入第一反应区5内,在一定的条件下进行第一催化裂化反应。反应物流与来自管线6的冷激剂和/或冷却的催化剂(图中未标出)混合进入第二反应区7,进行第二催化裂化反应,反应后的物流进入出口区8,该反应区提高物流的线速,使反应物流快速进入气固分离系统中的沉降器9、旋风分离器10,反应产物经管线11去分离系统19,经分馏得到干气经管线20进行后续处理;液化气经管线21经后续装置处理得到异丁烷;汽油优选地经管线22进入精制抽提装置45得到苯、甲苯和二甲苯目的产物;轻循环油任选地经管线23、管线52送出催化裂化装置、重循环油任选地经管线24、管线26进入到加氢装置31处理后回炼;油浆任选地经管线51外甩出装置。催化裂化反应后带炭的催化裂化待生催化剂进入汽提器12,经汽提后由待生立管14进入再生器15,待生催化剂在来自管线17的空气中烧焦再生,烟气经管线18出再生器,热的再生催化剂经再生斜管16返回提升管底部循环使用。下面的实施例将对本发明予以进一步说明,但并不因此而限制本发明。实施例、对比例中所使用的原料油列于表1。本发明实施例中所用的催化剂沸石是高硅y沸石和zrp沸石,活性组元重量比例:前者30%,后者70%,具体制备方法为:用4300克脱阳离子水将969克多水高岭土(中国高岭土公司产品,固含量73%)打浆,再加入781克拟薄水铝石(山东淄博铝石厂产品,固含量64%)和144ml盐酸(浓度30%,比重1.56)搅拌均匀,在60℃静置老化1小时,保持ph为2-4,降至常温,再加入预先准备好的含800克高硅y沸石(干基)和2000克含化学水的zrp沸石浆液,搅拌均匀,喷雾干燥,洗去游离na+,得催化剂。将得到催化剂经800℃和100%水蒸汽进行老化,老化后的催化剂代号为iba-1。实施例和对比例中催化剂选用催化剂分公司齐鲁催化剂厂所生产的cgp-1、mlc-500催化剂和dmmc-1催化剂。实施例和对比例所用加氢催化剂的商业牌号为rn-23v,保护剂商业牌号是rg-1,加氢催化剂和保护剂的装填体积比为95:5。实施例1采用本发明提供的方法,原料油a在中型变径提升管催化裂化装置上,与催化剂iba-1接触并进行催化裂化反应。预热的原料油a进入如图1所示的变径提升管反应器内,在水蒸汽存在下,与热的催化裂化催化剂在第一反应区和第二反应区接触进行第一催化裂化反应和第二催化裂化反应,分离反应产物得到干气、富含异丁烷的液化气、富含芳烃的汽油、轻循环油和重循环油(无油浆);轻循环油外甩出装置,重循环油循环至加氢装置进行选择性加氢处理所得加氢尾油送入中型变径提升管催化裂化装置进行催化裂化反应;待生催化剂经汽提进入再生器,经烧焦后循环使用。操作条件列于表2,产品分布列于表3,任选地汽油经抽提精制得到的产品性质见表3,抽提精制的条件为:抽提溶剂为环丁砜,温度为65℃,抽提溶剂与汽油的重量比为4。对比例1-a与实施例1相比,采用多环环烷烃含量低的原料油d。预热的催化裂化原料油d进入如图1所示的变径提升管反应器内,在水蒸汽存在下,与热的催化裂化催化剂cgp-1接触反应,分离反应产物得到干气、液化气、汽油、轻循环油、重循环油和油浆;轻循环油和油浆均外甩出装置,重循环油循环至加氢装置进行加氢处理后所得加氢尾油循环回催化裂化装置,待生催化剂经汽提进入再生器,经烧焦后循环使用。操作条件列于表2,产品分布列于表3。对比例1-b与实施例1相比,采用常规催化裂化催化剂mlc-500。预热的催化裂化原料油a进入常规的等径提升管反应器内,在水蒸汽存在下,与热的催化裂化催化剂接触反应,分离反应产物得到干气、液化气、汽油、轻循环油、重循环油和油浆;轻循环油和油浆均外甩出装置,重循环油循环至加氢装置进行加氢处理后所得加氢尾油循环回催化裂化装置,待生催化剂经汽提进入再生器,经烧焦后循环使用。操作条件列于表2,产品分布列于表3。对比例1-c与实施例1相比,采用催化裂解催化剂dmmc-1。预热的催化裂化原料油a进入提升管+流化床反应器内,在水蒸汽存在下,与热的催化裂化催化剂接触反应,分离反应产物得到干气、液化气、汽油、轻循环油、轻循环油和重循环油(无油浆);轻循环油外甩出装置,重循环油循环至加氢装置进行加氢处理后所得加氢尾油循环回催化裂化装置;待生催化剂经汽提进入再生器,经烧焦后循环使用。操作条件列于表2,产品分布列于表3。对比例1-d与实施例1相比,预热的催化裂化原料油a进入常规的等径提升管反应器内,在水蒸汽存在下,与热的催化裂化催化剂接触反应,分离反应产物得到干气、液化气、汽油、轻循环油、重循环油和油浆;轻循环油和油浆均外甩出装置,重循环油进行加氢处理后所得加氢尾油循环回催化裂化装置,待生催化剂经汽提进入再生器,经烧焦后循环使用。操作条件列于表2,产品分布列于表3。实施例2采用本发明提供的方法,先对原料油b进行加氢饱和得到原料油c,性质如表1所示。预热的催化裂化原料油c进入如图2所示的变径提升管反应器内,在水蒸汽存在下,与热的催化剂iba-1接触反应,分离反应产物得到干气、富含异丁烷的液化气、富含芳烃的汽油、轻循环油和重循环油(无油浆);轻循环油外甩出装置,重循环油循环至加氢装置进行加氢处理后所得加氢尾油循环回催化裂化装置,待生催化剂经汽提进入再生器,经烧焦后循环使用。操作条件列于表4,产品分布列于表4,任选地汽油经抽提精制得到的产品性质见表4。对比例2采用本发明提供的方法,原料油b未加氢,直接将预热的催化裂化原料油b进入如图1所示的变径提升管反应器内,在水蒸汽存在下,与热的催化剂iba-1接触反应,分离反应产物得到干气、液化气、汽油、轻循环油、重循环油和油浆;轻循环油和油浆外甩出装置,重循环油循环至加氢装置进行加氢处理后所得加氢尾油循环回催化裂化装置;待生催化剂经汽提进入再生器,经烧焦后循环使用。操作条件列于表4,产品分布列于表4。实施例3采用本发明提供的方法,原料油减压馏分油e经芳烃抽提装置处理后得到减压馏分油抽出油g和减压馏分油抽余油f,芳烃抽提装置条件:温度为60℃,溶剂与原料重量比为1.5,溶剂为糠醛。减压馏分油抽出油g和氢气混合后进入到加氢装置进行加氢处理得到加氢尾油,将预热的加氢尾油和减压馏分油抽余油f混合后作为催化裂化原料油进入如图3所示的变径提升管反应器内,在水蒸汽存在下,与热的催化剂iba-1接触反应,分离反应产物得到干气、富含异丁烷的液化气、富含芳烃的汽油、轻循环油和重循环油(无油浆);轻循环油外甩出装置,重循环油和减压馏分油抽出油g混合经加氢装置进行加氢处理后返回至催化裂化反应器;待生催化剂经汽提进入再生器,经烧焦后循环使用。原料性质列于表5,操作参数列于表6,产品分布列于表7,任选地汽油经抽提精制得到的产品性质见表7。对比例3采用本发明提供的方法,与实施例3相比,原料油e未经抽提和加氢处理,直接作为催化裂化原料油进入如图1所示的变径提升管反应器内,在水蒸汽存在下,与热的催化剂iba-1接触反应,分离反应产物得到干气、液化气、汽油、轻循环油、重循环油和油浆;和实施例相比,其中轻循环油、油浆外甩出装置,重循环油循环至加氢装置进行加氢处理后返回至催化裂化反应器;待生催化剂经汽提进入再生器,经烧焦后循环使用。原料性质列于表5,操作参数列于表6,产品分布列于表7;任选地汽油经抽提精制得到的产品性质见表7。实施例4采用本发明提供的方法,原料油减压渣油h经芳烃抽提装置处理后得到减压渣油抽出油j和减压渣油抽余油i,芳烃抽提装置条件:温度为60℃,溶剂与原料重量比为1.5,溶剂为糠醛。减压渣油抽出油j和氢气混合后进入到加氢装置进行加氢处理得到加氢尾油,将预热的加氢尾油和减压渣油抽余油i混合后作为催化裂化原料油进入如图3所示的变径提升管反应器内,在水蒸汽存在下,与热的催化剂iba-1接触反应,分离反应产物得到干气、液化气、汽油、轻循环油和重循环油(无油浆),轻循环油外甩出装置,重循环油和抽出油混合经加氢装置进行加氢处理后返回至催化裂化反应器;待生催化剂经汽提进入再生器,经烧焦后循环使用。原料性质列于表5,操作参数列于表6,产品分布列于表7,任选地汽油经抽提精制得到的产品性质见表7。对比例4采用本发明提供的方法,与实施例4相比,原料油h未经抽提和加氢处理,直接作为催化裂化原料油进入如图1所示的变径提升管反应器内,在水蒸汽存在下,与热的催化剂iba-1接触反应,分离反应产物得到干气、液化气、汽油、轻循环油、重循环油和油浆;其中轻循环油、油浆外甩出装置,重循环油循环至加氢装置进行加氢处理后返回至催化裂化反应器;待生催化剂经汽提进入再生器,经烧焦后循环使用。原料性质列于表5,操作参数列于表6,产品分布列于表7;任选地汽油经抽提精制得到的产品性质见表7。从实施例和对比例的比较可以看出,本发明的方法能够多产轻质芳烃和异丁烷。表1原料油编号abcd密度(20℃),千克/米3895.3943.2854.6890.5碳氢含量,重量%氮0.130.64<0.010.29硫0.371.11<0.010.13碳86.4988.7786.7286.40氢13.019.4813.2713.18族组成,重量%链烷烃20.3210.6018.6039.46环烷烃56.234.1066.3025.87一环8.002.219.3112.51二环35.681.1940.895.70三环13.650.7016.103.73四环0.000.000.003.93芳烃23.4585.3015.1024.20单环—2.5014.10—双环—74.001.00—三环—8.800.00—胶质0.000.000.0010.27沥青质0.000.000.000.20表2表3表4表5表6表7项目实施例3对比例3实施例4对比例4原料类型eehh催化剂类型iba-1iba-1iba-1iba-1反应器类型变径提升管变径提升管变径提升管变径提升管产品分布,重量%干气2.491.522.793.14液化气36.8120.7133.8316.51丙烯12.527.1011.315.82异丁烯1.313.191.122.52异丁烷13.754.1512.442.44汽油49.0442.7745.7036.16苯1.910.871.860.81甲苯8.875.318.565.83二甲苯12.847.3512.777.95btx23.6213.5323.1914.59轻循环油6.7024.878.1823.86油浆0.006.330.007.90焦炭4.963.809.5012.43合计100.00100.00100.00100.00当前第1页12