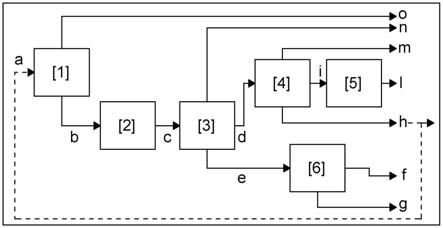
用于由生物质生产生物油和生物气的方法
1.描述
2.本发明涉及用于由生物质生产液体燃料(优选生物油)和气体燃料(优选生物气)的方法,其目的是获得其向高级生物燃料(advanced biofuel)的高转化与高能效的组合。
3.在本专利申请中,通过能效,申请人意旨在描述和要求保护方法产品(例如产生的液体和气体燃料,并且特别是生物油和生物气)的热量值的总和与在方法中作为原料引入的生物质的热量值之间的比率。
4.在本专利申请中,转化被理解为是指所产生的生物油的重量和所产生的生物气的重量之和与原料干重的重量比。
5.欧洲共同体强加了在制备燃料或发电过程中引入生物来源成分的义务。当前的生物燃料监管框架源自法规《燃料质量指令》(fqd 2009/30/ec)和《可再生能源指令》(red2009/28/ec)。在主要干预措施中,red 2009/28/ec强加了到2020年将“生物来源成分”以高至10%的热量值引入常规化石燃料中的义务。监管框架仍在不断发展:特别是迄今为止,正在讨论的提议是引入最高限制为7%的来自第一代来源(即与食品竞争的来源,(例如棕榈油、菜籽、大豆等))的生物燃料,并且引入最少量的高级生物燃料。
6.在本文中,“高级生物燃料”应理解为是指源自不与食品生产竞争的来源的液体和气体燃料,例如源自对城市固体废物进行的分类收集的有机材料,因为其具有满足在工业规模上应用的临界质量,并使其具有成本效益。在本文中,术语“生物质”是指以下元素或其混合物:
7.‑
有机来源的城市固体废物,其可以选自例如对废物进行分类收集得到的有机材料,从混合的城市固体废物中分选的有机材料,收集得到的城市固体废物的有机部分(也称为ofmsw),学校和公司食堂废物或其混合物;或所述有机材料与修剪插条和/或农业残留物的混合物;
8.‑
废水处理厂产生的生物性质的初级和次级污泥;
9.‑
来自农业和/或畜牧业的残留物和/或废物;
10.‑
来自农业和食品工业、包装工业和大型食品零售商的残留物和/或废物;
11.‑
来自农业加工、造林和/或林业的残留物和/或废物;
12.‑
微藻和/或大型藻类;
13.‑
细菌生物质、蓝细菌或其它微生物,例如酵母和霉菌。
14.在本专利申请中,即使没有明确指出,本文中陈述的所有操作条件也应被认为是优选条件。
15.为了本发明的目的,术语“包含”或“包括”也涵盖术语“由...组成”或“基本上由...组成”。
16.为了本发明的目的,除非另有说明,否则对区间的定义总是包含端值。
17.术语“包含”及其派生词无意排除存在任何其它组件/成分、步骤或过程,无论它们是否在本文中公开。为避免任何疑问,除非另有说明,否则本文中通过使用术语“包含”要求保护的所有方法都可以包括任何其它步骤。
18.用于处理城市固体废物的有机部分或者当前更一般使用的术语同化废物或生物质的技术可以被分为四种类型,其对这里列出的待获得的产品起作用:
19.‑
堆肥厂,旨在生产用于农业和园艺部门的高质量有机土壤改良剂;
20.‑
好氧稳定或生物稳定系统,旨在对有机部分进行预处理,以最大程度地减少垃圾填埋场中与易腐烂物质的存在有关的负面影响,或者旨在生产用于环境恢复的合适土壤改良剂(sof);
21.‑
厌氧消化厂,旨在通过将有机部分作为生物气和生物甲烷回收进行能量回收;
22.‑
热处理,旨在回收物质和能量。
23.热处理与上述提到的用于可能获得的产品和用于所需投资的技术不同,因为这通常更重要。
24.在热处理中,可以列出以下:
25.‑
焚化,其中原料转化为热和电;
26.‑
气化,其中原料通过费
‑
托合成(ft)转化成合成气,并且因此潜在地转化成其所有衍生物,包括柴油;
27.‑
热解,其中原料转化为生物油(液体燃料);
28.‑
液化,其中原料转化为生物油(液体燃料)。
29.在堆肥和好氧稳定中,生物质的部分有机成分损失并转化为co2和h2o,这会对co2向环境的排放产生负面影响。在厌氧消化中,有机成分利用数周的时间转化为生物气,即co2和甲烷。只有通过诸如气化与费
‑
托合成、热解或液化组合的热处理,有机成分才能转化为“高级生物燃料”的生物液体前体。
30.在上述热处理中,液化可在较低的温度下进行,因此与竞争的热技术相比具有经济优势。特别地,如果在亚临界条件下,即在范围(240
‑
310)℃的温度下进行,则控制该方法所需的能量是生物质中存在的能量,并且不需要引入外部能源。液化导致大量废水的形成,其中包含大部分存在于原始生物质中的有机物质和大部分养分(氮和磷)。此外,这些水还包含大量导致厌氧消化被强烈抑制的化合物。因此,该第一水相不能返回到环境中,并且必须进行进一步处理,通常是通过送至废水处理中心,并且具有与表征它们的高含量的化学耗氧量(cod)有关的高处理费。
31.cod是在水处理中使用的常用参数,并且代表将水相中存在的有机物充分燃烧(co2、h2o、so2、no2)所需的o2(氧气)量。cod通常以每升水相的o2克数表示,并通过六价铬(cr
6+
)滴定来确定。
32.关于以液化水的厌氧消化进行处理的文献很新。没有任何研究与城市固体废物的有机部分(ofmsw)的亚临界液化水处理直接相关,而在来自生物质(例如微藻和木质纤维素底物)的液化的水处理方面有大量实验。
33.对于当前这种类型,约50
‑
150g
cod
/l的水的cod值被认为是典型的。
34.综述“m.deniel等人renewable and sustainable energy reviews 54(2016)1632
‑
1652”描述了通过液化回收食物残留物的方法。对亚临界条件下的液化进行了充分的研究,并且对于大多数底物的最佳温度定义为约300℃。
35.第一座工业规模的液化设备是基于“changing world technology cwt”技术,该技术是在美国专利5,269,947的基础上开发的,其处理能力为200
‑
250吨/天的来自火鸡加
工业的废物,将其转化为柴油、化肥产品和煤炭。该设备已经关闭了许多次,并且从未达到过满负荷运转能力。2009年,拥有该设备的公司申请破产。2011年,从加拿大公司ridgeline energy services购得的设备重新启动,但运营了几年(http://www.carthagepress.com/article/20130416/news/13041 9181,17/05/2018)并且因亏损而被关闭。当前处于开发或示范阶段的液化方法在本领域中也是已知的。
36.以最高开发水平为特征的液化方法是nextfuel的“hydro
‑
thermal upgrading”(htu)和scf technology a/s的“catliq”,并且在us 7,262,331中进行了描述。htu在(300
‑
350℃)、(120
‑
180)巴下进行,接触时间为5
‑
20分钟。ep 1879981a2中描述的catliq方法在(350
‑
420℃)和(230
‑
250)巴下进行。ignite energy research的文献ep 2178625b1、us2013/0276361a1和wo 2009/015409中描述的cat
‑
htr方法在(360
‑
420)℃和(220
‑
300)巴下进行,接触时间为20
‑
30分钟,并且处于开发示范阶段。另一种处于良好开发程度的方法是伊利诺伊大学(university of illinois)开发的tcc方法,其在(295
‑
305)℃、180巴下进行并且接触时间为(15
‑
30)分钟(2001thermochemical conversion process of swine manure:operating temperature and retention time effects第43卷(6):1821
‑
1825american society of agricultural engineers)。
37.可以推断,液化技术已经在不同底物上以中试规模得到了有效证明,但是由于关键的技术因素以及经济和环境可持续性问题,这些方法中的许多已经停止,强调需要创新且可靠的可替代方案来管理有机废物(尤其是ofmsw和共同产生流)的转化。
[0038]“catliq”技术已经达到在土耳其的巴里克西尔建造了一个名为“pre
‑
commercial demonstration plant”的15t/h的设备的阶段。这一阶段是60kg/h的中试设备投产后开始的。最近在一次会议上的演讲(https://bioenergy.conferenceseries.com/abstract/2017/catliq
‑
catalytic
‑
hydrothermal
‑
liquefaction
‑
process
‑
from
‑
pilot
‑
scale
‑
to
‑
demo
‑
scale
‑
第七届国际生物燃料与生物能源大会,2017年10月2日
‑
4日,加拿大多伦多)中,解释了连续的中试管理受到工艺流体产生水垢、堵塞和颗粒流这一事实的限制。
[0039]
如wo 2006/117002中所述,通过膜系统进行液化水处理而不产生生物气。“cat
‑
htr”技术自2008年以来一直在开发中,并已准备好建造第一个商业化设备(2019),其利用塑料进料并且处理能力为1420kt/y(http://www.licella.com.au/facilities/)。
[0040]
在该方法中,不对产生的水进行处理以回收生物气。
[0041]
文献报道了通过厌氧消化处理水热液化产生的水以形成生物气的研究(chen等人.water research 106(2016)98
‑
107)。该文章表明,在厌氧中温消化条件(37℃)下和5天中,通过对稻草进行液化产生的水是48%可生物降解的。介入利用轻质石油进行提取的初步阶段,可以将残留cod的生物降解性进一步提高25%,这提示了抵抗对现有产品的消化的行为,因此在这种特定情况下,提出了使用溶剂提取系统。但是,溶剂系统的管理成本很高。
[0042]
对螺旋藻型藻类进行的液化产生具有85gcod/l的水相(zheng等人.energy conversion and management(2016),zheng,mingxia等人.anaerobic digestion of wastewater generatedfrom the hydrothermal liquefaction of spirulina:toxicity assessment and minimization.doi:j.enconman.2016.10.034),并且与其它有关藻类的研究(giovanna tommaso等人.bioresource technology 178(2015)139
‑
146)类似,在最有效的转化条件下,实现了初始cod的43%转化率。通过转化来自藻类(微拟球藻
(nannochloropsis))的以97gcod/l开始的液化水也获得了如先前所述相同水平的结果,并且通过用活性炭对产生的液化水进行预处理达到了溶液中cod的62%的最大转化率。(saravanan r.shanmugam et al.bioresource technology 223(2017)115
‑
120)。同样,需要进行预处理以去除抑制厌氧降解的顽固性物质。总之,已经重新进行了一些研究以获得利用相同测量单位的实验参数,并且该比较显示无法原样处理水相,缺少有关生物质(例如ofmsw)转化的数据,并且对于其它底物的研究,水中cod向生物气的最大转化率从未超过70%。
[0043]
现有文献概述了来自ofmsw液化的水实际上如何能够引起与存在的一些化学化合物有关的毒性问题,例如甲基羟基吡啶,其潜在地是可生物降解的,但特征在于对产甲烷微生物(能够激活生物气的形成的微生物)具有高毒性。
[0044]
就专利文献而言,有一些专利描述了其中除了进一步的一元操作外还进行生物质的液化和水相的厌氧消化二者的方法。特别地,在美国专利9,797,597中,提出了能量综合处理方案,其包括生物质(也为ofmsw)的液化和所产生的水相的厌氧消化。然而,在该专利中,液化是在消化物上进行(首先厌氧消化然后液化)并且在t=400℃和p=200巴的超临界条件下进行。如果在超临界条件下进行液化,则生物质中可用的能量不足,并且因此需要使用外部能源。产生的水相被送至所开发方案之外的二级和三级处理。没有关于如何处理该水相的技术指示。
[0045]
美国专利9,758,728描述了水热液化和催化水热气化(htl
‑
chg)的组合方案。液化的水中的有机物占原始生物质中存在的总碳的至少40%。这种有机材料的回收和水的再利用是保持高整体转化效率的关键因素。为了处理这些水,在与水热液化(htl)相同的操作条件下引入催化水热气化:在包含选自ru、rh、os、ni、cu及其混合物的金属的催化剂存在下,t=(300
‑
360)℃并且200巴压力。所提出的方案的缺点在于,除了接近超临界条件的水热液化条件之外,水处理也在特别苛刻的条件下进行,因此在投资、建筑材料和能耗方面非常昂贵。
[0046]
专利us 9,404,063描述了用于使生物油与通过水热液化(htl)产生的水相分离的方法,其通过使无机化合物和/或矿物固体沉淀的第一分离阶段然后冷却和使生物油与水相分离的阶段实现。
[0047]
专利us 9,695,093描述了用于处理农业或城市污水的方法,其包括在消化池中处理污水以产生包含生物气和污泥的产品的阶段。使生物气与污泥分离,然后通过水热液化工艺将其转化为液化产物和碳固体。
[0048]
已经对该反应研究了多年,但该方法尚未发现工业应用,这主要是因为与在高压(大于或等于200巴)下进行管理的设备放大相关的昂贵成本。此外,已发现该方法的能效远未达到能够达到的理论极限,因此,待引入到该方法中的能量通常高于在产品中获得的能量。在这种特定情况下,建议将由水热液化阶段获得的水加热到至少160℃,然后将其再循环。所提出的方案尽管避免了水热转化中的高能量消耗,但是具有用于蒸发整个水相的高能量强度,所述水相被干燥以获得固体碳化合物。
[0049]
有机生物质在超临界条件(其通常提供370℃至400℃的温度和220巴至250巴的压力)下的液化涉及投资成本和能量成本(由于需要从外部来源提供能量),这是非常重要的并且因此会减慢并推迟其工业性能。亚临界条件下的生物质液化会共同产生被视为“高级
生物燃料”的生物油和在标准厌氧消化条件下具有低生物降解性的水相,导致低生物气产量。这导致需要将仍负载cod的液化水送至到大型水处理厂,从而增加了处置成本。
[0050]
在亚临界条件下获得的液化水的厌氧消化中可以发现的问题有多种。
[0051]
首先,观察到抑制厌氧消化的化合物的存在或形成:
[0052]
通过减慢该方法或抑制微生物生长而起作用的物质,所述微生物负责降解存在的物质或由其衍生的中间体,例如氮和盐度。
[0053]
此外,还观察到存在难以以厌氧方式生物降解的化合物或源自消化本身的特定有毒化合物和代谢产物:分子结构与天然物质的分子结构不相似的化合物,其很困难地、缓慢地(通过非专用的共同代谢)分解或完全不分解。
[0054]
更详细地,在来自对有机生物质进行液化的水相中,存在一些特定的化学化合物(例如,甲基吡啶),其可能是可生物可降解的,但是特征在于对产甲烷菌具有极高的毒性。另外,水相的特征在于通常较高的氮碳(n/c)比,并且在厌氧消化后相对较高的ph,并且因此,氨和由此产生的抑制的作用是重要。
[0055]
为了克服涉及有限的cod去除能力和因此水中存在的cod本身向生物气的低转化率的已确定问题,申请人已经开发了通过多阶段反应定义的控制这种水的厌氧消化的不同模式。以此方式,可以将生物质在亚临界条件(240℃
‑
310℃)下的液化与液体燃料、优选生物油的生产整合在一起,并且以高生物气效率回收存在于水相中的cod。鉴于生物质的来源,生物油和生物气都可以归类为“高级生物燃料”。
[0056]
申请人发现了用于由生物质、优选有机废物和废料、更优选分类收集得到的城市固体废物的有机部分(ofmsw)、甚至更优选湿部分及其混合物生产液体燃料(优选生物油)和气体燃料(优选生物气)的方法,其目的是最大程度地利用生物质,并且目的是以高能效获得所述装料向“高级生物燃料”的高转化率。
[0057]
所述方法包括以下步骤:
[0058]
a.将生物质、优选有机来源的垃圾和废物、更优选分类收集得到的城市固体废物的有机部分(ofmsw)、甚至更优选湿部分及其混合物送至预处理区段以形成能够被移动和/或泵送的均相,其中进行以下操作:
[0059]
‑
使惰性部分(例如石头、玻璃、铁和其它惰性固体)与生物质分离,
[0060]
‑
将生物质切碎和/或研磨以减小其尺寸并且从而使得其能够被移动和/或泵送,形成均相;
[0061]
b.随后对通过预处理(a)获得的所述均相在240℃至310℃的温度下进行亚临界水热液化以形成液化相;
[0062]
c.随后对来自液化过程(b)的所述液化相进行:
[0063]
i.通过不同密度或动力学的物理分离,优选通过倾析或离心,获得:第一水相;气相,其在处理后被送入大气;油相,其随后被分离成生物油和固体残留物,所述固体残留物可被分类为二次固体燃料(ssf);或
[0064]
ii.通过不同尺寸的分离,优选过滤,以从包含气体部分、水性部分和油性部分的混合相除去固体残留物;
[0065]
d.分离之后,该方法以如下两种可替代且互斥的模式继续进行:
[0066]
a.1在第一种模式中
[0067]
‑
对(i)中获得的第一水相进行多阶段厌氧反应,由此产生生物气、厌氧污泥和第二水相;
[0068]
‑
在所述厌氧反应之后,然后对所述第二水相进行好氧反应以获得用于灌溉或供入地表水体(河流、湖泊)的水;并且
[0069]
‑
然后将来自通过不同密度的分离的油相分离成生物油和固体残留物。
[0070]
b.1在第二种模式中
[0071]
‑
然后将所述混合相进行通过不同密度或动力学的分离,获得第一水相、生物油和气相,所述气相在处理后送入大气;
[0072]
然后,
[0073]
‑
对所述第一水相进行多阶段厌氧反应,由此产生生物气、泥流和第二水相;
[0074]
‑
随后对所述第二水相进行好氧反应以获得用于灌溉或供入地表水体的水。
[0075]
由于液化水中存在的有机物质转化为生物气,所描述和要求保护的方法具有提高生物质向高级生物燃料转化的技术优势。当液化水中存在的有机物质以50至200g/升的cod被测量时,向生物气的转化是吸引人的。
[0076]
通过下面的描述和附图,将更清楚本发明的其它目的和优点,这些描述和附图仅通过示出了本发明的优选实施方案的非限制性实例给出。
[0077]
图1示出了根据第一方法的作为本专利申请的主题的方法的优选实施方案。图1显示了构成该方法的以下单元:
[0078]
‑
[1]是生物质预处理单元(a),其形成均相(b)和废物(o);
[0079]
‑
[2]是液化单元,其形成液化生物质(c);
[0080]
‑
[3]是分离单元,例如离心或倾析,其将液化物质分离成气相(n)(主要是co2)、第一水相(d)和油相(e);
[0081]
‑
[4]是多阶段厌氧反应器,其产生生物气(m)、第二水相(i)和厌氧污泥(h);
[0082]
‑
[5]是好氧反应器,其将第二水相(l)纯化至与供入地表水体相适应的质量;
[0083]
‑
[6]是过滤单元,其使生物油(f)与固体残留物(g)分离。
[0084]
图2还示出了根据第二种模式的形成本专利申请的目的的方法的优选实施方案。图2显示了与图1相同的单元操作,但是单元操作[3]和[6]相反。
[0085]
图3显示了通过esi
‑
fticr ms技术以高分辨率分析的水,如对比例1中解释的。
[0086]
图4显示了随时间的cod转化。报告了cod的转化、进料到厌氧反应器的水的cod、来自位于反应器下游的沉积槽的流出cod和来自反应器的流出cod。图4中的图(黑色虚线)显示了归因于液化水相对于总体的贡献的cod进料的%。总cod是来自液化水和蔗糖的cod的总和。沉降器是在实施例中使用的设备中存在的辅助体积,以有助于使来自反应器的水澄清并且使作为重相的污泥变稠并且将其再循环到反应器中。
[0087]
图5显示了随时间的生物气产生。图显示了以升/克表示的生物气和被转化的cod之间的比率的趋势;以升/天表示的所产生的气体得流速的趋势;以每天每立方米反应器的cod的kg数表示的反应器的容积负荷的趋势;ph趋势。
[0088]
图6显示了随时间的污泥浓度和组成。图显示了以克/升水相表示的污泥浓度的趋势;以小时表示的反应器的水力停留时间的趋势;以重量百分比表示的污泥的挥发性固体与总固体之间的比率的趋势。
[0089]
图7显示了实施例2中测试25的执行模式。
[0090]
图8显示了40℃下随时间的cod转化。图显示了进料到反应器的cod、cod的总转化率、已转化为生物气的cod的量的趋势。在这些条件下,cod已主要转化为挥发性脂肪酸(vfa),显示出在水相处理过程中观察到与在常规反应器中一样的产甲烷菌群落中毒的现象。
[0091]
图9显示了厌氧反应的第一阶段中60℃下随时间的cod转化。图显示了进料到反应器的cod、cod的总转化率、已转化为生物气的cod的量、已转化为vfa的cod的量的趋势。
[0092]
图10显示了厌氧反应第二阶段中40℃下随时间的cod转化。图显示了进料到反应器的cod、cod的总转化率、已转化为生物气的cod的量、已转化为vfa的cod的量的趋势。
[0093]
图11示出了实施例3的测试的执行模式,其中(d)是液化水,[201]是在60℃的产酸反应器,[202]是vfa,[204]是在40℃的产甲烷反应器,[203]是反应器流出物的再循环,(m)是生物气,并且(i)是经处理的废水。
[0094]
图12显示了第二反应阶段中40℃下随时间的cod转化。图显示了进料到反应器的cod、cod的总转化率、已转化为生物气的cod的量、已转化为vfa的cod的量的趋势。
[0095]
图13显示了用于液化水处理(d)和获得生物气(m)所需的基本功能元件。该系统由串联设置的厌氧消化反应器(4a、4b、4c、4d)组成,所述反应器依次分隔并保持在降低的温度(70℃、60℃、50℃、40℃)下。在厌氧消化反应器的末端,设置有分离系统(7),其分离固体消化物(h)、生物气(m)和液体(i),液体(i)在好氧消化罐(5)中处理并且在系统开始时被部分再循环(o)以稀释进入第一个厌氧反应器的水流(d)。
[0096]
图14描述了根据本发明的优选实施方案的厌氧消化阶段和好氧消化阶段。将第一水相(d)泵入多阶段反应器,该多阶段反应器由一系列串联的包含悬浮细菌生物质的厌氧阶段[4a、4b、4c、4d、4e、4f]组成。从厌氧反应器中出来的流(m)由生物气组成,流(i)是供给好氧消化反应器[5]的所述定义的第二水相。经纯化的水流(f)从好氧消化反应器中流出。来自好氧消化反应器的至少部分的经纯化的水可以被再循环(o),并且与第一水相混合以形成进入厌氧反应器的流(q)。或者,可以在厌氧反应器的产甲烷阶段开始时将至少部分的经纯化的水再循环(p)。
[0097]
具体描述
[0098]
现在详细描述作为本专利申请的目的的方法。
[0099]
所述方法由生物质、优选有机废物和废料、更优选分类收集得到的城市固体废物的有机部分(ofmsw)、甚至更优选湿部分及其混合物生产液体燃料(优选生物油)和气体燃料(优选生物气)。
[0100]
用于本专利申请的目的的商业设施的实例是食品加工和包装中心、食堂、饭店、酒吧、水果和蔬菜市场(市场废物)、公园和花园、割草和修剪(绿色部分)。
[0101]
所描述和要求保护的方法可以以间歇、半连续或连续模式运行。
[0102]
生物质被送至预处理区段以形成能够被移动和/或泵送的均相,在其中进行以下操作。
[0103]
使惰性部分(例如石头、玻璃、铁和其它惰性固体材料)与生物质分离;然后根据初始尺寸将生物质切碎和/或研磨以减小其尺寸并且从而使得其能够被移动和/或泵送,以形成所述均相。
[0104]
然后对通过预处理获得的均相在240℃至310℃的温度下进行亚临界水热液化以形成液化相。
[0105]
随后对来自液化过程(b)的所述液化相进行通过不同密度或动力学的物理分离(i),优选离心或倾析,或通过不同尺寸的分离(ii),优选过滤。
[0106]
通过不同的密度或动力学的物理分离产生了第一水相;气相,其在处理后被送入大气;油相,其随后被分离成生物油和固体残留物,所述固体残留物可被分类为二次固体燃料(ssf)。
[0107]
通过不同尺寸的分离,从包含气体部分、水性部分和油性部分的混合相除去固体残留物。
[0108]
分离之后,该方法以两种可替代且互斥的模式继续进行。
[0109]
在第一种模式中,对通过不同密度或动力学的物理分离(i)获得的第一水相进行多阶段厌氧反应,由此产生生物气、厌氧污泥和第二水相。
[0110]
在所述厌氧反应之后,随后对所述第二水相进行好氧反应以获得用于灌溉或供入地表水体的水。
[0111]
然后将来自通过不同密度的分离的油相分离成生物油和固体残留物。
[0112]
在第二种模式中,然后对通过不同尺寸的分离(ii)获得的所述混合相进行通过不同密度或动力学的分离,获得第一水相、生物油和气相,所述气相在处理后送入大气。然后,对所述第一水相进行多阶段厌氧反应,由此产生生物气、泥流和第二水相。然后对所述第二水相进行好氧反应以获得用于灌溉或供入地表水体的水。
[0113]
多阶段厌氧消化可以通过使来自液化过程的第一水相通过串联的多个反应器或者通过在其内部包括具有空间隔离的悬浮细菌生物质的多个阶段的单个反应器来进行。厌氧消化处理可以在本领域已知的反应器中进行,只要其保持上述空间隔离的悬浮细菌生物质(活性污泥)即可。这些反应器也可以是uasb型(上流式厌氧污泥床反应器)、固定床反应器,利用膨胀床流化、通过机械作用搅拌或具有附着或负载的生物质的膜。
[0114]
厌氧反应器的阶段数可以大于或等于2,优选为3至6。
[0115]
水热液化必须在240℃至310℃的温度和保持水相冷凝的压力(优选40巴至110巴)的亚临界条件下进行。更优选地,液化温度在280℃至300℃之间变化,并且压力在70巴至110巴之间变化。
[0116]
通过在亚临界条件下的液化并且通过整合多个阶段中的液化水的厌氧消化,相对于在单个反应阶段进行厌氧消化,可以提高液化水中存在的高cod向生物气的转化率。
[0117]
多阶段厌氧处理可以使转移到水中的有机成分发生高度的生物降解,并伴随产生生物气。
[0118]
进入厌氧反应器的水相的水力停留时间(用于厌氧消化的总水力停留时间)在80至800小时、优选160至500小时之间变化。
[0119]
本专利申请中的水力停留时间被定义为厌氧反应器的体积与水相的每小时体积流速的比率。
[0120]
在70℃至150℃的温度下使水相与通过液化产生的其它流分离。
[0121]
该第一水相可以具有50g/l至200g/l的cod,并且在上述分离和任选的冷却或热回收之后,处于高于或等于65℃的温度。
[0122]
第一水相可以优选地与部分的好氧反应流出物以1:2至1:10w/w的比率(第一水相/部分的好氧反应流出物)混合以使得第一水相的cod在被进料至厌氧消化反应器之前得到稀释。例如,比率1:2表示对于每一重量单位的第一水相,添加相等重量的来自好氧反应器的水;比率1:10表示对于每一重量单位的第一水相,添加9倍重量的来自好氧反应器的水。
[0123]
第一水相可以任选地通过来自设备的废热进行预热,以使得在与部分的好氧反应器流出物混合之后获得至少60℃的温度的溶液。
[0124]
预热操作在设备的启动阶段特别有用。
[0125]
第一水相也可以与,作为好氧反应器流出物的替代物,来自厌氧产酸阶段或来自厌氧产甲烷阶段的流出物混合。
[0126]
此外,可通过在好氧反应器流出物的厌氧消化部分的产甲烷阶段的入口处进行再循环来进行混合。混合比率将由不同流的相对cod决定。
[0127]
参照图1,将生物质或在示例情况下的ofmsw(a)送至预处理区段[1],在其中对其进行大部分惰性部分例如石头、玻璃、铁和其它惰性固体物质的分离,形成废物(o)。将纯化了惰性部分的ofmsw切碎和研磨以减小其尺寸,以获得能够被移动和/或泵送的均相(b)。均相在经过热交换单元使其达到反应温度之后,被送到液化区段[2]。
[0128]
液化的ofmsw(c)离开液化单元[2],然后被送至分离单元(例如,通过一个或多个阶段的离心或倾析)[3],在分离单元[3]中分离出气相(n)(主要是co2)、水相(d)和油相(e)。水相(d)被进料至多阶段厌氧反应器[4],其产生生物气(m)、第二水相(i)和厌氧污泥(h)。第二水相(i)被进料至好氧反应器[5]用于进一步纯化(1)。油相(e)在[6]中被分离为生物油(f)和固体残留物(g)。厌氧污泥(h)可以被再循环到用于预处理[1]的进料中。
[0129]
好氧反应器[5]恢复了允许回收水相用于灌溉目的或供入地表水体[l]的参数。
[0130]
图2显示了与图1相同的单元操作,但是单元操作[3]和[6]相反。
[0131]
液化的ofmsw(c)离开液化单元[2],然后被送至分离单元(例如过滤)[6],在分离单元[6]中分离出固体残留物(g)。剩余的相被进料至分离单元[3],由此获得气相(n)(主要是co2)、第一水相(d)和生物油(f)。第一水相(d)被进料至多阶段厌氧反应器[4],其产生生物气(m)、第二水相(i)和厌氧污泥(h)。第二水相(i)被进料至好氧反应器[5]以用于进一步纯化(1)。
[0132]
参照图15,将水相(d)泵入多阶段反应器,该多阶段反应器由一系列包含悬浮细菌生物质的厌氧阶段[4a、4b、4c、4d、4e、4f]组成。这些反应阶段的特征在于将温度从65℃降低至最后阶段的38℃的最终温度,其中温度可以在40℃至35℃之间变化。
[0133]
在由超嗜热菌和嗜热产酸群落定居的第一反应阶段中,发生水溶液进料(q)中存在的有机物质(包括厌氧消化抑制剂)转化为vfa和其它可溶性中间体。在由嗜温微生物群落定居的随后阶段中,发生所述可溶性中间体转化为生物气,获得了以减少的化学需氧量和低的溶解有机物质含量为特征的第二水相(i)。任选地,将第二水相转移到储罐中,通过好氧活性污泥工艺处理[5],并且部分与进入厌氧消化的第一阶段的液化水相[d]混合。
[0134]
可以根据现有技术中描述的不同方式进行好氧消化,例如,在取决于所选反应器配置具有悬浮、附着或负载的生物质的反应器中,利用机械搅拌、外部再循环或本领域已知的其它模式。
[0135]
好氧消化流出物(f)可以取决于待获得的组分的残留含量根据现有技术中已知的方法被进一步处理,例如,通过与活性炭接触、超滤、反渗透或电渗析以去除残留的盐,并且如果要实现更强的纯化,则通过电氧化。厌氧和好氧消化过程中产生的污泥在被增稠和可能被进一步浓缩(例如通过压滤或离心)之后,可以与其它生物质一起被进料回到液化反应器中。或者,可以将其脱水并送至例如堆肥厂。
[0136]
液化水含有大量的元素,例如氮、磷、铁和微量元素,它们充当活性污泥(厌氧和好氧细菌生物质)的营养素并使其生长。如本领域技术人员所知,如果出现在第一水相中这些化合物不足的情况,则有必要在水处理区段中添加它们。
[0137]
多阶段厌氧反应器可以以连续或间歇管理模式运行。连续管理模式是足够的,并且适合于工业目的待处理的水流,分批或半连续管理模式对于实验室规模来说是有意义的。如图14的方框图所示,对于实施例4,其中通过液化产生了90℃温度的cod为130 000mg/kg的10m3/h水相(d)。将液化水与以残留cod为约150mg/kg为特征的来自好氧消化阶段的40m3/h水(o)混合,形成cod为约26 000mg/kg的稀释流(q)。流(o)被称为长再循环。提出的方案的稀释比为1:4。厌氧反应器的总体积为12000m3,由在空间上通过隔板隔开但是在下方通过通孔并且在顶部通过交替空间(alternating pitch)相连的6个连续的体积之和得出。这使得污泥得以保留,其需要以下降(下降流)然后上升的方式(上升流)(优选在上升区段中)通过不同的体积。每个隔离的体积等于2000m3。前四个体积用产酸污泥工作,并且四个产酸反应器中的水力停留时间总体略超过5天。在第四个厌氧产酸阶段之后,在实施例4中,其cod已转化为挥发性酸的水相通入其中含有产甲烷污泥的体积,并且其中水相保留在两个反应器中的总水力停留时间仅不足3天。可以任选地进行第二次稀释,目的是将来自挥发性酸的cod降低到更低的值。来自好氧消化器并且被进料至具有产甲烷污泥的第一反应器[4e]的稀释流(p)被定义为短再循环。离开好氧阶段的流(f)具有与排放到地表水相容的残留cod(在意大利,第152/06号法令及随后的修订(法令第三部分,附件5,表3)定义了地表水和排水沟的极限排放值)。
[0138]
厌氧消化反应器由不同的微生物群落定居。来自亚临界液化的第一水相(d)相继在以不同温度和不同细菌群体为特征的各隔室中进行厌氧消化。在维持在70℃和55℃之间温度的超嗜热
‑
嗜热条件下的第一阶段中,存在产酸细菌群落,其将溶解的有机化合物(包括具有高抑制潜力的化合物)转化为挥发性酸。在维持在40℃和35℃之间温度的嗜温温度的随后阶段中,存在产甲烷微生物群落,其将所述挥发性酸转化为甲烷,从而产生以cod水平低于输入cod水平为特征的经处理的流出物。
[0139]
在所描述和要求保护的方法中,悬浮液中的厌氧生物质可以具有在5至50g/l、优选地7至15g/l之间的浓度。
[0140]
在所描述和要求保护的方法中,多阶段反应器的每个阶段(产酸和产甲烷)的停留时间在1至14天、优选地2至8天之间变化。
[0141]
以kgcod/m3/天表示的反应器的容积负荷在0.5至5、优选地1至4kgcod/m3/天之间变化。
[0142]
根据本发明的另一实施方案是生物气用于产生电流的用途,以在消除二氧化碳含量之后用于家庭和工业目的在网络中分配。根据本发明的另一个实施方案是生物油在生物柴油和绿色柴油的生产过程中的用途。
[0143]
现在给出本发明的应用的一些实例的描述,其具有纯粹的描述性和非限制性目的,并且代表根据本发明的优选实施方案。
[0144]
对比例1:城市固体废物的有机部分(ofmsw)的液化和单阶段液化水厌氧消化
[0145]
在中试设备中以连续运行进行液化。中试设备将来自城市固体废物的有机分类收集的原料进料至由叶片粉碎机和涡轮机组成的均化单元,以获得粒径小于5mm的奶油状产品。将均化产品以2kg/小时的恒定流速泵入9升标称体积的完全混合式(cstr)反应器中,在该反应器中在280℃、80atm下进行反应,停留时间为2小时。借助于在用于向反应器进料的带夹套的管中、在反应器夹套本身中并且在燃油控制单元中循环的导热油进行加热。反应器在恒定压力下运行。在反应器的顶部,分离气体流并测量其流速。反应流出物在100微米过滤单元中然后在20μm第二过滤单元中通过,其允许分离出固体残留物,在测试结束时进行定量。在设置在称重单元上的温度为90℃的最终罐中收集浓缩流,其中使生物油(轻相)与完全未混合的水相(重相)分离。
[0146]
为了分析的目的,将部分的匀浆(6g)在烘箱中干燥以确定其干重,发现为按重量计26.2%。均浆原样和干燥后的组成在表1中。脂质通过用溶剂从干燥的生物质中提取来确定,并通过在空气中在600℃下煅烧来对灰分进行按重量定量。通过将干燥装料的元素n含量(%重量)乘以6.25来确定蛋白质。通过差异估算碳水化合物。
[0147]
表1
[0148][0149]
进行气相采样以用于连续分析,其确定了具有超过95%的co2的组成,并抽取了部分的水相(10ml)进行分析(分析总有机碳toc、糖和羧酸)。
[0150]
为了定量产生的生物油,将溶剂添加到油相(乙酸乙酯)中,然后通过添加na2so4使其脱水并且再次过滤;将溶剂在旋转蒸发仪中蒸发并且对获得的生物油称重。结果示于表2中,以原样(“原样产率”)或干燥后(“干物质产率”)的按重量计产率%表示。
[0151]
表2
[0152][0153]
从表2中的数据可以看出,大量的废物(相对于干物质原料为43%)被溶解在水相中。
[0154]
水相在105℃下的残留物为10重量%,其中在600℃下的灰分为2重量%。表3显示了水相在105℃下的残留物的元素分析。在100%的补充等于19.3%,表明存在无机灰分,证
实了先前在105℃下的残留物上确定的600℃下2%的灰分。以铵的形式存在的氮等于3900mg/kg,并且用六价铬试剂盒测定的cod为125000mg/kg。
[0155]
表3
[0156]
c(%)h(%)n(%)s(%)o(%)41.35.44.90.228.9
[0157]
关于水相的表征:通过使用pa100柱的离子色谱法进行酸和糖的测定,安培检测系统和naoh梯度洗脱用于糖,电导率检测系统和naoh等度洗脱用于酸。
[0158]
通过测量样品有机碳氧化产生的co2量进行水中toc(总有机碳)的分析。
[0159]
以toc(总有机碳)表示的水相中的酸化合物和单糖(甲酸、乙酸、丙酸、丁酸、甘露醇、葡萄糖)的总和等于8300mg/kg,对比于分析发现的总toc值为41000mg/kg。这表明水相包含许多其它有机化合物。通过萃取到ch2cl2中和气相色谱法,这些化合物的性质估计主要由酮、醛、醇、烷基酚、含氮杂环、烷基吡咯烷酮和二酮哌嗪组成。还使用esi
‑
fticr ms技术以高分辨率15以1:1000稀释在meoh中对原样水进行了分析(图2)。
[0160]
获得具有数千个峰的质谱。此外,含氮化合物以高浓度存在,特别是属于n1、n2、o1n1、o1n2类的那些(除了c和h以外还含有这些元素的经验式)。
[0161]
从质谱的初步处理来看,具有两个氮原子的化合物可视为水中最丰富的类别。因为可以从经验式追溯到双键当量(double bonds equivalent,dbe)的平均数目。下面给出的是n2类别的碳原子、dbe原子的数目和相对峰强度(可以与浓度大致相关)的初步图。n2类别的主要化合物具有6个双键当量和10至14个c原子。更一般地说,可以说这些化合物大多数具有芳香性质。氮可以存在于杂芳族环中,或者可以以氨基形式存在(由于亲水性)。
[0162]
鉴定的化合物不像单糖和酸那样容易生物降解。已经通过icp/xrf分析确定液化水的无机成分的主要元素。表4显示了两种分析,其代表了多个样品中各个被定量元素的变化的极端情况。
[0163]
表4
[0164][0165]
在厌氧消化实验室设备中处理由ofmsw在280℃和2小时的接触时间下产生的液化水。
[0166]
所使用的连续工作的系统由2l的玻璃反应器组成,其通过磁力搅拌进行混合,并且通过在反应器夹套和设定温度的恒温浴中的水再循环加热至35℃。在反应器的输出处有1l的沉降器。从容积为约5升的玻璃罐中抽出水通过蠕动泵将水进料至反应器中。向罐中填充氮以除去微量的氧。在截锥沉积槽中,拖动的污泥稠化为重相,并且通过蠕动泵被再循环到反应器中。经消化的水被排入收集池。生物气积聚在反应器顶部,并且从那里被传送到升测量仪,以测量其流速。在进料时、在反应器中并且在来自沉积槽的输出中定期对水取样,以测量cod、ph。在测试过程中,当仅具有来自蔗糖的cod的水被进料时,添加营养素((nh4)2hpo4和nh4hco3)和微量营养素(kcl、mgso4、cacl2),以维持比率cod:n:p=50:2:1,并且添加碳酸氢盐(nahco3)以使反应器的ph保持在约7。此外,添加fecl2以促进污泥的沉积。当在测试过程中还进料液化水时,由于液化水中已经存在其它元素,因此不添加营养素和微量元素,而仅添加nahco3来保持ph稳定。
[0167]
活性污泥保持平均总固体浓度(tss)等于10g/l,其中75%为挥发性部分(vss)(图5)。
[0168]
厌氧消化测试的过程将借助以下三个附图进行描述。
[0169]
在从2016年11月1日持续到2017年1月14日的测试中,有4个主要阶段:
[0170]
1)2017年11月1日至2017年11月9日:来自工业废水处理厂的污泥的驯化,其平均cod为2000mg/kg的蔗糖,水力停留时间hrt为13.6小时,并且容积负荷为2.8kg
cod
/m3/天。在此阶段结束时,cod的转化率为约90%,输出cod为200mg/kg,产生的生物气为0.32升/g的被转化的cod;
[0171]
2)2017年11月10日至2017年11月18日:添加来自液化水的cod以代替部分的蔗糖,以暂时将测试的cod进料保持在约2000mg/kg,平均hrt为40小时,并且容积负荷为0.8kg
cod
/m3/天。
[0172]
归因于液化水的cod进料是图3中用虚线描绘的,并且使其增长至达到总cod进料的80%。随着液化水的添加,cod转化率迅速下降到60%,然后又上升到70%。在该阶段结束时,cod输出为420mg/kg,随后是去除进料中的液化水的阶段,这使cod的转化率恢复到接近90%的值。
[0173]
3)2016年11月23日至2016年12月20日:除了2000mg/kg的来自蔗糖的cod外,添加来自液化水的cod,平均hrt为55小时,并且容积负荷为1
‑
1.4kg
cod
/m3/天。归因于液化水的cod进料是图3中用虚线描绘的,并且使其增长至达到总cod进料的35%。随着液化水的添加,cod转化率迅速下降到60%。在此阶段结束时,cod输出超过1500mg/kg,并且生物气产量降至0.19升/g的被转化的cod。这之后是去除液化水进料并且用蔗糖代替的阶段,这再次使cod的转化率恢复到接近90%的值。
[0174]
4)2017年1月2日至2019年2月10日:除了2000ppm的来自蔗糖的cod外,最初添加来自液化水的cod,平均hrt为53小时,并且容积负荷为0.9至1.8kg
cod
/m3/天。归因于液化水的cod进料是图3中用虚线描绘的,并且使其增长至达到总cod进料的100%,等于4200mg/kg。随着液化水的添加,cod转化率迅速下降至35%。在此阶段结束时,cod输出超过2500mg/kg,并且生物气产量降至0.13升/g的被转化的cod。
[0175]
该测试表明,很难除去液化水的cod与强烈抑制厌氧消化的化合物的存在有关。因此,该水相不能再次进入环境,并需要被进一步处理。
[0176]
实施例2:来自ofmsw的液化水的两阶段厌氧消化(在20ml注射器式反应器中的分批测试)
[0177]
在20ml注射器式反应器中在与实施例1中描述的相同的液化水(水p9)中进行厌氧消化测试,测量cod转化率、生物气产生以及厌氧消化中间体(特别是vfa)的产生。
[0178]
进行测试的方法如下所述,并且如图6所示。
[0179]
1)取出柱塞,用橡皮帽封闭注射器的尖端,添加总计20ml的厌氧泥浆(接种物)和液化水。
[0180]
2)用柱塞封闭注射器。
[0181]
3)翻转注射器,并且使内容物沉降在底部。
[0182]
4)通过取下帽排出空气来缓慢释放内部压力。
[0183]
5)用帽封闭注射器。
[0184]
6)将注射器放入调节至40℃或60℃的反应温度的烘箱中。
[0185]
7)确定每24小时产生的生物气,读取液化水中产生的气体的ml数,并且将其从注
射器中排出。
[0186]
8)取下帽并且对消化物(接种物+液化水)取样。
[0187]
9)对消化物进行离心以使待重新注入注射器式反应器的致密相与待分析的液体分离。
[0188]
10)添加液化水进行消化,并且用其再次吸收点9分离出的致密相。
[0189]
在40℃(嗜温)和60℃(嗜热)下进行了两项测试:
[0190]
两项测试均重复进行。图(图7和8)中显示的数据是每项测试2次重复的平均值。生物气和vfa的各自浓度根据被转化的原始cod(mg/kg)报道。
[0191]
最初,向注射器进料1600mg/kg的葡萄糖溶液,然后直至第17天,从液化水施用增加浓度的cod,直至约24000mg/kg,对应于3.4kg/m3/天的容积负荷。在逐渐添加cod之后,观察到生物气中的高co2含量,和随后生物气产生的完全抑制。从第47天开始,施用来自液化水的cod的其它部分,这产生了vfa(直至最高约10g/kg,等于21000mg/kg的cod)而不是生物气的进一步增加。这表明产甲烷菌完全失活,但保持了有效的产酸活性(将原始cod转化为vfa)。在测试结束时(第74天),输入cod向生物气和vfa的转化率为约90%。
[0192]
然后将第二组反应器设置在40℃,向其中施用来自第一组反应器的液体,其vfa浓度为约13g/kg,总cod为18000mg/kg,并且最大容积负荷为2kgcod/m3/天。结果总结在图9中,并且表明cod向生物气的转化率达到80%,并且尤其是没有显示出停滞状态,而是作为cod进料的函数增加的趋势,这与在单一步骤中进行消化时发生的不同(参见图3)。68天后向挥发性酸vfa的转化率保持在约18%。
[0193]
实施例3:来自ofmsw的液化水的两阶段厌氧消化(在80ml各反应器中连续测试)
[0194]
在各自具有80ml体积的反应器中在实施例1中所述的液化水(水p9)中进行连续两阶段厌氧消化测试。通过电加热将各反应器温度保持在60℃和40℃。借助于蠕动泵将水相进料至第一反应器和第二反应器。提供了利用蠕动泵从第二反应器到第一反应器的外部再循环。对离开第二反应器的气体和液体进行采样并送去分析。
[0195]
借助图10描述了进行测试的方法,并且结果如图11所示。
[0196]
最初用30ml的活性污泥接种物和50ml的水和葡萄糖至cod为21400mg/kg来启动各反应器。将相同溶液以5ml/天连续进料至第一反应器,对应于每个反应器16天的hrt(水力停留时间)。葡萄糖溶液的施用延长至第16天。从第17天至第21天,以2ml/天向反应器进料cod=22600mg/kg的液化水,然后从第22天起进料增加到5ml/天。
[0197]
实施例4:来自ofmsw的液化水的六阶段厌氧消化(模拟以10m3/h的流速进行的连续测试)
[0198]
该测试在实验室规模下进行,其具有串联设置的总计等于12升的厌氧反应器体积(每个阶段为2升)和4升的好氧反应器。
[0199]
阶段的体积(2升)是指在其中细菌生物质增稠的水相的上升阶段。阶段的总体积较大,但仅在上升部分中存在大量细菌生物质。
[0200]
对于每个阶段,通过与在反应器的不同腔室(加热夹套)中循环的受控温度的水流进行热交换来保证期望的温度。
[0201]
第一水相的处理通过经由厌氧反应器然后经由好氧反应器来连续进行。处理的开始致力于使可用的活性污泥(来自工业水处理厂的污泥)驯化,以专门化不同阶段的细菌。
这种驯化是用合成水进行的,其中用蔗糖产生cod并且以现有技术中已知的厌氧消化中的典型使用比率添加了肥料和微量元素。在污泥已经专门化并且离开好氧反应器的水相小于150mg/kg之后,进料具有相同cod(来自蔗糖)的液化水。随后是过渡阶段,第二水相中的cod增大,但是随后又下降并达到稳定值。参照图15,将水相(d)进料至由一系列厌氧阶段[4a、4b、4c、4d、4e、4f]形成的多阶段反应器的第一阶段。这些反应阶段的特征是温度从65℃降低至最后阶段中38℃的最终温度。
[0202]
表5显示了厌氧反应器的六个隔室的温度谱和主要流的流速。
[0203]
表5
[0204][0205]
在由超嗜热和产酸嗜热细菌群落定居的厌氧反应器的前4个阶段中,发生水溶液进料(q)中存在的有机物质转化为vfa和其它可溶性中间体。在由嗜温微生物群群落定居的接下来2个阶段中,发生所述可溶性中间体转化为生物气,获得了特征在于cod≤5000mg/kg的第二水相(i)。最初将0.3kg/天的cod为130000mg/kg的第一水相与1.2kg/天的井水(并且当可用时,替代地与1.2kg/天的cod为150mg/kg的离开好氧消化阶段的水(o))混合,形成cod等于约26000mg/kg的稀释流(q)。流(o)被定义为长再循环。提出的方案的稀释比为1:4。
厌氧反应器的总体积为12l,由6个连续体积的总和得出。每个隔离的体积等于2l。前四个体积处理产酸污泥,并且4个产酸反应器中的水力停留时间总计为128小时。在第四个产酸厌氧阶段之后,水相移动到其中包含产甲烷细菌生物质的体积中,并且在其中水相保持64小时的水力停留时间(两个反应器中的总和)。从最后一个厌氧阶段,气流(m)流出并被送至体积计数器,以估算产生的生物气的量。当充分运行时,发现在产酸反应器中cod向vfa的转化率为90%(从cod=26 000mg/kg开始),并且在产甲烷反应器中cod向生物气的转化率为80%,因此生物气生产率为20升/天或512n升的生物气/kg的被转化的cod,并且在待送至好氧反应器[5]的第二水相中cod=5000mg/kg。厌氧反应器的总有机负荷为3.2kg
cod
/m
3反应器
/天。
[0206]
产生的第二水相进入好氧反应器,在好氧反应器中其保持悬浮,这是因为来自设置在容积为4升的圆柱形反应器底部的分配环的空气的引入。反应器的溢流供入具有约0.5升可用体积的沉降器,增稠的污泥从沉降器的底部再循环至反应器。从沉降器的顶部回收经处理的澄清水以备后用。在好氧反应器中的水力停留时间为2.7天。离开好氧阶段的流(f)的残留cod小于160mg/kg。
[0207]
第一水相保留在厌氧反应器中的总时间为192小时,等于8天,并且第二水相保留在好氧反应器中的时间为2.7天。
[0208]
根据图15中的图表,从实验室规模的数据中模拟出一个案例,该案例的工业规模尺寸等于需要处理10m3/h的来自ofmsw液化的特征在于cod=130 000mg/kg的第一水相。预期厌氧反应器以3.2kg
cod
/m3反应器/天的有机负荷运行。根据完全处理(排出中的cod≤160mg/kg)上述ofmsw液化水的这些假设,估计总厌氧反应器体积为12000m3,随后好氧反应器体积为4000m3(包括20%的过大尺寸),其与全速下665nm3的生物气/小时的产量相关。