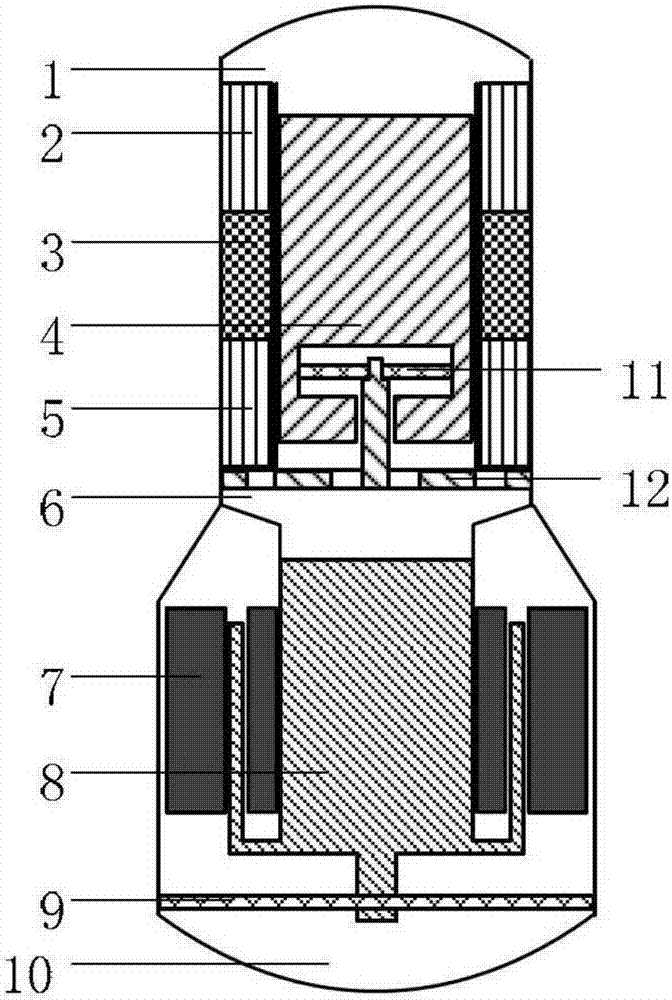
本发明涉及热能动力技术,尤其涉及一种自由活塞斯特林热机。
背景技术:自由活塞斯特林热机是热声热机的一种结构形式。它使用排出器代替了传统斯特林热机中的曲轴结构,通过控制排出器的动质量和板簧刚度等调节其声场相位分布实现高效的热声或者声热的转换,并通过阻抗匹配和声场耦合方式实现与直线电机或直线压缩机之间的高效耦合,构建自由活塞斯特林发电机或电驱动自由活塞斯特林制冷机。采用正向斯特林循环的斯特林发动机通过高温换热器吸热,室温换热器放热,在回热器中基于热声效应实现热能向声功的转化。采用逆向斯特林循环的斯特林制冷机在回热器内消耗声功,从而实现熵流从冷端向室温端的输运,实现制冷效应。其理论效率均为卡诺效率。由于取消了机械传动结构,自由活塞斯特林热机内部无油润滑装置,因此具有振动小,结构简单和高可靠性的优点;其采用氦气或氢气等为工质,绿色环保;此外,作为外燃式热机,其能源利用形式多样,可采用太阳能、地热、生物质等清洁能源和工业余热等作为热源。基于以上特点,自由活塞斯特林热机在太阳能发电、余热发电和高温强电超导冷却等领域具有广阔的应用前景。虽然自由活塞斯特林热机优点突出,应用潜力巨大,但是其排出器加工、装配精度要求较高,排出器间隙密封的加工装配难度和可靠性是自由活塞斯特林热机大规模应用的主要限制因素之一。现有自由活塞斯特林热机主要有两种结构形式,分别如图1、图2所示。现有的自由活塞斯特林热机主要包括膨胀腔1、热端(冷端)换热器2、回热器3、排出器4、室温换热器5、压缩腔6、定子7、动力活塞8、动力活塞支撑9、直线电机背腔10。图1所示结构中,排出器的隼部与直线电机耦合,动力活塞支撑板簧置于电机背腔,这种结构降低了平面板簧的设计难度,容易实现较大的径轴刚度比,但是排出器的隼部为细长杆,因其与动力活塞之间为间隙密封,所以对设计、加工和装配精度要求较高,且因其两侧受力不平衡而存在结构失稳因素。图2所示结构中,其排出器支撑板簧11置于排出器内部,排出器的隼部与排出器底座12一体,这种结构消除了排出器的隼部较长易变形失稳的缺点,但是排出器支撑板簧尺寸受排出器尺寸的制约,显著增加了设计、材料、和加工工艺的难度,其可靠性也受影响。
技术实现要素:本发明提供一种自由活塞斯特林热机,用于克服现有技术中的缺陷,增强排出器运动的平稳性和可靠性,提高系统的使用寿命,同时特降低了工艺和装配难度,提高了其实用性。为达到上述目的,本发明采用的技术方案如下:一种自由活塞斯特林热机,所述斯特林热机包括若干个斯特林发动机和若干个直线振荡电机,所述任一斯特林发动机包括排出器4,所述排出器4包括上塞体4-1、下塞体4-2、隼部4-3、平面支撑板簧4-4、高温筒4-5、腔体4-6和底座4-7;所述底座4-7固定在室温换热器5的底部,底座4-7上设置阶梯式气缸4-8,阶梯式气缸4-8的内侧壁上设置台阶4-9,台阶4-9上部的阶梯式气缸4-8内壁间隙密封设置上塞体4-1,台阶4-9下部的阶梯式气缸4-8内壁间隙密封设置下塞体4-2,所述上塞体4-1与下塞体4-2之间空腔形成间隙密封的腔体4-6;所述隼部4-3设置在腔体4-6内且两端分别固定在上塞体4-1和下塞体4-2上,隼部4-3穿过平面支撑弹簧4-4并固定在平面支撑弹簧4-4上,平面支撑弹簧4-4固定在台阶4-9上,上塞体4-1上部设置高温筒4-5。本发明中,所述上塞体4-1和下塞体4-2均为圆筒形结构。本发明中,所述上塞体4-1直径大于下塞体4-2直径。本发明中,所述平面支撑弹簧4-4包括两组呈平行状设置的弹簧。本发明中,所述直线振荡电机包括定子7、动力活塞8和动力活塞支撑9。本发明中,所述动力活塞支撑9为板簧支撑或气浮轴承支撑。在本发明中,腔体4-6中工质压力(高压氦气)与其他部件(如膨胀腔、压缩腔、回热器、电机等充满工质的空间)的工质压力相同。其含义为:腔体4-6与其他部件空间相连通,因而各个工质空间中工质具有相同的平均工作压力。但排出器运动时则为动态密封,其他部件中的压力波动不会影响到腔体4-6中的压力。本发明中,所述斯特林发动机的数量为一个或两个。所述直线振荡电机的数量为一个或两个。当斯特林发动机的数量为一个,直线振荡电机的数量为两个时,直线振荡电机呈对称设置。当斯特林发动机的数量为两个,直线振荡电机的数量为两个时,斯特林发动机和直线振荡电机分别呈对称设置。本发明中,所述排出器上塞体与下塞体之间形成密封腔体,内部气体具有与其他部件相同的平均压力。排出器上塞体的直径大于下塞体直径,因此随着排出器的运动,排出器腔体体积发生变化,腔体内气体随之经历绝热压缩或者膨胀过程,从而实现了气体弹簧的效果,如此便可以减小平面支撑板簧的轴向刚度,有利于降低板簧的设计难度和选材要求。此外,两组平面支撑板簧结构有利于减小排出器运动时产生的抖动,从而保证排出器与气缸之间的间隙密封,降低活塞与气缸发生接触摩擦的风险。假设随排出器腔体内部气体随其运动经历绝热压缩和膨胀过程,采用集总参数法可得气体弹簧的刚度为假设随排出器腔体内部气体随其运动经历绝热压缩和膨胀过程,采用集总参数法可得气体弹簧的刚度为Kgas=γP0A2/V。V为腔体容积,P0为腔体内气体的平均压力,A为腔体横截面积,γ为气体比热比。所述平面支撑板簧外圆固定在底座上。相对于图2所示结构即排出器支撑板簧中心固定,本发明采用的外圆固定方式更稳定,而且相同排出器位移下板簧的动质量更小。排出器的受力平衡方程:分别为膨胀腔和压缩腔的压力波动,为排出器往复运动速度,Adis、Arod分别为排出器和排出器杆(即排出器隼部)的面积,Rm、M、K分别为排出器等效机械阻尼、排出器动质量、平面支撑板簧轴向刚度,ω为系统运行角频率。根据上述方程,在谐振频率不变的情况下,动质量减小,运行在谐振状态下需要的板簧刚度也进一步减小。所述排出器上塞体和下塞体通过隼部与平面支撑板簧密封连接。排出器上下塞体布置在两组平面支撑板簧的两侧,结构更稳定;排出器隼部长度大大缩短,可以保证排出器隼部的结构强度。所述底座上具有阶梯型气缸结构,排出器上塞体和气缸之间、排出器下塞体和气缸之间均采用间隙密封以减小膨胀腔1和压缩腔5之间的窜气和漏热损失。间隙密封的结构包为迷宫、镀层等形式。本发明热机中的任一斯特林发动机还包括耐压壳体,排出器4与耐压壳体之间空腔形成膨胀腔1,排出器4与直线振荡电机之间空腔形成压缩腔6。本发明热机中的任一斯特林发动机还包括热端(冷端)换热器2、回热器3和室温换热器5,上述结构按顺序从膨胀腔至压缩腔依次设置在热机外壁上,均可采用本领域的常规设置方式。所述热端(冷端)换热器与室温换热器均包含两部分组件,一是外部换热器,实现外部热源(如燃烧器热量或者制冷机被冷却负载的热负荷)和换热器外壁面的换热,另一部分是内部换热器,实现内部工质气体和换热器壁面之间的换热。换热器一般在换热量较小时采用结构紧凑的翅片式而在换热量较大时采用壳管式。所述回热器3内部填充多孔材料,如不锈钢丝网或不锈钢纤维毡。根据经典热声学,回热器是热声热机功热转换的核心部件,同时也是损失产生的主要部件。其内部填充物参数对整机系统性能有着显著的影响。回热器水力半径与工质气体热穿透深度之比越小,气体与回热器填充物之间的换热就越好,热损失也就越小,但此时的流动损失也越大。因此,优选实施方式需要权衡换热损失与流动损失,合理的选择填充物参数,包括丝径和孔隙率。所述动力活塞支撑既可采用图1-3中所示平面支撑板簧支撑,也可采用气浮轴承支撑。直线振荡电机既可采用动磁式,、动铁式,也可采用动圈式,此处不作任何限制。本发明所提供的自由活塞斯特林热机采用阶梯排出器结构,利用排出器上下塞体之间的空腔作为气体弹簧,降低了所需平面支撑弹簧的轴向刚度,既保证了排出器与气缸之间的间隙密封,降低排出器与气缸发生接触摩擦的风险,也降低了平面支撑板簧的设计、材料和工艺难度,提升了平面支撑板簧的寿命。平面支撑板簧外圆固定在底座上,其动质量小,有利于进一步减小所需的平面支撑板簧的轴向刚度。排出器由两组平面支撑板簧支撑,该结构在排出器往复振动时更稳定。因此,本发明提出的自由活塞斯特林热机新结构既降低了工艺和装配难度,又提高了系统的稳定性和可靠性。附图说明图1为现有技术中排出器-动力活塞耦合型自由活塞斯特林热机示意图;图2为现有技术中排出器-动力活塞分置式自由活塞斯特林热机示意图;图3为本发明实施例1提供的自由活塞斯特林热机结构示意图;图4为本发明实施例2提供的自由活塞斯特林热机结构示意图;图5为本发明实施例3提供的自由活塞斯特林热机双置式结构示意图;图6a、图6b、图6c、6d为本发明的自由活塞斯特林热机的工作原理图;附图标记:1、膨胀腔;2、热端(冷端)换热器;3、回热器;4、排出器;4-1、上塞体;4-2、下塞体;4-3、隼部;4-4、平面支撑板簧;4-5、高温筒;4-6、腔体;4-7、底座;4-8、阶梯式气缸;4-9、台阶;5、室温换热器;6、压缩腔;7、定子;8、动力活塞;9、动力活塞支撑;10、直线电机背腔;11、排出器支撑板簧;12、排出器底座。具体实施方式下面以附图和具体实施方式对本发明作进一步详细的说明。实施例1图3为本发明实施例1提供的自由活塞斯特林热机结构示意图。一种自由活塞斯特林热机,所述斯特林热机包括一个斯特林发动机和一个直线振荡电机,所述任一斯特林发动机包括排出器4,所述排出器4包括上塞体4-1、下塞体4-2、隼部4-3、平面支撑板簧4-4、高温筒4-5、腔体4-6和底座4-7;所述底座4-7固定在室温换热器5的底部,底座4-7上设置阶梯式气缸4-8,阶梯式气缸4-8的内侧壁上设置台阶4-9,台阶4-9上部的阶梯式气缸4-8内壁间隙密封设置上塞体4-1,台阶4-9下部的阶梯式气缸4-8内壁间隙密封设置下塞体4-2,所述上塞体4-1与下塞体4-2之间空腔形成间隙密封的腔体4-6;所述隼部4-3设置在腔体4-6内且两端分别固定在上塞体4-1和下塞体4-2上,隼部4-3穿过平面支撑弹簧4-4并固定在平面支撑弹簧4-4上,平面支撑弹簧4-4固定在台阶4-9上,上塞体4-1上部设置高温筒4-5。本发明中,所述上塞体4-1和下塞体4-2均为圆筒形结构。本发明中,所述上塞体4-1直径大于下塞体4-2直径。本发明中,所述平面支撑弹簧4-4包括两组呈平行状设置的弹簧。本发明中,所述直线振荡电机14包括定子7、动力活塞8和动力活塞支撑9。本发明中,所述动力活塞支撑9为板簧支撑,动力活塞支撑9与耐压壳体13之间形成直线电机背腔10。本发明斯特林发动机还包括耐压壳体,排出器4与耐压壳体之间空腔形成膨胀腔1,排出器4与直线振荡电机之间空腔形成压缩腔6。本发明斯特林发动机还包括热端(冷端)换热器2、回热器3和室温换热器5,上述结构按顺序从膨胀腔至压缩腔依次设置在热机外壁上,均可采用本领域的常规设置方式。图6a、图6b、图6c、图6d为本发明提供的自由活塞斯特林热机的工作原理图;通过设计合理的排出器上下塞体直径、排出器动质量、平面支撑板簧的刚度及排出器腔体内的气体弹簧刚度,可以为回热器提供合适的声场阻抗,进而满足热机高效运行的声场要求。参照图6a-图6d,本实施例提供的自由活塞斯特林热机作为发电机的工作原理如下:图6a-图6b过程,动力活塞8从下止点与排出器4同时上行,使的气体在压缩腔6内被压缩,并通过室温换热器5向外界放热。图6b-图6c过程,动力活塞8继续行,排出器4下行,气体从压缩腔6流经回热器3进入膨胀腔1,图中将热量释放给回热器3,温度降低。图6c-图6d过程,气体在膨胀腔1内,通过高温换热器2从外界吸热膨胀,使得排出器4下行,并推动动力活塞8下行。此过程中,回热器3将热能转化为声能,并通过气体推动动力活塞9从而使得直线电机动子切割磁力线向外界输出电能。图6d-图6a过程,动力活塞8继续下行,排出器4上行,气体从膨胀腔1流经回热器3进入压缩腔6,图中将热量释放给回热器3,回热器3温度升高,气体温度降低。完成上述完整循环过程后,气体从外部热源吸热,向环境放热,实现热能向机械能的转化,并推动直线电机动力活塞切割磁力线从而向外界输出电能。排出器4和动力活塞8做往复直线运动,前者相位领先后者。本实施例提供的自由活塞斯特林发电机中排出器和动力活塞的工作机理与现有技术相同。但本实施例提供的自由活塞斯特林发电机的结构设计和工艺特点与现有技术有较大的差别。排出器在平衡位置上方时,排出器腔体内的气体膨胀,气体动态压力降低,排出器受到气体弹簧和平面支撑弹簧的回复力指向向下。排出器在平衡位置下方时,排出器内气体被压缩,气体动态压力升高,排出器受到气体弹簧和平面支撑弹簧的合力指向向上。由于平面支撑板簧外周与底座固定,在排出器往复运动过程中,板簧参与运动的质量较小,同时由于采用了气体弹簧,平面支撑板簧所需提供的回复力较小,所需板簧轴向刚度减小,从而有利于实现较大的径轴刚度比,约束了排出器的径向位移,防止间隙密封遭到破坏。基于上述,本发明提供的自由活塞斯特林热机,其排出器利用气体弹簧,并减小了板簧动质量,减小了排出器抖动,降低平面支撑板簧的设计、工艺和装配难度,有效降低了制造成本,提高了系统的可靠性和使用寿命。实施例2图4是本发明实施例2的自由活塞斯特林热机结构示意图。由图4可知,本实施例的自由活塞斯特林热机由一个自由活塞斯特林发动机(或制冷机)和两个直线振荡电机组成;直线振荡电机对称布置,与发动机(或制冷机)之间用连接管耦合。实施例2的工作原理与实施例1相同,区别在于实施例2中的直线电机为两个,且结构参数完全相同,并对称布置;这种布置方式可以使两个电机动力活塞运动相位相差180度,从而完全抵消电机动力活塞引起的机壳振动。相比实施例1,实施例2的振动和噪声均更小。实施例3:图5为本发明实施例3所提供的自由活塞斯特林热机双置式结构示意图;如图5所示,本实施例的自由活塞斯特林热机由两个自由活塞斯特林发动机(或制冷机)和两个直线振荡电机组成;发动机(制冷机)和直线电机分别呈对称布置,发动机和直线电机之间用连接管连接。实施例3的工作原理与实施例1相同,区别在于实施例3中的发动机(制冷机)和直线电机均为两个,且结构参数完全相同,呈对称布置。这种布置方式可以完全抵消排出器和电机活塞运动产生的机壳振动。相比实施例1和2,实施例3的振动和噪声更小,功率密度更高。最后应说明的是:以上各实施例仅用于说明本发明的技术方案,而非对其限制;尽管参照前述各实施例对本发明进行了详细的说明,本领域的普通技术人员应当理解:其依然可以对前述各实施例所载的技术方案进行修改,或者对其中部分或者全部技术特征进行等同替换;而这些修改或者替换,并不使相应技术方案的本质脱离本发明各实施例技术方案的范围。