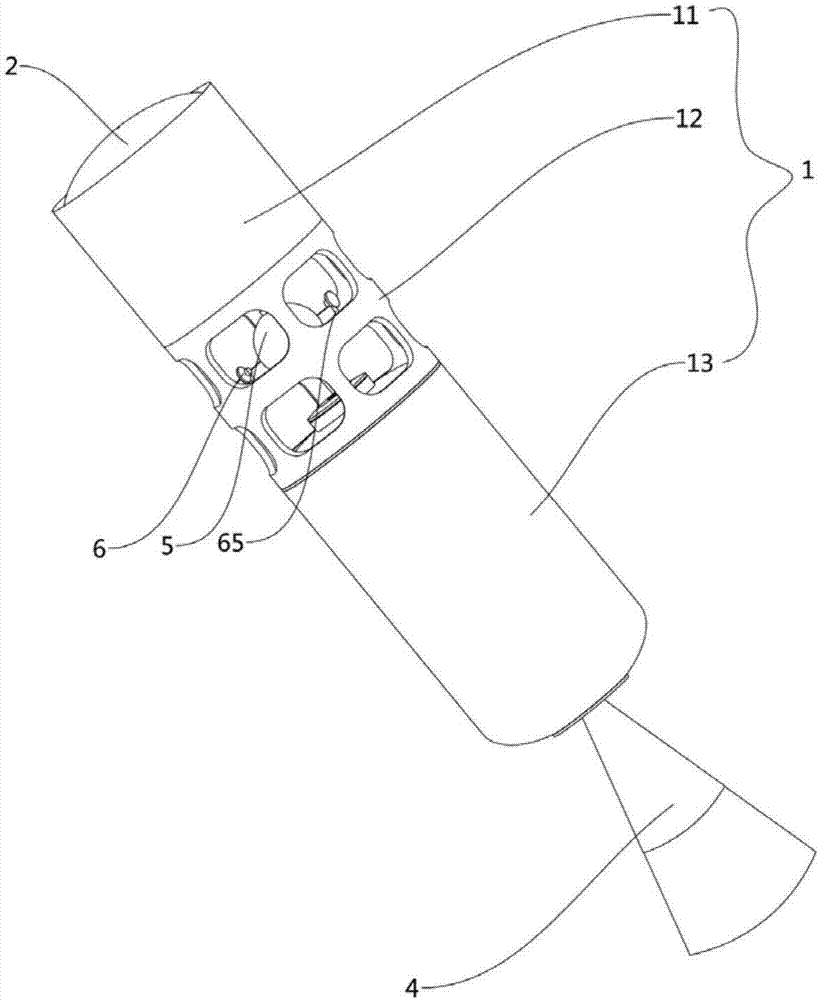
本发明涉及航空航天
技术领域:
,尤其是涉及一种双泵固液火箭发动机。
背景技术:
:近年来,随着高能量密度电池技术、无刷直流电机技术、3d增材制造等技术的突破性发展,电动泵压式推进剂供应方式,因其具有高效率、调节方便、结构简单等优点而重新得到了国际上的重视。同时随着小型有效载荷如微小卫星需求的不断地提高,故为实现低成本、快速发射的小型运载火箭,尤其是为了实现用于100公斤级小型有效载荷质量的太阳同步圆轨道运输运载器,电动泵固液火箭发动机应运而生。但是现有的电动泵固液火箭发动机,往往采用的是单个电动泵,容易造成发动机重心偏心且电动泵的抽吸性能降低的后果。技术实现要素:本发明的目的在于提供一种双泵固液火箭发动机,以解决现有技术中的发动机重心偏心且电动泵的抽吸性能低的技术问题。本发明的上述技术问题主要是通过下述技术方案得以解决的:一种双泵固液火箭发动机,包括机壳,所述机壳内部设有依次连接的贮箱、推力室和摆动喷管,其中,所述贮箱和所述推力室成间隔设置,所述机壳内部还设有气瓶和电动泵组件,且所述气瓶和所述电动泵组件设于所述贮箱和所述推力室之间,所述电动泵组件设有两个,且分别设置在所述气瓶的两侧。作为优选,所述电动泵组件包括电动泵、电机、逆变器及用于供电的电池,所述电动泵、电机、逆变器与电池依次电性连接并形成回路。作为优选,两个所述的电动泵组件沿所述气瓶的轴线成对称设置,所述气瓶与所述机壳成同轴设置。作为优选,所述机壳包括依次连接的第一段机壳、第二段机壳和第三段机壳,所述贮箱设于所述第一段机壳内,所述气瓶和所述电动泵组件设于所述第二段机壳内,所述推力室设于所述第三段机壳内。作为优选,所述机壳为圆柱形,且所述第一段机壳、所述第二段机壳和所述第三段机壳的外径为相同设置,其中,所述第二段机壳为铝蜂窝夹芯板或者泡沫铝夹芯板制成的。作为优选,所述第二段机壳的管壁上均匀分布有两个或两个以上的通孔,所述的电动泵组件通过连接杆固定在所述第二段机壳的内壁上。作为优选,所述推力室包括燃烧室外壳和固体装药,所述燃烧室外壳内壁上包覆有绝热层,所述固体装药设于所述外壳内且与所述摆动喷管连接,所述固体装药为圆柱形,且固体装药径向截面为无中心孔的车轮状。作为优选,所述燃烧室外壳一端与所述摆动喷管连接,另一端上连接有顶盖,所述顶盖包括顶盖本体,所述顶盖本体上设有能与所述燃烧室外壳相抵的凸缘,所述顶盖本体的中心位置上凸设有凸起部,所述凸起部的上表面上设有氧化剂均流板,所述氧化剂均流板上设有盖板,所述凸起部的下表面上设有催化床,且所述顶盖本体下表面除所述凸起部之外覆盖有绝热层。作为优选,所述摆动喷管包括依次连接的连接部、喉部和喷管,其中,所述连接部伸入所述燃烧室外壳,并与所述燃烧室外壳螺纹连接,所述喷管为锥形,且所述喷管包括由外至内依次设置的外表面层和隔热层,所述喉部包括喉衬和收敛段,所述收敛段的顶端与所述连接部相连,尾端与所述喉衬相连,且所述收敛段由顶端至尾端的内径依次减小,且所述喉衬与所述喷管相连。作为优选,所述高压气瓶通过第一管道与所述贮箱相连,所述贮箱通过第二管道与所述电动泵组件相连,所述电动泵组件通过第三管道与所述推力室相连,所述第一管道上分别安装有气体充气阀、气瓶泄压阀、减压器、电爆阀和贮箱加注泄气阀;所述第二管道上分别安装有贮箱加注泄出阀、膜片阀和泵前阀;所述第三管道上分别安装有气蚀文氏管和泵后阀。本发明采用双电动泵对置布局,两个相同的电动泵组件对称布置于高压气瓶两侧,减小了发动机重心偏心,提高了电动泵的抽吸性能。再者由于本发明以两个并联的电动泵作为其输送系统,将本发明作为火箭动力,既满足了总体需求的发动机流量,又可利用电动泵输送系统比涡轮泵输送系统启动速度快、比挤压式输送系统所需贮箱压力显著减小的优势,提高发动机可靠性和安全性。本发明尤其适合用于100公斤级小型有效载荷质量的太阳同步圆轨道运输运载器。基于此,本发明较之原有技术,具有发动机重心偏心程度小,电动泵的抽吸性能高的优点。附图说明为了更清楚地说明本发明具体实施方式或现有技术中的技术方案,下面将对具体实施方式或现有技术描述中所需要使用的附图作简单地介绍,显而易见地,下面描述中的附图是本发明的一些实施方式,对于本领域普通技术人员来讲,在不付出创造性劳动的前提下,还可以根据这些附图获得其他的附图。附图1为本发明的结构示意图;附图2为本发明的剖视图;附图3为附图2的a部放大图;附图4为附图2的b部放大图;附图5为本发明固体装药的截面图;附图6为本发明管道连接示意图。图标:1-机壳;11-第一段机壳;12-第二段机壳;121-通孔;13-第三段机壳;2-贮箱;3-推力室;31-燃烧室外壳;32-绝热层;33-固体装药;34-顶盖;341-顶盖本体;342-凸缘;343-凸起部;344-氧化剂均流板;345-盖板;346-催化床;347-顶盖绝热层;4-摆动喷管;41-连接部;42-喉部;421-喉衬;422-收敛段;43-喷管;431-外表面层;432-隔热层;5-气瓶;6-电动泵组件;61-电动泵;62-电机;63-逆变器;64-电池;65-连接杆;7-第一管道;71-气体充气阀;72-气瓶泄压阀;73-减压器;74-电爆阀;75-贮箱加注泄气阀;8-第二管道;81-贮箱加注泄出阀;82-膜片阀;83-泵前阀;9-第三管道;91-气蚀文氏管;92-泵后阀。具体实施方式下面将结合附图对本发明的技术方案进行清楚、完整地描述,显然,所描述的实施例是本发明一部分实施例,而不是全部的实施例。基于本发明中的实施例,本领域普通技术人员在没有做出创造性劳动前提下所获得的所有其他实施例,都属于本发明保护的范围。在本发明的描述中,需要说明的是,术语“中心”、“上”、“下”、“前”、“后”、“竖直”、“液平”、“内”、“外”等指示的方位或位置关系为基于附图所示的方位或位置关系,仅是为了便于描述本发明和简化描述,而不是指示或暗示所指的装置或元件必须具有特定的方位、以特定的方位构造和操作,因此不能理解为对本发明的限制。此外,术语“第一”、“第二”、“第三”仅用于描述目的,而不能理解为指示或暗示相对重要性。在本发明的描述中,需要说明的是,除非另有明确的规定和限定,术语“安装”、“相连”、“连接”应做广义理解,例如,可以是固定连接,也可以是可拆卸连接,或一体地连接;可以是机械连接,也可以是电连接;可以是直接相连,也可以通过中间媒介间接相连,可以是两个元件内部的连通。对于本领域的普通技术人员而言,可以具体情况理解上述术语在本发明中的具体含义。双泵固液火箭发动机的实施例一:见图1、图2,一种双泵固液火箭发动机,包括机壳1,机壳1内部设有依次连接的贮箱2、推力室3和摆动喷管434,其中,贮箱2和推力室3成间隔设置,机壳1的内部还设有气瓶5和电动泵组件6,且气瓶5和电动泵组件6设于贮箱2和推力室3之间,电动泵组件6设有两个,且分别设置在气瓶5的两侧。本发明采用双电动泵对置布局,两个相同的电动泵组件对称布置于高压气瓶两侧,减小了发动机重心偏心,提高了电动泵的抽吸性能。再者由于本发明以两个并联的电动泵作为其输送系统,将本发明作为火箭动力,既满足了总体需求的发动机流量,又可利用电动泵输送系统比涡轮泵输送系统启动速度快、比挤压式输送系统所需贮箱压力显著减小的优势,提高发动机可靠性和安全性。本发明尤其适合用于100公斤级小型有效载荷质量的太阳同步圆轨道运输运载器。需要说明的是,本实施例中,发动机质量≤3.75吨,真空比冲不小于≥310秒,总冲≥9.91×103kn·s,平均推力≥66kn,工作时间≥150s。本发明为使用摆动喷管进行推力矢量控制的98%h2o2/htpb基固液混合火箭发动机,采用固体燃料和液体氧化剂的推进剂组合。本发明的氧化剂输送系统采用双电动泵循环系统。本发明的贮箱采用圆柱段加椭球封头的结构形式,并为碳纤维复合材料制成的。气瓶为球形结构,同样为碳纤维复合材料制成的。气瓶内的气体为氮气。其中,发动机贮箱和气瓶的主要设计参数如下表所示:见图6,电动泵组件6包括电动泵61、电机62、逆变器63及用于供电的电池64,电动泵61、电机62、逆变器63与电池64依次电性连接并形成回路。在本实施例中,电动泵采用单级氧化剂离心泵即过氧化氢泵,具有低成本、系统简单、贮箱压力低、结构质量轻、可变推力范围大、工作模式灵活、适应总体赋形设计等优势。其中,电动泵主要设计参数如下表所示:参数数值参数数值工质98%过氧化氢入口压力0.3mpa密度1440kg/m3出口压力7.5mpa温度298k流量17.7kg/s计算参数值计算参数值体积流量0.0121m3/s转速35000rpm扬程474.53m比转速138.52容积效率0.98机械效率0.96水力效率0.82总效率0.77泵功率115.21kw最小轴径6mm见图1、图2,两个电动泵组件6沿气瓶5的轴线成对称设置,气瓶5与机壳1成同轴设置。两个电动泵组件沿气瓶的轴线成对称设置,气瓶与机壳成同轴设置,即两个电动泵在对称布置于高压气瓶两侧的同时还沿机壳的轴线成对称布置,结构更为合理,减小了发动机重心偏心,提高了电动泵的抽吸性能。见图1,机壳1包括依次连接的第一段机壳11、第二段机壳12和第三段机壳13,贮箱2设于第一段机壳11内,气瓶5和电动泵组件6设于第二段机壳12内,推力室3设于第三段机壳13内。本实施例中,机壳的设置,主要是完成发动机部件之间的连接,同时为发动机各个部件的布置提供空间。本发明还可以在机壳内部设置加强筋,以提高机壳的刚性。需要指出的是,本实施例中,机壳为圆柱形,但是,机壳也可以采用锥台的形式,内部结构同样采用四根加强筋的形式,其中,为使直径变化较缓慢,可以采用多段的形式或者采用小锥度的锥面适当延长长度。见图1、图2,机壳1为圆柱形,且第一段机壳11、第二段机壳12和第三段机壳13的外径为相同设置,其中,第二段机壳12为铝蜂窝夹芯板或者泡沫铝夹芯板制成的。第二段机壳为铝蜂窝夹芯板或者泡沫铝夹芯板制成的,由于第二段机壳的设置,是为了给气瓶和电动泵的布置提供空间,故为了减轻重量,可以将第二段的管壁设置为薄壁中空结构,并在中间填充铝蜂窝夹层或者泡沫铝。同时第二段机壳为铝蜂窝夹芯板或者泡沫铝夹芯板制成的,使得本发明可以在保证强度和刚度的前提下,通过较轻的质量能够完成支撑全箭及有效载荷的全部质量和风载引起的载荷即弯矩的联合作用。见图1、图2,第二段机壳12的管壁上均匀分布有两个或两个以上的通孔121,电动泵组件6通过连接杆65固定在第二段机壳12的内壁上。第二段机壳是采用桁条式结构,通过各桁条之间的间隔形成多个通孔,可以保证强度和刚度的前提下,大幅度减轻重量,减少了耗费能源,提高本发明的机动性和续航能力。连接杆的设置,可以缓冲振动,减少机壳对电动泵组件的影响。见图2、图3,推力室3包括燃烧室外壳31和固体装药33,燃烧室外壳31内壁上包覆有绝热层32,固体装药33设于外壳内且与摆动喷管434连接,固体装药33为圆柱形,且固体装药33径向截面为无中心孔的车轮状。本发明固体装药内型面采用无中心孔的四孔车轮形装药形式,使得药型燃面比有中心孔的的固体装药大,提高了推力。需要指出的是,在固体装药外侧还可以包覆厚度为1mm的绝热层,以提高绝热效果。需要说明的是,在本实施例中,燃烧室总长为1980mm,总质量为854kg左右。燃烧室外壳采用碳纤维复合材料,燃烧室外壳直径为1100mm,壁厚为3.5mm。在壳体内壁面包覆有绝热层,绝热层材料为三元乙丙橡胶。本实施例根据三元乙丙橡胶的烧蚀速度和壳体各处在燃气中的暴露时间,确定了绝热层厚度,其中前、后燃室的绝热层厚度为11.6mm,包覆药柱处的绝热层厚度为1mm。固体装药部分,本实施例药柱长度为1105mm,装药质量为630.7kg左右,固体燃料装药配方为60%htpb+28%al+10%mg+2%c。其中,燃烧室主要设计参数如下表所示:见图2、图3,燃烧室外壳31一端与摆动喷管434连接,另一端上连接有顶盖34,顶盖34包括顶盖本体341,顶盖本体341上设有能与燃烧室外壳31相抵的凸缘342,顶盖本体341的中心位置上凸设有凸起部343,凸起部343的上表面上设有氧化剂均流板344,氧化剂均流板344上设有盖板345,凸起部343的下表面上设有催化床346,且顶盖本体341下表面除凸起部343之外覆盖有顶盖绝热层347。顶盖与燃烧室外壳通过焊接连接,凸缘的设置,方便焊接。催化床采用分解效率高和耐受98%过氧化氢的银网催化床,设置在顶盖的凸起部,并位于氧化剂均流板的下方,通过氧化剂均流板使得氧化剂均匀流入催化床,再进入燃烧室参与燃烧。其中,氧化剂采用过氧化氢。需要说明的是,本实施例中催化床主要设计参数如下表所示:参数单位设计参数氧化剂流量kg/s17.7催化床床载g/(cm2s)20催化银网直径mm336催化床预估质量kg21.3见图2、图4,摆动喷管434包括依次连接的连接部41、喉部42和喷管43,其中,连接部41伸入燃烧室外壳31,并与燃烧室外壳31螺纹连接,喷管43为锥形,且喷管43包括由外至内依次设置的外表面层431和隔热层432,喉部42包括喉衬421和收敛段422,收敛段422的顶端与连接部41相连,尾端与喉衬421相连,且收敛段422由顶端至尾端的内径依次减小,且喉衬421与喷管43相连。需要说明的是,本实施例中,喷管为锥形,摆动喷管的外表面层采用复合材料,摆动喷管的隔热层采用碳布/高硅氧布/酚醛树脂复合缠绕,喉部的收敛段采用模压碳纤维材料,喉衬采用t705高强石墨材料和钨渗铜,其中,喉衬背壁采用5-ii材料,其中,摆动喷管主要设计参数如下表所示。参数单位数值喷管总长mm1500喉径mm95收敛半角°45扩张半角°15扩张比80见图6,高压气瓶5通过第一管道7与贮箱2相连,贮箱2通过第二管道8与电动泵组件6相连,电动泵组件6通过第三管道9与推力室3相连,第一管道7上分别安装有气体充气阀71、气瓶泄压阀72、减压器73、电爆阀74和贮箱加注泄气阀75;第二管道8上分别安装有贮箱加注泄出阀81、膜片阀82和泵前阀83;第三管道9上分别安装有气蚀文氏管91和泵后阀92。实际使用过程,发动机开机前将98%过氧化氢贮存在贮箱中,各阀门关闭。开机指令下达后,气瓶出口第一管道上的各个阀门打开,氮气进入过氧化氢贮箱增压。之后贮箱第二管道上各个阀门打开,过氧化氢进入电动泵。同时电机启动带动电动泵起转,过氧化氢经过电动泵增压后进入第三管道上的气蚀文氏管以保证流量和压力的稳定,再通过催化床进入燃烧室参与燃烧。过氧化氢与固体装药燃烧产生燃气,通过喷管中的流动产生需要的推力。喷管处的作动机构能够控制喷管方向,从而调节推力的方向,达到矢量控制的目的。故本发明具有可变推力范围大、工作模式灵活、适应总体赋形设计等优势。最后应说明的是:以上各实施例仅用以说明本发明的技术方案,而非对其限制;尽管参照前述各实施例对本发明进行了详细的说明,本领域的普通技术人员应当理解:其依然可以对前述各实施例所记载的技术方案进行修改,或者对其中部分或者全部技术特征进行等同替换;而这些修改或者替换,并不使相应技术方案的本质脱离本发明各实施例技术方案的范围。当前第1页12