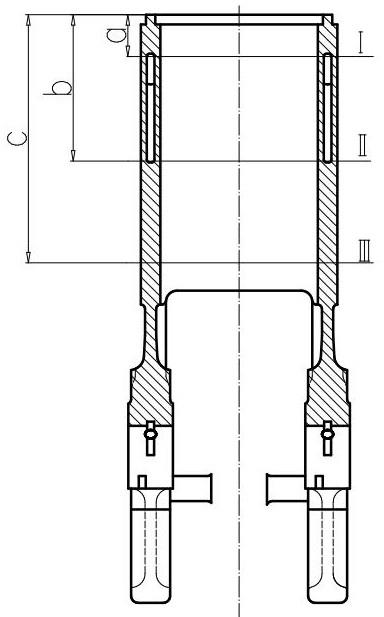
1.本发明属于发动机领域,涉及一种降低发动机漏气量的试验方法。
背景技术:2.众所周知,发动机在工作过程中,燃料燃烧产生的高温、高压燃气会通过活塞环、活塞与气缸套之间的间隙进入曲轴箱,不仅会降低发动机有效功率的输出,也会增加机油的消耗;高温、高压燃气还会使曲轴箱内的机油温度进一步升高,机油的粘度下降,性能恶化,以至于影响发动机的正常工作。发动机在工作过程中,虽然活塞、活塞环和气缸套组成了燃气下窜的防漏系统,起到一定的密封作用,但是,如何有效地降低发动机漏气量仍然是发动机行业亟待解决的难题之一。
3.目前,通常采用的减少发动机漏气量的方法,主要集中在活塞或活塞环的优化改进方面。现有技术中对该领域的研究不乏其例,例如:国家知识产权局2016.09.07授权的实用新型专利:一种多功能活塞环组结构,申请号: cn201620008816.3,申请日: 2016.01.06,公告号: cn205559096u,公告日: 2016.09.07 。该专利提出了一种多功能活塞环组结构,通过双梯形活塞环设计,增加排积碳能力,防止活塞环颤振,增强密封,降低漏气量。其中,第一道活塞环、第二道活塞环均采用梯形结构,第一道活塞环为梯形桶面环,第二道活塞环为梯形锥面环;分别与第一道活塞环和第二道活塞环配合的第一活塞环槽和第二活塞环槽之间设置有泄压槽,以降低第一道活塞环下侧气体压力,降低第一道活塞环悬浮的风险。
4.国家知识产权局2009.10.07授权的实用新型专利:一种减少漏气量的发动机活塞,申请号:cn200820113564.6,申请日: 2008.11.12,公告号:cn201321911y,公告日: 2009.10.07。该专利提出了一种减少漏气量的发动机活塞,包括至少两道活塞环槽,相邻两道活塞环槽之间设置有一道减压密封槽,减压密封槽容积大于活塞环槽的容积,减压密封槽可根据需要做成半圆形或方形结构。
5.通过以上分析,不难发现上述两个专利的技术方案有以下不足:其一,为降低发动机漏气量,如果单一地从活塞或者活塞环角度进行改进,没有考虑到发动机缸套变形对活塞漏气量的影响,方案设计仍然不够全面;其二,在活塞的活塞环槽之间设置泄压槽结构,一定程度上会增大活塞的加工难度,降低活塞的整体强度,不利于活塞在高温、高压的环境下正常工作。
6.基于上述原因,我们从多次试验中筛选出一种降低发动机漏气量的方法,经过反复试验验证,取得了明显的效果。
技术实现要素:7.本发明的目的在于提出一种全面、有效的降低发动机漏气量的方法,按照该方法能行之有效地降低发动机漏气量。
8.本发明提出的降低发动机漏气量方法主要涉及:活塞、活塞环、缸体三个方面。
9.一、活塞方面:由于活塞结构设计方面的原因,一些发动机的燃烧室中心相对于气缸孔中心有一定偏移,在膨胀冲程初期,高压气体作用在活塞顶面的力并不均匀,会形成一个相对于活塞中心的偏心力,该偏心力能够使活塞翻转,在上止点活塞换向时敲击气缸,引起气缸套和活塞的振动,使得活塞环与缸套和环槽的配合受到影响,加大发动机漏气量。因此,要减少活塞对缸套的敲击,活塞型线和头部尺寸要设计合理,活塞配缸间隙不能过大。
10.二、活塞环方面:活塞环组件包括气环和油环,气环主要作用是保证气缸和活塞间的密封性,防止漏气;油环主要起布油和刮油作用。依据实践经验,活塞环断面为梯形结构除积炭效果好;活塞环断面为桶面结构有利于润滑油进入摩擦面,减少磨损;活塞环断面为锥面结构,由于减少了环与气缸壁的接触面,提高了表面接触压力,有利于磨合和密封;活塞环断面为正(反)扭曲结构,使得活塞环对气缸表面的适应性更好。
11.三、缸体方面:发动机工作过程中,控制缸孔及气缸套的变形量对减少发动机漏气量十分重要,如何在高温、高压燃气的冲击下,减少气缸套及缸孔的整体变形,非常有意义。通过取消传统气缸套的使用,让特殊珩磨后的缸孔本身起到气缸套的作用;这样消除了因气缸套装入缸孔后,产生的整体变形对发动机漏气量的不利影响。另外,取消气缸套的使用,缸孔加工时不再需要保留气缸套安装余量,在一定程度上增加了缸孔的厚度,正向减少了缸孔的变形量,对降低发动机漏气量是有利的。
12.基于以上分析,对发动机的活塞、活塞环、缸体的结构进行优化设计,对于降低发动机漏气量是有成效的。具体方法如下:【1】首先,分别对活塞最外圆尺寸和缸套内圆尺寸公差值进行平均等分,分别定义为a组公差值和b组公差值;【2】然后,装配前对活塞和缸套进行测量,依据测量值分别归为a组、b组,分类存放;【3】活塞环第一道气环为“梯形+桶面+正扭曲”结构、活塞环第二道气环“锥面+反扭曲”结构;【4】最后,装配时将a组活塞装入a组缸套内,b组活塞装入b组缸套内;通过活塞分组装配,能够使得活塞和缸套的配合最优化,满足配缸间隙要求;配缸间隙设计值:0.108~0.127;【5】直接在缸体内壁珩磨气缸套网纹,相关网纹参数满足行业标准。
13.本发明采用上述方法后取得的有益效果是:方法主要涉及:活塞、活塞环、缸体三个方面,活塞的装配旨在控制活塞配缸间隙,同步给出一个配缸间隙设计值,该值是通过试验验证得出。将活塞环第一道气环设计为“梯形+桶面+正扭曲”结构、活塞环第二道气环“锥面+反扭曲”结构;取消传统气缸套的使用,直接在缸体内壁珩磨气缸套网纹,让特殊珩磨后的缸孔本身起到气缸套的作用;采用上述方法通过对某型号发动机的验证,发动机转速在2200r/min时,发动机漏气量为75l/min,较改进前的96l/min,降幅达21%,效果明显。
附图说明
14.图1为本发明一种降低发动机漏气量的试验方法的缸孔测量位置示意图;图2为图1的俯视结构示意图;图3为本发明的发动机第一道活塞环断面结构示意图;图4为本发明的发动机第二道活塞环断面结构示意图。
具体实施方式
15.下面结合附图及实施例对本发明做进一步描述。
16.1、按照本发明提出的改进方法,在某款四缸发动机缸孔内壁直接按照行业标准珩磨网纹,取消传统气缸套的使用,让特殊珩磨后的缸孔本身起到气缸套的作用,网纹参数要满足行业标准要求。珩磨工艺完成后,使用专业设备进行检测,得出网纹检测数据,缸体加工完成后,对缸孔内圆尺寸进行测量,依据测量值将缸孔公差值归为a组或者b组,图1~2为缸孔测量位置示意图,测量位置分为ⅰ段、ⅱ段、ⅲ段,测量尺寸a为30mm,b为105mm,c为178mm,实际测量值见表1。
17.表1:发动机缸孔尺寸检测数据,单位:mm(基础尺寸
∅
110,表中只列出小数点后数值)本实施例中的某款发动机,成品缸孔尺寸为:
∅
110~
∅
110.015 mm,定义a组尺寸为
∅
110~
∅
110.007 mm,b组尺寸为
∅
110.007~
∅
110.015 mm;与缸套配套的活塞最外圆尺寸为:
∅
109.89
±
0.009 mm,定义a组尺寸为
∅
109.881~
∅
109.89 mm,b组尺寸为
∅
109.89~
∅
109.899 mm;发动机装配时,按照a组活塞配合a组缸套,b组活塞配合b组缸套的方法装配发动机,最终使得活塞配缸间隙达到设计值0.108~0.127。
18.2、如图3所示,按照本发明提出的改进方法,将活塞环第一道气环设计为双梯形桶面正扭曲结构,能同时兼顾活塞环的密封及排除积碳能力,适应性更好;如图4所示,活塞环第二道气环设计为锥面反扭曲结构,提升了活塞环组刮油能力,密封和润滑性能更好。
19.上述方法主要从活塞、活塞环、缸体三个方面入手,活塞在于控制活。