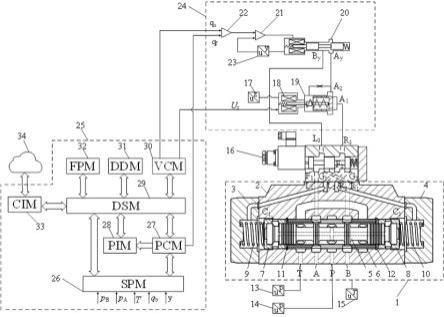
1.本发明涉及一种液压控制阀,具体是一种流量检测与高精智能控制一体化的电液比例流量方向连续控制阀。
背景技术:2.流量阀是作为液压传动的核心控制元件,广泛应用于各类重大装备,是实现各类重大装备自动化、智能化的关键,其核心功能是阀口流量高精度控制。现有流量阀控制流量的方式为:在比例节流阀的主流道设置压差补偿器,维持主阀进出油口两端压差基本恒定,油液要经过主阀和压差补偿器二次节流,增大了阀的节流损失并减小了阀的通流能力,并且补偿器补偿精度受稳态液动力影响,这种类型阀的压差损失大,动态流量超调大。
3.降低液压系统能耗和实现流量的闭环控制离不开流量的测量。理论上,若存在类似于压力传感器这样安装方便、能够高精度高动态检测流量的传感器,通过闭环控制流量即可高精度,且不受负载压力变化,但现有流量传感器难以精确测量流量,且只能测得静态流量,不能实时感知流量;流量传感器使用时需要串联在管路中,损失大、成本高、操作难。在流量闭环控制时,一旦有传感器失效,整个系统将不能继续工作。
4.现有电液比例阀智能化程度低,不具备对负载、环境以及自身变化的自学习自适应能力,且不能对阀的健康状况进行预测和故障诊断,都是事故后维修,导致安全事故和经济损失。此外,未利用历史融合数据进行分析、计算、比较、决策,使得资源浪费,阀的控制精度低。
技术实现要素:5.为解决现有技术存在的上述问题,本发明提供了一种电液比例流量方向连续控制阀,先导流量闭环控制单元既可以测量流量又可以闭环控制流量,并通过主阀流量放大的原理对先导闭环控制单元的小流量放大,不需要在主阀上安装压差补偿器;多功能控制器可以计量流量、能量、功率、温度等数据,构建阀的流量孪生模型;对数据进行显示、存储、分析、联想、判断,通过通讯模块上传至云端存储器,实现对阀的参数配置、寿命预测、故障诊断、自学习自适应等功能;即便传感器失效,多功能控制器也能冗余控制,保证阀的继续工作,以解决背景技术中的提出的问题。
6.本发明采用如下技术方案:一种电液比例流量方向连续控制阀,包括:主阀1,其特征在于,进一步增设了第ⅰ压力传感器13、第ⅱ压力传感器14、温度传感器15、先导闭环流量控制单元、多功能控制器25、云端存储器34;所述主阀1包括:主阀体2、第ⅰ端盖3、第ⅱ端盖4、主阀芯5、定阀套6、第ⅰ动阀套7、第ⅱ动阀套8、第ⅰ弹簧9、第ⅱ弹簧10、第ⅰ孔用弹性卡圈11、第ⅱ孔用弹性卡圈12、主阀出油口t、主阀左腔工作油口a、主阀右腔工作油口b、主阀进油口p、主阀左腔进油口l1、主阀左腔出油口l2、主阀右腔进油口r1、主阀右腔出油口r2、主阀左腔节流槽c1、主阀右腔节流槽c2;第
ⅰ
压力传感器13与主阀出油口t连接,输出主阀出口腔压力pb,第ⅱ压力传感器14与主阀进油口p连接,输出主阀进口腔压力pa,温度传感器15与主阀1连接,输出主阀出口腔温度t;所述先导闭环流量控制单元包括:流量传感器19和比例先导阀20;比例先导阀20包括:比例先导阀进油口ay、比例先导阀出油口by,匹配设置有先导阀比例放大器21、流量控制器22、第ⅱ位移传感器23;流量传感器进油口、比例先导阀出油口可切换的分别连接主阀左腔出油口l2与主阀左腔进油口l1/主阀右腔出油口r2与主阀右腔进油口r1,流量传感器出油口a2与比例先导阀进油口ay连通;所述先导阀比例放大器21输出端连接比例先导阀电磁铁,流量控制器22接收流量设定信号qs和流量反馈信号qf,流量控制器22输出端连接到先导阀比例放大器21的输入端,第ⅱ位移传感器23检测比例先导阀20的阀芯位移,输出先导阀位移信号y到先导阀比例放大器21反馈端;所述多功能控制器25包括:信号处理模块26、计算模块27、积分模块28、数据存储模块29、控制模块30、显示模块31、故障预测模块32、通讯模块33;所述信号处理模块26接收比例先导阀芯位移信号y、主阀进口腔压力pa、主阀出口腔压力pb、流量传感器信号qb、温度传感器信号t;信号处理模块对上述信号滤波和归一化处理后,经过信号处理模块的输出端输入到计算模块27和数据存储模块29的输入端;所述计算模块27计算出的主阀流量q、流量反馈信号qf、主阀进出口压差
∆
p、主阀输入功率p1、主阀输出功率p2、主阀节流损失功率p3并将其计算出的结果输入到积分模块28输入端和数据存储模块29;计算模块27将计算出的流量反馈信号qf输入到流量控制器22反馈端;所述积分模块28计算出主阀输入能量e1、主阀输出能量e2、主阀节流损失能耗e3、主阀效率η输入到数据存储模块29,数据存储模块29经过双向数据总线与控制模块30、显示模块31、故障预测模块32、通讯交互模块33连接;所述控制模块30计算出流量设定信号qs,流量设定信号qs连接到流量控制器22的输入端;控制模块30计算出流量传感器补偿信号uz输入到电-机械转换器18。
7.所述的一种电液比例流量方向连续控制阀,其特征在于,所述流量传感器19为插装式结构、滑阀式的节流型传感器,或涡轮形式的耐高压流量传感器。
8.所述的一种电液比例流量方向连续控制阀,其特征在于,所述流量传感器19为插装式结构,所述流量传感器包括有:流量传感器进油口a1、流量传感器出油口a2,进一步增设了第ⅰ位移传感器17和电—机械转换器18;所述电-机械转换器18输入端连接控制模块30,控制模块30计算出流量传感器补偿信号uz输入到电-机械转换器18,电-机械转换器18输出力作用到流量传感器阀芯断面。
9.所述的一种电液比例流量方向连续控制阀,其特征在于,所述流量传感器19为滑阀式结构,所述流量传感器包括有:滑阀阀套36、滑阀阀芯37、液阻38、第ⅲ位移传感器39、第ⅱ电-机械转换器40、滑阀式流量传感器进油口k、滑阀式流量传感器出油口j、流量传感器左端容腔u、流量传感器右端容腔w;所述滑阀阀芯37、第ⅲ位移传感器39、第ⅱ电-机械转换器40同轴连接,第ⅱ电机械转换器输出力作用在滑阀芯右端面,流量传感器出油口j经液阻38与流量传感器右端容腔w连通,流量传感器左端容腔u与流量传感器进口k连通;控制模
块30计算出流量传感器补偿信号uz输入到第ⅱ电-机械转换器40。
10.所述的一种电液比例流量方向连续控制阀,其特征在于,所述计算模块27根据运算公式(1)、公式(2)、公式(3)、公式(4)、公式(5)、公式(6)计算出如下参数:主阀流量q=(g(x)+1)
·
qb(1)主阀进出口压差δp=p
a-pb(2)主阀输入功率p1=pa·
q(3)主阀输出功率p2=pb·
q(4)主阀节流损失功率p3=δp
·
q(5) 流量反馈信号qf=k
·
qb(6);式中,g(x)—流量放大系数、qb—流量传感器信号、pa—主阀进口腔压力、pb—主阀出口腔压力、k—流量反馈增益。
11.所述的一种电液比例流量方向连续控制阀,其特征在于,所述积分模块28通过公式(7)、公式(8)、公式(9)、公式(10)积分计算得到如下参数:主阀输入能量(7)主阀输出能量(8)主节流损失能耗(9)主阀效率(10)。
12.所述的一种电液比例流量方向连续控制阀,其特征在于,所述故障预测模块32根据存储的主阀输入功率p1、主阀输入能量e1、主阀进口腔压力pa、主阀出口腔压力pb等信号对集成单元主动运维和故障诊断,一旦累计能量达到故障报警阈值gy,系统将主动进行检测维护,利用专家知识和专家库,完成从故障特征到故障原因的识别工作,准确给出故障定位、解析故障诊断结果,进行阀的寿命预测。
13.所述的一种电液比例流量方向连续控制阀,其特征在于,所述通讯交互模块33为以太网、工业互联网或蓝牙,将数据存储模块29存储数据传输到云端存储器34,也可以读取云端存储器存储的数据信息。
14.所述的电液比例流量方向连续控制阀,其特征在于,所述先导闭环流量控制单元数量为一组,即第一先导闭环流量控制单元24;所述主阀1匹配有电磁换向阀16,所述电磁换向阀16包括:电磁换向阀左位出油口f1、电磁换向阀左位进油口f2、电磁换向阀右位出油口g1、电磁换向阀右位进油口g2、电磁换向阀进油口l3、电磁换向阀出油口r3;主阀左腔进油口l1与电磁换向阀左位出油口f1连通,主阀左腔出油口l2与电磁换向阀左位进油口f2连通,主阀右腔进油口r1与电磁换向阀右位出油口g1连通,主阀右腔出油口r2与电磁换向阀右位进油口g2连通;流量传感器进油口a1与电磁换向阀出油口r3连通,流量传感器出油口a2与比例先导阀进油口ay连通,比例先导阀出油口by与电磁换向阀进油口l3连通。
15.所述的电液比例流量方向连续控制阀,其特征在于,所述先导闭环流量控制单元数量为两组,即第一先导闭环流量控制单元24和第二先导闭环流量控制单元35;
所述第一先导闭环流量控制单元24、第二先导闭环流量控制单元35对称布置,通过将主阀两腔流量引入各自对应的先导闭环流量控制单元,实现主阀流量检测和连续控制,具体为,所述第一先导闭环流量控制单元24的流量传感器进油口a1与主阀左腔出油口l2连通,流量传感器出油口 a2与比例先导阀进油口ay连通,比例先导阀出油口by与主阀左腔进油口l1连通;所述第二先导闭环流量控制单元35的流量传感器进油口b1与主阀右腔出油口r2连通,流量传感器出油口b2与比例先导阀进油口cy连通,比例先导阀出油口dy与主阀右腔进油口r1连通。
16.本发明具有以下有益效果:(1)本发明无需在液压系统主油路中安装流量传感器即可高精度检测和控制执行器流量,解决了现有流量传感器无法闭环控制流量、成本高、不易安装、压损大等问题,流量控制阀兼有流量传感器功能,实现了流量检测与控制一体化。
17.(2)本发明无需压力补偿器,通过闭环控制先导阀流量,经过主阀放大,即可不受负载变化影响连续控制主阀流量,控制精度高、压力损失小;(3)本发明可实时监测液压系统中各部分流量、功率、能量、效率等信息,并可以实时显示存储和上传云端存储器,而在现有液压系统中不方便获得功率和能量信息,为进一步优化系统能效奠定了基础,即使传感器失效,也能通过多功能控制器对系统进行冗余控制。
18.(4)本发明通过对功率和能量信息的实时监测与分析,可以对所述控制阀生命周期进行主动运维和故障诊断,实现对控制阀关键元件状态监控、寿命预测及故障定位。
附图说明
19.为了更清楚地说明本发明实施例或现有技术中的技术方案,下面将对实施例中所需要使用的附图作简单地介绍,显而易见地,下面描述中的附图仅仅是本发明的一些实施例,对于本领域普通技术人员来讲,在不付出创造性劳动性的前提下,还可以根据这些附图获得其他的附图。
20.图1为电液比例流量方向连续控制阀实施例一的结构示意图;图2为电液比例流量方向连续控制阀实施例二的结构示意图;图3为本发明提供的电液比例流量方向连续控制阀工作流程图;图4为本发明实施例所采用的滑阀式流量传感器结构原理图。
21.图中,1—主阀、2—主阀体、3—第ⅰ端盖、4—第ⅱ端盖、5—主阀芯、6—定阀套、7—第ⅰ动阀套、8—第ⅱ动阀套、9—第ⅰ弹簧、10—第ⅱ弹簧、11—第ⅰ孔用弹性卡圈、12—第ⅱ孔用弹性卡圈、13—第ⅰ压力传感器、14—第ⅱ压力传感器、15—温度传感器、16—电磁换向阀、17—第ⅰ位移传感器、18—电—机械转换器、19—流量传感器、20—比例先导阀、21—先导阀比例放大器、22—流量控制器、 23—第ⅱ位移传感器、24—第一先导闭环流量控制单元、25—多功能控制器、26—信号处理模块、27—数据计算模块、28—积分模块、29—存储模块、30—控制模块、31—显示模块、32—故障预测模块、33—通讯交互模块、34—云端存储器、35—第二先导闭环流量控制单元、36—滑阀阀套、37—滑阀阀芯、38—液阻、39—第ⅲ位移传感器、40—第ⅱ电-机械转换器。
22.a—主阀左腔工作油口、a1—流量传感器进油口、a2—流量传感器出油口、ay—比例
先导阀进油口、by—比例先导阀出油口、b—主阀右腔工作油口、c1—主阀左腔节流槽、c2—主阀右腔节流槽、f1—电磁换向阀左位出油口、f2—电磁换向阀左位进油口、g1—电磁换向阀右位出油口、g2—电磁换向阀右位进油口、l1—主阀左腔进油口、l2—主阀左腔出油口、l3—电磁换向阀进油口、j—滑阀式流量传感器出油口、k—滑阀式流量传感器进油口、p—主阀进油口、r1—主阀右腔进油口、r2—主阀右腔出油口、r3—电磁换向阀出油口、u—流量传感器左端容腔、w—流量传感器右端容腔、t—主阀出油口。
具体实施方式
23.下面将结合本发明实施例中的附图,对本发明实施例中的技术方案进行清楚、完整地描述,显然,所描述的实施例仅仅是本发明一部分实施例,而不是全部的实施例。基于本发明中的实施例,本领域普通技术人员在没有做出创造性劳动前提下所获得的所有其他实施例,都属于本发明保护的范围。
24.为使本发明的上述目的、特征和优点能够更加明显易懂,下面结合附图和具体实施方式对本发明作进一步详细的说明。
25.说明书中各参数含义:pa—主阀进口腔压力、pb—主阀出口腔压力、t—主阀出口腔温度、qb—流量传感器信号、qf—反馈流量信号、qs—设定流量信号、uc—电—机械转换器控制信号、y—先导阀位移信号、g(x)—流量放大系数、q—主阀流量、
∆
p—主阀进出口压差、p1—主阀输入功率、p2—主阀输出功率、p3—主阀节流损失功率、e1—主阀输入能量、e2—主阀输出能量、e3—主阀节流损失能耗、η—主阀效率、gy—故障报警阈值、k—流量反馈增益、uz—流量传感器补偿信号。
26.实施例一:如图1所示,一种电液比例流量方向连续控制阀,包括:主阀1、电磁换向阀16,进一步增设了第ⅰ压力传感器13、第ⅱ压力传感器14、温度传感器15、第一先导闭环流量控制单元24、多功能控制器25、云端存储器34。
27.主阀1包括:主阀体2、第ⅰ端盖3、第ⅱ端盖4、主阀芯5、定阀套6、第ⅰ动阀套7、第ⅱ动阀套8、第ⅰ弹簧9、第ⅱ弹簧10、第ⅰ孔用弹性卡圈11、第ⅱ孔用弹性卡圈12、主阀出油口t、主阀左腔工作油口a、主阀右腔工作油口b、主阀进油口p、主阀左腔进油口l1、主阀左腔出油口l2、主阀右腔进油口r1、主阀右腔出油口r2、主阀左腔节流槽c1、主阀右腔节流槽c2;第ⅰ压力传感器13与主阀出油口t连接,输出主阀出口腔压力pb,第ⅱ压力传感器14与主阀进油口p连接,输出主阀进口腔压力pa,温度传感器15与主阀1连接,检测并输出主阀出口腔温度t。
28.电磁换向阀16包括:电磁换向阀左位出油口f1、电磁换向阀左位进油口f2、电磁换向阀右位出油口g1、电磁换向阀右位进油口g2、电磁换向阀进油口l3、电磁换向阀出油口r3;主阀1的左腔进油口l1与电磁换向阀左位出油口f1连通,主阀左腔出油口l2与电磁换向阀左位进油口f2连通,主阀右腔进油口r1与电磁换向阀右位出油口g1连通,主阀右腔出油口r2与电磁换向阀右位进油口g2连通。
29.第一先导闭环流量控制单元24包括:流量传感器19、比例先导阀20、先导阀比例放大器21、流量控制器22、第ⅱ位移传感器23。流量传感器19设置有流量传感器进油口a1和流量传感器出油口a2。比例先导阀20设置有比例先导阀进油口ay、比例先导阀出油口by。流量
传感器进油口a1与电磁换向阀出油口r3连通,流量传感器出油口a2与比例先导阀进油口ay连通,比例先导阀出油口by与电磁换向阀进油口l3连通。
30.先导阀比例放大器21输出端连接比例先导阀电磁铁,流量控制器22接收流量设定信号qs和流量反馈信号qf,流量控制器22输出端连接到先导阀比例放大器21的输入端,第ⅱ位移传感器23检测比例先导阀20的阀芯位移,输出先导阀位移信号y到先导阀比例放大器21反馈端。
31.多功能控制器25包括:信号处理模块26、计算模块27、积分模块28、数据存储模块29、控制模块30、显示模块31、故障预测模块32、通讯模块33。
32.信号处理模块26接收比例先导阀芯位移信号y、主阀进口腔压力pa、主阀出口腔压力pb、流量传感器信号qb、温度传感器信号t;信号处理模块对上述信号滤波和归一化处理后,经过信号处理模块的输出端输入到计算模块27和数据存储模块29的输入端。
33.计算模块27将计算出的主阀流量q、流量反馈信号qf、主阀进出口压差
∆
p、主阀输入功率p1、主阀输出功率p2、主阀节流损失功率p3输入到积分模块28输入端和数据存储模块29;计算模块27将计算出的流量反馈信号qf输入到流量控制器22反馈端。
34.积分模块28计算出主阀输入能量e1、主阀输出能量e2、主阀节流损失能耗e3、主阀效率η输入到数据存储模块29,数据存储模块29经过双向数据总线与控制模块30、显示模块31、故障预测模块32、通讯交互模块33连接。
35.所述控制模块30计算出流量设定信号qs,流量设定信号qs连接到流量控制器22的输入端;控制模块30计算出流量传感器补偿信号uz输入到电-机械转换器18。
36.流量传感器19可以是插装式结构、滑阀式的节流型传感器,也可以是涡轮等形式的耐高压流量传感器。
37.当流量传感器为插装式结构,流量传感器包括有:流量传感器进油口a1、流量传感器出油口a2,进一步增设了第ⅰ位移传感器17和电—机械转换器18;电-机械转换器18输入端连接控制模块30,控制模块30计算出流量传感器补偿信号uz输入到电-机械转换器18,电-机械转换器18输出力作用到流量传感器阀芯断面。
38.如图4所示,当流量传感器为滑阀式,流量传感器包括有:滑阀阀套36、滑阀阀芯37、液阻38、第ⅲ位移传感器39、第ⅱ电-机械转换器40、滑阀式流量传感器进油口k、滑阀式流量传感器出油口j、流量传感器左端容腔u、流量传感器右端容腔w;滑阀阀芯37、第ⅲ位移传感器39、第ⅱ电-机械转换器40同轴连接,第ⅱ电机械转换器输出力作用在滑阀芯右端面,流量传感器出油口j经液阻38与流量传感器右端容腔w连通,流量传感器左端容腔u与流量传感器进口k连通;控制模块30计算出流量传感器补偿信号uz输入到第ⅱ电-机械转换器40。
39.电-机械转换器18、第ⅱ电-机械转换器40可以是单向输出力,也可以是双向输出力。
40.计算模块27根据运算公式(1)、公式(2)、公式(3)、公式(4)、公式(5)、公式(6)计算出如下参数:主阀流量q=(g(x)+1)
·
qb(1)主阀进出口压差δp=p
a-pb(2)主阀输入功率p1=pa·
q(3)
主阀输出功率p2=pb·
q(4)主阀节流损失功率p3=δp
·
q(5) 流量反馈信号qf=k
·
qb(6)。
41.积分模块28通过公式(7)、公式(8)、公式(9)、公式(10)积分计算得到如下参数:主阀输入能量(7)主阀输出能量(8)主节流损失能耗(9)主阀效率(10)。
42.显示模块31通过程序显示存储在数据存储模块29中的信息。
43.故障预测模块32根据存储的主阀输入功率p1、主阀输入能量e1、主阀进口腔压力pa、主阀出口腔压力pb等信号对集成单元主动运维和故障诊断,一旦累计能量达到故障报警阈值gy,系统将主动进行检测维护,利用专家知识和专家库,完成从故障特征到故障原因的识别工作,准确给出故障定位、解析故障诊断结果,同时可进行阀的寿命预测。
44.通讯交互模块33为以太网、工业互联网或蓝牙,将数据存储模块29存储数据传输到云端存储器34,接收存储在云端存储器的数据信息。
45.控制模块30对数据存储模块29中的全部数据进行分析、比较、判断、联想,不断的积累知识,构建阀的流量孪生模型,根据负载压力、油液温度的变化,设计基于工况识别的多控制模式切换策略,实现位移闭环控制、压力闭环控制、流量闭环控制模式,适应外部环境变化;并采用pid控制、模糊控制、神经网络、深度学习等算法,对流量孪生模型进行修正,实现电液比例流量方向连续控制阀的并行调控、状态监测、自学习自适应等功,即使所有传感器发生故障,控制模块30根据阀的运行规律和超前运行数据保证阀继续工作。
46.其中,本发明中采用的左、右、上、下是为了描述的清晰化相对于纸面显示位置而言,实际应用中不作为具体位置的限定。
47.基于此,本发明上述实施例中提供的电液比例流量方向连续控制阀开始工作时,若电磁换向阀16的电磁铁不得电,电磁换向阀阀芯在电磁换向阀复位弹簧力作用下处于左位,此时主阀左腔进油口l1和电磁换向阀进油口l3接通、主阀左腔出油口l2和电磁换向阀出油口r3接通;若第一先导闭环流量控制单元24中比例先导阀20无外加设定流量信号qs,比例先导阀20在比例先导阀复位弹簧的作用下处于关闭位置,无油液通过,使得电磁换向阀进油口l3和电磁换向阀出油口r3不连通。高压油液流入主阀进油口p油口,并通过主阀芯5内部流道流入两侧动阀套的内部容腔,再通过两侧动阀套上节流槽c
1 和c
2 流入两侧端盖与主阀体2组成的容腔内,由于电磁换向阀进油口l
3 和电磁换向阀出油口r
3 不连通,主阀芯5两端油液压力相等,均等于主阀进油口p油口压力,主阀芯5在两端油压作用下处于对中位置,主阀芯5不运动。
48.当进行流量控制时,控制模块30输出设定流量信号qs输入到流量控制器22,在流量控制器22中将其与计算模块27计算得到的反馈流量信号qf比较得到偏差值采用比例—积分—微分控制,闭环控制比例先导阀20的流量,使通过比例先导阀20的流量不随负载压
力变化而改变;先导流量控制器22的输出端连接先导阀比例放大器21,在先导阀比例放大器21中将其与第ⅱ位移传感器24检测的比例先导阀阀芯位移反馈值y比较得到偏差值,比例先导阀阀芯位移采用pd控制,其输出值输入到比例先导阀电磁铁,局部闭环控制先导阀阀芯的位移,使得比例先导阀20进油口ay和出油口by连通,控制比例先导阀20通过的流量,进而通过主阀流量放大原理控制主阀1通过的流量。
49.如想使主阀工作在左位,即电磁换向阀16的电磁铁不得电,电磁换向阀阀芯在电磁换向阀复位弹簧力作用下处于左位,此时主阀左腔进油口l
1 和电磁换向阀进油口l3接通、主阀左腔出油口l
2 和电磁换向阀出油口r3接通。此时主阀芯5左端容腔压力降低,而右端容腔压力不变,主阀芯5向左移动,同时带动第ⅰ动阀套7向左移动,而第ⅱ动阀套8由于机械限位,不会向左移动。主阀1左端容腔的油液经节流槽c1从电磁换向阀出油口r3流入流量传感器进油口a1,流量传感器出油口a2流出的油液流入比例先导阀进油口ay,比例先导阀出油口by排出的油液流入电磁换向阀进油口l3,流入主阀1的左腔工作油口a。同时通过定阀套6上的导流孔流入第ⅰ动阀套7和定阀套6左端面形成的环形容腔内,主阀的p-a油口接通、b-t油口接通,当流过第ⅰ动阀套7节流槽c
1 的流量和比例先导阀出油口by排出的流量相等时,主阀芯5不再移动。由此可知,只要控制比例先导阀20的开度,以及在不受负载变化影响地控制主阀1的左腔出油口l2排出的流量,即可实现主阀1流量不受负载变化影响地从p到a、从b到t的比例控制。
50.若想主阀1工作在右位,只需比例先导阀20在控制模块30设定流量信号qs作用下进出油口ay和by按上述操作连通,控制电磁换向阀电磁铁得电,推动电磁换向阀阀芯移动到右位,使主阀右腔出油口r
2 和电磁换向阀出油口r3接通、主阀右腔进油口r
1 和电磁换向阀进油口l3接通。此时主阀芯5右端容腔压力降低,而左端容腔压力不变,主阀芯5向右移动,同时带动第ⅱ动阀套8向左移动,而第ⅰ动阀套7由于机械限位,不会向右移动。主阀右端容腔的油液经节流槽c2由电磁换向阀出油口 r3油口流入流量传感器19的进油口a1,流量传感器出油口a2流出的油液流入比例先导阀进油口ay,比例先导阀出油口by排出的油液流入电磁换向阀进油口l3,流入主阀右腔工作油口b。同时通过定阀套6上的导流孔流入第ⅱ动阀套8和定阀套6右端面形成的环形容腔内,主阀的p-b油口接通、a-t油口接通,当流过第ⅱ动阀套8节流槽c
2 的流量和比例先导阀20的出油口by排出的流量相等时,主阀芯5不再移动。由此可知,只要控制比例先导阀20的开度,进而不受负载变化影响地控制主阀右腔出油口r2排出的流量,实现主阀1流量不受负载变化影响地从p到b、从a到t的比例控制。
51.如图3所示,当比例先导阀20中有流量通过时,信号处理模块26接收比例先导阀芯位移信号y、主阀进口腔压力pa、主阀出口腔压力pb、流量传感器信号qb、温度传感器信号t;对信号滤波和归一化处理,并将输出端连接计算模块27和数据存储模块29。
52.计算模块27将计算出的主阀流量q、流量反馈信号qf、主阀进出口压差
∆
p、主阀输入功率p1、主阀输出功率p2、主阀节流损失功率p3输入到积分模块28输入端和数据存储模块29;计算模块27将计算出的流量反馈信号qf输入到流量控制器22反馈端。
53.积分模块28计算出主阀输入能量e1、主阀输出能量e2、主阀节流损失能耗e3、主阀效率η输入到数据存储模块29,数据存储模块29经过双向数据总线与控制模块30、显示模块31、故障预测模块32、通讯交互模块33连接;所述显示模块31通过程序可以显示存储在数据存储模块29中的信息,包括实时显
示流量传感器信号qb、主阀进口腔压力pa、主阀出口腔压力pb、比例先导阀位移信号y、主阀出口腔温度t、主阀流量q、主阀输入功率p1、主阀输出功率p2、主阀节流损失功率p3、主阀输入能量e1、主阀输出能量e2、主阀节流损失能耗e3、主阀效率η等状态参数的动态信号曲线。
54.故障预测模块32根据存储的主阀输入功率p1、主阀输入能量e1、主阀进口腔压力pa、主阀出口腔压力pb等信号对集成单元主动运维和故障诊断,一旦累计能量达到故障报警阈值gy,系统将主动进行检测维护,利用专家知识和专家库,完成从故障特征到故障原因的识别工作,准确给出故障定位、解析故障诊断结果,同时可进行阀的寿命预测。
55.数据存储模块29存储的数据通过通讯交互模块33传输到云端存储器34,在云端存储器34中构建集的集阀实体运行数据、虚拟仿真数据、历史融合数据的大数据。
56.控制模块30对数据存储模块29中的全部数据进行分析、比较、判断、联想,不断的积累知识,构建阀的流量孪生模型,根据负载压力、油液温度的变化,设计基于工况识别的多控制模式切换策略,实现位移闭环控制、压力闭环控制、流量闭环控制模式,适应外部环境变化;并采用pid控制、模糊控制、神经网络、深度学习等算法,对流量孪生模型进行修正,实现电液比例流量方向连续控制阀的并行调控、状态监测、自学习自适应等功能,即使所有传感器发生故障,控制模块30可根据阀的运行规律和超前运行数据保证阀继续工作。
57.流量传感器精度会受到油液温度变化和液动力影响,通过温度传感器15测量主阀油液的温度,控制模块反馈补偿信号uz到电-机械转换器18,补偿流量和流量传感器阀芯位移z的非线性关系,减小温度和液动力对测量流量精度的影响。
58.实施例二如图2所示,一种电液比例流量方向连续控制阀,相较于实施例一,将电磁换向阀16去掉,增加一个相同且对称布置第二先导闭环流量控制单元35,第一先导闭环流量控制单元24和第二先导闭环流量控制单元35将主阀两腔流量引入各自对应的先导闭环流量控制单元,实现主阀流量检测和连续控制。
59.第一先导闭环流量控制单元24的流量传感器进油口a1与主阀左腔出油口l2连通,流量传感器出油口a2与比例先导阀进油口ay连通,比例先导阀出油口by与主阀左腔进油口l1连通;第二先导闭环流量控制单元35的流量传感器进油口b1与主阀右腔出油口r2连通,流量传感器出油口b2与比例先导阀进油口cy连通,比例先导阀出油口dy与主阀右腔进油口r1连通。
60.其中,本发明中采用的左、右、上、下是为了描述的清晰化相对于纸面显示位置而言,实际应用中不作为具体位置的限定。
61.如图2所示,基于此,本发明上述实施例中提供的电液比例流量方向连续控制阀开始工作时,若第一先导闭环流量控制单元24和第二先导闭环流量控制单元35中比例先导阀的电—机械转换器不得电,比例先导阀阀芯在比例先导阀复位弹簧的作用下处于初始位置,比例先导阀和流量传感器无流量通过。此时,高压油液进入主阀进油口p,并通过主阀芯5内部流道流入两侧动阀套的内部容腔,再通过两侧动阀套上节流槽c
1 和c
2 流入两侧端盖与主阀体2组成的容腔内,由于比例先导阀中无流量通过,主阀芯5两端油液压力相等,均等于主阀进油口p压力,主阀芯5在两端油压作用下处于对中位置,主阀芯5不运动。
62.当进行流量控制时,要想主阀工作于左位,此时第一先导闭环流量控制单元24工作,第二先导闭环流量控制单元35不工作。同理,若要想主阀工作于右位,此时流量控制系
统24不工作,第二流量控制系统35工作。主阀工作在左位和右位的两种情况下,主阀1、第一先导闭环流量控制单元24、第二先导闭环流量控制单元35的工作原理和动作与实时方式1相同,同时多功能控制器25进行与实施方式1相同的操作。