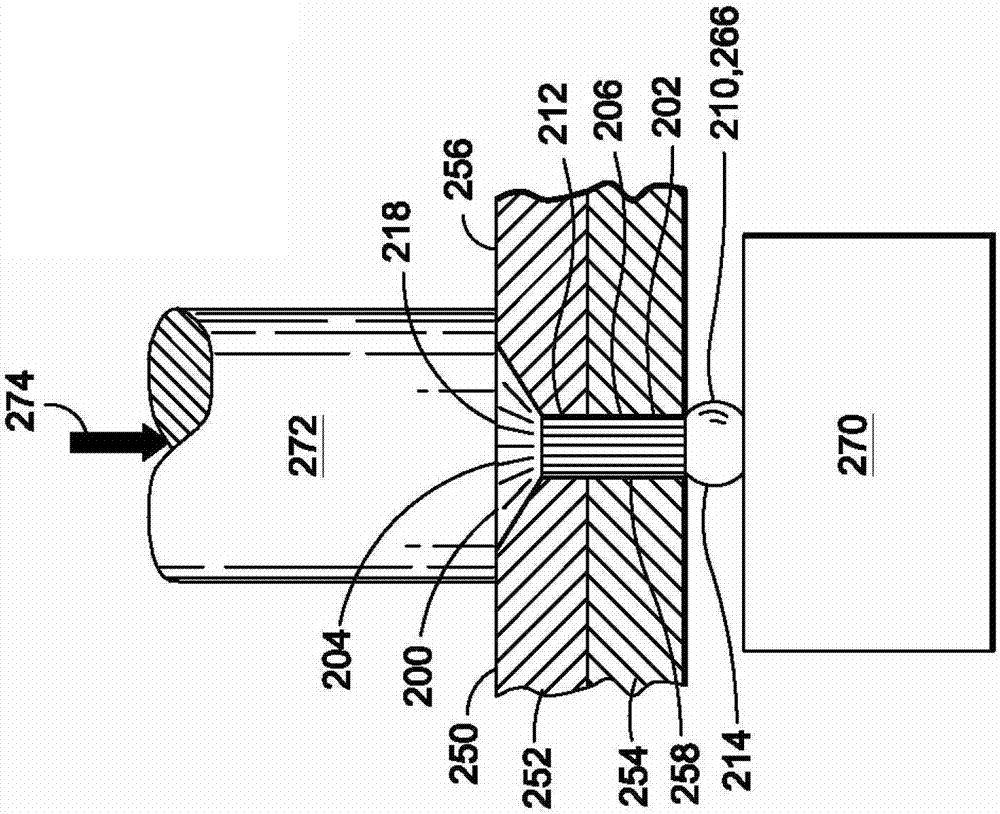
本发明一般涉及紧固件,更具体地,涉及制备具有局部冷加工区段的单件紧固件的系统和方法。
背景技术:机械紧固件被广泛应用于接合两个或者更多个结构组装件的组件。例如,机械紧固件被广泛用于接合飞机机身的结构组件。两件式紧固件被用于各种应用,其包括紧固件的张力负荷较高的情况下的应用。这样的两件式紧固件可包括螺栓或者销,该螺栓或者销可被插入孔眼和螺母或者模锻套(swagecollar),其可被机械地固定至螺纹或者在螺栓或者销的自由端上形成的其他零件/特征。通过将螺母或者套环紧固抵靠结构,结构组装件的组件可被夹紧在一起。虽然一般两件式紧固件提供较高的夹持和张力负荷-承载力,但是两件式紧固件具有减损其整体效用的一些缺陷。例如,由于需要制造、加工、以及存储大量的系统的每个组件,其中该系统包括两件式紧固件系统,所以采购成本较高。另外,在结构中安装以及装配两件式紧固件所需的时间较高,并且需要用于两件式紧固件配置的各种组件的分开的、独特的工具,这将增加生产成本。进一步地,需要为每个两件式紧固件系统处理两个分开的件增加了安装的复杂性,考虑到相当大量的将被安装在单个飞机机身中的紧固件(例如,几万个),这将令人不希望地增加整体生产时间。甚至进一步,由于配合的螺母或者套环的所需尺寸或者长度,要足以啮合销或者螺栓的末端上所形成的螺纹,从而提供足够的夹持和张力负荷承载力,所以两件式紧固件较重。由于单个飞机机身中利用的高容量的紧固件,即使在与紧固件有关的重量、成本、和时间上的小的节省都能够导致在工程进度期限内生产的飞机机身数量的显著的节省。可以看出,本领域存在需要具有减少安装复杂性的紧固件系统,并且可以在减少的时间内安装该紧固件系统,同时提供至少等效于传统的两件式紧固件的强度性能。
技术实现要素:通过本发明解决以及减轻与两件式紧固件系统有关的上述需要,在实施例中,提供了具有头部和自头部延伸并且在尾端部分终止的轴杆或者杆的单件紧固件系统。轴杆或者杆可包括位于邻接头部的冷加工杆区段,以及在冷加工杆区段和尾端部分之间延伸的可延展的杆区段。同样地,公开了用于形成单件紧固件系统的方法。本方法可包括提供具有相对端/相反端的坯体前体的步骤。坯体前体可被插入成形模的孔。成形模可具有扩大的孔部分。优选地,本方法可包括将额外的轴向压缩力施加至坯体前体,将头部冷加工至坯体前体,并且相应于扩大的成形模的孔部分,在坯体前体上形成扩大的轴杆或者杆部分。公称的杆部分可自扩大的杆部分延伸。公称的杆部分可具有大约等于紧固件的最终直径的直径。本方法可还包括将公称的杆部分插入最终的减小模的孔,并且将轴向压缩力施加至扩大的杆部分。本方法可额外地包括将扩大的杆部分推进最终的减小模的孔,并且通过减小扩大的杆部分的横截面积,形成冷加工杆区段/部分(section),以便坯体前体形成最终的紧固件配置。本公开还包括装配结构的方法。本方法可包括提供具有头部和在尾端部分终止的杆的单件紧固件(例如,铆钉)的步骤。头部可包含冷加工头部区段。杆可包括冷加工杆区段和从冷加工杆区段延伸至尾端部分的可延展的杆区段。冷加工头部区段和冷加工杆区段可具有比可延展的杆区段高的强度。本方法可额外地包括在结构的孔眼内安装紧固件,以及镦锻(upsetting)可延展的杆区段的尾端部分。根据本发明的方面,紧固件包含冷加工头部区段、冷加工杆区段、以及从冷加工杆区段延伸至紧固件的尾端部分的可延展的杆区段,其中可延展的杆部分非冷加工。优选地,冷加工头部区段和冷加工杆区段具有比可延展的杆区段高的强度。优选地,可延展杆区段具有比冷加工头部区段和冷加工杆区段高的延展性水平。优选地,紧固件具有至少一种下列材料成分:铝、铝合金。优选地,紧固件具有至少一种下列材料成分:钢、钢合金。优选地,紧固件具有至少一种下列材料成分:钛、钛合金。优选地,紧固件具有超精细颗粒材料。优选地,通过冷加工工艺形成冷加工头部区段和冷加工杆区段。优选地,紧固件使用耐腐蚀的、可固化有机涂层/涂敷材料涂层。优选地,紧固件还包含至少一个埋头/平头(flushhead)配置,以及凸头配置。根据本发明的方面,形成紧固件的方法包含将坯体前体插入具有扩大的孔部分的成形模的孔、将轴向压缩力施加至坯体前体、相应于扩大的孔部分,在坯体前体上形成冷加工头部区段和扩大的杆部分,其中扩大的杆部分具有在其中延伸的公称的杆部分、将公称的杆部分插入最终的减小模的孔、将轴向压缩力施加至扩大的杆部分、将扩大的杆部分推进至最终的减小模的孔、以及通过减小扩大的杆部分的横截面积,形成冷加工杆区段。优选地,减小扩大的杆部分的横截面积的步骤包含将扩大的杆部分的横截面积减小大约百分之2至5。优选地,提供坯体前体的步骤包含提供具有至少一种下列材料成分的坯体前体:钛、钛合金。优选地,本方法还包含提供具有超细颗粒材料成分的坯体前体。优选地,本方法还包含在形成冷加工杆区段和冷加工头部区段之前,至少一次坯体前体退火/热处理(annealing),以及在形成冷加工头部区段和冷加工杆区段之后,退火紧固件。优选地,本方法还包含使用耐腐蚀的、可固化有机涂层材料为紧固件涂层的步骤。根据本发明方面,装配结构的方法包含提供具有头部和在尾端部分终止的杆的紧固件,其中头部包含冷加工头部区段,杆包括冷加工杆区段以及从冷加工杆区段延伸至尾端部分的可延展的杆区段,并且冷加工头部区段和冷加工杆区段具有比可延展的杆区段高的强度、在结构的孔眼内安装紧固件、以及镦锻可延展的杆区段的尾端部分。优选地,提供紧固件的步骤包含提供至少一种下列材料成分的紧固件:钛、钛合金。优选地,提供紧固件的步骤包含提供超细颗粒材料的紧固件。优选地,可延展杆区段具有比冷加工头部区段和冷加工杆区段的延展性水平高的延展性水平。优选地,通过冷加工工艺形成冷加工头部区段和冷加工杆区段。优选地,本方法还包含提供使用耐腐蚀的、可固化有机涂层材料涂层的紧固件。优选地,安装紧固件的步骤包含在飞机机身的结构内安装紧固件。能够在本公开的各种实施例中单独地实现或者可以在其他实施例中组合已描述的特征、功能、和优势,参考下列描述和附图能够理解其中的进一步细节。附图说明参考附图,本公开的这些和其他特征将变得更加清晰,其中附图中的标识号涉及其中相同的部件,并且其中:图1示出具有冷加工头部区段、冷加工杆区段、以及可延展的杆区段的单件紧固件实施例的示例性侧视图,其中可延展的杆区段从冷加工杆区段延伸至紧固件的尾端部分;图2示出被安装在结构内的埋剪头/平剪头(flushshearhead)、单件紧固件的示例性侧视图;图3示出被安装在结构内的埋张力头/平张力头(flushtensionhead)、单件紧固件的示例性侧视图;图4示出被安装在结构内的凸剪头、单件紧固件的示例性侧视图图5示出被安装在结构内的凸张力头、单件紧固件的示例性侧视图图6示出在镦锻紧固件的尾端部分之前,结构内的半管状、单件紧固件的示例性侧视图;图7示出在镦锻紧固件的尾端部分之后,半管状、单件紧固件的示例性侧视图;图8示出一个或者更多操作的流程图,所述操作可被包括在将单件紧固件安装至结构中的方法中,其中在该结构中,单件紧固件具有冷加工头部区段、冷加工杆区段、以及可延展的杆区段;图9示出在将紧固件安装至穿过结构组件延伸的孔眼之前,具有冷加工头部和杆区段的单件紧固件的示例性的侧视图;图10示出被安装在孔眼内的单件紧固件的示例性侧视图,并且示出冷加工头部和具有长度大体上等于孔眼长度的杆区段,并且还示出在预安装或者预镦锻的条件下,位于紧固件尾端部分的可延展的杆区段从孔眼延伸出来;图11示出在预安装或者处于镦锻中的条件下,具有工具和铆钉顶棒被设置在紧固件的相对端的单件紧固件的示例性侧视图;图12示出被安装在结构中的单件紧固件的示例性侧视图,并且示出在被镦锻后的条件下的紧固件的尾端部分;图13示出在工具和铆钉顶棒被移除的情况下,被安装在结构内的单件紧固件的示例性侧视图,并且示出紧固件的镦锻后的端部,其中紧固件包含紧固件可延伸杆区段;图14示出一个或者更多操作的流程图,所述操作可被包括在形成具有冷加工头部区段和冷加工杆区段的单件紧固件的方法中;图15示出坯体前体的透视图,其可以按照图16-23所示的操作顺序形成具有冷加工头和杆区段的埋头、单件紧固件;图16示出成形模的示例性侧视图,其中成形模具有埋头孔以及成形锤体,以用于冷加工埋头以及在坯体前体上形成扩大的杆部分;图17示出在通过成形锤体将轴向压缩力施加至坯体前体之前,被安装在成形模内的坯体前体的示例性侧视图;图18示出在施加轴向压缩力之后,与成形模接触的成形锤体的示例性侧视图,并且示出坯体前体部分呈现出大体上相应于成形模和成形锤体形状的形状,从而形成坯体前体的冷加工头部区段和扩大的杆部分;图19示出中间形成的坯体前体的示例性侧视图,其由于施加轴向压缩力,在其中形成扩大的杆部分;图20示出具有埋头孔和减小锤体的最终的减小模的示例性侧视图,以用于在坯体前体上冷加工扩大的杆部分;图21示出中间形成的坯体前体的示例性侧视图,其在通过减小锤体将轴向压缩力施加至埋头之前,被安装在最终的减小模内;图22示出减小锤体的示例性侧视图,其在施加轴向压缩力以及减小扩大的杆部分的尺寸之后,与最终减小模接触,从而形成埋头、单件紧固件的冷加工头部区段和冷加工杆区段;图23示出埋头的、单件紧固件的最终配置的示例性侧视图,其中由于施加轴向压缩力,在紧固件上形成冷加工头部和杆区段;图24示出坯体前体的透视图,其按照如图25-32所示的操作顺序,可形成具有冷加工头部和杆区段的凸出头部、单件紧固件;图25示出成形模和成形锤体的示例性侧视图,其中成形模和成形锤体用于冷加工凸出头部并且在坯体前体上形成扩大的杆部分;图26示出在通过成形锤体将轴向压缩力施加至坯体前体之前,被安装在成形模内的坯体前体的示例性侧视图;图27示出成形锤体的示例性侧视图,其在施加轴向压缩力之后,与成形模接触,并且示出坯体前体部分呈现出大体上相应于成形模和成形锤体形状的形状,从而形成坯体前体的冷加工头部区段和扩大的杆部分;图28示出中间形成的坯体前体的示例性侧视图,其中由于施加轴向压缩力,在坯体前体上形成扩大的杆部分;图29示出最终减小模和减小锤体的示例性侧视图,其中最终减小模和减小锤体用于在中间形成的坯体前体上冷加工扩大的杆部分;图30示出在通过减小锤体将轴向压缩力施加至凸出头部之前,被安装在最终减小模内的中间形成的坯体前体的示例性侧视图;图31示出减小锤体的示例性侧视图,其在施加轴向压缩力以及减小扩大的杆部分的尺寸之后,与最终减小模接触,从而形成凸出头部、单件紧固件的冷加工杆区段;图32示出凸出头部、单件紧固件的最终配置的示例性侧视图,其中由于施加轴向压缩力,在紧固件上形成冷加工头部和杆区段;图33示出半管状坯体前体和插入工具的透视图,其中按照与图2-9所示的顺序相似的操作顺序,在坯体前体形成单件紧固件的最终配件的过程中,可实施插入工具,以稳定坯体前体的管腔;图34示出被安置在成形模内的半管状坯体前体,以及被放置在坯体前体的管腔下面的插入物的示例性侧视图;图35示出半管状坯体前体和插入物的示例性侧视图,其中坯体前体被安置在成形模内,并且在将轴向压缩力施加至半管状坯体前体之前,插入物被安装在管腔内;以及图36示出一个或者更多操作的流程图,所述操作可被包括在形成具有冷加工头部和杆区段的单件紧固件的方法内,并且该流程图包括一个或者更多可选的热处理步骤,以及将有机涂层施加至单件紧固件。具体实施方式现在参考附图,其中所示是为了说明本公开的优选和不同实施例的目的,图1中示出形成于单件紧固件配置中的紧固件200的实施例的示例性视图。单件紧固件200(例如,铆钉)具有头部203和轴杆或者杆206。杆206从头部203延伸并且在尾端部分210终止。头部203被冷加工并且头部203包含单件紧固件200的冷加工头部区段204。杆206具有可延展的杆区段214和冷加工杆区段212。冷加工杆区段212也被冷加工,并且位于邻近单件紧固件200的冷加工头部区段204的地方。可延展杆区段214可从冷加工杆区段212延伸至杆206的尾端部分210。虽然杆206沿着杆206的长度可形成大体上恒定的杆直径208,但是杆206沿着杆206的不同位置在中间形成两个或者更多不同的直径(未示出)。应当注意,虽然本公开是在铆钉的情况下描述单件紧固件200,但是在无限制的情况下,单件紧固件200可被提供在各种配置的任何一种中,而不被限制于铆钉配置。甚至进一步地,紧固件200不被限制于用作单件紧固件200。例如,紧固件200和其有关的形成步骤可被施加至多件紧固件系统以及在多件紧固件系统中被实施,例如在两件紧固件系统中,从而实现相似的优势益处。有利地,由于冷加工工艺效应,紧固件200的冷加工头部区段204和冷加工杆区段212比可延展的杆区段214的强度高,其中如下面更加详细地描述,冷加工工艺可被施加至头部203和杆206部分。例如,冷加工头部区段204和冷加工杆区段212可具有比可延展杆区段214的抗剪强度高的抗剪强度。对于具有超细颗粒的钛或者钛合金成分的紧固件200,冷加工头部区段204和冷加工杆区段212可具有至少95ksi(每平方寸的千磅数)的极限抗剪强度,并且更优选地,至少100ksi(每平方寸的千磅数)的极限抗剪强度。如下面更加详细地描述,由于冷加工头部区段204和杆区段212的工艺,相对于传统的紧固件,紧固件200可还具有较高的张力承载力。有利地,在紧固件200未被热处理的情况下,可以实现局部增加冷加工头部区段204和冷加工杆区段212的强度水平。如下所述,冷加工头部区段204和冷加工杆区段212的较高强度水平还部分地由于使用具有较小平均粒度的紧固件材料。可以通过使用低温球磨、等径角挤压、或者其他粒度减小工艺实现较小的平均粒度。优选地,相对于传统的、钛或者钛合金材料,紧固件200中使用减小的粒度,例如低温球磨的钛或者钛合金材料,产生改良的强度、改良的可模锻性、以及增加的高温稳定性。另外,在无需后续的热处理的情况下,可以实现改良的机械性能,其通过具有较小粒度的材料提供,例如减小的、超细颗粒材料。如本文中所公开的,增加冷加工紧固件200产生冷加工头部区段204和冷加工杆区段212。具有较高机械性能的冷加工头部区段204和冷加工杆区段212的组合,产生张力和夹持力类似于传统两件式紧固件所提供的张力和夹持力的单件紧固件200,其中较高机械性能是通过较小粒度的材料提供,例如低温球磨的超细颗粒材料。优选地,能够使用简单的单件紧固件200代替传统的两件式紧固件简化了紧固件安装过程,这样导致较低的紧固件安装成本。另外,在本文中公开的单件紧固件200具有比两件式紧固件要低的重量(例如,降低百分之30),其中两件式紧固件具有可比的机械性能。有利地,可延展杆区段214可具有比冷加工头部区段204和冷加工杆区段212的延展性水平高的延展性水平。如下所述,在紧固件安装(例如,铆接或者是镦锻操作)过程中,可延展杆区段214的高延展性水平有助于适当变形或者是镦锻紧固件200的尾端部分210。可延展杆区段214的高延展性水平与坯体前体12的高延展性水平大体上类似,其中由坯体前体12可形成紧固件200。更具体地,相对于冷加工头部区段204和冷加工杆区段212的延展性,通过将紧固件200的冷加工局部地限制于冷加工头部区段204和冷加工杆区段212,并且避免任何冷加工杆206的剩余部分(即,可延展杆区段214),可以产生高延展性水平的可延展杆区段214。在实施例中,在无故障或者其他不可接受的条件的情况下,可延展杆区段214可具有促进紧固件200的尾端部分210适当变形的延展值。例如,在杆206压裂或者故障之前,可延展杆区段214可具有沿紧固件200纵向轴的拉长至少大约百分之10的延展值。在杆206压裂或者故障之前,可延展杆区段214可还具有这样的延展性水平,其由横截面积减小至少大约百分之30表示。可延展杆区段214的较高的延展性水平是由较小粒度的材料所致,其中可由较小粒度的材料形成紧固件200(即,坯体前体12)。优选地,在实施例中,可以由具有较小平均粒度的超细颗粒材料形成紧固件200。例如,可以由具有平均粒度小于大约10000纳米(nm)(即,小于大约10微米)的材料形成紧固件200。这样的超精细颗粒材料可以通过摩擦搅拌工艺和/或通过等径角挤压(EAE)、或者其他工艺生产。在进一步实施例中,可以由具有平均粒度小于大约500纳米(nm)以及,尤其是平均粒度小于大约300纳米的材料形成紧固件200。例如,材料可以具有从大约100纳米到300纳米的平均粒度。然而,用于形成紧固件200的材料不被限制于具有平均粒度小于大约10000纳米的材料,而是可以由具有任何粒度的任何材料形成。例如,可以由具有被描述为平均粒度大于大约100000纳米的粗粒材料的材料形成紧固件200。可还由被描述为具有平均粒度小于大约100000纳米,例如在大约50000至75000纳米之间的细粒材料的材料形成紧固件200材料。在实施例中,可使用摩擦搅拌工艺(未示出)形成坯体前体12的材料。摩擦搅拌工艺可使用粗粒(例如,平均粒度大于大约100000nm)金属材料,例如钛或者钛合金材料。可使用搅拌室(未示出)和搅拌工具(未示出)加工粗粒金属材料。当粗粒材料通过搅拌室时,其中在搅拌室中搅拌工具搅拌材料,并且使用若干机械变形减小粒度以及提高材料的微观结构的均匀性或者一致性时,粗粒材料的温度增加。基于退出搅拌室时产生具有超细颗粒微观结构的较高均质材料,材料可被固结。可选地,可以使用等径角挤压(EAE)工艺减小材料的粒度,其中由该材料形成坯体前体12,在等径角挤压工艺中,材料被迫通过具有大约九十度弯曲的锻模。在等径角挤压工艺中,压迫材料通过九十度弯曲导致机械、冷加工材料。机械、冷加工材料可减小材料的平均粒度。可还使用低温球磨工艺生产材料粒度,其中球式、磨碎装置(未示出)可被用于减小材料微观结构的尺寸。通过使用球式磨碎装置的若干机械变形,材料可被磨碎至较精细的颗粒粉末浆料。可以在液态氢或者氮或者其他冷却介质中磨碎材料。使用高温等静力压制(HIP)工艺或者是其他固结工艺,固结超细颗粒粉末材料。本工艺将导致具有超细、亚微细粒颗粒微结构。例如,可以在低温球磨工艺中生产钛和/或钛合金粉末,其中钛和/或钛的合金粉末可以以预定的量或百分比与其他的合金元素混合,并且进行低温球磨加工。如上所述,在低温球磨工艺中,在液态氮、氩、氢浆料、或者其他环境下,通过使用不锈钢球体的超微磨碎型球磨设备碾磨金属合金粉末混合物。响应于低温球磨工艺过程中的粉末金相组织的极端机械变形,金属合金粉末混合物的化学成分可被改变。例如,在低温球磨工艺过程中,由于低温球磨工艺的氮、氩、氧、或者其他气氛,可产生非常精细的氧化物或者氮化物相。精细的氧化物和氮化物相可提高所产生的亚微细粒、超细粒度材料的温度稳定性。在这方面,通过使用低温球磨工艺,可以产生被改良的高的强度、稳定、超细粒度粉末。例如通过使用高温等静力压制(HIP)、Ceracon-型锻造工艺、或者其他的固结工艺,钛粉末可被除去气味并且被固结,从而提供具有高均匀性水平的超细颗粒微结构的钛或者钛合金材料。虽然本文在钛和钛合金的情况下描述用于形成紧固件200的材料,但是紧固件200(即,坯体前体12)材料可被提供为任何材料成分,其包括,但不限制于,铝、铝合金、钢、例如不锈钢的钢合金、以及各种其他材料成分中的任何一种,并非限制。这样的材料成分可优选地具有上述的较小的平均粒度。仍参考图1,可以通过冷加工工艺形成紧固件200的冷加工头部区段204和冷加工杆区段,其中在冷加工工艺中,可以冷加工紧固件200的坯体前体12(图15)。在实施例中,冷加工工艺可包含冷加工坯体前体12,从而形成冷加工头部区段204,同时形成中间形成的坯体前体13(图19)的扩大的杆部分32(图19)。冷加工工艺可还包含局部地减小扩大的杆部分32的横截面积,从而形成紧固件200的冷加工杆区段212,如下面更加详细地描述。在实施例中,扩大的杆部分32的横截面积可被减小大约百分之2至5,如下面更加详细地描述。然而,冷加工工艺可包含减小小于大约百分之2或者多于大约百分之5的扩大的杆部分32的横截面积。在实施例中,冷加工工艺可包含减小大约百分之3.5的扩大的杆部分32的横截面积。在这方面,中间形成的坯体前体13(图19)的扩大的杆直径34可经冷加工减小至紧固件200的最终杆直径208的近似直径。通过局部地冷加工头部203和杆206(图1),在所产生的冷加工头部区段204和冷加工杆区段212(图1)中能够实现局部地增加强度水平,同时杆206(即,可延展杆区段214)的剩余部分保留较高的延展性水平(即,可模锻性)和耐用性,这有助于提高紧固件200(图1)安装的性能。例如,通过局部地冷加工杆206,相对于可延展杆区段214(图1)中的强度,在或者邻近冷加工头部区段204和冷加工杆区段212中的紧固件200抗剪强度和张力强度可被局部地增加。相反地,通过将冷加工限制于局部的冷加工头部区段204和冷加工杆区段212,杆206的可延展杆区段214(即,杆206的剩余物)保留较高的延展性、可模锻性、以及耐用性水平,这是由于材料的较小的粒度(例如,超细粒度)所产生。有利地,对于单件紧固件200配置,例如图1所示铆钉,通过提供改良的操作性,或者通过提高的拉伸镦锻铆钉尾端部分210,可延展杆区段214的高延展性水平改善紧固件200安装,这样改善了随后在两个或者更多部件252、254(图2)之间实现的夹持,其中两个或者更多部件252、254可以通过紧固件200紧固。优选地,在没有热处理工艺(例如,退火、人工老化等等)的情况下,可以实现较高强度水平的冷加工头部区段204和冷加工杆区段212,这将极大地减小紧固件200的制作成本和紧固件200的制作时间。然而,如下所述,一个或者更多热处理可被包括在紧固件200的形成工艺中,从而增强或者稳定紧固件200的冷加工头部区段204和冷加工杆区段212和/或进一步改善紧固件200的机械性能,例如增加冷加工头部区段204和冷加工杆区段212的抗剪强度。通过将防腐蚀有机涂层202(图1)施加至紧固件200,可以实现紧固件200(图1)性能的额外的改良。涂层202可改善紧固件200的润滑性,这将有助于紧固件200的安装。通过涂层202提供的改良的润滑性可还避免了与紧固件的湿安装有关的复杂性、时间、以及费用。涂层202可还提供了对抗环境(例如,湿气)腐蚀、电解腐蚀、和/或应力腐蚀的用于紧固件200的增强的腐蚀保护。在实施例中,涂层202可包含可固化防腐蚀、有机涂层材料,其在形成紧固件200的任何时间之前、过程中、和/或之后,可被用于紧固件200的溶液中。在实施例中,涂层202(图1)可包含可与一种或者多种增塑剂混合的酚醛树脂。涂层202可还包括例如聚四氟乙烯的有机成分。可还包括无机添加剂,例如铝粉和/或铬酸锶。这样的涂层成分和添加剂可在溶剂中被溶解,从而促进涂层202应用。溶剂可包含乙醇、甲苯、丁酮(MEK)、和/或其他溶剂。在实施例中,将在这样的溶液中提供涂层202,其中具有作为溶剂的乙醇重量占大约百分之30、甲苯重量占大约百分之7、以及丁酮(MEK)重量占大约百分之45,以及铬酸锶重量占大约百分之2、铝粉重量占大约百分之2。涂层成分的剩余物可包含作为涂层材料的酚醛树脂和增塑剂,以及可包括较小量的聚四氟乙烯。作为Hi-KoteTM1的涂层202可以从Lisi航空与航天...