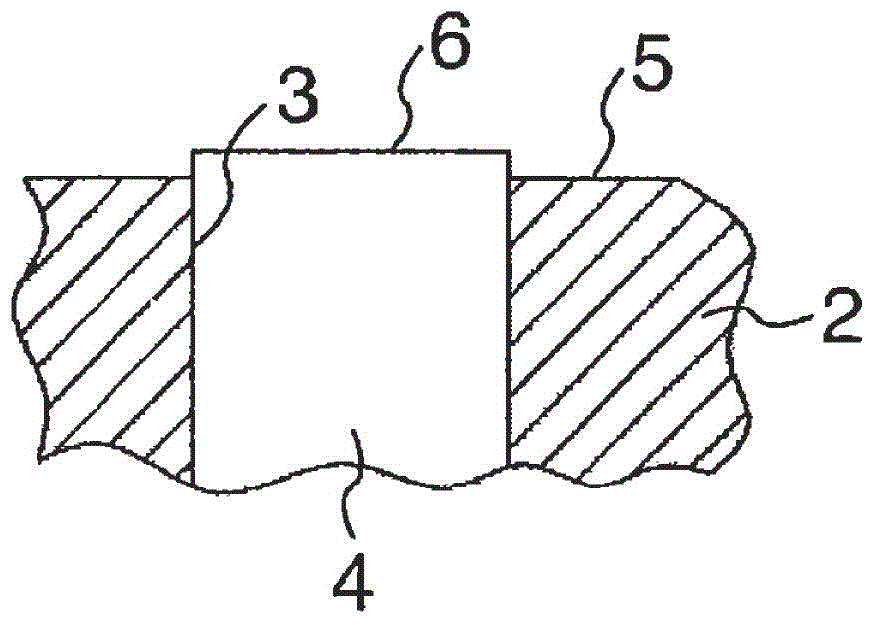
本发明涉及在坝的水闸的滑动部或排水泵等用途中于水中使用的水中滑动构件,更具体涉及在金属基体埋设有润滑塞的水中滑动构件。
背景技术:
:水中滑动构件在坝的水闸的滑动部或排水泵等低速、高负荷的条件下使用,例如轴等配合件浸于水中,水中滑动构件被用于支持该轴等。作为这样的水中滑动构件,已知在金属基体形成多个孔或凹部,在该孔或凹部埋设有润滑塞的构件。作为埋入金属基体使用的润滑塞(压丸)的构造,专利文献1中记载了在由石墨形成的压丸母体部设置凹部,填充石蜡、石墨等固体润滑剂及聚乙烯的混合物的构件。认为石墨物理吸附水,石墨自身的劈裂强度变弱,摩擦系数降低。而且记载了如果该水中滑动构件在使用时滑动面的温度因摩擦而上升,则构成润滑塞的聚乙烯及石蜡发生热膨胀,而且石蜡从固相变成液相,体积膨胀,籍此混合物从滑动面突出,被挤压于配合件的表面,从而易于向滑动面间供给石墨等固体润滑剂。此外,在专利文献2中,认为使用含石墨的润滑塞的滑动构件在滑动面形成被膜的能力不足,提出了含有三聚氰胺氰尿酸盐来代替石墨的、由聚乙烯和蜡和三聚氰胺氰尿酸盐形成的润滑塞。记载了三聚氰胺氰尿酸盐为与石墨等相同的层状结构,认为具有劈裂性,从而具有使滑动构件的耐磨损性提高的作用。专利文献专利文献1:日本专利特开昭51-46668号公报专利文献2:国际专利第2004/046285号技术实现要素:专利文献1的滑动构件在水中使用时,轴开始动作时、即启动时,由于金属基体的滑动面与润滑塞的表面处于同一平面内,因此轴和金属基体的滑动面直接接触,存在在金属基体的滑动面发生损伤及粘附的问题。专利文献2的润滑塞也由于金属基体的滑动面与润滑塞的表面处于同一平面内,因此启动时轴和金属基体的滑动面直接接触,存在在金属基体的滑动面发生损伤及粘附的问题。本发明的目的是解决上述现有技术的问题,提供采用水中用滑动构件的装置启动时,金属基体的滑动面与配合件不会直接接触,在金属基体的滑动面不易发生损伤及粘附的水中滑动构件。本发明的水中滑动构件的特征是:具备具有滑动面的金属基体与润滑塞,在金属基体形成开口于滑动面的多个孔或凹部,在该孔或凹部埋设有润滑塞。润滑塞由合成树脂形成,润滑塞具有滑动表面,该润滑塞的滑动表面以润滑塞的滑动表面的当量圆直径的0.05%~5%的突出高度从金属基体的滑动面突出。这里,“润滑塞的滑动表面的当量圆直径”指具有与润滑塞的滑动表面的面积相等的面积的圆的直径。润滑塞的滑动表面从金属基体的滑动面突出的高度优选0.005~0.2mm。优选润滑塞为圆筒形状,润滑塞的滑动表面为圆形。润滑塞优选由聚乙烯形成。这种情况下,润滑塞还可以含有20体积%以下的选自酚醛、聚酰胺、聚酰亚胺、聚酰胺酰亚胺、聚四氟乙烯、聚苯硫醚、聚氧苯甲酰的1种以上的树脂。润滑塞可以含有5体积%以下的作为固体润滑剂的、选自石墨、二硫化钼、二硫化钨的1种以上的固体润滑剂。还有,润滑塞可以含有1体积%以下的着色剂。金属基体优选具有内周面为滑动面的圆筒形状的基体。本发明的其他目的、特征及优点从与附图相关的以下的本发明的实施 例的记载中可知。附图说明图1是本发明的水中滑动构件的一具体例的立体图。图2是图1的水中滑动构件的滑动面附近的剖视图。图3是本发明的水中滑动构件的其他具体例的滑动面附近的剖视图。具体实施方式图1及图2所示为本发明的水中滑动构件的一具体例。水中滑动构件1具有圆筒形状的金属基体2、贯穿金属基体2的内周面与外周面之间的壁厚的多个圆筒形状的孔3、和埋设于该孔3的圆筒形状的润滑塞4。金属基体2的内周面为滑动构件的滑动面5。金属基体2的组成没有特别的限定,可以使用铜合金、铁合金等各种合金,可通过烧结或铸造来制造。金属基体2的尺寸(内径、外径、宽度)没有限定,可以根据使用水中滑动构件1的装置的滑动部的尺寸来设定。滑动构件1的滑动面5上的孔3的孔径为3~30mm左右即可,滑动面5上的多个孔3的开口的面积率(润滑塞的面积率)为10%~50%即可,但不限于该尺寸及面积率,也可以变更。润滑塞4的内周面侧的表面6相较金属基体2的内周面5突出,成为与配合件发生滑动的滑动表面。这样,由于滑动构件1预先形成使润滑塞4的表面从滑动面5(即金属基体2的内周面)突出的结构,因此使用滑动构件1的装置启动时,也是从滑动面5突出的润滑塞4的滑动表面6与配合件的表面接触。在滑动面5与配合件的表面之间形成间隙,籍此在该间隙形成水膜,避免金属基体2与配合件直接接触。润滑塞4的尺寸和形状按照与金属基体2的孔3的孔径及形状匹配的条件来制造。在该例中,润滑塞4按照圆筒形状来说明,但其形状不限于圆筒形状,可以是棱柱、椭圆柱、圆锥、棱锥、椭圆锥等其他形状。润滑塞的滑动表面6从金属基体2的滑动面5的突出高度为润滑塞的滑动表面6的直径的0.05%~5%。润滑塞4不是圆筒形,润滑塞的滑动表面不是 圆形时,为润滑塞的滑动表面的当量圆直径的0.05%~5%。通常、润滑塞的滑动表面从金属基体2的滑动面5的突出高度优选0.005~0.2mm,更好的值是0.01~0.05mm。润滑塞4由聚乙烯树脂、酚醛树脂、聚酰胺树脂、聚甲醛等合成树脂形成。润滑塞4可以通过将作为原材料的合成树脂粉末注射成型为圆筒形状来制造,但润滑塞4的制造方法不限于此,可以是挤出成型、压缩成型等其他方法。润滑塞4被埋设于金属基体2的孔3后,对金属基体2的内周面施以切削加工。该切削加工使用刀尖为圆弧形状的切削刀,而且使切削刀对作为切削面的金属基体2的内周面施加的垂直方向的加压力比通常高,对金属基体2的内周面进行车削。圆弧形状的切削刀是使切削刀的圆弧形状的刀尖在各润滑塞4的表面通过数次,籍此对润滑塞4的整个表面施以切削加工。因此,加工时,圆弧形状的刀尖只与润滑塞4的表面的一部分接触。在该加工时,由于金属基体2的内周面及润滑塞4的表面在受到比通常更高的切削刀的加压力的状态下被切削,因此由合成树脂形成的润滑塞4在该加压力的作用下在相对被加工的表面垂直的方向上被弹性压缩。由于该润滑塞4的弹性形变量大于金属基体2的内周面的弹性形变量,因此切削刀通过后加压力解除时,由加压力引起的弹性形变复原,润滑塞4的表面变得比金属基体2的内周面突出。通过调节切削刀对金属基体2的内周面的加压力,可以控制润滑塞4从金属基体2的滑动面5的突出量。润滑塞4为由合成树脂形成的单相的组织,即使滑动时与配合件接触而变形也不易发生剪切。而且,润滑塞4优选由吸水率低的聚乙烯树脂形成。还有,本发明的润滑塞4使用聚乙烯树脂时,也可以在聚乙烯树脂中以大于0体积%且小于等于20体积%的范围添加选自酚醛、聚酰胺、聚酰亚胺、聚酰胺酰亚胺、聚四氟乙烯、聚苯硫醚、聚氧苯甲酰的1种以上的树脂来调节润滑塞4的强度等。尤其是,在水中滑动构件1的使用中润滑塞4的温度因与配合件的摩擦而升高时也能够保持强度。聚乙烯树脂可以使用一般市售的各种聚乙烯树脂。而且,聚乙烯树脂优选分子量为20万以上的聚乙烯树脂。其原因是润滑塞4的强度提高,可减少滑动时润滑塞4的表面的磨损量。作为该分子量为20万以上的聚乙烯树脂,可以使用例如以下的聚乙烯树脂。三井化学株式会社(三井化学(株))制商品名ハイゼックスミリオン(注册商标)(分子量50万以上)三井化学株式会社制商品名リュブマー(注册商标)(分子量20万以上)、旭化成化学株式会社(旭化成ケミカルズ(株))制商品名サンファイン(注册商标)UH(分子量350万以上)润滑塞4中也可以含有1体积%以下的着色剂,用于施以任意的着色。作为着色剂只要是一般用于树脂着色的着色剂即可,可以使用炭黑、氧化铁、氧化铬等。但是,着色剂并不限于此,可以使用一般市售的各种着色剂。此外,润滑塞4还可以含有5体积%以下的作为固体润滑剂的、选自石墨、二硫化钼、二硫化钨的1种以上。由于配合件与润滑塞4的滑动,比金属基体2的表面突出的部分的润滑塞4受到平行于其表面的方向的力,发生形变。由于石墨、二硫化钼、二硫化钨具有劈裂性,因此在该形变的作用下,存在于润滑塞4的内部的石墨、二硫化钼、二硫化钨等固体润滑剂的粉末发生劈裂(剪切),但在润滑塞4含有超过5体积%的这些固体润滑剂的情况下,保持固体润滑剂粉末的合成树脂也容易发生剪切。因为该剪切,表面附近的润滑塞4被除去。或者,在比金属基体2的表面(滑动面5)突出的润滑塞4的部分与被金属基体2的孔部约束的部分的边界附近发生应力集中,导致在该边界附近的固体润滑剂粉末发生劈裂(剪切),而且保持固体润滑剂粉末的合成树脂也发生剪切,从而容易发生润滑塞4被除去的损伤。使润滑塞4含有5体积%以下的作为固体润滑剂的、选自石墨、二硫化钼、二硫化钨的1种以上时,不易发生这样的润滑塞4被除去的损伤。此外,润滑塞4应避免含有碳纤维等硬质的纤维状粒子。其原因是:在对金属基体2的内周面进行切削加工时,在比通常更高的来自切削刀的加压 力的作用下,润滑塞4的表面附近所含的硬质的纤维状粒子被剪切,在滑动时这些硬质的纤维状粒子的剪切碎片从润滑塞4的表面脱落到配合件与金属基体2之间的间隙,金属基体2的滑动面5受到损伤。图3所示为本发明的水中滑动构件的其他具体例的滑动面附近的剖视图。该例中,在金属基体2形成仅开口于滑动面5而不开口于外周面的凹部3’来代替贯通孔,在该凹部3’埋设润滑塞4’。润滑塞4’的滑动表面6’从金属基体2的滑动面5突出。除了在金属基体2形成凹部3’代替孔以外的结构与图1及图2所述的具体例相同,如关于图1和图2所做的说明同样。本发明的水中滑动构件不限于图1~图3所示的结构,能够有其他的变形。例如,水中滑动构件的金属基体不限于圆筒形状,也可以是半圆筒形状或平板形状或其他的形状。金属基体的孔或凹部不限于圆筒形状,也能够采用椭圆柱或棱柱形状。当然,润滑塞形成与金属基体的孔或凹部匹配的形状。此外,与本发明不同,在金属基体不形成孔,仅在金属基体的整个平滑的内周面被覆合成树脂层的水中滑动构件存在滑动时在金属基体的表面与合成树脂层的界面上发生剪切的问题。实施例通过以下的工序制造实施例1~4和比较例1~3的各滑动构件。金属基体的制造实施例及比较例的金属基体使用相同的金属基体。该金属基体如下制造。即,将具有Cu-25质量%Zn-6质量%Al-3质量%Fe-3质量%Mn的组成的铜合金熔化,铸造成内径20mm、外径28mm、宽20mm的圆筒体。接着,形成贯通圆筒体的外周面和内周面的多个圆筒形状的孔。孔径为4mm,作为金属基体的滑动面的内周面中的多个孔的开口面积率为25%。润滑塞的制造实施例和比较例的润滑塞通过将表1所示的组成的原材料注射成型,得到直径为4mm、长度为4mm的圆筒形状。此外,聚乙烯树脂使用三井化学株式会社制商品名リュブマー(注册商标)(分子量50万)。聚酰胺树脂 使用旭化成化学株式会社制レオナ1300S。实施例3的润滑塞含有1体积%的作为着色剂的炭黑。炭黑使用三菱化学株式会社(三菱化学(株))制、商品名:RCF#44。表1润滑塞组成有无损伤实施例1聚乙烯无实施例2聚乙烯-20体积%酚醛无实施例3聚乙烯-1体积%炭黑-5体积%石墨无实施例4聚酰胺无比较例1聚乙烯-25体积%石蜡-25体积%石墨有比较例2聚乙烯-25体积%石蜡-25体积%三聚氰胺氰尿酸盐有比较例3聚酰胺(同一平面)有将准备好的润滑塞埋设于金属基体的孔,在各实施例和比较例1、2中,对作为金属基体的滑动面的内周面实施施加如上所述的加压力的切削加工,使润滑塞的滑动表面相对于金属基体的内周面的突出高度为0.02mm。比较例3中,对作为金属基体的滑动面的内周面侧实施研磨加工,使得金属基体的内周面与润滑塞的表面处于同一平面内。通过以上的工序,得到实施例1~4和比较例1~3的滑动构件。评价对实施例1~4和比较例1~3的滑动构件,进行表2所示条件的滑动试验,评价滑动构件的金属基体的滑动面有无损伤。具体的评价方法是:对以表2所示的条件进行了试验的实施例和比较例的滑动构件的滑动面,使用形状测定器(粗糙度测定器),在金属基体的滑动面确认有0.05mm以上的伤(摩擦损伤)时,判定为金属基体的滑动面受到损伤。其结果示于表1的“有无损伤”一栏。表2试验机圆筒式旋转试验机表面压力24.5MPa速度0.01m/s试验形式5s启动10s停止循环次数1000环境水中配合件不锈钢配合件粗糙度1μm(Rmax)实施例1~4的滑动构件中,金属基体的滑动面都没有与配合件的摩擦损伤,维持着平滑的面。实施例2例示了在聚乙烯树脂中添加作为选择成分的酚醛树脂的例子,但添加作为酚醛以外的选择成分的、选自聚酰胺、聚酰亚胺、聚酰胺酰亚胺、聚四氟乙烯、聚苯硫醚、聚氧苯甲酰的1种以上时,如果选择成分的添加量为20体积%以下,则经滑动试验可以确认润滑塞的表面无损伤。实施例4中,确认了在润滑塞中使用聚酰胺也能够得到与聚乙烯同样的效果。比较例1~3的滑动构件中,均确认在金属基体的滑动面上产生了大量的因与配合件的摩擦造成的深度0.05mm的摩擦损伤。在比较例1及2的润滑塞的表面观察到损伤,那些表面呈不规则的凹凸面,确认了是从润滑塞的表面附近的内部被剪切的形态。比较例1及比较例2的润滑塞分别含有大量的具有劈裂性的石墨及三聚氰胺氰尿酸盐。因此可以认为,在滑动时,在润滑塞的表面附近的内部发生剪切,由此金属基体与配合件接触导致摩擦损伤的发生。虽然在比较例3的润滑塞的表面未观察到损伤,但由于润滑塞与金属基体处于同一平面内,因此可以认为金属基体与配合件的接触导致产生摩擦损伤。符号的说明1水中滑动构件2金属基体3孔3’凹部4、4’润滑塞5滑动面6、6’润滑塞の滑动表面当前第1页1 2 3