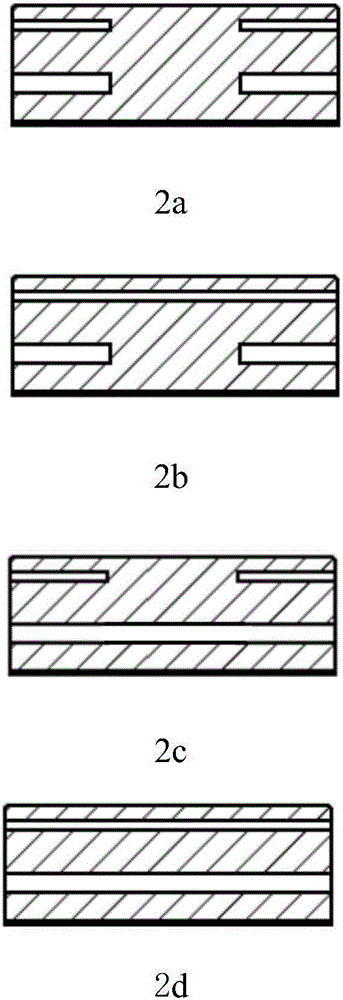
本发明属于车辆变速箱领域,涉及一种用于减振降噪的顶底双孔齿轮及其设计方法。
背景技术:
:振动和噪声性能指标是评价变速箱质量的重要参数。近年来,随着车辆舒适性能的提高以及整车加速通过噪声限值标准的升级,各大整车厂以及终端客户都将振动和噪声作为评价车辆质量性能的重要参数。变速箱作为整车传动系重要总成部件,振动噪声性能是其产品市场竞争力的重要体现。变速箱的振动和噪声来源于齿轮运转过程中的动态激励,变速箱齿轮运转过程中,齿轮齿顶的啮入和齿根的啮出是形成齿轮间冲击振动的主要来源。技术实现要素:本发明的目的在于克服现有技术缺陷,提供一种用于减振降噪的顶底双孔齿轮及其设计方法,降低齿轮啮合过程中由于啮入和啮出而引起的振动冲击,达到降低齿轮动态激励的效果,降低变速箱的振动和噪声值;同时通过正交分析方法得到优化以后的顶底孔参数,达到改善齿根弯曲强度的结果。为达到上述目的,本发明采用如下技术方案:一种用于减振降噪的顶底双孔齿轮,在齿轮端面沿齿牙中心线、平行于齿宽方向钻有孔洞,孔洞包括靠近齿顶的顶孔和靠近齿根的底孔,顶孔小于底孔孔径,在满足齿根弯曲强度要求前提下,通过正交分析方法,选取最优的顶底双孔齿轮参数作为顶孔和底孔的位置、直径和深度参数。进一步,所述顶孔和底孔为沿着齿轮端面开设的盲孔。进一步,所述顶孔和底孔,其中一个为沿着齿轮端面开设的盲孔、另一个为通孔。进一步,所述顶孔和底孔为沿着齿轮端面开设的通孔。一种双孔齿轮设计方法,通过正交分析方法,选取最优的顶底双孔齿轮参数作为顶孔和底孔的位置、直径和深度参数;具体方法为:第一,从齿轮节圆到齿顶圆沿径向等距离取3个节点作为备选顶孔,3个节点沿齿牙中线作为中心,3个节点位置依次为(da+3d)/4、(2da+2d)/4和(3da+d)/4,其中d为节圆直径,da为齿顶圆直径;节点直径依次取m/20、m/15、m/10,m为齿轮模数;节点深依次取齿轮宽度的B/4、B/2和B,B为齿轮宽度;第二,通过仿真计算齿根弯曲应力值,结果如表1所示:表1顶孔参数列表下的齿根弯曲应力计算结果孔径1孔径2孔径3孔深a孔径b孔径c顶孔径向AA1A2A3AaAbAc顶孔径向BB1B2B3BaBbBc顶孔径向CC1C2C3CaCbCc孔深aa1a2a3———孔径bb1b2b3———孔径cc1c2c3———第三,根据表1计算结果,选取一组最优保证齿根弯曲强度的尺寸参数作为顶孔的参数;第四,顶孔计算完成后以顶孔完成后的实际结构作为仿真计算模型计算底孔参数;底孔尺寸参数信息的计算过程与顶孔相同,底孔直径参数计算时依次取0.1πm、0.2πm和0.3πm,πm为齿轮模数与圆周率的乘积;确定顶底孔参数齿轮设计结束。本发明用于减振降噪的顶底双孔齿轮,在齿轮端面沿齿牙中心线、平行于齿宽方向钻有孔洞,孔洞包括靠近齿顶的顶孔和靠近齿根的底孔,顶底双孔齿轮可以增加齿轮结构的柔性度,其特有的柔性结构可以降低齿轮啮合过程中由于齿顶啮入和齿根啮出而引起的振动冲击,达到降低齿轮动态激励的效果。同时,顶底双孔齿轮需保证齿根弯曲强度满足设计要求,通过正交分析方法,选取最优的顶底双孔齿轮参数,不仅能够满足原齿根弯曲强度设计要求,而且能够改善齿根弯曲应力的分布,提高齿根弯曲强度。通过与采用其它方法,如增大齿轮副重合度,直齿轮改为斜齿轮等,降低变速箱齿轮啮合振动相比较,新型顶底双孔齿轮结构仅需要沿着齿向方向,在齿轮端面合理位置打钻孔洞,可以最大限度保证齿轮原有的设计结构与设计参数,无需改变其它零件设计,也不需要增加特殊的工艺夹具和刀具,能够最大限度的节省成本,具有市场实用性。附图说明图1孔洞结构齿轮端面图图2顶底双孔齿轮结构变型图图2a顶底双孔齿轮-齿顶齿根双盲孔示意图图2b顶底双孔齿轮-齿顶通孔齿根盲孔示意图图2c顶底双孔齿轮-齿顶盲孔齿根通孔示意图图2d顶底双孔齿轮-齿顶齿根双通孔示意图具体实施方式下面结合附图对本发明做进一步详细描述:如图1所示,用于减振降噪的顶底双孔齿轮,顶孔位于齿顶圆与节圆之间,底孔位于齿根圆附近,在齿轮端面沿齿牙中心线C、平行于齿宽方向钻有孔洞,孔洞包括靠近齿顶的顶孔A和靠近齿根的底孔B,顶孔A小于底孔B孔径。图1中顶孔和底孔的位置、直径和深度三个参数,通过有限元方法计算齿根弯曲强度,并以齿根弯曲强度作为优化目标,采用正交分析的方法来确定顶底双孔参数。如图2所示,顶孔A和底孔B可以采用图2a-2d中的任一种孔型,顶孔A和底孔B可以为沿着齿轮端面开设的盲孔;或者顶孔A和底孔B,其中一个为沿着齿轮端面开设的盲孔、另一个为通孔;或者顶孔A和底孔B为沿着齿轮端面开设的通孔。工程实际中可采用图2中图2a到图2d中的任一结构,齿轮齿牙结构具有轴对称性,孔洞中心一般位于齿牙中线C上,根据以“齿根弯曲强度为优化目标”的计算结果,确定底孔顶孔的径向位置,孔径以及孔深。下面以顶孔A为例,介绍顶底双孔的参数优化过程。首先,将节圆和齿顶圆沿径向距离4等分(节圆直径d,齿顶圆直径da),3个节点(节点位置依次为(da+3d)/4、(2da+2d)/4和(3da+d)/4)沿齿牙中线作为顶孔中心(节点直径依次为157.02mm、160.19mm和163.36mm);考虑到齿牙实际尺寸,顶孔直径依次取m/20、m/15、m/10(m为齿轮模数,直径φ依次为0.25mm、0.33mm和0.5mm),孔深依次取齿轮宽度的B/4、B/2和B(B为齿轮宽度,孔深依次取5mm、10mm和20mm);具体参数如表1所示。表1顶孔参数列表样本水平顶孔径向尺寸/mm孔径/mm孔深/mm1157.020.2552160.190.33103163.360.520其次,根据表1参数数据,通过仿真计算齿根弯曲应力值。三组参数,每组参数各三个变量,最终得到27个仿真结果,结果如表2所示。表2顶孔参数列表下的齿根弯曲应力计算结果孔径1孔径2孔径3孔深a孔径b孔径c顶孔径向AA1A2A3AaAbAc顶孔径向BB1B2B3BaBbBc顶孔径向CC1C2C3CaCbCc孔深aa1a2a3———孔径bb1b2b3———孔径cc1c2c3———最后,根据表2计算结果,选取一组“最优保证齿根弯曲强度”的尺寸参数作为顶孔的加工尺寸。底孔尺寸参数信息的计算与顶孔相同,底孔参数计算时依次取0.1πm、0.2πm和0.3πm(πm为齿轮模数与圆周率的乘积,依次为1.58mm、3.16mm和4.74mm)。需要注意的是,底孔的计算需要在顶孔计算完成以后并且以顶孔完成以后的实际结构作为仿真计算模型。图2是顶底双孔齿轮结构的剖面图,图2a到图2d分别是不同孔深下的结构剖面图。以上内容是对本发明所作的进一步详细说明,不能认定本发明的具体实施方式仅限于此,对于本发明所属
技术领域:
的普通技术人员来说,在不脱离本发明构思的前提下,还可以做出若干简单的推演或替换,都应当视为属于本发明由所提交的权利要求书确定发明保护范围。当前第1页1 2 3