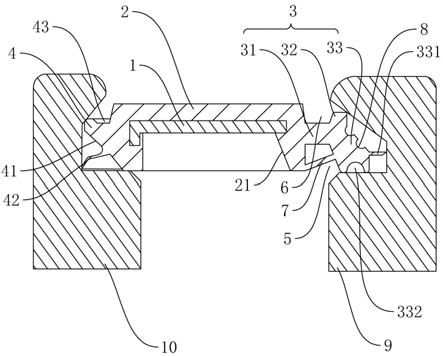
1.本实用新型涉及密封件技术领域,特别涉及一种用于轴承的新型油脂密封圈。
背景技术:2.轴承密封圈是一种安装于轴承内外圈的密封部件,是轴承防尘、防漏脂与温升性能相关的主要影响部件,其结构对性能具有着关键的作用。常见的轴承密封圈一般有单唇、双唇与三唇三种唇结构,在内圈密封槽轴承中,多为双唇与三唇。针对密封圈需具备防尘、防水要求较高的工况,大多现有密封圈是通过加大密封圈内唇与内圈密封槽过盈配合,以达到防尘与防水的效果,但是上述方式在高转速中将会加剧轴承的温升,造成较大的损坏,所以需对传统结构进行优化设计,减小磨损。
技术实现要素:3.本实用新型的目的是提供一种用于轴承的新型油脂密封圈,具有磨损较小、密封效果较好的作用。
4.本实用新型的上述技术目的是通过以下技术方案得以实现的:一种用于轴承的新型油脂密封圈,包括环形的骨架,骨架周围设置有环形的密封橡胶体,密封橡胶体的内圈侧壁设置有内唇,密封橡胶体的外圈侧壁设置有外唇;外唇的外壁与密封橡胶体之间设置有倒角斜面,倒角斜面向外一体成型有密封环,密封环的截面设置为l字形;内唇包括连接部及一体成型于连接部的上内唇和下内唇,连接部连接于密封橡胶体内圈侧壁;下内唇的外侧壁沿径向设置有环形的密封片。
5.通过采用上述技术方案,倒角斜面的设置便于将密封圈安装于外圈轴承的密封槽内,当密封圈外唇安装于密封槽内时,外唇上端与密封槽的斜侧壁相抵实现密封配合,密封环与密封槽的竖直侧壁相抵实现密封配合,当密封圈的内唇安装于内圈轴承的密封槽内时,其主要接触应力来源于内唇的厚度,避免内唇直接与内圈轴承的密封槽接触过盈,便于内圈轴承摩擦力矩的控制。上内唇顶端与密封槽的斜侧壁相抵实现密封配合,下内唇的底端与密封槽的下侧壁相抵紧实现密封配合,且密封片与密封槽的竖直侧壁相抵实现密封配合,如此,外唇与外圈轴承之间具有双道密封的效果,内唇与内圈轴承之间具有三道密封的效果,并且内唇具有磨损补偿功能,能使内唇与内圈轴承密封槽始终保持良好的接触,密封作用较好,从而保证密封圈对防尘、防水、防漏脂性能的要求,且内、外唇与轴承的密封槽间的接触面积较小,轴承转动过程中,磨损较小,使用寿命较长。
6.本实用新型的进一步设置为:外唇与密封橡胶体之间开设有泄压槽,泄压槽环形开设。
7.通过采用上述技术方案,开设泄压槽,在降低外唇翻沿的情况下加大了外唇对外圈轴承密封槽的摩擦力矩,从而可降低密封圈随外圈轴承跟转的可能。
8.本实用新型的进一步设置为:下内唇开设有环形槽,环形槽的两侧端面均设置为圆弧形。
9.通过采用上述技术方案,下内唇的底端与内圈轴承的密封槽底壁间形成双道密封隔离,环形槽可起到暂时的储油作用,密封效果较好,此外,由于环形槽的两侧下端面为圆弧形,圆弧形的顶端与密封槽底壁密封配合,两者之间的接触面积较小,使得轴承转动过程中,相对磨损更小。
10.本实用新型的进一步设置为:密封橡胶体、连接部与下内唇之间形成下端凹槽,密封橡胶体、连接部与上内唇之间形成上端凹槽。
11.本实用新型的进一步设置为:下端凹槽的截面设置为梯形,下端凹槽内设置有若干加强筋,加强筋的一端固定于密封橡胶体外壁,加强筋的另一端固定于下内唇内壁,且加强筋整体倾斜设置。
12.通过采用上述技术方案,加强筋的设置对下内唇具有支撑作用,使得下内唇侧壁的密封片能够与内圈轴承的密封槽竖直壁之间始终具有较好的抵紧力,从而提高密封效果。
13.本实用新型的进一步设置为:下内唇的外侧壁周向开设有储油槽,储油槽位于上内唇与密封片之间。
14.通过采用上述技术方案,当内唇安装于内圈轴承的密封槽内时,下内唇、上内唇和内圈轴承的密封槽之间形成空腔,当内部的油脂经下内唇泄漏至空腔内时,储油槽可起到储油的作用,上内唇未成功阻挡的外部粉尘颗粒也可暂存于空腔中。
15.本实用新型的进一步设置为:储油槽设置为平行的双道储油槽。
16.通过采用上述技术方案,双道储油槽的设置可在一定程度上增大储油量,减小溢油的可能性。
17.本实用新型的进一步设置为:密封橡胶体靠近内唇的内侧壁设置为导油斜面。
18.通过采用上述技术方案,导油斜面的设置可初步阻挡异物进入内圈轴承的密封槽中,导油斜面能有效引导在运转中的油脂回到内圈轴承沟道内,提高防漏脂的性能。
19.综上所述,本实用新型具有以下有益效果:
20.1.采用外唇与外圈轴承之间设置为双道密封,内唇与内圈轴承之间设置为三道密封,并且内唇具有磨损补偿功能,使内唇与内圈轴承密封槽始终保持良好的接触,密封作用较好,从而保证密封圈对防尘、防水、防漏脂性能的要求,且内、外唇与轴承的密封槽间的接触面积较小,轴承转动过程中,磨损较小,使用寿命较长;
21.2.采用在外唇与密封橡胶体间开设泄压槽的方式,在降低外唇翻沿的情况下加大了外唇对外圈轴承密封槽的摩擦力矩,从而可降低密封圈随外圈轴承跟转的可能;
22.3.采用导油斜面的方式,可初步阻挡异物进入内圈轴承的密封槽中,导油斜面能有效引导在运转中的油脂回到内圈轴承沟道内,提高防漏脂的性能。
附图说明
23.图1是实施例的整体结构关系示意图。
24.图2是实施例的另一视角的整体结构关系示意图。
25.图3是实施例的俯视图。
26.图4是图3中a-a截面的剖视图。
27.图5是实施例安装于轴承的部分结构剖视图。
28.图中:1、骨架;2、密封橡胶体;21、导油斜面;3、内唇;31、连接部;32、上内唇;33、下内唇;331、密封片;332、环形槽;4、外唇;41、倒角斜面;42、密封环;43、泄压槽;5、下端凹槽;6、上端凹槽;7、加强筋;8、储油槽;9、内圈轴承;10、外圈轴承。
具体实施方式
29.下面结合附图对本实用新型作进一步的说明。为了便于说明,下面所述的“上”、“下”均与附图5所示方向一致。
30.一种用于轴承的新型油脂密封圈,如图1-5所示,包括有环形的骨架1,骨架1周围设置有环形的密封橡胶体2,密封橡胶体2的内圈侧壁设置有内唇3,密封橡胶体2的外圈侧壁设置有外唇4。
31.如图4和图5所示,外唇4的外壁与密封橡胶体2之间设置有倒角斜面41,倒角斜面41向外一体成型有密封环42,密封环42的截面设置为l字形,外唇4与密封橡胶体2之间开设有泄压槽43,泄压槽43环形开设于上端面;内唇3包括有连接部31及一体成型于连接部31的上内唇32和下内唇33,连接部31的外侧壁连接于密封橡胶体2内圈侧壁;下内唇33的外侧壁沿径向设置有环形的密封片331,下内唇33的下端面开设有环形槽332,环形槽332的两侧端面均设置为圆弧形,密封橡胶体2、连接部31与下内唇33之间形成下端凹槽5,密封橡胶体2、连接部31与上内唇32之间形成上端凹槽6,下端凹槽5的截面设置为梯形,下端凹槽5内设置有若干加强筋7,加强筋7的一端固定于密封橡胶体2外壁,加强筋7的另一端固定于下内唇33内壁,且加强筋7整体倾斜设置,加强筋7的设置对下内唇33具有支撑作用,使得下内唇33侧壁的密封片331能够与内圈轴承9的密封槽竖直壁之间始终具有较好的抵紧力,从而提高密封效果。下内唇33的外侧壁周向开设有平行的双道储油槽8,储油槽8位于上内唇32与密封片331之间。
32.开设泄压槽43,在降低外唇4翻沿的情况下加大了外唇4对外圈轴承10密封槽的摩擦力矩,从而可降低密封圈随外圈轴承10跟转的可能。下内唇33的底端与内圈轴承9的密封槽底壁间形成双道密封隔离,环形槽332可起到暂时的储油作用,密封效果较好,此外,由于环形槽332的两侧端面为圆弧形,圆弧形的顶端与密封槽底壁密封配合,两者之间的接触面积较小,使得轴承转动过程中,相对磨损更小。当内唇3安装于内圈轴承9的密封槽内时,下内唇33、上内唇32和内圈轴承9的密封槽之间形成空腔,当内部的油脂经下内唇33泄漏至空腔内时,储油槽8可起到储油的作用,上内唇32未成功阻挡的外部粉尘颗粒也可暂存于空腔中,双道储油槽8的设置可在一定程度上增大储油量,减小溢油的可能性。
33.如图5所示,密封橡胶体2靠近内唇3的内侧壁设置为导油斜面21,导油斜面21由上至下向密封圈中心倾斜。导油斜面21的设置可初步阻挡异物进入内圈轴承9的密封槽中,导油斜面21能有效引导在运转中的油脂回到内圈轴承9沟道内,提高防漏脂的性能。
34.本实用新型的基本工作原理为:倒角斜面41的设置便于将密封圈安装于外圈轴承10的密封槽内,当密封圈外唇4安装于密封槽内时,外唇4上端与密封槽的斜侧壁相抵实现密封配合,密封环42与密封槽的竖直侧壁相抵实现密封配合,当密封圈的内唇3安装于内圈轴承9的密封槽内时,其主要接触应力来源于内唇3的厚度,避免内唇3直接与内圈轴承9的密封槽接触过盈,便于内圈轴承9摩擦力矩的控制。上内唇32顶端与密封槽的斜侧壁相抵实现密封配合,下内唇33的底端与密封槽的下侧壁相抵紧实现密封配合,且密封片331与密封
槽的竖直侧壁相抵实现密封配合,如此,外唇4与外圈轴承10之间具有双道密封的效果,内唇3与内圈轴承9之间具有三道密封的效果,并且内唇3具有磨损补偿功能,能使内唇3与内圈轴承9密封槽始终保持良好的接触,密封作用较好,从而保证密封圈对防尘、防水、防漏脂性能的要求,且内、外唇与轴承的密封槽间的接触面积较小,轴承转动过程中,磨损较小,使用寿命较长。
35.以上所述仅是本实用新型的较佳实施方式,故凡依本实用新型专利申请范围所述的构造、特征及原理所做的等效变化或修饰,均包括于本实用新型专利申请范围内。