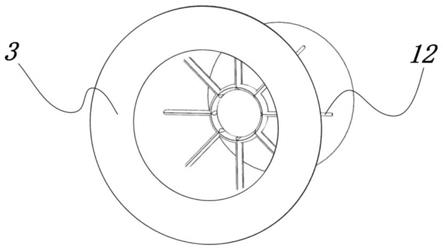
[0001]
本发明属于航空发动机测试系统领域,尤其涉及一种航空发动机进气温度畸变发生器设计方法。
背景技术:[0002]
在航空发动机的实际工作过程中,常常可能由于吸入发射武器的尾流,多机编队飞行时吸入前机的尾流以及火灾救援时吸入燃烧气体或者垂直起降飞机吸入矢量喷管尾流向地面喷射后反弹的高温燃气。当航空发动机在短时间内吸入上述高温气体后推力将下降,稳定工作范围缩小,极端情况还可能导致发动机停车。航空发动机因吸入高温气体在进口平面温度的时间、空间分布不均匀称为进气温度畸变。鉴于上述工作情况,在航空发动机研制和测试阶段,必须依照现有的航空发动机进气温度畸变评定标准对发动机开展温度畸变测试,测试的主要目标包括:确定发动机进口温度畸变的临界参数和评定防喘系统的有效性和可靠性。在航空发动机的测试阶段,只能通过人为方式在地面试车台上模拟制造出不同工况下带有温度畸变的气流输送至发动机以完成测试。这类能够模拟制造出带有温度畸变流场的装置称为温度畸变发生器。温度畸变发生器的性能参数包括:出口面平均温升、临界温升、临界温升响应、高温区范围、面平均温升率、总压损失,总压畸变等。目前,世界各主要航空工业大国均研制并投入使用了多种航空发动机进气温度畸变发生器。根据资料调研,已有的温度畸变发生器依据采用的热源不同,可分为外部热流导入式和嵌入燃烧式两大类。第一类外部热流导入温度畸变发生器是在发动机测试通道外部,利用加热、燃烧以及换热等方式产生高温工质,然后利用布置的管路导入发动机测试通道,最终在发动机气动交界面形成所需温度畸变图谱或者所需温度畸变系数的流场。外部热流导入的温度畸变发生器又可以根据工质的不同分为以下几类:换热器产生的高温空气导入、外部燃烧产生的高温燃气导入和外部高温蒸汽导入。典型的外部热流导入式温度畸变发生器有美国阿诺德工程发展中心研发的多点顺流向高温射流温度畸变发生器,美国海军研究生院研发的高温蒸汽射流温度畸变发生器等。第二类嵌入燃烧式温度畸变发生器在发动机进气道内部设计微型燃烧腔,将气态或液态燃料通过管路导入后通过控制微型燃烧腔的燃烧状态实现发动机入口不同温度畸变流场的生成或者在测试开始前将固体燃料布置于温度畸变发生器燃烧腔,待测试开始时点燃燃料或燃料自燃形成温度畸变流场。典型的嵌入燃烧式温度畸变发生器有美国航空航天局李维斯研究中心研发的氢燃烧温度畸变发生器,中国燃气涡轮研究院研发的氢燃烧温度畸变发生器以及美国弗吉尼亚理工大学研发的丙烷燃烧温度畸变发生器。
[0003]
两类温度畸变发生器各有优缺点,适用范围也不同。第一类外部热流导入式温度畸变发生器的优点在于热流产生的装置位于发动机进气道的外部,进气道内部的热流输送管路和热流喷射装置结构相对简单。并且,由于热流发生装置位于发动机模拟管道外部,高温工质的产生较为安全、操作容易。由于采用管路输送热流,这类模拟技术的缺点也比较突出,对于较大的温度瞬间变化的状态难以生成获得,常用于面平均温升相对较低且需要长
时间测试的情况。第二类嵌入燃烧式温度畸变发生器能够实现面平均温升、畸变范围以及温度瞬变等重要温度畸变参数的模拟,但是,由于微型燃烧腔位于发动机进气道的内部,对温度畸变参数的准确模拟需要独立控制每一个燃烧腔的供油和火焰稳定,结构复杂,控制难度大,常用于对温度畸变周向和径向分布位置精度要求相对较低,但对瞬态温度突变指标有严格要求的短时间测试。
技术实现要素:[0004]
本发明的目的在于解决现有技术中的上述问题,提供一种航空发动机进气温度畸变发生器设计方法,在第一类外部热流导入式温度畸变发生器基础上提出重大改进,克服其高温射流单元喷注方式和喷注位置相对固定导致的高温射流在气动交界面的温升空间分布难以精确控制的缺陷,实现稳态周向和径向温升范围精确单独可控的温度畸变流场生成。
[0005]
为达到上述目的,本发明采用如下技术方案:
[0006]
一种航空发动机进气温度畸变发生器设计方法,包括以下步骤:
[0007]
(1)根据航空发动机进气整流锥最大半径和发动机入口半径,确定进气温度畸变发生器中心支撑环半径和外圆半径,选定径向支杆数量以及单个径向支杆上射流喷嘴数量,计算最小扇形角和最小环形面积,并校验最小扇形角和最小环形面积是否满足设计要求,若不满足设计要求,重新选择径向支杆数量以及单个径向支杆上射流喷嘴数量;
[0008]
(2)利用等面积法计算单个径向支杆上射流喷嘴所处位置的半径;
[0009]
(3)选定径向支杆截面翼型参数和翼型宽度;
[0010]
(4)根据最大半径处射流喷嘴位置计算最大扩张角相交线位置,并判断是否满足相交条件,若不满足相交条件,则回到步骤(1),重新选择径向支杆数量以及单个径向支杆上射流喷嘴数量,或者回到步骤(3),重新选定径向支杆截面翼型参数和宽度;
[0011]
(5)计算并判断堵塞度,若堵塞度大于35%,则回到步骤(1),重新选择径向支杆数量以及单个径向支杆上射流喷嘴数量;
[0012]
(6)通过缩比模型风洞试验或者计算机数值模拟校验性能,若性能不满足设计要求,则回到步骤(1),重新选择径向支杆数量以及单个径向支杆上射流喷嘴数量,或者回到步骤(3),重新选定径向支杆截面翼型参数和翼型宽度;
[0013]
(7)性能校验合格,设计完成。
[0014]
所述航空发动机进气温度畸变发生器安装于进气道内,其包括中心支撑环、多个径向支杆和通气管;所述径向支杆连接于中心支撑环的外周,二者完全包裹于进气道内部;所述通气管插于径向支杆的末端,通气管的末端接口位于进气道的外部并连接高温工质生成器,用于将高温工质引向径向支杆。
[0015]
所述通气管上开设有射流孔,所述径向支杆上设有与射流孔对应的射流喷嘴。
[0016]
所述径向支杆上设有安装口,所述射流喷嘴可拆卸插接于安装口内。
[0017]
所述射流喷嘴的喷射通道尺寸由入口到出口处逐渐扩张或等直设置。
[0018]
所述中心支撑环和径向支杆的横截面为翼型,以减小气动阻力。
[0019]
所述中心支撑环与径向支杆的横截面的翼型参数和翼型宽度相同。
[0020]
相对于现有技术,本发明技术方案取得的有益效果是:
[0021]
本发明基于高温工质射流原理,提出利用可替换射流喷嘴,向发动机通道中注入高温热源,在不改变温度畸变发生器基本结构的前提下实现高温区周向和径向空间分布单独可控,利用该方法设计得到的温度畸变发生器可以满足多种状态下航空发动机温度畸变测试需求,并节约大量测试成本,缩短航空发动机温度畸变的测试周期。
附图说明
[0022]
图1为航空发动机进气温度畸变测试试验台示意图;
[0023]
图2为航空发动机与进气道示意图;
[0024]
图3为未安装进气温度畸变发生器时航空发动机入口顺进气方向正视图;
[0025]
图4为安装进气温度畸变发生器后进气道剖视图;
[0026]
图5为进气温度畸变发生器示意图;
[0027]
图6为进气温度畸变发生器径向支杆与射流喷嘴安装示意图;
[0028]
图7为安装射流喷嘴后的温度畸变发生器逆流向视图;
[0029]
图8为通气管示意图;
[0030]
图9为进气温度畸变发生器径向支杆喷射高温工质示意图;
[0031]
图10为进气温度畸变发生器安装于进气道内示意图;
[0032]
图11为进气温度畸变发生器安装于进气道中顺进气方向正视图;
[0033]
图12为单个径向支杆射流喷嘴喷射能够影响的周向高温区范围示意图;
[0034]
图13为同一半径位置的射流喷嘴喷射能够影响的径向高温区范围示意图;
[0035]
图14为单个径向支杆射流喷嘴全部开启时气流流动示意图;
[0036]
图15为单个径向支杆射流喷嘴部分开启时气流流动示意图;
[0037]
图16为不同扩张角的射流喷嘴示意图;
[0038]
图17为径向支杆横截面与气动交界面相对位置示意图;
[0039]
图18为径向支杆横截面示意图;
[0040]
图19为同一半径位置相邻射流喷嘴横截面沿圆周方向展开示意图;
[0041]
图20为本发明设计方法流程图。
具体实施方式
[0042]
为了使本发明所要解决的技术问题、技术方案及有益效果更加清楚、明白,以下结合附图和实施例,对本发明做进一步详细说明。
[0043]
图1所示为航空发动机进气温度畸变测试试验台示意图,(1)为试车台支架,被测试的航空发动机(2)和进气道(3)安装于推力导轨(4)上,推力导轨(4)安装于试车台支架(1)上,在航空发动机测试过程中,航空发动机(2),进气道(3)连同推力导轨(4)可沿发动机轴线方向小范围前后移动,(5)为测试时吸入航空发动机的空气流动方向。
[0044]
图2所示为航空发动机(2)与进气道(3)示意图,发动机地面测试所采用的进气道(3)的基本结构为喇叭形进气口,等直圆形截面管道,进气道(3)直接与发动机(2)对接,在进气道与发动机之间存在一个人为定义的气动交界面(6),如图2中的虚线所示。气动交界面(6)定义进气道(3)出口与发动机(2)入口的分界面位置,同时气动交界面(6)也是航空发动机进气温度畸变参数测量平面的位置。
[0045]
图3所示为未安装进气温度畸变发生器时航空发动机入口顺进气方向正视图,(7)为发动机进气整流锥最大半径,用r1表示,(8)为发动机入口半径,用r2表示,r1和r2为航空发动机固有参数。
[0046]
图4所示为安装进气温度畸变发生器后进气道剖视图,进气温度畸变发生器(9)安装于进气道(3)内部的等直段,位于进气道的喇叭进气口与气动交界面(6)之间。
[0047]
图5所示为进气温度畸变发生器示意图,温度畸变发生器的基本结构由中心支撑环(10)和多个径向支杆(11)组成,中心支撑环(10)和径向支杆(11)的横截面为翼型,目的是减小气动阻力,且中心支撑环(10)与径向支杆(11)横截面的翼型参数和翼型宽度相同。在每一个径向支杆(11)的末端都插入通气管(12),通气管(12)将外部高温工质引入径向支杆。
[0048]
图6所示为进气温度畸变发生器径向支杆与射流喷嘴安装示意图,径向支杆(11)为固定件,射流喷嘴(13)为可替换件,可以根据不同的测试要求进行替换。
[0049]
图7所示为安装射流喷嘴后的温度畸变发生器逆流向视图,射流喷嘴(13)只安装于径向支杆(11)上,中心支撑环(10)上不安装射流喷嘴。
[0050]
图8为通气管(12)示意图,通气管(12)上的射流孔(14)位置与径向支杆(11)上射流喷嘴(13)位置对应。
[0051]
图9所示为进气温度畸变发生器径向支杆喷射高温工质示意图,高温工质(15)由外部生成器生成,可以为加热后的高温空气,高温燃气或高温蒸汽,高温工质(15)先经过通气管(12)引入径向支杆(11),然后通过射流孔(14)进入射流喷嘴(13),最终喷注至进气道中,与发动机吸入的空气掺混,产生温度畸变流场。
[0052]
图10所示为进气温度畸变发生器安装于进气道内示意图,进气温度畸变发生器(9)安装于进气道(3)内部后,中心支撑环(10)和径向支杆(11)结构完全被包裹于进气道通道内部,通气管(12)的末端接口位于进气道(3)外部,用于连接高温工质生成器。
[0053]
图11所示为进气温度畸变发生器安装于进气道中顺进气方向正视图,(16)为进气温度畸变发生器中心支撑环半径,用rd1表示,(17)为进气温度畸变发生器外圆半径,用rd2表示。
[0054]
图12中(18)为单个径向支杆射流喷嘴喷射能够影响的周向高温区范围,此参数为设计要求,用δθ表示,单位为度。
[0055]
图13所示为同一半径位置的射流喷嘴喷射能够影响的径向高温区范围示意图,(19)为射流喷嘴分布位置的半径,用r(i)表示,(20)为径向影响范围,此参数为设计要求,用δs表示,单位为平方米。
[0056]
图14所示为单个径向支杆射流喷嘴全部开启时气流流动示意图,高温工质(15)通过通气管(12)进入径向支杆(11),进一步,高温工质(15)从射流孔(14)进入射流喷嘴(13),在射流喷嘴(13)中进一步膨胀后喷出,与发动机吸入的空气掺混,最终在气动交界面(6)形成温度畸变流场,(21)为射流喷嘴中心线,(22)为发动机中心线。
[0057]
图15所示为单个径向支杆射流喷嘴部分开启时气流流动示意图,在某些测试状态下,单个径向支杆(11)上的射流喷嘴(13)不需要全部开启,在对应位置放入实心射流喷嘴堵塞高温工质,同时,与实心射流喷嘴对应位置的通气管(12)无射流孔。
[0058]
图16所示为不同扩张角的射流喷嘴(13)示意图,喷嘴入口半径相同,出口扩张角
介于零度和和最大扩张角之间,最大扩张角用amax表示,图16中从左向右三个射流喷嘴(13)扩张角由amax逐渐减小至零度,实心射流喷嘴为射流喷嘴的特例,起堵塞气流的作用,无扩张角参数。
[0059]
图17所示为径向支杆横截面与气动交界面相对位置示意图,(23)为翼型前缘与气动交界面(6)之间的距离,用l1表示,(23)为固定设计参数,由测试需求方提供。
[0060]
图18所示为径向支杆(11)横截面示意图,径向支杆(11)的横截面形状为翼型,其基本设计参数为翼型和翼型宽度(24),翼型宽度(24)用l2表示,翼型可以通过nasa的翼型数据库查询获得,推荐采用00系列对称翼型,减小气动阻力。(25)为翼型最大厚度,用h1表示,翼型最大厚度在选定翼型参数后自动确定。(26)为径向支杆中心圆半径,用r3表示,且r3小于翼型最大厚度h1(25),为了保证结构强度,推荐r3=(0.9~0.95)
×
(h1/2),(27)为中心圆与翼型尾缘之间的距离,用l3表示,推荐l3=(0.6~0.65)
×
l2。
[0061]
图19所示为同一半径位置相邻射流喷嘴横截面沿圆周方向展开示意图,(28)为射流喷嘴内径,用rd3表示,射流喷嘴内径(28)与射流孔(14)半径相同,为设计参数,(29)为射流喷嘴外径,用rd4表示,射流喷嘴直径与翼型最大厚度(25)相同,即rd4=h1/2,(30)为射流喷嘴长度,用ls表示,射流喷嘴长度(30)与中心圆和翼型尾缘之间的距离相同,即ls=l3,(31)为射流喷嘴与气动交界面(6)之间的距离,用ld表示,且ld=l1-l2,(32)为同一半径位置相邻射流喷嘴沿圆周方向展开后中心线(21)之间的距离,用h2表示,且h2=2π
×
r(nr)/nc,r(nr)为射流喷嘴的最大半径,nc为径向支杆(11)数量,nr为单个径向支杆上射流喷嘴(13)数量,(33)为射流喷嘴最大扩张角amax,(34)为喷管最大扩张角延长线,(35)为射流喷嘴最大扩张角下扩张角延长线(34)和气动交界面(6)交点与射流喷嘴中心线(21)与气动交界面(6)交点之间的距离,用h3表示。
[0062]
如图20所示,本发明一种航空发动机进气温度畸变发生器设计方法流程包括以下步骤:
[0063]
步骤一:根据航空发动机进气整流锥最大半径r1(7)和发动机入口半径r2(8),确定进气温度畸变发生器中心支撑环半径rd1(16)和进气温度畸变发生器外圆半径rd2(17),其中,rd1=1.05
×
r1,rd2=r2。根据进气温度畸变测试空间分辨率的要求,选定径向支杆(11)的数量nc和单个径向支杆上的射流喷嘴(13)数量nr,计算最小周向扇形角θi和最小圆环面积si,其中θi=360/nc,单位为度,si=π
×
(rd2
2-rd1
2
)/(nr+1),判断最小周向扇形角θi是否小于等于设计要求中的单个径向支杆周向影响范围δθ(18)以及判断最小环形面积si是否小于等于设计要求中的同一半径位置的射流喷嘴喷射能够影响的径向高温区范围δs(20),若两个校验判断均满足,进行步骤二,若其中一个校验不满足,则重新选定径向支杆(11)数量nc和单个径向支杆上射流喷嘴(13)数量nr。
[0064]
步骤二:利用等面积法计算单个径向支杆上射流喷嘴分布位置的半径r(i)(19),其中
[0065]
步骤三:选定径向支杆截面翼型参数,其中翼型参数包括二维翼型横坐标x(x1,x2,x3,
…
,xn)和翼型纵坐标y(y1,y2,y3,
…
,yn),n为坐标点个数,二维翼型参数坐标通常选用naca 4位数对称系列翼型(naca4-digit symmetrical airfoil),翼型坐标可以通过
公开文献查询获得,查询得到的翼型横纵坐标为无量纲参数,x坐标范围为0~1,选定翼型宽度l2(24),基准翼型真实坐标x0和y0即可确定,其中x0=x
×
l2,y0=y
×
l2,获得基准翼型真实坐标x0和y0后通过计算机三维建模设计得到进气温度畸变发生器的三维型面。
[0066]
步骤四:根据最大半径处射流喷嘴位置计算最大扩张角相交线位置,如图19所示,根据射流喷嘴内径rd3(28),射流喷嘴外径rd4(29),射流喷嘴长度ls(30),射流喷嘴与气动交界面之间的距离ld(31)四个参数计算射流喷嘴最大扩张角下扩张角延长线(34)和气动交界面(6)交点与射流喷嘴中心线(21)与气动交界面(6)交点之间的距离h3(35),计算方法为首先根据式:计算得到最大扩张角amax,然后根据式:h3=rd3+tan(amax)
·
(l1-l2+l3)计算得到h3(35),最大半径处两相邻喷嘴的最大扩张角延长线(34)需要相交才能保证高温射流工质对所有空间区域的覆盖,因此,需要判断h2和h3之间的关系,当2
×
h3≥h2时,相邻喷嘴的最大扩张角延长线在气动交界面处可以相交,设计合格,若2
×
h3<h2,则相邻喷嘴的最大扩张角延长线在气动交界面处不相交,设计不合格,回到步骤一,重新选定径向支杆(11)数量nc和单个径向支杆上射流喷嘴(13)数量nr,或者回到步骤三,重新选定径向支杆截面翼型参数和翼型宽度l2(24)。
[0067]
步骤五:估算进气温度畸变发生器堵塞度,堵塞度的计算方法为:若最大堵塞度du大于35%,则回到步骤一,重新选定径向支杆(11)数量nc和单个径向支杆上射流喷嘴(13)数量nr。
[0068]
步骤六:若最大堵塞度du小于等于35%,通过缩比模型风洞试验或者计算机数值模拟校验性能,性能参数包括高温区范围和面平均温升,若性能不满足设计要求,则回到步骤一,重新选定径向支杆(11)数量nc和单个径向支杆上射流喷嘴(13)数量nr,或者回到步骤三,重新选定径向支杆截面翼型参数和翼型宽度l2(24)。
[0069]
步骤七:若校验合格,则完成设计。
[0070]
本发明的工作原理如下:
[0071]
基于高温工质射流原理,将在发动机进气道外部生成的高温工质,如高温空气、高温燃气或高温蒸汽通过通气管导入进气温度畸变发生器中,再利用进气温度畸变发生器上延周向和径向分布的射流喷嘴将高温工质喷入进气道中,高温工质与进气道中的常温空气发生掺混,实现局部高温区的生成,最终获得测试所需的温度畸变流场。本发明的特征在于,在不同的温度畸变测试中,温度畸变流场高温区的分布不同,利用通气管上不同位置射流孔的开和关以实现对应空间位置高温射流的开和关,再利用不同扩张角的可替换射流喷嘴实现射流开启的情况下高温区分布大小的调节。在不同的测试状态中,仅需替换所需的通气管和射流喷嘴即可生成不同空间位置分布的温度畸变流场。