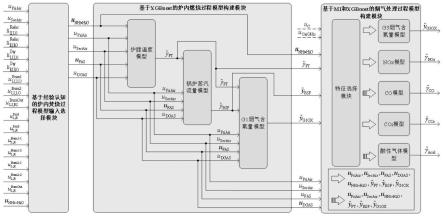
1.本发明涉及城市固体废物处理技术领域,特别是涉及一种面向控制的数据驱动城市固废焚烧全流程建模方法。
背景技术:2.城市固体废物(municipal solid waste incineration,msw)是导致我国城市污染问题逐渐严重的一个主要因素,伴随着国家对垃圾分类的逐渐重视,其热值逐渐提高,使得msw焚烧(municipal solid waste incineration,mswi)技术成为处理msw的一个重要手段。相较于其他处理手段,具有无害化、减量化和资源化等特点的mswi技术能够节约大量土地资源,具有明显的社会效益,经济效益和环境效益。但国内mswi技术多引进于国外,使得国内mswi电厂自动燃烧控制(automatic combustion control,acc)系统难以稳定运行,目前多依靠领域专家手动维护。领域专家依据专家经验,结合mswi过程运行监控状况,面对已出现的问题进行控制,从而保证mswi电厂安全稳定运行。然而,根据专家经验的不同,解决问题的控制手段与及时性难以得到保证,会导致mswi过程控制效率较低、污染物排放可能存在短期超标等问题,因此研究mswi过程智能化控制成为首要解决的问题。
3.mswi过程全流程建模,由于其机理复杂,多采用计算流体动力学(computational fluid dynamics,cfd)软件方式进行研究。然而已有研究多针对炉膛内部进行研究建模,同时大多数cfd软件多应用于建厂前,对现有运行中的工厂指导性较小。因此,设计一种面向控制的数据驱动城市固废焚烧全流程建模方法是十分有必要的。
技术实现要素:4.本发明的目的是提供一种面向控制的数据驱动城市固废焚烧全流程建模方法,能够实现全流程模型搭建,为现有运行中的工厂进行指导,能够为后续mswi过程先进智能优化控制算法的研究提供参考。
5.为实现上述目的,本发明提供了如下方案:
6.一种面向控制的数据驱动城市固废焚烧全流程建模方法,包括如下步骤:
7.步骤1:搭建mswi全流程模型,其中,mswi全流程模型包括炉内燃烧过程模型输入选择模块、炉内燃烧过程模型构建模块及烟气处理过程模型构建模块,所述炉内燃烧过程模型输入选择模块连接所述炉内燃烧过程模型构建模块,所述炉内燃烧过程模型构建模块连接所述烟气处理过程模型构建模块;
8.步骤2:基于梯次串并联训练机制对mswi全流程模型进行训练。
9.可选的,步骤1中,搭建mswi全流程模型,具体为:
10.搭建基于经验认知的炉内燃烧过程模型输入选择模块,根据领域专家的经验认知选择炉内燃烧过程模型的输入,其中,包括炉排速度、燃烧空气流量及sncr系统;
11.通过控制推料器速度及干燥炉排阶段速度对炉排速度进行控制,对炉内燃烧过程模型的输入进行简化,将推料器速度u
fas
及干燥炉排阶段速度u
dgas
取均值处理,得到:
[0012][0013][0014]
燃烧空气流量由一次风流量及二次风流量组成,根据领域专家的经验将一次风挡板开度设定为固定比例,将一次风流量u
priair
及二次风流量u
secair
作为风量输入特征;
[0015]
通过控制氨水的入炉量控制sncr系统,根据sncr系统在mswi过程中实际喷入位置,将氨水入炉量加入炉内燃烧过程的炉膛温度模型作为输入特征,最终得到炉内燃烧过程模型的基本输入特征为:
[0016][0017]
可选的,步骤1中,搭建mswi全流程模型,具体为:
[0018]
搭建基于xgboost的炉内燃烧过程模型构建模块,其中,炉内燃烧过程模型构建模块包括炉膛温度模型、锅炉蒸汽流量模型及g1烟气含氧量模型,炉膛温度模型的输出连接锅炉蒸汽流量模型及g1烟气含氧量模型,锅炉蒸汽流量模型的输出连接g1烟气含氧量模型,炉膛温度模型、锅炉蒸汽流量模型及g1烟气含氧量模型的输出连接烟气处理过程模型构建模块;
[0019]
搭建炉膛温度模型,具体为:基于炉内燃烧过程模型的基本输入特征,确定ft模型为:
[0020][0021]
结合ft模型,基于xgboost搭建炉膛温度模型,利用在xgboost的损失函数中引入正则项的方式控制模型的复杂度,xgboost的损失函数可表示为:
[0022][0023]
式中,c
xgboost
表示xgboost模型中下一个基学习器的预测值,表示xgboost模型中第j个基学习器的预测值,将损失函数进行泰勒展开,分解得到:
[0024][0025]
对其进行简化,将一阶导数和二阶导数简写为g和h,得到:
[0026][0027]
根据简化后的公式得到:
[0028][0029]
删除无输出值的项,得到:
[0030][0031]
并对其求导,令上式导数等于0,得到最优解为:
[0032][0033]
重复上述操作,直至基学习器数量达到设定值,确定炉膛温度模型为:
[0034][0035]
搭建锅炉蒸汽流量模型,具体为:在炉膛温度模型的基础上,加入作为模型输入,确定锅炉蒸汽流量模型为:
[0036][0037]
搭建g1烟气含氧量模型,具体为:在锅炉蒸汽流量模型的基础上,加入作为模型输入,确定g1烟气含氧量模型为:
[0038][0039]
可选的,步骤1中,搭建mswi全流程模型,具体为:
[0040]
搭建基于mi和xgboost的烟气处理过程模型构建模块,将烟气处理过程模型的输入特征表示为:
[0041][0042]
其中,u
fgcp
={uc,u
ca(oh)2
}为常值,将其删去,得到烟气处理过程模型的输入特征为:
[0043][0044]
结合互信息及mswi过程机理,对输入特征进筛选,最终确定烟气处理过程模型为:
[0045][0046][0047][0048][0049][0050]
可选的,步骤2中,基于梯次串并联训练机制对mswi全流程模型进行训练,具体为:
[0051]
对炉内燃烧过程模型进行梯次串行训练,即在炉膛温度模型训练完成后,将炉膛温度模型的输出输入至锅炉蒸汽流量模型,进行训练,训练完成后,将锅炉蒸汽流量模型的输出输入至g1烟气含氧量模型进行训练,完成训练;
[0052]
在炉内燃烧过程模型训练完毕后,对其输出进行特征选择,对烟气处理过程模型进行并行训练,训练完毕后,确定最终的基于梯次串并联训练机制的mswi全流程模型。
[0053]
根据本发明提供的具体实施例,本发明公开了以下技术效果:本发明提供的面向控制的数据驱动城市固废焚烧全流程建模方法,首先,基于经验认知,对炉内焚烧过程模型的输入特征进行选择;接着,利用xgboost构建炉内焚烧过程串联模型;然后,基于互信息分析结果选择烟气处理过程模型输入特征,进行相关建模;最后,梯次训练所提出的全流程串并联模型;通过工厂实际运行数据验证了所提模型的有效性,为后续mswi过程先进智能优化控制算法的研究提供了参考。
附图说明
[0054]
为了更清楚地说明本发明实施例或现有技术中的技术方案,下面将对实施例中所需要使用的附图作简单地介绍,显而易见地,下面描述中的附图仅仅是本发明的一些实施例,对于本领域普通技术人员来讲,在不付出创造性劳动性的前提下,还可以根据这些附图获得其他的附图。
[0055]
图1为本发明实施例面向控制的数据驱动城市固废焚烧全流程建模方法流程示意图;
[0056]
图2为mswi电厂工艺流程图;
[0057]
图3a为操作变量与炉内燃烧过程中炉膛温度之间的相关系数图;
[0058]
图3b为操作变量与炉内燃烧过程中锅炉蒸汽流量之间的相关系数图;
[0059]
图3c为操作变量与炉内燃烧过程中g1部分烟气含氧量之间的相关系数图;
[0060]
图4a为操作变量与烟气处理过程中g3部分烟气含氧量之间的相关系数图;
[0061]
图4b为操作变量与烟气处理过程中g3部分nox含量之间的相关系数图;
[0062]
图4c为操作变量与烟气处理过程中g3部分co含量之间的相关系数图;
[0063]
图4d为操作变量与烟气处理过程中g3部分co2含量之间的相关系数图;
[0064]
图4e为操作变量与烟气处理过程中g3部分酸性气体含量之间的相关系数图;
[0065]
图5为mswi全流程模型结构示意图;
[0066]
图6为mswi全流程模型训练过程示意图;
[0067]
图7a为操作变量与烟气处理过程中g3部分烟气含氧量的mi评价结果示意图;
[0068]
图7b为操作变量与烟气处理过程中g3部分nox含量的mi评价结果示意图;
[0069]
图7c为操作变量与烟气处理过程中g3部分co含量的mi评价结果示意图;
[0070]
图7d为操作变量与烟气处理过程中g3部分co2含量的mi评价结果示意图;
[0071]
图7e为操作变量与烟气处理过程中g3部分酸性气体含量的mi评价结果示意图;
[0072]
图8a为炉膛温度测试结果示意图;
[0073]
图8b为锅炉蒸汽流量测试结果示意图;
[0074]
图8c为g1部分烟气含氧量测试结果示意图;
[0075]
图8d为g3部分烟气含氧量测试结果示意图;
[0076]
图8e为g3部分nox含量测试结果示意图;
[0077]
图8f为g3部分co含量测试结果示意图;
[0078]
图8g为g3部分co2含量测试结果示意图;
[0079]
图8h为g3部分酸性气体含量测试结果示意图;
[0080]
图9为mswi过程互信息结果示意图;
[0081]
图10为mswi过程关键被控变量全流程控制过程示意图。
具体实施方式
[0082]
下面将结合本发明实施例中的附图,对本发明实施例中的技术方案进行清楚、完整地描述,显然,所描述的实施例仅仅是本发明一部分实施例,而不是全部的实施例。基于本发明中的实施例,本领域普通技术人员在没有做出创造性劳动前提下所获得的所有其他实施例,都属于本发明保护的范围。
[0083]
本发明的目的是提供一种面向控制的数据驱动城市固废焚烧全流程建模方法,能够实现全流程模型搭建,为现有运行中的工厂进行指导,能够为后续mswi过程先进智能优化控制算法的研究提供参考。
[0084]
为使本发明的上述目的、特征和优点能够更加明显易懂,下面结合附图和具体实施方式对本发明作进一步详细的说明。
[0085]
如图1所示,本发明实施例提供的面向控制的数据驱动城市固废焚烧全流程建模方法,包括如下步骤:
[0086]
步骤1:搭建mswi全流程模型,其中,mswi全流程模型包括炉内燃烧过程模型输入选择模块、炉内燃烧过程模型构建模块及烟气处理过程模型构建模块,所述炉内燃烧过程模型输入选择模块连接所述炉内燃烧过程模型构建模块,所述炉内燃烧过程模型构建模块连接所述烟气处理过程模型构建模块;
[0087]
步骤2:基于梯次串并联训练机制对mswi全流程模型进行训练。
[0088]
某mswi电厂工艺流程如图2所示,msw由车辆运输,经地磅称重后排入固废池,经过3~7天的生物发酵和脱水后,固废池中的msw由抓斗投入到料斗中;然后,进料器将msw推至炉排,经过干燥、燃烧、烧烬三个阶段后,燃烧过程为保证高温烟气中的有害物质充分分解和燃烧,烟气温度应控制在850℃以上,烟气停留2秒以上和足够的烟气湍流度;之后,高温烟气进入余热锅炉,换热产生的高温蒸汽带动汽轮发电机组发电;随后,与石灰和活性炭混合的烟气进入脱酸反应器,发生中和反应,吸附烟气中的dxn和重金属;接下来,在袋式除尘器中去除烟气颗粒、中和反应物和活性炭吸附剂;最后,含有粉尘、co、nox、so2、hcl、hf、hg、cd和dxn等其他物质的废气通过烟囱排入大气,焚烧产生的灰渣通过捞渣机输送至渣坑后由车辆运输至指定地点填埋。
[0089]
为实现msw处理过程最小无害化风险的目的,现有mswi过程控制主要遵循“3t+e”原则,即炉膛温度大于850℃、烟气停留时间大于2秒、一定的烟气湍流强度以及充足的空气量。“3t+e”原则能有效确保燃烧过程产生的有害物质得到充分分解,从源头处控制酸性气体、dxn的生成。受限于国内外mswi电厂的差异性和msw组分的不确定性,目前国内acc系统难以正常运行,主要依赖于领域专家手动控制方式,如图10所示。
[0090]
其中:
[0091]
γ
g3
={γ
nox
,γ
co
,γ
co2
,γ
acid
}
ꢀꢀꢀꢀꢀꢀꢀꢀꢀꢀꢀ
(1)
[0092][0093][0094][0095]
图例含义为:为流量检测仪表,为蒸汽检测仪表,为氧气含量检测仪表,为烟气检测仪表,为温度检测仪表,为剂量控制器,为变频器控制器,为炉排速度控制器,为挡板开度控制器;
[0096]
符号物理含义为:r
max
为设定目标上限,r
min
为设定目标下限,r
*
为设定目标值,w
speed
为炉排速度设定值,w
baffle
为一次风挡板开度设定值,w
priair
为一次风流量设定值,w
secair
为二次风流量设定值,为进料器左内、左外、右内、右外速度设定值,为干燥炉排左内、左外、右内、右外速度设定值,为燃烧1段炉排左内、左外、右内、右外速度设定值,为燃烧2段炉排左内、左外、右内、右外速度设定值,为燃烬炉排左内、右内速度设定值,为干燥炉排1段左、右进风管道挡板开度设定值,为干燥炉排2段左、右进风管道挡板开度设定值,为燃烧炉排1-1段左、右进风管道挡板开度设定值,为燃烧炉排1-2段左、右进风管道挡板开度设定值,为燃烧炉排2-1段左、右进风管道挡板开度设定值,为燃烧炉排2-2段左、右进
风管道挡板开度设定值,为燃烬炉排左、右进风管道挡板开度设定值,w
priair
为一次风流量设定值,w
secair
为二次风流量设定值,w
nh3
·
h2o
为氨水喷入量设定值,wc为活性炭设定值,w
ca(oh)2
为消石灰设定值,为进料器左内、左外、右内、右外速度控制机构控制量,为干燥炉排左内、左外、右内、右外速度控制机构控制量,为燃烧1段炉排左内、左外、右内、右外速度控制机构控制量,为燃烧2段炉排左内、左外、右内、右外速度控制机构控制量,为燃烬炉排左内、右内速度控制机构控制量,为干燥炉排1段左、右进风管道挡板开度控制机构控制量,为干燥炉排2段左、右进风管道挡板开度控制机构控制量,为燃烧炉排1-1段左、右进风管道挡板开度控制机构控制量,为燃烧炉排1-2段左、右进风管道挡板开度控制机构控制量,为燃烧炉排2-1段左、右进风管道挡板开度控制机构控制量,为燃烧炉排2-2段左、右进风管道挡板开度控制机构控制量,为燃烬炉排左、右风管挡板开度控制机构控制量,u
priair
为一次风流量控制机构控制量,u
secair
为二次风流量控制机构控制量,u
nh3
·
h2o
为氨水控制机构控制量,uc为活性炭控制机构控制量,u
ca(oh)2
为消石灰控制机构控制量,为炉排温度检测值,为干燥炉排左内、左外、右内、右外温度检测值,为燃烧1段炉排左内、左外、右内、右外温度检测值,为燃烧2段炉排左内、左外、右内、右外温度检测值,为燃烬炉排左内、右内温度检测值,为干燥炉排1段左、右进风管道挡板开度检测值,为干燥炉排2段左、右进风管道挡板开度检测值,为燃烧炉排1-1段左、右进风管道挡板开度检测值,为燃烧炉排1-2段左、右进风管道挡板开度检测值,为燃烧炉排2-1段左、右进风管道挡板开度检测值,为燃烧炉排2-2段左、右进风管道挡板开度检测值,为燃烬炉排左、右进风管道挡板开度检测值,y
priair
为一次风流量检测值,y
secair
为二次风流量检测值,y
ft
为炉膛温度检测值,y
bsf
为锅炉蒸汽流量检测值,y
g1ox
为g1部分烟气含氧量检测值,y
g3ox
为g3部分烟气含氧量检测值,γ
g3
为g3部分污染物浓度,γ
nox
为g3部分nox含量,γ
co
为g3部分co含量,γ
co2
为g3部分co2含量,γ
acid
为g3部分酸性气体含量。
[0097]
由图10可知,mswi流程的输入可表示为:
[0098][0099]
其中,u
fcp
和u
fgcp
分别表示炉内燃烧过程和烟气处理过程的控制输入,具体如下:
[0100][0101]ufgcp
={uc,u
ca(oh)2
}
ꢀꢀꢀꢀꢀꢀꢀꢀꢀꢀꢀ
(7)
[0102]
领域专家手动控制策略如下:
[0103]
步骤1:根据生产需求与污染排放指标,领域专家依据丰富的专家经验对mswi过程中关键被控变量进行经验设定;
[0104]
步骤2:根据经验设定的目标设定值和范围,各回路控制机构进行运算得到对应执行机构的控制量,输入至mswi过程中以达到稳定运行的目的;
[0105]
步骤3:根据物理检测设备对被控变量的检测结果,各种检测信息通过集散控制系统(distributed control system,dcs)系统上传至监控室大屏实现实时在线监测,实现生成报表、显示数据趋势和报警等功能
[0106]
步骤4:根据实时在线监测结果,领域专家结合专家经验,针对当前运行工况进行判断和决策,通过循环步骤1~步骤3,从而保证mswi过程稳定运行。
[0107]
由上可知,领域专家感知的过程可描述为:
[0108][0109]
可见,依赖于领域专家的焚烧运行控制存在较大随意性和滞后性等问题,从而导致mswi过程控制效率低。由于实际工业现场的安全性和mswi过程的复杂性,智能优化控制算法难以直接应用于实际工业现场,因此为研究炉内燃烧过程的被控变量的控制算法和烟气处理过程污染物排放指标的优化,本发明提出了mswi全流程模型。
[0110]
根据mswi流程,将其分为两部分:炉内燃烧过程和烟气处理过程。炉内燃烧过程包含炉膛温度(furnace temperature,ft)、锅炉蒸汽流量(boiler steam flow,bsf)和g1部分烟气含氧量(oxygen content offlue gas in g1 part,g1ox);烟气处理过程包含g3部分烟气含氧量(oxygen content offlue gas in g3 part,g3ox)、g3部分nox含量(g3nox)、g3部分co含量(g3co)、g3部分co2含量(g3co2)和g3部分酸性气体含量(g3acid)。
[0111]
1)炉内燃烧过程
[0112]
采用皮尔逊相关系数(pearson correlation coefficient,pcc)对操作变量与炉内燃烧过程关键被控变量之间的关系进行因素分析,具体结果如图3所示。其中蓝色条形柱表示正相关关系,红色形柱表示负相关关系,绝对值大小表示相关性强度;
[0113]
由图3可知,各操作变量与炉内燃烧过程关键被控变量之间存在不同的正负相关关系,且相同操作变量在不同关键被控变量中正负相关性不同,如二次风与ft存在正相关关系,与bsf和g1ox存在负相关关系;操作变量与ft、bsf之间的相关性强于g1ox。
[0114]
2)烟气处理过程
[0115]
烟气处理过程关键被控变量与操作变量之间的相关性如图4所示。其中蓝色条形柱表示正相关关系,红色形柱表示负相关关系,绝对值的大小表示相关性强度;
[0116]
由图4可知,相比于炉内焚烧过程,g3部分关键被控变量/污染物排放浓度与操作变量的相关性较弱,其pcc绝对值普遍在0.2以内,且同样存在相同操作变量在不同关键被控变量/污染物排放浓度中贡献度不一致的情况;但操作变量对nox含量的影响强于其他关键被控变量/污染物排放浓度;
[0117]
综上所述,mswi全流程关键被控变量/污染物排放浓度与操作变量的关系复杂,难以依据流程顺序简单选择模型输入特征,因此,本发明针对mswi过程不同部分的关键被控变量/污染物排放浓度模型输入特征进行区分筛选。
[0118]
如图5所示,根据北京某mswi电厂工艺流程,采用本发明提出的面向控制的数据驱动城市固废焚烧全流程建模方法,建立面向控制的数据驱动mswi全流程模型,包含基于经验认知的炉内焚烧过程模型输入选择模块、基于xgboost的炉内燃烧过程模型构建模块和基于mi和xgboost的烟气处理过程模型构建模块,其中氨水、活性炭和消石灰作为有害物质去除试剂,根据实际喷入位置添加进模型输入特征;
[0119]
其中,u
fas
和u
dgas
分别表示进料器均速和干燥炉排均速控制量,u
nh3
·
h2o
表示氨水注入量,uc表示活性炭注入量,u
ca(oh)2
表示消石灰注入量;表示消石灰注入量;和分别表示ft、bsf、g1ox和g3ox模型输出;和分别表示各污染物模型输出;实尾箭头所表征的模型输入为虚尾箭头所表征的模型输入为
[0120]
基于炉内燃烧过程操作变量与被控变量的影响因素分析,进一步根据领域专家的经验认知选择燃烧过程模型输入。为满足生产需求与污染排放达标,mswi过程稳定控制是领域专家操作的主要目标。通常,领域专家考虑日运行计划调度、运行工况记录、运行期间操作工作票、mswi过程实时监控信息和mswi运行车间设备状态等信息后,根据当前目标设定值,调整各控制回路中执行机构的控制量,以达到稳定运行目的。因此,mswi过程考虑上述众多因素的强耦合才能有效实现稳定控制;
[0121]
在常规运行工况下,不考虑mswi厂的启炉、停炉和低效率运行维护等非常规工况的运行工况,本发明通过mswi运行过程的实际案例分析炉内燃烧过程模型的输入选择。炉内燃烧过程包含炉排速度控制、燃烧空气流量控制和sncr系统控制,其目的是实现稳定的燃烧过程、均匀的蒸汽量、msw的完全燃烧和最低的有害气体产生。ft、bsf和g1ox作为燃烧过程的被控变量具有显著跟随性,例如:ft高,则bsf大和g1ox小;
[0122]
在实际操作过程中,当ft出现的异常波动时,炉排速度控制和燃烧空气流量控制是领域专家首先考虑的操作。炉排速度增快和减慢可用于控制msw的厚度实现加快燃烧和延迟燃烧的目的,目前领域专家主要通过控制推料器速度和干燥炉排阶段速度来实现上述
目的,其它段炉排速度保持较大推进速度以维持msw的日处理速率。为约简模型输入特征将推料器速度u
fas
和干燥炉排阶段速度u
dgas
同类操作变量取均值处理,如下:
[0123][0124][0125]
在图10中,燃烧空气流量控制由一次风量和二次风量组成,其中一次风控制包含14个支路。一次风量的控制主要用于msw的干燥和助燃,二次风量的控制主要用于促进烟气中可燃成分的进一步燃烧和增大烟气的湍流度,一二次风的分配控制还决定着炉膛的过量空气系数。领域专家主要控制一次风总量(14个支路采用固定比例分配总一次风量)和二次风辅助控制的策略实现燃烧控制。因此,本发明将一次风挡板开度基于领域专家经验设定为固定比例,不作为输入特征进行模型训练;一次风流量u
priair
和二次风流量u
secair
作为风量输入特征。
[0126]
为最小化nox的产生,sncr控制系统采用向炉内喷射氨水实现nox的达标排放,领域专家主要通过控制氨水的入炉量实现上述目的。因此,根据其在mswi过程实际喷入位置,将氨水入炉量加入至炉内燃烧过程的炉膛温度模型作为输入特征。
[0127]
综上所述,确定炉内焚烧过程模型的基本输入特征为:
[0128][0129]
基于xgboost的炉内燃烧过程模型构建模块:
[0130]
1)炉膛温度模型
[0131]
首先,基于经验认知的炉内焚烧过模型输入选择模块输出结果,确定ft模型可表示为:
[0132][0133]
以下结合ft模型的构建xgboost的建模过程:
[0134]
xgboost模型是在梯度提升决策树(gradient boosting decision tree,gbdt)算法上改进提出,通过纠正训练完毕的学习器残差生成新的基学习器,最终将所有基学习器的预测结果求和形成预测结果。
[0135]
以第i个模型为例,描述xgboost模型构建过程,具体如下:
[0136]
xgboost利用在损失函数中引入正则项的方式控制模型的复杂度并防止过拟合,其损失函数可表示为:
[0137][0138]
式中,c
xgboost
表示xgboost模型中下一个基学习器的预测值,表示xgboost模型中第j个基学习器的预测值,将损失函数进行泰勒展开,分解得到:
[0139][0140]
对式(34)进行简化,将一阶导数和二阶导数简写为g和h,得到:
[0141][0142]
根据简化后的公式,将公式(27)表示为:
[0143][0144]
接着,为使损失函数得到最小值,删除式(36)中无输出值的项,如下所示:
[0145][0146]
并对其求导,令上式导数等于0,得到最优解为:
[0147][0148]
重复上述操作,直至基学习器数量达到设定值,确定炉膛温度模型为:
[0149][0150]
搭建锅炉蒸汽流量模型,具体为:在炉膛温度模型的基础上,加入作为模型输入,确定锅炉蒸汽流量模型为:
[0151][0152]
在炉膛出口位置检测g1ox,搭建g1烟气含氧量模型,具体为:在锅炉蒸汽流量模型的基础上,加入作为模型输入,确定g1烟气含氧量模型为:
[0153][0154]
搭建基于mi和xgboost的烟气处理过程模型构建模块,将烟气处理过程模型的输入特征表示为:
[0155][0156]
考虑到目前的mswi过程的u
fgcp
={uc,u
ca(oh)2
}为常值,将其删去,得到烟气处理过程模型的输入特征为:
[0157][0158]
结合互信息(mutual information,mi)及mswi过程机理,对输入特征进筛选,以g3ox为例,第k个输入特征与其之间的互信息计算公式为:
[0159][0160]
其中,和ρ
prob
(y
g3ox
)表示和y
g3ox
的边界概率密度,表示联合概率密度,h(y
g3ox
)表示信息熵,表示条件熵;
[0161]
剔除特征输入选择模块中mi值小于设定阈值θ
mi
的输入特征,最终确定烟气处理过程模型,并记为:
[0162][0163]
其中,表示基于θ
mi
在中为g3烟气含氧量模型f
g3ox
(
·
)选择的输入,即存在
[0164]
类似的,nox模型、co模型、co2模型和酸性气体模型可分别表示为::
[0165][0166][0167][0168][0169]
其中,和分别表示基于θ
mi
在x
fgcp
中为nox模型、co模型、co2模型和酸性模型选择得模型输入,即
[0170]
mswi全流程模型训练过程顺序具体如图6所示,其中各模型输入输出见图5,由图6可知,根据mswi全流程处理过程,由于炉内焚烧过程逐阶段进行,因此确定炉内燃烧过程模
型梯次串行训练,即前一模型训练完毕后,将其输出加入至下一模型的输入特征进行训练,直至炉内焚烧过程模型全部训练完毕;同时,烟气处理过程阶段统一进行有害物的去除,因此,对烟气处理过程模型采取并行训练方式,即在炉内焚烧过程模型训练完毕后,对其输出进行特征选择,并行训练烟气处理过程模型,直至所有模型训练完毕,确定基于梯次串并联训练机制的mswi全流程模型。
[0171]
为验证模型的准确性,本发明采用北京某mswi电厂2021年3月19日8:00至24:00共计16个小时连续运行所产生的过程数据。在对过程数据取60s均值数据后剔除异常值,最终共计857组数据,采用间隔采样,其中50%用于训练集,25%用于测试集,25%用于验证集。
[0172]
采用mi对操作变量与烟气处理过程中的关键被控变量/污染物排放浓度之间的关系进行评价,具体结果如图7所示。
[0173]
其中,特征顺序为:一次风流量、二次风流量、进料器均速、干燥炉排均速、氨水、ft、bsf、g1ox、石灰、活性炭。
[0174]
由图7可知,各操作变量在不同烟气处理过程中的关键被控变量/污染物排放浓度影响因素不相同,因此根据mi评价结果,剔除mi值小于0.3的特征进行相关模型建模。
[0175]
相应的,烟气处理过程模型的输入输出关系可表示为;
[0176]
1)g3烟气含氧量模型
[0177]
g3烟气含氧量模型的输入为进料器均速、干燥炉排均速、一次风流量、二次风流量、氨水注入量、ft预测输出、bsf预测输出和g1ox预测输出,输出为g3烟气含氧量,可表示为:
[0178][0179]
2)nox模型
[0180]
该模型输入为进料器均速、干燥炉排均速、一次风流量、二次风流量、氨水注入量、ft预测输出、bsf预测输出和g1ox预测输出,输出为g3部分nox含量,可表示为:
[0181][0182]
3)co模型
[0183]
该模型输入为一次风流量、二次风流量、氨水注入量、ft预测输出、bsf预测输出和g1ox预测输出,输出为g3部分co含量,可表示为:
[0184][0185]
4)co2模型
[0186]
该模型输入为进料器均速、干燥炉排均速、一次风流量、二次风流量、氨水注入量、ft预测输出、bsf预测输出和g1ox预测输出,输出为g3烟气co2量,可表示为:
[0187][0188]
5)酸性气体模型
[0189]
该模型输入为一次风流量、二次风流量、氨水注入量、ft预测输出、bsf预测输出和g1ox预测输出,输出为g3部分酸性气体含量,可表示为:
[0190]
[0191]
针对上述8个模型,采用梯次串并联训练机制,其参数设置如表3所示。rmse值如表4所示。拟合效果如图8所示。
[0192]
表3模型参数设置
[0193][0194]
表4模型rmse
[0195][0196][0197]
由表4和图8可知,所提出的mswi全流程串联模型均具有良好的逼近能力,但面对波动较大的真值时,会出现预测值较低的情况。
[0198]
为与本发明所提方法进行对比,采用mi对操作变量与关键被控变量/污染物排放浓度之间的关系进行评价,具体结果如图9所示;
[0199]
由图9可知,一次风流量、二次风流量、进料器左内速度、进料器左外速度、进料器右内速度、进料器右外速度、干燥炉排左内速度、干燥炉排左外速度、干燥炉排右内速度、干燥炉排右外速度与关键被控变量/污染物排放浓度的影响关系相比于其他操作变量相关系数较高;同时,在不同关键被控变量/污染物排放浓度中,其产生的影响又不相同。其mi结果与本发明中基于经验认知的分析基本一致,因此,可进一步确定炉内焚烧过程模型输入特征为:{u
fas
,u
dgas
,u
priair
,u
secair
,u
nh3
·
h2o
}。
[0200]
典型复杂工业过程mswi过程具有多输入、多输出、多耦合的特性,单一的被控对象建模难以表征其全流程和表征其工艺特性。针对这一问题,本发明构建了面向控制的数据
驱动mswi全流程模型,贡献为:结合mswi工艺流程设计了一种全流程串并联模型结构,为基于数据驱动的全流程建模研究提供了参考;利用过程机理和专家经验依据工艺逐模型确定输入输出,并根据流程处理顺序梯次串并联进行模型训练。本发明所提出的mswi全流程模型贴合过程机理,能够为后续先进智能优化控制算法奠定了基础。
[0201]
本发明提供的面向控制的数据驱动城市固废焚烧全流程建模方法,首先,基于经验认知,对炉内焚烧过程模型得输入特征进行选择;接着,利用xgboost构建炉内焚烧过程串联模型;然后,基于互信息分析结果选择烟气处理过程模型输入特征,进行相关建模;最后,梯次训练所提出的全流程串并联模型;通过工厂实际运行数据验证了所提模型的有效性,为后续mswi过程先进智能优化控制算法的研究提供了参考。
[0202]
本文中应用了具体个例对本发明的原理及实施方式进行了阐述,以上实施例的说明只是用于帮助理解本发明的方法及其核心思想;同时,对于本领域的一般技术人员,依据本发明的思想,在具体实施方式及应用范围上均会有改变之处。综上所述,本说明书内容不应理解为对本发明的限制。