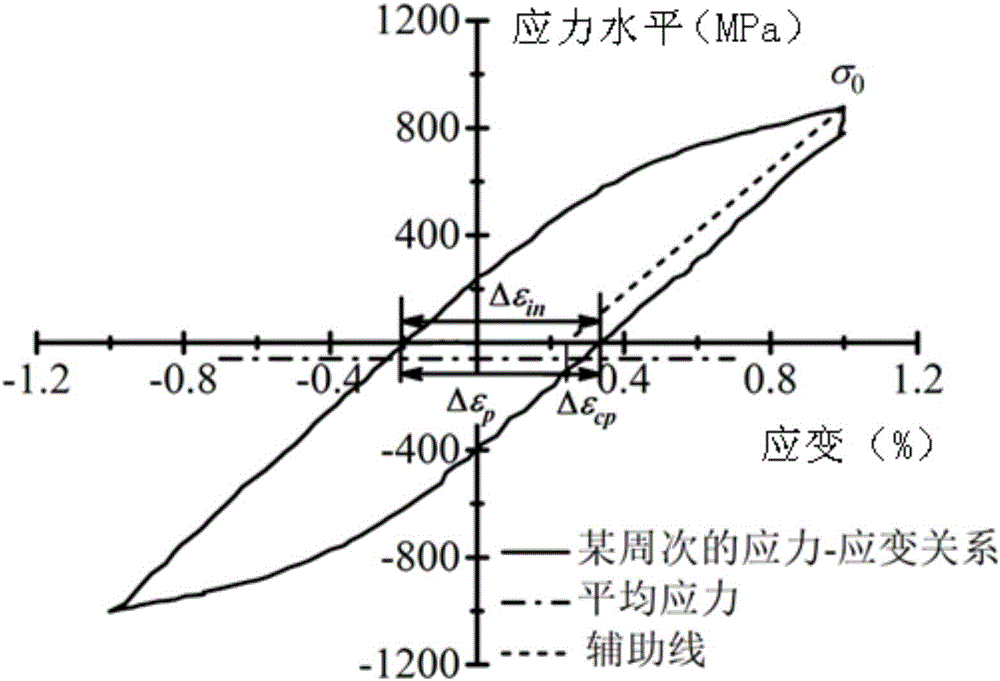
本发明涉及损伤评定领域,尤其涉及一种时间相关的蠕变疲劳损伤评定方法
背景技术:
:在能源动力、石油化工和航空航天等领域中,许多结构部件长期运行在高温条件下受应变波形控制,循环失效寿命往往不足105次,即,在高温低周疲劳载荷下,其寿命往往受到蠕变、疲劳和蠕变疲劳交互作用等多种机制的制约。在蠕变疲劳交互作用的条件下,材料的损伤评估非常重要,而利用线性损伤累积准则进行较为准确的实时损伤累积评估是亟需突破的重点和难点。自20世纪70年代以来,国内外学者推演出了许多蠕变疲劳交互作用下的损伤评估方法。但是在这些损伤评估方法中,基于线性损伤累积准则,即可以实现损伤的每周次实时评估。经典的利用线性损伤累积准则并写入美国ASME设计准则(AmericanSocietyofMechanicalEngineers.BoilerandPressureVesselCode,SectionIII,subsection-NH2005)和英国R5设计准则(BritishEnergy.Assessmentprocedureforthehightemperatureresponseofstructures.R5Issue3,2003)的模型有时间分数法和延性耗竭法。在时间分数法中,主要以应力水平σ和蠕变断裂时间tR为基本参量推演蠕变损伤公式;在延性耗竭法中,主要以蠕变延性εf和非弹性应变率为基本参量推演蠕变损伤公式。在两种方法中,疲劳损伤的定义则为固定值1/N0,其中N0为特定工况纯疲劳的寿命。但是这两种经典的方法都有各自的缺陷。在时间分数法中,计算损伤的结果通常偏于非保守;而在延性耗竭法中,计算损伤的结果又过于保守。并且,在这两种模型中,疲劳损伤仅为一个固定的数值,对疲劳损伤的表述过于简单粗略。技术实现要素:针对上述现有技术中的不足,本发明提供一种时间相关的蠕变疲劳损伤评定方法,能够更好地实现材料在蠕变疲劳交互作用下的实时损伤累积评估,具有精确度高、灵活性强、可实施评估和直观的优点。为了实现上述目的,本发明一种时间相关的蠕变疲劳损伤评定方法,包括步骤:S1:对一目标材料进行多次实验获取所需的一参数组;S2:根据所述参数组计算获得各周次的蠕变损伤dc和各周次的疲劳损伤df;S3:根据所述各周次的蠕变损伤dc计算第n周次时的累积蠕变损伤Dc(n)和第n周次时的累积疲劳损伤Df(n),n为大于0的自然数;S4:以所述第n周次时的累积蠕变损伤Dc(n)为纵坐标并以和第n周次时的累积疲劳损伤Df(n)为横坐标绘制一蠕变疲劳损伤交互图;S5:结合所述蠕变疲劳损伤交互图和至少一损伤累积法则评估所述目标材料的实时累积损伤情况。进一步地,所述S2步骤包括利用公式(1)和公式(2)计算获得各周次的蠕变损伤dc和各周次的疲劳损伤df:dc=∫0th[M1+t-N1+t·log(1+t)min(D·w·inn1,wf0)-M1+t-N1+t·log(1+t)wf0]dtM=(σ0+σm)·(A·logΔϵp+B)E·ln10N=(A·logΔϵp+B)2E·ln10---(1);]]>其中,dc为蠕变损伤,t为时间,D为第一线性回归参数,n1为第一线性回归幂指数,wf0为平台值,为非弹性应变能密度耗散率,σ0为最大应力,σm为平均应力,Δεp为塑性应变范围参数,A为第一松弛参数,B为第二松弛参数;E为弹性模量;th为蠕变疲劳保持时间;df=1α·(Δϵp)β---(2);]]>其中,df为疲劳损伤,α为第一线性回归参数,β为第二线性回归参数。进一步地,在所述S3步骤中,根据公式(3)计算所述第n周次时的累积蠕变损伤Dc(n)和所述第n周次时的累积疲劳损伤Df(n):{Dc(n)=Σi=1ndc(i)Df(n)=Σi=1ndf(i)---(3);]]>其中,dc(i)为第i周次的蠕变损伤,df(i)为第i周次的疲劳损伤,i为大于零的自然数。进一步地,所述损伤累积法则包括一线性损伤累积法则,所述线性损伤累积法则的数学表达式为公式(4):Dc+Df=1(4);其中,Dc为累积蠕变损伤,Df为累积疲劳损伤,当公式(4)成立时判定所述目标材料失效。进一步地,所述损伤累积法则还包括一双线性损伤累积法则,所述双线性损伤累积法则的数学表达式为公式(5):其中,所述双线性损伤累积法则的折点坐标为当公式(5)成立时判定所述目标材料失效。进一步地,所述损伤累积法则还包括一简化的非线性累积损伤法则,所述简化的非线性累积损伤法则的数学表达式为公式(6):Dcm+Dfm=1(6);其中,m为简化的非线性损伤累积法则系数,当公式(6)成立时判定所述目标材料失效。进一步地,所述S1步骤进一步包括步骤:S11:通过一不同应力水平下的高温蠕变试验,获得所述目标材料的每个应力水平下的一蠕变延性数据εf、一蠕变断裂时间tR、所述第一线性回归参数D、所述第二线性回归参数n1和所述平台值wf0;S12:通过一相同温度不同应力水平的应力松弛试验,获得每个应变水平下应力与松弛时间的变化关系,并根据所述变化关系获得所述第一松弛参数A和所述第二松弛参数B;S13:通过一相同温度不同应变幅的应变控制下的纯疲劳试验,获得各应变幅下的所述塑性应变范围参数Δεp和疲劳寿命参数N0,根据纯疲劳实验条件下的所述塑性应变范围参数Δεp和疲劳寿命参数N0获得所述第一线性回归参数α和第二线性回归参数β;S14:通过一相同温度的应变控制下的蠕变疲劳试验,记录各周次的应力应变关系,获得各周次的所述最大应力σ0、各周次的所述平均应力σm以及各周次的蠕变疲劳实验条件下的所述塑性应变范围参数Δεp。进一步地,所述步骤S12中,根据所述变化关系和公式(7)计算获得所述第一松弛参数A和所述第二松弛参数B:σ(t)=σ0-(A·logΔεp+B)·log(1+t)(7);其中,t为时间,σ(t)为t时的应力水平。进一步地,所述步骤S13中,根据所述塑性应变范围参数Δεp和疲劳寿命参数N0并通过公式(8)计算获得所述第一线性回归参数α和第二线性回归参数β:N0=α·(Δεp)β(8);其中,N0为疲劳寿命参数,Δεp为塑性应变范围参数。本发明由于采用了以上技术方案,使其具有以下有益效果:(1)本发明利用应变能耗散的概念,具有清晰的物理意义,并有较为精确的预测结果;(2)本发明利用损伤交互图,能够实时评估材料的累积损伤,也可以直观观察材料剩余的蠕变疲劳持久性能;(3)本发明具有很强的灵活性,在不同的部件、不同的设计要求下,可以利用不同的损伤累积法则,进行实时累积损伤的评估。附图说明图1为本发明实施例的时间相关的蠕变疲劳损伤评定方法的流程图;图2为本发明实施例的实验中的应力应变关系图;图3为本发明实施例的在自然坐标损伤交互图中的线性损伤累积法则、双线性损伤累积法则以及简化的累积损伤法则示意图;图4为本发明实施例的高温镍基GH4169超合金650℃下不同应力水平下高温蠕变试验参数拟合结果图;图5为本发明实施例的高温镍基GH4169超合金650℃下不同应变水平的应力松弛试验参数拟合结果图;图6为本发明实施例的高温镍基GH4169超合金650℃下不同应变幅下的纯疲劳试验参数拟合结果图;图7为本发明实施例一的对数坐标下损伤交互图中的蠕变疲劳实时损伤累积评估结果图;图8为本发明实施例二的对数坐标下损伤交互图中的蠕变疲劳实时损伤累积评估结果图;图9为本发明实施例三的对数坐标下损伤交互图中的蠕变疲劳实时损伤累积评估结果图。具体实施方式下面根据附图1-9,给出本发明的较佳实施例,并予以详细描述,使能更好地理解本发明的功能、特点。请参阅图1,本发明的一种时间相关的蠕变疲劳损伤评定方法:首先,进行S1步骤:使用高温蠕变试验机,对一目标材料进行多次实验获取所需的一参数组。其中,S1步骤进一步包括步骤:S11:使用高温蠕变试验机,通过一不同应力水平下的高温蠕变试验,获得目标材料的每个应力水平下的一蠕变延性数据εf、一蠕变断裂时间tR、第一线性回归参数D、第二线性回归参数n1和平台值wf0;如以应变百分比数值为横轴,应力为纵轴作一应力应变关系图,第一线性回归参数D为应力应变关系图中实线的截距、n1线性回归幂指数为蠕变能量耗散图中实线的斜率;S12:使用高温蠕变试验机,通过一相同温度不同应力水平的应力松弛试验,获得每个应变水平下应力与松弛时间的变化关系,根据变化关系和公式(7)即应力松弛公式,计算获得第一松弛参数A和第二松弛参数B:σ(t)=σ0-(A·logΔεp+B)·log(1+t)(7);其中,t为时间,σ(t)为t时的应力水平。S13:使用高温蠕变试验机,通过一相同温度不同应变幅的应变控制下的纯疲劳试验,获得各应变幅下的塑性应变范围参数Δεp和疲劳寿命参数N0,根据纯疲劳条件下塑性应变范围参数Δεp和疲劳寿命参数N0并通过公式(8)计算获得第一线性回归参数α和第二线性回归参数β:N0=α·(Δεp)β(8);其中,N0为疲劳寿命参数,Δεp为塑性应变范围参数。S14:通过一相同温度的应变控制下的蠕变疲劳试验,记录各周次的应力应变关系,获得各周次的最大应力σ0、各周次的平均应力σm以及各周次的蠕变疲劳条件下塑性应变范围参数Δεp。接着,进行S2步骤:在蠕变疲劳工况下,根据参数组并利用公式(1)和公式(2)计算获得各周次的蠕变损伤dc和各周次的疲劳损伤df:dc=∫0th[M1+t-N1+t·log(1+t)min(D·w·inn1,wf0)-M1+t-N1+t·log(1+t)wf0]dtM=(σ0+σm)·(A·logΔϵp+B)E·ln10N=(A·logΔϵp+B)2E·ln10---(1);]]>其中,dc为蠕变损伤,t为时间,D为第一线性回归参数,n1为第二线性回归参数指数,wf0为平台值,为非弹性应变能密度耗散率,σ0为最大应力,σm为平均应力,Δεp为塑性应变范围参数,A为第一松弛参数,B为第二松弛参数;E为弹性模量;th为蠕变疲劳保持时间;df=1α·(Δϵp)β---(2);]]>df为疲劳损伤,α为第一线性回归参数,β为第二线性回归参数,以应变百分比数值为横轴,应力为纵轴作一应力应变关系图,应力应变关系图可如图2所示,显示了某一个周次下的蠕变疲劳试验中的应力应变关系。请继续参加图1,其中,失效应变能密度wf与非弹性应变能密度耗散率之间的函数关系表示为公式(9):wf=D·w·inn1---(9);]]>D为第一线性回归参数,为非弹性应变能密度耗散率,n1为第一线性回归幂指数,其中,wf=σ·εf(10);w·in=σ·ϵftR---(11);]]>其中,σ表示蠕变试验中施加的应力水平,εf表示蠕变试验中获取的蠕变延性,tR表示蠕变试验中获取的蠕变断裂时间。然后,进行S3步骤:根据各周次的蠕变损伤dc计算第n周次时的累积蠕变损伤Dc(n)和第n周次时的累积疲劳损伤Df(n),n为大于0的自然数;具体地,根据公式(3)计算第n周次时的累积蠕变损伤Dc(n)和第n周次时的累积疲劳损伤Df(n):{Dc(n)=Σi=1ndc(i)Df(n)=Σi=1ndf(i)---(3);]]>其中,dc(i)为第i周次的蠕变损伤,df(i)为第i周次的疲劳损伤,i为大于零的自然数。之后,进行S4步骤:根据第n周次时的累积蠕变损伤Dc(n)和第n周次时的累积疲劳损伤Df(n)绘制一蠕变疲劳损伤交互图。最后,进行S5步骤:结合蠕变疲劳损伤交互图和至少一损伤累积法则评估目标材料的实时累积损伤情况。其中,损伤累积法则包括一线性损伤累积法则,线性损伤累积法则的数学表达式为公式(4):Dc+Df=1(4);其中,Dc为累积蠕变损伤,Df为累积疲劳损伤,当公式(4)成立时判定目标材料失效。损伤累积法则还包括一双线性损伤累积法则,双线性损伤累积法则的数学表达式为公式(5):其中,双线性损伤累积法则的折点坐标为当公式(5)成立时判定目标材料失效。损伤累积法则还包括一简化的非线性累积损伤法则,简化的非线性累积损伤法则的数学表达式为公式(6):Dcm+Dfm=1(6);其中,m为简化的非线性损伤累积法则系数,当公式(6)成立时判定目标材料失效。针对不同的材料、部件以及设计要求,选取不同的非线性损伤累积法则,根据美国ASME以及英国R5准则,越是重要的部件以及苛刻的设计要求,所选取的损伤累积法则越是保守,当进行累积损伤的评估时,设计准则可以表示在在蠕变疲劳损伤交互图中。请参阅图3,图示了一种在自然坐标损伤交互图中的线性损伤累积法则、双线性损伤累积法则以及简化的累积损伤法则示意图。本发明的一种材料的蠕变疲劳实时损伤累积评估方法基于线性损伤累积准则,结合应变能密度耗散的概念,并引用蠕变疲劳损伤交互设计图。不同于时间分数法和延性耗竭法,该方法主要以失效应变能密度wf和非弹性应变能耗散率为基本参量,并且修正了每周次疲劳损伤df的表达式。通过蠕变疲劳损伤交互图,该方法能够实时评估材料的累积损伤,也可以直观观察材料剩余的蠕变疲劳持久性能。以下实施例1~3中,采用本发明的材料蠕变疲劳实时损伤累积评估方法对650℃下的高温镍基GH4169超合金进行验证。通过10个应力水平,650℃下的不同应力水平下高温蠕变试验结果,并利用公式(9)~(11)求出的纯蠕变试验中的三个参数:σ蠕变试验中施加的应力水平,εf蠕变试验中获取的蠕变延性,tR蠕变试验中获取的蠕变断裂时间。如图4所示;通过2个应变水平,650℃下的不同应变水平的应力松弛试验结果,求出公式(7)中应力松弛公式中的两个参数A和B,如图5所示;通过4个应变水平,650℃下的不同应变幅下的纯疲劳试验,求出式(2)中每周次疲劳损伤df的两个参数α和β。如图6所示。另外,该材料在650℃下的弹性模量为161.64MPa。实施例1:选取数据为总应变范围为2.0%,在应变最大处的保载时间为120s,温度为650℃下的轴向等幅蠕变疲劳交互试验,参照标准为GB/T15248-2008《金属材料轴向等幅低循环疲劳试验方法》。其蠕变疲劳实验寿命为255周次,实时损伤累积评估所用的参数包括:失效应变能密度wf、非弹性应变能密度耗散率蠕变试验中施加的应力水平σ、时间t、疲劳寿命参数N0、塑性应变范围参数Δεp,各参数的关系请参阅图4、图5和图6。实验中可得塑性应变范围参数Δεp、最大应力σ0以及平均应力σm随着循环周次n的变化,根据公式(1)依次计算每个周次的蠕变损伤dc,根据公式(2)依次计算每个周次的疲劳损伤df,然后根据公式(3)计算循环至某个周次n的累积损伤,其中,第n周次时的累积蠕变损伤Dc(n)表示为在损伤交互图中某个周次n的纵坐标,第n周次时的累积疲劳损伤Df(n)表示为损伤交互图中的横坐标。每个循环周次坐标点在蠕变疲劳损伤交互图中所连成轨迹线则为该材料在该工况下实时的累积损伤,当轨迹线与损伤累积法则线相交时,则判定为在该工况、该设计准则下材料失效,即不能进行实际工况的服役。在科学研究中,一般采用经典的线性损伤累积法则进行寿命评估和预测。但是在实际工程运用中,双线性损伤准则考虑了蠕变疲劳的交互作用,这使得该准则更为保守也更加适用于工程。在核电以及压力管道领域中,双线性损伤准则得到广泛使用。21世纪以来,英国能源科技评估研究小组提出了简化的损伤累积法则,它因更为保守、更为简明的表达而被广泛认可。依据美国ASME和英国R5准则,这里给出的公式(5)中双线性累积损伤法则的折点推荐坐标值为(0.3,0.3),公式(6)中简化的非线性损伤累积法则的系数m=0.576。图7表示了本实例中在蠕变疲劳损伤交互途中实时损伤累积评估的结果,其中,黑点表示选取的某个循环周次n的累积损伤(Df(n),Dc(n))的位置。已知实验失效时的寿命为255周次,在放大图中可以看出,公式(4)中线性损伤累积法则计算失效时的寿命为236周次,公式(5)中双线性损伤累积法则计算失效时的寿命为226周次,公式(6)中简化的非线性损伤累积法则计算失效时的寿命为197周次。结果显示,预估的寿命较为准确并且均略微保守。实施例2:选取数据为总应变范围为1.6%,在应变最大处的保载时间为1800s,温度为650℃下的轴向等幅蠕变疲劳交互试验,参照标准为GB/T15248-2008《金属材料轴向等幅低循环疲劳试验方法》。其蠕变疲劳实验寿命为353周次,实时损伤累积评估所用的参数包括:失效应变能密度wf、非弹性应变能密度耗散率蠕变试验中施加的应力水平σ、时间t、疲劳寿命参数N0、塑性应变范围参数Δεp,各参数的数值请参阅图4、图5和图6。实验中可得塑性应变范围参数Δεp、最大应力σ0以及平均应力σm随着循环周次n的变化,根据公式(1)依次计算每个周次的蠕变损伤dc,根据公式(2)依次计算每个周次的疲劳损伤df,然后根据公式(3)计算循环至某个周次n的累积损伤,其中,第n周次时的累积蠕变损伤Dc(n)表示为在损伤交互图中某个周次n的纵坐标,第n周次时的累积疲劳损伤Df(n)表示为损伤交互图中的横坐标。每个循环周次坐标点在蠕变疲劳损伤交互图中所连成轨迹线则为该材料在该工况下实时的累积损伤,当轨迹与损伤累积法则线相交时,则判定为在该工况下材料发生失效,即不能进行实际工况的服役。依据美国ASME和英国R5准则,这里给出的公式(5)中双线性累积损伤法则的折点坐标为(0.3,0.3),公式(6)中简化的非线性损伤累积法则的系数n=0.576。图8表示了本实例中在蠕变疲劳损伤交互途中实时损伤累积评估的结果,其中,黑点表示选取的某个循环周次n的累积损伤(Df(n),Dc(n))的位置。已知实验失效时的寿命为353周次,在放大图中可以看出,在实际材料失效时并未达到公式(4)中的线性损伤累积法则的实现,这表示线性损伤累积法则并不保守,但若是按照累积损伤轨迹线的趋势来看,失效时的寿命约为411周次,公式(5)中双线性损伤累积法则计算失效时的寿命为296周次,公式(6)中简化的非线性损伤累积法则与公式(5)的计算结果非常接近,为295周次。结果显示,预估的寿命较为准确,但是运用线性累积损伤法则会使得结果略微保守,而双线性累积损伤法则和简化的非线性损伤累积法则依然使得结果略微保守。实施例3:选取数据为总应变范围为1.0%,在应变最大处的保载时间为300s,温度为650℃下的轴向等幅蠕变疲劳交互试验。其蠕变疲劳实验寿命为2862周次,实时损伤累积评估所用的参数包括:失效应变能密度wf、非弹性应变能密度耗散率蠕变试验中施加的应力水平σ、时间t、疲劳寿命参数N0、塑性应变范围参数Δεp,各参数的数值请参阅图4、图5和图6。实验中可得塑性应变范围Δεp、最大应力σ0以及平均应力σm随着循环周次n的变化,根据公式(1)依次计算每个周次的蠕变损伤dc,根据公式(2)依次计算每个周次的疲劳损伤df,然后根据公式(3)计算循环至某个周次n的累积损伤,其中,第n周次时的累积蠕变损伤Dc(n)表示为在损伤交互图中某个周次n的纵坐标,第n周次时的累积疲劳损伤Df(n)表示为损伤交互图中的横坐标。每个循环周次坐标点在蠕变疲劳损伤交互图中所连成轨迹线则为该材料在该工况下实时的累积损伤,当轨迹线与损伤累积法则线相交时,则判定为在该工况下材料发生失效,即不能进行实际工况的服役。依据美国ASME和英国R5准则,这里给出的公式(5)中双线性累积损伤法则的折点推荐坐标值为(0.3,0.3),公式(6)中简化的非线性损伤累积法则的系数n=0.576。图9表示了本实例中在蠕变疲劳损伤交互途中实时损伤累积评估的结果,其中,黑点表示选取的某个循环周次n的累积损伤(Df(n),Dc(n))的位置。由于在小应变范围的工况,每个循环贡献的损伤数值较小,因此在30周及以下的累积损伤尚未达到10-4,超出了图9的横纵坐标范围,故这里标出的累积损伤从第40周开始。已知实验失效时的寿命为2862周次,在放大图中可以看出,公式(4)中线性损伤累积法则计算失效时的寿命为2661周次,公式(5)中双线性损伤累积法则计算失效时的寿命为2037周次,公式(6)中简化的非线性损伤累积法则计算失效时的寿命为1815周次。结果显示,预估的寿命较为准确并且均略微保守。以上记载的,仅为本发明的较佳实施例,并非用以限定本发明的范围,本发明的上述实施例还可以做出各种变化。即凡是依据本发明申请的权利要求书及说明书内容所作的简单、等效变化与修饰,皆落入本发明专利的权利要求保护范围。当前第1页1 2 3