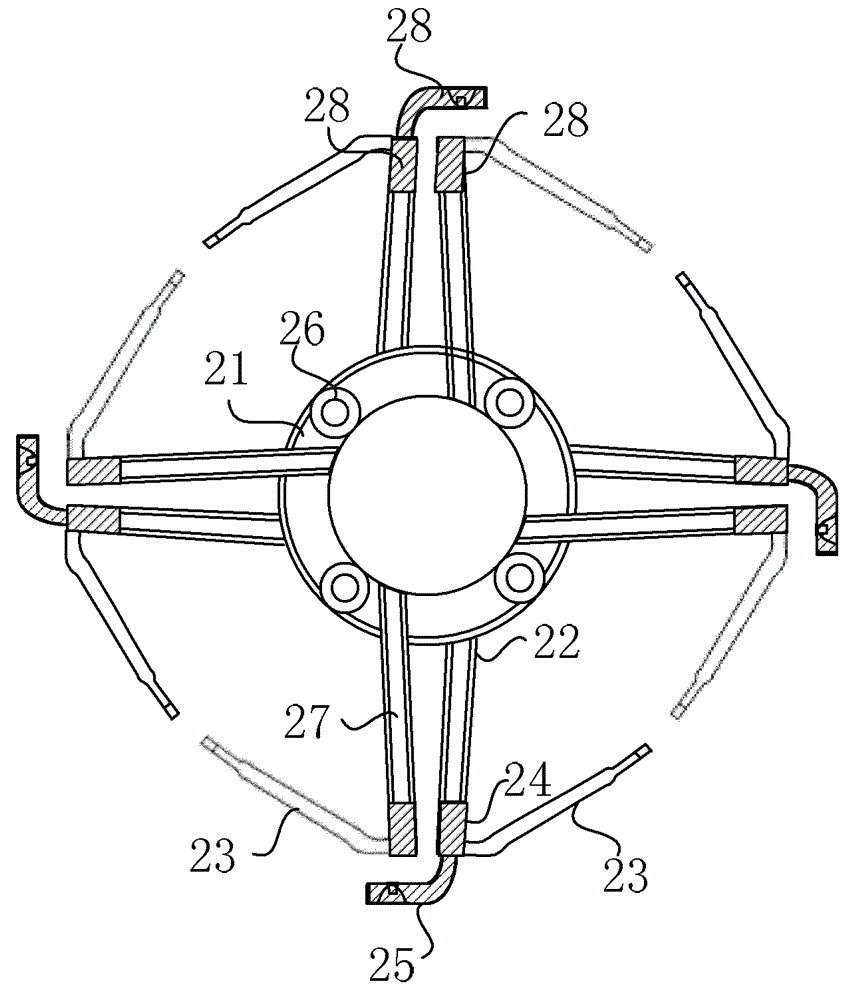
本发明实施例涉及通信设备领域,尤其涉及一种天线振子及其制造方法。
背景技术:天线振子是无线基站天线的核心器件,为了满足天线的功能要求,其结构一般比较复杂。图1为现有技术天线振子的示意图,如图1所示,目前天线振子多采用一体、一次压铸成型。天线振子与馈线的连接主要通过焊接方式,焊接要求天线振子的基材耐高温。现行的一体、一次压铸成型的天线振子,为了保证焊接区域的可焊接性,往往使用重量较重、耐高温的材料,如压铸铝合金、压铸锌合金等,使得天线振子整体重量较大。
技术实现要素:本发明实施例的目的是提出一种天线振子及其制造方法,旨在解决传统一体、一次压铸成型的天线振子质量重的问题。为实现上述目的,本发明提供了一种天线振子,所述天线振子包括:焊接区和非焊接区,所述焊接区与所述非焊接区相连以组成所述天线振子;所述焊接区包括焊接点区域以及所述焊接点区域周围的部分;其中,所述焊接点区域为所述天线振子与其它部件需要焊接的区域;所述焊接区采用耐高温的第一材料制成,使得当在所述焊接点区域进行焊接操作时,所述焊接区能够承受所述焊接操作时产生的高温,并且所述焊接操作时产生的高温经过所述焊接区传导到所述非焊接区后,所述非焊接区能够承受住传导过来的温度;所述非焊接区为所述天线振子除所述焊接区外的其余部分,所述非焊接区采 用比所述第一材料密度低的第二材料制成,以降低所述非焊接区的重量。本发明实施例还提出了一种天线振子的制造方法,所述方法包括:利用耐高温的第一材料将焊接区加工成型;利用第二材料将非焊接区加工成型,所述第二材料密度比所述第一材料密度低;将所述焊接区与所述非焊接区接合以组成所述天线振子。本发明实施例提出的天线振子及其制造方法,通过分别在焊接区和非焊接区采用不同的材料,从而大大降低了天线振子的重量。附图说明图1为现有技术天线振子的示意图;图2为本发明又一实施例天线振子的示意图;图3为本发明再一实施例天线振子的示意图;图4为本发明实施例天线振子的制造方法的流程图。具体实施方式下面通过附图和实施例,对本发明的技术方案做进一步的详细描述。本发明实施例提出了一种天线振子,改变了传统天线振子一体、一次成型的方式,采用将焊接区和非焊接区分别单独成型,然后将焊接区与非焊接区接合起来组成天线振子。本发明实施例的天线振子在焊接区采用耐高温的焊接材料,非焊接区采用比焊接区密度低且易成型的材料,从而大大降低了天线振子的重量,且降低了天线振子的成型难度。天线振子与馈线的连接主要通过焊接的方式,焊接要求天线振子的基材要有耐高温性,但是天线振子与馈线焊接的区域仅占整个天线振子的很少部分,天线振子的绝大部分无需焊接。本发明实施例的天线振子分为焊接区和非焊接区,焊接区为天线振子需要与其它部件焊接的焊接点区域以及焊接点区域周围的部分;非焊接区域为天线振子除焊接区以外的其它区域。本发明实施例的焊接点区域为天线振子与馈线焊接的区域,在焊接点区域通过焊接将天线振子与馈线连接在一起。本发明实施例的焊接点区域周围部分的具体形状、大小可根据实际情况来确定,例如,根据焊接点的大小来确定;根据焊接材料的耐高温性、传热性来确定;根据天线振子的使用环境来确定;或者根据整个天线振子的实际形状及大小来等因素来确定。本发明实施例的焊接区采用耐高温的焊接材料,当焊接点区域进行焊接操作时,使得焊接区能够承受焊接操作时产生的高温。本发明实施例天线振子的焊接区采用的焊接材料高温可以承受高于450℃,低温可以承受低于-55℃,可以采用一些合金材料,如铜合金、铝合金、锌合金等;也可以采用耐高温塑料,如聚醚醚酮(PEEK)、聚醚酰亚胺(PEI)、聚苯硫醚(PPS)等。本发明实施例的非焊接区采用质量轻、易成型、成本低、去毛刺简单的非焊接材料,非焊接区采用的材料不需要耐高温,只要能够承受住焊接操作时产生的高温经过焊接区传导到非焊接区的温度即可。本发明实施例天线振子的非焊接区采用在-55℃~65℃条件下正常工作的材料,如普通热塑材料ABS树脂、轻质烧结铝合金等。本发明实施例的天线振子非焊接区采用的是质量轻、成本低、去毛刺简单的非焊接材料,只在焊接区采用质量重、成本高的焊接材料,但焊接区只占整个天线振子的很少部分,因而可以有效降低天线振子的重量及成本。本发明实施例的天线振子先将焊接区与非焊接区单独加工成型,再将成型后的焊接区与非焊接区接合组成天线振子,焊接区与非焊接区可以采用插接、胶结或者勾连的方式连接在一起,也可以利用嵌件压铸的方式连接在一起。需要说明的是,本发明实施例天线振子使用的焊接材料和非焊接材料的外部需要镀一层能传导电磁波的金属涂层,从而使得天线振子能够发射和接收电磁波。金属涂层可以采用金属铜材料、金属锡材料、金属银材料,或者其它能够传导电磁波的材料。传统的天线振子多采用一体、一次压铸成型,为了保证焊接区域的可焊接性,通常整个天线振子都采用耐高温的焊接材料,如铜合金、铝合金等,使得天线振子整体重量大,成本高,并且材料去毛刺非常的困难,从而造成天线振子在使用中有诸多不便。本发明实施例的天线振子改变了传统天线振子采用一体、一次压铸成型的方式,采取先将焊接区与非焊接区单独加工成型,再将成型后的焊接区与非焊接区接合组成天线振子的工艺,在焊接区使用耐高温的焊接材料,非焊接区使用质量轻、成本低、易成型、去毛刺简单的材料,有效减少天线振子的重量,降低天线振子的成本,同时降低了天线振子的成型难度。图2为本发明又一实施例天线振子的示意图,如图2所示,本实施例的天线振子分为焊接区和非焊接区两部分,其中非焊接区包括:圆环21、第一支架22、支脚23;焊接区包括:第二支架24与管脚25。圆环21上分布有攻丝孔26,天线振子通过攻丝孔26与反射板相连接,例如可以用螺丝通过攻丝孔26将天线振子固定在反射板上。第一支架22均匀的分布在圆环21四周,第一支架22的一端与圆环21相连接,另一端与第二支架24的一端相连接;第一支架22一方面起到支撑作用,保持天线振子的结构稳定性;另一方面第一支架22上分布有凹槽27,凹槽27用于放置馈线。支脚23一端与第二支架24的外端相连,对称分布在第二支架24的两边。在第二支架24和支脚23的连接处还连接有“L”型的管脚25。馈线的外线焊接在第二支架24上,馈线的内线焊接在“L”型管脚25上。本发明实施例的天线振子改变了传统的天线振子整体采用同一种材料的模式,在不同的区域采用不同的材料,在焊接区采用耐高温(可承受温度高于450℃)的焊接材料,在非焊接区则采用在-55℃~65℃条件下正常工作即可的材料。再如图2所示,本发明实施例天线振子的馈线的外线焊接在第二支架24上,因此第二支架24采用可承受温度高于450℃的焊接材料28(如图2中阴影部分);馈线的内线焊接在“L”型管脚25上,因此“L”型管脚25 也采用可承受温度高于450℃的焊接材料28;天线振子的其他部分不需要焊接,因而可以采用在-55℃~65℃条件下正常工作即可的材料。再如图2所示,本发明实施例天线振子改变了传统天线振子一体、一次压铸成型的制作工艺,而是先将焊接区与非焊接区单独加工成型,在不同区域采用不同材质,然后再将焊接区域与非焊接区域连接成整体的天线振子,不同区域之间的连接方式具体如下:第一支架22的一端与圆环21采用插接或者胶结或者勾连的方式连接在一起。第一支架22的另一端与第二支架24的一端采用插接或者胶结或者勾连的方式连接在一起。支脚23与第二支架24外端采用插接或者胶结或者勾连的方式连接在一起。管脚25与第二支架24的外端端焊接在一起,也可以采用插接或者胶结或者勾连的方式连接在一起。本实施和上述实施例的天线振子都是改变了传统天线振子采用一体、一次压铸成型的方式,采取在焊接区使用耐高温的焊接材料,非焊接区使用质量轻、成本低、易成型的材料,有效减少天线振子的重量,降低天线振子的成本。图3为本发明再一实施例的天线振子的示意图,如图3所示,本实施例天线振子分为焊接区和非焊接区两部分,其中非焊接区包括:圆环21、第一支架22;焊接区包括:支脚23、第二支架24和管脚25。第一支架22与圆环21采用一体、一次压铸成型;第二支架24与支脚23、管脚25采用一体、一次压铸成型。第一支架22与圆环21采用非焊接材料;第二支架24与支脚23、管脚25因需要焊接则采用焊接材料。第一支架22的外端与第二支架24的内端之间采用插接、胶结、勾连或者采用嵌件压铸的方式连接在一起。本实施例的天线振子的第一支架的内端和圆环采用一体、一次压铸成型,且采用非焊接材料;第二支架的外端和支脚及管脚采用一体、一次压铸成型,且采用焊接材料;第一支架外端与第二支架内端的交界处采取插接或者胶结 或者勾连或者采用嵌件压铸的方式连接在一起。这样大大减少了天线振子各个部分之间的组装与连接,使产品的制备工艺简单,且同样降低了天线振子的质量。需要说明的是,在嵌件压铸过程中,先将支脚、管脚及第二支架通过压铸一体、一次成型(即焊接区为一个整体),然后将一体的焊接区放入磨具中,再将非焊接材料熔融注入模具中通过压铸或注塑方式将非焊接区与焊接区连接为一体。也可以将焊接区通过压铸一体、一次成型,非焊接区也通过压铸一体、一次成型,将成型后的焊接区与非焊接区通过勾连、插接或胶接的方式连接在一起。本实施例的天线振子的焊接区与非焊接区的结构及连接方式不限于本发明实施例列举的方式,还可以根据实际情况采用其它结构或连接方式。本实施例的天线振子与上述两个实施例的天线振子相同,都是改变了传统天线振子采用一体、一次压铸成型的方式,采取在焊接区使用耐高温的焊接材料,非焊接区使用质量轻、成本低、易成型的材料,有效减少天线振子的重量,降低天线振子的成本,同时降低天线振子的成型难度。本发明实施例还提出了一种天线振子的制造方法,图4为本发明实施例天线振子的制造方法的流程图,如图4所示,本发明实施例天线振子的制造方法具体包括如下步骤:步骤101,利用耐高温的第一材料将焊接区加工成型;具体的,将耐高温的焊接材料通过挤压或机械加工的方式成型为天线振子的焊接区;或将耐高温的焊接材料熔融后充入模具通过压铸的方式成型为天线振子的焊接区。本发明实施例的焊接区采用的焊接材料高温可以承受高于450℃,低温可以承受低于-55℃,可以采用一些合金材料,如铜合金、铝合金、锌合金等;也可以采用耐高温塑料,如聚醚醚酮(PEEK)、聚醚酰亚胺(PEI)、聚苯硫醚(PPS)等。步骤102,利用第二材料将非焊接区加工成型,第二材料密度比第一材 料密度低;具体的,将质量轻、易成型、成本低、去毛刺简单的非焊接材料通过挤压或机械加工的方式成型为天线振子的非焊接区;或者将质量轻、易成型、成本低、去毛刺简单的非焊接材料熔融后充入模具中通过压铸方法成型为天线振子的非焊接区。本发明实施例天线振子的非焊接区采用在-55℃~65℃条件下正常工作的材料,如普通热塑材料ABS树脂、轻质烧结铝合金等。步骤103,将焊接区与非焊接区接合以组成天线振子。具体的,将步骤101中成型的焊接区与步骤102中成型的非焊接区连接起来组成天线振子。本发明实施例天线振子的焊接区与非焊接区可以通过插接、胶结或者勾连的方式接合在一起,也可以通过嵌件压铸的方式接合在一起。需要说明的是,焊接区与非焊接区通过嵌件压铸的方式接合在一起具体为,将成型后的焊接区与熔融后的非焊接材料放入模具压铸,使得非焊接材料成型为非焊接区,同时使得焊接区与非焊接区接合在一起。本发明实施例提出的天线振子的制造方法,改变了传统天线振子一体、一次成型的方式,而是采用将焊接区和非焊接区分别单独成型,然后将焊接区与非焊接区连接起来组成天线振子的工艺。本发明实施例天线振子的制造方法在焊接区采用耐高温的焊接材料,非焊接区采用比焊接区密度低且易成型的材料,从而大大降低了天线振子的重量,且降低了天线振子的成型难度。以上所述的具体实施方式,对本发明的目的、技术方案和有益效果进行了进一步详细说明,所应理解的是,以上所述仅为本发明的具体实施方式而已,并不用于限定本发明的保护范围,凡在本发明的精神和原则之内,所做的任何修改、等同替换、改进等,均应包含在本发明的保护范围之内。