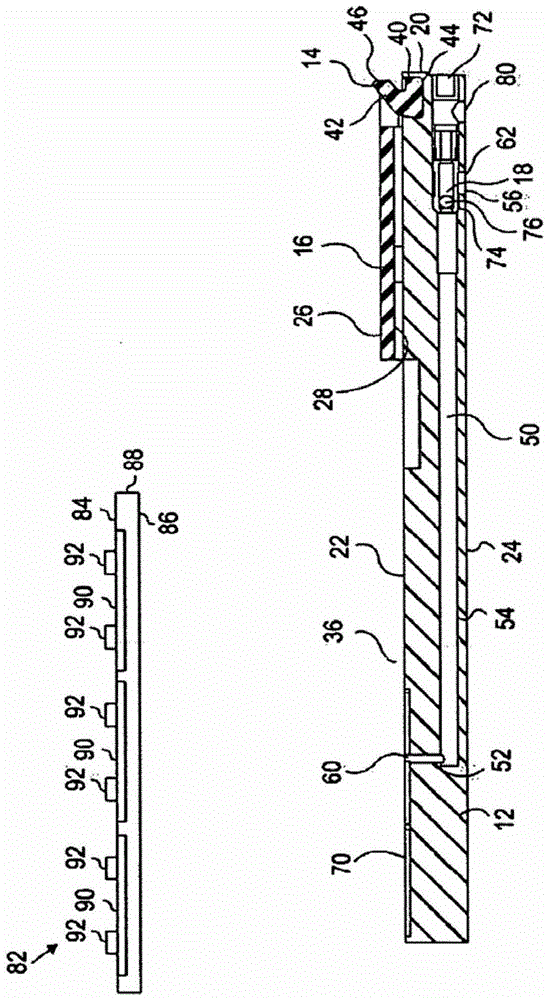
测试微电子电路的方法、测试器设备及便携式组装本申请是申请日为2008年4月4日、申请号为200880018734.5、发明名称为“具有信号配电盘的电子测试器和具有不同热膨胀系数的晶圆卡盘”的中国专利申请的分案申请。相关申请本申请要求2007年4月5日提交的美国临时专利申请No.60/910,433的优先权,其整体被引入作为参考。技术领域本发明涉及一种用于全晶圆(wafer)测试和/或老化测试(burn-intesting)和/或内建自测试(built-inself-testing)。
背景技术:一般在半导体晶圆中或上制造微电子电路。该晶圆随后被“单个化”或“切割”成单独的晶粒。该晶粒一般被安装到为其提供刚性以及提供与晶粒的集成电路或微电子电路的电子通信的支撑基片。最后的封装可包括晶粒封装,然后将得到的封装装运给客户。可以在将晶粒或封装装运给客户之前对其进行测试。理想地,可以在较早阶段测试晶粒,从而识别在较早阶段的制造中出现的缺陷。可以测试晶粒的最早阶段是在晶圆级别时微电子电路制造完成之后,以及晶圆被单个化之前。进行全晶圆测试具有很多难题。全晶圆测试中的一个难题是在晶圆上有大量的接点,因此大量的能量、接地以及信号连接需要被制造。另一个难题是老化测试需要热管理系统,其可在相对较高的温度下维 持晶圆稳定,同时提供操作简单且相对便宜的系统。
技术实现要素:提供一种便携式组装,其包括便携式支撑结构,该支撑结构用于支撑基片,该基片载有微电子电路,且具有连接至微电子电路的多个端子;在便携式支撑结构上的多个接点,该接点与端子匹配以用于与端子接触;第一接口,其在便携式支撑结构上且与接点相连接,用于当便携式支撑结构被固定结构可移走地支撑时,第一接口与固定结构上的第二接口连接。便携式支撑结构可包括第一组件和第二组件,用于将该基片支撑在它们之间,接点位于第二组件上,该组件可以相对于彼此移动,以确保在接点和端子之间的适当接触。第二组件可包括信号配电盘和接触器,其中该信号配电盘的CTE与该接触器的CTE的CTE比率不等于1。在微电子电路的测试期间,该接触器可以从第一接触器温度加热到第二接触器温度,该信号配电盘可以从第一信号配电盘温度加热到第二信号配电盘温度,并且温度变化率是第二信号配电盘温度和第一信号配电盘温度之间的差值与第二接触器温度和第一接触器温度之间的差值的比,温度变化率乘以CTE比率的乘积比CTE比率更接近1。热膨胀系数比率乘以温度变化率的乘积可以在0.8至1.2之间。第一组件可以是具有支撑基片的表面的基片卡盘。便携式组装可进一步包括压力差动空腔封条,其位于该第一组件和第二组件之间,该压力差动空腔封条与该第一组件的表面和第二组件的表面一起形成封闭的压力差动空腔,以及包括在该压力差动空腔中的压力减小通道,通过该压力减小通道可以排出该压力差动空腔中的空气,从而使得该第一组件和第二组件彼此相向移动。该压力差动空腔封条可围绕该接点和端子。当该第一组件和第二组件分离时,该压力差动空腔封条可以被固定到该第一组件。该压力差动空腔封条可以是唇缘(lip)封条。可以形成通过该组件中的一个的压力减小通道,该压力减小通道具有在该压力差动空腔处的入口和该压力差动空腔外部的出口,在具有该压力减小通道的该组件中的第一阀,打开该第一阀使得空气可以从该压力差动空腔中排出,并可以关闭该第一阀以阻止空气进入该压力差动空腔。该第一阀可以是止回阀,真空释放通道被形成通过具有该止回阀的组件,该真空释放通道具有在该压力差动空腔处的入口和在该压力差动空腔外部的出口,以及在具有该真空释放通道的该组件中的第二真空释放阀,打开真空释放阀使得空气可以进入压力差动空腔,并且关闭该真空释放阀可以阻止空气从压力差动空腔中逸出。该便携式组装可进一步包括在该第一组件中的基片抽气通道,通过该基片抽气通道可以将空气抽出,以减小该基片的面向该第一组件的一侧上的压力,从而相对着该第一组件支撑该基片。该接点可以被该端子可回复按压,该便携式组装进一步包括在该第二组件上的托脚,该托脚具有限制至少一个接点的按压的表面。多个独立的托脚可以位于该接点之间。该便携式组装可进一步包括具有第一侧和与该第一侧相对的第二侧的层,所述第一侧是带粘性的并粘接到所述第二组件,所述第二侧是带粘性的,所述托脚可被粘接到该第二侧。该第一接口可包括多个连接盘,且该第二接口可包括多个构件,该构件具有与该连接盘匹配并且可以被该连接盘可回复按压的接触表面,使其可相对于固定结构移动。该连接盘和该端子可以在平行平面内。该基片可以是具有多个微电子电路的晶圆。该接点可以是插脚,每个插脚具有弹簧,当各自的接点被各自一个端子按压时,插脚顶着弹簧的弹簧力而被按压。本发明还涉及一种测试器设备,其包括:支撑基片的便携式支撑结构,其中该基片承载有微电子电路并具有多个连接到微电子电路的端子;在便携式支撑结构上的多个接点,该接点与该端子匹配以用于与端子接触;在便携式支撑结构上且连接到接点的第一接口;固定结构,该便携式支撑结构是可被该固定结构容纳以被支撑,且可以从该固定结构移走;在该固定结构上的第二接口,当该便携式结构被该固定结构支撑时,该第二接口被连接到该第一接口,当该便携式支撑结构被从该固定结构移走时,该第二接口和第一接口被断开连接;电测试器,通过该第二接口、该第一接口以及该接点连接到该端子,使得可以在该电测试器和该微电子电路之间传送信号,从而测试该微电子电路。该便携式支撑结构可包括支撑该基片于其间的第一组件和第二组件,该接点位于该第二组件上,该组件相对彼此是可以移动的,从而确保该接点和该端子之间的适当接触。该第二组件可包括信号配电盘和接触器,其中该信号配电盘的CTE与该接触器的CTE的CTE比率不等于1。在测试微电子电路期间,该接触器可以从第一接触器温度加热到第二接触器温度,且该信号配电盘可以从第一信号配电盘温度加热到第二信号配电盘温度,温度变化率是第二信号配电盘温度和第一信号配电盘温度之间的差值与第二接触器温度和第一接触器温度之间的差值之比,温度变化率乘以CTE比率的乘积比CTE比率更接近1。热膨胀系数的比率乘以温度变化率的乘积可以在0.8至1.2之间。该第一组件可以是具有支撑该基片的表面的基片卡盘。该测试器设备可进一步包括在该第一组件和第二组件之间的压力差动空腔封条,该压力差动空腔封条与该第一组件和第二组件的表面一起形成封闭的压力差动空腔;在该压力差动空腔中的压力减小通道,通过该压力减小通道可以排出该压力差动空腔中的空气,从而使该第一组件和第二组件相对彼此移动。该压力差动空腔封条可围绕该接点和该端子。当该第一组件和第二组件分离时,该压力差动空腔封条可被固定到该第一组件。该压力差动空腔封条可以是唇缘封条。可以形成通过组件中的一个的压力减小通道,该压力减小通道具有在该压力差动空腔处的入口和该压力差动空腔外部的出口,在具有该压力减小通道的该组件中的第一阀,打开该第一阀使得空气可以从该压力差动空腔中排出,并且关闭该第一阀可以阻止空气进入该压力差动空腔。该第一阀可以是止回阀,真空释放通道被形成通过具有该止回阀的该组件,该真空释放通道具有在该压力差动空腔处的入口和在该压力差动空腔外部的出口,在具有该真空释放通道的该组件中的第二真空释放阀,打开真空释放阀使得空气可以进入压力差动空腔,并且关闭该真空释放阀可以阻止空气从压力差动空腔中逸出。该测试器设备可进一步包括在该第一组件中的基片抽气通道,通过该基片抽气通道可以将空气抽出,以减小该基片面向该第一组件的一侧上的压力,从而相对着该第一组件支撑该基片。该接点可以被该端子可回复按压,进一步包括在该第二组件上的托脚,该托脚具有限制至少一个接点的按压的表面。多个独立的托脚可以位于该接点之间。该测试器设备可进一步包括具有第一侧和与第一侧相反的第二侧的层, 该第一侧是粘性的并粘接到该第二组件,第二侧是粘性的,该托脚可被粘接到该第二侧。该第一接口可包括多个连接盘,该第二接口可包括多个构件,该构件具有和该连接盘匹配并且可以被该连接盘可回复按压的接触表面,使其可相对于固定结构移动。该连接盘和该端子可以在平行平面内。该固定结构可包括热卡盘,该便携式支撑结构接触该热卡盘,使得热量可以在该便携式支撑结构和该热卡盘之间传递。在该便携式支撑结构和该热卡盘之间可限定热接口空腔,穿过该热卡盘到该热接口真空可形成热接口真空通道。该测试器设备可进一步包括与该便携式支撑结构和热卡盘均接触的热接口空腔封条,使得该热接口空腔封条与该便携式支撑结构和热卡盘一起限定热接口空腔。该测试器设备可进一步包括在该固定结构上的热卡盘,该热卡盘具有热控制通道,该热控制通道具有入口、出口以及介于入口与出口之间用于流体从入口流至出口的至少一个部分,热量通过热卡盘在该基片和该热控制通道中的流体之间传递。该热控制通道可具有沿着流体路径依次串联的第一、第二和第三部分,在横截面视图中该第三部分可被置于该第一部分和第二部分之间。该热控制通道可具有沿着流体路径在该第三部分之后串联的第四部分,该第四部分被置于该第二和第三部分之间。该热控制通道可具有沿着流体路径在该第三部分之后串联的第四部分,该第四部分被置于该第一部分和第二部分之间。该第一、第二和第三部分可以是第一螺旋的部分。该第一部分和第二部分可以是第一螺旋的部分,且该第三部分可以是位 于该第一螺旋上的第二螺旋的部分。该测试器设备可进一步包括加热器,当该流体在该热控制通道外部时,热量由该加热器传递至该流体。该加热器可以是电加热器。热量可以从该基片传递至在高于21摄氏度进入流体入口的该流体。该流体在高于21摄氏度进入流体入口之后,热量可首先从流体传递至该基片。当该流体进入该流体入口时,该流体的温度可以高于100摄氏度。该流体可以是重复循环的。该测试器设备可进一步包括至少一个接口致动器,该接口致动器具有相互可致动的第一致动器部件和第二致动器部件,以相对于该固定结构移动该便携式支撑结构并使该第一接口和该第二接口接合。该第一致动器部件和第二致动器部件可以分别是汽缸和活塞,该活塞沿着该汽缸的内表面滑动。该测试器在该微电子电路上执行的测试可以是老化测试。该基片可以是具有多个微电子电路的晶圆。该接点可以是插脚,每个插脚具有弹簧,当各自的接点被各自的一个端子按压时,插脚顶着弹簧的弹簧力而被按压。本发明还涉及一种测试由基片支撑的微电子电路的方法,包括将该基片支撑在便携式支撑结构中,该便携式支撑结构具有相对着连接到微电子电路的基片的端子的接点;通过固定结构容纳该便携式支撑结构,该便携式支撑结构上的第一接口连接到该固定结构的第二接口,通过该端子、接点、以及第一接口和第二接口,在电测试器和微电子电路之间传输信号,从而测试该微电子电路。该基片可以被支撑在该便携式支撑结构的第一组件和第二组件之间,该 接点可在该第二组件上,进一步包括该第一组件和第二组件相对彼此相向移动,以确保该接点和该端子之间的适当接触。该便携式支撑结构与该基片一起可包括第一元件和第二元件,其中第一元件的CTE与第二元件的CTE之间的CTE比率不等于1。该CTE比率乘以温度变化率的乘积优选在0.8至1.2之间。该第一元件和第二元件可以是在该基片相同侧的信号配电盘和接触器。该元件之一是该基片。该第一组件可以是具有支撑该基片的表面的基片卡盘。该方法可进一步包括在该第一组件和第二组件之间设置压力差动空腔封条,以由该第一组件的表面和第二组件的表面与压力差动空腔封条形成封闭的空腔,减小压力差动空腔封条空腔中的压力,以使该第一组件和第二组件相对彼此相向移动。该压力差动空腔封条可围绕该接点和该端子。当该第一组件和第二组件分离时,该压力差动空腔封条可被固定到该第一组件。该基片空腔封条可以用唇缘封条形成。压力减小通道可被形成穿过该组件中的一个,该压力减小通道具有在该压力差动空腔处的入口和该压力差动空腔外部的出口,在具有该压力减小通道的该组件中的第一阀,进一步包括打开该第一阀允许空气可以从该压力差动空腔中排出,且关闭该第一阀可以阻止空气进入该压力差动空腔。该第一阀可以是止回阀,真空释放通道被形成通过具有该止回阀的该组件,该真空释放通道具有在该压力差动空腔处的入口和在该压力差动空腔外部的出口,在具有该真空释放通道的该组件中的第二真空释放阀,进一步包括:打开真空释放阀使得空气可以进入压力差动空腔,关闭该真空释放阀可以阻止空气从压力差动空腔中逸出。在该便携式支撑结构被该固定结构容纳之前,可以形成该压力差动空腔中的压力。该方法进一步包括通过该第一组件中的基片抽气通道抽出空气,以减小该基片面向该第一组件的一侧上的压力,并将该基片支撑在该第一组件上。该接点可以是被该端子可回复按压的,进一步包括限制至少一个接点的按压,该至少一个接点具有在该第二组件上的托脚的表面。多个单独的托脚可以被置于该接点之间。该方法可进一步包括具有第一侧和与第一侧相反的第二侧的层,第一侧是粘性的并粘接到该第二组件;第二侧是粘性的,该托脚可被粘接到该第二侧。该方法可进一步包括将第一接口的连接盘相对着该固定结构上的第二接口的多个匹配构件设置在该便携式支撑结构上,并用连接盘可回复按压该构件。该方法可进一步包括将该便携式支撑结构的表面相对着热卡盘的表面设置在该固定结构上,并通过该表面传递热量。该方法可进一步包括减小限定在该便携式支撑结构和该热卡盘的表面之间的热接口空腔中的气压。热接口空腔可被限定在该便携式支撑结构和该热卡盘之间,穿过该热卡盘到该热接口真空可形成热接口真空通道。该方法可进一步包括将热接口空腔封条置于该便携式支撑结构和该热卡盘之间,使得该热接口空腔可以由该热接口空腔封条与该便携式支撑结构和该热卡盘一起限定。该方法可进一步包括通过在该固定结构上的热卡盘中的热控制通道的至少一个部分,将流体从流体入口流到流体出口,并在该热控制通道中的该流体和该基片之间传递热量,从而控制该基片的温度。该热控制通道可具有沿着流体路径的依次串联第一、第二和第三部分,在横截面视图中该第三部分可被置于该第一部分和第二部分之间。该热控制通道可具有沿着流体路径在该第三部分之后串联的第四部分,该第四部分被置于该第二和第三部分之间。在该第二和第三部分之间的该热卡盘的温度可以介于该第一部分和第二部分中的流体的温度之间,在该第一和第四部分之间的该热卡盘的温度可以介于该第一部分和第二部分中的流体的温度之间。该第一部分中的流体和第四部分中的流体之间的温度差比该第二部分中的流体和第三部分中的流体之间的温度差大。该热控制通道可具有沿着流体路径在该第三部分之后串联的第四部分,该第四部分被置于该第一部分和第二部分之间。该第一、第二和第三部分可以是第一螺旋的部分。该第一部分和第二部分可以是第一螺旋的部分,且该第三部分可以是不在该第一螺旋上的第二螺旋的部分。当该流体进入该流体入口时,该流体的温度高于21摄氏度。热量可以从该基片传递至以高于21摄氏度的温度进入该流体入口的流体。在该流体以高于100摄氏度的温度进入该流体入口之后,热量可以从该流体传递至该基片。该流体可以是重复循环的。在该微电子电路上执行的该测试可以是老化测试。该基片可以是具有多个微电子电路的晶圆。该接点可以是插脚,每个插脚具有弹簧,当各自接触被各自一个端子按压时,插脚顶着弹簧的弹簧力而被按压。本发明进一步提供一种热控制设备,包括热卡盘,该热卡盘具有热控制 通道,该热控制通道具有入口、出口、以及沿着从流体入口到流体出口的流体路径的依次串联的至少第一、第二、和第三部分,在横截面视图中该第三部分位于该第一部分和第二部分之间。该热控制通道可具有沿着流体路径在该第三部分之后串联的第四部分,该第四部分位于该第二和第三部分之间。该热控制通道可具有沿着流体路径在该第三部分之后串联的第四部分,该第四部分位于该第一部分和第二部分之间。该第一、第二和第三部分可以是第一螺旋的部分。该第一部分和第二部分可以是第一螺旋的部分,且该第三部分可以是不在该第一螺旋上的第二螺旋的部分。本发明进一步涉及测试器设备的电学方面,该测试器设备包括电测试器,通过该接点连接到承载至少一个集成电路的至少一个基片的多个端子,并具有连接到该集成电路的端子,使得电流在电测试器和集成电路之间传导以测试该集成电路。该测试器设备可进一步包括连接至接点的电源电路,其中通过连接至该接点的电源电路提供电能。多个n+1个电源电路互相并联连接,使得n+1个电源电路给集成电路提供电能,如果该电源中的一个故障,则n个该电路仍然给集成电路提供电能。该测试器设备可进一步包括均流电路,其(i)检测至少n+1个电源电路中的一个的功率降低,以及(ii)将从n+1个电源电路中的一个的连接切断,以消除来自该n+1个电源电路中的一个的电流,使得该n个电源电路分担电流。该均流电路可包括多个故障检测电路,每个检测各自的一个电源电路的功率损失。该测试器设备可进一步包括电源控制电路,其由多个电源电路中的至少 一个供电,该电源控制电路将电源电路在测试模式和节能模式之间切换,在该测试模式中多个电源电路中的第一数量的电源电路供电,在该节能模式中第二数量的电源电路供电,第二数量小于第一数量。该测试器设备可进一步包括电流配置电路,该电流配置电路可被配置成在第一配置和第二配置之间切换电流,其中在该第一配置中不同大小的单独电流被提供给单独通道,在该第二配置中供给单独通道的电流遵循公共基准。该电流配置电路可包括多个电流放大器,当电流配置电路在第一配置时,每个电流放大器具有遵循单独基准的输出电流。该测试器设备可进一步包括放大到单独通道的电流的电流放大器。该测试器设备可进一步包括给集成电路提供信号的信号电子装置。该测试器设备可进一步包括支撑至少一个基片的支撑结构,和多个与该端子匹配从而与该端子接触的接点,电测试器通过该接点连接到该端子,使得电流在该电测试器和该集成电路之间传导以测试该集成电路。本发明还涉及一种测试由至少一个基片支撑的至少一个电路的方法的电学方面,包括相对连接到该集成电路的该基片的端子设置接点,并在电测试器和集成电路之间通过该端子和接点传导电流从而测试该集成电路。可通过连接到该接点的电源电路提供电能。多个n+1个电源电路互相并联连接,这样n+1个电源电路给至少一个基片的集成电路提供电能,当电源电路中的一个故障时,n个电路仍然给集成电路供电。该方法可进一步包括检测至少n+1个电源电路中的一个中的功率降低,并且将n+1个电源电路中的一个的连接切断,以消除来自该n+1个电源电路中的一个的电流,使得电流可以被该n个电源电路分担。该方法进一步包括用单独的故障检测电路检测每一个电源电路的功率 损失。该方法可进一步包括从多个电源电路中的至少一个给电源控制电路供电,并利用该电源控制电路在测试模式和节能模式之间切换,其中在该测试模式中多个电源电路中的第一数量的电源电路供电,在该节能模式中第二数量的电源电路供电,第二数量小于第一数量。该方法可进一步包括在第一配置和第二配置之间切换,其中在该第一配置中不同大小的单独电流被提供给单独通道,在该第二配置中供给单独通道的电流遵循公共基准。该电流配置电路可包括多个电流放大器,当电流配置电路在第一配置时,每个电流放大器具有遵循单独基准的输出电流。该方法可进一步包括放大至单独通道的电流。该方法可进一步包括给集成电路提供信号。附图说明本发明进一步通过参考附图的实施方式来描述:图1是晶圆卡盘部件的立体图;图2是图1中2-2的截面侧视图,其是晶圆卡盘部件的一部分和晶圆基片的一部分,其中晶圆基片的垂直方向被放大以用于说明;图3是根据本发明一个实施方式的便携式组装的立体图,其包括晶圆卡盘部件和配电盘部件;图4是从下面看便携式组装的立体图;图5是便携式组装被装配之后与图4相似的视图;图6是图5中便携式组装的6-6上的截面侧视图;图7是便携式组装和固定结构组件的截面侧视图,包括信号分配板、接触器以及热卡盘,其示出了主要的电子细节;图8是固定结构组件和便携式组装的截面侧视图,示出了主要的结构细节;图9是热卡盘和贴附于热卡盘的组件的立体图;图10示出了根据本发明的一个实施方式的测试器设备的组件的示意图;图11是图10中所示的一个电子测试器的平面图;图12是图11的电子测试器的配置功率板的结构图;图13A是图12的配置功率板的电源电路和功率分担电路的电路图;图13B是图12的配置功率板的电压主控器(master)DACS和MUXES的电路图;图13C是图12的配置功率板的高电流从动装置的“主”群的电路图;图14是图13C的主要组的六个电流放大器之一的电路图;以及图15是图12的配置功率板的一个高压从动装置的电压和电流放大器的电路图。具体实施方式附图的图1示出了晶圆卡盘部件10的立体图,图2示出了晶圆卡盘部件10的一部分的截面侧视图。晶圆卡盘部件10包括晶圆卡盘组件12、压力差动基片空腔封条14、偏置环16以及基片抽气通道阀18。晶圆卡盘组件12由铝或另一种具有相对高的热传导率并具有预定的、相对低的热膨胀系数的金属制成。晶圆卡盘组件12具有圆形外表面20以及上表面22和下表面24。外表面20的直径典型地介于350mm和450mm之间,更典型地大约为400mm。上表面22具有形成在其中的多个槽并延伸至外表面20。下表面24也形成在延伸至外表面20的单个平面中。上表面22和下表面24的平面互相平行。下表面24和上表面22具有相同的表面积。偏置环16具有上表面26和下表面28。偏置环16的下表面28被设置在 晶圆卡盘组件12的上表面22的顶端,偏置环16用紧固件30固定到晶圆卡盘组件12上。因此,偏置环16的上表面26在和晶圆卡盘组件12的上表面22的平面垂直隔开的平面内。偏置环16还具有内表面32和外表面34。内表面32与晶圆卡盘组件12的上表面22的中央部分共同定义了容纳具有圆形外缘的晶圆的圆形凹部36。在提供的示例中,晶圆可以具有大约200mm的直径。通过移走偏置环16可以容纳更大的晶圆。基片空腔封条14被形成为封闭圆环,其完全地包围偏置环16和用于晶圆的凹部36。基片空腔封条14是唇形封条,具有下锚部40和上唇42。下锚部40被固定在形成于晶圆卡盘组件12的上表面22的外部区域的槽中。由于基片空腔封条14的热伸缩性,下锚部40锚定在槽中。唇42具有上表面46,其在和偏置环16的上表面26的平面垂直隔开的平面内。唇42的上表面46在朝着晶圆卡盘组件12的方向上是可回复按压的。在上表面46上施加压力使唇42弯曲,使得上表面46向下移动,当撤去压力后,由于唇42的回复力上表面46向上移动。基片抽气通道50形成在晶圆卡盘组件12中。基片抽气通道50包括第一部分52、第二部分54和第三部分56。第一部分52从晶圆卡盘组件12的外表面向中心钻入。第二部分54的长度大约是晶圆卡盘组件12的外表面20的直径的三分之一。第一部分52从晶圆卡盘组件12的上表面22钻入,第一部分52在晶圆卡盘组件12的上表面22上形成有进气口60。第三部分56从晶圆卡盘组件12的下表面24接近下表面24的外围钻入第二部分54。第三部分56在下表面24形成出气口62。三个圆形槽64、66和68以及狭槽70被形成在晶圆卡盘组件12的上表面22中。圆形槽64、66和68是同心的,且中心和晶圆卡盘组件12的外表面20的中心重合。狭槽70形成为和圆形槽64、66以及68的深度相同,且 将圆形槽64、66和68互相连接。进气口60位于圆形槽66和68之间的狭槽70中。基片抽气通道阀18是梭形滑阀,其从晶圆卡盘组件12的外表面20插入到基片抽气通道50的第二部分54,然后用插塞72封闭基片抽气通道的第二部分54。基片抽气通道阀18具有底座74和球形阀组件76。当出气口62的压力低于进气口60的压力时,球形阀组件76抬起底座74使得空气从进气口60流入出气口62。当进气口60的压力低于出气口62的压力时,球形阀组件76靠在底座74上,从而防止空气从出气口62流到进气口60。压力释放开口80被形成在晶圆卡盘组件12的下表面24中,并在基片抽气通道阀18的与进气口60相反的一侧上与基片抽气通道50的第二部分54连接。在进气口60的压力低于出气口62的压力,球形阀组件76靠在底座74上的情况下,释放开口80的压力可以被降至低于进气口60的唇缘压力,使得球形阀组件76抬起底座74。当球形阀组件76抬起底座74时,空气从进气口60经过球形阀组件76流到出气口62。图2进一步示出了插入到晶圆卡盘部件10之前的晶圆基片82。晶圆基片82的垂直尺寸被放大以利于示出。晶圆基片82具有上表面84、平行的下表面86以及圆形边缘88。晶圆基片82还包括多个集成微电子电路90,形成在上表面84的下面并和下表面86隔开。每个集成微电子电路90包括多个电子元件,例如电容器、二极管、和/或晶体管,通过用金属线、插塞或通孔互相连接。晶圆基片82还具有在上表面84的多个金属端子92。在当前示例中,端子92具有上表面,其形成了稍高于上表面84的平面。因此在当前示例中,晶圆基片82的总厚度是测量从下表面86到端子92之一的上表面。集成微电子电路90的每一个具有多个与之连接的端子92。在使用中,进气口60和释放开口80被保持在环境压力下。晶圆基片82被置于凹部36中。晶圆基片82的下表面86被设置在晶圆卡盘组件12的上 表面22的顶部。晶圆基片82的边缘88与偏置环16的内表面32配合。在狭槽70和下表面86之间定义了一个小封闭空间。参考图1和2,封闭空间延伸至圆形槽64、66和68,被晶圆基片82的下表面86从顶部封闭。泵连接到出气口62,用于将出气口62处的压力降至环境压力以下。此时出气口62的压力低于进气口60的压力,使得球形阀组件76将底座74抬起。由圆形槽64、66、68和狭槽70限定的封闭空腔中的少量空气被抽出,通过基片抽气通道50、通过基片抽气通道阀18、然后到出气口62之外。此时由圆形槽64、66、68和狭槽70限定的封闭空腔在环境压力以下。晶圆基片82的上表面84处于环境压力。比在晶圆基片82的上表面84处低的下表面86的压力顶着晶圆卡盘组件12的上表面22而支撑晶圆基片82的下表面86。晶圆基片82的对准,尤其是相对于晶圆卡盘部件10的端子92的对准,是通过顶着晶圆卡盘组件12的上表面22支撑晶圆基片82来保持的。出气口62可以再次被置于环境压力。因为进气口60仍然低于环境压力,球形阀组件76保持在底座74上,甚至在出气口62恢复到环境压力之后。由于在任何时候都可能需要将晶圆基片82从晶圆卡盘部件10移走,释放开口80的压力可以被置于低于进气口60的压力。此时进气口60的压力高于释放开口80的压力,使得球形阀组件76抬起底座74。进气口60被连接至出气口,且少量空气从出气口流到进气口60,再到圆形槽64、66、68,并进入狭槽70。因此晶圆基片82的下表面86被置于环境压力下,从而和晶圆基片82的上表面84的压力相同。此时晶圆基片82可以从晶圆卡盘部件10被移走。图3和4示出了用于支撑晶圆基片82的便携式组装108,其包括晶圆卡盘部件10和配电盘部件110。图3和图4没有详细地示出配电盘部件110的电路径,包括接点、接口和通孔。仅仅示出了配电盘部件110的结构组件。结构组件包括金属背板114、信号配电盘116、和接触器的背部构件118。金属背板114具有基本矩形形状。圆形开口120形成在金属背板114中。金属背板114的两个相对边缘122用机器加工,使得金属背板114其余部分稍厚于相对边缘122,并且相对边缘122的每个都定义各自的凸缘。信号配电盘116包括基片124,其具有比金属背板114稍小的基本矩形形状。信号配电盘116位于相对边缘122限定的凸缘之间,紧固件126被用于将基片124固定在金属背板114上。接触器的背部构件118是圆形的且位于基片124的中心,与信号配电盘116相对。夹紧环128位于背部构件118的边缘之上。紧固件130被用于将夹紧环固定到信号配电盘116的基片124。夹紧环128具有比接触器的背部构件118大的外部边缘,以及比接触器的背部构件118稍小的内部边缘。由于夹紧环128的尺寸,夹紧环128将接触器的背部构件118固定到信号配电盘116的基片124。夹紧环128的外径稍小于晶圆卡盘部件10的偏置环16的内表面32的直径。信号配电盘116进一步具有基片124上的金制底座134。金制底座134是环形形状,其内径和外径分别比基片空腔封条14的上表面46的直径稍小和稍大。配电盘部件110的组件都具有相似的、相对高的热膨胀系数。图5示出了将配电盘部件110置于晶圆卡盘部件10顶部后的便携式组装108。金制底座134被置于配电盘部件110的底部,并位于晶圆卡盘部件10顶部的基片空腔封条14的顶部。参考图6,基片空腔封条14被置于底部的晶圆卡盘组件12和顶部的信号配电盘116的基片124之间。晶圆卡盘组件12、基片空腔封条14、和信号配电盘116的基片124共同限定了封闭的压力差动空腔140。压力差动空腔140延伸至晶圆基片82和接触器的背部构件118之间的空间。在基片空腔封条14的唇42偏移之前,压力差动空腔140也延伸至晶圆卡盘部件10 的偏置环16和信号配电盘116的基片124之间的空间。压力差动空腔140还延伸至形成在晶圆卡盘组件12的上表面22上的圆形槽142中,夹紧环128的凸出部分位于槽142中。在夹紧环128的下表面和槽142的上表面之间提供小空间,以允许夹紧环128的内部和外侧的压力差动空腔140的内部和外部体积之间可以连通。压力减小通道144被形成在晶圆卡盘组件12中,压力减小通道止回阀146被置于压力减小通道144内。压力减小通道144包括第一部分148、第二部分150、和第三部分152。第一部分148是从晶圆卡盘组件12的上表面22钻入,并在上表面22形成进口154。第三部分152是从晶圆卡盘组件12的下表面24钻入,并在下表面24形成出口156。第二部分150是从晶圆卡盘组件12的外表面20钻入,并将第一148和第二部分150互相连接起来。压力减小通道止回阀148从晶圆卡盘组件12的外表面20插入到第二部分150,插塞158用于封闭外表面20的第二部分150的入口。压力减小通道止回阀具有阀组件162和底座164。当空气从入口154流到出口156时,阀组件162抬起底座164。因为阀组件162靠在底座164上,所以空气被阻止从出口156流到入口154。偏置环16具有形成在其下侧的多个狭槽168。图6示出狭槽168的一个的横截面,其将压力减小通道144的入口154连接到压力差动空腔140。另外,狭槽168向偏置环16的中心放射状地延伸,并且将压力减小通道144的入口154与偏置环16下侧的圆形槽142连接。在使用中,压力差动空腔140最初在环境压力下,出口156连接泵,使得出口156在低于环境压力下。这样在进气口154和出口156之间产生压力差量,使得通过压力减小通道144中的压力减小通道止回阀146,空气从压力差动空腔140被抽出。压力差动空腔140中的压力降至低于环境压力。便携式组装108外侧的压力保持在环境压力,由此产生压力差量,其中压力差 动空腔140中的压力低于信号配电盘116的基片124上方的压力和晶圆卡盘组件12的下表面24下方的压力。压力差量使基片空腔封条14的唇42偏移,并使压力差动空腔140的垂直高度减小。压力差动空腔140的垂直高度继续减小直到信号配电盘116的基片124的下表面和偏置环16的上表面接触。这样,偏置环16限制信号配电盘116的基片124和晶圆卡盘组件12之间的相对运动。之后,出口156可以再次被置于环境压力下并且与泵断开连接。阀组件162靠在底座164上,并阻止空气通过压力减小通道144进入压力差动空腔140。因此压力差动空腔140保持减小的尺寸,其中信号配电盘116的基片124接触偏置环16。便携式组装108可以从用于将泵连接到开口156并降低压力差动空腔140中的压力的任何设备移走,然后传送到子系统的测试器。如图7所示,背部构件118形成了接触器170的部分,接触器170还包括多个插脚172、托脚(stand-off)174、粘合剂176。每一个插脚172具有第一组件178和第二组件179以及各自的弹簧182。第一组件178在其中具有空腔,弹簧182位于空腔中。第二组件179的一部分也在空腔中,并支撑弹簧182。第一组件178和第二组件179被互相安装并可以相对彼此移动。第二组件179的端子相对第一组件178的端子的移动压缩弹簧182。因此第一组件178和第二组件179的端子相向移动需要力来克服弹簧182的弹力。该力确保插脚172和晶圆基片82的端子92之间的适当接触。当撤去该力时,第一组件178和第二组件179的端子由于弹簧182的弹力而互相远离对方移动。在可替代实施方式中,可以通过组件例如隔板或不是卷簧的另一个弹簧来产生弹力。背部构件118被形成为两个半部分,每个半部分分别具有形成在其中的开口组。插脚172之一的端子之一通过背部构件118的半部分之一中的一个开口被插入,而插脚172的另一个端子通过构件118的另一个半部分的开口 之一被插入。每个插脚172的端子通过背部构件118的两个半部分中的各自的一对开口被插入。当背部构件118的半部分互相固定时,插脚172被保持在背部构件118中。插脚172的端子在接触器170的底部形成各自的接点184阵列,并在接触器170的顶部形成相应的接点186阵列。除基片124之外,信号配电盘116还包括多个接点188、多个连接盘193、多个金属线191。接点188和连接盘193位于基片124的相同侧。接点188在图4示出的基片空腔封条14的内侧,连接盘193在基片空腔封条14的外侧。每一个金属线191将各自的接点188中的一个和各自的连接盘193中的一个连接。这样,通过信号配电盘116的各自的接点188、各自的金属线191、和各自连接盘193形成各自导体。当接触器170的背部构件118被固定到信号配电盘116的基片124时,接触器170的各自的接点186的一个接触信号配电盘116的各自的接点188的一个。托脚174是粘附到接触器70的背部构件118的下表面的薄层材料。粘合剂176是具有上和下粘接表面的层。粘合剂176的下粘接表面被粘附到托脚174之一的上表面。粘合剂176的上粘接表面被粘附到接触器170的背部构件118的下表面,从而将托脚174粘附到接触器170的背部构件118上。当图6中的压力差动空腔140中的压力降低时,托脚174也靠近晶圆基片82移动。托脚174朝向晶圆基片82的移动造成接触器170的接点184被晶圆基片82的端子92弹性压缩。此时,托脚174的下表面和晶圆基片82的上表面84接触。因此托脚174的下表面限制接点184压缩到接触器170的背部构件118中。多个分离的托脚174位于接点184之间。多个传导路径被形成。每个传导路径包括晶圆基片82的各自的端子92中的一个、接触器170的各自的插脚172以及信号配电盘116的各自的接点188、金属线191以及连接盘193。信号配电盘116的连接盘193和接点188在与晶圆基片82的端子92的平面平行的平面中。再次参考图1,便携式支 撑结构具有底部的晶圆卡盘组件12和顶部的配电盘部件110的结构组件,其中晶圆基片82在晶圆卡盘组件12和配电盘部件110的结构组件之间。再次参考图7,接触器170的接点184提供了晶圆基片82的端子92的电接点,且配电盘部件110具有由连接盘193形成的用于连接另一个装置的接口。如图4至7所示的便携式组装108现在被传送至测试系统,其可以接触由连接盘193形成的接口,并向晶圆基片82提供测试信号、功率以及接地端。接触器170的接点184和晶圆基片82的端子92被基片空腔封条14整体地围绕,从而防止污染物或湿气。如图8所示,便携式组装108被固定结构180容纳。固定结构180具有位于系统(未示出)中固定位置的框架181。固定结构180的组件是相互可移走的。除框架181之外,固定结构180包括容纳便携式组装108的支撑结构185、四个致动器187(仅示出其中之一)、接口部件189、热卡盘190以及热卡盘190的装配装置192。致动器187包括汽缸194、汽缸194中的活塞196以及连接到活塞196的连接块198。活塞196可以在汽缸194中垂直地向上或向下滑动,在活塞196的后面以及前面可以增加和减小压力,从而在垂直向上或向下方向上移动活塞。连接块198具有安装在活塞196上的下端和安装在支撑结构185上的上端。从而支撑结构185与活塞196一起向上和向下移动。接口部件189具有接口部件基片200和多个插脚202。插脚202支撑在接口部件基片200内。接口部件基片200被固定在框架181的上表面。接口部件基片200和框架181限定了圆形开口204,其稍大于晶圆卡盘组件12的外表面20的直径。水平狭槽205形成在支撑结构185的内侧。相似的狭槽(未示出)形成在支撑结构185的另一部分。配电盘部件110的金属背板114的边缘122上的凸缘在进入纸面的方向上被插入狭槽205。相对的边缘(参见图3)同时 被插入支撑结构185的另一个狭槽。此时,便携式组装108被支撑结构185的相对的部分悬挂。狭槽205支持形成在边缘122的凸缘,以防止便携式组装108相对于支撑结构185垂直向上或向下移动。当活塞196在汽缸194中向下移动时,支撑结构185也向下移动,且便携式组装108向下移动与固定结构180的接口部件189接触。再次参考图7,示出了图8的固定结构180的组件,包括接口部件189和信号与功率板206。插脚202的每一个包括第一组件208和第二组件210以及弹簧212。第二组件210具有位于第一组件208的一部分中的部分。弹簧212也位于第一组件208的一部分中。插脚202具有两个相对的接点,分别在第一组件208和第二组件210上。接点的相向移动需要力来克服弹簧212的弹力以压缩弹簧212。当压缩弹簧212的力撤去时,接点背向彼此移动。接口部件基片200具有两个半部分,在每一半部分上形成有多个开口。第一组件208的插脚部分和第二组件210的插脚部分被插入该两个半部分的相对开口中。由此每个插脚202具有在接口部件189的顶部的接点和底部的接点。信号与功率板206具有基片214、多个接点216、和以迹线、金属线和/或通孔形式的多个金属导线218。接点216被形成在基片214的上表面。金属导线218连接到接点216。接口部件基片200被安装到信号与功率板206的基片214上。每个插脚202的每个第一组件208的接点与信号与功率板206的各自的接点216接触。图7所示的接口部件189通过信号与功率板206被安装到图8所示的框架181。当便携式组装108向下移动与接口部件189接触时,信号配电盘116的每一个连接盘193接触接口部件189的各自插脚202的各自第二组件210的各自的接点。在便携式组装108向下进一步的移动后,连接盘193压缩插脚202顶部的接点。图8中致动器187产生的力确保了连接盘193和插脚202 之间的适当接触。此时,晶圆基片82的端子通过接触器170的插脚172、信号配电盘116的接点188、金属线191和连接盘193、以及接口部件189的插脚202连接到信号与功率板206的接点216和金属导线218。再次参考图8,装配装置192包括多个安装块220(仅示出其中之一)、弹簧装置224。热卡盘190通过安装块220的每一个和各自弹簧装置224被安装到框架181。便携式组装108向下的移动使得晶圆卡盘组件12的下表面24与热卡盘190的上表面接触。晶圆卡盘组件12的下表面24和热卡盘190的上表面之间的平面性的微小差别通过弹簧装置224调整。图9示出了热卡盘190、安装块220、热接口空腔封条226以及两个转接器228和230。热接口空腔封条222是形成在热卡盘190的上表面232中圆形槽242中的O形环状封条。热接口空腔封条226形成了围绕热卡盘190中心点的封闭环。热接口空腔封条226的大约三分之二被插入热卡盘190的上表面232中的槽中,热接口空腔封条226的大约三分之一保持在上表面232之上。用于热接口空腔封条222的槽的横截面近似为矩形,并可以容纳整个热接口空腔封条226。如果上表面232之上的热接口空腔封条226的三分之一被压缩到槽中,则热接口空腔封条226的上表面将在和上表面232相同的平面内。从热卡盘190的上表面232到下表面236形成热接口真空通道234。多个真空槽240被形成在热接口空腔封条226中区域的热卡盘190的上表面232中。热接口真空通道234在真空槽240之一中具有入口。真空槽240之一是从热卡盘190的上表面232的中心点放射延伸的狭槽。四个真空槽240是同心环,其中心在热卡盘190的上表面232的中心。真空槽240被互相连接,从而在热卡盘190的上表面的下面形成了单个的互相连接的空腔。在热接口空腔封条226外侧的上表面232的区域中从上表面232到下表 面236形成真空口242。真空口封条244被形成在围绕真空口242的槽中。真空口242与图6所示的晶圆卡盘组件12中压力减小通道144的出口156对准并连接。在使用中,图6中的晶圆卡盘组件12的下表面24与图9中所示的热接口空腔封条226以及真空口封条244接触。热接口空腔的底部由热卡盘190的上表面232限定、顶部由热卡盘组件12的下表面24限定,侧部由将热卡盘190的上表面232和晶圆卡盘组件12的下表面24连接的热接口空腔封条226限定。热接口真空通道234通过阀(未示出)永久地连接至泵,且通过热接口真空通道,空气从热接口空腔中被抽出,从而减小了热接口空腔中的压力。因此热接口空腔中的压力低于便携式组装108上的环境压力和热卡盘190下的环境压力。热接口空腔的尺寸减小,直到晶圆卡盘组件12的下表面24与热卡盘190的上表面232接触,并且热接口空腔封条226被压缩到其槽中。此时,热接口空腔仅剩余的部分由真空槽240限定,且减小的压力在真空槽240中被保持以保持表面24和232互相相对。因为表面24和232互相相对,因此热量可以在热卡盘190和晶圆卡盘组件12之间的两个方向上传导。真空口封条244通过晶圆卡盘组件12的下表面24围绕压力减小通道144的出口156来密封。在压力减小通道止回阀146发生泄漏时,泵将真空口242保持在减小的压力下,从而将出口156保持在减小的压力下。热卡盘190由互相铜焊的上片和下片252和254来补偿。热控制通道256被机器加工在上片252的下表面中。如图9所示,热控制通道256具有通过下片254形成的入口258和出口260。流体可以从入口258流过热控制通道的连续部分并从出口260流出。热控制通道256的第一个半部分形成第一螺旋268,从平面图上看是顺时针方向至热卡盘190的中心。热控制通道256的第二个半部分形成第二螺旋270,逆时针方向远离热卡盘190的中心。第 一螺旋268的两个部分之间有第二螺旋270的一个部分。第二螺旋270的两个部分之间有第一螺旋268的一个部分。这样,热控制通道256具有例如依次串联的第一、第二和第三部分,从横截面的平面图看,第三部分位于第一部分和第二部分之间。热控制通道256还具有第三部分之后串联的第四部分。取决于在何处选择第四部分,第四部分可以在第二和第三部分之间,也可以在第一部分和第二部分之间。在任何一种情况下,第一部分和第二部分均为第一螺旋部分,第三部分是不在第一螺旋上的第二螺旋部分。例如,流过入口258的流体和流出出口260的流体之间有10摄氏度的温度差。热卡盘190的外部区域中的热控制通道256邻近部分的温度将有10摄氏度的温差。但是,热卡盘190的外部区域的两个部分之间的温度是入口258和出口260的温度的平均值,即,入口258温度以上5摄氏度和出口260温度以下5摄氏度。当流体流向热卡盘190的中心,流体传导热量,在热卡盘190中心附近,热控制通道256的邻近部分之间的流体的温度可能仅为4摄氏度。但是,热卡盘190中心附近的热控制通道256的邻近部分之间的温度差仍然和入口258和出口260的平均温度一样。因此热卡盘190的外部区域和中心附近具有相同的温度。转接器228和230被安装到热卡盘190,并连接到入口258和出口260。图10示出了测试器设备300,其包括多个图8中所示的组件,包括多个便携式组装108、多个热卡盘190、以及多个接口部件180。每个便携式组装108被连接到各自的热卡盘190,且每个便携式组装108具有各自的连接盘接口,其与各自的插脚接口接触而不考虑接口部件180。测试器设备300进一步包括多个电测试器302和热控制系统304。一个或两个电测试器302被连接到每个便携式组装108。每个电测试器302被配置成根据预编程的指令集运行老化测试。指令被用来通过各自的一个接口部件189传送电子信号到支撑在便携式组装108的晶圆基片的微电子 电路(未示出),并接收来自该微电子电路的电子信号。热控制系统包括入口管306和出口管308、入口总管310和出口总管312、冷却热交换器314、循环泵316以及加热装置318。每个入口管306从各自的转接器,例如图9中的转接器228断开连接,每个出口管308被连接至各自的转接器,例如图9中的转接器230。闭环阀由热卡盘190的一个中的热控制通道256、出口管308的一个、出口总管312、通过热交换器314的路径、泵316、通过加热装置318的路径、入口总管310以及入口管306中的一个来形成。热卡盘190的热控制通道256与总管310和312并行连接。热交换器314还具有连接至水源和排水设备的路径。室温下的水流过热交换器314,且热量可以传导至水。加热装置318具有连接至电压源的电线圈。当电源打开时电线圈加热。当电流流过加热线圈时,热量可从加热线圈传输。在使用中,定义重复循环路径的组件最初用油填充。泵316打开,油通过加热装置318、入口总管310、入口管306、热卡盘190、出口管308、出口总管312以及热交换器314重复循环返回泵316。当打开电压源时,加热装置318的电线圈加热,热量从电线圈传输至油。油从室温21摄氏度加热至100摄氏度以上,尤其到接近170摄氏度的温度。170摄氏度的油进入热卡盘190,并逐渐加热热卡盘190。因为热量被传送至热卡盘190,所以通过出口管308留在热卡盘190的油处在较低温度,例如,150摄氏度。当热卡盘190被加热到足够高的温度用于测试图2中的集成微电子电路90时,电子测试器测试集成微电子电路90。尤其是在集成微电子电路90上执行老化测试。当集成微电子电路被测试,它们逐渐加热且需要被冷却以保持在适于老化测试的温度。到加热装置318的电线圈的电流被切断。来自水源的水被打开。热量从油传输至水源的水,从而将油冷却。进入热卡盘190的油现在可 以在例如160摄氏度,保留在热卡盘190中的油可以在170摄氏度。热交换器314将油从170摄氏度冷却到160摄氏度。应当注意,油一般不需要冷却至150摄氏度以下。根据实施的测试,发现没必要将油温降到例如100摄氏度以下或到室温。而油的高流速典型地介于3到5公升(liter)每分钟,足以防止热卡盘190过热,并保持在170摄氏度。局部加热被用于测试器设备300中。相反,常规的老化测试具有老化加热炉和运载集成微电子电路封装老化舱,该集成微电子电路封装被插入到老化加热炉。热量从老化加热炉中的空气中转换到集成微电子电路封装和老化板上。在一般的加热装置中,加热的空气围绕载有集成微电子电路封装的老化板。在图10的测试器设备的局部加热装置中,围绕便携式组装108的空气一般大约在21摄氏度的室温下,且便携式组装108的局部区域通过热卡盘190而被加热(或冷却)。局部加热具有其自身独特的问题。再次参考图3和4,信号配电盘部件116没有在室温之上加热到和接触器170的背部构件118一样多,接触器170的背部构件118没有在室温之上加热到和晶圆基片82一样多。接触器170的背部构件118可以例如从21摄氏度加热到171摄氏度,同时信号配电盘部件116可以从21摄氏度加热到121摄氏度。接触器170的背部构件118和信号配电盘部件116的热膨胀系数被设计,使得接触器170的背部构件118和信号配电盘部件116以相近的速率膨胀和收缩。在一个给定示例中,信号配电盘部件116的热膨胀系数(CTE)可以是百万分之十(10ppm),接触器170的背部构件118的CTE可以是4.5,同时,晶圆基片82的CTE可以是给定的3.2。在另一个示例中,在不同的热条件下,信号配电盘116的CTE可以在5和6之间,或者可以甚至低于接触器170的背部构件118的CTE。在给定示例中,信号配电盘116的CTE和接触器170的背部构件118的CTE的CTE比率是2.22。CTE比率定义如下:CTE比率=第一元件的CTE/第二元件的CTE信号配电盘116可以从低的信号配电盘温度加热到高的信号配电盘温度,接触器170的背部构件118可以从低的接触器温度加热到高的接触器温度以及温度比率。温度增长比率定义如下:温度增长比率=(第二组件的高温-第二组件的低温)/(第一组件的高温-第一组件的低温)CTE比率和温度增长比率的乘积可以被定义如下:CTE比率×温度增长比率=χ理想地,χ应该尽可能接近1。在优选实施方式中,χ可以比CTE比率更接近1。典型地,CTE比率在0.2和5之间,更优选地在0.9和1.1之间,而χ优选在0.8和1.2之间。再次参考图8。在完成集成微电子电路90的老化测试之后,升起支撑结构185,从而将便携式组装108的连接盘接口从接口部件189断开。此时,在出纸面的方向上通过滑动便携式组装108将便携式组装108从支撑结构185上移走。再次参考图6。穿过晶圆卡盘组件12形成真空释放通道272,真空释放阀274被置于真空释放通道272中。真空释放通道272具有第一部分276、第二部分278和第三部分280。第一部分276和第二部分278分别从晶圆卡盘组件12的下表面24和上表面22被钻入。第二部分336从外表面20被钻入,并将第一部分276和第二部分278互相连接。第一部分276具有进气口282,第二部分336在压力差动空腔140中具有出气口284。真空释放阀是梭形滑阀,释放阀开口286形成在真空释放阀274的与真空释放通道272的出气口284相反的一侧上的晶圆卡盘组件12的下表面24中。进气口282通常保持在环境压力下。压力差动空腔140中的较低压力保持真空释放阀274的球形阀组件288在其底座290上。为了打开便携式组装 108,释放阀开口286的压力被降低至低于压力差动空腔140中的压力。压力差动空腔140和释放阀开口286之间的压力差使得球形阀组件288移开底座290。此时进气口282与出气口284连通,空气经过真空释放通道272流到压力差动空腔140中。压力差动空腔140回到环境压力。因为压力差动空腔140的和便携式组装108外部的空气压力相同,因此配电盘部件110可以被晶圆基片82和晶圆卡盘部件10抬起。此时可以从晶圆卡盘部件10上移走晶圆基片82。图11示出了图7和8中所示的基片214中的两个,其形成单个接口,并且还示出图10的电测试器302中的一个。电测试器302包括底板322、配置电源板(CPB)324、插脚电子板(PEB)326、测试电子板(TEB)328、压模电源板(DPB)330和多个电源总线333。配置电源板324和插脚电子板326通过底板322在结构上被连接至压模电源板330。配置电源板324和插脚电子板326还电连接到各自的一个电源总线333。测试电子板328安装在顶部并与插脚电子板326电连接。电测试器302和从热和机械上与基片214断开。多个柔性附件(未示出)被用于将压模电源板330连接到基片214。多个连接器332位于基片214上并通过导体218连接至图7中的接点216。另一组连接器334位于压模电源板330上。每个柔性附件具有在相对端的两个连接器。柔性附件的连接器的一个被连接到连接器332中的一个,而柔性附件的相对的连接器连接至连接器334中的一个。配置电源板324、插脚电子板326和测试电子板328可以通过底板322中的连接器335、压模电源板330以及至图2中集成电路92的柔性附件提供电能、信号和接地。板324,326,328和330中的每一个具有各自的基片和在各自的基片上的各自的电路,通过这些板可以给电路92提供或从电路92提供电能、接地或信号。如图12所示,配置电源板324包括四个电源电路340(IBC48V至12V@500W)。电源电路340互相并联连接。如果电源电路340中的一个故障,其余的电源电路340仍然可以提供电能。因此四个电源电路340是n+1,其中n是3。如果电源电路340中的一个故障,n个电源电路340仍然可以提供电能。均流电路将电源电路340连接至电源总线341。均流电路检测来自电源电路340之一的电能何时减小至零以下。在检测n+1个电源电路340中的一个的电能损失后,均流电路切换掉从n+1个电源电路340中故障的一个的连接,以消除来自失效的n+1个电源电路340中故障的一个的电流。此时,n个没有故障的电源电路340分担电流。图13A示出了每一个电源电路340被连接到各自的故障检测电路342。故障检测电路342共同地弥补了图12的均流电路。每个故障检测电路342检测各自的一个电源电路340的功率损失,并断开各自电源电路340与电源总线341的连接。在故障检测电路342中,为了将电源电路340连接至电源总线341,输入电压(VIN)必须比输出电压(VOUT)正向更大。如果VIN不比VOUT正向更大,则GATE被释放能量且在故障线上提供故障信号(IBCFAULTIN)。在图12中,故障被提供给电源控制电路344,其被连接到控制线(IBC_INHIBIT_N)。电源控制电路344可以用于切换电源电路340提供的电能的开或关。所有的电源电路340在电源控制电路344的控制下。电源控制电路344也由电源电路340通过电源总线341供电。电源控制电路344被编程以控制哪一个电源电路340切换为开和哪一个切换为关。电源电路340中的一个一直开启,由此一直给电源控制电路344供电。这样,避免了电源控制电路344的功率损失,且不需要重启和重新编程。这样使得电源控制电路344在测试模式和节能模式之间切换,其中在测试模式中所有四个电源电路340都供电,在节能模式中只有一个电源电路340供电。均流 电路检测到除一个电源电路340之外的所有电源电路340的功率损失,并将除一个电源电路340之外的所有电源电路340从电源总线341上断开。图13A中所示的电路给电源总线314提供12V电能。图12示出了电压主控器DACS和MUXES电路346,其也示于图13B中。图13B中的电路设立了四个主控器电压等级(HIC_VMASTER0到HIC_VMASTER4)。单独的数模转换器(12BITDAC)调节主控器电压。这样,图13B的电路可以同时提供四个不同电压,每个可以由多路服用器(DG408)切换五个不同的等级。图13B的电路处在图12的电源控制电路344的控制下。再次参考图12,电压主控器DACS和MUXES电路346连接到高电流从动装置348、高电压从动装置350、和另外的从动装置352。每个高电流从动装置348排列在六个高电流模块的“主”群中。高电流从动装置348的八个“主”群排列在48个高电流模块的“超”群中。四个高电压从动装置350排列在高电压从动装置350的“主”群中,高电压从动装置350的四个“主”群排列在16个高电压模块的一个“超”群中。由电压主控器DACS和MUXES电路346提供的四个电压在四条单独的导线上被提供给高电流从动装置348的每个“主”群和高电压从动装置350的每个“主”群。图13C示出了图12的高电流从动装置348的“主”群之一。六个电流放大器356被提供。电流放大器356的电压调节线(VADJ)连接到公共导线358。导线358通过开关360、两个放大器362和364、以及电压选择器366连接到图13B中电路右边的四个电压导线(VMASTER)。电压选择器366用于选择提供给电流放大器356的四个电压中的各自的一个。图14示出了图13C中的电流放大器356中的一个。电流放大器356具有电流放大模块370、放大器372、开关374、以及到放大器372的第一输入导线376和第二输入导线378。电流放大模块370具有电压基准(V0ADJ),其连接到图13A中的电源 总线341上的12V电源,以提供电流到输出(VOUT)。电压基准导线(V0ADJ)通过放大器372和第一输入导线376连接到图13C中的公共导线358。电流放大模块370将输出(VOUT)驱动为和电压基准导线(V0ADJ)相同的电压。当开关374在第一配置时,其中第二输入导线378从读出线(VSENSE)断开,第二输入导线378上的电压遵循VOUT,因此保持VOUT局部锁定到VADJ。当开关374为第二配置时,其中读出线(VSENSE)连接到放大器372的第二输入导线378,放大模块370上的基准遵循读出线(VSENSE)上的远程电压。此时输出(VOUT)上的电压在读出线(VSENSE)的控制中。应当理解输出(VOUT)和输入(VSENSE)最终都连接到图2中基片82的端子92。再次参考图13C,每一个电流放大器356具有单独输出(VOUT)和单独的读出线(VSENSE)。在各自读出线上可以读出单独的电压,当图13C和14中所示的电流配置电路在第二配置时,到各个输出导线的电流可以不同。在第二配置中,开关360将公共导线358连接到放大器362。在第一配置中,开关360将公共导线358连接到放大器384。放大器384具有第一输入导线386和第二输入导线388。第一输入导线386连接到来自放大器362的输出。第二输入导线388连接到仅一个电流放大器356的读出线(VSENSE0)。因此当图13C和14的电流配置电路在第一配置时,公共导线358上的电压遵循读出线(VSENSE0)上的电压。再次参考图12,除了每一个电流放大器356被用作电流和电压放大器,高电压从动装置350的每个“主”群包括与图13C中电流配置电路相同的电路。每一个电流和电压放大器具有各自的电路,如图15所示。除了具有四个电压分压器电阻R1、R2、R3和R4之外,图15的电压和电流放大器和图 14的电流放大器相同,且图14中的电流放大模块370作为电流和电压放大模块。读出线(HIV_VSENSE)通过电阻R1连接到开关374。读出线(HIV_VSENSE)还连接到电阻R1和R2再接地。因此电阻R1和R2作为读出线(HIV_VSENSE)到开关374上电压的电压分压器。相似地,开关374通过电阻R4连接到电压和电流放大模块370的电压读出线(VSENSE)和输出(VOUT),并且开关374上同样的端子还通过电阻R3连接到地。电压和电流放大模块370根据其VTRIM导线上的电压来放大电压。尤其参考图13和14,可以看出,操作者可以在第一配置和第二配置之间切换。在第一配置中,可以提供例如60A的电流并被六个从动模块输出分担。在第二配置中,六个不同模块输出中的每一个可提供大约10A的电流,并且电流可以互相独立地浮动。这些示例性的实施方式已经被描述并示于附图中,应当理解这些实施方式仅是说明性的,并不限制本发明,因为本领域技术人员可以做出变型,所以本发明不限于示出并描述的具体的结构和排列。