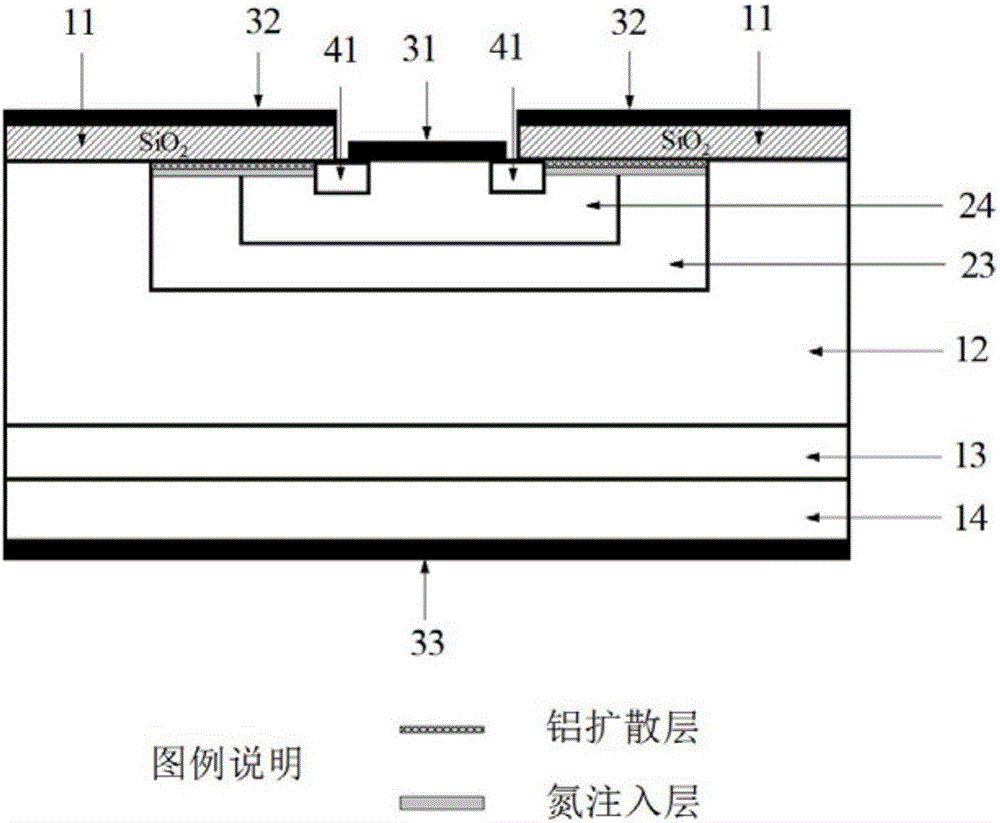
本发明属于高压电力电子
技术领域:
,涉及电压控制型功率半导体器件,涉及减小4H-SiC/SiO2界面态密度、提高4H-SiC电压控制型功率半导体器件反型层迁移率、降低4H-SiC电压控制型功率半导体器件的导通和开关损耗、稳定4H-SiC电压控制型功率半导体器件阈值电压的方法。特别地,本发明是采用引入三价元素和五价元素的方法来改善4H-SiC电压控制型功率半导体器件反型层迁移率,具体的是一种低功耗4H-SiC电压控制型功率半导体器件。
背景技术:
::长期以来,硅(Si)材料一直在半导体领域占据着主导地位,并应用于高温、高频电路当中。但随着技术的进步和应用领域的扩展,在一些要求苛刻的领域如航空航天、军工、石油勘探、核工业和通讯等,由于其超大功率、高温高频以及强辐射的环境条件,传统的硅(Si)和砷化镓(GaAs)半导体材料出于自身结构和特性等原因,越来越显得“力不从心”。相比于传统的半导体材料,4H碳化硅(4H-SiC)具有以下几个优势:(1)化学性质稳定,可以通过热氧化生成优质的绝缘层;(2)电子饱和速度高,使得4H-SiC器件的导通损耗相当低;(3)热导率是Si的3倍,临界击穿电场是Si的10倍,不仅提高了器件的散热特性,而且使得4H-SiC器件的耐压容量、工作频率和电流密度都得到了较大提高。更为重要的是,在第三代宽禁带半导体材料中,4H-SiC是唯一能通过热氧化生长SiO2绝缘层的半导体材料,且形成的SiO2质量和在Si上形成的SiO2无任何差别,质地紧密且缺陷少,因而能和当今主流的Si工艺线相兼容。这些特性使4H-SiC材料用于制造诸如MOSFET、IGBT、MCT之类的功率半导体器件来说是Si的理想替代物,而这些功率半导体器件对于应用在高压、高频、高温环境下是非常适合的。目前,困扰基于4H-SiC电压控制型功率半导体器件发展的一个突出问题是器件的反型层迁移率很低、导通电阻很高、开关和导通损耗大。未经任何钝化处理的4H-SiC电压控制型功率半导体器件的迁移率低于10cm2/Vs,不到4H-SiC体迁移率的1%。目前绝大多数观点认为这是由于在4H-SiC电压控制型功率半导体器件的SiC/SiO2界面存在很高的缺陷密度造成的,在器件工作过程中,缺陷捕获了大量的自由载流子,降低了器件的电流密度,并且,这些被捕获的载流子作为库仑散射中心,进一步阻碍沟道载流子的运动,降低了器件的反型层迁移率,增加了器件的开关损耗。因而在4H-SiC电压控制型功率半导体器件的研究过程中,大量的努力和不同的实验方法被开发用来降低SiC/SiO2界面态密度,以期取得好的开关特性。在由SaritDhar等人于2010年在IEEETransactionsonElectronDevices上第57卷发表的《AStudyonPre-OxidationNitrogenImplantationfortheImprovementofChannelMobilityin4H-SiCMOSFETs》文章中,公开了通过在P型4H-SiC衬底上采用氮离子注入减小SiC/SiO2界面态密度、提高4H-SiCMOSFET反型层迁移率、降低损耗的方法,并且指出随着SiC/SiO2界面氮浓度的增加,界面态密度减小,反型层迁移率增加,其不足之处在于,器件的阈值电压不断减小、甚至出现负值的现象,这无法在实际应用中使用,不具备实际使用价值,所以本领域的技术人员根本不会使用该技术生产器件。在由DaiOkamoto等人于2014年在IEEETransactionsonElectronDevices上第35卷发表的《ImprovedChannelMobilityin4H-SiCMOSFETsbyBoronPassivation》(用硼钝化提高4H-SiCMOSFETs反型层迁移率)文章中,公开了先使用干氧氧化技术生成氧化层,然后在P型衬底上通过硼钝化工艺减小SiC/SiO2界面态密度、提高4H-SiCMOSFET迁移率的方法,其不足之处在于,整个氧化层为掺硼的SiO2,降低了SiO2的稳定性,增加了器件的泄漏电流,导致器件的损耗增加,因而不利于器件的实际应用。中国发明专利,公开号:CN105206513A,公开日:2015.12.30,公开了用氮和硼改善4H-SiCMOSFET反型层迁移率的方法,属于微电子
技术领域:
。步骤如下:A、采用离子注入工艺将五价元素氮植入到4H-SiC外延层表面;B、采用湿氧氧化工艺形成栅氧化层;C、采用扩散工艺将三价元素硼植入到外延层与氧化层的界面;扩散工艺的温度为950℃,时间为1.5-2.5小时,确保硼掺杂剂在热动力的驱使下能穿透栅氧化层到达4H-SiC/SiO2界面;硼扩散工艺后,在惰性气体的保护下退火。其不足之处在于,该专利是将整个栅氧化层都掺了高浓度的硼,而硼在一定程度上能改变氧化层的性质,降低氧化层的质量,增加器件的泄漏电流,增加器件阈值电压的不稳定性,这会阻碍该方法的推广使用;另外,在4H-SiC外延层表面注入氮,会降低器件的阈值电压,并有可能形成负值,根本无法使用,尽管通过氧化层来扩散硼抵消注入氮对阈值电压的影响,但是该扩散温度比较低,而且硼在4H-SiC中的扩散系数没有铝的高,因而此种方法形成的硼在4H-SiC外延层中的深度很小,不足5nm,浓度也非常低,不足1×1014cm-3,对抵消因氮注入而降低阈值电压的不利影响的效果微乎其微。技术实现要素::1.要解决的技术问题针对现有技术中4H-SiC电压控制型功率半导体器件的反型层迁移率低、开关损耗大的问题,提出一种低功耗4H-SiC电压控制型功率半导体器件。该方法不但能够大幅提高4H-SiC电压控制型功率半导体器件反型层的迁移率、降低4H-SiC电压控制型功率半导体器件开关损耗和导通损耗,而且能够使4H-SiC电压控制型功率半导体器件的阈值电压也控制在合适的范围之内。2.技术方案一种低功耗4H-SiC电压控制型功率半导体器件,包括外延层与氧化层,在外延层表面有五价元素氮的注入层和三价元素的扩散层。优选地,氮注入层的厚度为18-20nm。优选地,三价元素为铝,铝在外延层中的扩散深度为10-20nm,即三价元素所形成的扩散层的深度为10-20nm。优选地,三价元素铝在外延层(12)中的浓度呈高斯分布,峰值浓度范围为2×1017-1×1018cm-3。一种低功耗4H-SiC电压控制型功率半导体器件的制备方法,其主要步骤如下:A、采用高温扩散工艺将三价元素植入到4H-SiC外延层表面,形成扩散层;B、利用干法刻蚀工艺减薄高温扩散工艺所生长的氧化层;C、利用减薄后的氧化层作为掩蔽层,采用离子注入工艺将五价元素氮植入到外延层与氧化层的界面,形成氮注入层;D、利用干氧氧化工艺将氧化层生长至所需要的厚度;E、在4H-SiC晶片上镀上金属层,并采用剥离工艺形成金属电极,随后用快速退火的方法形成性能良好的欧姆接触。优选地,步骤A是区别于常规扩散工艺的高温扩散,扩散温度在1500℃~1800℃之间,以此来保证铝在4H-SiC外延层中的分布深度为10-20nm,温度越高,扩散时间越短,扩散效果越好。优选地,高温扩散后的铝原子在外延层中的浓度呈高斯分布,峰值浓度范围为2×1017-1×1018cm-3,同时生长的氧化层为掺铝的SiO2。优选地,步骤B中的减薄工艺采用等离子体干法刻蚀技术,精确控制刻蚀后的氧化层厚度为18-20nm。优选地,步骤A中的三价元素为铝或硼。优选地,高温扩散后的铝原子在4H-SiC外延层中的形状呈高斯分布,峰值浓度范围为2×1017-1×1018cm-3。优选地,步骤B中等离子体刻蚀气体采用CHF3+CF4的组合气体,步骤C中经激活的氮在4H-SiC外延层表面的浓度为3×1018-1×1019cm-3,深度范围为18-20nm。优选地,步骤D中的干氧氧化的温度范围为1100℃-1250℃,氧化时间范围1.5-2小时,生长的氧化层的厚度为30nm。优选地,铝掺杂剂由氮化铝和三氧化二铝按照1:1的重量比例组成.优选地,铝离子注入后,在惰性气体的保护下、1550℃的温度进行退火。优选地,步骤C中的离子注入后和步骤D中的干氧氧化后需进行退火处理,采用的保护气体为氩气。3.有益效果相比现有技术,本发明具有如下优点:1)采用高温扩散工艺,一方面能将铝原子植入到4H-SiC外延层表面内,同时也生长掺了铝的SiO2。铝是SiO2的网络形成体和修饰体,能减轻SiC/SiO2的界面应力,降低SiC/SiO2的界面态密度;另一方面,对于n沟道4H-SiC电压控制型功率半导体器件的P型外延层而言,植入的铝是正掺杂,能提高n沟道器件的阈值电压;2)起反掺杂作用的氮,会减小n沟道增强型4H-SiC电压控制型功率半导体器件的阈值电压,这不利于器件的应用,引入的三价元素铝,能抵消由于引入的五价元素氮对4H-SiC电压控制型功率半导体器件阈值电压的影响,4H-SiC电压控制型功率半导体器件的阈值电压会控制在合适的范围之内,因而4H-SiC电压控制型功率半导体器件能正常工作;对于p型沟道器件而言,铝是反掺杂,降低器件的阈值电压,而注入的氮是正掺杂、提高器件的阈值电压,因而两者的作用互相抵消,能稳定p沟道器件的阈值电压;3)铝作为SiO2的网络形成体,比现有技术采用的硼,铝掺杂的SiO2的稳定性更好,降低SiC/SiO2的界面态密度的效果也更好;并且铝在SiC中的扩散系数比硼的系数高,尤其是在超过1500℃的高温下,效果更为明显,在要求相同的掺杂浓度和扩散结深的情况下,用铝代替硼能缩短扩散时间、节省能源、提高生产效率、降低高温对设备的损害;在本专利的扩散工艺中,采用三价元素铝,与三价元素硼相比,由于铝的高温扩散系数比硼的高,形成本专利外延层的三价元素扩散层,硼扩散需要3-5小时,而铝扩散时间需要2-4小时,因而用铝作为三价元素的扩散剂,缩短器件生产周期的同时,生产效率提高了20%,能耗降低了20%,节约成本;本专利是直接在4H-SiC外延层表面采用超过1500℃的温度来扩散铝,扩散深度和浓度都比硼的高,效果比公开号为CN105206513A专利要好得多;4)采用超过1500℃的高温扩散,能起到将铝植入到4H-SiC外延层和生长氧化层的双重目的,同时该氧化层也作为后续氮离子注入工艺的掩蔽层,因而减少了工艺步骤和工艺设备;5)本发明采用先铝扩散后氮离子注入工艺,并采用等离子体刻蚀工艺减薄氧化层,这样既能提高器件的反型层迁移率,又能稳定、甚至提高器件的阈值电压;同时,采用等离子体刻蚀能精确控制减薄后的氧化层厚度,比传统的湿法腐蚀而言,精度更高、表面粗糙度更低,有利于后续离子注入的氮在4H-SiC/SiO2界面均匀分布;6)本发明所设计的4H-SiC电压控制型功率半导体器件的氧化层,只是部分厚度的SiO2掺了铝,尽管铝在一定程度上影响了SiO2的稳定性,但是后续干氧氧化生长的SiO2厚度占整个氧化层厚度的五分之三,并且该氧化层经退火处理,质地致密、质量良好,大大降低氧化层的泄漏电流和不稳定性;7)本发明采用先扩散铝后离子注入氮制备的4H-SiC电压控制型功率半导体器件,在功耗方面降低了60-78%,阈值电压能稳定在2V以上,特别适合高频、高温、高功率的应用场合;8)现有技术中氧化层是一次性生长而成,本发明为降低器件的功耗,先生长出一定厚的氧化层,然后通过干法刻蚀工艺进行减薄。传统的氧化层减薄和去除工艺是湿法腐蚀,干法刻蚀工艺一般是用于微细加工,用于更精确的图形转移,一般不用于功率器件栅氧层这种大面积的图形减薄,但是本发明中采用干法刻蚀,可以精确控制减薄的氧化层厚度,也不会像湿法腐蚀对栅氧层的侧墙形成钻蚀,保证栅氧层的完整性,并且形成更为平整的表面,为后续电极制备形成更好的条件,而且也不会增加工艺成本;9)本发明对基于4H-SiC材料的MOSFET、IGBT、MCT这类带有绝缘栅的电压控制型功率半导体器件及其派生器件皆适用,P型或N型也都适用,对于上述不同类型的器件,仅仅是因为器件的结构和类型不同,所以后面具体实施例的工艺步骤不同,但是在提高迁移率、稳定阈值电压、降低功耗方面的工艺方法及其特征是相同的。附图说明图1为低功耗4H-SiCMOSFET或者4H-SiCIGBT的结构示意图;图2为低功耗4H-SiCMCT的结构示意图;图3为本发明的制备方法流程图。图中标号名称:11、氧化层;12、外延层;13、缓冲层;14、4H-SiC衬底;23、P阱或N阱;21、电极接触区域;22、体接触区域;24、P阱或N阱;31、电极1;32、栅极电极;33、电极2;41、体接触区域。具体实施方式下面结合说明书附图和具体的实施例,对本发明作详细描述。结合图1,一种低功耗4H-SiC电压控制型功率半导体器件,包括外延层12与氧化层11,外延层12表面下有氮注入层和三价元素的扩散层,氮注入层的厚度为18-20nm,在具体应用时,可以取值为18cm、19cm、20cm;三价元素为铝,三价元素铝在外延层12中的扩散深度为10-20nm,在具体应用时,可以取值为10cm、15cm、20cm;三价元素铝在外延层12中的浓度呈高斯分布,峰值浓度范围为2×1017-1×1018cm-3。在具体应用时,三价元素铝在外延层12中的峰值浓度分别可以取值为2×1017cm-3,5×1017cm-3和1×1018cm-3,都能获得低功耗4H-SiC电压控制型功率半导体器件。一种低功耗4H-SiC电压控制型功率半导体器件的制备方法中,扩散温度在1500℃~1800℃范围内,在具体应用时,可以取值为1500℃、1800℃、1700℃;氧化层11的厚度为18-20nm;在具体应用时,可以取值为18nm,20nm,19nm。以上数值范围的取值,在实施例1-3中均适用,且能够取得本发明所描述的技术效果。实施例1结合图1和图3,对于电压控制型功率半导体器件,一种低功耗n沟道4H-SiCMOSFET的制备方法,其步骤如下:A、选择N型4H-SiC外延片,由掺杂浓度分布为5×1015cm-3的N型衬底14、6×1017cm-3的N+缓冲层13、1×1016cm-3的N型外延层12组成。采用离子注入工艺在4H-SiC外延层上形成P阱23、漏极31(电极1)的N+接触区域21、P+体接触区域22;离子注入工艺是在4H-SiC外延层12表面进行的室温下多能量注入;B、采用高温扩散工艺将三价元素铝植入到4H-SiC外延层12表面;之所以不选择同样为三价元素的硼,因为高温下铝比硼更活跃,在4H-SiC中的扩散系数更大,这样铝在4H-SiC中的浓度更高,分布也更深,并且形成铝掺杂的SiO2在稳定性、网络粘结性等方面比硼掺杂的SiO2更好;稳定性好意味着器件的泄露电流小、阈值电压的漂移也小,因而器件的静态特性好;网络粘结性好,意味着减小界面态密度的效果更好,器件的导通电阻和开关损耗都能降低;高温扩散温度为1500℃,高温扩散后的铝原子在外延层12中的浓度呈高斯分布,峰值浓度范围为2×1017cm-3,深度范围为15nm;C、利用干法刻蚀工艺,在等离子体刻蚀系统中,使用氩气作为载气,采用CF4+CHF3混合气体作为刻蚀气体,其中氩气的流量占总流量的50%,调节气压为5Pa,射频功率为500W,反应室温度为45℃,基片冷却温度为5℃,通过膜厚监测系统,将高温扩散阶段生长的氧化层减薄至20nm。D、减薄后的4H-SiC晶片在退火炉中利用氩气保护、1150℃退火温度下、时间30分钟的退火,目的是固化SiO2的网络特性,进一步减小SiC/SiO2的界面态密度,并为后续的氮离子注入形成质量良好的掩蔽层。E、采用离子注入工艺将五价元素氮植入到4H-SiC外延层12表面;之所以不选择同样为五价元素的磷,因为在后续的氧化工艺过程中,磷会进入到SiO2中,变成磷硅玻璃(PSG),这是一种极性材料,增加了器件的栅极泄漏电流,并导致器件的阈值电压出现不稳定现象;离子注入工艺是在4H-SiC外延层12表面进行的550℃条件下的多能量注入。F、选择惰性气体为高温下化学性质更为稳定的氩气作为保护气体,在1550℃高温下对注入的氮进行激活;高温激活后的氮离子在4H-SiC外延层12中的分布,经过二次离子质谱仪(SIMS)测量,形状呈高斯分布,峰值浓度范围为3×1018-1×1019cm-3,在实际应用时,可以取值为3×1018cm-3,1×1019cm-3,8×1018cm-3,深度范围为10-20nm,在实际应用时,可以取值为10nm,20nm,18nm;离子注入氮,一方面,能钝化4H-SiC外延层12与氧化层11界面的悬挂键、减小界面态密度;另一方面,对于n沟道4H-SiC的P阱是反掺杂,能使器件工作时形成的反型层远离SiC/SiO2界面,降低由于SiC/SiO2粗糙界面对迁移率的影响,提高反型层的迁移率。但起反掺杂作用的氮,会减小n沟道增强型4H-SiC的阈值电压,这不利于器件的应用。G、采用干氧氧化工艺继续生长氧化层11;干氧氧化的温度范围为1100-1200℃,在实际应用时,可以取值为,1100℃,1200℃,1500℃,氧化时间范围为1.5-2小时,生长后的整个氧化层11的厚度经过椭偏仪测量,其范围为46-50nm,在实际应用时,可以取值为,46nm,50nm,48nm,以满足制造4H-SiC的工艺标准。尽管干氧氧化温度比湿氧氧化温度高,有可能对已经注入的氮产生不利影响,但是干氧氧化工艺是在氮离子激活之后进行,之前的1550℃高温已经将氮激活,并且此时有厚度为20nm的氧化层11作为保护层,1200℃的干氧氧化温度不会促使注入的氮逃逸出4H-SiC的表面。而且干氧氧化生长的氧化层致密,生长过程中引入的不利于4H-SiC特性的各种电荷的密度也比湿氧氧化条件下的少,更有利于提高4H-SiC的稳定性,降低4H-SiCMOSFET的导通损耗和开关损耗。H、4H-SiC在干氧氧化后,在退火炉中利用氩气作为保护气体、温度为1150℃的条件下退火30分钟,进一步固化干氧氧化生长的氧化层,消除生长过程中引入的各种有害电荷。I、利用蒸发工艺在掩膜版的保护下在4H-SiC晶片上镀上金属层,并采用剥离工艺形成金属电极,即图1中的漏极31(电极1)、栅极电极32和集电极33(电极2),随后在退火炉中利用氩气作为保护气体、1180℃、时间为5分钟的快速退火,形成性能良好的欧姆接触。本发明采用先扩散铝后氮离子注入,并采用干法刻蚀工艺减薄氧化层,这样既能提高反型层迁移率、降低4H-SiCMOSFET的导通和开关损耗,又能稳定甚至提高4H-SiCMOSFET的阈值电压;同时,利用减薄后的氧化层作为掩蔽层进行氮离子注入,最后采用干氧氧化工艺继续生长氧化层11,这样能减少工艺环节,减少工艺设备的投资,降低生产成本,而生长氧化层过程中所带来的有害电荷也大为减少。实施例2结合图1和图3,对于电压控制型功率半导体器件,一种p沟道低功耗4H-SiCIGBT的制备方法,其步骤如下:1)选择N型衬底的P型外延片,由掺杂浓度分布为5×1017cm-3的N+型衬底14、3×1018cm-3的P+缓冲层13、1×1016cm-3的P型外延层12组成外;2)在4H-SiC外延层12上采用离子注入工艺注入硼离子形成N阱23、N+体接触区域22,采用离子注入工艺注入氮形成发射极(电极1)P+接触区域21;a、其中N阱23是采用三次室温下的离子注入工艺,注入硼离子剂量的范围为1×1010~1×1014cm-2;发射极P+接触区域21的注入能量在10keV到50keV之间;b、离子注入后,在氩气保护、外延层12表面覆盖碳膜的真空条件下退火,退火温度为1500℃、时间30分钟左右,充分保证注入的硼和氮离子激活并且没有挥发逃逸。3)铝的高温扩散;铝的高温扩散是低功耗4H-SiC的关键工艺,一方面要保证铝在4H-SiC外延层12中有一定的深度分布,另外一方面要生长掺铝的氧化层11。扩散温度和时间都会影响铝在4H-SiC外延层和氧化层中的分布。1500℃~1800℃的高温下,铝的活跃性大大增加,在4H-SiC中的扩散系数比传统的硼要高。高温扩散温度为1800℃,高温扩散后的铝原子在外延层12中的浓度呈高斯分布,峰值浓度范围为1×1018cm-3,深度范围为20nm;根据反应式:2Al2O3+3Si=4Al+3SiO2,铝的扩散剂Al2O3与4H-SiC中的Si原子反应后,置换出的Al原子一部分进入4H-SiC的外延层12,一部分进入扩散过程中生长的SiO2。铝是SiO2的网络形成体和网络修正体,改善了SiC/SiO2的界面特性,降低了SiC/SiO2的界面态密度。4)氧化层减薄工艺;经过高温扩散后生长的氧化层11的厚度在200nm左右,不利于后续氮离子注入,但是又不能全部将氧化层11去除掉,此时铝已经改善了SiC/SiO2的界面特性,需要保留部分厚度的氧化层,维持掺铝的氧化层降低界面态密度的效果。如果采用减薄工艺保留氧化层11的厚度至18nm,既能达到上述目的,同时可以作为接下来的氮离子注入工艺所需要的掩蔽层。在等离子体刻蚀机中,采用CHF3+CF4(20sccm+20sccm)作为刻蚀气体,射频功率设定为450W,气压为5Pa,利用膜厚监测系统将减薄后的氧化层11的厚度控制在18nm。减薄后的4H-SiC晶片进入退火炉中,在氩气的保护下、1160℃的温度下进行退火30分钟。5)氮离子注入;a、采用三次550℃下的离子注入工艺,注入氮离子剂量的范围为1×1010~1×1014cm-2;b、离子注入后,在氩气保护、晶片表面覆盖碳膜的真空条件下退火,退火温度为1500℃、时间30分钟左右,充分保证注入的氮离子激活并且没有挥发逃逸;确保经过高温激活后,氮在外延层12中的分布呈高斯形状,峰值浓度为1×1019cm-3;注入能量为10keV到50keV之间,经SIMS测得氮在外延层12中的深度为20nm。6)干氧氧化;将高温激活氮后的4H-SiC晶片转移到氧化炉中,在1180℃的条件下,将整个氧化层11的厚度生长至52nm。7)退火;在干氧氧化后,在退火炉中利用氩气作为保护气体、温度为1120℃的条件下退火35分钟,进一步固化干氧氧化生长的氧化层,消除生长过程中引入的各种有害电荷。8)欧姆电极的制备利用磁控溅射工艺在掩膜版的保护下在4H-SiC晶片上镀上金属层,形成图1中的发射极31(电极1)、栅极电极32和集电极33(电极2),随后在退火炉中利用氩气作为保护气体、1160℃、时间为6分钟的快速退火,形成性能良好的欧姆接触。本发明采用铝在N阱上实现反掺杂,降低器件的阈值电压,但是随后注入的氮能抵消引入的铝降低4H-SiCIGBT阈值电压的负面作用;同时,引入的铝和氮,都能降低4H-SiC/SiO2的界面态密度,因而4H-SiCIGBT的导通损耗和开关损耗降低65%,阈值电压为-2.6V。实施例3结合图2和图3,对于电压控制型功率半导体器件,一种低功耗n沟道4H-SiCMCT的制备方法,其步骤如下:1)选择衬底;选用硼掺杂的P型4H-SiC的衬底14,掺杂浓度为9.6×1018cm-3,厚度为10μm,这有利于降低半导体-金属之间的势垒,形成良好的欧姆接触电极—漏极;上面是厚度为3μm的N+型的外延层13,掺杂浓度为1.3×1018cm-3,这个浓度有利于降低器件的导通电阻;在N+外延层13上是N-漂移层12,厚度为165μm,掺杂浓度为3.5×1014cm-3,该漂移层和后续的注入铝形成P阱浓度相配合,设置合适的器件的阈值电压。2)利用自对准掩膜工艺,在外延层12上采用高能铝离子注入,形成深P阱23,形成P型半导体,注入能量为420keV,剂量为2.4×1016cm-2。随后在氩气的保护下进行1600℃、30分钟退火,激活注入的铝离子。3)氮离子注入形成深N阱24,注入顺序的能量和剂量见表1,注入后在氩气的保护下进行1520℃、30分钟退火,激活注入的氮离子。表1氮离子注入顺序的能量和剂量注入顺序能量(keV)剂量(cm-2)1138.34×10152241.23×10163442.56×10164)硼离子注入形成两个P+体接触区域41,注入顺序的能量和剂量见表2,注入后4H-SiC衬底在氩气的保护下进行1520℃、30分钟退火,激活注入的硼离子。表2硼离子注入顺序的能量和剂量注入顺序能量(keV)剂量(cm-2)1161.43×10142221.51×10143382.84×10144472.67×10145)铝扩散与氧化层减薄在无水乙醇均匀配置AlN+Al2O3溶液,采用甩胶的方式均匀地将溶液涂在4H-SiC晶片表面,随后进入烘箱中烘干,烘干后置于高温扩散炉中,将炉温设置为1650℃,扩散时间定为2.5小时。在铝扩散的过程中,4H-SiC晶片表面会生长出厚度为186nm的氧化层,利用等离子体干法刻蚀的方法将该氧化层厚度减至20nm,高温扩散后的铝原子在外延层12中的浓度呈高斯分布,峰值浓度范围为3.5×1017cm-3,随后将晶片在退火炉中、1160℃的温度下退火35分钟。6)起钝化和反掺杂作用的氮离子注入利用减薄后的氧化层作为掩蔽层,采用自对准工艺在外延层12表面的沟道区域进行加温至550℃下的氮离子注入,注入顺序的能量和剂量见表3,注入后在氩气的保护下进行1560℃、30分钟退火,激活注入的氮离子;高温激活后的氮离子在4H-SiC外延层12中的分布,经过二次离子质谱仪(SIMS)测量,形状呈高斯分布,峰值浓度为5.6×1018cm-3,深度为18nm。表3氮离子注入顺序的能量和剂量注入顺序能量(keV)剂量(cm-2)198.42×10102133.23×10123251.18×10147)干氧氧化继续生长氧化层11,氧化炉中心温度设定为1170℃,氧化时间2.0小时,生长的氧化层11的厚度经SIMS测量为52nm。8)在衬底14背部依次蒸发100nm/45nm厚的Ti/Ni作为集电极33(电极2),在顶部利用金属蒸发的工艺镀上100nm/45nm厚的Ti/Ni,并采用剥离工艺形成发射极31(电极1)和栅极电极32。9)在退火炉中并在氩气保护条件下进行980℃、5分钟快速退火形成上述三个电极的半导体-金属之间的欧姆接触,以便不产生明显的附加阻抗,有利于降低器件的。本实施例采用铝扩散、干法刻蚀、氮离子注入、干氧氧化等工艺,制备得到的4H-SiCMCT的迁移率达到了223cm2/Vs,导通损耗和关断损耗降低70%,阈值电压为2.3V。本实施例在降低生产成本、提高生产效率的同时,器件的关键参数得到进一步提高,因此,本发明的方法更适合器件的实际应用。以上示意性地对本发明创造及其实施方式进行了描述,该描述没有限制性,附图中所示的也只是本发明创造的实施方式之一,实际的结构并不局限于此。所以,如果本领域的普通技术人员受其启示,在不脱离本创造宗旨的情况下,不经创造性的设计出与该技术方案相似的结构方式及实施例,均应属于本专利的保护范围。当前第1页1 2 3