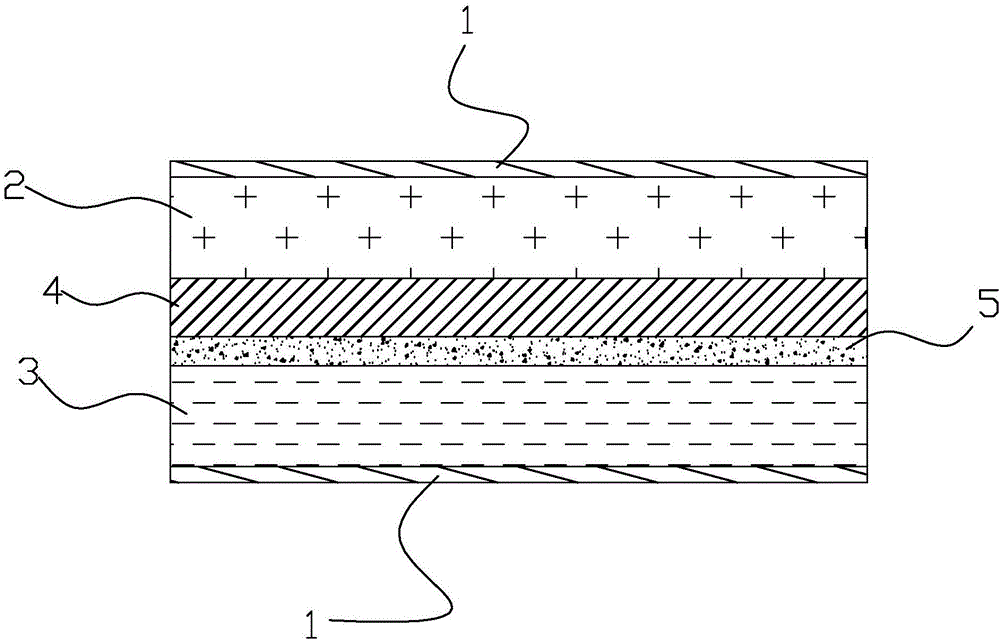
本发明涉及锂电池制备
技术领域:
,特别涉及一种可快速检测安全性的锂电池。
背景技术:
:锂离子二次电池因其比容量高、工作电压高、工作温度范围宽、自放电率低、循环寿命长、无污染、重量轻等优点,因而应用领域广泛。锂离子二次电池通常包括正极、负极、电解液、隔离膜以及外包装。其中,所述正极通常包括正极集流体和附着在其上的正极材料组成;所述负极通常包括负极集流体和附着在其上的负极材料组成;隔离膜在正极与负极之间起到电子阻隔作用防止正极与负极短路;电解液由正极、负极和隔离膜吸收形成锂离子通路。锂离子二次电池在正常工作时,由正极集流体引出正极端和负极集流体引出的负极端与外电路形成电子通路,电解液和正负极材料中锂离子形成离子通路,电子通路和离子通路共同形成回路,以达到正常工作的目的。锂离子二次电池在制造/使用不当的情况下,例如机械损伤、高温环境等,有可能会正负极直接接触造成短路,电池一旦短路会在短时间内放出大量的热,可能起火甚至爆炸,危害到使用者的安全。为此,锂离子电池公司在电池极片的正极表面,负极表面和隔膜表层涂覆上专用的涂层,如氧化铝涂层,主要作用是增加电池界面上的电子电阻,使电池在正负极短路时减少放出的热量,以改善电池内部短路的风险。然而随着锂离子二次电池的需求量逐渐增大,制造的速度加快,生产的数量日益庞大,在锂电池制作的过程中很容易发生保护涂层没有完全涂覆、涂布不均匀、已经涂覆有保护涂层的隔膜打皱或破孔等现象,因此如何检测出正极片/负极片/隔膜上面的保护涂层是否涂覆完整、涂覆有保护涂层的隔膜是否发生打皱或破孔现象,有效避免批量性的短路风险,确保锂电池的安全性,成为了一个重要的研究课题。技术实现要素:本发明针对现有技术存在之缺失,提供一种可快速检测安全性的锂电池,其能快速检测出正极片/负极片/隔膜上面的保护涂层是否涂覆完整、涂覆有保护涂层的隔膜是否发生打皱或破孔现象,有效避免造成批量锂电池内部短路的风险,确保锂电池的安全,减少不必要的损失。为实现上述目的,本发明采用如下之技术方案:一种可快速检测安全性的锂电池,包括电池外壳以及设于电池外壳内的正极极片、负极极片和隔膜,所述正极极片和负极极片设于隔膜的两侧,所述正极极片/负极极片/隔膜的表面涂覆有指示保护涂层,所述指示保护涂层内含有具有射线吸收能力的指示物质。作为一种优选方案,所述指示保护涂层涂覆于正极极片朝向隔膜的一面。作为一种优选方案,所述指示保护涂层涂覆于负极极片朝向隔膜的一面。作为一种优选方案,所述射线为X-ray、γ射线或β射线。作为一种优选方案,所述指示物质的射线吸收能力大于锂电池中其他组成部分的射线吸收能力。作为一种优选方案,所述指示物质的射线吸收能力为锂电池中其他组成部分的射线吸收能力的两倍。作为一种优选方案,所述指示物质为原子序数大于30的金属及其金属化合物中的一种或数种。作为一种优选方案,所述指示物质优选为锌、锆、钼、锡、锑、钡、铅、钨、铈、钕或镧金属及其金属化合物中的一种或几种。作为一种优选方案,所述指示物质特别优选为钡、钨、铈、钕或镧金属及其金属化合物中的一种或几种。作为一种优选方案,所述指示保护涂层的厚度为5μm。本发明与现有技术相比,具有以下优点和优势,具体而言,在正极极片/负极极片/隔膜表面涂覆添加具有比电池其他组分具有更高的射线吸收系数的指示物质的保护涂层,并调整其中指示物质的质量比例使其能在射线成像仪中成像,这样就快速检测出正极片/负极片/隔膜表面的保护涂层是否涂覆完整、涂覆有保护涂层的隔膜是否发生打皱或破孔现象,有效避免造成批量锂电池内部短路的风险,确保锂电池的安全,减少不必要的损失。为更清楚地阐述本发明的结构特征、技术手段及其所达到的具体目的和功能,下面结合附图与具体实施例来对本发明作进一步详细说明:附图说明图1是本发明之锂电池的一种内部结构示意图;图2是本发明之锂电池的另一种内部结构示意图;图3是本发明之锂电池的又一种内部结构示意图。附图标识说明:1-电池外壳,2-正极极片,3-负极极片,4-隔膜,5-指示保护涂层。具体实施方式如图1-3所示,一种可快速检测安全性的锂电池,包括电池外壳1以及设于电池外壳1内的正极极片2、负极极片3和隔膜4,所述正极极片2和负极极片3设于隔膜的两侧,所述正极极片2/负极极片3/隔膜4的表面涂覆有指示保护涂层5,所述指示保护涂层5内含有具有射线吸收能力的指示物质。所述射线为X-ray、γ射线或β射线。所述指示物质的射线吸收能力大于锂电池中其他组成部分的射线吸收能力,所述指示物质优选的射线吸收能力为锂电池中其他组成部分的射线吸收能力的两倍。所述指示物质为原子序数大于30的金属及其金属化合物中的一种或数种,如锌、锆、钼、锡、锑、钡、铅、钨、铈、钕、镧等,优选为钡、钨、铈、钕、镧。所述指示保护涂层5的涂覆厚度为5μm。所述指示保护涂层5包括无机填料、粘接剂、指示物质和水。所述无机填料的质量比为15-35%,所述粘接剂的质量比为1-5%,所述指示物质的质量比为15-35%,所述水的质量比为40-60%。所述无机填料为氧化铝、氢氧化铝、氮化铝、氧化镁、氢氧化镁、氧化硅、氧化钛和氧化钛中的一种或几种。所述粘接剂为聚聚偏二氟乙烯、聚四氟乙烯、偏二氟乙烯-六氟丙烯共聚物、聚酰胺酰亚胺、聚丙烯腈、聚丙烯酸和丁苯橡胶中的一种或几种。需要说明的是所述指示保护涂层5涂覆于正极极片2朝向隔膜4的一侧,所述指示保护涂层5涂覆于负极极片3朝向隔膜4的一侧,所述隔膜4既可为单面涂覆,也可为双面涂覆。实施例1:负极制作:按质量比取,将93份人造石墨、2份碳黑、2份粘接羧甲基纤维素、3份丁苯橡胶和100份水混合均匀,得到待涂覆的负极涂料,然后将负极涂料涂覆于厚度为9μm的铜箔上,经烘干、冷压后得到每平方厘米含有1.75克负极活性物质的负极膜卷,然后按一定尺寸对负极膜卷进行分切,得到负极极片;保护涂料配置:按质量比取,将50份氧化铝、5份聚丙烯腈、45份钛酸钡和100份水混合均匀,得到指示保护涂料;涂覆:将上述步骤得到的指示保护涂料涂覆在负极极片上,涂覆厚度约为5微米,并于负极极片的长度方向上留空约20mm2的区域,作为检测区域;所述指示保护涂料为单面涂覆于负极极片上;正极制作:按质量比取,将95份钴酸锂、2份碳黑、3份聚偏二氟乙烯和80份N-甲基吡咯烷酮混合均匀,得到待涂覆的正极涂料,然后将正极涂料涂覆于正极用铝箔集流体上,经烘干、冷压后得到每平方厘米含有4克正极活性物质的正极膜卷,然后按一定尺寸对正极膜卷进行分切,得到正极极片;电解液配置:将碳酸二乙酯、碳酸二甲酯和碳酸乙烯酯按照体积比例为2:2:5混合均匀后,再与六氟磷酸锂混合均匀,得到浓度为1mol/L的电解液;隔膜制作:将厚度为14μm的聚乙烯按照一定尺寸分切,得到隔膜;电池装配:将上述步骤得到的负极极片、正极极片和隔膜卷绕成涡卷状的电芯,然后与5克上述步骤得到的电解液一同密封到电池外壳中,经封口后制得锂电池。对比例1:负极制作:按照实施例1所描述的方法制作负极极片;保护涂料配置:按质量比取,将95份氧化铝、5份聚丙烯腈和100份水混合均匀,得到保护涂料;涂覆:按照实施例1所描述的方法将保护涂料涂覆在负极极片上;正极制作:按照实施例1所描述的方法制作正极极片;电解液配置:按照实施例1所描述的方法配置电解液;隔膜制作:按照实施例1所描述的方法制作隔膜;电池装配:按照实施例1所描述的方法装配制得锂电池。实施例2:负极制作:按质量比取,将93份人造石墨、2份碳黑、2份粘接羧甲基纤维素、3份丁苯橡胶和100份水混合均匀,得到待涂覆的负极涂料,然后将负极涂料涂覆于厚度为9μm的铜箔上,经烘干、冷压后得到每平方厘米含有1.75克负极活性物质的负极膜卷,然后按一定尺寸对负极膜卷进行分切,得到负极极片;正极制作:按质量比取,将95份钴酸锂、2份碳黑、3份聚偏二氟乙烯和80份N-甲基吡咯烷酮混合均匀,得到待涂覆的正极涂料,然后将正极涂料涂覆于正极用铝箔集流体上,经烘干、冷压后得到每平方厘米含有4克正极活性物质的正极膜卷,然后按一定尺寸对正极膜卷进行分切,得到正极极片;保护涂料配置:按质量比取,将50份氧化铝、5份聚丙烯腈、45份钛酸钡和100份水混合均匀,得到指示保护涂料;涂覆:将上述步骤得到的指示保护涂料涂覆在正极极片上,涂覆厚度约为5微米,并于正极极片的长度方向上留空约20mm2的区域,作为检测区域;电解液配置:将碳酸二乙酯、碳酸二甲酯和碳酸乙烯酯按照体积比例为2:2:5混合均匀后,再与六氟磷酸锂混合均匀,得到浓度为1mol/L的电解液;隔膜制作:将厚度为14μm的聚乙烯按照一定尺寸分切,得到隔膜;电池装配:将上述步骤得到的负极极片、正极极片和隔膜卷绕成涡卷状的电芯,然后与5克上述步骤得到的电解液一同密封到电池外壳中,经封口后制得锂电池。对比例2:负极制作:按照实施例2所描述的方法制作负极极片;正极制作:按照实施例2所描述的方法制作正极极片;保护涂料配置:按质量比取,将95份氧化铝、5份聚丙烯腈和100份水混合均匀,得到保护涂料;涂覆:按照实施例2所描述的方法将保护涂料涂覆在正极极片上;电解液配置:按照实施例2所描述的方法配置电解液;隔膜制作:按照实施例2所描述的方法制作隔膜;电池装配:按照实施例2所描述的方法装配制得锂电池。实施例3:负极制作:按质量比取,将93份人造石墨、2份碳黑、2份粘接羧甲基纤维素、3份丁苯橡胶和100份水混合均匀,得到待涂覆的负极涂料,然后将负极涂料涂覆于厚度为9μm的铜箔上,经烘干、冷压后得到每平方厘米含有1.75克负极活性物质的负极膜卷,然后按一定尺寸对负极膜卷进行分切,得到负极极片;正极制作:按质量比取,将95份钴酸锂、2份碳黑、3份聚偏二氟乙烯和80份N-甲基吡咯烷酮混合均匀,得到待涂覆的正极涂料,然后将正极涂料涂覆于正极用铝箔集流体上,经烘干、冷压后得到每平方厘米含有4克正极活性物质的正极膜卷,然后按一定尺寸对正极膜卷进行分切,得到正极极片;电解液配置:将碳酸二乙酯、碳酸二甲酯和碳酸乙烯酯按照体积比例为2:2:5混合均匀后,再与六氟磷酸锂混合均匀,得到浓度为1mol/L的电解液;隔膜制作:将厚度为14μm的聚乙烯按照一定尺寸分切,得到隔膜;保护涂料配置:按质量比取,将50份氧化铝、5份聚丙烯腈、45份钛酸钡和100份水混合均匀,得到指示保护涂料;涂覆:将上述步骤得到的指示保护涂料涂覆在隔膜上,涂覆厚度约为5微米,并于隔膜上留空约20mm2的区域,作为检测区域;电池装配:将上述步骤得到的负极极片、正极极片和隔膜卷绕成涡卷状的电芯,然后与5克上述步骤得到的电解液一同密封到电池外壳中,经封口后制得锂电池。对比例3:负极制作:按照实施例3所描述的方法制作负极极片;正极制作:按照实施例3所描述的方法制作正极极片;保护涂料配置:按质量比取,将95份氧化铝、5份聚丙烯腈和100份水混合均匀,得到保护涂料;涂覆:按照实施例3所描述的方法将保护涂料涂覆在隔膜上;电解液配置:按照实施例3所描述的方法配置电解液;隔膜制作:按照实施例3所描述的方法制作隔膜;电池装配:按照实施例3所描述的方法装配制得锂电池。以上实施例和对比例中的保护涂料涂覆于正极极片朝向隔膜的一面或负极极片朝向隔膜的一面,而在隔膜上的既可为单面涂覆,也可为双面涂覆。测试:将由上述实施例和对比例中制备得到的锂电池分别放入X光成像仪中进行检测,并观察故意留空的检测区域是否能够被检测出来。测试原理:由于指示物质具有比电池其他组分具有更高的射线吸收系数,只要调整其中指示物质的质量比例,便能使其满足射线成像仪的成像分辨率要求。通过X光成像仪便能立即显示出指示保护涂层是否涂覆完整、是否涂布不均匀,涂覆完整的隔膜是否被打皱或破孔。测试结果:实验漏涂区域是否有显示漏涂区域是否能够清晰分辨大小实施例1有是对比例1无否实施例2有是对比例2无否实施例3有是对比例3无否从上表的测试结果可知,本发明设计的锂电池在制造时故意漏涂的检测区域能有效的被检测出来,这样在锂电池生产的初期便能快速检测出正极片/负极片/隔膜上面的保护涂层是否涂覆完整,检测出涂覆有保护涂层的隔膜是否有打皱或破孔的现象发生,有效避免造成批量锂电池内部短路的风险,确保锂电池的安全,减少不必要的损失。以上所述,仅是本发明的较佳实施例而已,并不用以限制本发明,故凡是依据本发明的技术实际对以上实施例所作的任何修改、等同替换、改进等,均仍属于本发明技术方案的范围内。当前第1页1 2 3