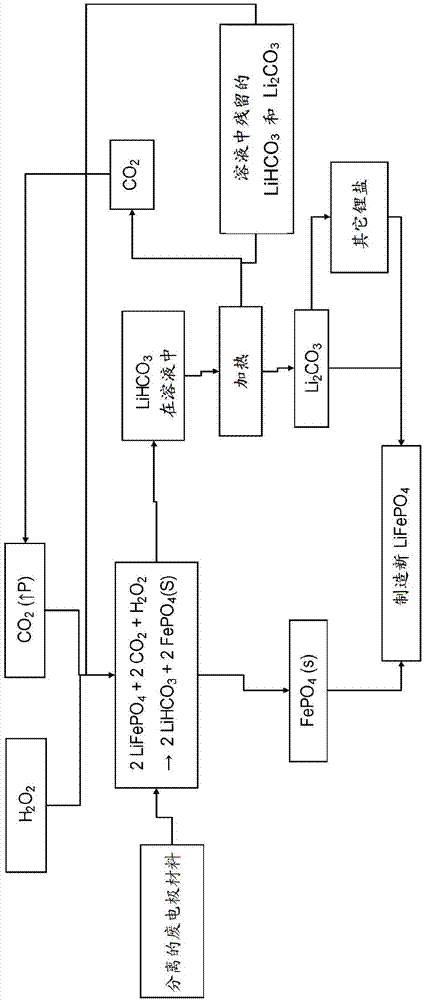
根据适用法律,本申请要求2016年5月20日提交的美国临时申请no.62/339,470的优先权,其内容作为出于所有目的的整体通过引用并入本文。本
技术领域:
一般涉及使锂电池电极材料再循环的方法,更具体地涉及使使用过的锂金属和锂离子电池再循环的方法。背景锂电池广泛用于家用电子或汽车推进等
技术领域:
。然而,在使用寿命结束时处置这些电池在安全和环境方面都是危险的。此外,高材料成本涉及制造锂电池的昂贵工艺。这就是为什么需要开发用于锂电池材料的拆解和再循环的有效方法的原因。通常,放电的电池必须首先经历去活化步骤以最小化与剩余存储能量相关的任何危险。已经使用了数种策略,例如低温方法(costoflithium-ionbatteriesforvehicles,lindagainesandroycuenca,argonnenationallaboratory,september2000)或在惰性气氛下处理。可以通过蒸发回收溶剂或通过其他手段,例如使用临界co2作为溶剂(yuanlongliuetal.,rscadvances,2014,97,54525-54531;和美国专利no.8,067,107)。一旦确定失活,压碎和切碎步骤,然后进行分选和筛分操作,就可以机械分离锂电池的外壳、隔板和电极。通过将粘合剂溶解在适当的溶剂(tongdonggeetal.,journalofchemicalindustryandengineering(china),2005,56,10,4)如n-甲基-2-吡咯烷酮(nmp)中或其在高温下的热分解来实现电极材料和集电箔的分离。目前,有两种主要方法用于回收活性电极材料,也称为电化学活性材料。第一种是基于高温冶金技术,其中电池成分经受非常高的温度以回收元素如钴,镍或锰,并且到目前为止,其中锂和铝不回收(life-cycleanalysisforlithium-ionbatteriesproductionandrecycling,lindagaines,john,90thannualmeetingofthetransportationresearchboard,washingtond.c,january2011)。另一种方法基于湿法冶金技术,主要是酸沥滤(或沥滤),然后是提取和/或沉淀步骤。常规方法中使用的已知沥滤剂是盐酸(p.zhanetal.,hydrometallurgy,47(1998)259-271),硫酸和过氧化氢的混合物(d.p.mantuanoetal.,j.powersources,159(2006)1510-1518),或硝酸和过氧化氢的混合物(c.k.lee,k.i.rhee,hydrometallurgy,68(2003)5-10)。目前提出的湿法冶金技术的主要缺点是使用强酸进行沥滤导致所有活性电极组分(即锂和过渡金属)的非选择性溶解。这意味着需要数个进一步的提取和/或沉淀步骤(s.castilloetal.,journalofpowersources,112(2002)247-254)以回收每种元素。此外,上述强酸必须以高浓度和相对高的温度使用。在盐酸的情况下,释放的氯的处理还涉及更高的操作成本以及额外的环境问题。当将lifepo4在75℃下在h2o2存在下与h2so4(4m)溶液接触时,整个活性电极材料溶解为锂和硫酸铁。这涉及选择性沉淀铁的额外步骤,通常通过调节ph(包括使用大量氢氧化物来中和过量的酸),然后通常通过添加碳酸盐如碳酸钠或将其转化为氢氧化锂来回收锂。从使用过的电极材料选择性提取锂的唯一报道的情况是基于草酸的使用,其也涉及使用相对昂贵的试剂。该方法还需要在高温(即80℃)下进行(j.s.sohnetal.,advancedprocessingofmetalsandmaterials,sohninternationalsymposium,proceedings,sandiego,ca,usa,27-31august2006(2006),vol.6,135-143)。因此,可以看出,用于从用过的锂电池再循环活性电极材料的常规方法不是选择性的,并且涉及使用相当腐蚀性的试剂、高温条件和数种副产物的形成,导致更高的回收成本。因此需要一种再循环方法,其涉及侵蚀性较小的试剂,非临界条件和/或允许选择性再循环活性电极材料。摘要根据第一方面,本发明涉及再循环电化学活性材料的方法。该方法包括以下步骤:(a)使电化学活性材料与氧化剂或还原剂在溶剂(例如水性溶剂)中反应,以产生锂盐和电化学活性材料前体沉淀物;(b)将电化学活性材料前体沉淀物与锂盐分离;(c)从电化学活性材料前体再生电化学活性材料。在一个实施方案中,溶剂是水。根据一个实施方案,步骤(a)还包括注入气态co2以增加锂盐在溶剂中的溶解度。根据另一个实施方案,步骤(c)包括加热锂盐以回收气态co2和循环锂盐。根据另一个实施方案,氧化剂包括过氧化氢,或臭氧,或氧气。氧化剂还可包括过硫酸盐。根据一个实施方案,步骤(c)还包括将锂盐电解,钠盐溶液处理或co2注入以回收循环锂盐。在某些情况下,如此回收的锂盐用于再生电化学活性材料。根据另一方面,本技术还涉及一种从锂电池再循环电极材料的方法,其中将分离的用过的电极材料悬浮在水性介质中并在氧化剂或还原剂存在下与co2反应以选择性地并且有效地将锂内容物作为碳酸氢锂分离并通过分离方法将剩余的活性电极材料作为固体回收。然后处理分离的液相以回收锂内容物,该锂内容物将与从固相回收的其它电极材料元素一起再循环用于制造新电极材料。根据一个实施方案,反应器中的co2压力可在1至10atm之间变化,但更优选在1至5atm之间变化。可以将反应混合物冷却至室温以下,以提高碳酸氢锂的溶解度。反应可在10至30℃之间进行,例如,在20至25℃之间。根据另一个实施方案,氧化剂或还原剂是过氧化氢,其相对于待氧化或还原的过渡金属以化学计量量或略微过量使用。根据一个实例,分离的固相含有高纯度的fepo4,fepo4保持其晶体结构,因此允许其再用于制造新的电极材料。根据一个实施方案,一旦分离固相,将液相加热至高温,优选约90℃,以回收碳酸锂沉淀形式的锂。然后将碳酸锂沉淀物干燥并再用于制造电极材料,释放的气态co2和含有残余锂碳酸盐和/或碳酸氢盐的溶液再循环于与其它用过的电极材料的反应中。根据另一方面,本技术还涉及一种从锂电池再循环电极材料的方法,其中将分离的用过的电极材料悬浮在水性介质中并与li2s2o8反应以从电极材料中作为在液相中的硫酸锂提取锂,过渡金属氧化物保留在固相中。通过常规分离方法分离固相,并重新用于形成新的电极材料。然后将液相分成两部分。一部分用作添加到电解池的阳极电解液中的材料,其中硫酸锂被氧化回过硫酸锂,其将再次用于处理其他用过的电池电极材料。另一部分含有硫酸锂的液相将用于通过盐解离电解以其他盐的形式回收锂,例如碳酸锂(使用co2或另一种碳酸盐如碳酸钠na2co3)或氢氧化锂lioh。根据一个实施方案,反应在5和60℃之间,或在20和40℃之间进行,因为在较高温度下,过硫酸盐较不稳定。根据另一个实施方案,通过电解将含有硫酸锂的第一部分液相转化为氢氧化锂和硫酸。然后使lioh与过硫酸铵反应以产生过硫酸锂,其用于处理其他用过的电池电极材料。根据另一个实施方案,lioh和(nh4)2s2o8之间的反应在真空下进行以促进消除气态nh3,其通过形成硫酸铵,然后将其加入到电解池的阳极电解液中产生过硫酸铵而再循环。附图的简要说明图1是根据一个实施方案的方法的示意图。图2显示了进行根据一个实施方案的方法的样品的x射线衍射图谱。图3是根据另一个实施方案的方法的示意图。图4显示了根据本说明书实施例1的不同类型活性材料的沥滤效率随时间的变化。图5显示了根据本说明书实施例2的不同类型活性材料的沥滤效率随时间的变化。图6显示了根据说明书实施例3的不同类型活性材料的沥滤效率随时间的变化。图7显示了根据本说明书实施例5的不同类型活性材料的沥滤效率随时间的变化。图8显示了根据本说明书实施例6的不同类型活性材料的沥滤效率随时间的变化。图9显示了根据本说明书实施例7的不同类型活性材料的沥滤效率随时间的变化。图10显示了根据本说明书实施例8的不同类型活性材料的沥滤效率随时间的变化。详细说明本申请涉及从锂电池再循环电化学活性材料的方法。更具体地,本申请的主题涉及一旦电极材料与其余电池元件分离,就回收电极材料的电化学活性组分。在下文中提出了实现从电化学活性电极材料中选择性提取锂组分而不使用强酸或高温条件的新方法。在第一方面,使从电池组分的分离中回收并包含电化学活性材料的电极材料与溶剂中所含的氧化剂或还原剂接触,任选地在co2存在下。该步骤不包括强酸如盐酸,硫酸,硝酸等的存在。氧化剂或还原剂的选择取决于所用电极材料的类型。本方法可适用于阴极材料再循环或阳极材料再循环。因此,该方法的第一步是电化学活性材料与氧化剂或还原剂在溶剂中的反应。这产生锂盐和电化学活性材料前体沉淀物(即,完全或部分脱锂的电化学活性材料),在后面称为前体沉淀物。在一个实施方案中,将包含电化学活性材料的混合物分散在溶剂中。在优选的实施方案中,溶剂是水,产生的锂盐在溶液中。电化学活性材料可以是氧化物,复合氧化物,磷酸盐,硅酸盐等。例如,它可以是lifepo4,或本领域技术人员已知的任何其他电化学活性材料。在lifepo4的情况下,形成的前体沉淀物是fepo4。生成的锂盐可以是例如lihco3或li2so4。有用的氧化剂的实例是过氧化氢(h2o2)。可以使用其他氧化剂,例如氧气(o2),臭氧(o3),空气等。本领域技术人员将认识到过氧化氢可以用作氧化剂和还原剂。相对于待氧化或还原的过渡金属,氧化剂或还原剂可以化学计量量或略微过量(即过量5mol%-10mol%)使用。然而,本领域技术人员将理解,氧化剂或还原剂可以以更大的过量使用。该方法的第一反应步骤还可包括将co2注入溶液中。在溶液中鼓泡co2并增加锂盐在溶剂中的溶解度。这因此提高了该方法的沥滤效率。例如,如图4所示,已经发现,当含有lifepo4的粉末与含有氧化剂如h2o2的水溶液反应时,在存在鼓泡的co2的情况下,锂可以以高达100%的提取率以非常选择性的方式从粉末中提取,例如,与锂一起提取少于1%的铁fe或4%的磷p。包含在固相中的前体沉淀物在反应步骤中基本上或完全保持其晶体结构。由于电化学活性材料与氧化剂或还原剂之间的反应动力学在室温下非常快,因此不需要高温条件。可以将反应混合物冷却至室温以下,以提高碳酸氢锂的溶解度。但是,出于经济原因,反应可在10至30℃之间,或在20至25℃之间进行。事实上,在较高温度下,锂盐(例如碳酸锂)的溶解度降低,这需要具有较高体积的反应器和较低锂回收率。反应可在反应器中在大气压或更高压力下进行。观察到锂盐的溶解度随着co2压力的升高而增加。然而,在超过10atm的压力下,溶解度开始达到平稳阶段并且溶解度仅有少许增加。因此,反应压力优选在1至10atm之间。在第二步中,将生成的锂盐和前体沉淀物的混合物进行分离。由于前体沉淀物在反应过程中保持固态,因此可以通过本领域技术人员已知的任何分离技术将其与锂盐溶液分离,例如通过过滤或离心。一旦前体沉淀物和锂盐分离,该方法包括从所述前体沉淀物中再生电化学活性材料。因此,在本技术的一个实施方案中,再循环方法包括再生步骤。在分离步骤中回收的前体沉淀物用于制造新的锂电化学活性材料。在一些实施方案中,再生步骤还包括回收锂盐中包含的锂。锂回收包括加热从分离中回收的锂盐,以产生循环锂盐、气态co2和残留的锂盐溶液。锂盐可以在50℃至100℃的温度下加热,优选在85℃至95℃的温度下加热。在一些实施方案中,锂盐在高温下加热,优选约90℃。然后将循环锂盐用于制造新的电化学活性材料,并且可以将回收的气态co2再注入本发明方法的第一反应步骤中。最后,残留的锂盐溶液也可以再引入前述第一步的反应混合物中。在该方法的一个实施方案中,如图1所示,将包含电化学活性材料lifepo4的阴极材料的回收电极混合物分散在含有过氧化氢h2o2的水溶液中,并用co2处理,所述co2在悬浮液中鼓泡。在这种情况下,过氧化氢(h2o2)作为lifepo4的氧化剂,其中所含的锂根据下式作为碳酸氢锂(lihco3)沥滤出来:2lifepo4(s)+h2o2+2co2→2lihco3+2fepo4(s)(式1)锂盐在液相中作为碳酸氢锂回收,其可以作为锂盐再循环,例如作为固体碳酸锂(li2co3)沉淀物而不添加任何其他化学试剂。在第一反应步骤中形成的磷酸铁(fepo4)保持为固体并且可以与悬浮液分离。x射线衍射分析表明fepo4晶体结构保持完整,因此该材料可以容易地返回新的lifepo4阴极材料的制造中。例如,图2显示了使用co2和h2o2进行如本文所述的锂提取的样品的x射线衍射光谱以及所得含量表。通过过滤分离的固体显示fepo4含量为97.3%,lifepo4含量为2.3%。然后可以在沉淀器中加热分离的含有碳酸氢锂lihco3的锂盐溶液,以回收固体碳酸锂li2co3,根据下式:2lihco3→li2co3(s)+h2o+co2↑(式2)如图1所示,残留的碳酸锂和碳酸氢锂以及释放的co2可以再引入第一反应步骤(或碳酸化步骤)以处理用过的电极材料。或者,可以将碳酸氢锂转化为除碳酸锂之外的锂盐。取决于应用,这种锂盐可包含本领域技术人员已知的任何锂盐。从再生步骤回收的磷酸铁、碳酸锂或其他潜在的锂盐可用于制造包含lifepo4的新电化学活性电极材料,例如,用于锂电池。在本技术的另一个方面,使从电池组分的分离中回收并包含电化学活性材料的电极材料与溶剂中所含的氧化剂或还原剂接触。氧化剂可以是过硫酸盐。该接触产生锂盐和电化学活性材料前体沉淀物(前体沉淀物)。在一个实施方案中,将包含电化学活性材料的混合物分散在溶剂中。溶剂可以是水,以便锂盐作为锂盐溶液回收。反应可在5℃至60℃之间进行,但更特别地在20℃至40℃之间。实际上,在较高温度下,过硫酸盐不太稳定。在一个实施方案中,在第一反应步骤中产生的锂盐在溶剂中高度可溶,使得不必使用co2来增加锂盐溶解度。如前所述,将在反应步骤中产生的锂盐和前体沉淀物进行分离步骤。由于前体沉淀物在反应过程中保持固态,因此可以通过过滤、离心等将其与锂盐溶液分离。在分离步骤之后,该方法包括从前体沉淀物中再生电化学活性材料,其可以直接用于制造新的电化学活性材料。在一些实施方案中,再生步骤还包括回收锂盐中包含的锂。为此,将从分离步骤回收的锂盐进行电解、钠盐处理或co2处理。在一些实施方案中,部分锂盐作为过硫酸盐回收并在第一反应步骤中再用作氧化剂或还原剂。剩余的回收的锂盐可以转化为其他锂盐,例如碳酸锂(使用co2或碳酸钠)或氢氧化锂(通过电解),以便再用于制造锂电池电化学活性材料(例如作为lifepo4)。在一个实施方案中,氢氧化锂可通过其与过硫酸铵((nh4)2s2o8)的反应用于生产过硫酸锂(li2s2o8)。通过与从硫酸锂(li2so4)电解获得的硫酸反应,可以回收释放的氨(nh3)以形成硫酸铵((nh4)2so4)。以这种方式形成的硫酸铵可通过其直接电解容易地转化为过硫酸铵。在一个优选的实施方案中,如图3所示,用过硫酸锂水溶液处理包含lifepo4的用过的电极材料的悬浮液,这导致锂作为硫酸锂li2so4的选择性和完全沥滤。如图4所示,该方法导致少于1%的铁沥滤。根据以下反应,磷酸铁主要以悬浮固体的形式保留:2lifepo4(s)+li2s2o8→2li2so4+2fepo4(s)(式3)关于图3,在第一反应步骤中形成的磷酸铁保持固体形式,其可以与悬浮液分离并且容易地再用于制造新的lifepo4阴极材料。然后将硫酸锂溶液再循环以产生其他锂盐,例如碳酸锂(通过添加碳酸钠或通过使用co2)或氢氧化锂(通过盐解离操作中的电解)。如图3所示,硫酸锂电解产生氢氧化锂和硫酸。此外,所获得的部分锂盐可用于再生过硫酸锂并再引入该方法中。过硫酸锂再生可以通过在适于过硫酸盐生产的电解池的阳极侧的硫酸锂直接电解来完成。根据以下反应,过硫酸锂也可通过部分生成的lioh和过硫酸铵之间的反应再生:2lioh+(nh4)2s2o8→li2s2o8+2nh3↑(式4)上述反应在真空下进行,优选将惰性气体鼓入溶液中,以快速排出释放的气态氨并使其与过硫酸铵的反应最小化。氨可以回收并通过其与硫酸锂电解转化成氢氧化锂过程中形成的硫酸反应形成硫酸铵。然后将硫酸铵用于电解生产过硫酸铵,其然后根据式4用于生产过硫酸锂。以下实施例用于说明目的,决不应解释为限制本申请中描述的本发明的范围。实施例实施例1为了模拟基于使用气态co2和氧化剂的所提出的沥滤(或浸出)条件的应用,使用主要含有lifepo4以及少量聚偏二氟乙烯(pvdf)和石墨的新阴极材料代表回收的用过的电极材料。将一份该材料在搅拌反应器中分散在100份含有0.5wt%h2o2的水溶液中,在30psi的压力和25℃下将co2气体鼓入水溶液中。因此lifepo4/h2o2摩尔比为2.77。每30分钟收集样品,通过电感耦合等离子体(icp)分析测定溶液中li、fe和p的浓度。然后将结果用于计算该方法对每种元素的沥滤效率。这些结果显示在图4中。发现在30分钟后,来自电极材料的所有锂内容物作为碳酸氢锂溶解,而小于0.5%的铁和3.5%的磷被提取。这证明了本发明方法对锂沥滤的非常高的选择性和效率。当在相同的lifepo4/h2o2比但不存在co2的情况下进行相同的反应时,仅提取3%的锂。此外,当仅使用co2处理电极材料时,即使在75psi的co2压力下,也仅提取了12%的锂(参见下表1)。这些结果表明,co2和h2o2的存在对于锂沥滤的高效率是必不可少的。在所有情况下,提取对锂具有很高的选择性,如表1中li和fe的沥滤效率所证明。表1沥滤条件li沥滤效率(%)fe沥滤效率(%)用h2o2沥滤3%<0.1%用co2沥滤12%0.2%用co2和h2o2沥滤100%0.3%实施例2为了比较,用硫酸代替co2进行相同的反应。将一份含有lifepo4的阴极材料在两种不同条件下加入到4mh2so4水溶液中,一种在5wt%h2o2存在下,另一种在不存在h2o2的情况下。在两种情况下,在搅拌下将悬浮液加热至75℃,并通过icp分析来自水相的过滤样品,以确定不同时间间隔的li和fe含量。如图5所示,在没有h2o2的情况下,仅提取70%的锂,而添加h2o2允许达到100%的锂提取效率。然而,在两种情况下,大量的fepo4(65%至90%)也被沥滤到溶液中,表明li和fe提取之间绝对缺乏选择性。因此,在强酸如硫酸的存在下,铁与锂的分离需要在锂回收步骤之后施加额外的化学试剂和步骤(例如受控的ph调节和过滤步骤)。此外,与本发明的方法不同,回收的铁在用于制备新的电极材料之前需要转化回fepo4。实施例3重复实施例1中给出的实验,但这次是五倍的固体量。因此,在搅拌反应器中将5份阴极材料悬浮在100份含有0.5wt%h2o2的水溶液中,在30psi的压力和25℃下将co2气体鼓入溶液中。在这种情况下,lifepo4/h2o2摩尔比为0.55,相对于完全沥滤li所需的化学计量量的h2o2,仅略微超过10%。图6显示了li、fe和p的沥滤效率结果。锂的总沥滤效率高于92%,而fe的沥滤效率为1%。这再次证实了本发明的锂提取方法的高效率和非常高的选择性,以及回收几乎所有fepo4以制造新电极材料的可能性。如本文所述,然后可以加热来自该操作的含有锂盐溶液的滤液,以回收作为碳酸锂li2co3沉淀物的提取的锂,然后将其与回收的fepo4一起用于制造新的电极材料。实施例1和3的比较结果证实氧化剂或还原剂的量可保持在化学计量比附近。化学计量过量仅为10%,使锂沥滤效率超过92%。本领域技术人员将理解,出于经济原因,并且由于在本发明方法的后续步骤中可能损失过量的氧化剂或还原剂,因此所述试剂可保持在化学计量比或非常接近化学计量比。实施例4为了验证甚至在更高的固/液比下仍能达到高沥滤效率,改变实施例3的实验,使用悬浮在100份含有1wt%h2o2的水溶液中的10份阴极材料,其中co2压力为30psi。再次,获得了约90%的li沥滤效率,而该操作导致fe的沥滤率小于0.5%而p的沥滤率小于2.5%。这再次证实了本锂提取方法的高选择性。此外,由于fepo4固体保持完整,因此可以通过简单过滤轻松回收。实际上,过滤固相的x射线衍射分析显示fepo4含量为97.7%,lifepo4含量为2.7%,表明li沥滤效率甚至更高(见图2)。实施例5在该实施例中,将7.5份固体lioh溶解在100份水中,并加入到含有35.5份(nh4)2s2o8在150份水中的水溶液的搅拌反应器中。将混合物搅拌3小时,使反应器处于真空下以促进释放的气态nh3的排出。通过观察溶液ph值从14降至约10来监测li2s2o8的形成和nh3消除,表明存在非常少量的nh3,从而根据下式确认反应完成:2lioh+(nh4)2s2o8→li2s2o8+2nh3↑然后将含li2s2o8的溶液用于处理21份阴极材料。从图7中可以看出,2小时后,92%的锂从阴极材料中提取,而在溶液中发现不到1%的p和几乎没有fe,再次证明了对锂提取的非常高的选择性,对于h2o2和co2。过滤的固体的x射线衍射分析证实在固相中fe和p作为fepo4回收(fepo4含量高于99.7%)。实施例6通过将一份相同类型的主要含有lifepo4的阴极材料分散在100份水中,并在反应器中搅拌和鼓泡co2气体,重复实施例1中给出的实验。这次,用臭氧作为氧化剂代替过氧化氢。将气态臭氧(由供给氧的臭氧发生器产生)以约4gr/h的速率注入水性分散体中。反应器压力保持在5psi,反应温度为约25℃。如在图8中可以观察到的,每30分钟收集的样品的icp分析显示,在150分钟后,约90%的锂被提取为lihco3。在同一时期提取不超过0.5%的铁和少于4.5%的磷的事实表明该方法是非常有选择性的并且非常有效。实施例7使用不同的氧化剂(在这种情况下为气态氧)重复实施例6中给出的试验。同样,将一份主要含有lifepo4的相同类型的阴极材料分散在100份水中,将该分散体在反应器中搅拌。将气态氧和co2以约1.8l/min的流速鼓入反应器中,同时保持反应器压力为30psi并且其温度为约25℃。图9显示了作为时间函数的li、fe和p沥滤效率。可以观察到,使用气态氧可以获得li的选择性提取,因为其提取百分比随着反应的进行而不断增加(在270分钟后达到35%)而fe和p的提取百分比迅速达到稳定水平并且对于铁保持在约0.5%并且对于磷保持在低于4%。反应动力学似乎比臭氧或h2o2慢,可能是由于气态氧在水中的溶解度低得多。另一方面,这些结果表明使用气态氧作为氧化剂的反应的可行性。显然,通过用于改进反应器中气体分散的常规方法可以提高反应动力学和提取效率。实施例8在相同条件下重复实施例7中给出的实验,但是用空气作为氧化剂代替氧气。结果(图10中显示)进一步证明了选择性锂提取的可行性,尽管动力学比用氧气获得的动力学慢,因为在300分钟反应后沥滤效率为约24%。同样,fe和p的沥滤率非常低(分别低于0.4%和4%),这证实了li提取的高选择性。至于氧气,结果证实使用空气作为氧化剂完全可以进行选择性li提取。因此,本发明方法提供了包含在回收的用过的电极材料中的锂的选择性和有效沥滤,而不使用强酸或临界压力和温度条件。与常规方法相比,这允许以较低的经济和环境成本再生锂电池的电化学活性材料。在不脱离本发明范围的情况下,可以对上述实施方案中的一个或另一个进行许多修改。来自本申请中提及的科学文献的参考文献、专利或文献通过引用作为整体和用于所有目的并入本文。当前第1页12