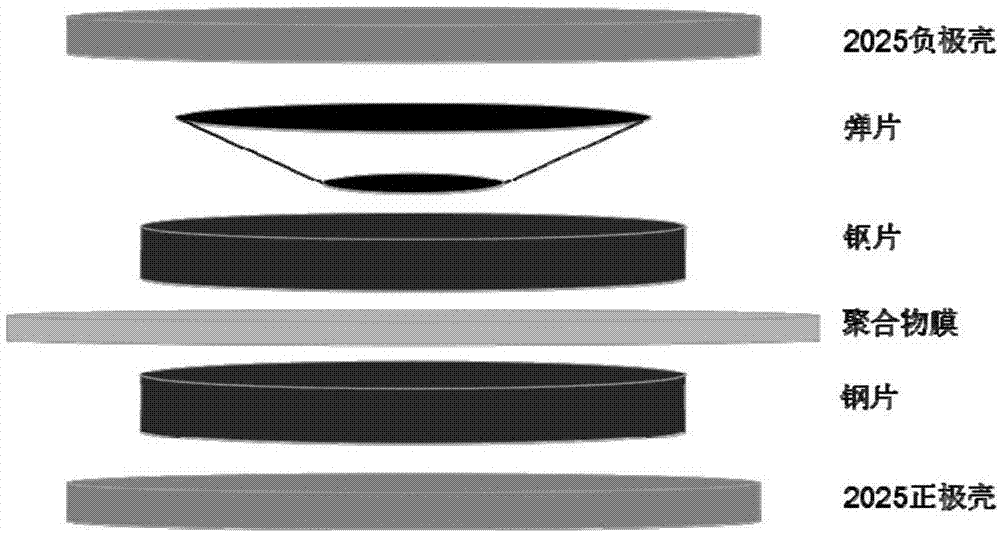
本发明属于锂离子电池材料领域,尤其涉及一种提高阻塞电池界面接触性的阻塞电池组装方法。
背景技术:
聚碳酸酯基聚合物固体电解质具有很高的室温离子电导率以及优异的电化学性能,在全固态电池技术中具有极大的应用前景。在固体电解质的表征领域,利用阻塞电池测试固体电解质的离子电导率是最基本且最重要的一项测试表征技术。但是由于聚碳酸酯基聚合物的刚性较大,这导致其测试离子电导率时阻塞电池的界面接触较差,产生很高的界面阻抗,导致无法测试出阻塞电池的阻抗谱。一般聚合物在加热时可以软化从而提高界面的润湿性;但是聚碳酸酯类高分子的热稳定性一般,在120℃以上时即产生失重。若采用提高温度以软化聚合物从而提高阻塞电池界面接触性的方法,很有可能导致聚合物发生分解或者发生其他副反应,严重影响聚碳酸酯聚合物本体电导率的正确表征,而且加热软化也会导致聚合物膜发生形变,在厚度方向上发生收缩,导致电导率计算不准确。技术实现要素:本发明所要解决的技术问题是,克服以上
背景技术:
中提到的不足和缺陷,提供一种提高基于聚碳酸酯基固体电解质的阻塞电池界面接触性的方法,该方法可以保证聚碳酸酯基固体电解质室温离子电导率的“无损”表征。为解决上述技术问题,本发明提出的技术方案为:一种提高阻塞电池界面接触性的阻塞电池组装方法,包括以下步骤:(1)用极性溶剂处理聚合物电解质膜的正反两面;(2)用两片不锈钢片或金片放在步骤(1)处理后的聚合物电解质膜的两侧,形成阻塞电池前驱体;(3)将阻塞电池前驱体充分烘干,进行模具封装,即得到阻塞电池。上述的组装方法,优选的,所述聚合物电解质膜为聚碳酸酯电解质膜。上述的组装方法,优选的,所述的极性溶剂为n-甲基吡咯烷酮、n,n-二甲基甲酰胺、n,n-二甲基乙酰胺、二甲基亚砜、氯苯、丁二腈、甲苯、四氢呋喃、二氯甲烷、氯仿、丙酮、乙腈、苯、乙酸乙酯、六氟异丙醇的一种或几种。上述的组装方法,优选的,所述步骤(1)中,极性溶剂采用涂覆方法涂在聚合物电解质膜的表面。进一步优选的,采用滴涂的方式涂在聚合物电解质膜的表面。上述的组装方法,优选的,所述步骤(1)中,极性溶剂在聚合物电解质膜上的涂覆量为0.01~0.05ml/cm2。充分保证聚合物膜进行适当溶解,不至于溶解不充分或者溶解过度。上述的组装方法,优选的,所述步骤(3)中,烘干是指先在25~60℃下鼓风干燥24h以上,再进行真空干燥,真空干燥的温度为80~120℃,时间为12~24h。采用鼓风和真空相结合的方式进行干燥,既可以保证聚合物膜被充分干燥,又不至于会起泡。上述的组装方法,优选的,所述模具为2016电池壳、2025电池壳或2032电池壳。本发明利用极性溶剂来溶化硬度较高的聚碳酸酯电解质膜,改善阻塞电池的界面接触。所处理的阻塞电池界面接触性好,可以避免聚合物由于热稳定性差而不能通过热熔化来改善界面接触性的矛盾,实现了聚碳酸酯基固体电解质室温离子电导率的“无损”表征。与现有技术相比,本发明的优点在于:本发明提供的阻塞电池组装方法能够提高阻塞电池界面接触性,避免传统聚合物由于热稳定性差而不能通过热熔化来改善界面接触性的矛盾,可以在避免高温加热时,就实现聚合物膜和阻塞电极的良好贴合,实现了聚碳酸酯基固体电解质室温离子电导率的“无损”表征。附图说明图1是本发明实施例1中阻塞电池组装方法。图2是本发明实施例1和对比例1b的阻塞电池膜的阻抗对比图。具体实施方式为了便于理解本发明,下文将结合说明书附图和较佳的实施例对本文发明做更全面、细致地描述,但本发明的保护范围并不限于以下具体实施例。除非另有定义,下文中所使用的所有专业术语与本领域技术人员通常理解含义相同。本文中所使用的专业术语只是为了描述具体实施例的目的,并不是旨在限制本发明的保护范围。除非另有特别说明,本发明中用到的各种原材料、试剂、仪器和设备等均可通过市场购买得到或者可通过现有方法制备得到。实施例1:一种提高阻塞电池界面接触性的阻塞电池组装方法,包括以下步骤:(1)将总厚度为200μm的纤维素膜无纺膜支撑下的ppc基(聚碳酸丙烯酯)聚合物电解质膜裁切为直径19mm的圆片,用dmf滴涂在聚合物电解质膜的正反两面使其两表面润湿(涂覆量为0.02ml/cm2);(2)将两片厚度为0.8mm、直径为16mm的不锈钢片正对贴合于聚合物电解质膜(圆片)的两表面,形成阻塞电池前驱体;(3)将阻塞电池前驱体在60℃下鼓风干燥24小时,再移入真空箱中于120℃下干燥24小时,最后用弹片、2025电池壳封装(安装示意图如图1所示),得到最终的阻塞电池。在手套箱中用2025电池壳组装“不锈钢/聚合物膜/不锈钢”结构的阻塞电池进行阻抗测试,频率范围为1mhz—1hz。测试电池按本实施例方法进行组装;将另一采用熔化法测试阻抗的电池不做处理,仅在用传统方法组装完毕后在130℃下加热24小时后,测试阻抗,结果如图2所示,膜的阻抗值为半圆与横轴的右交点。由图2可见,本实施例方法组装的电池测试得出的阻抗谱有代表高频区、中频区的半圆和低频区的直线,而熔化法无法得出半圆,仅存在一条代表界面扩散的直线。对比例1a:在手套箱中用2025电池壳组装“不锈钢/聚合物膜/不锈钢”结构的阻塞电池后直接测试阻抗。对比例1b:在手套箱中用2025电池壳组装“不锈钢/聚合物膜/不锈钢”结构的阻塞电池后在140℃下加热24小时后,测试阻抗。实施例2:一种提高阻塞电池界面接触性的阻塞电池组装方法,包括以下步骤:(1)将总厚度为80um的pec(聚碳酸丙烯酯)基聚合物电解质膜裁切为直径18mm的圆片,用四氢呋喃滴涂在聚合物电解质膜的正反两面,使其两表面润湿(涂覆量为0.01ml/cm2);(2)将两片厚度为0.5mm、直径为12mm的金片正对贴合于聚合物电解质膜(圆片)的表面,形成阻塞电池前驱体;(3)将阻塞电池前驱体在60℃鼓风干燥30小时,再移入真空箱中于120℃下干燥24小时,最后用2032电池壳封装,得到最终的阻塞电池。对比例2a:在手套箱中用2032电池壳组装“不锈钢/聚合物膜/不锈钢”结构的阻塞电池后直接测试阻抗对比例2b:在手套箱中用2032电池壳组装“不锈钢/聚合物膜/不锈钢”结构的阻塞电池后在130℃下加热24小时后,测试阻抗。实施例3:一种提高阻塞电池界面接触性的阻塞电池组装方法,包括以下步骤:(1)将总厚度为120μm的玻璃纤维支撑下的pvc基(聚(碳酸亚乙烯酯))聚合物电解质膜裁切为直径14mm的圆片,用二甲基亚砜涂在聚合物电解质膜的正反两面,使其两表面润湿(涂覆量为0.04ml/cm2);(2)将两片厚度为1.5mm、直径为12mm的不锈钢片正对贴合于聚合物电解质膜(圆片)的表面,形成阻塞电池前驱体;(3)将阻塞电池前驱体于40℃下鼓风干燥48小时,再移入真空箱中于90℃下干燥24小时,最后用2025电池壳封装,得到最终的阻塞电池。对比例3a:在手套箱中用2025电池壳组装“不锈钢/聚合物膜/不锈钢”结构的阻塞电池后直接测试阻抗对比例3b:在手套箱中用2025电池壳组装“不锈钢/聚合物膜/不锈钢”结构的阻塞电池后在130℃下加热24小时后,测试阻抗。实施例4:一种提高阻塞电池界面接触性的阻塞电池组装方法,包括以下步骤:(1)将总厚度为40μm的ptmc基(聚(三亚甲基碳酸酯))聚合物电解质膜裁切为直径24mm的圆片,用n-甲基吡咯烷酮滴涂在聚合物电解质膜的正反两面使其两表面润湿(涂覆量为0.02ml/cm2);(2)将两片厚度为1.5mm、直径为22mm的不锈钢片正对贴合于聚合物电解质膜(圆片)的两表面,形成阻塞电池前驱体;(3)将阻塞电池前驱体在50℃下鼓风干燥36小时,再移入真空箱中120℃干燥24小时,最后用2032电池壳封装,得到最终的阻塞电池。对比例3a:在手套箱中用2025电池壳组装“不锈钢/聚合物膜/不锈钢”结构的阻塞电池后直接测试阻抗对比例3b:在手套箱中用2025电池壳组装“不锈钢/聚合物膜/不锈钢”结构的阻塞电池后在130℃下加热24小时后,测试阻抗。利用上述各个实施例和对比例中的方法测试阻塞电池中膜的阻抗,结果见表1所示。表1各个实施例和对比例中的方法测试阻塞电池中膜的阻抗实施例对比例a对比例b135ω无法得出2.3ω276ω>10000ω9.4ω390ω无法得出7.8ω495ω>10000ω5.5ω由表1可知,不进行加热保温的聚碳酸酯电解质膜得到的阻抗图谱均杂乱无章或者无限大;而进行130℃加热保温的电池所得到的阻抗谱均没有半圆(对比例b中的阻抗值虽然更低,但是由于采用了熔化法,其聚合物的结构已经发生破坏,生成了小分子的软聚合物、液体,显然这些都是“有损表征”,得到的阻抗值不准确,在实际应用中是不可接受的),以上两种情况均无法得出电解质膜的阻抗;而采用本发明的方法组装后的电池则可以准确的测出电解质膜的阻抗,和现有技术中报道的理论值基本接近。当前第1页12