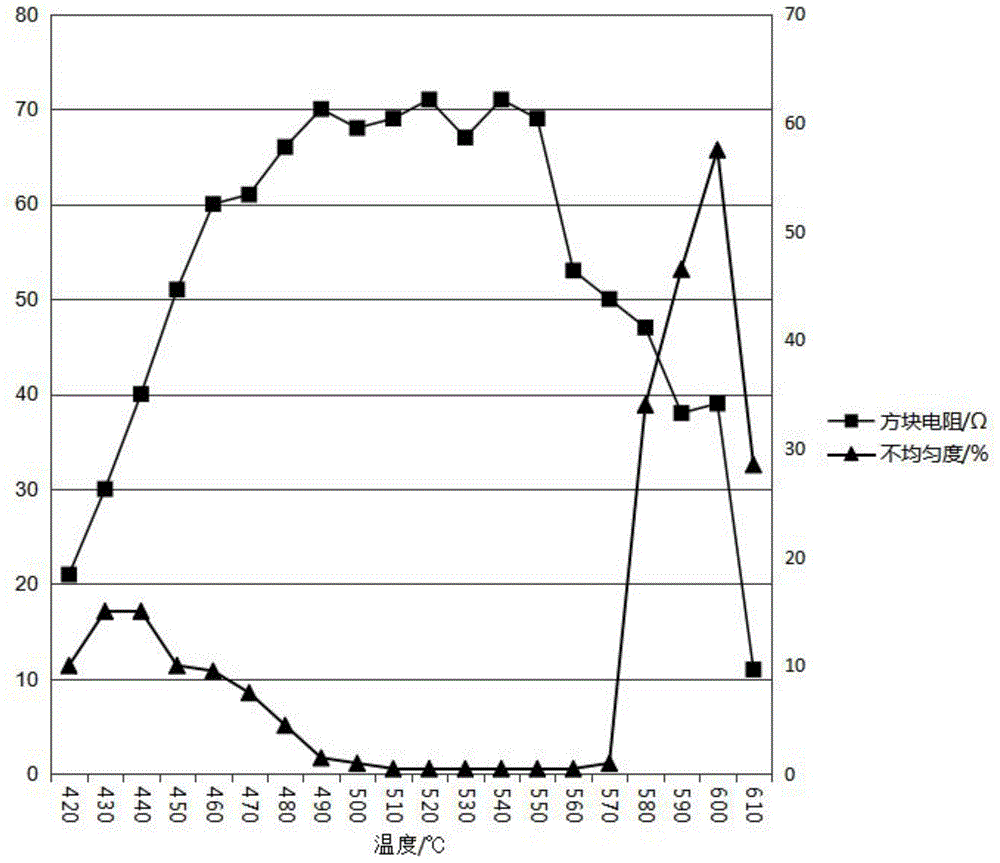
本发明涉及半导体
技术领域:
,尤其是涉及一种监控退火设备控温性能的方法。
背景技术:
:在超大规模集成电路领域,随着芯片尺寸的设计规则缩小和器件的比例缩放,对接触电阻的极限要求越来越高。产业需要寻找新的替代品,钴自对准硅化物被发现了。在其制备过程中,通常需要对生产时的状况进行监测。例如,硅化钴的相关制程工艺中,包括利用快速退火设备进行的快速热退火工艺(rta),如果快速退火设备的退火温度不稳定,会对形成的硅化钴以及半导体器件造成重要影响。以闪存为例,如果快速退火设备的实际温度偏移设定温度较大,会导致硅化钴形成超过规格、均匀度变差甚至跟pn结直接接触,造成编程功能失效(programfail),从而影响器件性能,故快速退火设备的温度监控至关重要。现有的一种监控快速退火设备温度的方法为:使用监控晶圆,先期进行了离子注入,然后进行快速热退火激活掺杂离子,接着测量掺杂离子一侧的监控晶圆表面的方块电阻(sheetresistance)。由于方块电阻对快速退火工艺具有一定的敏感性,方块电阻的变化一定程度上可以反应出退火温度的变化。但是,这种方法通常仅适用于硅化钛制程工艺中对退火设备温度的监控。硅化钛的形成温度为650度-750度,而硅化钴的形成温度较低,在450度-540度之间,这样的温度区间对常用的快速退火设备来说属于低温控制范畴,采用离子注入过的含有掺杂离子的监控晶圆难以完全激活掺杂离子,导致无法通过方块电阻对工作温度进行有效监控。为了对在低温区间工作的快速退火设备进行监控,现有另外一种监控快速退火设备温度的方法中,监控晶圆上事先形成有钴、氮化钛和钛的叠层结构,或者钴和钛的叠层结构,或者钴和氮化钛的叠层结构,在进行低温快速热退火后,监控晶圆上形成硅化钴,然后测量方块电阻,这种方法利用方块电阻对硅化钴相转变的温度变化敏感来监控快速退火设备温度的变化。通常,获得方块电阻时,需要对监控晶圆多处的方块电阻值进行测量,因此方块电阻值分布的均匀性也是评价方块电阻测量的准确性的标准之一。图1为一种监控晶圆经过低温退火后的方块电阻及其不均匀度随温度变化的示意图,可以看出,在420度-470度范围内,虽然方块电阻是比较线性的增长,但是均匀性太差导致不能准确反映设备状况;在490度-550度范围内,虽然均匀性很好,但是方块电阻的阻值基本保持不变,难以从中获得工作温度的变化;550度-600度范围内与420度-470度范围情况类似。因此,现有的监控方法在监控低温退火温度下的快速退火设备的实际工作温度时,并不是非常有效和准确的。技术实现要素:为了提高对快速退火设备的实际工作温度监控的有效性和准确性,本发明提供了一种监控退火设备控温性能的方法。所述监控退火设备控温性能的方法包括:提供一监控晶圆,所述监控晶圆在退火前后的热波变化量与退火温度之间具有一线性关系;测量退火前的所述监控晶圆的热波,得到第一热波值;将所述监控晶圆放入监控的退火设备中,并在设定温度下进行退火;取出所述监控晶圆,并测量退火后的所述监控晶圆的热波,得到第二热波值;计算第一热波值和第二热波值的差值;利用所述线性关系,获得与所述差值对应的实际退火温度;以及通过所述设定温度与实际退火温度的偏离程度,判断监控的退火设备的控温性能。可选的,所述设定温度的范围为400度至600度。可选的,所述监控晶圆具有第一表面和第二表面,在测量退火前的所述监控晶圆的热波之前,对所述监控晶圆的第一表面进行离子注入。可选的,所述离子注入采用的注入离子为铟离子,注入电压为115千伏至180千伏,离子注入浓度为5×10-13个原子/cm2至8×10-13个原子/cm2。可选的,监控的退火设备中,在离子注入之前,在所述监控晶圆的第二表面形成低反射层,在完成退火之后,通过监控的退火设备的日志文件获得对应的低反射率,通过所述低反射率判断监控的退火设备在低反射环境下的控温稳定性。可选的,所述低反射层包括在所述监控晶圆的所述第二表面上依次叠加形成的氧化层和多晶硅层。可选的,所述氧化层的厚度为800埃至1200埃,所述多晶硅层的厚度为1500埃至2000埃。可选的,所述第一热波值为退火前对应所述监控晶圆表面多个不同位置测量得到的热波值的平均值,所述第二热波值为退火后对应所述监控晶圆表面多个不同位置测量得到的热波值的平均值。可选的,利用退火前和退火后所述热波值在晶圆上的分布,监控所述退火设备的加热均匀性。可选的,所述线性关系通过多个实测退火温度以及在所述多个实测退火温度下进行退火的热波变化量拟合获得。本发明提供的监控退火设备控温性能的方法,根据监控晶圆在退火前后的热波变化量与退火温度之间具有的线性关系对退火设备在退火时的控温性能进行监控,根据设定温度与实际退火温度的偏离程度大小即可判断出控温性能的好坏,相对于测量监控晶圆的方块电阻的监控方式,在低温退火时尤其具有优势,可以提高监控的有效性和准确性;此外,利用退火前和退火后测量的多个热波值在晶圆上的分布,可以监控退火设备加热的均匀性;利用对低反射率的监控,可以监控退火设备控温性能的稳定性。通过本发明提供的监控退火设备控温性能的方法,可以对退火设备的控温性能(尤其是低温退火下的控温性能,例如400度至600度)进行较为全面、有效、准确地监控。附图说明图1为一种监控晶圆经过低温退火后的方块电阻及其不均匀度随温度变化的示意图。图2为本发明一实施例的监控退火设备控温性能的方法的流程示意图。图3为本发明一实施例的监控晶圆退火前后的热波差值随温度变化的示意图。图4为本发明另一实施例的监控晶圆退火前后的热波差值随温度变化的示意图。具体实施方式下面将结合示意图对本发明的具体实施方式进行更详细的描述。根据下列描述,本发明的优点和特征将更清楚。如
背景技术:
所述,现有的监控方法在监控快速退火设备的实际工作温度时,并不是均能获得有效和准确的结果。为了提高对快速退火设备的实际工作温度监控的有效性和准确性,本发明实施例提供了一种监控退火设备控温性能的方法。图2为本发明一实施例的监控退火设备控温性能的方法的流程示意图。如图2所示,本实施例中的监控退火设备控温性能的方法包括以下步骤:步骤s1:提供一监控晶圆,所述监控晶圆在退火前后的热波变化量与退火温度之间具有一线性关系;步骤s2:测量退火前的所述监控晶圆的热波,得到第一热波值;步骤s3:将所述监控晶圆放入监控的退火设备中,并在设定温度下进行退火;步骤s4:取出所述监控晶圆,并测量退火后的所述监控晶圆的热波,得到第二热波值;步骤s5:计算第一热波值和第二热波值的差值;步骤s6:利用所述线性关系,获得与所述差值对应的实际退火温度;以及步骤s7:通过所述设定温度与实际退火温度的偏离程度,判断监控的退火设备的控温性能。本实施例中,上述退火设备例如是快速退火设备,用于执行快速热退火工艺。上述方法根据监控晶圆在退火前后的热波变化量与退火温度之间具有的线性关系对退火设备在低温退火时的控温性能进行监控,根据设定温度与实际退火温度的偏离程度大小即可判断出控温性能的好坏,相对于测量监控晶圆的方块电阻的监控方式,在低温退火时尤其具有优势,可以提高监控的有效性和准确性。下面对每一步骤进行详细阐述。本实施例中的监控退火设备控温性能的方法包括步骤s1,提供一监控晶圆,所述监控晶圆在退火前后的热波变化量与退火温度之间具有一线性关系。本实施例中,所述监控晶圆可以是无掺杂多晶硅晶圆或进行过imp离子注入的晶圆。经多次实验发现,对于经过掺杂的晶圆和无掺杂的晶圆,利用退火设备例如快速退火设备进行退火时,在一定范围内,监控晶圆在退火前后的热波变化量与实际退火温度之间满足一线性关系。在对退火设备控温性能进行监控前,需要获取此线性关系,本实施例中,此线性关系可以通过对多个实测退火温度以及在所述多个实测退火温度下进行退火的热波变化量拟合获得。具体的,首先以无掺杂的监控晶圆为例,如表1所示,为无掺杂多晶硅晶圆作为监控晶圆时,退火前后的热波变化量与退火温度。其中,设置了四个退火温度实验点,退火条件分别为在快速退火设备中于490度、510度、530度以及550度下保温30秒,此处退火温度为对快速退火设备进行校准后的实测退火温度,也即为表1中与热波值对应的真实温度。第一热波值为利用例如热波测量机测得的退火前热波值,第二热波值为利用例如热波测量机测得的退火后热波值。表1退火温度/度第一热波值/tw第二热波值/tw热波变化量/tw4901092.0787603.6393488.445101096.5436595.3176501.235301096.5304584.353512.185501096.6172575.966520.65以退火温度作为自变量x,热波变化量作为因变量y,可以得到图3所示的本发明一实施例中监控晶圆退火前后的热波差值随温度变化的示意图。从图3可以看出,监控晶圆在退火前后的热波变化量与退火温度之间的关系近似呈线性,对其进行拟合,可以得到如下线性关系公式(1):y=0.5379x+225.9(1)其中,热波变化量随温度变化的灵敏度即为斜率,约0.54tw/度;决定系数r2=0.992,表明线性拟合优度较大,线性关系公式(1)参考价值较高。类似的,采用获得线性关系公式(1)的方法可以获取掺杂有离子的监控晶圆的热波变化量与退火温度之间的线性关系。由于掺杂原子量大的离子时,晶圆的热波值大,便于热波数值收集。故在本实施例中,以掺杂离子为铟离子为例,如表2所示,为掺杂铟离子的监控晶圆退火前后的热波变化量与退火温度。其中,为了获得更高的灵敏度,离子注入电压为150千伏,离子注入浓度为5×10-13个原子。实验时,设置了3个退火温度实验点,退火条件分别为在快速退火设备中于470度、490度以及510度下保温30秒。表2退火温度/度第一热波值/tw第二热波值/tw热波变化量/tw4704045.0503540.6663504.38434904036.6414416.38743620.2545104033.0994142.10823890.9912以退火温度作为自变量x,热波变化量作为因变量y,可以得到图4所示的本发明另一实施例的监控晶圆退火前后的热波差值随温度变化的示意图。从图4可以看出,掺杂铟离子的监控晶圆在退火前后的热波变化量与退火温度之间的关系近似呈线性,对其进行拟合,可以得到所述线性关系的公式(2):y=9.6652x-1064.1(2)其中,热波变化量随温度变化的灵敏度即为斜率,约9.67tw/度;决定系数r2=0.9492,表明线性拟合优度较大,线性关系公式(2)参考价值较高。由此,利用监控晶圆在退火前后的热波变化量与实测退火温度数据之间可以获得满足基本线性条件的关系。由于掺杂大原子量元素的离子时,热波变化量随温度变化的灵敏度更高,从而监控的准确度也更高。因此为了更有效、更准确地对退火设备的控温性能进行监控,监控晶圆优选采用掺杂大原子量元素的离子的晶圆,例如掺杂铟离子、镓离子的晶圆,其中,离子注入电压和注入浓度也可以根据需要调整,具体的,注入电压可以为115千伏至180千伏,离子注入浓度可以为5×10-13个原子/cm2至8×10-13个原子/cm2。另外,获得所述线性关系的退火温度实验点的数量也不以上述为限,宜在实验温度区间内以较小的温度间隔区间设置尽量多的退火温度实验点,并在确定所述退火温度实验点对应的实测退火温度的前提下,获得在所述多个实测退火温度下进行退火的热波变化量。获得监控晶圆在退火前后的热波变化量与退火温度之间的线性关系后,可以对退火设备的控温性能进行监控。监控时采用的监控晶圆的离子掺杂方式与获得线性关系时的监控晶圆的离子掺杂方式宜保持一致。在获得监控晶圆以及对应的线性关系后,可以执行本实施例中的监控退火设备控温性能的方法的步骤s2,测量退火前的所述监控晶圆的热波,得到第一热波值。优选的,获得线性关系时或者利用所述线性关系进行监控时,获得的第一热波值为退火前对应所述监控晶圆表面多个不同位置测量得到的热波值的平均值,以提高测得的第一热波值的准确性。然后执行本实施例中的监控退火设备控温性能的方法的步骤s3,将所述监控晶圆放入监控的退火设备中,并在设定温度下进行退火。本实施例中,退火工艺的设定温度可以根据需要选择,本实施例的监控退火设备控温性能的方法中,设定的退火稳定可以选择低温范围,例如400度至600度,以应对低温退火时退火设备的控温能力难以利用方阻测量方法准确监控的问题。当然,设定温度宜包含在获得对应线性关系的实验温度区间内。此外,除了设定温度,退火过程的其它参数可以设定为与获得对应线性关系时的参数一致。在完成退火过程后,接着执行本实施例中的监控退火设备控温性能的方法的步骤s4,取出所述监控晶圆,并测量退火后的所述监控晶圆的热波,得到第二热波值。类似的,获得线性关系时或者利用所述线性关系进行监控时,获得的第二热波值也优选为退火前对应所述监控晶圆表面多个不同位置测量得到的热波值的平均值。然后可以执行本实施例中的监控退火设备控温性能的方法的步骤s5,计算第一热波值和第二热波值的差值。在步骤s1提供的监控晶圆在退火前后的热波变化量与退火温度之间的线性关系中,第一热波值和第二热波值的差值可以作为因变量y1。获得监控晶圆在退火前后的热波差值后,接着执行本实施例中的监控退火设备控温性能的方法的步骤s6,利用获得的退火前后的热波变化量与退火温度之间具有的线性关系线性关系,得到与第一热波值和第二热波值的差值对应的实际退火温度。根据已知的退火前后的热波变化量与实际退火温度之间的线性关系,将第一热波值和第二热波值的差值y1带入线性关系的公式中,可以求得自变量x1,即获得了实际的退火温度。在得到了监控的退火设备的设定温度和实际退火温度后,即可得到二者的偏离程度,因此可执行本实施例中的监控退火设备控温性能的方法的步骤s7,通过所述设定温度与实际退火温度的偏离程度,判断监控的退火设备的控温性能。根据产品的质量要求不同,设定温度与实际退火温度之间有一允许的偏离范围,若位于此偏离范围内,可以认为退火设备的控温性能满足要求,其中,设定温度与实际退火温度之间的偏差绝对值越小,退火设备在低温退火时控温的准确性越高;若设定温度与实际退火温度之间的偏离值不在允许的偏离范围内,则认为退火设备的控温性能不满足要求,退火设备在低温退火时控温的准确性较差,需要进行维修或更换。本发明实施例利用监控晶圆在退火前后的热波变化量与退火温度之间的线性关系,可以对快速退火设备的控温的准确性实现监控。优选的,上述方法中,还可以通过测量监控晶圆上不同位置的多个热波值以及获得低反射率来进一步综合判断其控温性能。具体来说,上述方法还可包括以下两方面的判断依据。一方面,根据退火前和退火后在所述监控晶圆表面多个不同位置测量获得的多个第一热波值和第二热波值,测定所述多个第一热波值和第二热波值在晶圆上分布的均匀性,例如,通过计算所述多个第一热波值和第二热波值的方差来衡量其分布的均匀性,从而监控退火设备的加热均匀性也即控温的均匀性。另一方面,低反射率是晶圆在进行快速热退火工艺时的一个重要参数。其中,监控晶圆例如具有正面和背面,上述离子注入例如是对监控晶圆的正面进行操作,在例如一种监控的退火设备中,包括两个温度探测头,且均设置于退火晶圆的背面一侧,在退火过程中利用辐射式测温方式进行测温。通过在退火晶圆背面沉积低反射层,在执行退火工艺后,从退火设备的日志文件(生产工艺文件)中可以获得该退火工艺中的低反射率的具体值。如果低反射率过低,则会反映出这两个温度探测头之间的温差过大,从而表明快速退火设备的温度波动过大,控温的稳定性差。为了获得所述低反射率,可以在进行离子注入之前,在所述监控晶圆的背面形成低反射层。本实施例中,所述低反射层例如包括在所述监控晶圆背面依次叠加形成的氧化层和多晶硅层,其中,所述氧化层例如为氧化硅,厚度为800埃至1200埃,更具体的,可以为1000埃;所述多晶硅层的厚度为1500埃至2000埃,更具体的,可以为1800埃。形成所述低反射层的方法可包括如下过程:利用炉管工艺的热氧化法在监控晶圆的正面和背面均形成氧化硅;然后,同样地采用炉管工艺在监控晶圆的正面和背面均沉积多晶硅;接着通过例如干法刻蚀去除位于监控晶圆正面的氧化硅层和多晶硅层,获得只位于所述监控晶圆背面的低反射层。本领域技术人员也可通过其他材料或方法在监控晶圆背面形成上述低反射层。并在退火后,从退火设备的日志文件获取所述退火设备中记录的低反射率,以评估退火设备控温性能的稳定性。本发明实施例提供的监控退火设备控温性能的方法,根据监控晶圆在退火前后的热波变化量与退火温度之间具有的线性关系对退火设备在退火时的控温性能进行监控,根据设定温度与实际退火温度的偏离程度大小即可判断出控温性能的好坏,相对于测量监控晶圆的方块电阻的监控方式,在低温退火时尤其具有优势,可以提高监控的有效性和准确性;此外,利用退火前和退火后测量的多个热波值在晶圆上的分布,可以监控退火设备加热的均匀性;利用对低反射率的监控,可以监控退火设备控温性能的稳定性。通过本发明实施例提供的监控退火设备控温性能的方法,可以对退火设备的控温性能(尤其是低温退火下的控温性能,例如400度至600度)进行较为全面、有效、准确地监控。上述仅为本发明的优选实施例,并非对本发明权利范围的限定。任何本领域
技术领域:
的技术人员,在不脱离本发明的精神和范围内,都可以对本发明揭露的技术方案和技术内容做任何形式的等同替换或修改等变动。因此,凡是未脱离本发明技术方案的内容,依据本发明的技术实质对以上实施例所作的任何简单修改、等同变化及修饰,均属于本发明的保护范围之内。当前第1页12