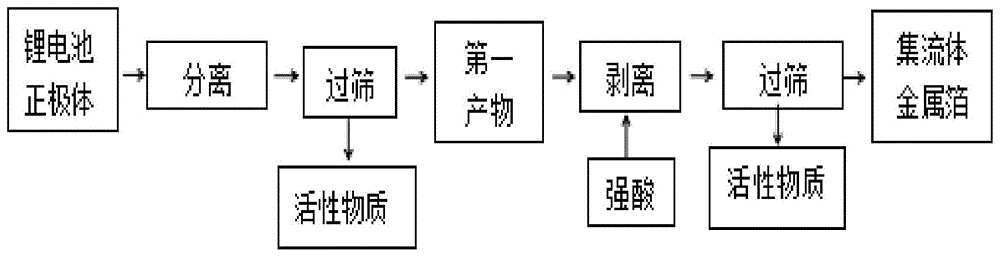
本发明涉及化学材料回收利用的
技术领域:
,尤其涉及一种分离装置、剥离装置以及电池正极的回收方法。
背景技术:
:当今社会,以锂离子电池为动力的手机、手提电脑、玩具等各种便携式电器被广泛使用。这些电池或电器的报废将产生大量废旧锂离子电池,如若不对其回收处理将成为新的环境污染源。同时,对资源也是一种极大浪费。锂离子电池一般由外壳、正极、隔膜、负极、电解质组成。外壳常为不锈钢、正极由约90%的正极活性物质钴酸锂、锰酸锂或是镍钴锰酸锂、乙炔黑导电剂用有面黏合剂如pvdf(聚偏氟乙烯)均匀混合后,涂布于集流体上构成,负极则是采用插锂碳材料天然石墨涂覆于集流体铝/铜箔构成。如果对其有价成分进行回收,需要对正极进行剥离,使活性物质与集流体进行分离,方便后续的回收处理。目前市场上的锂电池正极一般为极片料或粉料,回收时,粉料经过破碎处理但其中夹杂集流体较多,处理难且复杂。技术实现要素:本发明的目的在于提供一种分离装置、剥离装置。为实现以上目的,本发明还提供一种电池正极的回收方法。本发明通过以下技术方案实现:一种分离装置,其结构包括筛分装置和接料装置;所述筛分装置为底面带筛孔的容器或者带筛孔的平板;所述筛分装置与所述接料装置可拆卸连接,且所述筛分装置位于所述接料装置的上方,所述接料装置的开口对应所述筛分装置带筛孔的底面或平板。进一步的,所述筛分装置筛孔尺寸为10~40目。进一步的,所述筛分装置与所述接料装置连接的方式包括螺纹连接、卡接等。进一步的,所述分离装置采用耐高温的材料制成,如不锈钢等。一种剥离装置,其结构包括反应槽和至少一个喷射装置;所述喷射装置设置在所述反应槽的侧壁和/或其中一个端头的内壁;所述喷射装置的喷射口朝向所述反应槽内,流体接入口朝向所述反应槽外。进一步的,所述剥离装置采用耐高温耐腐蚀的材料制成,如不锈钢等。进一步的,所述反应槽为长方体形或者圆柱体形;所述长方体的长宽高的比例为7:1:1;所述圆柱体的长度和直径的比例为7:1。进一步的,所述喷射装置在反应槽内的分布密度为70~90个/平方米;优选分布密度为81个/平方米。进一步的,所述喷射口的内径为1~2mm,喷射压力≥6mpa。进一步的,所述喷射装置设置在端头时,其流体喷出方向与所述端头的内壁垂直;所述喷射装置设置在侧壁时,其流体喷出方向朝向所述反应槽无喷射装置的另一个端头,且与侧壁呈15~45度斜角。一种电池正极的回收方法,包括以下操作:分离:将活性物质和集流体初步分离,产物包括第一产物;剥离:对第一产物进一步剥离。进一步的,所述分离操作包括:将电池正极置于分离装置上,高温烘烤,实现融化黏合剂及电解液的目的,筛分融化的液体和固体,实现初步分离。分离操作分别得到活性物质与第一产物;活性物质包括钴酸锂、锰酸锂或镍钴锰酸锂,第一产物需要进一步处理。进一步的,所述烘烤过程中同时振动分离装置,加速分离。所述振动操作采用市售的振动装置,任意震动参数均可。进一步的,所述高温烘烤的温度为200~450℃。进一步的,所述高温烘烤的时间为:1~4小时。进一步的,所述剥离操作包括:冲击和酸浸泡。进一步的,所述剥离操作具体包括:加水加酸,调节ph值;将第一产物置于剥离装置内;冲击、搅拌。进一步的,所述剥离操作中,所述第一产物不经冷却,在200~450℃高温时直接置于剥离装置内进行剥离操作。进一步的,所述冲击为高速流体冲击。进一步的,所述流体冲击压力≥6mpa。进一步的,所述酸浸泡采用强酸,维持ph值≦4.5。进一步的,搅拌反应时间为1~4小时。进一步的,所述电池正极的回收方法还包括固液分离,具体操作为:剥离操作后,进行10~40目过筛,所得固体物质(即第二产物)为集流体金属箔,所得反应液体中包括钴酸锂、锰酸锂或镍钴锰酸锂。本发明的有益效果:本发明的分离装置中,所述筛分装置与所述接料装置可拆卸连接,可拆卸的性质方便加料取料,同时其固定为一体时又能防止振动时接料装置中的液体溅出。本发明的剥离装置利用流体冲击力,可连续性作业,筛上物会随着水流向另一端汇集,在没有喷射嘴的一端可进行出料操作。通常情况下,如果只利用单个因素控制总冲击力,则必然对该单个因素有更加精准的要求,本发明的剥离装置通过反应槽的长度和宽度以及喷射压力,多方联合控制了流体对第一产物以及酸溶液的总冲击力,使对装置的要求更低,节约了生产成本。本发明的剥离装置的喷射装置的分布密度是即是冲击点的密度,在如此小而密的冲击点的冲击下,正极金属箔上的再细小杂物、贴合得再紧密的杂物也能得到很好的剥离。本发明的回收方法工艺流程短,设备简单,剥离率高,且生产过程中不增加副产物,剥离出来的集流体纯净几乎不夹杂其他金属成分、电解液等,方便后续的回收处理。本发明方法,利用喷射装置口径的设置形成冲击点,更利于精细物质的剥离。本发明方法选择用流体冲击,具有更好的渗透力和清洁力,可以更好的使较精细的结构和较紧密连接处实现解体,同时起到清洁表面的作用。附图说明为了更清楚地说明本发明实施例的技术方案,下面将对实施例中所需要使用的附图作简单地介绍,应当理解,以下附图仅示出了本发明的某些实施例,因此不应被看作是对本发明范围的限定。图1为本发明锂离子电池正极的回收方法的工艺流程图。图2为本发明的分离装置的一种实施例的结构示意图。图3为本发明的剥离装置的一种实施例的结构示意图;其中图3a为侧视图;图3b为俯视图。图4为本发明的剥离装置侧壁上的喷射装置的两种分布示意图,分别为图4a和图4b所示。标号说明:01、筛分装置;02、接料装置;03、剥离装置;031、喷射装置;032、反应槽;0321、侧壁。具体实施方式如本文所用之术语:“由……制备”与“包含”同义。本文中所用的术语“包含”、“包括”、“具有”、“含有”或其任何其它变形,意在覆盖非排它性的包括。例如,包含所列要素的组合物、步骤、方法、制品或装置不必仅限于那些要素,而是可以包括未明确列出的其它要素或此种组合物、步骤、方法、制品或装置所固有的要素。连接词“由……组成”排除任何未指出的要素、步骤或组分。如果用于权利要求中,此短语将使权利要求为封闭式,使其不包含除那些描述的材料以外的材料,但与其相关的常规杂质除外。当短语“由……组成”出现在权利要求主体的子句中而不是紧接在主题之后时,其仅限定在该子句中描述的要素;其它要素并不被排除在作为整体的所述权利要求之外。当量、浓度、或者其它值或参数以范围、优选范围、或一系列上限优选值和下限优选值限定的范围表示时,这应当被理解为具体公开了由任何范围上限或优选值与任何范围下限或优选值的任一配对所形成的所有范围,而不论该范围是否单独公开了。例如,当公开了范围“1~5”时,所描述的范围应被解释为包括范围“1~4”、“1~3”、“1~2”、“1~2和4~5”、“1~3和5”等。当数值范围在本文中被描述时,除非另外说明,否则该范围意图包括其端值和在该范围内的所有整数和分数。“和/或”用于表示所说明的情况的一者或两者均可能发生,例如,a和/或b包括(a和b)和(a或b)。本发明提供一种分离装置,如图2所示为本发明的分离装置的其中一种实施例的结构示意图,其结构包括筛分装置01和接料装置02;所述筛分装置01为底面带筛孔的容器或者带筛孔的平板;所述筛分装置01与所述接料装置02可拆卸连接,且所述筛分装置01位于所述接料装置02的上方,所述接料装置02的开口对应所述筛分装置01带筛孔的底面或平板。在一些实施例中,所述筛分装置01筛孔尺寸为10~40目。在一些实施例中,所述筛分装置01与所述接料装置02连接的方式包括螺纹连接、卡接等。在一些实施例中,所述分离装置采用耐高温的材料制成,如不锈钢等。本发明还提供一种剥离装置03,如图3所示为本发明的剥离装置03的其中一种实施例的结构示意图;其中图3a为侧视图;图3b为俯视图,其结构包括反应槽032和至少一个喷射装置031;所述喷射装置031设置在所述反应槽032的侧壁0321和/或其中一个端头的内壁;所述喷射装置031的喷射口朝向所述反应槽032内,流体接入口朝向所述反应槽032外。在一些实施例中,所述剥离装置03采用耐高温耐腐蚀的材料制成,如不锈钢等。在一些实施例中,所述反应槽032为长方体形或者圆柱体形;所述长方体的长宽高的比例为7:1:1;所述圆柱体的长度和直径的比例为7:1。在一些实施例中,所述喷射装置031在反应槽032内的分布密度为70~90个/平方米;优选分布密度为81个/平方米。在一些实施例中,所述喷射口的内径为1~2mm,喷射压力≥6mpa。喷射口径的设置形成冲击点,更利于精细物质的剥离。在一些实施例中,所述喷射装置031设置在端头时,其流体喷出方向与所述端头的内壁垂直;所述喷射装置031设置在侧壁0321时,其流体喷出方向朝向所述反应槽032无喷射装置031的另一个端头,且与侧壁0321呈15~45度斜角。参见图3和图4,在一些实施例中,所述喷射装置031设置在侧壁0321时,其排布方式多种多样,可以是均匀分布(例如图3a),也可以是按一定图形分布(例如图4a),还可以是不均匀的弥散性分布(例如图4b)等。本发明提供一种锂离子电池正极的回收方法,包括以下操作:分离:将活性物质和集流体初步分离,产物包括第一产物;剥离:对第一产物进一步剥离。如图1的流程图所示:在一些实施例中,所述分离操作包括:将电池正极置于分离装置上,高温烘烤,实现融化黏合剂及电解液的目的,筛分融化的液体和固体,实现初步分离。分离操作分别得到活性物质与第一产物;活性物质包括钴酸锂、锰酸锂或镍钴锰酸锂,第一产物需要进一步处理。在一些实施例中,所述烘烤过程中同时振动分离装置,加速分离。所述振动操作采用市售的振动装置,任意震动参数均可。在一些实施例中,所述高温烘烤的温度为200~450℃。在一些实施例中,所述高温烘烤的时间为:1~4小时。在一些实施例中,所述剥离操作包括:冲击和酸浸泡。在一些实施例中,所述剥离操作具体包括:加水加酸,调节ph值;将第一产物置于剥离装置03内;冲击、搅拌。在一些实施例中,所述剥离操作中,所述第一产物不经冷却,在200~450℃高温时直接置于剥离装置03内进行剥离操作。骤冷可以加速活性物质和集流体分离。在一些实施例中,所述冲击为高速流体冲击。本操作以额外施加的冲击力加速第一产物的进一步解体,同时对酸浸泡起到搅拌作用,加速酸的作用。在一些实施例中,所述流体冲击压力≥6mpa。在一些实施例中,所述酸浸泡采用强酸,维持ph值≦4.5。本方法通过循环使用反应槽032内的酸溶液,即将反应槽032内的酸溶液抽回再经喷射装置031喷射到反应槽032内的方式,维持反应槽032内酸溶液的ph值在一定范围内不变,加速活性物质和集流体的分离,实现两者的彻底分离。在一些实施例中,搅拌反应时间为1~4小时。在一些实施例中,所述锂离子电池正极的回收方法还包括固液分离,具体操作为:剥离操作后,进行10~40目过筛,所得固体物质(即第二产物)为集流体金属箔,所得反应液体中包括钴酸锂、锰酸锂或镍钴锰酸锂。下面将结合具体实施例对本发明的实施方案进行详细描述,但是本领域技术人员将会理解,下列实施例仅用于说明本发明,而不应视为限制本发明的范围。实施例中未注明具体条件者,按照常规条件或制造商建议的条件进行。所用试剂或仪器未注明生产厂商者,均为可以通过市售购买获得的常规产品。实施例1采用本发明的回收方法对电池正极进行回收原料:以铝箔为集流体的锂电池正极极片料,分析检测其成分为:co含量4.83%,ni含量15.19%,mn含量8.46%,li含量3.82%,al含量17.13%。回收方法:分离:将锂电池正极置于40目的分离装置的筛分装置01中,在220℃温度下烘2小时每一小时将料盘振动筛分一次,融化的流体通过筛孔落在与筛分装置01卡接的接料装置02中,留在筛分装置01上的为第一产物。剥离:剥离装置03为一个长宽高的比例为7:1:1的长方形槽型装置,所述喷射装置031在反应槽032内的分布密度为70个/平方米,喷射装置031喷射口的内径为1.5mm,喷射方向与侧壁0321呈30度斜角;所述剥离装置03外接有水循环装置。剥离装置03的反应槽032内装入常温水,加入硫酸,调节ph值为1.5,开启水循环装置和喷射装置031,控制喷射压为6mpa。加入刚分离得到的第一产物,反应2小时。进行40目过筛得筛上的固体物质(即第二产物)和筛下的反应液。取两次筛下物综合样检测结果:al含量0.13%;剥离后筛上的固体物质(即第二产物)为片状铝箔,表面少量附着物,分析检测其组成及含量为:co含量0.030%,ni含量0.019%,mn含量0.046%,li含量0.011%,al含量99.13%。实施例2采用本发明的回收方法对电池正极进行回收原料:以铝箔为集流体的锂电池正极极片料,分析检测其成分为:co含量4.83%,ni含量15.19%,mn含量8.46%,li含量3.82%,al含量17.13%。回收方法:分离:将锂电池正极置于30目的分离装置的筛分装置01中,在250℃温度下烘2小时每一小时将料盘振动筛分一次,融化的流体通过筛孔落在与筛分装置01卡接的接料装置02中,留在筛分装置01上的为第一产物。剥离:剥离装置03为一个长宽高的比例为7:1:1的长方形槽型装置,所述喷射装置031在反应槽032内的分布密度为90个/平方米,喷射装置031喷射口的内径为1mm,喷射方向与侧壁0321呈45度斜角;所述剥离装置03外接有水循环装置。剥离装置03的反应槽032内装入常温水,加入硫酸,调节ph值为4.5,开启水循环装置和喷射装置031,控制喷射压为7.5mpa。加入刚分离得到的第一产物,反应4小时。进行10目过筛得筛上的固体物质(即第二产物)和筛下的反应液。取两次筛下物综合样检测结果:al含量0.017%;剥离后筛上的固体物质(即第二产物)为片状铝箔,表面少量附着物,分析检测其组成及含量为:co含量0.011%,ni含量0.013%,mn含量0.022%,li含量0.017%,al含量99.21%。实施例3采用本发明的回收方法对电池正极进行回收原料:以铝箔为集流体的锂电池正极极片料,分析检测其成分为:co含量4.83%,ni含量15.19%,mn含量8.46%,li含量3.82%,al含量17.13%。回收方法:分离:将锂电池正极置于10目的分离装置的筛分装置01中,在200℃温度下烘4小时每一小时将料盘振动筛分一次,融化的流体通过筛孔落在与筛分装置01卡接的接料装置02中,留在筛分装置01上的为第一产物。剥离:剥离装置03为一个长度和直径的比例为7:1的圆柱体槽型装置,所述喷射装置031在反应槽032内的分布密度为84个/平方米,喷射装置031喷射口的内径为2mm,喷射方向与侧壁0321呈15度斜角;所述剥离装置03外接有水循环装置。剥离装置03的反应槽032内装入常温水,加入硫酸,调节ph值为3,开启水循环装置和喷射装置031,控制喷射压为6mpa。加入刚分离得到的第一产物,反应1小时。进行30目过筛得筛上的固体物质(即第二产物)和筛下的反应液。取两次筛下物综合样检测结果:al含量0.017%;剥离后筛上的固体物质(即第二产物)为片状铝箔,表面少量附着物,分析检测其组成及含量为:co含量0.15%,ni含量0.17%,mn含量0.24%,li含量0.09%,al含量98.32%。实施例4采用本发明的回收方法对电池正极进行回收原料:以铝箔为集流体的锂电池正极极片料,分析检测其成分为:co含量4.83%,ni含量15.19%,mn含量8.46%,li含量3.82%,al含量17.13%。回收方法:分离:将锂电池正极置于40目的分离装置的筛分装置01中,在200℃温度下烘4小时每一小时将料盘振动筛分一次,融化的流体通过筛孔落在与筛分装置01卡接的接料装置02中,留在筛分装置01上的为第一产物。剥离:剥离装置03为一个长宽高的比例为7:1:1的长方形槽型装置,所述喷射装置031在反应槽032内的分布密度为81个/平方米,喷射装置031喷射口的内径为1.5mm,喷射方向与侧壁0321呈30度斜角;所述剥离装置03外接有水循环装置。剥离装置03的反应槽032内装入常温水,加入硫酸,调节ph值为1.5,开启水循环装置和喷射装置031,控制喷射压为6.5mpa。加入刚分离得到的第一产物,反应4小时。进行40目过筛得筛上的固体物质(即第二产物)和筛下的反应液。取两次筛下物综合样检测结果:al含量0.019%;剥离后筛上的固体物质(即第二产物)为片状铝箔,表面少量附着物,分析检测其组成及含量为:co含量0.11%,ni含量0.13%,mn含量0.19%,li含量0.11%,al含量98.77%。实施例5采用本发明的回收方法对电池正极进行回收原料:以铝箔为集流体的锂电池正极极片料,分析检测其成分为:co含量4.83%,ni含量15.19%,mn含量8.46%,li含量3.82%,al含量17.13%。回收方法:分离:将锂电池正极置于40目的分离装置的筛分装置01中,在350℃温度下烘4小时每一小时将料盘振动筛分一次,融化的流体通过筛孔落在与筛分装置01卡接的接料装置02中,留在筛分装置01上的为第一产物。剥离:剥离装置03为一个长度和直径的比例为7:1的圆柱体槽型装置,所述喷射装置031在反应槽032内的分布密度为75个/平方米,喷射装置031喷射口的内径为1.8mm,喷射方向与侧壁0321呈35度斜角;所述剥离装置03外接有水循环装置。剥离装置03的反应槽032内装入常温水,加入硫酸,调节ph值为1.5,开启水循环装置和喷射装置031,控制喷射压为6.5mpa。加入刚分离得到的第一产物,反应4小时。进行40目过筛得筛上的固体物质(即第二产物)和筛下的反应液。取两次筛下物综合样检测结果:al含量0.057%;剥离后筛上的固体物质(即第二产物)为片状铝箔,表面少量附着物,分析检测其组成及含量为:co含量0.011%,ni含量0.013%,mn含量0.022%,li含量0.009%,al含量99.21%。实施例6采用本发明的回收方法对电池正极进行回收原料:以铝箔为集流体的锂电池正极极片料,分析检测其成分为:co含量4.83%,ni含量15.19%,mn含量8.46%,li含量3.82%,al含量17.13%。回收方法:分离:将锂电池正极置于40目的分离装置的筛分装置01中,在400℃温度下烘4小时每一小时将料盘振动筛分一次,融化的流体通过筛孔落在与筛分装置01卡接的接料装置02中,留在筛分装置01上的为第一产物。剥离:剥离装置03为一个长度和直径的比例为7:1的圆柱体槽型装置,所述喷射装置031在反应槽032内的分布密度为70个/平方米,喷射装置031喷射口的内径为1mm,喷射方向与侧壁0321呈45度斜角;所述剥离装置03外接有水循环装置。剥离装置03的反应槽032内装入常温水,加入硫酸,调节ph值为1.5,开启水循环装置和喷射装置031,控制喷射压为7.0mpa。加入刚分离得到的第一产物,反应4小时。进行25目过筛得筛上的固体物质(即第二产物)和筛下的反应液。取两次筛下物综合样检测结果:al含量0.007%;剥离后筛上的固体物质(即第二产物)为片状铝箔,表面少量附着物,分析检测其组成及含量为:co含量0.0019%,ni含量0.0014%,mn含量0.0024%,li含量0.0011%,al含量99.57%。实施例7采用本发明的回收方法对电池正极进行回收原料:以铝箔为集流体的锂电池正极极片料,分析检测其成分为:co含量4.83%,ni含量15.19%,mn含量8.46%,li含量3.82%,al含量17.13%。回收方法:分离:将锂电池正极置于40目的分离装置的筛分装置01中,在450℃温度下烘1.5小时每一小时将料盘振动筛分一次,融化的流体通过筛孔落在与筛分装置01卡接的接料装置02中,留在筛分装置01上的为第一产物。剥离:剥离装置03为一个长宽高的比例为7:1:1的长方形槽型装置,所述喷射装置031在反应槽032内的分布密度为85个/平方米,喷射装置031喷射口的内径为1.5mm,喷射方向与侧壁0321呈20度斜角;所述剥离装置03外接有水循环装置。剥离装置03的反应槽032内装入常温水,加入硫酸,调节ph值为3,开启水循环装置和喷射装置031,控制喷射压为7.0mpa。加入刚分离得到的第一产物,反应4小时。进行40目过筛得筛上的固体物质(即第二产物)和筛下的反应液。取两次筛下物综合样检测结果:al含量0.019%;剥离后筛上的固体物质(即第二产物)为片状铝箔,表面少量附着物,分析检测其组成及含量为:co含量0.0083%,ni含量0.0077%,mn含量0.0093%,li含量0.0010%,al含量99.27%。实施例8采用本发明的回收方法对电池正极进行回收原料:以铝箔为集流体的锂电池正极极片料,分析检测其成分为:co含量4.83%,ni含量15.19%,mn含量8.46%,li含量3.82%,al含量17.13%。回收方法:分离:将锂电池正极置于40目的分离装置的筛分装置01中,在450℃温度下烘2小时每一小时将料盘振动筛分一次,融化的流体通过筛孔落在与筛分装置01卡接的接料装置02中,留在筛分装置01上的为第一产物。剥离:剥离装置03为一个长度和直径的比例为7:1的圆柱体槽型装置,所述喷射装置031在反应槽032内的分布密度为70个/平方米,喷射装置031喷射口的内径为1.5mm,喷射方向与侧壁0321呈30度斜角;所述剥离装置03外接有水循环装置。剥离装置03的反应槽032内装入常温水,加入硫酸,调节ph值为1.5,开启水循环装置和喷射装置031,控制喷射压为7.5mpa。加入刚分离得到的第一产物,反应4小时。进行40目过筛得筛上的固体物质(即第二产物)和筛下的反应液。取两次筛下物综合样检测结果:al含量0.037%;剥离后筛上的固体物质(即第二产物)为片状铝箔,表面少量附着物,分析检测其组成及含量为:co含量0.047%,ni含量0.059%,mn含量0.082%,li含量0.013%,al含量99.22%。实施例9采用本发明的回收方法对电池正极进行回收原料:以铝箔为集流体的锂电池正极极片料,分析检测其成分为:co含量4.83%,ni含量15.19%,mn含量8.46%,li含量3.82%,al含量17.13%。回收方法:分离:将锂电池正极置于40目的分离装置的筛分装置01中,在450℃温度下烘4小时每一小时将料盘振动筛分一次,融化的流体通过筛孔落在与筛分装置01卡接的接料装置02中,留在筛分装置01上的为第一产物。剥离:剥离装置03为一个长宽高的比例为7:1:1的长方形槽型装置,所述喷射装置031在反应槽032内的分布密度为70个/平方米,喷射装置031喷射口的内径为1.5mm,喷射方向与侧壁0321呈30度斜角;所述剥离装置03外接有水循环装置。剥离装置03的反应槽032内装入常温水,加入硫酸,调节ph值为1.5,开启水循环装置和喷射装置031,控制喷射压为6.5mpa。加入刚分离得到的第一产物,反应2小时。进行40目过筛得筛上的固体物质(即第二产物)和筛下的反应液。取两次筛下物综合样检测结果:al含量0.029%;剥离后筛上的固体物质(即第二产物)为片状铝箔,表面少量附着物,分析检测其组成及含量为:co含量0.013%,ni含量0.032%,mn含量0.074%,li含量0.0087%,al含量99.30%。对比例采用常规的回收方法对电池正极进行回收原料:以铝箔为集流体的锂电池正极极片料,分析检测其成分为:co含量4.83%,ni含量15.19%,mn含量8.46%,li含量3.82%,al含量17.13%。回收方法:对比例1-8使用的是传统的处理方法:将上述原料利用带分级和收尘的破碎机,采用机械破碎的方式,将物料粉碎。再经过重力分级和收尘,分别得集流体(铝箔)和活性物质。其中,对比例1-4控制破碎机进料速度为500kg/小时,引风风门打开1/4。通过破碎分级收尘得到的物料;对比例5-8控制破碎机进料速度为1000kg/小时,引风风门3/4打开。通过破碎分级收尘得到的物料。检测结果对比:1、收集除剥离得到的集流体(铝箔)以外的活性物质(相当于实施例1-9的两次筛下物综合样),进行成分检测,结果见表1:表1:活性物质中铝含量编号铝含量编号铝含量对比例12.01%实施例10.13%对比例22.68%实施例20.017%对比例31.77%实施例30.017%对比例42.33%实施例40.019%对比例54.93%实施例50.057%对比例63.87%实施例60.007%对比例72.41%实施例70.019%对比例83.47%实施例80.037%实施例90.029%均值2.93%0.037%2、回收得到的集流体(铝箔)的成分分析数据(与表1的编号对应),见表2所示,表3为实施例1-9回收得到的集流体(铝箔)的成分分析数据汇总。表2:对比例回收得到的集流体(铝箔)的成分及含量表3:实施例1-9回收的集流体(铝箔)的成分及含量。编号conimnlial实施例10.030%0.019%0.046%0.011%99.13%实施例20.011%0.013%0.022%0.017%99.21%实施例30.15%0.17%0.24%0.09%98.32%实施例40.11%0.13%0.19%0.11%98.77%实施例50.011%0.013%0.022%0.009%99.21%实施例60.0019%0.0014%0.0024%0.0011%99.57%实施例70.0083%0.0077%0.0093%0.0010%99.27%实施例80.047%0.059%0.082%0.013%99.22%实施例90.013%0.032%0.074%0.0087%99.30%均值0.042%0.049%0.076%0.029%99.11%通过表2和表3的对比,可以看出:本发明回收方法回收的集流体(铝箔)杂质少,铝元素丢失少,平均含量超过99%。最后应说明的是:以上各实施例仅用以说明本发明的技术方案,而非对其限制;尽管参照前述各实施例对本发明进行了详细的说明,本领域的普通技术人员应当理解:其依然可以对前述各实施例所记载的技术方案进行修改,或者对其中部分或者全部技术特征进行等同替换;而这些修改或者替换,并不使相应技术方案的本质脱离本发明各实施例技术方案的范围。此外,本领域的技术人员能够理解,尽管在此的一些实施例包括其它实施例中所包括的某些特征而不是其它特征,但是不同实施例的特征的组合意味着处于本发明的范围之内并且形成不同的实施例。例如,在上面的权利要求书中,所要求保护的实施例的任意之一都可以以任意的组合方式来使用。公开于该
背景技术:
部分的信息仅仅旨在加深对本发明的总体
背景技术:
的理解,而不应当被视为承认或以任何形式暗示该信息构成已为本领域技术人员所公知的现有技术。当前第1页12