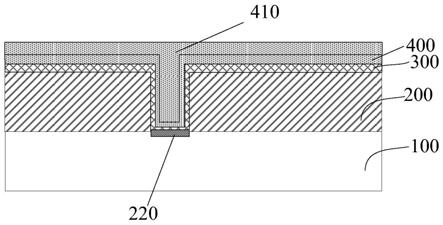
[0001]
本发明涉及半导体制造技术领域,尤其涉及一种半导体器件的形成方法。
背景技术:[0002]
随着半导体制造技术的飞速发展,半导体器件朝着更高的元件密度,以及更高的集成度的方向发展。器件作为最基本的半导体器件,目前正被广泛应用,传统的平面器件对沟道电流的控制能力变弱,产生短沟道效应而导致漏电流,最终影响半导体器件的电学性能。
[0003]
在半导体器件的制作过程中,需要在晶体管的源区、漏区或栅极结构等上形成接触孔,然后在接触孔内填充金属层,以形成金属插塞,以使晶体管等元件通过金属插塞与互联金属层形成电连接。但是目前形成的金属层与接触孔之间的具有较差的成形质量。
[0004]
如何使得金属层与接触孔之间具有较好的成形质量,从而保证形成的半导体器件具有良好的性能,这是目前急需解决的问题。
技术实现要素:[0005]
本发明解决的问题是提供一种半导体器件的形成方法,使得形成的金属层与接触孔之间具有较好的成形质量,保证形成的半导体器件具有良好的性能和良率。
[0006]
为解决上述问题,本发明提供一种半导体器件的形成方法,包括:提供基底,所述基底上具有层间介质层;刻蚀所述层间介质层形成接触孔,所述接触孔暴露出所述基底表面;在所述接触孔的底部和侧壁上形成粘附层;采用选择性生长法在所述粘附层的底部和侧壁上形成金属籽层;在所述金属籽层上形成金属层,所述金属层填充满所述接触孔。
[0007]
可选的,所述选择性生长法的工艺参数包括:有机源为codcp,反应气体包括氢气、氨气以及氩气,其中氢气的气体流量为1000~8000sccm、氨气的气体流量为1000~5000sccm以及氩气的气体流量为10~500sccm;源射频功率为100~2000瓦、温度为100~400℃、压强为10~40托。
[0008]
可选的,所述金属籽层的材料为钴。
[0009]
可选的,所述金属层的材料为钴。
[0010]
可选的,采用电化学镀的方法形成所述金属层。
[0011]
可选的,所述粘附层为单层粘附层或叠层粘附层。
[0012]
可选的,当所述粘附层为叠层粘附层时,所述叠层粘附层包括反应金属层和第一扩散阻挡层,形成所述叠层粘附层的步骤包括:在所述接触孔的底部和侧壁上形成所述反应金属层;在所述反应金属层上形成所述第一扩散阻挡层。
[0013]
可选的,形成所述第一扩散阻挡层之后,还包括:在所述第一扩散阻挡层上形成第二扩散阻挡层。
[0014]
可选的,当所述粘附层为单层粘附层时,所述单层粘附层的材料为钨或钽或钛。
[0015]
可选的,当所述单层粘附层的材料为钨或钽时,在形成所述单层粘附层之前,还包
括:在所述接触孔内的所述基底上形成硅化层。
[0016]
可选的,当所述单层粘附层的材料为钛时,在形成所述金属层之后,还包括:在所述接触孔内的所述基底上形成硅化层。
[0017]
可选的,形成所述单层粘附层方法为原子层气相沉积法。
[0018]
与现有技术相比,本发明的技术方案具有以下优点:
[0019]
采用选择性生长法在接触孔的底部和侧壁上形成金属籽层,使得形成的金属籽层能够很好的粘附在粘附层上,在金属籽层上形成金属层的时候,金属籽层与粘附层之间不会发生剥离,从而避免形成金属层的过程中,出现孔洞的缺陷,保证形成的金属层与接触孔之间具有较好的成形质量,使得形成的半导体器件的性能和良率得到提高。这是由于选择性生长法形成的金属籽层表面具有与粘附层表面相似的性质,在形成金属籽层的时候,粘附层表面会形成吸附金属籽层的作用力,不仅使得金属籽层更容易填入到接触孔的底部,形成附着质量好的金属籽层,而且金属籽层与粘附层之间的作用粘附力强,两者之间不易发生剥离,从而在形成金属层的过程中,不会出现由于金属籽层与粘附之间发生剥离而产生孔洞的缺陷,保证了形成的半导体器件具有较高的质量和性能稳定性。
附图说明
[0020]
图1至图5是一实施例中半导体器件形成过程的结构示意图;
[0021]
图6至图10是本发明第一实施例中半导体器件形成过程的结构示意图;
[0022]
图11至图14是本发明第二实施例中半导体器件形成过程的结构示意图;
[0023]
图15至图18是本发明第三实施例中半导体器件形成过程的结构示意图。
具体实施方式
[0024]
在半导体器件的形成过程中,需要在接触孔内填充金属层,以形成金属插塞。但是在形成金属插塞的过程中,金属层与接触孔之间的成形质量差,金属层与接触孔之间内具有孔洞的缺陷,导致半导体器件在使用的过程中容易出现漏电或失效等现象,限制了半导体器件的使用,具体的形成过程参考图1至图5。
[0025]
首先参考图1,提供基底1,所述基底1上形成有层间介质层2。
[0026]
参考图2,刻蚀所述层间介质层2,在所述层间介质层2内形成接触孔3。
[0027]
参考图3,在所述接触孔3的底部、侧壁以及所述层间介质层2的表面依次形成反应金属层4、扩散阻挡层5。
[0028]
所述反应金属层4与所述基底1表面形成硅化层41。
[0029]
参考图4,在接触孔3内的所述扩散阻挡层5上采用物理气相沉积或化学气相沉积的方法形成金属籽层6。
[0030]
参考图5,在接触孔3内的金属籽层6上形成金属层7。
[0031]
发明人发现,这种方法形成的半导体器件的使用性能的稳定性差,容易出现失效等现象,限制了半导体器件的使用。这是由于接触孔3的尺寸较小,在形成金属籽层6的时候,接触孔3内部的结构和内部环境对金属籽层6的作用较强,阻止金属籽层6的沉积,从而导致形成的金属籽层6在扩散阻挡层5上的覆盖效果差,两者之间的粘附力小,后续形成金属层的时候,金属籽层与扩散阻挡层之间容易发生剥离,从而导致形成金属层和接触孔之
间出现孔洞的缺陷,造成形成的半导体器件性能的降低。
[0032]
发明人研究发现,采用选择性生长法在粘附层的底部和侧壁上形成金属籽层,形成的金属籽层与粘附层之间的粘附力强且金属籽层在接触孔的底部和侧壁上的附着效果好,这样保证在形成金属层的过程中,不会在接触孔与金属层之间出现孔洞的缺陷,从而提高形成的半导体器件的质量。
[0033]
为使本发明的上述目的、特征和优点能够更为明显易懂,下面结合附图对本发明的具体实施例做详细地说明。
[0034]
第一实施例
[0035]
图6至图10是本发明第一实施例中半导体器件形成过程的结构示意图。
[0036]
首先参考图6,提供所述基底100,所述基底100上具有层间介质层200。
[0037]
本实施例中,所述基底100包括衬底,以及位于包括所述衬底上存储器件以及逻辑器件等。
[0038]
本实施例中,所述层间介质层200的材料为氧化硅。
[0039]
其他实施例中,所述层间介质层200的材料还可为氮化硅、氮硼化硅、氮碳氧化硅或氮氧化硅等。
[0040]
本实施例中,采用化学气相沉积的方式在所述基底100上形成所述层间介质层200。所述化学气相沉积工艺的工艺参数包括采用的气体包括氧气、氨气(nh3)、和n(sih3)3气体,氧气的流量为20sccm~10000sccm,氨气(nh3)气体的流量为20sccm~10000sccm,n(sih3)3气体的流量为20sccm~10000sccm,腔室压强为0.01~10托,温度为30℃~90℃。
[0041]
参考图7,刻蚀所述层间介质层200,在所述层间介质层200内形成接触孔210,所述接触孔210的底部暴露出所述基底100的表面。
[0042]
本实施例中,采用干法刻蚀工艺形成所述接触孔210;所述干法刻蚀工艺的参数包括:采用的气体包括cf4和ch3f,cf4的流量为20sccm~200sccm,ch3f的流量为20sccm~50sccm,源射频功率为200瓦~500瓦,腔室压强为1torr~10torr。
[0043]
本实施例中,所述接触孔210暴露出所述基底100上的源/漏区;其他实施例中,所述接触孔210还可暴露出所述基底100上的栅极结构等。
[0044]
参考图8,在所述接触孔210的底部和侧壁上形成粘附层,所述粘附层为单层粘附层300。
[0045]
本实施例中,所述单层粘附层300的材料为钨(w);其他实施例中,所述单层粘附层300的材料为钽(ta)。
[0046]
本实施例中,所述单层粘附层300延伸到所述层间介质层200上。
[0047]
本实施例中,采用原子层气相沉积法形成所述单层粘附层300。
[0048]
本实施例中,采用原子层气相沉积法(ald)形成所述单层粘附层300;其他实施例中,还可采用化学气相沉积法(cvd)或者物理气相沉积法(pvd)形成所述单层粘附层300。
[0049]
本实施例中,采用原子层气相沉积法形成所述单层粘附层300的原因是因为原子层气相沉积法形成的所述单层粘附层300具有较高的致密度,这样可以起到提高阻挡离子扩散的作用。
[0050]
本实施例中,由于形成所述单层粘附层300在前驱工艺的作用下表面带有大量的电荷和极性键,这样在后续采用选择性生长法形成所述金属籽层的时候,能够提供一个吸
附所述金属籽层的吸附力,保证在接触孔的底部和侧壁上形成质量好的金属籽层,同时使得所述单层粘附层300与金属籽层之间能够具有较强的粘附力。
[0051]
本实施例中,在形成所述单层粘附层300之前,还包括,在所述接触孔210的底部以及侧壁上形成所述反应金属层(图中未示出)、以及在所述反应金属层上形成扩散阻挡层(图中未示出),利用形成的所述反应金属层与所述基底100反应形成硅化层220,所述硅化层220是在热处理的工艺中形成,形成所述硅化层220之后去除形成的未参加反应的所述反应金属层和所述扩散阻挡层。
[0052]
本实施例中,去除所述反应金属层和所述扩散阻挡层的原因是所述反应金属层和所述扩散阻挡层具有较大的电阻,后续在形成金属层的时候,金属层与接触孔底部的器件之间就会有较大的接触电阻,这样形成的半导体器件在使用的过程中容易出现发热的现象和降低运行速度,从而限制了半导体器件的使用。
[0053]
参考图9,采用选择性生长法在所述单层粘附层300的底部和侧壁上形成所述金属籽层400。
[0054]
本实施例中,所述金属籽层400的材料为钴(co)。
[0055]
本实施例中,所述选择性生长法的工艺参数包括:有机源为codcp,反应气体包括氢气(h2)、氨气(nh3)以及氩气(ar),其中氢气(h2)的流量为1000~8000sccm、氨气(nh3)的流量为1000~5000sccm以及氩气(ar)的气体流量为10~500sccm;源射频功率为100~2000瓦、温度为100~400℃、压强为10~40托。
[0056]
本实施例中,采用选择性生长法使得形成的所述金属籽层400的表面具有大量的极性键或电荷等,同时形成的所述单层粘附层300由于前驱工艺的作用,表面也具有大量的极性键或电荷,这样所述金属籽层400和所述粘附层300表面性质相互吸引,那么在形成所述金属籽层400的时候,所述金属籽层400就容易粘附在所述单层粘附层300上,同时所述单层粘附层300还可在所述金属籽层400填充的时候提供吸附力,使得在所述金属籽层400能够更好的粘附在所述接触孔210的底部和侧壁上,所以形成的所述金属籽层400不仅在所述接触孔210内的具有较高的成形质量,同时由于所述金属籽层400表面与所述单层粘附层300之间具有相似的性质,从而使得两者之间的具有较高的粘附力。
[0057]
本实施例中,所述前驱工艺是在形成所述金属籽层400之前,对各个面进行处理的过程。
[0058]
本实施例中,所述金属籽层400延伸到所述层间介质层200上的所述单层粘附层300上。
[0059]
参考图10,在所述金属籽层400上形成金属层410,所述金属层410填充满所述接触孔210。
[0060]
本实施例中,所述金属层410的材料为钴(co)。
[0061]
本实施例中,由于形成的金属籽层400与所述单层粘附层300之间的粘附力强,在形成金属层410的过程中,所述金属籽层400与所述单层粘附层300之间不易被剥离开,从而保证在形成所述金属层410的过程中,所述金属层410与所述接触孔210之间不会出现孔洞的缺陷,使得形成的半导体器件的性能和良率得到提高。
[0062]
本实施例中,采用电化学镀的方法形成所述金属层410。
[0063]
本实施例中,所述电化学镀方法形成所述金属层410的工艺为常规工艺手段,这里
不再累赘说明。
[0064]
本实施例中,形成所述金属层410之后,再进行退火处理,退火的温度在400℃~450℃。经过退火处理后,在金属层与接触孔接触的界面处形成w/co-w-si/wsi的非晶相作为金属层的扩散阻挡层,不仅阻止离子的扩散,同时由于w/co-w-si/wsi的非晶相的电阻较小,也能使得形成的半导体器件的接触电阻得到降低,提高形成半导体器件的电学性能。
[0065]
本实施例中,形成所述金属层410之后,采用化学机械研磨法平坦化所述金属层410。
[0066]
相应的,利用上述方法形成的一种半导体器件,包括:基底100;层间介质层200,位于所述基底100上;接触孔210,位于所述层间介质层200内,且底部暴露出所述基底100的表面;硅化层220,位于所述接触孔210内的所述基底100上;单层粘附层300,位于所述接触孔210底部和侧壁上;金属籽层400,位于所述接触孔210内的所述单层粘附层300的底部和侧壁上;金属层410,位于所述金属籽层400上,且填充满所述接触孔210。
[0067]
第二实施例
[0068]
图11至图14是本发明第二实施例中半导体器件形成过程的结构示意图。
[0069]
本实施例与第一实施例的差别在于所述粘附层为叠层粘附层。
[0070]
本实施例中,从提供基底到形成接触孔的过程与第一实施例中相同,具体参考图6至图7。
[0071]
参考图11,在所述接触孔的底部和侧壁上形成粘附层500,所述粘附层500为叠层粘附层,所述叠层粘附层的材料包括反应金属层510和第一扩散阻挡层520。
[0072]
本实施例中,形成所述粘附层500的步骤包括:在所述接触孔210的底部和侧壁上形成所述反应金属层510,在所述反应金属层510上形成所述第一扩散阻挡层520。
[0073]
本实施例中,所述反应金属层510的材料为ti;其他实施例中,所述反应金属层510的材料还可为钴或nipt等。
[0074]
本实施例中,所述反应金属层510与所述基底100反应形成硅化层220。
[0075]
本实施例中,采用定向自组装(dsa)工艺形成所述硅化层220。
[0076]
本实施例中,所述第一扩散阻挡层520的材料为tin;其他实施例中,所述扩散阻挡层520的材料还可为tan等。
[0077]
本实施例中,在所述反应金属层510的表面形成所述第一扩散阻挡层520的目的是防止在形成所述硅化层220的过程中,所述反应金属层510被氧化掉,导致形成的硅化层存在孔洞等缺陷,影响形成的半导体器件的性能。
[0078]
参考图12,形成所述第一扩散阻挡层520之后,在所述第一扩散阻挡层520上形成第二扩散阻挡层530。
[0079]
本实施例中,形成所述硅化层220之后,在形成所述金属籽层400之前,在所述第一扩散阻挡层520上再形成一层新的扩散阻挡层即所述第二扩散阻挡层530,再形成所述第二扩散阻挡层530的原因是,在采用定向自组装(dsa)工艺形成所述硅化层220的过程中,所述第一扩散阻挡层520内部的材料也会发生定向自组装,从而在所述第一扩散阻挡层520的表面形成缺口或破损,影响了所述第一扩散阻挡层520对扩散离子的阻挡作用,所以需要所述第二扩散阻挡层530,从而提高扩散阻挡层的阻挡能力,提高对扩散离子的阻挡作用。
[0080]
参考图13,采用选择性生长法在所述粘附层500的底部和侧壁上形成金属籽层
400。
[0081]
本实施例中,在所述第二扩散阻挡层530的侧壁和底部形成所述金属籽层400。
[0082]
本实施例中,形成所述金属籽层400的工艺参数与第一实施例中相同,这里不再累赘说明。
[0083]
参考图14,在所述金属籽层400上形成金属层410,所述金属层410填充满所述接触孔210。
[0084]
本实施例中,形成所述金属层410之后,采用化学机械研磨法平坦化所述金属层410。
[0085]
相应的,利用上述方法形成的一种半导体器件,包括:基底100;层间介质层200,位于所述基底100上;接触孔210,位于所述层间介质层200内,且底部暴露出所述基底100的表面;粘附层500,包括反应金属层510和第一扩散阻挡层520,其中所述反应金属层510,位于所述接触孔210的底部和侧壁上;第一扩散阻挡层520,位于所述反应金属层510上;第二扩散阻挡层530,位于所述第一扩散阻挡层520上;硅化层220,位于所述接触孔210底部的所述基底100上;金属籽层400,位于所述接触孔210内的所述第二扩散阻挡层530的底部和侧壁上;金属层410,位于所述金属籽层400上,且填充满所述接触孔210。
[0086]
第三实施例
[0087]
图15至图18是本发明第三实施例中半导体器件形成过程的结构示意图。
[0088]
本实施例与第一实施例的差别在于单层粘附层的材料为钛,且硅化层是在形成金属层之后形成。
[0089]
本实施例中,从提供基底到形成接触孔的过程与第一实施例中相同,具体参考图6至图7。
[0090]
参考图15,在所述接触孔210的底部和侧壁上形成单层粘附层300。
[0091]
本实施例中,所述单层粘附层300延伸到所述层间介质层200的表面。
[0092]
本实施例中,所述单层粘附层300的材料为钛。
[0093]
本实施例中,采用原子层气相沉积法形成所述单层粘附层300;其他实施例中,还可采用化学气相沉积法或物理气相沉积法形成所述单层粘附层300。
[0094]
本实施例中,利用原子层气相沉积法能够形成致密度高的所述单层钛层500,提高对扩散离子的阻挡作用。
[0095]
参考图16,采用选择性生长法在所述单层粘附层300的底部和侧壁上形成所述金属籽层400。
[0096]
本实施例中,选择性生长法形成所述金属籽层400的工艺参数与第一实施例中相同。
[0097]
参考图17,在所述金属籽层400上形成金属层410,所述金属层410填充满所述接触孔210。
[0098]
参考图18,在形成所述金属层410之后,在所述接触孔210内的所述基底100上形成硅化层220。
[0099]
本实施例中,对形成金属层410之后的基底100进行热处理,在所述接触孔210内的所述基底100上形成硅化层220。
[0100]
本实施例中,在形成所述金属层之后,利用所述单层粘附层300与所述基底100进
行化学反应,形成所述硅化层220,保证形成的所述硅化层220具有较高的成形质量,这是由于在所述单层粘附层300上形成的金属籽层和金属层对所述单层粘附层300起到保护作用,在进行热处理过程中所述单层粘附层300与所述基底100反应形成硅化层220的时,金属籽层和金属层将所述单层粘附层300与氧气之间隔离开,这样所述单层粘附层300就不会在形成所述硅化层220的过程中被氧化掉,保证了形成的硅化层的质量,提高形成的半导体器件的性能。
[0101]
虽然本发明披露如上,但本发明并非限定于此。任何本领域技术人员,在不脱离本发明的精神和范围内,均可作各种更动与修改,因此本发明的保护范围应当以权利要求所限定的范围为准。