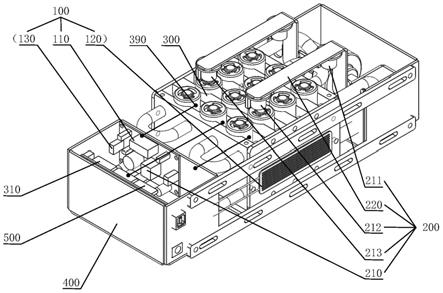
[0001]
本发明涉及电池热安全技术领域,具体涉及一种耦合热管理及热失控抑制的电池安全系统。
背景技术:[0002]
锂离子电池作为一种能量载体,广泛应用于各个领域,尤其是新能源电动汽车。随着新能源电动汽车保有量的大幅提升,其事故发生率也在逐年提高。由于电动汽车采用的动力电池组属于高密度储能装置,一旦电池出现热失控异常状况,极有可能波及整个电池组,继而发展成为整车火灾,甚至引发爆炸事故。为增加新能源电动汽车的性能及续航里程,动力电池组通常由数十上百甚至成千个单体电池组装而成。单体电池的质量均一性以及装配过程均有可能对电池组的安全性能的产生一定的影响。
[0003]
当前动力电池组多采用充放电性能优异,循环寿命较长的锂电池。锂电池的安全测试表明,一旦电池达到不可控热失控温度,在较短时间内便会发展为剧烈热失控,释放大量热量,引发明火,造成火灾事故。由于锂离子电池生产制造、电池组组装、电池组充放电及运行过程中的诸多因素,均有可能造成电池组内个别电池出现温度异常,引起电池组局部热失控,进而引发整个电池组以及用电设备的火灾事故。
[0004]
近一段时间发生的多起电动汽车起火事故,证明了电动汽车在电池的车载安全系统方面,尤其是消防系统仍存在相当大的缺陷。当前,大部分电动汽车的锂电池组均集成安装单功能的热管理系统,热管理系统可在电池充放电过程中对电池组产生的热量进行释放,但面对超出其工作范围的异常状况,例如面对电动汽车出现过充电、炎热天气、单体电池质量不合格时导致的电池温度过高,热管理系统无法及时将热量释放至外界环境,其局限性便凸显出来。
[0005]
另一方面,新能源电动汽车可额外加装车载电池消防系统,进一步提高动力电池组在运行过程中的安全性能,弥补电池组热管理系统的不足,抑制火灾事故的发生,用于火灾事故中电动汽车的自救。值得注意的是,已有的电动汽车用消防系统主要为箱体结构或覆盖到锂电池组上部,通过喷洒灭火剂或水雾的方式灭火。此类消防系统在灭火性能方面能够起到一定的作用,可在锂电池组出现明火时抑制火灾的蔓延,为人员安全撤离及电动汽车火灾扑救提供宝贵的时间。但此类消防系统往往体积较大,会占用宝贵的乘用空间。此外无法使灭火剂深入电池组内部,无法避免电池火灾复燃的发生。因此,已上市的新能源电动汽车中极少有安装此类消防系统,电动汽车在面对热管理系统工作范围外的异常状况时,均不能采取有效的措施。
技术实现要素:[0006]
针对现有车载电池安全系统无法兼顾热管理及火灾消防的缺陷,本发明提出一种耦合热管理及热失控抑制的电池安全系统,提高电动汽车电池组安全性,增加火灾处置响应及人员撤离时间。
[0007]
本发明的目的通过如下的技术方案来实现:
[0008]
一种耦合热管理及热失控抑制的电池安全系统,其特征在于,该系统包括箱体以及设置在所述的箱体内通过导线电性连接的智能控制模块、电池状态监测模块、危险气体检测模块、主动热管理及被动消防模块;
[0009]
所述的电池状态监测模块用于获得单体电池及电池组的温度以及实时电流、电压;
[0010]
所述的危险气体检测模块用于检测不同空气流动方向下电池组内危险气体的浓度,并定时将数据上传至所述的智能控制模块;
[0011]
所述的主动热管理及被动消防模块包括热管理及消防控制器、多个金属导热结构块、多组第一温度传感器,以及由冷却液体输送管道、液体储存箱、液体泵组成的冷却液体循环系统;电池均匀布置在相邻的金属导热结构块之间并留有一定的间隙,由所述的金属导热结构块固定单体电池,所述的冷却液体输送管道穿过金属导热结构块,且与每个电池均接触;所述的多组第一温度传感器布置在每个单体电池表面,组成第一温度监测网,用于监测单体电池的温度;所述的热管理及消防控制器用于处理第一温度传感器的温度,当温度升高至一定的阈值,提高所述的液体泵的功率,并向用户发出报警信号;
[0012]
所述的冷却液体输送管道与每个单体电池接触的位置均开有孔洞,所述的孔洞由隔膜进行密封后与电池直接接触;当温度超过所述的隔膜的可承受温度,所述的隔膜收缩破损并使管道内液体流出,使冷却液体直接与温度异常的电池接触,对电池进行降温和热失控火灾抑制;
[0013]
所述的智能控制模块用于接收其他模块的信号,并将信号传送至所述的主动热管理及被动消防模块采取加速冷却或者释放冷却液体的措施保障电池组运行安全。
[0014]
进一步地,所述的电池状态监测模块包括光纤应变传感器、多组第二温度传感器和状态监测控制器,所述的光纤应变传感器安装在电池表面及电池组侧面,用于获得单体电池及电池组的形变信号,并将其上传至所述的智能控制模块;所述的多组第二温度传感器布置在电池组的上面,组成第二温度监测网,用于获得单个电池的实时温度,并将其上传至所述的智能控制模块;所述的状态监测控制器通过导线选择性地连接于电池及电池组两极,用于获得电池的实时电流、电压,并将其上传至所述的智能控制模块。
[0015]
进一步地,所述的危险气体检测模块包括气体传感器数据采集板以及布置在电池组放置位置周围的多个一氧化碳气体传感器、氢气传感器、甲烷气体传感器,用于不同空气流动方向下电池组内危险气体的检测。
[0016]
进一步地,所述的智能控制模块用于接收其他模块的信号,并储存电池组运行时的电压、电流、温度信息,在线上传数据,并通过声光预警的方式对电池组热失控状态进行提示。
[0017]
进一步地,所述的冷却液体输送管道包括环绕单体电池的导热及液体泄放管道,以及连接导热及液体泄放管道的连接弯管。
[0018]
进一步地,金属导热结构块的材料为金属铝,直接与电池接触吸收电池热量;隔膜的材质选自特氟龙、聚酰亚胺、双向拉伸聚丙烯、聚乙烯任意一种。
[0019]
进一步地,所述的第一温度传感器和第二温度传感器为热电偶或热敏电阻,两种传感器结合应用于电池组的不同位置。
[0020]
进一步地,所述的智能控制模块包括中心控制芯片、低功率显示屏幕、数据储存器、无线传输模块。中心控制芯片负责实时监测其他各模块的工作状态,收集温度、电压、电流、电池容量、危险气体信息,并将数据储存于数据储存器中,并按用户需要通过无线传输模块将数据导出;中心控制芯片与汽车车机系统或其他用电系统连接,并进行数据交互,实现电池组安全状态的预测、监控和预警。
[0021]
本发明的有益效果如下:
[0022]
1、本安全的安全系统将锂电池组热管理系统与锂电池消防安全系统的功能结合并进一步扩展,能够实现锂电池组正常工作下的主动热管理及对温度异常升高引起的热失控火灾进行抑制的功能。
[0023]
2、本发明克服了以往锂电池组热管理系统与消防安全系统结合使用在实际应用场景中空间利用率低,空间隔离,数据互联功能缺失的缺陷。
[0024]
3、通过对主动热管理液体输送管道结构的改造以及系统功能的优化,通过在热管理系统的金属管道上开设孔洞,采用隔膜密封的方式,实现了根据电池温度释放冷却液体的功能,取消了以往电池组消防系统复杂的电气系统和工作逻辑,提高了热失控火灾响应措施的可靠性。
[0025]
4、本发明可实现实时监测单体电池温度、电池组整体温度、电池组电压电流数据、危险气体浓度;对电池组正常充放电进行热管理,对发生温度异常的单体电池进行降温,对发生的热失控火灾进行抑制,并通过智能控制系统向用户进行危险提示和预警。
附图说明
[0026]
图1为本发明的耦合热管理及热失控抑制的电池安全系统的整体示意图;
[0027]
图2为本发明中主动热管理及被动消防模块的结构分布示意图;
[0028]
图3为本发明中导热及液体泄放管道的内部结构及工作原理示意图;
[0029]
图4为现有技术及本发明的系统中电池的散热途径示意图;
[0030]
图5为孔洞直径为3mm条件下得到的电池组温度变化图;(a)隔膜材料为特氟龙;(b)隔膜材料为聚酰亚胺;(c)隔膜材料为双向拉伸聚丙烯;(d)隔膜材料为聚乙烯;
[0031]
图6为为孔洞直径为5mm条件下得到的电池组温度变化图;(a)隔膜材料为特氟龙;(b)隔膜材料为聚酰亚胺;(c)隔膜材料为双向拉伸聚丙烯;(d)隔膜材料为聚乙烯;
[0032]
图7为3mm孔洞直径下使用四种不同隔膜材料时发生热失控电池的数量对比图;
[0033]
图中,电池状态监测模块100、第二温度传感器110、光纤应变传感器120、状态监测控制器130、危险气体检测模块200、气体传感器数据采集板210、一氧化碳气体传感器211、氢气传感器212、甲烷气体传感器213、传感器支架220、主动热管理及被动消防模块300、热管理及消防控制器310、金属导热结构块320、导热及液体泄放管道330、连接弯管340、液体泵350、液体储存箱360、孔洞370、隔膜380、第一温度传感器390、箱体400、智能控制模块500。
具体实施方式
[0034]
下面根据附图和优选实施例详细描述本发明,本发明的目的和效果将变得更加明白,应当理解,此处所描述的具体实施例仅仅用以解释本发明,并不用于限定本发明。
[0035]
除非有定义外,本文中使用的所有技术和科学术语与属于本发明领域的技术人员通常理解和含义相同。本文在说明书中使用的术语只是为了描述具体的实施方式的目的,不局限于本发明。本文所使用的属于“第一”、“第二”等在本文中用于区分对象,但这些对象不受上述术语的限制。
[0036]
如图1~3所示,本发明的耦合热管理及热失控抑制的电池安全系统,包括箱体400以及设置在箱体400内通过导线电性连接的智能控制模块500、电池状态监测模块100、危险气体检测模块200、主动热管理及被动消防模块300。
[0037]
电池状态监测模块100用于获得单体电池及电池组的温度以及实时电流、电压,其包括光纤应变传感器120、多组第二温度传感器110和状态监测控制器130,所述的光纤应变传感器120安装在电池表面及电池组侧面,用于获得单体电池及电池组的形变信号,并将其上传至所述的智能控制模块500;所述的多组第二温度传感器110布置在电池组的上面,组成第二温度监测网,用于获得单个电池的实时温度,并将其上传至所述的智能控制模块500;所述的状态监测控制器130选择性地连接于电池及电池组两极,用于获得电池的实时电流、电压,并将其上传至所述的智能控制模块500。
[0038]
所述的危险气体检测模块200用于检测不同空气流动方向下电池组内危险气体的浓度;危险气体检测模块200包括气体传感器数据采集板210以及布置在电池组放置位置周围的多个一氧化碳气体传感器211、氢气传感器212、甲烷气体传感器213,用于不同空气流动方向下电池组内危险气体的检测。三种气体为锂离子电池热失控期间释放的典型可燃气体,常用于判断电池是否进入热失控状态及热失控火灾预警。气体传感器数据采集板210定时将数据上传至智能控制系统,进行处理以判断电池是否处于危险状态并采取进一步控制措施。
[0039]
所述的主动热管理及被动消防模块300包括热管理及消防控制器310、多个金属导热结构块320、多组第一温度传感器390,以及由冷却液体输送管道、液体储存箱360、液体泵350组成的冷却液体循环系统。电池均匀布置在相邻的金属导热结构块320之间并留有一定的间隙,由所述的金属导热结构块320固定单体电池。金属导热结构块320与电池的接触面积不少于电池轴向侧面面积的50%,从而达到保证电池本体温度梯度一致的目的。根据电池组的设计需求,可更改每一块金属导热结构块320的具体尺寸及结构以应对圆柱形电池,方形电池以及其他形状的电池。金属导热结构块320上未与单体电池接触的位置设计加工有通孔,用于安装导热及液体泄放管道330,导热及液体泄放管道330与金属导热结构块320直接接触,通过热传导的方式将热量传递给冷却液体。
[0040]
冷却液体输送管道包括环绕单体电池的导热及液体泄放管道330,以及连接导热及液体泄放管道的连接弯管340,导热及液体泄放管道330穿过金属导热结构块320,且与每个电池均接触,将电池组产生的热量传递与外界环境进行热交换。液体泵350用于为整个冷却液体循环系统提供动力。液体储存箱360用于储存足量冷却液体,用于电池热管理的散热以及电池火灾的抑制。所述的多组第一温度传感器390布置在每个单体电池表面,组成第一温度监测网,用于监测单体电池的温度。所述的冷却液体为阻燃剂与水的混合物。液体泵350为可调流量的电子水泵。
[0041]
第一温度传感器390用于获取特定情况下电池组的温度,其数据用于判断电池是否进入不可逆的热失控状态。第二温度传感器110安装于电池表面,以获得单体电池的实时
温度数据。第一温度传感器390和第二温度传感器110为热电偶或热敏电阻,两种传感器结合应用于电池组的不同位置,互为冗余。
[0042]
如图3所示,金属导热结构块320、单体电池及导热及液体泄放管道330形成一个短时储存冷却液体的有限空间,导热及液体泄放管道330与每个单体电池接触的位置均开有孔洞370,所述的孔洞370由隔膜380进行密封后与电池直接接触。隔膜的主要特性为高温下收缩破损,与导热及液体泄放管道330结合,对管道开孔位置进行密封。当温度超过所述的隔膜380的可承受温度,所述的隔膜380收缩破损并使管道内液体流出,使冷却液体直接与温度异常的电池接触,对电池进行降温和热失控火灾抑制。与此同时,有限空间的存在会将大部分冷却液体约束在发生热失控的电池周围,减少对其他正常的单体电池的影响,从而达到电池组内部点对点热失控火灾抑制的效果。
[0043]
更具体地,导热及液体泄放管道330的表面的隔膜380的一部分会与单体电池形成一个接触范围。根据设计需要,每个单体电池可与多个隔膜380接触,强化单体电池热失控的火灾抑制性能。
[0044]
导热及液体泄放管道330为金属铝或其他易导热材料制成,表面进行开孔处理,便于冷却液体渗出。
[0045]
所述的热管理及消防控制器310用于处理第一温度传感器390的温度,当温度升高至一定的阈值,提高所述的液体泵350的功率,增加冷却液体在循环系统内部的流动速度,并向用户发出报警信号,提示用户尽快采取措施。
[0046]
所述的智能控制模块500用于接收其他模块的信号,储存电池组运行时的电压、电流、温度信息,在线上传数据,并通过声光预警的方式对电池组热失控状态进行提示。并将信号传送至所述的主动热管理及被动消防模块300采取加速冷却或者释放冷却液体的措施保障电池组运行安全。智能控制模块500包括中心控制芯片、低功率显示屏幕、数据储存器、无线传输模块。中心控制芯片负责实时监测其他各模块的工作状态,收集温度、电压、电流、电池容量、危险气体信息,并将数据储存于数据储存器中,并按用户需要通过无线传输模块将数据导出;中心控制芯片与汽车车机系统或其他用电系统连接,并进行数据交互,实现电池组安全状态的预测、监控和预警。
[0047]
如图1所示,智能控制模块500、状态监测控制器130、热管理及消防控制器310、气体传感器数据采集板210均设置在箱体500内的一侧的隔离空间中,并进行密封防水处理,以保护智能控制系统及与其相连接电子元件的工作安全。
[0048]
本发明的智能控制模块500的工作逻辑分为正常工作状态+异常工作状态两种模式。系统上电启动后,首先激活电池状态监测模块100及危险气体检测模块200,读取电池组温度、电压、形变、可燃气体泄漏等信息,判断电池组是否存在异常,若电池组状态安全则进入正常工作状态,启动主动热管理及被动消防模块300的热管理功能,电池状态检测模块100和危险气体检测模块200进入后台运行,保持电池组工作期间的常态运行,实时监测相关数据。主动热管理及被动消防模块300通过电池组内置的温度传感器分析电池组整体温度,当电池组温度升高时,增加液体泵350运行功率,当电池组温度回落时,降低液体泵350运行功率,节省电池组能量。新能源电动汽车在运行过程有一定几率会出现超出可承受的震动和碰撞等状况,对单体电池产生一定的损伤,严重时会影响的单体电池和电池组内部结构的完整性。一旦损伤超过单体电池和电池组的可承受范围,会出现异常温度上升,电池
产热增加,此时主动热管理及被动消防模块300的散热不足以抵消电池本身的放热,单体电池会进入热失控状态。若系统上电启动后或电池组充放电过程中检测到温度异常,则激活主动热管理及被动消防模块300的消防功能,系统进入异常工作状态,第一温度监测网会对电池组进行第二次温度数据识别,若温度数据同样异常,且危险气体检测模块200检测到可燃气体,则判定单体电池已进入热失控状态,智能控制模块向车机系统和用户发出电池温度异常提示,同时降低电池组放电功率,液体泵350以正常工作状态的2倍功率运行,缓解异常状况。若单体电池温度继续升高,隔膜380会在单体电池温度进入不可逆热失控时自动破损,冷却液体直接对电池进行降温,智能控制模块向车机系统及用户发出红色危险信号,同时切断电池组主要电源输出,仅保留数据记录及危险信号提示功能。
[0049]
如图4的上半部分,现有一般结构的液体冷却热管理系统在进行电池组热管理及热失控抑制过程中的散热途径,其主要方式为:(1)通过导热模组将电池产生的热量传递至冷却液体,冷却液体通过循环将热量释放至外界环境;(2)单体电池或电池模组与外界环境(空气、其他组件)的热对流及热传导。如图4的下半部分,本发明的电池安全系统中,抑制热失控过程中电池产热,热管理散热和热失控抑制的主要热传递过程包括:
[0050]
(1)电池内部的焦耳热、不可逆电化学反应热、可逆电化学反应热;
[0051]
(2)电池本体与空气的热对流散热、电池与金属结构块的热传导换热、金属管道及冷却液体与金属结构块的热传导换热、冷却液体与外界环境的热对流散热;
[0052]
(3)隔膜与电池的热传导、冷却液体与电池的热传导散热、冷却液体蒸发汽化潜热;其中冷却液体与电池的热传导散热和冷却液蒸发汽化潜热是吸收热失控电池热量的主要途径。冷却液体直接与电池接触,降低了热阻,提高了冷却液体吸收热失控热量的效率,从而实现短时间内将热失控电池释放的大量热转移至外界环境,抑制电池组早期热失控的目的。
[0053]
为了更好的解释本发明对提高热管理及热失控抑制效果的促进作用,下面以部分实验数据进行具体说明:
[0054]
一共开展了9组电池热失控抑制实验,其中孔洞370的直径分别为3mm和5mm,隔膜380的材质主要为:特氟龙、聚酰亚胺、双向拉伸聚丙烯、聚乙烯;以及一组无安全措施的对照实验组别;实验中使用的电池组由7节18650尺寸的圆柱形电池组成,电池表面布置若干热电偶,用于测量电池的表面温度;冷却液体的主要成分为:水、浓度3%丙二醇的水溶液、浓度5%溴化物的水溶液;使用一个加热棒诱发电池热失控进程。实验过程中电池的表面温度是衡量单体电池是否进入热失控的主要指标,因此实验主要通过测量电池表面温度并结合发生热失控电池的数量判断不同热失控抑制方法的效果,出于安全考虑,将单体电池的安全温度设定为80℃。
[0055]
如图5所示,对于熔点温度高于电池热失控起始温度的特氟龙(ptfe),加热棒外圈附近电池的温度会超过热失控起始温度并进入不可逆的热失控状态,随后电池发生热失控,电池温度瞬间升高至500℃以上,特氟龙隔膜破损,释放冷却液体通过液体换热和蒸发吸热的作用将热量导出至外界环境,当电池组所有单体电池的温度下降至80℃后可认为不会继续发生热失控传播。聚酰亚胺和双向拉伸聚丙烯的作用机理与特氟龙隔膜类似,隔膜的破损均发生于电池热失控的瞬间。对于熔点温度低于电池热失控起始温度的聚乙烯,当电池表面温度超过约150℃后,聚乙烯隔膜破损,释放冷却液体,尚未热失控电池的温度随
即下降,电池表面温度由接近150℃下降至安全温度,当电池组所有电池的温度下降至80℃后,判定不会进一步诱发电池组的热失控传播。
[0056]
如图6所示,当孔洞370的直径由3mm增加至5mm后,电池发生热失控的几率减小。具体可见图6(a)和图6(b),特氟龙作为密封隔膜时,3mm的孔洞370导致3节单体电池热失控,而5mm的孔洞370仅仅有1节单体电池发生了热失控,这主要是由于直径的增大一方面增加了隔膜380与电池表面的接触面积,增加了隔膜的吸热面积,使得隔膜380发生破损的几率更大。另一方面直径的增加使得冷却液体泄放的流量增加,相同时间内吸收的热量更多。对于不同的隔膜材料,随着材料熔点的降低,电池发生热失控的数量和几率也在下降。具体可见图6(d),熔点最低的聚乙烯材料隔膜在150℃左右时发生熔毁,随即泄放的冷却液体发挥冷却作用,使电池温度迅速降低,电池并未进入不可逆的热失控状态,而其他熔点相对高的隔膜材料均发生了一个或多个电池的热失控。通过上述分析可以说明,通过采用此方法,可有效抑制电池组内早期热失控火灾,避免电池进入不可逆的热失控状态,降低热失控传播及引发大型电池组火灾的几率。
[0057]
如图7所示,通过对电池组加装一种耦合热管理及热失控抑制的电池安全系统,通过优化孔洞直径和隔膜材料,可以逐步将电池组热失控的严重程度和热失控电池数量逐步降至最低,通过采用四种不同隔膜材料和两种不同孔洞直径的组合,本发明将电池组热失控电池数量控制在1个以下,实现了比较好的热失控抑制效果。
[0058]
本领域普通技术人员可以理解,以上所述仅为发明的优选实例而已,并不用于限制发明,尽管参照前述实例对发明进行了详细的说明,对于本领域的技术人员来说,其依然可以对前述各实例记载的技术方案进行修改,或者对其中部分技术特征进行等同替换。凡在发明的精神和原则之内,所做的修改、等同替换等均应包含在发明的保护范围之内。