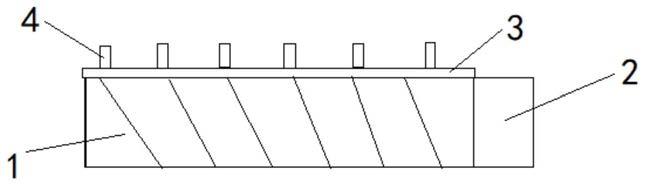
[0001]
本发明涉及电池技术领域,尤其涉及一种多极耳电池极片及其制作方法。
背景技术:[0002]
随着锂离子电池技术的快速发展,人们对锂离子电池的充电速度和能量密度的要求越来越高,需要通过调整电芯极耳结构来平衡电池的电流分布,以提高电池的充电速度,因此,有必要将电池的电芯结构设计为多极耳结构。目前,多极耳结构的电池的极耳在焊接过程中,容易发生折断,焊接可靠性低。
技术实现要素:[0003]
本发明实施例提供一种多极耳电池极片及其制作方法,以解决现有的多极耳电池的电池的极耳在焊接过程中,容易发生折断,焊接可靠性低的问题。
[0004]
第一方面,本发明实施例提供了一种多极耳电池极片,包括:
[0005]
第一涂膏、箔材、和陶瓷层,所述箔材包括第一表面,所述第一涂膏设置于所述箔材的第一表面上,多个极耳从所述箔材延伸出,所述箔材的第一边缘上设置有陶瓷涂层,在极片宽度方向上,陶瓷涂层与所述多个极耳同侧,所述陶瓷涂层靠近所述第一边缘的一侧为第一侧,所述陶瓷涂层远离所述第一边缘的一侧为第二侧,所述陶瓷涂层在第二侧的厚度小于陶瓷涂层在第一侧的厚度。
[0006]
可选地,所述多个极耳基于箔材形成,所述多极耳电池极片包括制作状态和清洗状态,在所述制作状态下,所述多个极耳上涂覆有第二涂膏,在所述清洗状态下,清洗掉所述第二涂膏,露出空箔区形成所述多个极耳。
[0007]
可选地,所述第二涂膏的内聚力大于所述第二涂膏对所述空箔的粘结力。
[0008]
可选地,所述第二涂膏的粘结剂含量小于2%。
[0009]
第二方面,本发明实施例还提供了一种电芯,包括第一方面所述的多极耳电池极片,每一极耳的宽度为电芯的宽度的1/10-1/3;和/或,所述陶瓷层的第二侧的高度为0.5-3mm,所述陶瓷层的第一侧的高度为1.5-5mm。
[0010]
第三方面,本发明实施例还提供了一种多极耳电池极片的制作方法,包括:
[0011]
形成箔材;
[0012]
在所述箔材上涂覆第一涂膏,形成多个第一涂膏区,相邻的两个所述第一涂膏区之间形成空箔区;
[0013]
在所述空箔区涂覆第二涂膏,所述箔材、所述第一涂膏区和所述空箔区形成所述多极耳电池极片结构;
[0014]
在所述第二涂膏与所述第一涂膏之间的箔材上设置有陶瓷涂层
[0015]
对所述多极耳电池极片结构进行辊压处理;
[0016]
在所述空箔区对所述多极耳电池极片结构进行模切得到若干个子极片;
[0017]
在所述子极片的空箔区进行裁剪处理得到包括多个极耳的电池极片。
[0018]
可选地,所述第一涂膏和所述第二涂膏之间满足第一预设关系如下:
[0019]
n1<(m2*ρ1)/(m1*ρ2)<n2;
[0020]
式中,m1表示第一涂膏的面密度,m2表示第二涂膏的面密度,ρ1表示第一涂膏的压实密度,ρ2表示第二涂膏的压实密度,n1表示第一阈值,n2表示第二阈值。
[0021]
可选地,所述在所述子极片的空箔区进行裁剪处理得到包括多个极耳的电池极片,包括:
[0022]
清洗辊压后的所述子极片的空箔区;
[0023]
对所述子极片的空箔区进行裁剪。
[0024]
可选地,所述在所述空箔区对所述多极耳电池极片结构进行模切得到若干个子极片,包括:
[0025]
清洗辊压处理后的所述多极耳电池极片结构的空箔区;
[0026]
在所述空箔区对清洗后的所述多极耳电池极片结构进行模切处理。
[0027]
可选地,包括清洗所述空箔区,清洗时,清洗掉部分陶瓷涂层,以使所述陶瓷层靠近第一涂膏的第一侧的厚度大于陶瓷层远离第一涂膏的第二侧的厚度。
[0028]
本发明实施例提供的技术方案中,多极耳电池极片包括第一涂膏、箔材、和陶瓷层,箔材包括第一表面,第一涂膏设置于箔材的第一表面上,多个极耳从箔材延伸出,箔材的第一边缘上设置有陶瓷涂层,在极片宽度方向上,陶瓷涂层与多个极耳同侧,陶瓷涂层靠近第一边缘的一侧为第一侧,陶瓷涂层远离第一边缘的一侧为第二侧,陶瓷涂层在第二侧的厚度小于陶瓷涂层在第一侧的厚度,这样,多个极耳通过弯折焊接在一起,陶瓷层靠近极耳空箔侧的厚度较小,此时陶瓷层对于极耳弯折角度限制较小,能够提高极耳弯折焊接可靠性。
附图说明
[0029]
为了更清楚地说明本发明实施例的技术方案,下面将对本发明实施例描述中所需要使用的附图作简单地介绍,显而易见地,下面描述中的附图仅仅是本发明的一些实施例,对于本领域普通技术人员来讲,在不付出创造性劳动性的前提下,还可以根据这些附图获取其他的附图。
[0030]
图1是本发明实施例提供的一种多极耳电池极片的结构示意图;
[0031]
图2是发明实施例提供的一种多极耳电池极片的制作方法的流程图。
[0032]
附图标记:
[0033]
1、第一涂膏;2、箔材;3、陶瓷层;4、极耳。
具体实施方式
[0034]
下面将结合本发明实施例中的附图,对本发明实施例中的技术方案进行清楚、完整地描述,显然,所描述的实施例是本发明一部分实施例,而不是全部的实施例。基于本发明中的实施例,本领域普通技术人员在没有作出创造性劳动前提下所获取的所有其他实施例,都属于本发明保护的范围。
[0035]
除非另作定义,本发明中使用的技术术语或者科学术语应当为本发明所属领域内具有一般技能的人士所理解的通常意义。本发明中使用的“第一”、“第二”以及类似的词语
并不表示任何顺序、数量或者重要性,而只是用来区分不同的组成部分。同样,“一个”或者“一”等类似词语也不表示数量限制,而是表示存在至少一个。“连接”或者“相连”等类似的词语并非限定于物理的或者机械的连接,而是可以包括电性的连接,不管是直接的还是间接的。
[0036]
请参见图1,本申请实施例提供了一种多极耳电池极片,多极耳电池极片包括,第一涂膏1、箔材2、和陶瓷层3,箔材2包括第一表面,第一涂膏1设置于箔材2的第一表面上,多个极耳4从箔材2延伸出,箔材2的第一边缘上设置有陶瓷涂层,在极片宽度方向上,陶瓷涂层与多个极耳4同侧,陶瓷涂层靠近第一边缘的一侧为第一侧,陶瓷涂层远离第一边缘的一侧为第二侧,陶瓷涂层在第二侧的厚度小于陶瓷涂层在第一侧的厚度。
[0037]
在该实施方式中,涂箔可以为金属涂箔,例如铜箔或者铝箔,此处,仅作示例说明,可变换地,在其他可行的实施例中,还可以采用其他类型的涂箔。
[0038]
在该实施方式中,陶瓷层3的材料可以是纳米化的氧化铝颗粒,通过设有陶瓷层3,可以提高极片的耐热性,进一步提高多极耳4电池极片结构的安全性。
[0039]
本发明实施例提供的技术方案中,多极耳4电池极片包括第一涂膏1、箔材2、和陶瓷层3,箔材2包括第一表面,第一涂膏1设置于箔材2的第一表面上,多个极耳4从箔材2延伸出,箔材2的第一边缘上设置有陶瓷涂层,在极片宽度方向上,陶瓷涂层与多个极耳4同侧,陶瓷涂层靠近第一边缘的一侧为第一侧,陶瓷涂层远离第一边缘的一侧为第二侧,陶瓷涂层在第二侧的厚度小于陶瓷涂层在第一侧的厚度,这样,多个极耳4通过弯折焊接在一起,陶瓷层3靠近极耳4空箔侧的厚度较小,此时陶瓷层3对于极耳4弯折角度限制较小,能够提高极耳4弯折焊接可靠性。
[0040]
可选地,多个极耳4基于箔材2形成,多极耳4电池极片包括制作状态和清洗状态,在制作状态下,多个极耳4上涂覆有第二涂膏,在清洗状态下,清洗掉第二涂膏,露出空箔区形成多个极耳4。
[0041]
第一涂膏1涂覆在涂箔上时,相邻的两个第一涂膏1之间预留一定间隔,这样,相邻的两个第一涂膏1区之间即可形成空箔区,在经过模切之后,空箔区最后形成极耳4。其中,第一涂膏1的材料可以是钴酸锂,第二涂膏的材料可以与第一涂膏1的材料不同,当第一涂膏1的材料为钴酸锂时,第二涂膏可以是锰酸锂、镍钴锰酸锂、镍钴铝酸锂、磷酸铁锂或者石墨中的至少一种。此处仅作示例说明,可变换地,第一涂膏1或者第二涂膏还可以是其他类型的材料。在其他可行的实施例中,第二涂膏还可以与第一涂膏1采用相同的材料。
[0042]
需要说明的是,在实际情况中,极片包括第一面(涂膏长面)和第二面(涂膏短面)。但不论对于该第一面或者第二面,在涂覆第一涂膏1时,都在相邻的两个第一涂膏1之间预留一定间隔以形成空箔区,这样,便于在极片的两个面上的空箔区都涂覆第二涂膏,可以从极片的两个面上都降低第一涂膏1与空箔区之间的延展率差,更有效地减少极片断带的发生。
[0043]
可选地,第二涂膏的内聚力大于第二涂膏对空箔的粘结力。第二涂膏的粘结剂含量小于2%。
[0044]
具体而言,控制第二涂膏的粘结剂含量小于2%,这样,可以保证第二涂膏的内聚力大于第二涂膏对空箔的粘结力,便于执行辊压后,对第二涂膏进行清洗。
[0045]
需要说明的是,在该实施方式中,在极片的走带方向上预留空箔,并在空箔上涂覆
第二涂膏,降低了极片辊压过程中的断带率,进一步地,便于在将多极耳4电池极片结构绕卷为卷芯时,使用铝箔外包的方式进行收尾,以使得外部封装壳体可直接与铝箔接触,可以保证壳体维持在一个较高的电位,防止壳体发生化学腐蚀。例如,如图所示,图中,正极片包括正极涂膏和铝箔,负极片包括负极涂膏和铜箔,正极片和负极片中间为隔膜,其中,上述的正极涂膏和负极涂膏为上述的第一涂膏1,铝箔和铜箔为上述的涂箔。
[0046]
本申请实施例还提供了一种电芯,包括如上所述的多极耳4电池极片,每一极耳4的宽度为电芯的宽度的1/10-1/3;和/或,陶瓷层3的第二侧的高度为0.5-3mm,陶瓷层3的第一侧的高度为1.5-5mm。
[0047]
请参见图2,本申请实施例提供了一种多极耳电池极片的制作方法,包括:
[0048]
步骤201、形成箔材;
[0049]
在该实施方式中,涂箔可以为金属涂箔,例如铜箔或者铝箔,此处,仅作示例说明,可变换地,在其他可行的实施例中,还可以采用其他类型的涂箔。
[0050]
步骤202、在箔材上涂覆第一涂膏,形成多个第一涂膏区,相邻的两个第一涂膏区之间形成空箔区;
[0051]
需要注意的是,第一涂膏涂覆在涂箔上时,相邻的两个第一涂膏之间预留一定间隔,这样,相邻的两个第一涂膏区之间即可形成空箔区,在经过模切之后,空箔区最后形成极耳。
[0052]
步骤203、在空箔区涂覆第二涂膏,箔材、第一涂膏区和空箔区形成多极耳电池极片结构;
[0053]
具体而言,第一涂膏的材料可以是钴酸锂,第二涂膏的材料可以与第一涂膏的材料不同,当第一涂膏的材料为钴酸锂时,第二涂膏可以是锰酸锂、镍钴锰酸锂、镍钴铝酸锂、磷酸铁锂或者石墨中的至少一种。此处仅作示例说明,可变换地,第一涂膏或者第二涂膏还可以是其他类型的材料。在其他可行的实施例中,第二涂膏还可以与第一涂膏采用相同的材料。
[0054]
步骤204、在第二涂膏与第一涂膏之间的箔材上设置有陶瓷涂层;
[0055]
步骤205、对多极耳电池极片结构进行辊压处理;
[0056]
步骤206、在空箔区对多极耳电池极片结构进行模切得到若干个子极片;
[0057]
步骤207、在子极片的空箔区进行裁剪处理得到包括多个极耳的电池极片。
[0058]
上述的多极耳电池极片结构的制作方法,通过将第一涂膏涂覆于涂箔上形成多个第一涂膏区,相邻的两个第一涂膏区之间形成空箔区,并将第二涂膏涂覆于空箔区,这样,可以减小在辊压过程中,空箔区与第一涂膏区之间的延展率差,降低极片的断带率,进一步提高多极耳电池在生产过程中的生产良率。
[0059]
可选地,所述第一涂膏和所述第二涂膏之间满足第一预设关系如下:
[0060]
n1<(m2*ρ1)/(m1*ρ2)<n2;
[0061]
式中,m1表示第一涂膏的面密度,m2表示第二涂膏的面密度,ρ1表示第一涂膏的压实密度,ρ2表示第二涂膏的压实密度,n1表示第一阈值,n2表示第二阈值。
[0062]
可选地,所述在所述子极片的空箔区进行裁剪处理得到包括多个极耳的电池极片,包括:
[0063]
清洗辊压后的所述子极片的空箔区;
[0064]
对所述子极片的空箔区进行裁剪。
[0065]
可选地,所述在所述空箔区对所述多极耳电池极片结构进行模切得到若干个子极片,包括:
[0066]
清洗辊压处理后的所述多极耳电池极片结构的空箔区;
[0067]
在所述空箔区对清洗后的所述多极耳电池极片结构进行模切处理。
[0068]
需要说明的是,第二涂膏并不做为多极耳电池极片中的结构使用,因此,在进行辊压处理后,需要将涂覆在空箔区的第二极耳清洗掉。具体而言,在清洗第二涂膏时,可以使用激光清洗第二涂膏。例如,可以先对上述的多极耳电池极片结构进行模切,然后使用激光清洗,这样,可以在第二涂膏使用完毕后,将第二涂膏在多极耳电池极片中清除,不影响多极耳电池极片的正常使用。
[0069]
此外,如果保留部分第二涂膏,由于第二涂膏粘接力较差,在后续的超声波焊接极耳时,会发生第二涂膏掉粉,影响电芯的安全性能,因此,在该实施方式中,全部清洗掉第二涂膏可以解决该问题。
[0070]
可选地,包括清洗所述空箔区,清洗时,清洗掉部分陶瓷涂层,以使所述陶瓷层靠近第一涂膏的第一侧的厚度大于陶瓷层远离第一涂膏的第二侧的厚度。
[0071]
对于现有的多极耳结构电池极片在涂布时,会预留一道或多道空箔区,这些留出来的空箔经过模切后可以作为极耳。在制作过程中,例如在辊压时,在极片上有涂膏的区域,受到的辊压机的挤压力很大,因此会出现比较明显的极片延展现象,而极片上没有涂膏的区域,例如空箔区,由于不能受到辊压机的挤压,因此空箔区的延展性很差,这样,导致有涂膏的区域的长度会在一定程度上增长,而没有涂膏的区域的长度不变,该二者之间的力度相差较大而使得有涂膏的区域对没有涂膏的区域有一个拉扯的力从而导致断带,且有涂膏区域的延展率越高,断带率越高,在很大程度上降低了多极耳电池在生产过程中的生产良率。因此,本申请提供的一种多极耳电池极片的制作方法,通过将第一涂膏涂覆于涂箔上形成多个第一涂膏区,相邻的两个第一涂膏区之间形成空箔区,并将第二涂膏涂覆于空箔区,这样,可以减小在辊压过程中,空箔区与第一涂膏区之间的延展率差,降低极片的断带率,进一步提高多极耳电池在生产过程中的生产良率。
[0072]
由于本实施例的技术方案包含了上述实施例的全部技术方案,因此至少能实现上述实施例的全部技术效果,此处不再一一赘述。
[0073]
以上,仅为本发明的具体实施方式,但本发明的保护范围并不局限于此,任何熟悉本技术领域的技术人员在本发明揭露的技术范围内,可轻易想到变化或替换,都应涵盖在本发明的保护范围之内。因此,本发明的保护范围应以权利要求的保护范围为准。