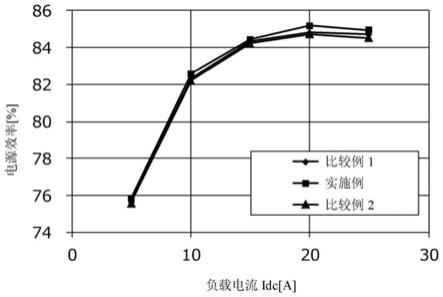
本发明涉及一种使用低铁损芯(core)的电抗器(reactor)。
背景技术:
:电抗器用于办公自动化(officeautomation,oa)设备、太阳能发电系统、汽车、不间断电源等各种用途。电抗器例如用于防止高次谐波电流向输出系统流出的滤波器、使电压升降的电压升降用转换器等中。这种电抗器是线圈(coil)卷绕于环状形状的芯而成。作为环状形状,可列举环形(toroidal)、uu型-uiu型组合的形状、θ形状等。作为芯的种类,一直以来使用铁氧体芯(ferritecore)。而且,在使用铁氧体芯的情况下,由多个铁氧体芯形成环状形状的芯。[现有技术文献][专利文献][专利文献1]日本专利特开2009-259971号公报技术实现要素:[发明所要解决的问题]在由多个铁氧体芯形成环状形状的芯的情况下,为了抑制芯内部的磁通饱和,有时在铁氧体芯构件之间设置间隙。若设置间隙来形成环状形状的芯,则导致电抗器的大型化。近年来,电抗器的用途也扩大,配置电抗器的空间也变小,因而强烈要求电抗器的小型化。因此,作为芯,期望不再是需要设置间隙的铁氧体芯,而置换为因饱和磁通密度高而不需要设置间隙的压粉磁心。本发明是为了解决所述课题而完成,其目的在于提供一种电抗器,其可将铁氧体芯置换为压粉磁心,实现小型化。[解决问题的技术手段]本发明的电抗器包括芯及安装于所述芯的线圈,其中,所述芯是频率为100khz、最大磁通密度100mt下的铁损在芯的温度为25℃以上且100℃以下的范围内为240kw/m3以下的压粉磁心,且所述压粉磁心包含铁硅铝(fesial)合金粉末。[发明的效果]根据本发明,可获得一种可实现小型化的电抗器。附图说明图1是示出实施例的芯的形状的示意图。图2是示出实施例的负载电流与电源效率之间的关系的图表。图3是示出实施例的芯温度与铁损之间的关系的图表。图4是示出实施例的负载电流与芯温度之间的关系的图表。图5是示出实施例的负载电流与线圈温度之间的关系的图表。具体实施方式(结构)电抗器是将电能转换为磁能进行存储及释放的电磁零件,例如,用作搭载于汽车等的升压电路的主要零件。电抗器包括芯及线圈,线圈卷绕于芯。芯包含磁性体。本实施方式的芯为压粉磁心。压粉磁心例如通过利用绝缘树脂被覆实施了热处理的软磁性粉末,并将其放入模具中加压成形且对成形体进行退火等热处理来制造。本实施方式的压粉磁心具有频率为100khz、最大磁通密度100mt下的铁损在芯的温度为25℃以上且100℃以下的范围内为240kw/m3以下的特性。特别是在相同条件下,最低的铁损为200kw/m3以下,所述最低的铁损出现在芯的温度为50℃以上且75℃以下的范围。(芯)作为软磁性粉末,使用fesial合金粉末。此外,软磁性粉末的制造方法不限。可通过粉碎法来制作,也可通过雾化法来制作。雾化法可为水雾化法、气体雾化法、水气雾化法中的任一种。fesial合金粉末使用实施了粉末热处理的粉末。在粉末热处理中,例如在真空环境或惰性气体环境即非氧化环境或者大气环境中加热1小时~6小时。作为惰性气体,可列举h2或n2。作为热处理温度,优选为500℃以上且700℃以下。若使热处理温度为500℃以上且700℃以下的范围,则可实现铁损的减少。绝缘被膜被覆fesial合金粉末的粒子表面,实现fesial合金粉末间的绝缘。本实施方式的绝缘被膜包括第一被膜及第二被膜的两层。第一被膜被覆fesial合金粉末的表面,被覆了fesial合金粉末的表面的第一被膜的表面由第二被膜被覆。第一被膜是硅烷偶合剂与硅酮寡聚物混合的混合层,第二被膜是硅酮树脂层。此外,作为被覆的形态,包括被覆fesial合金粉末的一个一个粒子的表面的情况、被覆几个粒子结合的结合粒子的表面的情况、被覆粒子的整个表面或表面的一部分的情况。即,可为第一被膜被覆fesial合金粉末的表面的一部分,第二被膜被覆未被第一被膜被覆的fesial合金粉末的表面。第一被膜是通过在fesial合金粉末中添加硅烷偶合剂及硅酮寡聚物并使其混合、干燥,从而在fesial合金粉末的表面形成包含硅烷偶合剂及硅酮寡聚物的混合物的第一被膜。作为干燥温度,优选为60℃以上且300℃以下。更优选为150℃以上且200℃以下。另外,干燥时间根据干燥温度而不同,例如为2小时左右。此外,硅烷偶合剂与硅酮寡聚物的添加方法可在混合了硅烷偶合剂与硅酮寡聚物的基础上添加至fesial合金粉末中进行混合,也可首先在fesial合金粉末中添加硅烷偶合剂,然后添加硅酮寡聚物进行混合。作为硅烷偶合剂,例如可使用氨基硅烷系、环氧硅烷系、异氰脲酸酯系、乙氧基硅烷系、甲氧基硅烷系,特别是可列举3-氨基丙基三乙氧基硅烷、3-缩水甘油氧基丙基三甲氧基硅烷、三-(3-三甲氧基硅烷基丙基)异氰脲酸酯。作为硅烷偶合剂的添加量,相对于fesial合金粉末,优选为0.25wt%以上且1.0wt%以下。通过使硅烷偶合剂的添加量为所述范围,可提高fesial合金粉末的流动性,同时可提高成形的压粉磁心的密度、磁特性、强度特性。硅酮寡聚物可使用:具有烷氧基硅烷基、不具有反应性官能基的甲基系、甲基苯基系的硅酮寡聚物;或具有烷氧基硅烷基及反应性官能基的环氧系、环氧甲基系、巯基系、巯基甲基系、丙烯酸甲基系、甲基丙烯酸甲基系、乙烯基苯基系的硅酮寡聚物;不具有烷氧基硅烷基、具有反应性官能基的脂环式环氧系的硅酮寡聚物等。特别是,通过使用甲基系或甲基苯基系的硅酮寡聚物,可形成厚且硬的绝缘层。另外,考虑到硅酮寡聚物层的形成容易度,也可使用粘度比较低的甲基系、甲基苯基系。相对于fesial合金粉末,硅酮寡聚物的添加量优选为0.25wt%以上且2.0wt%以下。若添加量少于0.25wt%,则不能作为绝缘被膜发挥作用,涡流损失增加,从而磁特性下降。若添加量多于2.0wt%,则压粉磁心膨胀,导致强度下降。第二被膜是通过在由第一被膜被覆的fesial合金粉末中添加硅酮树脂并进行干燥而形成于第一被膜的表面。硅酮树脂是在主骨架具有硅氧烷键(si-o-si)的树脂。通过使用硅酮树脂,绝缘被膜的挠性优异。作为硅酮树脂,可使用甲基系、甲基苯基系、丙基苯基系、环氧树脂改性系、醇酸树脂改性系、聚酯树脂改性系、橡胶系等。其中,特别是在使用甲基苯基系的硅酮树脂的情况下,绝缘被膜的耐热性优异。相对于fesial合金粉末,硅酮树脂的添加量优选为1.0wt%~2.0wt%。若添加量少于1.0wt%,则不能作为绝缘被膜发挥作用,涡流损失增加,从而磁特性下降。若添加量多于2.0wt%,则会导致压粉磁心的密度下降。硅酮树脂的干燥温度优选为100℃以上且200℃以下。其原因在于,若干燥温度小于100℃,则膜的形成不完全,涡流损失有时会变高,另一方面,若干燥温度大于200℃,则成形体的密度及磁导率有时会下降。干燥时间根据干燥温度而不同,例如为2小时左右。此外,在本实施方式中,第一被膜设为混合了硅烷偶合剂与硅酮寡聚物的混合层,但不限于此。例如,第一被膜也可为硅烷偶合剂或硅酮寡聚物的单一层。另外,被覆fesial合金粉末的绝缘被膜也可形成一层绝缘被膜,而非两层。在对形成有绝缘被膜的fesial合金粉末进行加压成形,形成了成形体的基础上,对于所述成形体,在n2气体中、n2+h2气体非氧化性环境中或大气中,在600℃以上且被覆于软磁性粉末的绝缘被膜被破坏的温度(例如设为900℃)以下进行热处理,由此制作压粉磁心。此外,成形时的压力为10ton/cm2~20ton/cm2,优选为平均12ton/cm2~15ton/cm2左右。(线圈)线圈是通过制作多根辫线(litzwire)并将多根辫线并联连接而构成,所述辫线由利用瓷漆(enamel)等进行了绝缘被覆的多根电线捆扎而成。线圈的端部通过焊接等与外部设备的端子接合。即,线圈经由端子与外部设备电连接。若自外部设备供给电力,则线圈中流过电流,产生磁通,在芯内形成闭合的磁路。此外,在本实施方式中,制作多根辫线且并联连接,但辫线也可为一根。另外,线圈也可包括利用瓷漆等进行了绝缘被覆的一根导电性构件。(实施例)接下来,对实施例进行说明。在本实施例中,如下所述制作比较例1、比较例2及实施例的三个试样。此外,表1中示出所制作的比较例1、比较例2及实施例的各结构。[表1]如表1所示,比较例1使用eer-35形状、材质为pc44材料的铁氧体芯(日本工业标准(japaneseindustrialstandards,jis)c2560-3-1)作为芯,在中脚的中央设置8mm的间隙。而且,制作将100根φ0.07mm的漆包线捆扎而成的辫线。制作三根所述辫线,对于铁氧体芯,并联卷绕三根辫线44圈,制作电抗器。另一方面,如表1所示,实施例及比较例2使用压粉磁心作为芯。实施例及比较例2的压粉磁心如下所述进行制作。此外,如下所述,实施例与比较例2的压粉磁心的不同之处在于是否进行了粉末热处理。(1)实施例及比较例2在软磁性粉末中使用fesial合金粉末。实施例在氮气环境中对所述fesial合金粉末进行了2小时粉末热处理。在热处理温度600℃下进行。另一方面,比较例2未进行粉末热处理。(2)对于进行了粉末热处理的实施例以及比较例2的fesial合金粉末,在混合的基础上添加硅烷偶合剂0.5wt%、硅酮寡聚物0.5wt%。然后,在干燥温度200℃下干燥2小时,形成包含硅烷偶合剂及硅酮寡聚物的混合物的第一被膜。(3)对于形成有第一被膜的fesial合金粉末,添加1.5wt%的硅酮树脂。然后,在干燥温度150℃下干燥2小时,形成第二被膜。(4)将形成有第二被膜的fesial合金粉末填充至模具中,在成形压力12ton/cm2下进行压制,制作成形体。成形体的形状设为eq型(eq3222)。具体而言,脚的长度设为l1=13.1mm,l2=9.4mm。脚的长度l1及l2是指图1所示的长度。此外,实施例及比较例2的成形体的外脚与中脚的长度相同,没有像比较例1那样设置间隙。(5)将制作的成形体在大气环境中,在700℃的温度下退火,制作实施例及比较例2的压粉磁心。(6)制作将60根φ0.1mm的漆包线捆扎而成的辫线。制作两根所述辫线,对于实施例及比较例2的压粉磁心,将两根辫线并联卷绕22圈,制作电抗器。测定如上所述制作的比较例1、比较例2及实施例的试样的体积。体积是基于宽度×深度×高度算出。如表1所示,使用铁氧体芯的比较例1的体积为44799mm3,与此相对,使用压粉磁心的实施例及比较例2的体积为28845mm3,使用压粉磁心的实施例及比较例2的体积与使用铁氧体芯的比较例1相比可削减35%,实现了小型化。接下来,对实施例及比较例1、比较例2的试样,在室温下负载5a~25a的电流,测定电源效率、芯温度、线圈温度。测定电源效率、芯温度及线圈温度的测定器使用最大输出600w的交流-直流(alternatingcurrent-directcurrent,ac-dc)电源。具体而言,卸下市售的最大输出600w的ac-dc电源制品的电源内装配的电抗器,更换为实施例及比较例1、比较例2的电抗器。在所述状态下启动电源,测定电源效率等。另外,关于实施例及比较例2的各压粉磁心,测定芯温度(-30℃~150℃)下的铁损。将实施例及比较例2的电抗器放入恒温槽中,在芯温度稳定在相应的温度时通电,测定铁损。铁损的测定使用磁性测量设备bh分析器(岩通测量股份有限公司:sy-8219)进行测定。在测定条件:频率100khz、最大磁通密度bm=100mt的条件下进行。表2及图2中示出关于电源效率的测定结果。电源效率是指电源的输出功率与输入功率的比。即,若输出功率变小,则电抗器的损失相应地增加,电源效率下降。此外,此处所谓的损失不仅包括后述的铁损,还包括铜损。[表2]比较例1比较例2实施例负载电流idc(a)电源效率(%)电源效率(%)电源效率(%)575.675.675.81082.382.282.61584.384.284.42084.884.785.22584.784.584.9如表2及图2所示,实施例及比较例1、比较例2的电源效率的优化依序为实施例、比较例1、比较例2。即,实施例的电源效率取得最优的结果。更详细而言,在所有的负载电流值中,相较于使用铁氧体芯的比较例1,实施例的电源效率提高,在施加20a的电流的情况下,电源效率也提高了0.4%。此次使用的是600w的电源,因此若电源效率提高0.1%则可减少0.6w的损失。即,若比较20a的电源效率,则与比较例1及比较例2相比,实施例的电源效率提高了0.4%~0.5%。即,若使用实施例的电抗器,则作为电源整体可减少2.4w~3.0w的损失,确认到作为电源而言有大的效果。由此显示出,相较于比较例1,实施例的电特性提高。另一方面,比较例2的电源效率在施加5a的电流的情况下,与使用铁氧体芯的比较例1的电源效率同等,但在施加大于5a的电流的情况下,低于比较例的电源效率。即,若施加大于5a的电流,则相较于实施例自不用说,比较例2的电特性相较于比较例1也变差。如上所述,相较于使用铁氧体芯的比较例1,使用实施粉末热处理而制作的压粉磁心的实施例可实现小型化,并且可提高电特性。另一方面,即使为相同的压粉磁心,未进行粉末热处理的比较例2的电特性也相较于实施例及比较例1而变差。因此,实施例的压粉磁心能够用铁氧体芯替代,但比较例2的压粉磁心不能用铁氧体芯替代。因此,以下对实施例与比较例2的不同进行讨论。表3及图3中示出各芯温度下的铁损的测定结果。[表3]实施例比较例2芯温度(℃)铁损(kw/m3)铁损(kw/m3)-30484.34494.94-20431.86448.75-10383.01408.550342.62378.9225239.51322.6650197.51343.6675201.06396.56100218.46437.62125250.84478.61150281.57515.50如表3及图3所示,关于0℃以下的铁损,实施例与比较例2并无太大差距。但是,若超过0℃,则其差距逐渐变大,相较于比较例2,实施例实现了低铁损化。若更详细地研究,则比较例2在芯温度为25℃时,铁损为322.66(kw/m3),铁损最低,若超过25℃,则铁损上升。另一方面,实施例在芯温度为25℃时,铁损为239.51(kw/m3),相较于比较例2减少了80(kw/m3)以上。进而,即使超过25℃,实施例的铁损也在减少,在芯温度为50℃时,为197.51(kw/m3),达到200(kw/m3)以下。而且,如图3所示,在芯温度为50℃~75℃之间,铁损最低,自此铁损逐渐增加。在芯温度为75℃时,铁损为201.06(kw/m3),在50℃~75℃时,明显表现出铁损的减少。另外,即使在100℃时,铁损也为218.46(kw/m3)而维持在240(kw/m3)以下的低铁损。如此,通过使用具有在芯温度为25℃~100℃的范围内铁损为240(kw/m3)以下,特别是在50℃~75℃的范围内铁损最低,所述铁损为200(kw/m3)以下的特性的实施例的压粉磁心,相较于使用铁氧体芯的比较例1,可提高电源效率。接下来,表4及图4中示出芯温度的测定结果。表4所示的测定温度是指利用测定器测定出的实际的芯的温度。所述测定温度是在未卷绕线圈的芯的表面装配热电偶,温度变化饱和时的温度。另外,表4及图4所示的芯温度是指自测定温度减去室温而得的温度。所述芯温度是指技术方案中所述的芯的温度。[表4]另外,表5及图5中示出线圈温度的测定结果。表5的测定结果是指利用测定器测定出的实际的线圈的温度。所述测定温度是在线圈的轴向与宽度方向的线圈表面的中央部分装配热电偶,线圈的温度变化饱和时的温度。另外,表5及图5所示的线圈温度是指自测定温度减去室温而得的温度。[表5]如表4及图4所示,实施例的芯温度与比较例1的芯温度相比,为相同程度或其以下的温度。另外,实施例的线圈温度与比较例1的线圈温度相比为相同程度或其以下的温度。另一方面,若比较实施例与比较例2,则在施加5a的电流的时刻,实施例的芯温度及线圈温度比比较例2的芯温度及线圈温度低7℃左右,在施加25a的电流时,实施例的芯温度及线圈温度低25℃左右。另外,如图4及图5所示,关于芯温度及线圈温度的温度上升,也是比较例2相较于实施例更大。如此,相较于比较例2,实施例可抑制芯及线圈的发热。因此,认为与比较例的压粉磁心相比,实施例可减少铁损。结果,相较于使用铁氧体芯的比较例1,实施例可提高电源效率,但相较于使用铁氧体芯的比较例1,比较例2有电源效率变差的倾向。如上所述,通过使用具有在芯温度为25℃~100℃的范围内铁损为240(kw/m3)以下,特别是在50℃~75℃的范围内铁损最低,所述铁损为200(kw/m3)以下的特性的实施例的压粉磁心,相较于使用铁氧体芯的情况,可实现电抗器的小型化,同时可提高电特性。(其他实施方式)在本说明书中,对本发明的实施方式进行了说明,但所述实施方式是作为例子来提示,并不意图限定发明的范围。如上所述的实施方式可以其他各种方式实施,在不脱离发明的范围的范围内,可进行各种省略、置换、变更。实施方式及其变形与包含在发明的范围及主旨内同样,包含在权利要求中记载的发明及其均等的范围内。当前第1页12