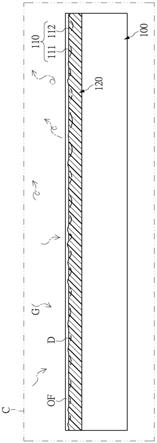
1.本发明涉及一种晶片(芯片)的加工方法,特别是涉及一种碳化硅晶片的表面加工方法。
背景技术:2.碳化硅晶片作为宽带隙半导体,具有高热导率及高饱和电子漂移速率等特点。随着高速及高频无线电技术日益增长的需要,宽带隙半导体越来越受到人们的关注,这种半导体器件能够满足普通硅基半导体所不能满足的诸多优点,例如能够在更高功率水平、更高温度、和更加恶劣的环境下工作。以此基础制造的金属半导体场效应管和金属氧化物半导体场效应管等均已实现。因此获得高质量(如:低缺陷率及高平坦度)的碳化硅晶片显得越来越重要。
3.事实上,磊晶薄膜对碳化硅晶片的依赖性很强,当晶片表面因存在着表面损伤而起伏较大时,将会严重影响磊晶薄膜质量。而生长出来的磊晶层也会受到晶片表面缺陷和平整度的影响。晶片上的所有缺陷会传递到新的磊晶层中。这类缺陷不仅会引起漏电现象,还会显着降低电子迁移率。
4.在现有技术中,为了将碳化硅晶片的表面损伤移除,可以在碳化硅晶片的表面形成牺牲氧化层,而后将牺牲氧化层移除,以一并将表面损伤移除,从而提升碳化硅晶片的表面平坦度。
5.然而,现有形成牺牲氧化层的方法存在着一些技术问题,例如:碳化硅晶片的碳面(损耗面)氧化速率过快、而其硅面(加工面)的氧化速率过慢,如此将因需要移除过多的碳面氧化层而容易造成材料的浪费、且因需要过度的机械加工而容易产生新的表面损伤。再者,为了让硅面氧化层成长至一定的厚度,牺牲氧化层的成长时间将会变得过于冗长,从而拉长了制程时间。
6.从另一个角度说,由于一般业界对于硅面(加工面)的加工质量要求较高,若加工的时间越长(为了要移除过多的碳面氧化层),其会增加硅面表面损伤的机会。
7.于是,本发明人认为上述缺陷可改善,乃特潜心研究并配合科学原理的运用,终于提出一种设计合理且有效改善上述缺陷的本发明。
技术实现要素:8.本发明所要解决的技术问题在于,针对现有技术的不足提供一种碳化硅晶片的表面加工方法。
9.本发明实施例公开一种碳化硅晶片的表面加工方法,其包括:提供一碳化硅晶片;其中,所述碳化硅晶片的一表面定义有一碳面及一硅面,并且所述碳面的晶向不同于所述硅面的晶向;实施一有机薄膜形成步骤,其包含:以一有机溶剂浸湿于所述碳化硅晶片的所述表面,以使得所述有机溶剂形成为覆盖于所述碳化硅晶片的所述表面上的一有机薄膜;其中,所述有机溶剂的碳数不小于2、且挥发速率不大于250;以及实施一牺牲氧化层形成步
骤,其包含:将覆盖有所述有机薄膜的所述碳化硅晶片置放于一高温氧化炉内,以使得所述碳化硅晶片的所述表面形成为一牺牲氧化层;其中,在所述牺牲氧化层形成步骤中,所述有机薄膜能辅助地使得所述硅面的一氧化速率大于所述碳面的一氧化速率。
10.优选地,在所述牺牲氧化层形成步骤中,所述硅面的所述氧化速率大于所述碳面的所述氧化速率的1.5倍以上。
11.优选地,在所述牺牲氧化层形成步骤中,所述硅面的所述氧化速率不小于100纳米/小时,并且所述碳面的所述氧化速率不大于80纳米/小时。
12.优选地,在所述有机薄膜形成步骤中,所述有机溶剂为一醇类溶剂。
13.优选地,在所述牺牲氧化层形成步骤中,所述硅面的所述氧化速率不小于200纳米/小时,并且所述碳面的所述氧化速率介于40至80纳米/小时。
14.优选地,在提供所述碳化硅晶片的步骤中,所述碳化硅晶片的所述表面存在着表面损伤;其中,在所述牺牲氧化层形成步骤中,所述牺牲氧化层的厚度范围完全涵盖所述表面损伤。
15.优选地,所述牺牲氧化层所形成的所述厚度范围不小于800纳米。
16.优选地,在所述牺牲氧化层形成步骤后,所述碳化硅晶片的表面加工方法进一步包括:实施一牺牲氧化层移除步骤,其包含:以一化学机械平坦化制程或一酸性蚀刻制程、将所述碳化硅晶片的所述表面上的所述牺牲氧化层移除,以使得所述碳化硅晶片的所述表面的一表面粗糙度(ra)不大于0.1纳米。
17.本发明实施例也公开一种碳化硅晶片的表面加工方法,其包括:提供一碳化硅晶片;其中,所述碳化硅晶片的一表面定义有一碳面及一硅面,并且所述碳面的晶向不同于所述硅面的晶向;实施一蜡膜形成步骤,其包含:以一液态蜡浸湿于所述碳化硅晶片的所述表面,以使得所述液态蜡形成为覆盖于所述碳化硅晶片的所述表面上的一蜡膜;以及实施一牺牲氧化层形成步骤,其包含:将覆盖有所述蜡膜的所述碳化硅晶片置放于一高温氧化炉内,以使得所述碳化硅晶片的所述表面形成为一牺牲氧化层;其中,在所述牺牲氧化层形成步骤中,所述蜡膜能辅助地使得所述硅面的一氧化速率大于所述碳面的一氧化速率。
18.优选地,所述硅面的所述氧化速率不小于100纳米/小时,并且所述碳面的所述氧化速率介于40至80纳米/小时。
19.综上所述,本发明所提供的碳化硅晶片的表面加工方法,其能通过“实施一有机薄膜(或蜡膜)形成步骤,其包含:以一有机溶剂(或液态蜡)浸湿于所述碳化硅晶片的所述表面,以使得所述有机溶剂(或液态蜡)形成为覆盖于所述碳化硅晶片的所述表面上的一有机薄膜(或蜡膜)”及“实施一牺牲氧化层形成步骤,其包含:将覆盖有所述有机薄膜(或蜡膜)的所述碳化硅晶片置放于一高温氧化炉内,以使得所述碳化硅晶片的所述表面形成为一牺牲氧化层”的技术方案,以使得在所述牺牲氧化层形成步骤中,所述有机薄膜(或蜡膜)能辅助地使得所述硅面的一氧化速率大于所述碳面的一氧化速率,从而减少材料的浪费、减少新的表面损伤产生的机会、及缩短牺牲氧化层的成长时间。
20.为能更进一步了解本发明的特征及技术内容,请参阅以下有关本发明的详细说明与附图,但是此等说明与附图仅用来说明本发明,而非对本发明的保护范围作任何的限制。
附图说明
21.图1为本发明第一实施例步骤s110的示意图。
22.图2为本发明第一实施例步骤s120的示意图。
23.图3为本发明第一实施例步骤s130的示意图(一)。
24.图4为本发明第一实施例步骤s130的示意图(二)。
25.图5为本发明第一实施例步骤s130的一变化态样示意图。
26.图6为本发明第一实施例步骤s140的示意图。
27.图7为本发明第一实施例步骤s150的示意图。
28.图8为本发明第二实施例步骤s110的示意图。
29.图9为本发明第二实施例步骤s120的示意图。
30.图10为本发明第二实施例步骤s130的示意图。
31.图11为本发明第二实施例步骤s140的示意图。
32.图12为本发明第二实施例步骤s150的示意图。
具体实施方式
33.以下是通过特定的具体实施例来说明本发明所公开的实施方式,本领域技术人员可由本说明书所公开的内容了解本发明的优点与效果。本发明可通过其他不同的具体实施例加以施行或应用,本说明书中的各项细节也可基于不同观点与应用,在不悖离本发明的构思下进行各种修改与变更。另外,本发明的附图仅为简单示意说明,并非依实际尺寸的描绘,事先声明。以下的实施方式将进一步详细说明本发明的相关技术内容,但所公开的内容并非用以限制本发明的保护范围。
34.应当可以理解的是,虽然本文中可能会使用到“第一”、“第二”、“第三”等术语来描述各种组件或者信号,但这些组件或者信号不应受这些术语的限制。这些术语主要是用以区分一组件与另一组件,或者一信号与另一信号。另外,本文中所使用的术语“或”,应视实际情况可能包括相关联的列出项目中的任一个或者多个的组合。
35.[第一实施例]
[0036]
请参阅图1至图7所示,本发明的第一实施例提供一种碳化硅晶片的表面加工方法。所述碳化硅晶片的表面加工方法包含:步骤s110、步骤s120、步骤s130、步骤s140、及步骤s150。必须说明的是,本实施例所载之各步骤的顺序与实际的操作方式可视需求而调整,并不限于本实施例所载。
[0037]
如图1所示,所述步骤s110为:提供一碳化硅晶片100(silicon carbide wafer)。其中,所述碳化硅晶片100具有位于相反侧的两个表面,所述碳化硅晶片100的至少其中一个表面110定义有一碳面111(carbon face)及一硅面112(silicon face),并且所述碳面111的晶向不同于所述硅面112的晶向。再者,所述碳面111可以称为损耗面,而所述硅面112可以称为加工面。
[0038]
进一步地说,在所述步骤s110中,所述碳化硅晶片100的表面存在着表面损伤d,并且所述表面损伤d分布于碳面111及硅面112。其中,所述表面损伤d可以例如是:表面微凸起、表面微凹陷、表面刮伤、或表面应力残留,但本发明不受限于此。
[0039]
值得一提的是,一般来说,磊晶薄膜对碳化硅晶片的依赖性很强。当晶片的表面因
存在着表面损伤而起伏较大时,磊晶薄膜的质量将会受到严重的影响,而生长出来的磊晶层也会受到晶片的表面损伤和平整度的影响。晶片上的所有缺陷会传递到新的磊晶层中。这类缺陷不仅会引起漏电现象,还会显著地降低电子迁移率。
[0040]
为了改善上述的技术问题,本发明的目的之一在于,通过“在所述碳化硅晶片100的表面110形成牺牲氧化层120(如图6)”、且通过“将所述牺牲氧化层120移除”,以使得所述碳化硅晶片100表面所存在的表面损伤d能一并被移除(如图7)。借此,所述碳化硅晶片100的表面110能够具有良好的平坦度,从而改善磊晶薄膜的质量(如:表面平坦度)。
[0041]
然而,现有形成牺牲氧化层的方式存在着一些技术问题,例如:碳面(损耗面)的氧化速率过快、而硅面(加工面)的氧化速率过慢,如此将因需要移除过多的碳面氧化层而容易造成材料的浪费、且因需要过度的机械加工而容易产生新的表面损伤。再者,为了让硅面氧化层成长至一定的厚度,牺牲氧化层的成长时间将会变得过于冗长,从而拉长了制程时间。
[0042]
从另一个角度说,由于一般业界对于硅面(加工面)的加工质量要求较高,若加工的时间越长(为了要移除过多的碳面氧化层),其会增加硅面表面损伤的机会。
[0043]
据此,本发明的另一目的在于,通过“在碳化硅晶片100的表面110上形成一有机薄膜of(如图4或图5)”,以使得所述有机薄膜of能辅助地调整硅面的氧化速率及碳面的氧化速率。更具体地说,所述有机薄膜of能辅助地使得硅面的氧化速率大于碳面的氧化速率,从而减少材料的浪费、减少新的表面损伤产生的机会、及缩短牺牲氧化层的成长时间。
[0044]
为了实现上述技术目的,本实施例将通过下述步骤s120至s150实现,以更清楚地描述本发明。
[0045]
如图2所示,所述步骤s120为:实施一晶片清洗步骤。所述晶片清洗步骤包含:以一清洗液体l对所述碳化硅晶片100的表面110进行清洗,以将所述碳化硅晶片100表面上的污染物(如:微粒、金属不纯物、有机污染物、自然生成氧化层、及晶圆表面的微粗糙
…
等)清除干净。
[0046]
在本实施例中,所述晶片清洗步骤主要是采用rca标准清洗法对碳化硅晶片100的表面110进行清洗。其中,所述清洗液体l可以例如是:sc-1(apm)、sc-2(hpm)、spm、hf、或bhf等,但本发明不受限于此。
[0047]
如图3及图4所示,所述步骤s130为:实施一有机薄膜形成步骤。所述有机薄膜形成步骤包含:以一有机溶剂os(organic solvent)浸湿于所述碳化硅晶片100的表面110,以使得所述有机溶剂os形成为覆盖于碳化硅晶片100的表面110上的一有机薄膜of(organic film)、且优选为一液态有机薄膜of。换句话说,所述碳化硅晶片100的表面110能通过有机溶剂os的浸湿,而形成有覆盖于其上的一有机薄膜of。
[0048]
为了让所述有机薄膜of发挥预期的效果(如:提升硅面的氧化速率及降低碳面的氧化速率),所述有机溶剂os的碳数具有一优选的范围。在本实施例中,所述有机溶剂os的碳数优选为不小于2、且特优选为介于2至8之间,但本发明不受限于此。
[0049]
为了让所述有机溶剂os能顺利地在晶片的表面110上形成为有机薄膜of,所述有机溶剂os的挥发速率及沸点也具有一优选范围。在本实施例中,基于乙酸丁酯的挥发速度为100,所述有机溶剂os的挥发速率优选为不大于250、且特优选为不大于230。再者,所述有机溶剂os的沸点优选为不小于70℃、且特优选为不小于75℃。
[0050]
再者,所述有机溶剂os的材料种类可以例如是醇类溶剂、酮类溶剂、烃类溶剂、或醚类溶剂等。
[0051]
在本实施例中,所述有机溶剂os优选为醇类溶剂。其中,所述醇类溶剂可以例如是乙醇、异丙醇、或丁醇,并且所述醇类溶剂优选为异丙醇。更详细地说,在上述例举的醇类溶剂中,乙醇的碳数为2、沸点为78.1℃、且挥发速度为203。异丙醇的碳数为3、沸点为82.5℃、且挥发速度为205。丁醇的碳数为4、沸点为117.1℃、且挥发速度为45。也就是说,上述例举的有机溶剂的碳数皆不小于2、挥发速率皆不大于250、且沸点皆不小于70℃。
[0052]
进一步地说,在本实施例中,所述有机薄膜of是通过浸泡的方式来形成。
[0053]
更具体地说,如图3所示,所述碳化硅晶片100可以例如是先浸泡于有机溶剂os中,以使得所述有机溶剂os浸湿于碳化硅晶片100的表面110。而后,如图4所示,所述碳化硅晶片100从有机溶剂os中被取出,以使得所述碳化硅晶片100的表面110上形成有覆盖于其上的有机薄膜of。其中,所述碳化硅晶片100浸泡于有机溶剂os中的一浸泡时间不大于5分钟、且优选为介于30秒至5分钟。所述碳化硅晶片100浸泡于有机溶剂os中的一浸泡温度不大于30℃、且优选为介于20℃至30℃之间。
[0054]
如图5所示,在本发明的另一实施例中,所述有机薄膜of也可以例如是通过液体涂布的方式将有机溶剂os浸湿于碳化硅晶片100的表面110,以使得所述有机溶剂os形成为覆盖于碳化硅晶片100的表面上的一有机薄膜of。
[0055]
如图6所示,所述步骤s140为:实施一牺牲氧化层形成步骤。所述牺牲氧化层形成步骤包含:将覆盖有所述有机薄膜of的碳化硅晶片100置放于一高温氧化炉c内,以使得所述碳化硅晶片100的表面110形成为一牺牲氧化层120。
[0056]
更具体地说,本实施例是采用一高温湿氧制程来形成牺牲氧化层120。所述高温湿氧制程包含:将覆盖有所述有机薄膜of的碳化硅晶片100置放于高温氧化炉c内。接着,在所述高温氧化炉c内通入水蒸气及氧气的混合气体g,借以使得所述碳化硅晶片100的表面110形成为所述牺牲氧化层120。其中,所述高温氧化炉c的温度优选是介于1000℃至1300℃之间、且特优选是介于1100℃至1200℃之间。再者,所述碳化硅晶片100于高温氧化炉c中的氧化时间优选是介于1小时至5小时之间、且特优选是介于2小时至4小时之间。
[0057]
在本实施例中,所述有机薄膜of是覆盖于牺牲氧化层120上(如图6所示),但本发明不受限于此,所述有机薄膜of也可以例如是于高温湿氧制程中蒸发而被移除。
[0058]
值得一提的是,本发明的主要特色之一在于,根据所述有机溶剂os的材料选择(如:碳数不小于2、且挥发速率不大于250的有机溶剂),在所述牺牲氧化层形成步骤中,所述有机薄膜of能辅助地使得硅面112的氧化速率大于碳面111的氧化速率。
[0059]
在相对值方面,所述硅面112的氧化速率优选地是大于所述碳面111的氧化速率的1.5倍以上,并且所述硅面112的氧化速率特优选地是大于所述碳面111的氧化速率的2.0倍以上。
[0060]
在绝对值方面,所述硅面112的氧化速率不小于100纳米/小时,并且所述碳面111的氧化速率不大于80纳米/小时。
[0061]
在本发明的一实施例中,若所述有机溶剂os为一醇类溶剂,则所述硅面112的氧化速率不小于200纳米/小时,并且所述碳面111的氧化速率是介于40至80纳米/小时。也就是说,所述醇类溶剂在辅助提升硅面112的氧化速率上、具有显著的效果。
[0062]
进一步地说,所述牺牲氧化层120所形成的厚度范围完全涵盖所述表面损伤d(如图6),借此,当所述牺牲氧化层120被移除时,所述表面损伤d也可以一并被移除。
[0063]
在本发明的一实施例中,所述牺牲氧化层120所形成的厚度范围优选地是不小于800纳米、且特优选地是介于800纳米至1,200纳米之间。
[0064]
值得一提的是,在本实施例中,所述有机薄膜of主要可以做为硅面112氧化的催化剂、以提升硅面112的氧化速率,并且可以做为碳面111氧化的抑制剂、以降低碳面111的氧化速率。进一步地说,由于所述有机薄膜of是由有机溶剂os所形成、其具有碳链,因此所述有机薄膜of与碳面111具有较高的亲合力(或能与碳面111形成凡德瓦尔力)。当所述有机薄膜of覆盖于碳化硅晶片100的表面110上时,所述有机薄膜of能遮蔽住碳面111、以降低碳面111的氧化速率,且能裸露出硅面112、以提升硅面112的氧化速率。需说明的是,所述有机薄膜of在牺牲氧化层120的形成步骤中,只是辅助氧化速率的提升或降低,其本身不会发生化学反应。
[0065]
另外,在所述牺牲氧化层120的厚度范围到达预定值后,所述碳化硅晶片100可以被移至室温环境下进行冷却,以利于后续的加工步骤。
[0066]
如图7所示,所述步骤s150为:实施一牺牲氧化层移除步骤。所述牺牲氧化层移除步骤包含:以一化学机械平坦化(chemical-mechanical planarization,cmp)制程或一酸性蚀刻制程,将所述碳化硅晶片100表面上的牺牲氧化层120及有机薄膜of移除。借此,所述碳化硅晶片100表面上的表面损伤也能一并被移除,从而使得所述碳化硅晶片100的表面具有高的平坦度。
[0067]
在本实施例中,所述碳化硅晶片100的表面110的一表面粗糙度(ra)优选为不大于0.1纳米(nm)、且特优选为不大于0.09纳米。
[0068]
[第二实施例]
[0069]
请参阅图8至图12,本发明的第二实施例也提供一种碳化硅晶片的表面加工方法。本实施例与上述实施例大致相同。不同之处在于,本实施例并非是通过有机薄膜来提升硅面的氧化速率及降低碳面的氧化速率,而是通过蜡膜来实现上述目的。
[0070]
进一步地说,本实施例的碳化硅晶片的表面加工方法包含步骤s110’、步骤s120’、步骤s130’、步骤s140’、及步骤s150’。必须说明的是,本实施例所载之各步骤的顺序与实际的操作方式可视需求而调整,并不限于本实施例所载。
[0071]
如图8所示,所述步骤s110’为:提供一碳化硅晶片100’。其中,所述碳化硅晶片100’的一表面110’定义有一碳面111’及一硅面112’,并且所述碳面111’的晶向不同于所述硅面112’的晶向。
[0072]
如图9所示,所述步骤s120’为:实施一晶片清洗步骤。所述晶片清洗步骤包含:以一清洗液体l对所述碳化硅晶片100’的表面110’进行清洗,以将所述碳化硅晶片100’表面上的污染物(如:微粒、金属不纯物、有机污染物、自然生成氧化层及晶圆表面的微粗糙
…
等)清除干净。
[0073]
如图10所示,所述步骤s130’为:实施一蜡膜形成步骤。所述蜡膜形成步骤包含:以一液态蜡(liquid wax)浸湿于所述碳化硅晶片100’的表面110’,以使得所述液态蜡形成为覆盖于碳化硅晶片100’的表面110’上的一蜡膜wf(wax film)。
[0074]
其中,所述液态蜡为一种混合物,并且该混合物的成分可以例如包含:水、脂肪酸、
脂醇、油状物质、及界面活性剂等。
[0075]
再者,为了让所述液态蜡能顺利地在晶片的表面上形成为蜡膜wf,所述液态蜡的闪火点具有一优选范围。在本实施例中,所述液态蜡的闪火点优选为不大于50℃,但本发明不受限于此。
[0076]
在本实施例中,所述蜡膜wf是通过将碳化硅晶片100’浸泡于液态蜡中(图未绘示)、而后再将所述碳化硅晶片100’取出而形成。
[0077]
值得一提的是,由于一般液态蜡的黏度偏高,为了避免所述碳化硅晶片100’的表面110’上存在过量的液态蜡,所述碳化硅晶片100’的表面110’上过量的液态蜡可以例如是通过卫生纸或吸湿布料沾附的方式、而局部地被移除(图未绘示),但本发明不受限于此。
[0078]
如图11所示,所述步骤s140’为:实施一牺牲氧化层形成步骤。所述牺牲氧化层形成步骤包含:将覆盖有所述蜡膜wf的碳化硅晶片100’置放于一高温氧化炉c内,以使得所述碳化硅晶片100’的表面110’形成为一牺牲氧化层120’。
[0079]
其中,在所述牺牲氧化层形成步骤中,所述蜡膜wf能辅助地使得硅面112’的氧化速率大于碳面111’的氧化速率。
[0080]
更具体地说,在本实施例中,所述硅面112’的氧化速率不小于100纳米/小时,并且所述碳面111’的氧化速率介于40至80纳米/小时。
[0081]
另外,值得一提的是,在本实施例中,所述蜡膜wf是覆盖于牺牲氧化层120’上(如图11所示),但本发明不受限于此。
[0082]
如图12所示,所述步骤s150’为:实施一牺牲氧化层移除步骤。所述牺牲氧化层移除步骤包含:以一化学机械平坦化制程或一酸性蚀刻制程,将所述碳化硅晶片100’表面上的牺牲氧化层120’及蜡膜wf移除。借此,所述碳化硅晶片100’表面上的表面损伤也能一并被移除,从而使得所述碳化硅晶片100’的表面具有高的平坦度。
[0083]
[实施例的有益效果]
[0084]
本发明的其中一有益效果在于,本发明所提供的碳化硅晶片的表面加工方法,其能通过“实施一有机薄膜(或蜡膜)形成步骤,其包含:以一有机溶剂(或液态蜡)浸湿于所述碳化硅晶片的所述表面,以使得所述有机溶剂(或液态蜡)形成为覆盖于所述碳化硅晶片的所述表面上的一有机薄膜(或蜡膜)”及“实施一牺牲氧化层形成步骤,其包含:将覆盖有所述有机薄膜(或蜡膜)的所述碳化硅晶片置放于一高温氧化炉内,以使得所述碳化硅晶片的所述表面形成为一牺牲氧化层”的技术方案,以使得在所述牺牲氧化层形成步骤中,所述有机薄膜(或蜡膜)能辅助地使得所述硅面的一氧化速率大于所述碳面的一氧化速率,从而减少材料的浪费、减少新的表面损伤产生的机会、及缩短牺牲氧化层的成长时间。
[0085]
以上所公开的内容仅为本发明的优选可行实施例,并非因此局限本发明的申请专利范围,所以凡是运用本发明说明书及图式内容所做的等效技术变化,均包含于本发明的申请专利范围内。