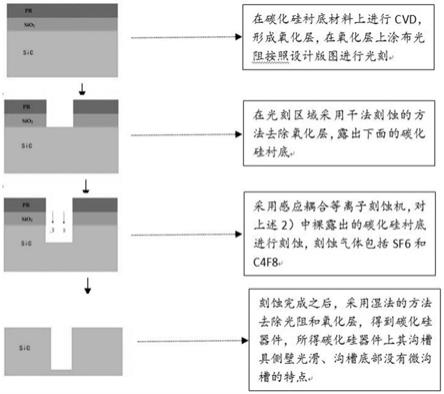
1.本发明属于微电子制作工艺领域,具体为一种碳化硅沟槽刻蚀方法。
背景技术:2.sic(碳化硅)材料具有禁带宽度大、击穿场强高、介电常数小等优点,在制备高温、高频、大功率、抗辐射的半导体器件及紫外光电探测器等方面具有极其广泛的应用,被誉为前景十分广阔的第三代半导体材料。刻蚀技术是sic器件研制中的一项关键支撑技术,刻蚀工艺的刻蚀精度、刻蚀损伤以及刻蚀表面的残留物均对sic器件的性能有重要影响。由于sic材料硬度高、化学性质稳定,湿法刻蚀无法达到要求,因此目前对sic的刻蚀常采用等离子体干法刻蚀工艺,干法刻蚀碳化硅衬底材料的沟槽一般采用cf4和o2为主,外加惰性气体相组合的刻蚀方法;然而采用上述气体刻蚀的方法得出的沟槽侧壁粗糙度较大且沟槽底部容易产生微沟槽,不能满足工艺需求。
技术实现要素:3.本发明的目的在于提供一种碳化硅沟槽刻蚀方法,以克服现有技术的不足。
4.为达到上述目的,本发明采用如下技术方案:
5.一种碳化硅沟槽刻蚀方法,包括以下步骤:
6.s1,在碳化硅衬底材料上进行cvd形成氧化层,在氧化层上涂布光阻后按照设计版图进行光刻;
7.s2,在光刻区域采用干法刻蚀的方法去除氧化层;
8.s3,采用sf6和c4f8的混合气体对去除氧化层的碳化硅衬底进行刻蚀,然后采用湿法去除光阻和氧化层,得到碳化硅器件,完成碳化硅沟槽刻蚀。
9.进一步的,cvd氧化层厚度为800nm~1500nm。
10.进一步的,在光刻区域采用干法刻蚀去除氧化层直至露出碳化硅衬底。
11.进一步的,干法刻蚀具体采用物理性刻蚀、化学性刻蚀或物理化学性刻蚀。
12.进一步的,物理性刻蚀刻蚀功率为1000w~1500w。
13.进一步的,采用感应耦合等离子刻蚀机对裸露出的碳化硅衬底进行刻蚀。
14.进一步的,sf6和c4f8流量比为3:1。
15.进一步的,去除光阻的湿法采用浓硫酸,温度为140
‑
150℃。
16.进一步的,去除光阻的湿法采用浓硫酸的温度为145℃。
17.进一步的,去除氧化层的湿法采用氢氟酸,温度为40
‑
45℃。
18.与现有技术相比,本发明具有以下有益的技术效果:
19.本发明一种碳化硅沟槽刻蚀方法,通过在碳化硅衬底材料上进行cvd形成氧化层,在氧化层上涂布光阻后按照设计版图进行光刻;在光刻区域采用干法刻蚀的方法去除氧化层;采用sf6和c4f8的混合气体对去除氧化层的碳化硅衬底进行刻蚀,能够发生化学反应生成聚合物,所生成的聚合物附着在图形的底部和侧壁上,能够对底部和侧壁,特别是图形沟
槽产生保护作用,从而减弱反应离子对图形拐角处的刻蚀,有效地防止了微沟槽在图形拐角处形成,本发明工艺流程简单,形成的碳化硅沟槽侧壁光滑、沟槽底部没有微沟槽效应;其方法理论简单易于理解,有效提高碳化硅衬底材料的沟槽的刻蚀效率。
20.进一步的,除光阻的湿法采用浓硫酸的温度为145℃时,能够得到光滑的沟槽结构。
附图说明
21.图1为本发明实施例中碳化硅沟槽刻蚀方法流程图。
22.图2为现有方法刻蚀中侧壁粗糙图。
23.图3为现有方法刻蚀中底部微沟槽图。
24.图4为本发明实施例中中侧壁光滑图。
25.图5为本发明实施例中底部没有微沟槽图。
具体实施方式
26.为了使本技术领域的人员更好地理解本发明方案,下面将结合本发明实施例中的附图,对本发明实施例中的技术方案进行清楚、完整地描述;以下实施例仅仅是本发明一部分的实施例,而不是全部的实施例,不用来限制本发明的范围。
27.参见图1,本发明一种碳化硅沟槽刻蚀方法,包括以下步骤:
28.s1,在碳化硅衬底材料上进行cvd(chemical vapor deposition)形成氧化层,在氧化层上涂布光阻后按照设计版图进行光刻;
29.cvd氧化层厚度为800nm~1500nm。
30.s2,在光刻区域采用干法刻蚀的方法去除氧化层,露出光阻下面的碳化硅衬底;
31.干法刻蚀具体采用物理性刻蚀、化学性刻蚀或物理化学性刻蚀;物理性刻蚀刻蚀功率为1000w~1500w。
32.s3,采用感应耦合等离子刻蚀机,对上述步骤s2中裸露出的碳化硅衬底进行刻蚀,刻蚀气体包括sf6和c4f8;sf6和c4f8流量比为3:1;
33.本发明采用sf6和c4f8混合气体,能够发生化学反应生成聚合物,所生成的聚合物附着在图形的底部和侧壁上,能够对底部和侧壁,特别是图形沟槽产生保护作用,从而减弱反应离子对图形拐角处的刻蚀,有效地防止了微沟槽在图形拐角处形成。
34.s4,刻蚀完成之后,采用湿法的方法去除光阻和氧化层,得到碳化硅器件,所得碳化硅器件上其沟槽具侧壁光滑、沟槽底部没有微沟槽。
35.去除光阻的湿法采用浓硫酸,温度为140
‑
150℃;去除氧化层的湿法采用氢氟酸,温度为40
‑
45℃。
36.下面结合附图对本发明做进一步详细描述:采用此优化后工艺方法完成了碳化硅沟槽刻蚀,具体如下:
37.sf6和c4f8刻蚀工艺及结果如表1所示:
38.采用现有方法及本发明方法针对碳化硅衬底材料的侧壁和底部微沟槽进行刻蚀,刻蚀出满足工艺需求的沟槽及侧壁,在碳化硅衬底材料上进行cvd形成氧化层,在氧化层上涂布光阻后按照设计版图进行光刻,cvd氧化层厚度为800nm,然后在光刻区域采用物理性
刻蚀去除氧化层,露出光阻下面的碳化硅衬底,采用感应耦合等离子刻蚀机对裸露出的碳化硅衬底进行刻蚀,刻蚀完成之后,采用湿法的方法去除光阻和氧化层,具体采用145℃的浓硫酸去除光阻,试验结果如图2
‑
图5所示,可以看出其结果侧壁光滑、底部没有微沟槽,试验数据见表2:
39.表1sf6和c4f8刻蚀参数表
40.press(mt)sf6(sccm)c4f8(sccm)rf1(w)rf2(w)time(s)1260201000101800
41.以上所述是一种沟槽的试验结果,并未对试验中各种可能的特征要求进行全面的组合;针对具体的设备和工艺要求,工艺技术人员可以作出类似的调整,然而这些在理论上均是可行的。
42.以上内容仅为说明本发明的技术思想,不能以此限定本发明的保护范围,凡是按照本发明提出的技术思想,在技术方案基础上所做的任何改动,均落入本发明权利要求书的保护范围之内。
技术特征:1.一种碳化硅沟槽刻蚀方法,其特征在于,包括以下步骤:s1,在碳化硅衬底材料上进行cvd形成氧化层,在氧化层上涂布光阻后按照设计版图进行光刻;s2,在光刻区域采用干法刻蚀的方法去除氧化层;s3,采用sf6和c4f8的混合气体对去除氧化层的碳化硅衬底进行刻蚀,然后采用湿法去除光阻和氧化层,得到碳化硅器件,完成碳化硅沟槽刻蚀。2.根据权利要求1所述的一种碳化硅沟槽刻蚀方法,其特征在于,cvd氧化层厚度为800nm~1500nm。3.根据权利要求1所述的一种碳化硅沟槽刻蚀方法,其特征在于,在光刻区域采用干法刻蚀去除氧化层直至露出碳化硅衬底。4.根据权利要求1所述的一种碳化硅沟槽刻蚀方法,其特征在于,干法刻蚀具体采用物理性刻蚀、化学性刻蚀或物理化学性刻蚀。5.根据权利要求4所述的一种碳化硅沟槽刻蚀方法,其特征在于,物理性刻蚀刻蚀功率为1000w~1500w。6.根据权利要求1所述的一种碳化硅沟槽刻蚀方法,其特征在于,采用感应耦合等离子刻蚀机对裸露出的碳化硅衬底进行刻蚀。7.根据权利要求1所述的一种碳化硅沟槽刻蚀方法,其特征在于,sf6和c4f8流量比为3:1。8.根据权利要求1所述的一种碳化硅沟槽刻蚀方法,其特征在于,去除光阻的湿法采用浓硫酸,温度为140
‑
150℃。9.根据权利要求8所述的一种碳化硅沟槽刻蚀方法,其特征在于,去除光阻的湿法采用浓硫酸的温度为145℃。10.根据权利要求1所述的一种碳化硅沟槽刻蚀方法,其特征在于,去除氧化层的湿法采用氢氟酸,温度为40
‑
45℃。
技术总结本发明公开了一种碳化硅沟槽刻蚀方法,通过在碳化硅衬底材料上进行CVD形成氧化层,在氧化层上涂布光阻后按照设计版图进行光刻;在光刻区域采用干法刻蚀的方法去除氧化层;采用SF6和C4F8的混合气体对去除氧化层的碳化硅衬底进行刻蚀,能够发生化学反应生成聚合物,所生成的聚合物附着在图形的底部和侧壁上,能够对底部和侧壁,特别是图形沟槽产生保护作用,从而减弱反应离子对图形拐角处的刻蚀,有效地防止了微沟槽在图形拐角处形成,本发明工艺流程简单,形成的碳化硅沟槽侧壁光滑、沟槽底部没有微沟槽效应;其方法理论简单易于理解,有效提高碳化硅衬底材料的沟槽的刻蚀效率。效提高碳化硅衬底材料的沟槽的刻蚀效率。效提高碳化硅衬底材料的沟槽的刻蚀效率。
技术研发人员:张飞 杨鹏翮 孟晨
受保护的技术使用者:西安微电子技术研究所
技术研发日:2021.06.15
技术公布日:2021/9/17