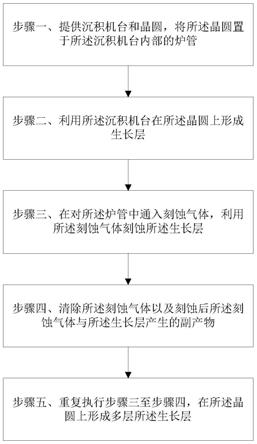
1.本发明涉及半导体技术领域,特别是涉及一种改善晶圆面内厚度均一性的方法。
背景技术:2.随着半导体器件关键尺寸的日益减小,良率提升对工艺过程精确度的要求越来越高。炉管原子气相沉积机台充分利用表面饱和反应天生具备厚度控制能力及高度的稳定性,但由于其固有的特性,即边缘的气流比中间的气流更充足,导致晶圆的边缘至中间呈梯度性减薄,造成同一片晶圆的面内厚度均一性变差,从而限制了其发展。
3.原子层沉积法(ald-atomic layer deposition)充分利用表面饱和反应天生具备厚度控制能力及高度的稳定性,这样得到的薄膜既纯度高、密度高、平整,又具有高度的保型性,即使对于纵宽比高达100:1的结构也可实现良好的阶梯覆盖性。但由于其固有的特性,即边缘的气流比中间的气流更充足,导致晶圆的边缘至中间呈梯度性减薄,造成同一片晶圆的面内厚度均一性变差,这对ald制程是一大挑战。
4.为此,需要一种新的方法,用以消除逐层生长过程中由于气流分布不均匀等因素对晶圆面内厚度均一性产生的影响,进而提升器件性能。
技术实现要素:5.鉴于以上所述现有技术的缺点,本发明的目的在于提供一种改善晶圆面内厚度均一性的方法,用于解决现有技术中在生长层形成时,边缘的气流比中间的气流更充足,导致晶圆的边缘至中间呈梯度性减薄,造成同一片晶圆的面内厚度均一性变差的问题。
6.为实现上述目的及其他相关目的,本发明提供一种改善晶圆面内厚度均一性的方法,包括:
7.步骤一、提供沉积机台和晶圆,将所述晶圆置于所述沉积机台内部的炉管;
8.步骤二、利用所述沉积机台在所述晶圆上形成生长层;
9.步骤三、在所述炉管中通入刻蚀气体,利用所述刻蚀气体刻蚀所述生长层;
10.步骤四、清除所述刻蚀气体以及刻蚀后产生的副产物;
11.步骤五、重复执行步骤二至步骤四,在所述晶圆上形成多层生长层。
12.优选地,步骤一中的所述沉积机台为化学气相沉积机台。
13.优选地,步骤二中的所述生长层的材料为氮化硅。
14.优选地,步骤三中的所述刻蚀气体为hf或f2。
15.优选地,步骤三中的所述炉管还通入稀释气体,用以降低所述刻蚀气体的浓度。
16.优选地,步骤三中所述稀释气体为氮气。
17.优选地,步骤三中的所述炉管的温度为500℃至600℃。
18.优选地,步骤三中的所述刻蚀气体的通入时间为1秒至2秒。
19.步骤四中向所述炉管中通入氮气用来清除所述刻蚀气体以及所述副产物。
20.如上所述,本发明的改善晶圆面内厚度均一性的方法,具有以下有益效果:
21.本发明通过在每层生长层形成的循环中通入刻蚀气体,缩小晶圆边缘至中间梯度性变薄趋势,进而改善晶圆面内厚度均一性。
附图说明
22.图1显示为现有技术中炉管中通入二氯二氢硅气体和氮气的示意图;
23.图2显示为现有技术中清除被吸收的反应的示意图;
24.图3显示为现有技术中通入氨气生成氮化硅的示意图;
25.图4显示为现有技术中清除过量的反应物和副产物的示意图;
26.图5显示为现有技术中一种生成层的成型示意图;
27.图6显示为现有技术中另一种生长层的成型示意图;
28.图7显示为本发明的工艺流程示意图;
29.图8显示为本发明的氮化硅层生成后通入刻蚀气体的示意图;
30.图9显示为本发明的氮化硅层平坦化后清除副产物的示意图;
31.图10显示为本发明的生成层的成型示意图。
具体实施方式
32.以下通过特定的具体实例说明本发明的实施方式,本领域技术人员可由本说明书所揭露的内容轻易地了解本发明的其他优点与功效。本发明还可以通过另外不同的具体实施方式加以实施或应用,本说明书中的各项细节也可以基于不同观点与应用,在没有背离本发明的精神下进行各种修饰或改变。
33.请参阅图7,本发明提供一种改善晶圆100面内厚度均一性的方法,包括:
34.步骤一,提供沉积机台和晶圆100,将晶圆100置于沉积机台内部的炉管;
35.在一种可能的实施方式中,步骤一中的沉积机台为原子层气相沉积机台。
36.在另一种可能的实施方式中,步骤一中的沉积机台为化学气相沉积机台。
37.步骤二,利用沉积机台在晶圆100上沉积形成生长层,对其形成方式不做具体限定,可以通过原子层气相沉积或是化学气相沉积;
38.在一种可能的实施方式中,步骤二中的生长层的材料为氮化硅103。
39.具体地,在采用原子层气相沉积机台,请参阅图1,现有技术中可以首先在炉管中通入二氯二氢硅101气体和氮气102,使二氯二氢硅101沉积在晶圆100表面,请参阅图2,之后清除被吸收的反应,请参阅图3,之后通入氨气104和氮气102的混合气体,通过二氯二氢硅101和氨气104反应在晶圆100上形成氮化硅103生长层,请参阅图4,最后再清除过量的反应物和副产物;
40.在另一种可能的实施方式中,利用化学气相沉积机台,可以通过二氯二氢硅101和氨气104反应在晶圆100上形成氮化硅103生长层。
41.在其他可能的实施方式中,步骤二中的生长层的材料也可为其他类型的材料,可对刻蚀气体105的类型、速率和浓度等参数进行调节,以使每层生长层更加平坦。
42.步骤三,请参阅图8,对炉管中通入刻蚀气体105,既在如图4所示的步骤后通入刻蚀气体105,利用刻蚀气体105刻蚀生长层,缩小生长层边缘至中间梯度差,使之平坦化;
43.在一种可能的实施方式中,步骤三中的刻蚀气体105通常情况下为hf或f2,可以用
于对氮化硅103进行刻蚀,通入刻蚀气体105的速率根据具体的工艺决定。
44.在一种可能的实施方式中,步骤三中的炉管还通入稀释气体,用以降低刻蚀气体105的浓度,便于控制其反应速率。
45.在一种可能的实施方式中,步骤三中稀释气体通常情况下为氮气102,通过在炉管中通入氮气102后,可以用于降低刻蚀气体105hf或f2的浓度。
46.示例性地,可向炉管中通入5sccm f2和n2的混合气体,其中f2在混合气体中的含量为20%。
47.在一种可能的实施方式中,步骤三中的炉管的温度优选为500℃至600℃。
48.在一种可能的实施方式中,步骤三中的刻蚀气体105的通入时间优选为1秒至2秒,通过控制通入时间控制每一层生长层的平坦度。
49.应当理解的是,在改变沉积的生长层的材料后,此处的刻蚀气体的通入时间可调整,用以使每一层的生长层平坦化。
50.步骤四,请参阅图9,由于刻蚀气体105在对晶圆100上的生长层刻蚀后会产生反应产生副产物,因此需清除刻蚀气体105以及刻蚀后产生的副产物;
51.在一种可能的实施方式中,若采用原子层气相沉积机台生成氮化硅103生长层,在通入刻蚀气体105对其氮化硅103生长层刻蚀后,需要再通入氮气102去除过量的反应物和副产物。
52.步骤五,多次在所述生长层上形成另一层所述生长层,每一次另一层所述生长层形成后均重复步骤二至步骤四,在晶圆100上形成多层生长层,由于每一层生长层都在生成后引入刻蚀气体105进行平坦化,因此多层生长层在晶圆100上形成后,缩小了晶圆100边缘至中间梯度性变薄趋势。
53.在一种可能的所述方式中,请参阅图5和图6,由于在淀积生长层时,边缘的气流比中间的气流更充足,导致晶圆100的边缘至中间呈梯度性减薄,造成同一片晶圆100的面内厚度均一性变差,在通过上述步骤在晶圆100上生成生长层时,可以得到如图10所示的结构。
54.需要说明的是,本实施例中所提供的图示仅以示意方式说明本发明的基本构想,遂图式中仅显示与本发明中有关的组件而非按照实际实施时的组件数目、形状及尺寸绘制,其实际实施时各组件的型态、数量及比例可为一种随意的改变,且其组件布局型态也可能更为复杂。
55.综上所述,本发明通过在每层生长层形成的循环中通入刻蚀气体,缩小晶圆边缘至中间梯度性变薄趋势,进而改善晶圆面内厚度均一性。所以,本发明有效克服了现有技术中的种种缺点而具高度产业利用价值。
56.上述实施例仅例示性说明本发明的原理及其功效,而非用于限制本发明。任何熟悉此技术的人士皆可在不违背本发明的精神及范畴下,对上述实施例进行修饰或改变。因此,举凡所属技术领域中具有通常知识者在未脱离本发明所揭示的精神与技术思想下所完成的一切等效修饰或改变,仍应由本发明的权利要求所涵盖。