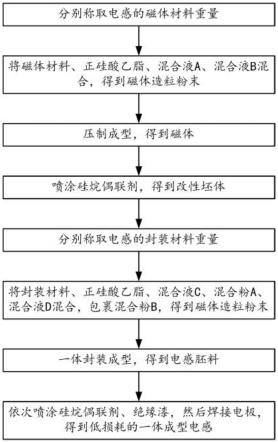
1.本发明涉及电子元器件技术领域,更具体地说,它涉及一种低损耗一体电感及其制备方法。
背景技术:2.随着科技的发展,便携移动设备使用越来越广泛。其从最初的的实用性产品转变为集实用和娱乐为一体的综合性电子产品,用户在享受其带来的娱乐功能的同时,越来越关注其寿命和续航能力。而在电池的储能能力没有大幅度提升的情况下,电源模块的低损耗化成为其关键指标之一,而电源模块中的电感是影响其损耗高低的重要因素之一。
3.电感材料中的软磁合金材料高饱和磁通密度、高磁导率、优异的电流叠加和高居里温度等特点被广泛用于电子设备电源技术中,在电源到器件的能量转换中起到关键作用。
4.然而传统的一体成型电感由于其采用分体式的热压工艺导致t型或u型磁芯和封装粉末间往往存在一定的间隙,导致在间隙处存在较大的漏磁,从而使电感损耗增加,且因间隙的存在需要更大的磁粉颗粒来提升电感值,降低直流电阻无法降低涡流损耗,从而进一步加急了损耗,尤其在高频低负载工作状态下损耗更高,体现在电感在其工作状态下的q值较低。
5.所以对一体成型电感的合金粉料进行成分和工艺设计以及结构设计对于提高材料的使用在高频下保持较高的q值从而使损耗降低具有重要作用,因此开发新的高性能的低损耗复合材料及其一体成型电感技术十分必要。
技术实现要素:6.针对现有技术存在的不足,本发明提供一种低损耗一体电感及其制备方法,在1mhz以上电感保持较高的q值,从而满足目前开关电源对高频化、大电流、低损耗的需求。
7.为实现上述目的,本发明采用如下技术方案:
8.一种低损耗一体电感的制备方法,包括如下步骤:
9.(1)称取电感的磁体材料,其成分为88~95wt%fe、3~5wt%si、1~3wt%ni、0.5~2.0wt%b、0.2~2.0wt%p、0.3~1.0wt%c;
10.(2)将步骤(1)中的磁体材料与正硅酸乙脂、辛基酚聚氧乙烯醚、正己烷、环乙烷、去离子水混合后干燥,并与粒径为1um的feni合金混合后加入环氧树脂、聚氨酯、硅溶胶中的一种或几种形成磁体造粒粉末;
11.(3)将步骤(2)中的磁体造粒粉末通过500~900mpa的压力压制成t型或u型,并在180℃下干燥10~30分钟,形成磁体;
12.(4)将线圈绕制在磁体的中柱部,并通过磁体的叶片固定形成坯体,向坯体表面喷淋硅烷偶联剂并干燥,形成改性坯体;
13.(5)称取电感的封装材料,其成分为88~95wt%fe、3~5wt%si、1~3wt%ni、0.5
~2.0wt%b、0.2~2.0wt%p、0.3~1.0wt%c;
14.(6)将步骤(5)中的封装材料与正硅酸乙脂、辛基酚聚氧乙烯醚、正己烷、环乙烷、去离子水混合后干燥,并与粒径为2~6um的fesi合金、羰基铁粉中的一种或几种混合后加入环氧树脂、不饱和聚氨酯、酚醛树脂中的一种或几种形成封装造粒粉末,并在封装造粒粉末表面包覆粒径为10~30nm的氧化硅、氧化铝中的一种或两种形成封装粉末;
15.(7)将步骤(4)中的改性坯体植入模具,并将步骤(6)中的封装粉末填入模具中,在15~30kg/mm2和100~150℃的条件下压制成内部带有线圈的电感坯料;
16.(8)将步骤(7)中的电感坯料在150~180℃的温度下保温2~6小时固化后,在电感坯料表面含浸一层硅烷偶联剂并干燥,接着在其表面喷涂绝缘漆并干燥,接着去除电感外部电极部位的表面皮膜和绝缘层,再制备电极,形成最终的一体成型电感。
17.可选的,步骤(1)中的磁体材料的粒径为3~8um。
18.可选的,步骤(2)中的磁体造粒粉末包括以下成分:10~30wt%feni、0.5~3wt%正硅酸乙脂、20~50wt%混合液a、0.8~2.0wt%混合液b;其中混合液a由辛基酚聚氧乙烯醚、正己烷、环乙烷、去离子水组成;其中混合液b由环氧树脂、聚氨酯、硅溶胶中的一种或几种组成。
19.可选的,混合液a中的各成分重量比为,辛基酚聚氧乙烯醚:正己烷:环乙烷:去离子水=1:1:1:5~8。
20.可选的,所述去离子水的电导率不大于15μs/cm。
21.可选的,步骤(4)中所述硅烷偶联剂为乙烯基硅烷、氨基硅烷、甲基丙烯酰氧基硅烷中的一种或几种。
22.可选的,步骤(6)中的封装粉末包括以下成分:10~30wt%混合粉a、0.3~2.0wt%正硅酸乙脂、20~50wt%混合液c、0.5~1.2wt%混合液d、0.1~1.0wt%混合粉b;其中混合粉a由fesi合金、羰基铁粉中的一种或两种组成;其中混合液c由辛基酚聚氧乙烯醚、正己烷、环乙烷、去离子水组成;其中混合液d由环氧树脂、不饱和聚氨酯、酚醛树脂中的一种或几种组成;其中混合粉b由氧化硅、氧化铝中的一种或两种组成。
23.可选的,混合液c中的各成分重量比为,辛基酚聚氧乙烯醚:正己烷:环乙烷:去离子水=1:1:1:5~8。
24.可选的,步骤(8)中所述硅烷偶联剂为乙烯基硅烷、氨基硅烷、甲基丙烯酰氧基硅烷中的一种或几种。
25.本发明相对于现有技术具有如下的优点:在1mhz以上电感保持较高的q值,从而满足目前开关电源对高频化、大电流、低损耗的需求。
附图说明
26.图1是本发明的制备流程图。
具体实施方式
27.下面结合实施例和附图对本发明作进一步的描述,但本发明要求保护的范围并不局限于实施例表述的范围。
28.实施例1
29.一种低损耗一体成型电感的制备过程如下:
30.(1)以磁体材料重量为100%计,称取88%fe、5%si、3%ni、2%b、1%p、1%c,使其混合均匀,并研磨至粒径为8um。
31.(2)以磁体造粒粉末重量为100%计,称取15%磁体材料、3%正硅酸乙脂、50%混合液a,将上述材料混合干燥,接着加入粒径为1um的30%feni合金进行混合,再加入2%混合液b进行混合,得到磁体造粒粉末;其中,混合液a中各成分的重量比为,辛基酚聚氧乙烯醚:正己烷:环乙烷:去离子水=1:1:1:5;混合液b的成分为环氧树脂,不包括聚氨酯及硅溶胶。
32.(3)上述磁体造粒粉末通过900mpa的压力压制成t型,并在180℃下干燥30分钟,形成磁体。
33.(4)将线圈绕制在磁体的中柱部,并通过磁体的叶片固定形成坯体,向坯体表面喷淋乙烯基硅烷偶联剂并干燥,得到改性坯体。
34.(5)以封装材料重量为100%计,称取88%fe、5%si、3%ni、2%b、1%p、1%c,使其混合均匀,并研磨至粒径为15um。
35.(6)以封装粉末重量为100%计,称取16.7%封装材料、2%正硅酸乙脂、50%混合液c,将上述材料混合干燥,接着加入粒径为6um的30%混合粉a进行混合,再加入1.2%混合液d进行混合形成封装造粒粉末,并在封装造粒粉末表面包覆粒径为30nm的0.1%混合粉b,形成封装粉末;其中,混合液c中各成分的重量比为,辛基酚聚氧乙烯醚:正己烷:环乙烷:去离子水=1:1:1:8;混合粉a的成分为fesi合金,不包括羰基铁粉;混合液d的成分为环氧树脂,不包括不饱和聚氨酯及酚醛树脂;混合粉b的成分为氧化硅,不包括氧化铝;其中去离子水的电导率为12μs/cm。
36.(7)将步骤(4)中的改性坯体植入模具,并将步骤(6)中的封装粉末填入模具中,在30kg/mm2和150℃的条件下压制成内部带有线圈的电感坯料。
37.(8)将步骤(7)中的电感坯料在180℃的温度下保温6小时固化后,在电感坯料表面含浸一层乙烯基硅烷偶联剂并干燥,接着在其表面喷涂绝缘漆并干燥,接着去除电感外部电极部位的表面皮膜和绝缘层,再制备对应的电极,最终形成低损耗的一体成型电感。
38.实施例2
39.一种低损耗一体成型电感的制备过程如下:
40.(1)以磁体材料重量为100%计,称取95%fe、3%si、1%ni、0.5%b、0.2%p、0.3%c,使其混合均匀,并研磨至粒径为3um。
41.(2)以磁体造粒粉末重量为100%计,称取67.5%磁体材料、0.5%正硅酸乙脂、20%混合液a,将上述材料混合干燥,接着加入粒径为1um的10%feni合金进行混合,再加入2%混合液b进行混合,得到磁体造粒粉末;其中,混合液a中各成分的重量比为,辛基酚聚氧乙烯醚:正己烷:环乙烷:去离子水
42.=1:1:1:8;混合液b的成分为聚氨酯,不包括环氧树脂及硅溶胶。
43.(3)上述磁体造粒粉末通过900mpa的压力压制成t型,并在180℃下干燥10分钟,形成磁体。
44.(4)将线圈绕制在磁体的中柱部,并通过磁体的叶片固定形成坯体,向坯体表面喷淋甲基丙烯酰氧基硅烷偶联剂并干燥,得到改性坯体。
45.(5)以封装材料重量为100%计,称取95%fe、3%si、1%ni、0.5%b、0.2%p、0.3%c,使其混合均匀,并研磨至粒径为15um。
46.(6)以封装粉末重量为100%计,称取69.1%封装材料、0.3%正硅酸乙脂、20%混合液c,将上述材料混合干燥,接着加入粒径为2um的10%混合粉a进行混合,再加入0.5%混合液d进行混合形成封装造粒粉末,并在封装造粒粉末表面包覆粒径为10nm的0.1%混合粉b,形成封装粉末;其中,混合液c中各成分的重量比为,辛基酚聚氧乙烯醚:正己烷:环乙烷:去离子水=1:1:1:5;混合粉a的成分为羰基铁粉,不包括fesi合金;混合液d的成分为不饱和聚氨酯,不包括环氧树脂及酚醛树脂;混合粉b的成分为氧化铝,不包括氧化硅;其中去离子水的电导率为12μs/cm。
47.(7)将步骤(4)中的改性坯体植入模具,并将步骤(6)中的封装粉末填入模具中,在30kg/mm2和100℃的条件下压制成内部带有线圈的电感坯料。
48.(8)将步骤(7)中的电感坯料在150℃的温度下保温6小时固化后,在电感坯料表面含浸一层甲基丙烯酰氧基硅烷偶联剂并干燥,接着在其表面喷涂绝缘漆并干燥,接着去除电感外部电极部位的表面皮膜和绝缘层,再制备对应的电极,最终形成低损耗的一体成型电感。
49.实施例3
50.一种低损耗一体成型电感的制备过程如下:
51.(1)以磁体材料重量为100%计,称取90.3%fe、4%si、2%ni、1.5%b、1.5%p、0.7%c,使其混合均匀,并研磨至粒径为6um。
52.(2)以磁体造粒粉末重量为100%计,称取36.9%磁体材料、1.8%正硅酸乙脂、40%混合液a,将上述材料混合干燥,接着加入粒径为1um的20%feni合金进行混合,再加入1.3%混合液b进行混合,得到磁体造粒粉末;其中,混合液a中各成分的重量比为,辛基酚聚氧乙烯醚:正己烷:环乙烷:去离子水=1:1:1:6;混合液b由环氧树脂、硅溶胶组成,不包括聚氨酯。
53.(3)上述磁体造粒粉末通过700mpa的压力压制成u型,并在180℃下干燥20分钟,形成磁体。
54.(4)将线圈绕制在磁体的中柱部,并通过磁体的叶片固定形成坯体,向坯体表面喷淋偶联剂混合物并干燥,得到改性坯体;其中,偶联剂混合物由氨基硅烷偶联剂和甲基丙烯酰氧基硅烷偶联剂组成。
55.(5)以封装材料重量为100%计,称取90.3%fe、4%si、2%ni、1.5%b、1.5%p、0.7%c,使其混合均匀,并研磨至粒径为15um。
56.(6)以封装粉末重量为100%计,称取47.8%封装材料、1.2%正硅酸乙脂、30%混合液c,将上述材料混合干燥,接着加入粒径为4um的20%混合粉a进行混合,再加入0.7%混合液d进行混合形成封装造粒粉末,并在封装造粒粉末表面包覆粒径为20nm的0.3%混合粉b,形成封装粉末;其中,混合液c中各成分的重量比为,辛基酚聚氧乙烯醚:正己烷:环乙烷:去离子水=1:1:1:6;混合粉a的成分为fesi合金,不包括羰基铁粉;混合液d的成分为酚醛树脂,不包括环氧树脂及不饱和聚氨酯;混合粉b的成分为氧化硅,不包括氧化铝;其中去离子水的电导率为12μs/cm。
57.(7)将步骤(4)中的改性坯体植入模具,并将步骤(6)中的封装粉末填入模具中,在
20kg/mm2和120℃的条件下压制成内部带有线圈的电感坯料。
58.(8)将步骤(7)中的电感坯料在170℃的温度下保温4小时固化后,在电感坯料表面含浸一层由氨基硅烷偶联剂和甲基丙烯酰氧基硅烷偶联剂组成的混合物并干燥,接着在其表面喷涂绝缘漆并干燥,接着去除电感外部电极部位的表面皮膜和绝缘层,再制备对应的电极,最终形成低损耗的一体成型电感。
59.对比例1
60.一种一体成型电感的制备过程如下:
61.(1)以磁体材料重量为100%计,称取88%fe、5%si、3%ni、2%b、1%p、1%c,使其混合均匀,并研磨至粒径为25um。
62.(2)以磁体造粒粉末重量为100%计,称取38.5%磁体材料、粒径为6um的60%feni合金进行混合,再加入1.5%环氧树脂进行混合干燥,得到磁体造粒粉末。
63.(3)上述磁体造粒粉末通过900mpa的压力压制成t型,并在180℃下干燥10分钟,形成磁体。
64.(4)将线圈绕制在磁体的中柱部,并通过磁体的叶片固定形成坯体。
65.(5)以封装材料重量为100%计,称取88%fe、5%si、3%ni、2%b、1%p、1%c,使其混合均匀,并研磨至粒径为25um。
66.(6)以封装粉末重量为100%计,称取39%封装材料、粒径为6um的60%羰基铁粉进行混合,再加入1%环氧树脂进行混合形成封装粉末。
67.(7)将步骤(4)中的改性坯体植入模具,并将步骤(6)中的封装粉末填入模具中,在30kg/mm2和150℃的条件下压制成内部带有线圈的电感坯料。
68.(8)将步骤(7)中的电感坯料在80℃的温度下保温6小时固化后,接着在其表面喷涂绝缘漆并干燥,接着去除电感外部电极部位的表面皮膜和绝缘层,再制备对应的电极,最终形成一体成型电感。
69.对实施例1~3和对比例1得到的电感进行电感值和q值测试,得到如下数据:
70.表1不同电感的测试数据(0420电感)
71.测试项目实施例1实施例2实施例3对比例1电感值2.2μh2.2μh2.2μh2.2μhq值10510810151
72.从表1可以看出:实施例和对比例制备的0420电感在同样的电感量下,实施例的q值优于对比例,因此在实际的应用中更具有低功耗的优势,从而提高产品应用电路的转换效率,这表明电感的磁体材料和封装材料及其粒径选择、工艺处理均影响着电感的功耗,需要材料与工艺合理结合才能制备得到低功耗电感。
73.以上所述仅是本发明的优选实施方式,本发明的保护范围并不仅局限于上述实施例,凡属于本发明思路下的技术方案均属于本发明的保护范围。应当指出,对于本技术领域的普通技术人员来说,在不脱离本发明原理前提下的若干改进和润饰,这些改进和润饰也应视为本发明的保护范围。