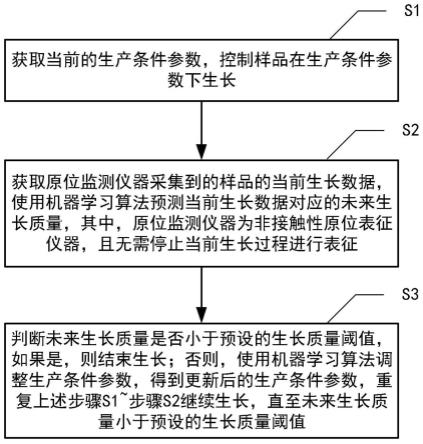
1.本发明涉及外延半导体薄膜生长技术领域,尤其涉及一种基于机器学习的半导体工艺过程控制方法。
背景技术:2.半导体器件的性能与半导体结果中每个薄膜层生长质量密切相关,只有高质量薄膜生长才能确保高品质的器件产出并提高最终器件的良品率。在半导体薄膜材料生长过程中,实时的原位监测技术是实现生长控制过程的前提,通过原位监测手段可以避免在材料生长过程中样品移出腔体的情况发生,减小二次生长引入的缺陷、杂质等问题,从而影响半导体材料的性能。
3.除此之外,若想获得高质量半导体材料,需要能及时反馈生长情况,在生长中避免生长过程中断而引入再生长,再生长过程会引入生长参数重新矫正的问题,若与先前生长参数存在偏差,及时是微小偏离,也会使生长材料发生严重转变,脱离材料生长规划路径,故对于需要停止生长过程而采集原位表征数据的方法也是必须避免的。
4.现有的原位表征方法要与材料接触,生长环境对材料表征手段发生的电子束或射线影响较大,如原位原子力显微镜,原位应力、原位悬梁臂测量、原位曲率测量等。而这种方法往往除了会导致当前生长过程停止,在测量表征过程中,已经与薄膜样品表面接触,存在极大的风险会在样品表面留下划痕、碎渣等杂物,从而增加材料缺陷、表面脏污等。
技术实现要素:5.鉴于上述问题,本发明提供了一种基于机器学习的半导体工艺过程控制方法,基于机器学习算法对半导体薄膜生长条件进行动态调控,整个生长过程不需要停止以进行原位表征,避免对样品产生影响或暂停当前生长过程,实现了有效的半导体高质量生长,有效提高半导体材料的良品率。
6.为达到上述目的,本发明提供了一种基于机器学习的半导体工艺过程控制方法,包括:步骤s1,获取当前的生产条件参数,控制样品在所述生产条件参数下生长;步骤s2,获取原位监测仪器采集到的样品的当前生长数据,使用机器学习算法预测所述当前生长数据对应的未来生长质量,其中,所述原位监测仪器为非接触性原位表征仪器,且无需停止当前生长过程进行表征;步骤s3,判断所述未来生长质量是否小于预设的生长质量阈值,如果是,则结束生长;否则,使用所述机器学习算法调整所述生产条件参数,得到更新后的生产条件参数,重复上述步骤s1~步骤s2继续生长,直至未来生长质量小于预设的生长质量阈值。
7.与现有技术相比,本发明提供的基于机器学习的半导体工艺过程控制方法,至少具有以下有益效果:
8.(1)采用非接触性且对材料生长过程影响较小甚至没有影响的原位表征手段作为数据获取来源,有效避免现有需要接触样品表面的原位表征手段,在表征过程中对材料表
面产生划痕、脏污、引入缺陷的影响;
9.(2)采用非接触且对样本生长过程影响较小的原位表征方法,避免生长过程中断和由再生长而引入生长参数偏离、缺陷增加等情形发生,保障材料生长质量;采用无需将样品移出当前生长环境的表征手段,即原位表征手段的收发装置与样品生长环境位于同一个生长室内,这种无需移出生长环境的方法,可以有效避免人在操作过程中,操作失误风险,也避免由此带来的时间成本压力;
10.(3)由上述原位表征手段获取的数据作为训练样本做训练以预测材料生长过程中,后续材料生长质量变化情况,预测到质量偏差较大的情况时,根据预测产生的判断结果,提前干预调整材料生长参数,避免该质量偏差持续扩大;
11.(4)通过在生长过程中调控生长参数,在原位表征手段帮助下,在上位机控制作用下,实现了对半导体薄膜生长条件的动态调控,整个生长过程不存在停止以进行原位表征,采用的为非接触式的动态监测,可在生长过程中实时反馈当前材料质量,在机器学习算法作用下,根据已有设置质量参数和尺寸需要,预测未来半导体生长状况,包括预测生长成品质量和尺寸、预测未生长部分半导体材料质量变化情况,该方法实现了有效的半导体高质量生长,可以有效提高半导体材料的良品率。
附图说明
12.通过以下参照附图对本发明实施例的描述,本发明的上述以及其他目的、特征和优点将更为清楚,在附图中:
13.图1示意性示出了根据本发明实施例的基于机器学习的半导体工艺过程控制方法的流程图;
14.图2示意性示出了根据本发明实施例的生长质量判断过程的流程图;
15.图3示意性示出了根据本发明实施例的生产条件参数调整过程的流程图。
具体实施方式
16.为使本发明的目的、技术方案和优点更加清楚明白,以下结合具体实施例,并参照附图,对本发明进一步详细说明。显然,所描述的实施例是本发明一部分实施例,而不是全部的实施例。基于本发明中的实施例,本领域普通技术人员在没有做出创造性劳动前提下所获得的所有其他实施例,都属于本发明保护的范围。
17.在此使用的术语仅仅是为了描述具体实施例,而并非意在限制本发明。在此使用的术语“包括”、“包含”等表明了所述特征、步骤、操作和/或部件的存在,但是并不排除存在或添加一个或多个其他特征、步骤、操作或部件。
18.在此使用的所有术语(包括技术和科学术语)具有本领域技术人员通常所理解的含义,除非另外定义。应注意,这里使用的术语应解释为具有与本说明书的上下文相一致的含义,而不应以理想化或过于刻板的方式来解释。
19.附图中示出了一些方框图和/或流程图。应理解,方框图和/或流程图中的一些方框或其组合可以由计算机程序指令来实现。这些计算机程序指令可以提供给通用计算机、专用计算机或其他可编程数据处理装置的处理器,从而这些指令在由该处理器执行时可以创建用于实现这些方框图和/或流程图中所说明的功能/操作的装置。
20.半导体薄膜的生长是材料的形貌和结构演变过程,若产生缺陷等不利于材料高质量生长的情况,一般无法主动消除,且会随着生长过程持续,这种不利特性会持续放大,影响的整个材料的性能,对后期制备成品器件的性能产生巨大影响。在生长过程中减少表征手段对材料生长的影响,采用对材料表面影响最小甚至无影响的表征手段来观察获取原位数据,并实现对该过程发生可能性进行预判,提前干预材料生长的各种参数条件,以减少来自材料本身不利因素的对材料生长成品的影响,可以极大保障材料生长稳定性。
21.虽然已有众多关于原位操作手段的报道,但关于原位监测并调控的手段屈指可数且仍停留在实验室阶段。并且,由于需要依靠实验人员手动操作配合,人力成本巨大且非智能化,投入到实际生产中也是不可取的,不利于工业自动化生产的发展。目前已有报道的原位检测手段也存在不足,其需要停止当前生长过程后将材料移动到原位表征环境中,才能进行性能特性表征,这种过程除了引入上述的缺陷、表面脏污等,其继续生长过程也称为材料再生长。由于生长过程不是连续的,不可避免生长参数会发生偏离,使得原本可抑制缺陷等不利因素的生长参数发生偏离,可能会放大材料表面原有缺陷,劣化薄膜成品性能。而且该过程需要人为操作在几种表征手段中切换,时间成本巨大且无法投入到自动化生产。若要避免再生长过程并缩小人力、时间成本,需要基于现有材料生长状态来预测未来生长质量,以此为前提来适应不同生长要求。
22.然而,即使是经验丰富的工艺师,在观测原位图像时也仅获得实时的图像和曲线,无法实现对未来生长成品的预测,当发现图像曲线异常时,样品已经产生缺陷并无法完美生长了。
23.有鉴于此,本发明提供了一种基于机器学习的半导体工艺过程控制方法,解决上述对样品产生影响或暂停当前生长过程的原位表征手段的影响,以及无法在半导体薄膜生长过程中动态监控并调整半导体参数以稳定甚至提高半导体生长质量的问题。
24.图1示意性示出了根据本发明实施例的基于机器学习的半导体工艺过程控制方法的流程图。
25.如图1所示,根据该实施例的基于机器学习的半导体工艺过程控制方法,目的在于对生长过程中的半导体薄膜进行检测并预测未来时间段或完成时刻薄膜的生长质量变化。该方法可以包括操作s1~操作s3。
26.步骤s1,获取当前的生产条件参数,控制样品在生产条件参数下生长。
27.步骤s2,获取原位监测仪器采集到的样品的当前生长数据,使用机器学习算法预测当前生长数据对应的未来生长质量,其中,原位监测仪器为非接触性原位表征仪器,且无需停止当前生长过程进行表征。
28.步骤s3,判断未来生长质量是否小于预设的生长质量阈值,如果是,则结束生长;否则,使用机器学习算法调整生产条件参数,得到更新后的生产条件参数,重复上述步骤s1~步骤s2继续生长,直至未来生长质量小于预设的生长质量阈值。
29.通过上述实施例,本发明基于机器学习算法调整样品当前的生产条件参数,预测薄膜各生长参数调整方向,对半导体薄膜生长条件进行动态调控,提高薄膜生长质量。其中,原位监测仪器为非接触性原位表征仪器,无需更换样品所处环境且表征过程对样品无影响。这种表征手段符合监测过程不与样品接触,且监测过程对薄膜生长过程无影响或影响极小,以至即使在高精度要求下,该影响可以忽略。
30.本发明实施例中,原位监测仪器的安装位置与所述样品位于同一生长室。由此可见,该原位监测仪器在表征过程对薄膜样品的质量影响极小甚至无影响,且仪器表征过程可以实现在薄膜样品生长过程中进行表征,即无需停止当前生长过程进行表征。
31.本发明实施例中,原位监测仪器包括反射高能电子衍射仪、低能电子衍射仪、质谱仪和吸收光谱仪中的至少一种。
32.需要说明的是,原位监测仪器与样品生长室在同一个环境中,这种安装方式使得在使用过程中,原位监测手段直接在样品生长环境中对正在生长的样品进行作用,不需要按照传统方式将样品移出当前样品生长环境中,有效避免传统过程中由生长室向缓冲室,再有缓冲室到监测室的移动,该移动过程首先由于衬底需要经过控制臂移动,需要控制臂对准样品支架或衬底方向,若有偏差,则样品将会掉入生长室底部造成样品损失,同时也存在磕碰风险,使得样品衬底支撑底座变形,无法再使用。在样品移动过程中,每两个环境室的压力需要平衡后再进行样品传递,该过程无法避免样品与缓冲室内空气或低压下的水或者氧气接触,造成样品表面氧化,形成表面氧化层,这对器件性能影响极大,且这个过程引入再生长过程,在再生长开始前,需要再次执行高温除气等操作,去除氧化层,但该过程也会使得材料内部、表面结构发生改变,甚至对于表面敏感相,在吉布斯自由能曲线上比较接近的两个稳定相发生快速相变,导致需要观测的相消失以及后续生长材料基于的生长底物影响发生极大变化,最终成品远远偏离设想方案。在传递过程中,由于衬底移动,无法避免会与周围环境发生磕碰,而周围环境中往往是未生长的样品,肉眼无法辨识的细小颗粒残渣,部分在高温下甚至是漂浮、悬浮状态,特别是两个环境室之间过度挡板位置,往往也会有残留肉眼无法观测到的残渣,这些残渣会掉落在样品表面,这对原位表征的表征选区极具挑战性。虽然在于缓冲室连接的手套箱中可以对此进行清洗,但手套箱相对于样品生长环境是富氧环境,将会进一步加剧表面氧化过程。若直接移入表征环境中,但在表征室内一般不会配备再清洗装置,且也是要求高真空,虽然部分表征设备可以对材料执行在有限范围内的变温表征,但该变温条件无法满足去除样品氧化层的要求。
33.采用的表征手段为非接触性质的,即与样品之间距离较远,主要通过由发生端口在与样品表面有一定距离情况下,通过发生电子束、光束、射线至样品表面,再由样品反馈,经过一段距离至探测器接收端获取数据,发射端端口与接收端端口虽然安装在样品生长环境内侧表面,但并不会对正在生长的样品造成影响,即在原位表征过程中,不会对样品表面接触,由此引进不需要的且不可逆的材料缺陷。且即使是对生长结束后的薄膜材料进行原位表征,表征发射端口与样品表面以及表征探测器与样品表面距离较远,不会给薄膜引入其他掺杂或缺陷,导致性能改变。
34.采用的原位表征手段几乎为瞬态获取材料表面信息变化,经过样品反馈立刻被探测器接收并处理显示在显示端界面,该过程甚至在100微秒以内就能得到一组数据。而传统通过原子力显微镜、悬梁臂、曲率监测装置不仅需要花时间将样品移出至表征环境中,还需要将原位表征手段与样品对准,随后才能进行原位表征。特别对于需要再制样的样品,还需要在手套箱等低正空环境中进行取样、制片后,再传递至表征环境中进行原位表征,该过程也费时费力,特别在取样过程中,由于刀具表面刻划,也会引入其他验证的表面切片,特别是产生倾斜切口时,若该切口不是后续实验所需选择的,也会导致极大材料缺陷,特别针对材料解离面,材料有碎裂风险。
35.在表征结束后还需要将样品移回生长室,这个过程需要人为通过机械臂操作,且花费时间较长,对于复杂的需要校准的表征手段,如原位原子力显微镜、原位应力、扫描隧道光谱法等,花费时间更长,且如上述描述,也会引入各种不需要的缺陷,虽然实现了原位表征,但会影响材料成品质量。
36.对于全自动化工艺,要最大化减少人为操作,而以上样品转移与制样表征过程中,这种接触性且需要转移样品所在环境的表征方法是需要人为全程操作的,无法排除人为操作的影响和可能性。故采用非接触性、无需更换样品所处环境且表征过程对样品无影响的原位表征手段是优势明显的,有利于后续全自动化半导体工艺线的发展。
37.本发明实施例中,样品的当前生长数据是由原位监测仪器采集后转换输出的可读取的动态光谱、能谱或质谱的至少一种。
38.本发明实施例中,在上述步骤s1之前还包括:获取样品的多个生长相关数据,作为原始数据集输入机器学习网络进行训练,得到训练好的机器学习模型。
39.其中,生长相关数据包括分别在历史时段和当前时段获取的生长相关数据,具体包括原位监测仪器采集到的数据、生长状态、成品尺寸和预设的生长质量阈值。
40.具体来说,可以选用原位监测仪器采集的数据、当前生长数据、生产条件参数的调整大小和调整方向、预设的生长质量阈值中的至少一种,作为原始数据集进行机器学习网络训练并得到训练模型。
41.在每次迭代过程中,原位监测仪器采集的数据以及样品的当前生长数据都会新增输入至该原始数据集中,来测试现有的机器学习网络,若测试结果误差较大,则优化机器学习网络的模型参数,并持续测试,直至测试结果误差满足要求。
42.通过上述实施例,本发明基于机器学习算法训练原始数据集,预测薄膜各生长参数调整方向,对半导体薄膜生长条件进行动态调控,提高薄膜生长质量。
43.本发明实施例中,原始数据集的数据类型包括曲线、图像和时域数据中的至少一种。
44.在半导体材料生长过程中极易出现欠拟合情况发生,这是由于数据集不够。为了丰富数据集,在上述步骤s3中,若未来生长质量不小于预设的生长质量阈值时,在使用机器学习算法调整生产条件参数之前,可以执行更新原始数据集的操作。
45.更新原始数据集会一直接收来自样品在当前的生产条件参数下的当前生长数据,以及来自原位监测仪器采集的数据,包括曲线、图像和时域数据,还接收未来生长质量是否小于预设的生长质量阈值的判断结果。
46.在更新原始数据集的操作中,该原始数据集包含但不限于历史原位监测仪器采集的数据、历史生长状态与生长参数的数据、历史生长参数调整大小和方向的数据、历史设定的生长质量阈值、历史生长质量数据、新增原位监测仪器采集的数据、新增生长状态与生长参数的数据、新增生长参数调整大小和方向的数据、新增设定的生长质量阈值、新增生长质量数据以及质量参数范围。
47.其中,生长状态与生长参数的数据包括但不限于源炉温度、衬底加热器温度、衬底加热器转速、束流强度、生长室压力。原位监测仪器采集的数据包含但不限于质谱仪曲线与图像、低能电子衍射曲线与图像、反射高能电子衍射曲线与图像、吸收光谱曲线与图像。
48.质量参数范围包含但不限于缺陷密度、掺杂浓度、粗糙度、电阻率、霍尔系数、磁
阻、补偿度、光电导、光吸收、禁带宽度、载流子迁移率、非平衡载流子寿命、杂质浓度、纯度、发光峰位、发光强度、晶体质量。
49.在本发明的一些实施例中,在上述作为原始数据集输入机器学习网络进行训练的操作之前,还包括:对所述原始数据集进行预处理。
50.该预处理例如可以包括:将曲线数据变换为数组对象,图像数据转换为可编程的多维数组对象,二值化保留灰度信息或者归一化处理。或者,可以对原始数据集中的每个数据采用数组降维或者升维的映射方法,统一数据的数组维数,在不足维度补零,且保留时间序列信息,以减少训练时间。
51.本发明实施例中,使用机器学习算法预测当前生长数据对应的未来生长质量,包括:将当前生长数据输入训练好的机器学习模型,输出对应的未来生长质量、生产条件参数的调整大小和调整方向。
52.图2示意性示出了根据本发明实施例的生长质量判断过程的流程图。
53.本发明实施例中,未来生长质量包括未来生长状态和未来成品尺寸,预设的生长质量阈值包括生长状态阈值和成品尺寸阈值。在此基础上,如图2所示,上述步骤s3具体可以包括步骤s31~步骤s32。
54.步骤s31,判断未来生长状态是否小于生长状态阈值,如果否,则使用机器学习模型输出生产条件参数的调整大小和调整方向,得到更新后的生产条件参数,重复上述步骤s1~步骤s2继续生长,直至未来生长状态小于生长状态阈值。
55.步骤s32,继续判断未来成品尺寸是否小于成品尺寸阈值,如果是,则继续生长,否则结束生长。
56.通过上述实施例,本发明在样品生长之前预先设置有尺寸要求(也即成品尺寸阈值)和生长状态要求(也即生长状态阈值)。在样品生长过程中,可在上位机控制作用下监测样品的当前生长尺寸,并获取当前生长数据,调用机器学习模型输出对应的未来生长质量、生产条件参数的调整大小和调整方向。然后双重判断样品的未来生长状态和未来成品尺寸是否都满足预设的生长质量阈值,具体是先判断未来生长状态,再判断未来成品尺寸,在两者都满足的情况下结束生长,从而获得所需的样品生长成品。
57.为了获得更稳定适应性更好的机器学习算法模型,需要不断对所采用的算法数据进行优化。由于半导体生长过程中参数调整缓慢,同时对所有需要调整的参数进行矫正,易造成模型过拟合或欠拟合,即导致已经训练的模型失效,为了减少该现象发生的可能性,高效地实现网络参数调整,可以对生产条件参数的调整大小和调整方向进行更为具体的界定。
58.图3示意性示出了根据本发明实施例的生产条件参数调整过程的流程图。
59.本发明实施例中,生产条件参数包括多组工艺参数。在此基础上,如图3所示,上述步骤s3中的使用机器学习算法调整生产条件参数,具体可以包括步骤s33~步骤s35。
60.步骤s33,计算每组工艺参数与预设的生长质量阈值之间的偏差程度。
61.步骤s34,获取最大偏差程度下的一组工艺参数,记为目标工艺参数。
62.步骤s35,利用梯度算法调整目标工艺参数,确定生产条件参数的调整大小和调整方向。
63.通过上述实施例,对生产条件参数的调整大小和调整方向进行进一步的参数筛
选。首先计算出每组工艺参数的偏差程度,找出与预设的生长质量阈值偏差最大的一组工艺参数。由于设备生长参数在调整过程中存在延迟现象,设备瞬间响应也会对材料生长质量造成较大影响,所以依据主循环周期设置梯度算法步幅大小,并由此作用计算每次需要调整的温度变化情况,在一定时间周期内完成对生长工艺参数的调整。由此调整可避免瞬态变化对生长薄膜的影响,减少由此产生的薄膜缺陷从而影响最终的性能。
64.本发明实施例中,作为原始数据集输入机器学习网络进行训练,得到训练好的机器学习模型,还包括:将原始数据集拆分为训练数据集和测试数据集,使用训练数据集输入机器学习网络进行训练,使用测试数据集测试机器学习模型的有效性,并在训练过程中引入交叉验证,直至得到训练好的机器学习模型。
65.具体地,可将原始数据集中的五分之四设定为训练数据集,五分之一设定为测试数据集,在训练过程中引入交叉验证,在模型测试阶段选取误差最小的网络参数作为最佳网络参数。
66.该机器学习模型具体根据原始数据集的数据量和预设的生长质量阈值进行设置。可选地,机器学习网络包括深度神经网络或者长短期记忆人工神经网络。
67.由于该训练过程包含时序特征,故在网络模型选择时优选长短期记忆人工神经网络,该网络可以保留过程时间序列对未来数据变化的影响。当原始数据集包含的数据类型不多时,可采用深度神经网络进行分析,经过测试显示中间层为三层左右,神经元个数为八个左右可以实现在较少数据下的低误差,由此确定机器学习模型。
68.综上所述,本发明实施例提供了一种基于机器学习的半导体工艺过程控制方法,采用非接触性且对材料生长过程影响较小甚至没有影响的原位表征手段作为数据获取来源,有效避免现有需要接触样品表面的原位表征手段,在表征过程中对材料表面产生划痕、脏污、引入缺陷的影响;采用非接触且对样本生长过程影响较小的原位表征方法,避免生长过程中断和由再生长而引入生长参数偏离、缺陷增加等情形发生,保障材料生长质量;采用无需将样品移出当前生长环境的表征手段,即原位表征手段的收发装置与样品生长环境位于同一个生长室内,这种无需移出生长环境的方法,可以有效避免人在操作过程中,操作失误风险,也避免由此带来的时间成本压力。
69.在本发明的描述中,需要理解的是,术语“非接触性”为绝对不碰到样品,且在表征过程中,由原位表征装置发射的探测信号与真实样品之间存在一定距离,该距离使得在整个生长室内,由源炉产生的分子束可以直接传输至待生长样品表面,该传输过程仅在真空中直线传输,不会收到原位表征装置的探测接收装置所处位置阻挡,即探测接收位置距离样品表面所处位置也有一段距离,整个原位表征装置发射端与接收端都距离样品有一定距离;术语“时域”为与时间变化相关的参数或数据形式,该参数对应的数据或参数会由于时间的改变而产生变化;术语“尺寸”一般为材料生长厚度尺寸信息;术语“吸收光谱”指光在半导体样品上作用时,某些波长的光被半导体样品吸收,因此在连续光谱中有一段或几段波长的光减弱了或消失了,连续光谱变化后的结果曲线为吸收光谱,吸收光谱仅为本发明实施例采用的一种具体的光学监测方法,本发明实施例包含但不限于该光学监测方法中的吸收光谱,也可为反射光谱、发光光谱穆斯堡尔光谱等一种或多种组合。
70.在本发明的描述中,“多个”的含义是至少两个,例如两个、三个等,除非另有明确具体的限定。此外,位于元件之前的单词“一”或“一个”不排除存在多个这样的元件。
71.以上所述的具体实施例,对本发明的目的、技术方案和有益效果进行了进一步详细说明,所应理解的是,以上所述仅为本发明的具体实施例而已,并不用于限制本发明,凡在本发明的精神和原则之内,所做的任何修改、等同替换、改进等,均应包含在本发明的保护范围之内。