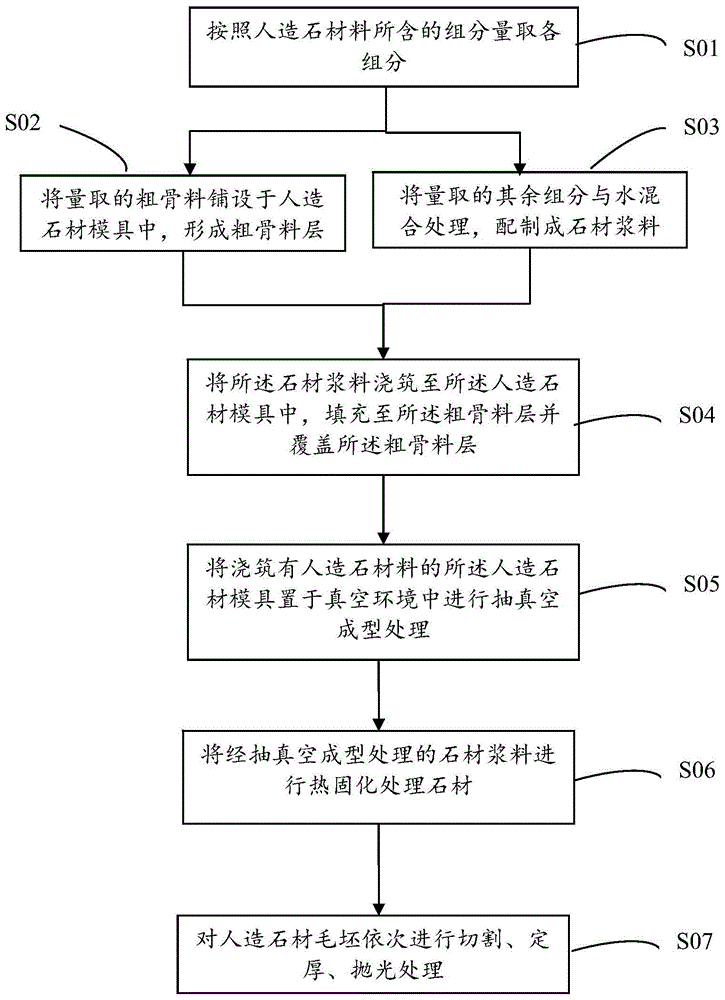
本发明属于建材
技术领域:
,具体涉及一种人造石材料、人造石材浆料和人造石材制备方法。
背景技术:
:我国天然石资源虽然十分丰富,但是浪费量惊人,成材率仅达30%左右,且能源开采有一定的局限性,故利用天然石材加工后的边角料及其它辅料加工合成生产人造石成为石材发展的主要方向。人造石具有高强度、高阻燃、高耐候、颜色可选性广、仿石材效果逼真、装饰效果好、适于工厂化生产、施工便利等优点,使其成为当今各种高档建筑物的内外墙装饰材料。市场中现有的人造岗石,主要是有机人造岗石,是由天然大理石碎料、石粉为主要原材料,以有机树脂为胶结剂,经真空搅拌、高压振动制成方料,再经过室温固化、切割、打磨、抛光等工序制成,耐磨性较差、硬度较软、耐候性差,怕日晒雨淋和紫外线照射,在强紫外线作用下易老化、变色、开裂、变形,强热条件下易变形,有异味,且石材本身带有有害射线,对人体有影响。目前也有少量无机人造岗石报道,是由天然大理石碎料、石粉为主要原材料,以水泥、矿物掺合料为胶结剂,经搅拌、真空压制成方料,再经过养护、切割、打磨、抛光等工序制成。由于方料板的厚度较厚,且拌合物为干硬性状态,需要大型压机,对设备要求较高,并且方料板容易出现表面气孔多的问题,如果将制作无机人造岗石的拌合物流动性较大,采用真空成型制备方料板,又容易造成粗骨料下沉的问题,从而导致无机人造岗石成分分散不均匀,抗压强度低,电通量大,而且还影响板面效果。技术实现要素:本发明的目的在于提供一种人造石材制备方法,以解决现有人造石材制备方法存在的容易造成粗骨料下沉、表面气孔多而且成本高的技术问题。为了实现上述发明目的,本发明的提供了一种人造石制备方法。所述人造石材制备方法包括以下步骤:按照人造石材料所含的组分量取各组分;所述人造石材料包括粗骨料和用于配制成石材浆料的组分;将量取的粗骨料铺设于人造石材模具中,形成粗骨料层;将量取的其余组分与水进行混合处理,配制成石材浆料;将所述石材浆料浇筑至所述人造石材模具中,填充至所述粗骨料层并覆盖所述粗骨料层;将浇筑有人造石材料的所述人造石材模具置于真空环境中进行抽真空成型处理;将经抽真空成型处理的所述石材浆料进行热固化处理。与现有技术相比,本发明具有以下的技术效果:本发明人造石材制备方法通过先将粗骨料铺设在待成型人造石材的模具中,然后再将含有细骨料的石材浆料填充至所述粗骨料中,这样有效提高了骨料组分分布的均匀性,减少流态人造石材离析、泌水、粗骨料下沉等问题,提高了人造石材密实度和力学性能及耐久性能,而且制备的人造石材体积稳定性好、低收缩、使用不翘曲变形,吸水率极低、耐久性能好,不存在老化等问题,表面耐污性能好,成本低。附图说明为了更清楚地说明本发明具体实施方式或现有技术中的技术方案,下面将对具体实施方式或现有技术描述中所需要使用的附图作简单地介绍,显而易见地,下面描述中的附图是本发明的一些实施方式,对于本领域普通技术人员来讲,在不付出创造性劳动的前提下,还可以根据这些附图获得其他的附图。图1为本发明实施例人造石材制备方法工艺流程示意图。具体实施方式为了使本申请要解决的技术问题、技术方案及有益效果更加清楚明白,以下结合实施例,对本申请进行进一步详细说明。应当理解,此处所描述的具体实施例仅仅用以解释本申请,并不用于限定本申请。本申请中,术语“和/或”,描述关联对象的关联关系,表示可以存在三种关系,例如,a和/或b,可以表示:单独存在a,同时存在a和b,单独存在b的情况。其中a,b可以是单数或者复数。字符“/”一般表示前后关联对象是一种“或”的关系。本申请中,“至少一个”是指一个或者多个,“多个”是指两个或两个以上。“以下至少一项(个)”或其类似表达,是指的这些项中的任意组合,包括单项(个)或复数项(个)的任意组合。例如,“a,b,或c中的至少一项(个)”,或,“a,b,和c中的至少一项(个)”,均可以表示:a,b,c,a-b(即a和b),a-c,b-c,或a-b-c,其中a,b,c分别可以是单个,也可以是多个。应理解,在本申请的各种实施例中,上述各过程的序号的大小并不意味着执行顺序的先后,部分或全部步骤可以并行执行或先后执行,各过程的执行顺序应以其功能和内在逻辑确定,而不应对本申请实施例的实施过程构成任何限定。在本申请实施例中使用的术语是仅仅出于描述特定实施例的目的,而非旨在限制本申请。在本申请实施例和所附权利要求书中所使用的单数形式的“一种”和“该”也旨在包括多数形式,除非上下文清楚地表示其他含义。本申请实施例说明书中所提到的相关成分的重量不仅仅可以指代各组分的具体含量,也可以表示各组分间重量的比例关系,因此,只要是按照本申请实施例说明书相关组分的含量按比例放大或缩小均在本申请实施例说明书公开的范围之内。具体地,本申请实施例说明书中的质量可以是μg、mg、g、kg等化工领域公知的质量单位。本发明实施例下文涉及的名称解释说明:粗骨料:指在人造石材中,砂、石起骨架作用,称为骨料或集料,其中粒径大于5mm的骨料称为粗骨料。细骨料:是与粗骨料相对的建筑材料,细骨料是一种直径相对较小的骨料。人造石材中起骨架或填充作用的粒状松散材料,粒径在4.75mm以下的骨料称为细骨料。本发明实施例提供了人造石材制备方法。所述人造石材制备方法的工艺流程如图1所示,其包括以下步骤:s01.按照人造石材料所含的组分量取各组分;所述人造石材料包括粗骨料和用于配制成石材浆料的组分;s02.将量取的粗骨料铺设于人造石材模具中,形成粗骨料层;s03.将量取的其余组分与水进行混合处理,配制成石材浆料;s04.将所述石材浆料浇筑至所述人造石材模具中,填充至所述粗骨料层并覆盖所述粗骨料层;s05.将浇筑有人造石材料的所述人造石材模具置于真空环境中进行抽真空成型处理;s06.将经抽真空成型处理的所述石材浆料热固化处理石材。其中,其中,所述步骤s01中的用于配制成石材浆料的组分优选包括矿物活性粉体、细骨料、二氧化硅、憎水剂、减水剂和颜料。因此,一实施例中,所述人造石材料包括如下组分:矿物活性粉体60~90份;粗骨料110~150份;细骨料30~70份;二氧化硅4~8份;憎水剂0.5~2份;减水剂2~6份;颜料4~10份。这样,所述人造石材料通过增添粗骨料、并使得粗骨料与细骨料构成复合骨料组分,在所含的其他组分的作用下,能够在凝固成型过程中增强骨料的密度并提高骨料分布的均匀性,从而提高人造石材的力学性能及耐久性能。同时所述人造石材体积稳定性好、低收缩、使用不翘曲变形,吸水率极低、耐久性能好,不存在老化等问题,表面耐污性能好,颜色稳定且可调。在一实施例中,所述粗骨料的包括粒径为5-40mm。如粒径为5-10mm和粒径为10-20mm的混合物。通过控制粗骨料的粒径或优选设置不同颗粒粒径的粗骨料,与细骨料构成复合骨料,减少骨料间的空隙,提高骨料的密实度,从而提高人造石材的抗压强度。在具体实施例中,所述粗骨料包括玄武岩碎石、石英碎石、石灰石碎石中的至少一种。选用该类型的粗骨料,强度高,而且颗粒可控,来源丰富。在另一实施例中,所述细骨料包括河砂、石英砂、机制砂中的至少一种。优选地,所述细骨料的粒径为20~70目。所述人造石材料所含的所述二氧化硅能够提高人造石板的耐磨性能和防水性能。优选地,所述二氧化硅的粒径为纳米级,也即是二氧化硅为纳米二氧化硅。所述人造石材料所含的矿物活性粉体能够起胶结作用,将骨料胶结成整体。在一实施例中,所述矿物活性粉体的粒径为5-45μm。在另一实施例中,所述矿物活性粉体是以白水泥为主体掺加白色硅灰、矿粉、玻璃微珠、沸石粉、偏高岭土中的至少一种活性粉体。所述人造石材料所含的憎水剂、减水剂等组分与上文所述细骨料与粗骨料协同作用,使得在提高所述复合骨料组分在人造石材凝固成型过程中分布的均匀性的前提下,赋予人造石材良好的体积稳定性、低收缩、不翘曲变形、吸水率极低、耐久性能好等优点。在一实施例中,所述憎水剂包括聚硅氧烷、有机硅中的至少一种。在另一实施例中,所述减水剂为高性能聚羧酸减水剂。在另一实施例中,所述颜料包括无机颜料(钛白、铁黑、铁红、铁黄、铁蓝、铁绿等)、有机颜料(酞青蓝、酞青绿、耐晒黄、永固红等)中的至少一种。所述步骤s02中的人造石材模具可以根据待成型人造石材的尺寸和形状进行设置。将粗骨料铺设在人造石材模具中可以是随机铺设,也可以根据所述待成型人造石材的应用需要或强度需要有针对性的铺设,使得所述粗骨料建议铺设的前提下以满足应用对待成型人造石材强度的需要。在一实施例中,在将所述粗骨料铺设至所述人造石材模具中的步骤之前,还包括先将所述粗骨料进行搅拌混合处理的步骤。通过预先对所述粗骨料进行混合处理,使得粗骨料在搅拌混合处理过程中互相碰撞摩擦处理,从而减少粗骨料的尖锐面,提高粗骨料与浆体的界面结合力,从而最终提高人造石材的力学性能。如在具体实施例中,所述搅拌混合处理可以是通过搅拌机进行搅拌混合处理。所述搅拌混合处理的时间至少为60s以上,以保证所述粗骨料颗粒范围的前提下,充分磨掉粗骨料所含的尖锐面,提高粗骨料与浆体的界面结合力。所述步骤s03中的其余组分如上文所述,包括上文所述矿物活性粉体、细骨料、二氧化硅、憎水剂、减水剂和颜料等,并按照上文该些组分的混合比例进行加料与水进行混合处理。所述混合处理可以按照常规石材浆料配制方法进行配制,使得各组分充分混合均匀即可。在一实施例中,步骤s03中将量取的其余组分与水混合处理包括如下步骤:s031:将细骨料、二氧化硅、憎水剂、颜料进行混料处理,得到第一混合料;s032:将矿物活性粉体和40~50wt%的水加入所述第一混合料进行混合处理,得到第二混合料;s033:将减水剂和剩余的水加入到所述第二混合料进行混合处理,得到所述石材浆料。其中,步骤s031中的混料处理和步骤s032和步骤s033中的混合处理均可以是采用常规的物理混合处理方式,如置于搅拌机中进行搅拌混合处理。另外,所述混料处理应该是充分的,如步骤s031和步骤s032中的搅拌混合处理1-2分钟。步骤s033的搅拌混合处理7-9分钟。在一实施例中,步骤s032和步骤s033中,所述水加入的量优选按照水与所述人造石材料中的所述粗骨料的重量比为(10~18):(110~150)的比例进行添加,也即是在步骤s03的所述人造石材浆料中,所述水与所述人造石材料中的所述粗骨料的重量比为(10~18):(110~150)。在另一实施例中,所述步骤s03中通过控制各物料与水混合比例优化和混合处理的优化,使得最终混合处理形成的石材浆料的扩展度为600~800mm,初凝凝结时间不小于60分钟,以使得各组分充分混合均匀,而且具有适度的流动性,从而使得所述石材浆料能够有效在步骤s04中充分填充至铺设于模具中的粗骨料层中,从而使得最终获得的人造石材强度高,且性能均匀。另外,所述步骤s03与步骤s02不分先后顺序。所述步骤s04中的将所述石材浆料浇筑至所述人造石材模具中的方法可以按照人造石材领域常规的灌浆方式浇筑所述石材浆料,使得所述石材浆料填充至所述粗骨料层的所述空隙部分并包覆所述粗骨料。所述步骤s05中的所述抽真空成型处理为人造石材模具处于负压环境中,使得所述石材浆料或粗骨料层中残留的空气在负压的作用下排除,从而使得石材浆料能够充分填充所述粗骨料层,并提高石材浆料的填充效率,提高石材浆料填充的均匀性。因此,在一实施例中,所述抽真空成型处理的抽真空时间不少于120s,真空压力为-0.07~-0.1mpa。所述步骤s06中的热固化过程中,浇筑在人造石材模具中的所述石材浆料被凝固。在一实施例中,所述热固化处理的方法包括如下步骤:先于35~45℃下固化8~12小时,再升温至80~90℃固化24~36小时。这样通过对热固化处理条件的控制和优化,提高固化形成人造石材的力学性能和提高人造石材体积稳定性和耐久性以及表面耐污性能,降低吸水率。在另一实施例中,所述热固化处理过程中,被浇筑至所述人造石材模具中所述石材浆料的湿度保持在75%以上,优选的是在80~90℃固化过程中湿度保持在75%以上。保持热固化处理过程中的湿度,提高热固化处理的效果。为了保证热固化处理过程中的湿度,在一实施例中,在所述热固化处理过程之前,先在被浇筑至所述人造石材模具中所述石材浆料的表面覆上隔离保湿膜,以保证所述被浇筑至所述人造石材模具中所述石材浆料的湿度,以提高热固化处理的效果。在一实施例中,通过对所述人造石材模具的如高度等尺寸控制或者通过对浇筑至所述人造石材模具中的所述石材浆料的量控制,使得经热固化处理形成的人造石材的厚度为600~1200mm。另外,经过所述步骤s06热固化处理后形成的人造石料可以理解是人造石料的毛坯料。因此,一实施例中,在所述步骤s06的热固化处理之后,还包括如果图1中所示的步骤s07:对人造石材毛坯依次进行切割、定厚、抛光处理等工艺步骤,得到人造石材产品。其中,所述切割、定厚、抛光处理等工艺可以采用石材加工常规的相应步骤进行操作即可。因此,上文所述人造石材制备方法通过先将粗骨料铺设在待成型人造石材的模具中,然后再将含有细骨料的石材浆料填充至所述粗骨料中,这样有效提高了骨料组分分布的均匀性,减少流态人造石材离析、泌水、粗骨料下沉等问题,提高了人造石材力学性能和密实度以及耐久性能,如人造石材的抗压强度大于100兆帕,而且经过抽真空成型处理,减少了所述人造石材可能残留的气泡,避免了后期二次修补气孔的工序,有效提高了生产效率。另外制备的人造石材体积稳定性好、低收缩、使用不翘曲变形,吸水率极低、耐久性能好,不存在老化等问题,表面耐污性能好,成本低。另外,所述制备方法工艺条件可控,能够有效保证制备的人造石材性能的稳定性,效率高。以下通过多个具体实施例来举例说明本发明实施例人造石材料和人造石材制备方法等。实施例1本实施例提供了一种人造石材料的人造石材制备方法。所述人造石材料包括:矿物活性粉体60份,白水泥+矿粉;粗骨料110份,玄武岩碎石,粒径5~20mm;细骨料30份,石英砂,粒径20~70目;纳米二氧化硅4份;憎水剂0.5份,聚硅氧烷;减水剂2份,高性能聚羧酸减水剂;颜料4份,钛白粉。所述人造石材制备方法包括如下步骤:s1.按配比计算各原材料用量,将不同粒径粗骨料投入搅拌机,搅拌90-120秒,得搅拌均匀的粗骨料,然后将粗骨料铺入模具中,粗骨料与模具上端面齐平,备用;s2.将全部细骨料、纳米二氧化硅、憎水剂、颜料加入搅拌机中搅拌1~2分钟;s3.将全部矿物活性粉体和40wt%的水加入步骤s2所得预混骨料中搅拌1~2分钟;s4.将全部减水剂和剩余60wt%的水加入到步骤s3所得预湿的混合料中,充分搅拌7~9分钟,得到混合物,混合物材料扩展度为600~800mm,搅拌混合后初凝凝结时间不小于60分钟,备用;s5.依据厚度计算并称取步骤s4备好的混合料均匀浇灌在布满碎石的模具内;s6.在步骤s5模具内的混合料上覆上隔离保湿膜,然后放入真空室进行抽真空排气,抽真空时间120s,真空压力为-0.07mpa;s7.将步骤s6抽真空成型的板在35℃下固化8小时,再升温至80℃固化24小时得到毛坯板,毛坯板的厚度为600mm,高温固化过程保持湿度在75%以上;s8.将步骤s7得到的毛坯板取掉隔离保湿膜进行切割、定厚、抛光,得到人造石材。实施例2本实施例提供了一种人造石材料的人造石材制备方法。所述人造石材料包括的组分如同实施例1。所述人造石材制备方法包括如下步骤:s1.按配比计算各原材料用量,将不同粒径粗骨料投入搅拌机,搅拌90-120秒,得搅拌均匀的粗骨料,然后将粗骨料铺入模具中,粗骨料与模具上端面齐平,备用;s2.将全部细骨料、纳米二氧化硅、憎水剂、颜料加入搅拌机中搅拌1~2分钟;s3.将全部矿物活性粉体和50wt%的水加入步骤s2所得预混骨料中搅拌1~2分钟;s4.将全部减水剂和剩余50wt%的水加入到步骤s3所得预湿的混合料中,充分搅拌7~9分钟,得到混合物,混合物材料扩展度为600~800mm,搅拌混合后初凝凝结时间不小于60分钟,备用;s5.依据厚度计算并称取步骤s4备好的混合料均匀浇灌在布满碎石的模具内;s6.在步骤s5模具内的混合料上覆上隔离保湿膜,然后放入真空室进行抽真空排气,抽真空时间120s,真空压力为-0.1mpa;s7.将步骤s6抽真空成型的板在45℃下固化12小时,再升温至90℃固化36小时得到毛坯板,毛坯板的厚度为1200mm,高温固化过程保持湿度在75%以上;s8.将步骤s7得到的毛坯板取掉隔离保湿膜进行切割、定厚、抛光,得到人造石材。实施例3本实施例提供了一种人造石材料的人造石材制备方法。所述人造石材料包括的组分如同实施例1。所述人造石材制备方法包括如下步骤:s1.按配比计算各原材料用量,将不同粒径粗骨料投入搅拌机,搅拌90-120秒,得搅拌均匀的粗骨料,然后将粗骨料铺入模具中,粗骨料与模具上端面齐平,备用;s2.将全部细骨料、纳米二氧化硅、憎水剂、颜料加入搅拌机中搅拌1~2分钟;s3.将全部矿物活性粉体和45wt%的水加入步骤s2所得预混骨料中搅拌1~2分钟;s4.将全部减水剂和剩余55wt%的水加入到步骤s3所得预湿的混合料中,充分搅拌7~9分钟,得到混合物,混合物材料扩展度为600~800mm,搅拌混合后初凝凝结时间不小于60分钟,备用;s5.依据厚度计算并称取步骤s4备好的混合料均匀浇灌在布满碎石的模具内;s6.在步骤s5模具内的混合料上覆上隔离保湿膜,然后放入真空室进行抽真空排气,抽真空时间120s,真空压力为-0.08mpa;s7.将步骤s6抽真空成型的板在40℃下固化10小时,再升温至85℃固化30小时得到毛坯板,毛坯板的厚度为900mm,高温固化过程保持湿度在75%以上;s8.将步骤s7得到的毛坯板取掉隔离保湿膜进行切割、定厚、抛光,得到人造石材。实施例4本实施例提供了一种人造石材制备方法。所述人造石材料包括:矿物活性粉体60份,白水泥+白硅灰;粗骨料110份,石英碎石,粒径5~20mm;细骨料30份,机制砂,粒径20~70目;纳米二氧化硅4份;憎水剂0.5份,有机硅;减水剂2份,高性能聚羧酸减水剂;颜料4份,钛白。所述人造石材制备方法包括如下步骤:s1.准备可拆装模具,组装好的模具为一个封闭的长方体,模具右侧下方留有一个直径50mm的灌浆孔球阀,模具右侧上方留有一个直径50mm的抽真空球阀;s2.按配比计算各原材料用量,将不同粒径粗骨料投入搅拌机,搅拌90-120秒,得搅拌均匀的粗骨料,然后将粗骨料铺入模具中,铺平,将模具组装好备用;s3.将全部细骨料、纳米二氧化硅、憎水剂、颜料加入搅拌机中搅拌1~2分钟;s4.将全部矿物活性粉体和40wt%的水加入步骤s2所得预混骨料中搅拌1~2分钟;s5.将全部减水剂和剩余60wt%的水加入到步骤s3所得预湿的混合料中,充分搅拌7~9分钟,得到混合物,混合物材料扩展度为600~800mm,搅拌混合后初凝凝结时间不小于60分钟,备用;s6.依据厚度计算并称取步骤s5备好的混合料从模具的灌料口泵送到步骤s2布满粗骨料的模具内;s7.将步骤s6模具连通真空泵,进行抽真空排气,抽真空时间为120s,真空压力为-0.07mpa;s8.将步骤s7抽真空成型的板在35℃下固化8小时,脱模,再升温至80℃固化24小时得到毛坯板,毛坯板的厚度为600mm,高温固化过程保持湿度在75%以上;s9.将步骤s8得到的毛坯板进行切割、定厚、抛光,得到人造石板。实施例5本实施例提供了一种人造石材制备方法。所述人造石材料包括:矿物活性粉体60份,白水泥+矿粉+偏高岭土;粗骨料110份,石灰石碎石,粒径5~20mm;细骨料30份,河砂,粒径20~70目;纳米二氧化硅4份;憎水剂0.5份,有机硅;减水剂2份,高性能聚羧酸减水剂;颜料4份,钛白。所述人造石材制备方法包括如下步骤:s1.准备可拆装模具,组装好的模具为一个封闭的长方体,模具右侧下方留有一个直径50mm的灌浆孔球阀,模具右侧上方留有一个直径50mm的抽真空球阀;s2.按配比计算各原材料用量,将不同粒径粗骨料投入搅拌机,搅拌90-120秒,得搅拌均匀的粗骨料,然后将粗骨料铺入模具中,铺平,将模具组装好备用;s3.将全部细骨料、纳米二氧化硅、憎水剂、颜料加入搅拌机中搅拌1~2分钟;s4.将全部矿物活性粉体和40wt%的水加入步骤s2所得预混骨料中搅拌1~2分钟;s5.将全部减水剂和剩余60wt%的水加入到步骤s3所得预湿的混合料中,充分搅拌7~9分钟,得到混合物,混合物材料扩展度为600~800mm,搅拌混合后初凝凝结时间不小于60分钟,备用;s6.依据厚度计算并称取步骤s5备好的混合料从模具的灌料口泵送到步骤s2布满粗骨料的模具内;s7.将步骤s6模具连通真空泵,进行抽真空排气,抽真空时间为120s,真空压力为-0.07mpa;s8.将步骤s7抽真空成型的板在35℃下固化8小时,脱模,再升温至80℃固化24小时得到毛坯板,毛坯板的厚度为600mm,高温固化过程保持湿度在75%以上;s9.将步骤s8得到的毛坯板进行切割、定厚、抛光,得到人造石板。对比例1本对比例提供了一种人造石材料和基于所述人造石材料的人造石材制备方法。所述人造石材料包括的组分如同实施例1。所述人造石材制备方法包括如下步骤:s1.按配比计算各原材料用量,将全部细骨料、纳米二氧化硅、憎水剂、颜料加入搅拌机中搅拌1~2分钟;s2.将全部矿物活性粉体和40wt%的水加入步骤s1所得预混骨料中搅拌1~2分钟;s3.将全部减水剂和剩余60wt%的水加入到步骤s2所得预湿的混合料中,充分搅拌7~9分钟,再将全部粗骨料加入,搅拌1~2分钟,得到混合物,混合物材料扩展度为600~800mm,搅拌混合后初凝凝结时间不小于60分钟,备用;s4.依据厚度计算并称取步骤s3备好的混合料均匀浇灌在模具内;s5.在步骤s4模具内的混合料上覆上隔离保湿膜,然后放入真空室进行抽真空排气,抽真空时间120s,真空压力为-0.07mpa;s6.将步骤s5抽真空成型的板在40℃下固化8小时,再升温至80~90℃固化24小时得到毛坯板,毛坯板的厚度为600mm,高温固化过程保持湿度在75%以上;s7.将步骤s6得到的毛坯板取掉隔离保湿膜进行切割、定厚、抛光,得到人造石材。人造石材相关特性测试对实施例1-3和对比例1所浇筑形成的人造石材进行了标准试件标准养护28天的抗压强度及电通量测试,试验数据见表1:表1人造石材试验数据编号抗压强度(mpa)电通量(c)毛坯板截面粗骨料分布实施例1101.993分布均匀实施例2109.579分布均匀实施例3115.755分布均匀实施例4105.386分布均匀实施例5103.990分布均匀对比例185.7285粗骨料分布不均匀,出现分层现象从表1来看,对比例1采用传统“砂浆裹石法”与实施例1堆积成型法相比,抗压强度下降较多,电通量升高较多,粗骨料分布不均匀,出现分层现象。而本发明实施例1-5成型的人造石材在粗骨料分布方面具有明显优势,其说明本发明实施例人造石制备方法使人造石材各组分材料分散更均匀,适合制备力学和耐久性能更优的人造石。相同材料配比时,本发明实施例制备方法可以提高人造石材强度,而且其无气泡,从而无需二次修补气孔的工序,提高生产效率。以上所述仅为本发明的较佳实施例而已,并不用以限制本发明,凡在本发明的精神和原则之内所作的任何修改、等同替换和改进等,均应包含在本发明的保护范围之内。当前第1页12